矿泉水瓶吹塑模设计.docx
《矿泉水瓶吹塑模设计.docx》由会员分享,可在线阅读,更多相关《矿泉水瓶吹塑模设计.docx(28页珍藏版)》请在冰豆网上搜索。
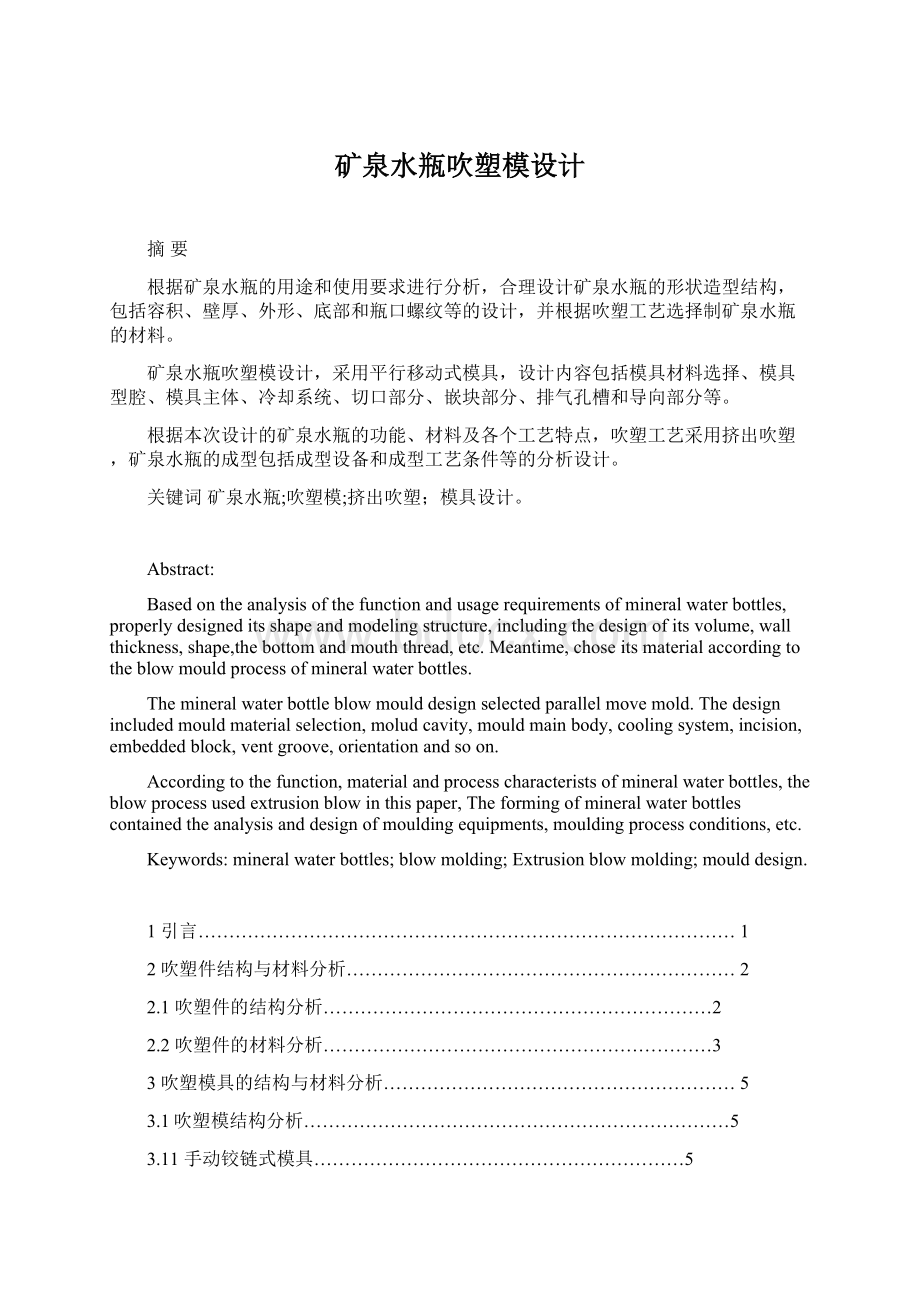
矿泉水瓶吹塑模设计
摘要
根据矿泉水瓶的用途和使用要求进行分析,合理设计矿泉水瓶的形状造型结构,包括容积、壁厚、外形、底部和瓶口螺纹等的设计,并根据吹塑工艺选择制矿泉水瓶的材料。
矿泉水瓶吹塑模设计,采用平行移动式模具,设计内容包括模具材料选择、模具型腔、模具主体、冷却系统、切口部分、嵌块部分、排气孔槽和导向部分等。
根据本次设计的矿泉水瓶的功能、材料及各个工艺特点,吹塑工艺采用挤出吹塑,矿泉水瓶的成型包括成型设备和成型工艺条件等的分析设计。
关键词矿泉水瓶;吹塑模;挤出吹塑;模具设计。
Abstract:
Basedontheanalysisofthefunctionandusagerequirementsofmineralwaterbottles,properlydesigneditsshapeandmodelingstructure,includingthedesignofitsvolume,wallthickness,shape,thebottomandmouththread,etc.Meantime,choseitsmaterialaccordingtotheblowmouldprocessofmineralwaterbottles.
