电转炉汽化烟道与汽包系统工艺管道方案.docx
《电转炉汽化烟道与汽包系统工艺管道方案.docx》由会员分享,可在线阅读,更多相关《电转炉汽化烟道与汽包系统工艺管道方案.docx(43页珍藏版)》请在冰豆网上搜索。
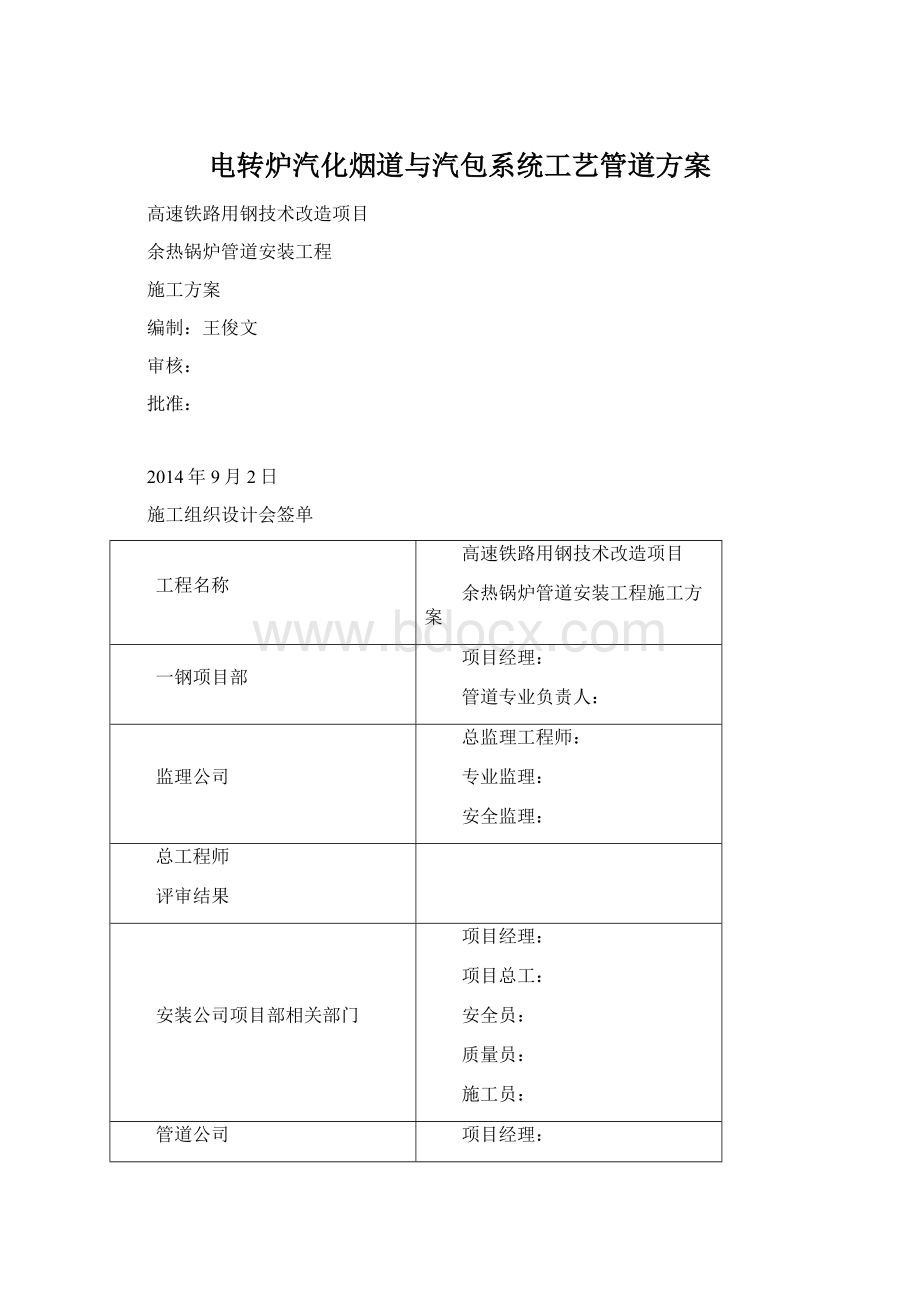
电转炉汽化烟道与汽包系统工艺管道方案
高速铁路用钢技术改造项目
余热锅炉管道安装工程
施工方案
编制:
王俊文
审核:
批准:
2014年9月2日
施工组织设计会签单
工程名称
高速铁路用钢技术改造项目
余热锅炉管道安装工程施工方案
一钢项目部
项目经理:
管道专业负责人:
监理公司
总监理工程师:
专业监理:
安全监理:
总工程师
评审结果
安装公司项目部相关部门
项目经理:
项目总工:
安全员:
质量员:
施工员:
管道公司
相关部门会签
项目经理:
项目副经理:
技术员:
安全员:
质量员:
施工员:
一、工程概况
本工程管道具有工程量大,温度高、压力高、工期紧等特点,需精心组织,严细策划。
1.工艺管道分8大系统
序号
简称
图号
1
蒸汽管道
010.16A104A21R-TE003
2
排汽管道
010.16A104A21R-TE005
3
给水、给水再循环及除盐水管道
010.16A104A21R-TE004
4
杂项管道
010.16A104A21R-TE007
5
蒸汽蓄热器设施设备及管道
010.16A119A01R-TE001
6
高、低压强制循环水管道
010.16A104A21DR-1487
7
高压自然循环水管道
010.16A104A21DR-1488
8
排污管道
010.16A104A21R-TE006
2.工程量:
共计管道10800延米,重量达291吨,阀门680个,各类管件2075个,管托及支吊架618个。
其中DN>=200管道2389m,193.9吨,约占总米数的1/4,约占总重量的2/3.
3.主要工作介质:
饱和蒸汽和汽水混合物
4.工作温度:
最高为271℃
5.工作压力:
高压强制循环水为5.6MPa,高压自然循环水为5.15MPa,主蒸汽为4.0MPa。
6.试验压力:
高压强制循环水为9.18MPa,高压自然循环水为8.2MPa,主蒸汽为8.19MPa。
7.按材质划分为3类:
(1)20G约220吨;占总量的75%。
(2)20#约60吨;占总量的20%。
(3)06Cr19Ni10约10吨;占总量的5%。
8.按介质类别划分为以下22项,见下表。
序号
管道名称
介质名称
工作参数
设计参数
耐压试验
压力管道等级
温度℃
压力Mpa
温度℃
压力Mpa
试压介质
压力Mpa
1
低压强制循环水
热水
224
2.5
224
2.6
清洁水
3.97
GC2
2
高压强制循环水
热水
271
5.6
271
5.7
清洁水
9.18
GC2
3
高压自然循环水
热水
250
5.15
259
5.2
清洁水
8.2
GC2
4
给水
热水
259
4.5
259
5.2
清洁水
7.8
GC2
5
给水再循环
热水
120
0.4
120
0.5
清洁水
0.75
GC3
6
除盐水
除盐水
20
0.6
50
0.6
清洁水
0.9
7
排污管道
热水
250
4
259
4.5
清洁水
8.19
GC2
8
排汽管道
蒸汽
250
1.6
259
1.9
清洁水
3.46
GC2
9
主蒸汽
蒸汽
252
4
259
4.5
清洁水
8.19
GC2
10
