江苏科技大学.docx
《江苏科技大学.docx》由会员分享,可在线阅读,更多相关《江苏科技大学.docx(21页珍藏版)》请在冰豆网上搜索。
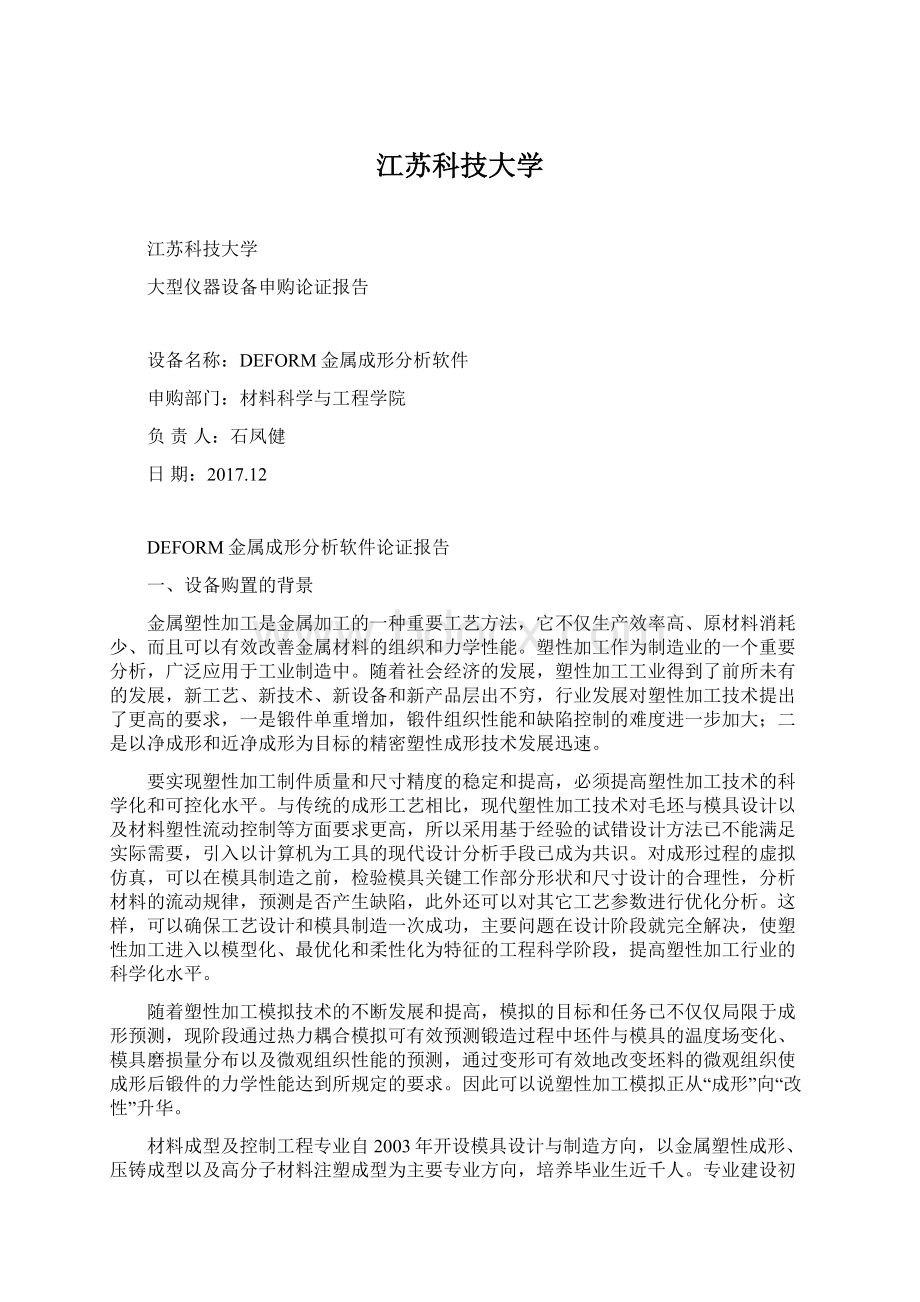
江苏科技大学
江苏科技大学
大型仪器设备申购论证报告
设备名称:
DEFORM金属成形分析软件
申购部门:
材料科学与工程学院
负责人:
石凤健
日期:
2017.12
DEFORM金属成形分析软件论证报告
一、设备购置的背景
金属塑性加工是金属加工的一种重要工艺方法,它不仅生产效率高、原材料消耗少、而且可以有效改善金属材料的组织和力学性能。
塑性加工作为制造业的一个重要分析,广泛应用于工业制造中。
随着社会经济的发展,塑性加工工业得到了前所未有的发展,新工艺、新技术、新设备和新产品层出不穷,行业发展对塑性加工技术提出了更高的要求,一是锻件单重增加,锻件组织性能和缺陷控制的难度进一步加大;二是以净成形和近净成形为目标的精密塑性成形技术发展迅速。
要实现塑性加工制件质量和尺寸精度的稳定和提高,必须提高塑性加工技术的科学化和可控化水平。
与传统的成形工艺相比,现代塑性加工技术对毛坯与模具设计以及材料塑性流动控制等方面要求更高,所以采用基于经验的试错设计方法已不能满足实际需要,引入以计算机为工具的现代设计分析手段已成为共识。
对成形过程的虚拟仿真,可以在模具制造之前,检验模具关键工作部分形状和尺寸设计的合理性,分析材料的流动规律,预测是否产生缺陷,此外还可以对其它工艺参数进行优化分析。
这样,可以确保工艺设计和模具制造一次成功,主要问题在设计阶段就完全解决,使塑性加工进入以模型化、最优化和柔性化为特征的工程科学阶段,提高塑性加工行业的科学化水平。
随着塑性加工模拟技术的不断发展和提高,模拟的目标和任务已不仅仅局限于成形预测,现阶段通过热力耦合模拟可有效预测锻造过程中坯件与模具的温度场变化、模具磨损量分布以及微观组织性能的预测,通过变形可有效地改变坯料的微观组织使成形后锻件的力学性能达到所规定的要求。
因此可以说塑性加工模拟正从“成形”向“改性”升华。
材料成型及控制工程专业自2003年开设模具设计与制造方向,以金属塑性成形、压铸成型以及高分子材料注塑成型为主要专业方向,培养毕业生近千人。
专业建设初期,学校投入专业建设经费进行了一定的硬件条件建设,在人才培养和科研方面发挥了积极作用。
但CAD、CAE软件作为本专业的重要工具已成为毕业生的必备技能,同时也是本专业教师开始教学与科研的重要工具,因此,急需购置一套塑性成形分析软件。
二、设备购置的意义和必要性
1.意义
DEFORM金属成形分析软件在金属塑性成形尤其是材料体积成形领域具有重要地位,作为智能制造、虚拟制造的一部分,在企业生产中应用越来越普遍。
该软件的购置作为材料学院虚拟仿真实验中心建设项目的重要部分,将为材料成型及控制工程专业本科课程教学(主流CAE软件概论、CAD/CAE软件应用训练)、毕业设计、本科生创新计划以及硕士、博士研究生课题开展提供条件。
该软件的购置也将为教师开展金属成形过程仿真、成形工艺优化、微观组织性能预测、多场耦合模拟仿真、热处理过程模拟、摩擦焊等相关科研提供工具,拓宽教师科研领域,提高教师科研水平和竞争力,凸显学科特色。