Themineralwaterbottleblowmoulddesignselectedparallelmovemold.Thedesignincludedmouldmaterialselection,moludcavity,mouldmainbody,coolingsystem,incision,embeddedblock,ventgroove,orientationandsoon.
Accordingtothefunction,materialandprocesscharacteristsofmineralwaterbottles,theblowprocessusedextrusionblowinthispaper,Theformingofmineralwaterbottlescontainedtheanalysisanddesignofmouldingequipments,mouldingprocessconditions,etc.
Keywords:
mineralwaterbottles;blowmolding;Extrusionblowmolding;moulddesign.
1引言……………………………………………………………………………1
2吹塑件结构与材料分析………………………………………………………2
2.1吹塑件的结构分析………………………………………………………2
2.2吹塑件的材料分析………………………………………………………3
3吹塑模具的结构与材料分析…………………………………………………5
3.1吹塑模结构分析……………………………………………………………5
3.11手动铰链式模具……………………………………………………5
3.12平行移动式模具……………………………………………………5
3.13挤出吹塑模具………………………………………………………6
3.2吹塑模具的材料分析……………………………………………………7
4挤出吹塑机头尺寸计算………………………………………………………7
4.1出模膨胀系数选择…………………………………………………………8
4.2挤出机头设计原则………………………………………………………8
5吹塑模具的型腔的设计………………………………………………………10
5.1分型面选择………………………………………………………………10
5.2型腔表面处理…………………………………………………………10
5.3型腔尺寸计算…………………………………………………………10
6吹塑模具的颈部及底部嵌块设计……………………………………………13
7吹塑模具的夹坯口与余料槽设计……………………………………………15
7.1剪口尺寸………………………………………………………………15
7.2剪口部位………………………………………………………………15
8吹塑模具的冷却系统设计……………………………………………………16
8.1冷却系统设计原则……………………………………………………16
8.2开设冷却系统…………………………………………………………17
9吹塑模具的排气系统设计……………………………………………………19
10成型设备选择…………………………………………………………………20
11中空制品缺陷的产生原因及解决措施………………………………………20
参考文献…………………………………………………………………………24
致谢………………………………………………………………………………25
1引言