自用蒸汽
蒸汽
250
1.6
260
1.9
清洁水
3.46
GC2
11
主蒸汽排汽
蒸汽
250
4
259
4.6
清洁水
7.46
GC2
12
定期排污扩容器排汽
蒸汽
250
0.4
259
0.5
清洁水
0.89
GC2
13
循环水管道蒸汽
蒸汽
120
1.9
120
2
清洁水
2.72
GC2
14
除氧器排汽
蒸汽
250
5.9
259
6
清洁水
9.23
GC2
15
除氧器安全放水、排污管道
热水
159
0.6
159
0.7
清洁水
1.05
GC3
16
汽包安全放水、排污管道
热水
250
4.77
259
4.9
清洁水
7.63
GC2
17
定排冷却水及冷凝水管道
常温水
35
0.5
35
0.5
清洁水
0.9
18
加药管道
氨溶液
159
0.7
159
0.8
清洁水
1.2
19
加药管道
磷酸盐溶液
250
5.05
259
5.1
清洁水
8.05
20
加药、取样管道
热水
250
5.05
259
5.1
清洁水
8.05
21
加药装置补水管道
除盐水
常温
0.6
50
0.6
清洁水
0.9
22
工业冷却水
冷却水
常温
0.6
50
0.6
清洁水
0.9
9.必须按压力管道质量体系文件进行施工
压力管道施工过程的监管要求严格,施工过程中要严格按照技术规定进行施工,施工保证环节多。
为确保施工质量,必须严格压力管道施工验收规范规定进行施工,施工过程中严格按规范进行检查。
二、工程实物量:
一
高、低压强制循环水管道010.16A104A21DR1487
序号
部位
管道规格
材质
管道(m)
管道(Kg)
1
低压循环水管道
DN25~DN200
20#
561
13973.98
2
高压循环水管道
DN25~DN450
20G
1474
105051.3
2035
119025.28
二
高压自然循环水管道010.16A104A21DR1488
序号
部位
管道规格
材质
管道(m)
管道(Kg)
1
垂直烟道下降管
φ73*5--φ273*14.2
20G
163
10828
2
垂直烟道上升管
φ73*5--φ114.3*6.3
20G
1016
9488
3
蒸发器支撑梁下降管
φ168.3*11
20G
140
5973
4
蒸发器支撑梁上升管
φ114.3*6.3
20G
53
889
5
水冷壁循环水下降管
5.1
φ323.9*16
20G
125
15186
5.2
φ73*5
20G
175
1466
5.3
φ219.1*12.5
20G
22
1400
6
水冷壁循环水上升管
6.1
φ73*5
20G
230
1927
6.2
φ73*5
20G
450
3771
6.3
φ73*5
20G
230
1927
7
余热锅炉蒸发器循环水下降管
φ219.1*12.5
20G
120
7639
8
余热锅炉蒸发器循环水上升管
φ114.3*6.3
20G
150
2517
9
垂直烟道内部循环水上升管
φ114.3*10
20G
150
3858
3024
66869
三
给水、给水再循环及除盐水管道010.16A104A21R-TE004
序号
部位
管道规格
材质
管道(m)
管道(Kg)
1
给水管道
φ21.3*2--φ168*4.5
20#或20G
240
5338
2
给水再循环管道
φ60.3*4
20#
48
266
3
除盐水管道
φ88.9*4~219.1*4
06Cr19Ni10
74