该软件还可为教师承担企业课题、加强校企合作提供平台。
2.必要性
(1)企业发展对人才的需要
金属成形是一个较为复杂的过程,尤其对于一些形状复杂或者成形难度大的材料尤其如此,传统的试错法周期长、成本高,已不能满足当前企业生产的需要,金属成形工艺以及工模具设计逐步由经验走向科学。
CAE分析已成为成形工艺制定、模具设计、生产指导的必备环节。
作为制造业大国,我国对于金属成形CAE分析人才需求量较大。
(2)本科教学需要
鉴于上述发展趋势,我校材料成型及控制工程专业自2008级本科人才培养方案便开设了“主流CAE软件概论”选修课,主要让学生了解材料成形数值模拟基础知识及软件,但当前软件条件不能满足教学的需要。
(3)虚拟仿真实验中心建设需要
随着虚拟现实技术的成熟,虚拟仿真实验室在教育领域越来越受到重视。
通过将虚拟现实技术与国内外典型的CAE有限元分析软件对接,能够对学生的自主设计方案进行分析与验证,给出真实、专业、针对性的反馈,实现设计的优化,有效提升学生能力。
(4)教师科研需要
材料成形过程仿真及工艺优化是材料学院尤其是材料成型及控制工程专业教师的主要科研方向之一,也是拟培育专业特色。
该软件作为重要的工具可为教师在材料成形新工艺、新技术开发、新材料成形工艺制定、模具设计、高端零件成形成性控制、多场耦合宏微观仿真等方面提供平台。
三、可行性分析
1.前期工作基础
金属塑性成形是材料成型及控制工程专业的主干方向之一,材料成形过程仿真作为金属塑性成形分析的重要手段一直受到专业的重视,在本科人才培养方案中开设了相关课程,专业教师在毕业设计、本科生创新计划、研究生培养方面以及教师科研等方面开展了多个材料成形新工艺、新技术的成形过程分析、模具设计优化以及微观组织预测等研究工作,因此,从教学以及科研的角度都急需购置金属成形分析软件以辅助教学与科研工作。
2.国内外相关研究进展
金属塑性成形向着大型、精密、优质、柔性、智能化等方向发展,金属塑性成形过程仿真随着计算机技术与材料成形新技术的发展而快速发展。
金属塑性成形模拟技术从上个世纪七八十年代开始已经在全球范围内得以应用,以DEFORM为主的计算机模拟软件在进入中国后得到了各制造领域、科研院所的逐步引入及应用,随着工艺制造水平的进一步提高,塑性成形模拟软件也得到了长足的发展,从最初的模锻模拟,到随后的自由锻、轧制、切削,再到热处理、组织计算等,随着工业技术的进步而不断发展完善。
国外的大多数著名制造企业如GE、GM、honeywell等都早就使用了模拟软件用于加工制造。
国内也具有大量的企业用户,涵盖军工、航空航天、车辆、汽车零部件、钢铁冶金等领域,这些企业通过使用塑性模拟软件缩短了研发周期、降低了生成实验成本、提高了产品质量及经济效益,并在技术水平的提升上取得了不错的成绩。
国内的绝大部分工科院校的材料加工专业、机械及机电专业都使用了DEFORM作为课题的研究开发、课程教学及与企业合作的产学研的项目的研究,取得了多项学术专利。
至今,国内已经有大量著名高校及企业在使用塑性成形软件,包括:
北京机电研究所北京科技大学高效轧制研究中心
内蒙古第一机械集团公司有色金属研究院研究生院
一汽技术中心燕山大学
安特精密仪器沈阳工业大学材料工程学院
