脱硫吸附剂.docx
《脱硫吸附剂.docx》由会员分享,可在线阅读,更多相关《脱硫吸附剂.docx(12页珍藏版)》请在冰豆网上搜索。
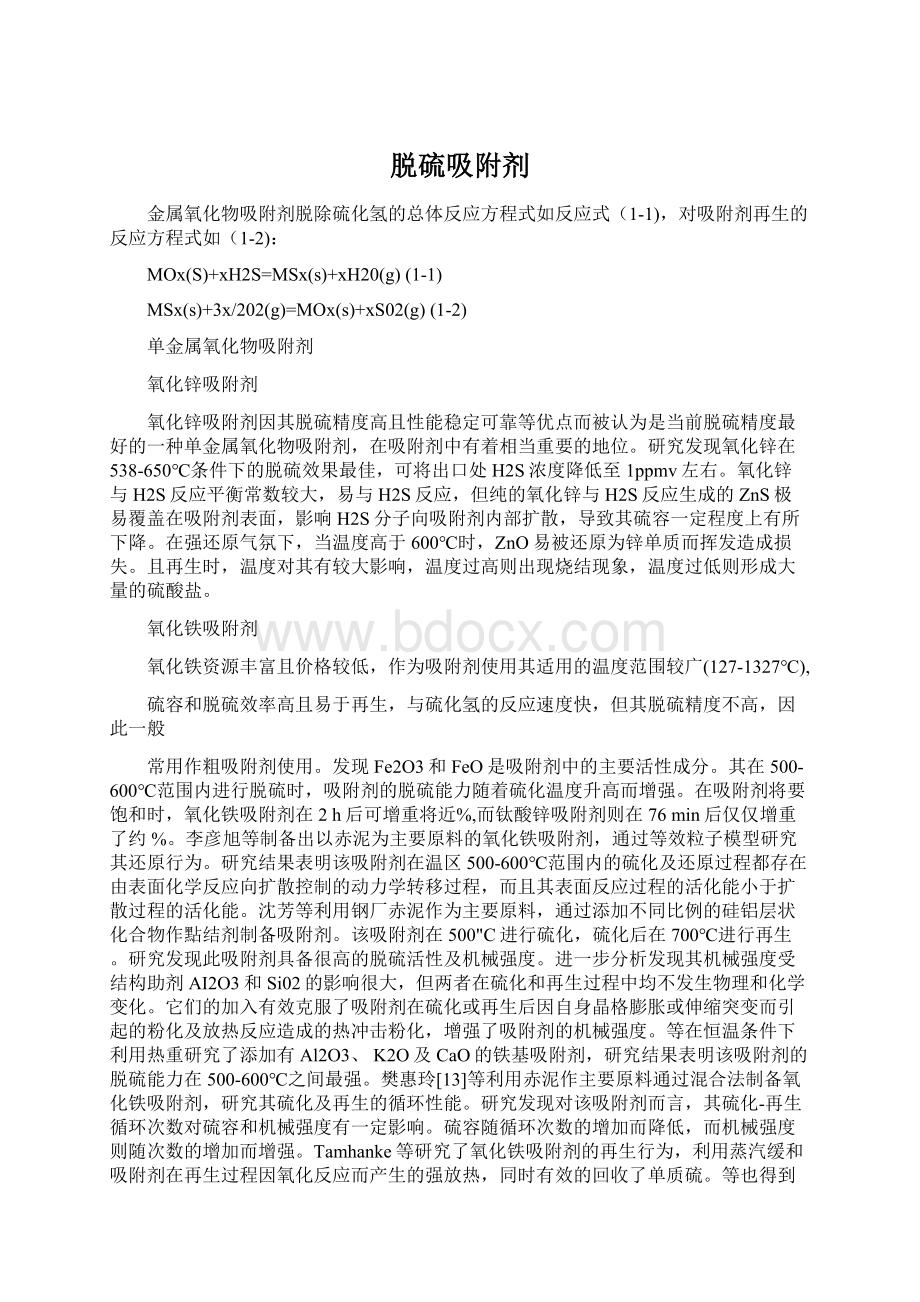
脱硫吸附剂
金属氧化物吸附剂脱除硫化氢的总体反应方程式如反应式(1-1),对吸附剂再生的反应方程式如(1-2):
MOx(S)+xH2S=MSx(s)+xH20(g)(1-1)
MSx(s)+3x/202(g)=MOx(s)+xS02(g)(1-2)
单金属氧化物吸附剂
氧化锌吸附剂
氧化锌吸附剂因其脱硫精度高且性能稳定可靠等优点而被认为是当前脱硫精度最好的一种单金属氧化物吸附剂,在吸附剂中有着相当重要的地位。
研究发现氧化锌在538-650℃条件下的脱硫效果最佳,可将出口处H2S浓度降低至1ppmv左右。
氧化锌与H2S反应平衡常数较大,易与H2S反应,但纯的氧化锌与H2S反应生成的ZnS极易覆盖在吸附剂表面,影响H2S分子向吸附剂内部扩散,导致其硫容一定程度上有所下降。
在强还原气氛下,当温度高于600℃时,ZnO易被还原为锌单质而挥发造成损失。
且再生时,温度对其有较大影响,温度过高则出现烧结现象,温度过低则形成大量的硫酸盐。
氧化铁吸附剂
氧化铁资源丰富且价格较低,作为吸附剂使用其适用的温度范围较广(127-1327℃),
硫容和脱硫效率高且易于再生,与硫化氢的反应速度快,但其脱硫精度不高,因此一般
常用作粗吸附剂使用。
发现Fe2O3和FeO是吸附剂中的主要活性成分。
其在500-600℃范围内进行脱硫时,吸附剂的脱硫能力随着硫化温度升高而增强。
在吸附剂将要饱和时,氧化铁吸附剂在2h后可增重将近%,而钛酸锌吸附剂则在76min后仅仅增重了约%。