986
4
放气管道
φ33.7*4
20#
20
38.4
382
6628.4
四
排汽管道010.16A104A21R-TE005
序号
部位
管道规格
材质
管道(m)
管道(Kg)
1
定期排污扩容器排汽管道
φ26.7*2.5--φ457*5
20#
145
6484
2
除氧器排汽管道
φ60.3*4.5--φ219.1*6.3
20#
175
5207
φ26.7*2.5-323.9*7.1
170
6190
3
主蒸汽管道排汽管道
φ26.7*2.5-323.9*16
175
11487
4
循环水管道排汽
φ60.3*4.5-168.3*6.3
880
9040
1545
38408
五
杂项管道010.16A104A21R-TE007
序号
部位
管道规格
材质
管道(m)
管道(Kg)
1
工业冷却水管道
φ33.7*3.5--φ21.3*2.8
06Cr19Ni10或20#
502
4651
2
加药取样管道
φ33.7*3.5--φ144.3*6.3
06Cr19Ni10
140
537
3
加药装置补水管道
φ33.7*3.5-48.3*4
06Cr19Ni10
100
378
742
5566
六
蒸汽管道010.16A104A21R-TE003
序号
部位
管道规格
材质
管道(m)
管道(Kg)
1
主蒸汽管道
φ33.7*4--φ273*16
20G
177.5
10697
2
自用蒸汽管道
φ33.7*2.5--φ273*7
20#
675.5
8199
853
18896
七
蒸汽蓄热器管道010.16A119A01R-TE001
序号
部位
管道规格
材质
管道(m)
管道(Kg)
1
蒸汽管道
φ88.9*5.5--φ355.6*10
20G或20#
417
23546
2
给水管道
φ88.9*6.3
20G
120
1539
3
加药装置补水管道
φ60.3*5-73*5
20G
80
661
4
排汽管道
φ219.1*7--φ323.9*8.5
20#
47
3129
5
疏放水、放气管道
φ21.3*2.8--φ60.3*5
20#
570
926
1234
29801
八
排污管道010.16A104A21R-TE006
序号
部位
管道规格
材质
管道(m)
管道(Kg)
1
汽包安全放水管道、排污管道
φ42.4*4--φ88.9*4.5
20#或20G
200
1308
2
除氧器安全放水管道、排污管道
φ60.3*6.3--φ88.9*8
20#
50
601
3
各管道低点排污管道D1~D12
φ33.7*4.0-88.9*6.3
20G
647
2629
4
定排冷却水管道及冷凝水管道
φ21.3*5-114.3*6.3
20#
92.5
1326
989.5
5864
汇总
10804.5
291057.68
其中:
20#钢约60吨
20G材质约220吨
06Cr19Ni10材质约10吨
三、施工准备:
1、施工前施工技术人员应熟悉施工图纸,了解施工中的重点难点。
2、安装前必须进行图纸自审,并向施工人员进行技术交底,做好交底记录。
3、施工验收规范和验评标准
1)、设备制造说明和图纸说明
2)、《蒸汽锅炉安全技术监察规程》
3)、《压力容器安全技术监察规程》
4)、《工业金属管道工程施工及验收规范》GB50235—2010
5)、《现场设备、工业管道焊接工程施工及验收规范》GB50236—2011
6)、《工业锅炉安装工程施工及验收规范》GB50273—2011