太平洋精密锻造大连理工大学材料工程学院
黑龙江北方模具哈尔滨工程大学机电工程学院
中国船舶工业集团公司重庆重型锻压厂上海大学
长安汽车西南交通大学应用力学系
东风汽车中国工程物理研究院
西安航空发动机(集团)股份有限公司华中科技大学塑性成形国家重点实验室
中国船舶重工集团公司第12研究所中南大学材料科学与工程系
日星金属制品(上海)有限公司西安交通大学机械工程学院
武汉钢铁(集团)公司科技创新部西北工业大学
宝山钢铁股份有限公司太原理工大学材料科学与工程学院
攀枝花钢铁研究院西安航空职业技术学院
可胜科技(苏州)有限公司上海交通大学
东风粉末冶金厂南京工程学院
纳铁福传动轴中南大学粉末冶金学院
文登天润曲轴太原科技大学
邢台中钢轧辊河北理工大学冶金与能源学院
蚌埠40电子研究所长春理工大学
浙江工业大学机电工程学院化机所东华大学
中国科学院金属研究所南昌航空工业学院
上海汇众汽车……
四、性能参数和设备选型
1.主要技术参数及配置
本次采购软件应具备如下配置:
●2D/3D锻造模块
✓冷、温、热锻的成形和热-力耦合分析。
✓丰富的材料数据库,包括各种钢、铝合金、钛合金和高温合金。
✓用户自定义材料数据库允许用户自行输入材料数据库中没有的材料。
✓提供材料流动、模具充填、成形载荷、模具应力、纤维流向、缺陷形成和韧性破裂等信息。
✓刚性、弹性和热粘塑性材料模型,特别适用于大变形成形分析。
✓弹塑性材料模型适用于分析残余应力和回弹问题。
✓多孔材料模型适用于分析粉末材料压实、锻造及烧结分析。
✓完整的成形设备模型可以分析液压成形、锤上成形、螺旋压力成形和机械压力成形。
✓用户自定义子函数允许用户定义自己的材料模型、压力模型、破裂准则和其他函数。
✓可准确预测折叠、充型不足、裂纹、飞边等缺陷,材料变形流线与实际物理结果保持一致。
✓流线和质点跟踪可以分析材料内部的流动信息及各种场量分布。
✓温度、应变、应力、损伤及其他场变量等值线的绘制使后处理信息更加丰富。
✓自动接触条件及完美的网格再划分使得在成形过程中即便形成了缺陷,模拟也可以进行到底。
✓多变形体模型允许分析一模多件或耦合分析模具应力。
✓磨损分析模型用于评估成形过程中模具磨损情况。
✓预成形设计模块为复杂锻件的多步模具设计提供指导。
✓基于损伤因子的裂纹萌生及扩展模型可以分析剪切、冲裁和机加工过程。
✓模具应力分析功能用于分析组合模具及多衬套挤压模具在成形过程中的变形和损伤。
✓完善的热边界条件可以分析热成形中材料与环境间的热交换。
✓恒定热流及热源功能用来分析保温模具加热部件的分布位置和焊接的温度场。
✓提供依据模具运动时间、载荷力、成形温度、闭模间隙等精确成形行程控制准则。
✓可计算热锻过程中由于空气或润滑剂高温蒸发所造成的材料填充不满缺陷。
✓实现薄板、厚板的冲压工艺分析,根据厚度云图预测冲压失稳、起皱、减薄率等缺陷。
✓可将计算结果数据传递到ansys软件,包括残余应力、单元、成形形状、应变,进行成形-结构-疲劳的连续性分析。
●Extruction型材挤压模块
✓高级ALE(ArbitraryLagrangianEulerian)及S-S(Steady-state)稳态算法适合复杂非对称截面型材挤压成形过程。