中空吹塑成型主要适合加工包装容器和中空制品.适于该种成型的原料有:
高压聚乙烯(HDPE)、低压聚乙烯(LDPE)、硬聚氯.乙烯(HPVC)、软聚氯乙烯(SPVC)、纤维紊塑料、聚苯乙烯(Ps)、聚丙烯(PP)、聚碳酸酯(Pc)等。
目前常用的吹塑制品原料是以聚乙烯(PE)和聚氯乙烯(PVC)为主。
因为聚乙烯制品无毒,容易加工,聚氯乙烯价廉,透明性和印刷性能较好。
中空成型是把熔融状态的塑料制成型坯,置入模具内闭合模具通入压缩空气(气压为2.7~5Kg/cm
),将型坯吹胀成模腔形状制品在模内保压条件下,冷却定型开模取出。
根据成型方法的不同,可以分为以下五种形式。
(1)挤出吹塑成型
目前我国以该种方法为主。
熔融型坯是用挤出机挤出。
其优点是设备和模具简单,缺点是型坯壁厚不易均匀,从而引起塑件壁厚差异。
(2)注射吹塑成型
利用注射模制成型坯,然后把热型坯移入中空吹塑模进行吹塑成型。
其优点是壁厚均匀无飞边,不需后加工。
由于坯料有底,因此制件底都无拼合缝,强度好生产效率也高。
但设备与模具价格较贵。
多用于小而精度高的制件且大批量生产。
(3)拉伸吹塑成型
这种方法是在注吹的基础上,增加了将型坯延伸的工序。
该方法和双向拉伸模的原理相同。
可使分子双轴取向、塑件透明度提高,强度增加。
尤其是可以利用这种方法使聚丙烯取代聚氯乙烯透明制品。
多用于高精度高强度高透明度的制品。
(4)多层吹塑成型
该方法有共挤吹塑法和多段注吹法。
现在实用还是共挤吹塑法。
其原理是挤出机头挤出多层型坯,供中空吹塑。
多层化的目的,无非是改善容器性能:
降低渗透性(加入聚偏氯乙烯层PVDC),遮光(黑色层)、绝热层(发泡层),降低可燃性(充填层)花色装饰(着色装饰层)等。
(5)片材吹塑成型
将压延、挤出成型的片材再加热,使之软化放入型腔,闭模后在片材中间吹入压缩空气,定型后取出制品。
本方法进一步发展即是目前的吸塑成型。
2吹塑件结构与材料分析
2.1吹塑件结构分析
塑件主要根据使用要求设计,由于塑料有其特殊物理机械性能,因此在塑件设计时必须充分发挥其性能上的优点,避免和补偿其缺点,在满足要求的前提下,塑件设计应尽可能简化模具结构,符合成型工艺要求。
a.塑件设计尽量壁厚均匀,无过薄过厚的部分。
外径设计应考虑吹胀比(图1中B/d=B
)B
=2.1~4.1,多取B
=2:
1。
这样可缩小机头尺寸。
b.塑件长度也应考虑延伸比S
(图1中S
=c/b),S
越大塑件强度越高,但也要结合保证塑件的实用剐度和实用壁厚,因此延伸比取S
·B
=4~6较合适。
c.瓶盖与瓶口部分应采用螺纹结合,也有采用凸缘或凸环结合的如图2,一般采用梯形螺纹,不选用细牙螺纹,为了使合模面上的飞边不致影响螺纹旋合,螺纹可设计成断续状。
d.塑件侧壁与底部的交接部分,一般不允许设计成尖角,二界面角采用圆弧过渡,三界面角可用球面过渡。
(R=0.3×
)只有造型装饰部分可采甩尖角。
e.塑件支承面,特别注意要减少结合缝与支承面的重合部分。
因切口的存在将影响塑件放置的平稳性。
同时也要增加底部刚度。
f.塑件的外表面,在无特殊的要求时,应做粗糙的外表面。
尖似磨沙玻璃,或做成绒面,木纹面,皮革面等。
容积:
V=750ml
容器的平均壁厚:
t=1mm
外形:
采用椭圆形容器,这种形状的吹塑制品是针对圆形和方形制品的缺点进行改进的。
它综合了它们的优点,在强度和刚度、变形性等力学性能方面都较好;外观造型好,开发应用颇多。
吹塑制品的外形的几何外形设计除了考虑其实用性外,还应注意美术造型、装饰图案、花纹,以增加制品的直观美.