7)、《工业金属管道工程检验评定标准》GB50184—2010
8)、设备和阀门厂提供的技术规定及安装使用说明书
四、施工方案
(一)工艺管道安装一般要求
1、管道系统施工流程图
2、管道进场检查:
到货钢管的生产标准及质量证明书上的规格、材质和精度等级必须与设计要求相符;管内外表面不得有裂纹、折叠、离层、结疤、氧化铁皮、锈蚀缺陷存在,管壁锈蚀、划道、刮伤深度总和不应超过标准规定的壁厚负偏差,内壁应光滑、清洁、无明显锈蚀。
3、管道除锈、刷底漆:
(1)施工程序(见流程图)
(2)管道表面处理
a.采用喷砂除锈达到Sa2.5级,即管子、管件表面不得有伤痕、气孔、夹渣、重叠皮、严重腐蚀斑点;加工表面必须平整,表面局部凸凹不得超过2mm;
b.管子、管件表面的锐角、棱角、毛边、铸造残留物,应彻底打磨清理,表面应光滑平整,圆弧过渡;
经处理后的金属表面,应及时涂刷底涂料。
(3)涂层施工
a.涂料的选用和涂层的层数、厚度应按设计要求;
b.当使用同一涂料进行多层涂刷时,宜采用同一品种不同颜色的涂料调配成不同的涂料,以防止漏涂;
c.为节约施工用周期,在除锈完毕后进行。
涂涮时应将全部焊缝预留,并将焊缝两侧的涂层作成阶梯状接头,待试验合格后,按涂层要求补涂。
涂装底漆时,管道接口处留出80-100mm的管道在焊接后进行补刷。
d.涂料应临用前按比例混合并搅拌均匀后使用,且应在规定时间内用完。
涂料如有结皮或其他杂物,必须清除后方可使用。
涂料开桶后,必须密封保存。
e.刷涂、滚涂、喷涂均应均匀,不得漏涂;面层应顺介质流向涂刷。
表面应平滑无痕,颜色一致,无针孔、气泡、流坠、粉化和破损等现象。
4、管道支架预制安装
a.支吊架最大跨距按表2确定,弯管处跨距其展开长度不大于直管的2/3,制作时支吊架之间,支架型钢与生根结构之间均采用连续焊接。
表2:
管道支架间距确定表
管径DN(mm)
15
20
25
32
40
50
65
80
100
125
最大跨距(m)
2.5
3
3.5
4
4.5
5
6
6
6.5
7
管径DN(mm)
150
200
250
300
最大跨距(m)
8
9
10
10
b.对于管子的外壁、法兰边缘、保温层外壁等管道最突出部分距离墙壁或柱边的距离应不小于100mm。
c.管道支吊架施工完毕后应清除表面污锈,刷防锈漆2遍,再刷灰色面漆2遍。
d.所有支架可根据现场实际情况安装,焊条采用E4303电焊条,焊角高度为5mm。
5、管道安装
(1)管道安装要保证横平竖直,并且符合《工业金属管道工程施工及验收规范》GB50235-2010,管道焊接应按GB50236-2011《现场设备,工业金属管道焊接施工及验收规范》的有关规定。
(2)管道安装完毕后,应按GB50235-2010《工业金属管道工程施工及验收规范》的要求进行管道系统的试压,吹扫及阀门气密性试验,试验压力为按施工说明执行。
(3)管道的坡度应按图纸的要求进行调整,调整方法可以利用支座达到坡度要求,焊缝应设置在便于检修、观察的地方。
(4)与传动设备连接的管道,安装前内部要处理干净,焊接固定管口一般应远离设备,以避免焊接产生应力对传动设备安装精度的影响。
(5)管道与机器连接前,应防止强力相对,在自由状态下检查法兰的平行度和同轴度。
(6)管道除法兰连接外,其余均采用焊接,焊条为E4315焊条,焊缝高度为最薄焊件厚度。
(7)管道除锈后进行保温和刷色,见保温专册Z193热5。
(8)现场管装管道碰撞,可根据具体情况协调变动。