✓具有向导式操作界面,自动产生型材或挤型模具,实现挤型设置过程的流程化管理,操作简便。
✓增量算法可模拟挤压过程材料分流及在焊合过程。
✓增量算法可实现型材挤压成形的裂纹、扭拧、波浪及弯曲等缺陷。
✓优秀的单元重划及节点粘接接触能力可模拟焊合过程中焊接面的形成。
✓ALE稳态算法可在很少的时间步内收敛,快速获得流速、温度等场变量。
✓增量算法与稳态算法相结合可高效模拟从棒料挤压-分流-焊合-挤出稳定端面的整个过程。
能够采用ALE算法快速预测型材变形、焊缝位置、焊合情况等。
✓分析挤压过程中再结晶现象及微观组织结构的变化。
●HT2/HT3热处理模块
✓模拟的热处理工艺类型:
正火、退火、淬火、回火、时效处理、渗碳、蠕变、高温处理、相变、金属晶粒重构、硬化和时效沉积等。
✓精确预测硬度、金相组织体积比值(如马氏体、残余奥氏体含量百分比等)、热处理工艺引起的挠曲和扭转变形、残余应力、碳势和含碳量等热处理工艺评价参数,得到热处理变形和碳含量分布。
✓专门的材料模型用于蠕变、相变、硬度和扩散。
✓可以输入淬火数据来预测最终产品的硬度分布。
✓可以分析各种材料金相,每种金相都有自己的弹性、塑性、热和硬度属性。
✓混合材料的特性取决于热处理模拟中每一步的各种金属相的百分比。
✓反向热处理辅助确定工件和热处理介质之间的界面换热系数。
✓具有FEM电感应加热及BEM电感应淬火等表面热处理分析功能,支持单频、双频感应电流。
✓可实现热处理工艺表制定、热处理介质设定、局部热处理等方式的设置。
✓通过材料合金成分配比及晶粒尺寸计算钢的热处理参数,包括TTT转变曲线、组织相性能(奥氏体、马氏体、珠光体、贝氏体等)。
●Microstructure微观组织模块
✓模拟微观组织在金属成形过程、热处理过程及加热、冷却过程中的演变。
✓可导入EBSD实验微观相图作为初始晶粒分布,准确计算晶粒演变过程。
✓模拟晶粒生长,分析整个过程的晶粒尺寸变化。
✓计算成形及热处理过程中的回复再结晶现象,包括动态再结晶、中间动态再结晶及静态再结晶。
✓模拟晶粒织构变化过程。
✓具有多种组织计算模型,包含典型的JAMK方程。
✓用户可二次开发自己的晶粒演变模型用于微观组织计算。
✓具有元胞自动机法、蒙特卡洛法及相区法计算方法,可现实微观组织相图、晶粒尺寸、晶界及晶向,实现微观组织演变的可视化观测,可获得晶粒尺寸、偏差角、晶粒尺寸比等数据。
✓可通过显式算法计算金属断裂过程的微观孔洞的形成及组织裂纹。
●Machinig切削过程模块
✓模拟车、铣、刨及钻孔等机械加工过程;
✓模拟切削过程工件温度、变形及切屑产生;
✓预测切削刀具的受力、温度变化;
✓评估刀具的磨损情况;
✓模拟切削过程中工件发生的热处理相变;
✓可以分析各种材料金相,每种金相都有自己的弹性、塑性、热和硬度属性;
✓混合材料的特性取决于热处理模拟中每一步的各种金属相的百分比;
●Cogging自由锻/旋揉成形模块
✓具有流程式的操作模板,可操作性强;
✓具有自由锻工模具模型自定义方式,方便使用;
✓可进行旋揉(径向锻造)成形的工艺分析,具备专业的旋揉成形设置流程;
✓可任意进行咬合、加热、锻打工序的多工步设置;
✓可分析成形过程金属流动、缺陷产生、工件形状、晶粒细化及优化工艺设计;
✓优化锻打次数、锻造比、拔长效率、加热温度、平砧结构等参数;