底部:
通常很少以整个平面作为制品的支承面,并要尽量减小支承面。
对于瓶类制品来说,一般采用环形支承面,若以整个平面作为支承面。
在钳贴熔接部分因存在钳切毛边而凸起,制品放置不稳,采用环形支承面,情况大为改善,且增加了制品底部的刚度。
从生产工艺可知,挤出吹塑制品的底部,一般都是型坯的夹断处,是制品力学性能的薄弱部位。
制品在底部夹缝处的壁厚,比其他部位厚,收缩率也较大,故容易产生翘曲现象,影响制品的直立。
因此,制品底部应设计成内凹形。
制品的转角处及内凹处,均作较大的圆弧过渡。
口部:
为使容器口部能更好地与盖及密闭器配合,容器口部有螺纹结构设计。
在挤出吹塑成型中,容器口部的外直径是由吹塑模具的模腔尺寸决定的;容器口部的内直径由吹塑模具的吹气型芯的外直径尺寸决定的。
这时,容器口部的厚度是由型坯压缩形成的。
若型坯壁的厚度发生变化,容器口部的内径也会发生变化。
生产时,容器口部还会产生收缩、凹陷等不良现象。
为使容器口部与密封盖或封闭器配合紧密,需对容器口部进行二次切削加工。
挤压式的柔性瓶,如眼药水瓶、滴液瓶,其容器孔口的直径很小,可采用吹气针方式。
图1矿泉水瓶结构图
2.2吹塑件的材料分析
吹塑用塑料的性能比较见表1
表1吹塑用塑料的性能比较
材料
密度
刚度
耐冲击强度
耐热性
透明性
POM
1
1
6
6
12
ABS
6
7
6
7
7
CA
3
8
11
7
1
PC
3
6
3
2
4
LDPE
11
11
1
4
17
HDPE
9
10
3
3
10
PP
12
9
6
1
7
PS
6
5
9
8
10
PVC
2
4
9
12
1
材料选择聚丙烯。
聚丙烯的性能:
聚丙烯(PP)是塑料中的后起之秀。
是由丙烯单体(CH
—CH=CH
)聚合而成。
是无毒、无味、半透明塑料。
具有质轻的特点,其密度为0.90~0.91g/cm
,是通用塑料中密度最低的一种。
聚丙烯具有优良的耐热性,长期使用温度可高达100~120℃,短期使用温度为140℃,无载荷时使用温度可达150℃,聚丙烯是通用塑料中唯一能在水中煮沸,并能经受135℃的消毒温度的品种。
以PP为基材的多层容器可在温度高达90℃条件下进行热灌装或消毒处理。
聚丙烯的耐低温性不如聚乙烯,力学强度、刚性和耐应力开裂性都超过高密度聚乙烯,聚丙烯是一种非极性塑料,具有优良的化学稳定性,并且结晶度越高,化学稳定性越好。
聚丙烯具有有优良的耐弯曲疲劳性,很适宜制造盖体合一的容器,带铰链的双层壁的吹塑工具箱等。
聚丙烯的成型性能:
聚丙烯的熔点较高,冷却速率较大,型坯热封性差,易在闭模时夹断。
聚丙烯的收缩率较大,约为1.0%~2.5%,收缩会随制品壁厚、成型工艺、填料加入量的不同而变化。
聚丙烯具有良好的成型性,可采用挤出吹塑、注射吹塑、注射拉伸吹塑等方法制成中空容器。
聚丙烯中空制品的应用:
聚丙烯制得的容器广泛用于食品(如番茄酱、调味品的包装)、药品、化妆品、化学试剂包装;它更适宜要求热灌装、高接触透明度时使用;聚丙烯还可用来吹塑工业制件,如双层壁中空制件、带铰链的工具箱、箱包、耐热容器等。
3吹塑模具的结构与材料分析
3.1吹塑模具结构分析
3.11手动铰链式模具
该种结构形式与玻璃吹塑模相同。
模腔由两个半模形成,在它的一侧装有铰链,另一侧装有开模手柄和闭模销子。
(如图2)。
这种结构一般用于小量生产或试制,成批的生产不采用,且多用于小尺寸的中空塑件。
图2手动铰链式模具
1——铰链2——型腔3——锁紧零件4——手柄