管道阀门等未给出安装标高的,可根据现场具体情况,安装在便于人员操作处。
(9)管道安装的质量控制措施:
a.管道布置应遵循横平竖直的基本原则。
b.管道敷设位置应便于装拆、检修、且不妨碍生产人员的操作、行走,以及机电设备的运转、维护和检修。
c.管子外壁与相临管道之管件边缘的距离应不小于10mm。
d.同排管道的法兰或活接头应相间错开100mm以上。
6、管道焊接
(1)坡口加工及接头组对。
管道接口位置应符合下列要求:
a.管子接口与支吊架边缘之间不得小于50mm。
b.管子接口应避开仪表的开孔位置,一般距开孔的边缘不得小于50mm,且不得小于孔径。
(2)管子、管件的对口应做道内壁平齐:
焊缝的对口,内壁错边量应不超过管壁厚度的20%,且不大于2mm。
(3)确保焊接质量的工艺措施
a.焊工应按有关规定进行考试,取得合格证书。
b.焊接材料应具有制造厂的合格证明书,焊条,焊剂在使用前按产品说明书的规定烘干,并在使用过程中保持干燥,焊条药皮应无脱落和显著裂纹,焊丝使用前应清除表面油污和锈蚀。
c.施焊前应对坡口及附近宽20mm范围内外管壁进行清理,清除其上的油、水、漆、锈及毛刺等,露出金属光泽。
d.管道点固焊时,点固焊的工艺措施及焊接材料应与正式焊接一致,点固焊后应认真检查焊肉,如发现有裂纹等缺陷,应及时处理。
e.焊接完毕,应将焊缝表面熔渣及两侧飞溅清理干净,并作好记录。
(4)焊接方法的选择:
碳钢管当管径比较大时可采用手工电弧焊焊接,内口进行清理后封底焊;对于管径比较小的碳钢管,采用氩电联焊的方法进行;镀锌管采用丝接。
(5)焊接材料选用:
1)对于管道材质为20#的无缝钢管焊条采用E4303型,氩弧焊丝TIG-J50型。
2)对于管道材质为20G的无缝钢管焊条采用J427型,焊丝采用H08Mn2SiA,φ2.5。
3)对于管道材质为06Cr19Ni10的不锈钢无缝钢管焊条采用钛钙型A102或低氢型A107焊条,氩弧焊丝H0Cr20Ni10型。
(6)管道焊缝应进行抽样射线探伤,比例不得小于10%,其质量不得低于Ⅲ级,或超声波探伤,其质量不得低于Ⅱ级,与炉底相接管子焊缝应全部进行射线探伤,厚壁的炉底管应加工或不大0.25坡度的坡口,过渡到与相接管子一致的管径和壁厚后,再进行焊接,焊接前注意除去管内的杂物。
7、阀门的安装
(1)安装前应进行压力试验,试验不合格的阀门应根据业主代表的意见退货或进行研磨,无法单独试验的阀门可以在管道系统中进行试验,但须做好标记;
(2)安装前应对阀门的外观、型号规格进行检查,并按设计文件和相关标准、范的规定进行强度试验和严密性试验;
(3)阀门搬运时不允许随手抛掷,应分门别类地进行摆放;
(4)大型阀门吊装搬运时,钢丝绳不得栓在手轮或阀杆上,应栓在法兰处;
(5)铸铁阀门阀件安装时,需防止强力连接或受力不均而引起的损坏;
(6)阀门介质流向要和阀门壳体上的箭头或标记的指示方向相同,介质流过截止阀的方向是由下向上流经阀盘;
(7)安全阀应垂直安装,在投入试运行时,要及时调校安全阀。
安全阀的最终调校在系统上进行,开启和回座压力要符合设计文件的规定。
(8)阀门安装前,按设计文件核对其型号,并按介质流向确定其安装方向。
当阀门与管道以法兰或螺纹方式连接时,阀门应在关闭状态下安装;如以焊接方式安装时,阀门不得关闭。
(9)仪表元件的临时替代:
所有仪表元件安装时,均采用临时元件替代,等试压、冲洗、吹扫工作结束后,投料前再正式安装。
8、法兰的安装