✓预测自由锻形状尺寸、折叠、表面裂纹、扭曲等成形缺陷;
✓具有锻锤设备库及多工步自由锤锻设置方式;
●Ringrolling环材轧制模块
✓具有专用环轧模板,操作方式流程化;
✓具有环件模型及模具模型自动产生方式;
✓复杂及多数量模具可实现准确自动定位;
✓可完全采用全六面体网格及重划分技术,保证模拟结果的高精度;
✓同时进行轧制及温度的耦合分析;
✓可任意设置模具旋转运动方式,实现多步轧制;
✓可进行环轧变形过程模拟、模具应力及磨损分析;
✓预测环轧过程中出现的折叠、凹坑、蝶形、壁厚不均、压扁、椭圆、锥度等成形缺陷;
●Shaperolling型材轧制模块
✓具有专用轧钢模板,操作方式流程化,简单易学;可用于板材、型材、线材、管材、减径机组等的轧制分析;
✓具有钢坯模型及轧具模型自动产生方式;复杂及多数量轧具可实现准确自动定位;
✓可采用ALE法、UL法及2.5D法计算轧制过程;
✓可完全采用全六面体网格及重划分技术,保证模拟结果的高精度;
✓同时进行轧制及温度的耦合分析,简便制定轧制工艺表;
✓可参数化建立轧辊界面模型,并结合DOE优化技术实现轧辊结构设计的自动优化;
✓可任意设置轧具旋转运动方式,实现多道次轧制;
✓可进行轧钢变形过程模拟、模具应力及磨损分析;
✓可实现多种型材、厚薄板、管件等的轧制成形工艺模拟;
✓预测轧制过程中出现的折叠、塔型卷曲、壁厚不均、变形、流线紊乱等轧制缺陷;
●Flowforming流动成形模块
✓具有专用筒形件、复杂截面等深冲压、旋压模板,操作方式流程化,简单易学;
✓具有筒型坯模型及轧具模型自动产生方式;
✓复杂及多数量轧具可实现准确自动定位;
✓可完全采用全六面体网格及重划分技术,保证模拟结果的高精度;
✓优化工具旋转速度、进给深度、轧具尺寸等参数,预测成形形状、成形缺陷等。
●DOE工艺参数优化模块
✓具备专业的DOE前后处理界面,可进行锻造、切削、热处理等工艺的多参数优化及结构尺寸设计优化;
✓可自动优化最佳毛坯尺寸、毛坯重量、模具结构、应力应变、残余应力、材料破坏、晶粒尺寸、飞边、无折叠、无充型不满等;
✓任意设定变量及数值范围,任意指定目标函数;
✓自动优化工艺参数及边界条件,包括成形速度、成形力、成形温度、加热温度、保温时间、冷却时间、切削屑形状等;
✓进行多工序预成形毛坯的尺寸自动优化;
●MAT材料本构及微观模型参数计算模块
✓能够通过提供的宏观实验数据对材料模型转换、微观性能计算、热处理转变数据等方面的材料性能进行计算,用复杂微观模型、材料本构模型等提供数据支持;
✓微观组织计算功能,预测成形及热处理过程中的微观组织及晶粒尺寸、织构等的演变过程,包括CA法、相场法、蒙特卡洛法、织构计算;
✓微观孔洞计算功能,能够预测毛坯内在微观孔洞的形变过程及相关数据。
能够参数化建立微观孔洞子模型,可用于铸锻一体化分析中的铸造缩孔缩松在锻造过程中的孔洞变形、闭合等分析,预测孔洞体积变化、方位流动以及由孔洞产生的裂纹等;
✓淬火TTT曲线计算功能,根据金属的合金配比计算热处理淬火转变曲线,用于新材料的热处理计算;
✓能够根据提供的流动应力参数转换为复杂的材料本构模型,通过提供的载荷-行程数据或应力应变数据拟合计算新材料的流动应力数据;