3.12平行移动式模具
该种结构由两半个相同模腔构成,通过合模机使之闭合。
模具(如图3)的安装采用直接安装法为好,即在模具上做出螺纹孔,用螺钉穿过合模机安装板直接紧固。
目前生产几乎都采用该种结构形式。
图3平行移动式模具图
综合考虑,本课题拟采用平行移动式模具,其基本结构包括两半部分,其中一半作为定模,另一半作为动模。
它是由模具型腔、模具主体、冷却系统、切口部分、排气孔槽和导向部分等组成。
3.13挤出吹塑模具
挤出吹塑是应用很广泛的塑件成型方法,它适用于将PE、PP、PVC热塑性工程塑料、热塑性弹性体等聚合物及各种共混物制成各类包装容器、存储罐与桶,还可成型工程配件(如汽车上的燃油箱、仪表板、保险杆、计算机的工作台、外壳及冰箱门等)。
挤出吹塑模具的结构:
吹塑模具主要由两半凹模构成。
因模颈圈与各夹料块较易磨损,故一般做成单独的嵌块,以便于修复或更换。
它们也可与模体做成一体。
吹塑模具起双重作用:
赋予制品形状与尺寸,并使之冷却。
挤出吹塑模具的特点:
与注射成型模具相比,挤出吹塑模具有以下特点:
吹塑模具型腔受到的压力为型坯的吹胀压力,而注射模具型腔内的压力要高得多(10~40MPa)。
因此,吹塑模具对材料的要求较低,选择范围较宽。
吹塑模具只有凹模,且其型腔一般不需经硬化处理,除非要求长期生产。
而注射模包括型芯与型腔。
注射模腔内熔体通过流动来成型,吹塑模腔内型坯则通过膨胀来成型,这可减小制品上的流痕与结合缝及模腔的磨损等问题。
由于没有型芯,吹塑制品上较深的凹陷也能脱模,不需设置像注射模所广泛采用的滑块、顶杆或凸轮等。
另外,吹塑模与真空成型模有相似之处,但其造价较低。
3.2吹塑模具的材料分析
吹塑模具材料的选择要综合考虑导热性能、强度、耐磨性能、抛光性能、成本以及所用塑料与生产批量等因素。
例如,对会产生腐蚀性挥发物的塑料(PVC),要采用耐腐蚀性材料来制造模具或最在模腔上镀耐腐蚀金属。
下面介绍吹塑模具采用的几种材料。
(1)铝;铝是挤出吹塑模具较早采用也是目前普遍采用的材料。
铝的导热性能高、机械加工性与可延性好、密度低,但硬度低、易磨损,当然铝合金的耐磨性会高些。
铝模具的使用寿命约为1×10
~2×10
次。
(2)铜基合金;铜铍合金是吹塑模具较常用的一种材料,具有很好的导热性能、硬度、耐磨性、耐腐蚀性与机械韧性,主要缺点是成本高、机械加工性能比铝差。
铜铍合金可通过机械加工、铸造与热挤压来制造模具。
铜铍合金多数用于制造夹料嵌块,与铝模具配合使用。
有时(尤其是对腐蚀性塑料),整套吹塑模具均由铜铍合金制成。
铜铍合金模具易于通过焊接或镶嵌法来修补。
除铜铍合金外,还有Ni/Si/Cu、Cr/Cu与铝/青铜合金。
(3)钢主要用于制造PVC与工程塑料的吹塑模具,这是因为钢的硬度、耐磨性与韧性极高,通过蚀刻可取得极好的表面花纹。
钢的主要缺点是导热性能差,要通过冷却系统的设计及冷却流体的温度与流动状态等来补偿。
对腐蚀性塑料(如PVC),要采用不锈钢。
钢模具可采用机械加工、冷挤压、铸造或焊接来制造。
钢模具的使用寿命可达10
次。
普通工具钢还用于制造要承受磨损的吹塑模具零件,如夹料嵌块、拉杆、导柱、导套等。
但总的来说,钢在制造吹塑模具方面用得较少。
(4)其他材料:
锌合金的导热性良好、成本低,可用于铸造大型模具或形状不规则模具,还可通过机械加工来制造模具。
锌镍合金也用作吹塑模具材料。
中空吹塑模用材料有:
铸铁、钢、铝、镀铜、锌等。