(1)法兰与管子组装应用弯尺对管子端面检查,管口端面倾斜尺寸不能大于1.5mm;
(2)法兰与管子组装时,要用法兰弯尺检查法兰的垂直度,法兰连接的平行度偏差尺寸当设计无明确规定时,则不应大于法兰外径1.5/1000,且不应大于2mm;
(3)法兰与法兰连接时,密封面应保持平行,法兰密封面的平行度允差见下表3
(4)为了便于装、拆法兰,紧固螺栓,法兰平面距支架和墙面的距离应大于或等于20cm;
(5)为了保障垫片各处均匀受力,拧紧螺栓时应对称成十字式交叉进行,拧紧露出丝扣的长度不应大于螺栓直径的一半,也不应少于两扣。
表3:
法兰平行度允差
公称通径
在下列公称压力下的允许偏差(mm)
<1.6Mpa
=1.6-4MPa
≤100
0.20
0.10
>100
0.30
0.15
9、管道冲冼、试压
(1)管道冲冼、试压程序(见流程图)
(2)压力试验前,应具备下列条件:
a.试验范围内的管道安装工程除涂漆外,已按设计图纸全部完成,安装质量符合有关规定。
b.焊缝和其它待检部位尚未涂漆。
c.管道上的膨胀节已设置了临时约束装置。
d.试验用压力表已经校验,并在周期内,其精度不得低于1.5级,表的满刻度值应为被测最大压力的1.5-2倍,压力表不得少于两块。
e.符合压力试验要求的液体或气体已备齐。
f.按试验要求,管道已经加固。
g.待试管道与无关系统已用盲板或采取其它措施隔开。
h.待试管道上的安全阀及仪表元件等已经拆下或加以隔离。
i.试验方案已经批准,并进行了技术交底。
(3)压力试验
a.试验介质,可采用水压进行试压,压力试验时,无关人员不得进入。
b.试验前,应将不能参与试验的系统、设备、仪表等加以隔离,安全阀应拆卸,加设盲板的部分应作出明显的标记和记录;
c.管道增压时,升压应缓慢,加压到一定数值时,应进行检查,无异常时再继续升压;
d.加压逐级升高,升压的次数和压力应视压力的高低而定,每一级可稳压5-10分钟,无问题方可继续升压,直至升到试验压力;
e.耐压试验合格后,降至设计压力,进行检查,如无泄漏,稳压半小时,压力不降,则严密性试验为合格;
10、管道系统的吹扫
为保证管道系统内部清洁,在试压合格后,投产前应全面将管路内部用水冲洗或用空气冲洗,蒸气冲洗.用水冲洗时,水流速度不得小于1-1.5m/sec直到管内排出清水为止.用压缩空气吹扫时,管内最小流速度不得小于20m/sec,用蒸汽吹扫时,管内最小流速度不得小于30m/sec,当吹出气流无铁锈时,脏物,油污时则以为合格.
(二)重点部位方案
1、不锈钢管的施工方案:
不锈钢管道焊接采用氩电联焊形式,小口径管道直接用氩弧焊完成,焊缝进行100%射线探伤检测。
本系统不锈钢管件使用量非常大,阀门数量多,施工中管道焊缝量大,焊接质量要求高,使施工难度加大,人力、物力投入非常大,基本使用人工组对安装,机械使用率低。
不锈钢管道安装应注意以下要点:
(1)安装前应对管子、阀件进行认真清洗、检查,以免由于牌号或化学成分与设计要求不符造成返工,如设计有特殊要求,需按要求处理。
(2)不锈钢管一般不宜直接与碳素钢管件焊接,当设计要求焊接时,必须采用异种焊条或不锈钢焊条。
(3)不锈钢管与碳钢制品接触处应衬垫不含氯离子橡胶、塑料、红柏纸或在钢法兰接触面涂以绝缘漆。
因为不锈钢管直接与碳钢支架接触或当采用钢活套法兰连接时,碳钢制品腐蚀后铁锈与不锈钢管表面长期接触,会发生分子扩散,使不锈钢管道受到腐蚀。
(4)不锈钢管道应尽量减少法兰个数。
为了安全,法兰不得设在主要出入口及门