✓能够通过宏观实验数据拟合JMAK及晶粒生长模型的系数,用于分析成形过程中的晶粒尺寸演变现象。
2.设备选型
经调研,目前国内外金属成形工艺仿真软件主要有SFTC公司研制的专业成形仿真软件DEFORM、法国Transvalor公司软件FORGE、德国Simufact公司软件SimufactForming,其主要技术参数和性能对比如表1、表2所示:
表1DEFORM与FORGE对比
功能
DEFORM
FORGE
前后处理
操作系统
LINUX,UNIX和Windows
LINUX和Windows
支持CAD
格式
STL,STP,IGES,GEO,IGES
提供GeometyTool模块用于查看、测量、修补、编辑、优化几何模型。
STL,STEP包含STL面网格划分模块,修改潜在的几何问题,但该模块容易导致面或体网格生成失败。
用户界面
界面友好,对于常见成形类型提供专用向导式模块,2D与3D集成功能强大
界面友好,2D与3D集成功能强大
语言版本
具有专业中文操作界面,另外包括其他国家的多种语言版本
具有英文操作界面
网格划分
支持六面体单元,拥有同类软件质量最好,稳定性最高的网格划分与重划分功能。
拥有与DEFORM相似的网格功能,对于重划分网格数目用户控制能力非常有限,网格密度窗口功能不可用
材料模型
刚性、刚塑性、弹性、弹塑性、热粘塑性、热弹塑性、多孔材料
刚塑性、弹塑性、热粘塑性、热弹塑性、无多孔材料
材料库
拥有大量的常用材料数据,包含美国、日本、德国、欧洲、俄罗斯、英国、韩国、国际等多种标准,材料库最为全面,包括成形、热处理、组织晶粒材料数据库,流变应力数据最为全面
拥有大量常用材料数据库,标准主要为欧洲标准,欧标之外的材料数据非常有限,热处理材料库很少,功能较弱,部分材料非经过严格测试,仅采用相关软件计算补充,精度偏差大
一般成形功能
设备模型
拥有大量的设备模型,且有高级的运动控制及用户自定义模型,能实现模具沿任意轨迹运动。
具有常用设备吨位库,包括设备运动参数
拥有常见的设备模型及设备自定义模型,功能与DEFORM相似但稍弱,无设备吨位库
对象定位
提供多种定位方式
提供多种定位方式
接触功能
接触功能强大且稳健,有摩擦窗口可实现一个对象上的不同摩擦
接触功能强大且稳健
几何更新
速度快
速度相对慢
求解器
隐式有限元求解器,计算过程中根据问题的不同自动转换求解算法类型,达到高速稳健求解问题的目的拥有ALE求解器,用于稳态分析
隐式有限元求解器,求解算法稳健但慢
多工步
拥有多工步设定功能,可进行全面的过工序模拟,功能强大
多工步功能目前仅处于初级阶段,相比较弱
材料断裂
模拟
提供多种韧性断裂准则,且支持用户自定义
提供多种韧性断裂准则,且支持用户自定义
自由锻
拥有向导式专用模块,支持六面体网格,拥有良好的用户反馈
模板可用,但成熟度和能力较低
轧制功能
轧制功能
具有轧制仿真能力,可以完成平板轧制、形轧、环轧、楔横轧等多种轧制的模拟。
对于环轧、形轧特别提供了向导式模块使操作更加简单
拥有与DEFORM相似的轧制功能,在平板轧制和形轧方面功能较弱
机加工功能
机加工过
程
拥有丰富的机加工功能车削、铣削、钻孔、磨削等
2008年采用有初级的切削成形功能,能力很弱
加工残余