铸铁用于手动铰链模及小批量生产中,大批量生产中一般不用,因它传热慢、刚性低、不适批量生产。
铝制模有重量轻、传热快、易加工等优点,巳广泛应用,由于其硬度低、耐久性差,故在必要部分采用铜质嵌件。
钢材适用于大批量生产,一般采用碳素结构钢。
在要求较严时采用合金结构钢,目前采用较少,铍铜强度低、传热快、耐磨,适于大批量生产,但成本高.一般用于冷却系统。
锌基台金易于铸造成型、传热快、
适于大型精细模具。
4矿泉水瓶挤出吹塑机头尺寸计算
4.1出模膨胀系数选择
日前各种资料所列的材料的出模膨胀系数均有差异,有的差异较大,与实际生产也有出入。
一方面,这种系数受到加工温度、螺杆的性能、螺杆转速、机头的性能等多方面因素的影响。
加上实际生产中往往采用混合材料,因此,具体某种材料的系数在生产中摸索。
校正是必要的。
表2为总结出来的系数。
聚丙烯的出模膨胀系数取1.6。
表2材料的出模膨胀系数
塑料名称
代号
出模膨胀系数
高密度聚乙烯
HDPE
1.04~1.90
低密度聚乙烯
LDPE
1.30~1.65
聚氯乙烯
PVC
1.05~1.10
聚丙烯
PP
1.55~1.80
聚苯乙烯
PS
1.30~1.60
聚对苯二甲酸乙二酯
PET
1.10~1.35
4.2挤出机头设计原则
从各类日化用品瓶及药葫瓶的整体外形、各种瓶体统计来看,一般瓶体直径是瓶口的2.5倍,这种比值正好是吹胀比的中间值。
因此设计机头时,就以瓶口螺坟外径或瓶口外径为基础,再以使用材料的出模膨胀系数计算,得出机头口模的计算公式。
机头口模内径的计算公式:
D=〔
+b〕
………………………………………………
(1)
=(
+3)
=25.5
式中
D
——模具型腔瓶口的外径(最大尺寸),取D
=36mm.
D——机头口模内径
m——材料的出模膨胀系数。
取1.6
b——修正系数,取3.
——口模内径公差,取0.072
模口:
吹塑中空容器时,模口部分即是吹管部分。
在吹塑时,因它是戚型塑件口部,
故要保证尺寸也要保证切断余料。
(如图4)。
图4(锥形口模口)(球形模口)
型坯尺寸:
塑料制品最大直径与型坯直径的比值称为吹胀比,吹胀比f可表示为
f=
…………………………………………
(2)
式中,
D---制品最大直径(mm);取D=120mm.
d---型坯直径(mm)。
吹胀比要选择适当,过大容易造成制品壁厚不均匀,根据经验,通常取吹胀比f=2~4。
取f=2则
d=
=
=60mm
型坯设计成圆管形状
一般要求型坯横截面形状与制品外形轮廓相似。
例如,若吹塑圆形横截面的瓶子,型坯应为圆管形状;若吹塑方桶,则型坯为方管形状.这样做的目的是使型坯各部位塑料的吹塑的吹胀比一直,从而使制品壁厚均匀。
另外,还要注意塑料的收缩率,对于尺寸精度要求不高的容器类塑料制品,成型收缩率对制品的影响不大;但对于有刻度的定量容器类和瓶口有螺纹的制品,要注意收缩率对制品精度的影响。
机头芯捧外径:
当吹胀比确定后,便可采用如下经验公式计算挤出机挤头的口模缝隙(成型机头口模与芯棒之间的间隙)。
b=ksf…………………………………………(3)
=1.25×1×2
=2.5mm
式中,
b---机头的口模缝隙(mm);
s---制品壁厚(mm),取s=1mm;
k---修正系数,一般取1.0~1.5,对与粘度大的塑料,k取小值。
取k=1.25
生产实践证明,用以上公式计算得到的机头、口模内径、芯棒外径挤出来的半熔坯管,经吹塑成型后,瓶口的纵向飞边少,有时基本上没有飞边,同时瓶底的切口线最短,强度最好。