应力
具有加工残余应力预测功能
无该功能
热处理功能
加热模型
可全面模拟工件与环境的热交换。
拥有感应加热、电阻加热、热处理炉加热模型。
可考虑热辐射视角因子的影响。
具有众多热处理专业客户,热处理功能全面
非常有限的热处理能力。
无热辐射视角因子和对流膜层散热系数不可定义为几何或面温度的函数。
热处理功能较弱,专业客户很少
相变
拥有各种相组织体积分数、硬度、应力,变形等预测功能,具备TTT和CCT计算能力
拥有体积分数、硬度、应力,变形等预测功能
渗碳
拥有模拟渗碳过程的功能
拥有模拟渗碳过程的功能
微观组织
具备业界最为完善和先进的微观组织模拟模型,包括JMAK,CA元胞自动机、中尺度等方法拥有再结晶和晶粒长大预测功能,具有成熟的微观组织相图模拟,能
够直观查看微观组织并模拟组织演变过程
拥有再结晶和晶粒长大预测功能,但微观模型过于老旧,研发能力较弱。
蠕变及应力松弛
拥有应力松弛模型,用于模拟蠕变,可以预测相应的应力释放和蠕变变形
无此功能
模具相关
模具应力
分析
拥有非耦合和耦合模具应力分析功能
拥有非耦合和耦合模具应力分析功能
模具磨损
分析
提供模具磨损本构及用户自定义接口,拥有很好的用户反馈
模具磨损功能为新加模块,还处于初级阶段,功能较弱
DOE优化技术
具备先进的DOE/OPT优化技术,业界最为领先,能够优化包括结构设计、工艺参数等多种变量
具备较为简单的优化功能,后期没进一步研发,总体能力较弱。
其他相关
并行计算
具有SMP、MPP方式的并行计算功能,并行效率高
具有一定的并行计算,单核计算效率较低,复杂模型需要很多核并行,对硬件及费用要求高
技术服务
全国有13个分公司及多个高校(清华、哈工大、燕大等)技术服务合作中心,提供地区化技术支持
全国有多家公司代理,均为小代理商,技术服务不方便,无地区化服务
表2DEFORM与SIMUFACTFORMING对比
功能
DEFORM
SIMUFACTFORMING
应用领域
金属成形及热处理专业分析软件。
金属成形专业分析软件。
界面及
易用性
专为金属成形及热处理专业工程师设计的分析软件,界面友好。
针对常用的成形类型及热处理配有向导式模板,使用更加简单流程化。
金属成形专业分析软件,界面易用性好。
网格划分功能
网格划分自动化,并可根据零件形状、场变量梯度等因素自动进行网格重划分,该功能非常成熟,在同类软件中十分突出。
与DEFORM有相似的网格划分功能,但其高级划分功能需要附加模块。
材料库
拥有国际、美国、日本、德国、俄罗斯、欧洲、韩国等标准的材料库,库中包含铝合金、钢、钛合金、高温合金、不锈钢、模具钢、工具材料等多种类型的随温度变化的材料参数。
开放性材料库,用户可以方便的修改添加自己的材料参数。
提供国际、美国英国标准常用的合金材料库,包含钢材、模具钢、铝合金、钛合金等。
材料模型
提供弹性、刚塑性、热弹塑性、热刚粘塑性、多孔材料、刚性等材料模型,可以考虑材料的超塑性、蠕变、各向异性的各种属性,并给用户开放自定义材料模型的接口。
材料模型包括:
刚体、弹性体、塑性体、弹塑性体,无多孔材料。
冷成形
功能
能够模拟各种方式的冷成形,例如板材冷成形、冲锻、弯管成形、冷挤压、拉拔、开坯等各种金属冷成形,并可计算回弹,可考