5吹塑模具的型腔
5.1分型面选择
设计吹塑模具时首先要考虑的一个问题是分型面的选择,其位置由吹塑制品的形状确定。
对横截面为圆形的容器,分型面通过其直径设置;对椭圆形容器,分型面通过椭圆形的长轴;矩形容器的分型面可通过中心线或对角线,其中后者可减小吹胀比,但与分型面相对的拐角部位壁厚较小。
对某些制品,要设置多个分型面。
本塑件为椭圆形容器,分型面通过椭圆形的长轴。
如图5所示:
图5
5.2型腔表面处理
对许多吹塑制品的外表面都有一定的质量要求,有的要雕刻文字图案,有的要做成镜面、绒面、皮革纹面等,因此,要针对不同的要求对型腔表面采用不同的加工方式,如采用喷砂处理将型腔表面做成绒面,采用镀铬抛光处理将型腔表面做成镜面,采用电化学腐蚀处理将型腔表面做成皮革纹面等。
本塑件在外表面上雕刻图案以增强制品的刚度和强度
5.3型腔尺寸的计算
容器类的制件一般要求不严格,成型收缩率影响不大,但对有刻度的部分或螺纹处,收缩率就有相当的影响,体积越大影响也越显著。
各种塑料的吹塑成型收缩率见表3。
聚丙烯的收缩率取2%。
表3塑料吹塑成型时收缩率
塑料名称
收缩率(%)
塑料名称
收缩率(%)
聚缩醛及其共聚物
1~3
聚丙烯
1.2~2
尼龙6
0.5~2
聚碳酸酯
0.5~0.8
低密度聚乙烯
1.2~2
聚苯乙烯及其改性品
0.5~0.8
高密度聚乙烯
1.5~3.5
聚氯乙烯
0.6~0.8
D=〔d(1+S
)-△/2〕
D
=〔120(1+2%)-0.68/2〕
=(120×102%-0.34)
=122.06
D
=〔90(1+2%)-0.68/2〕
=(90×102%-0.34)
=91.46
式中
D——模具型腔尺寸;
d
——塑件高度方向尺寸,设计要求得到的产品尺寸;
d
——塑件短轴尺寸,设计要求得到的产品尺寸;
S
——材料收缩率的中间值,取S
=2%
△——塑件尺寸公差,一般取5~6级,△
、△
取0.68;
——模具型腔尺寸公差,一般取△/5
腹板结构如下图6所示:
图6腹板
为了防止腹板磨损,腹板中嵌入一背板,避免腹板与工件直接接触。
背板结构如下图7所示:
图7背板
6吹塑模具的颈部嵌块及底部嵌块设计
成型容器颈部的嵌块主要有模颈圈与剪切块,剪切块位于模颈圈之上,有助于切去颈部余料,减小模颈圈的磨损。
模颈圈与剪切块由工具钢制成。
如图8所示定径进气杆插入型坯内时,可把型坯挤入模颈圈的螺纹槽内形成实心的螺纹,进气杆端部则可成型容器颈部的内表面。
图8容器颈部的定径成型法
1.容器颈部2.模颈圈3.剪切块4.剪切套5.带齿旋转套筒6.定径进气杆7.颈部余料
本次矿泉水瓶螺纹镶块设计采用锥形结构,如下图9所示:
图9螺纹镶块
吹塑模具底部一般设置单独的嵌块,以挤压、封接型坯的一端,并切去尾料。
设计模底块时应主要考虑夹料口刃与尾料槽,它们对吹塑制品的成型与性能有重要影响。
因此,对它们有四方面要求。
(1)要有足够的强度、刚度与耐磨性,以在反复的合模过程中承受挤压型坯熔体产生的压力。
(2)夹料区的厚度一般比制品壁的大些,积聚的热量较多。
为此,夹料嵌块要选用导热性能高的材料来制造。
同时要考虑夹料嵌块的耐用性,铜铍合金是一种理想的材料。
当然,由钢制成的夹料嵌块使用寿命会更长,但导热性能较差。
对软质塑料,夹料嵌块一般可用铝做成,并与模体做成一体。
(3)接合缝通常是吹塑容器最薄弱的部位,故要在合模后但未切断尾料前把少量熔体挤入接合缝,以适当增加其厚度与