李彦旭等制备出以赤泥为主要原料的氧化铁吸附剂,通过等效粒子模型研究其还原行为。
研究结果表明该吸附剂在温区500-600℃范围内的硫化及还原过程都存在由表面化学反应向扩散控制的动力学转移过程,而且其表面反应过程的活化能小于扩散过程的活化能。
沈芳等利用钢厂赤泥作为主要原料,通过添加不同比例的硅铝层状化合物作點结剂制备吸附剂。
该吸附剂在500"C进行硫化,硫化后在700℃进行再生。
研究发现此吸附剂具备很高的脱硫活性及机械强度。
进一步分析发现其机械强度受结构助剂AI2O3和Si02的影响很大,但两者在硫化和再生过程中均不发生物理和化学变化。
它们的加入有效克服了吸附剂在硫化或再生后因自身晶格膨胀或伸缩突变而引起的粉化及放热反应造成的热冲击粉化,增强了吸附剂的机械强度。
等在恒温条件下利用热重研究了添加有Al2O3、K2O及CaO的铁基吸附剂,研究结果表明该吸附剂的脱硫能力在500-600℃之间最强。
樊惠玲[13]等利用赤泥作主要原料通过混合法制备氧化铁吸附剂,研究其硫化及再生的循环性能。
研究发现对该吸附剂而言,其硫化-再生循环次数对硫容和机械强度有一定影响。
硫容随循环次数的增加而降低,而机械强度则随次数的增加而增强。
Tamhanke等研究了氧化铁吸附剂的再生行为,利用蒸汽缓和吸附剂在再生过程因氧化反应而产生的强放热,同时有效的回收了单质硫。
等也得到了相同的实验结论,发现铁基吸附剂的再生温度不能低于600℃,同时得到回收最大产率单质硫的H2O/O2比例。
氧化钙吸附剂
氧化在自然界大量存在,通常可用白云石或石灰石在高于527℃以上煅烧得到。
利用氧化钙制备吸附剂具有很多优点,如原料价格低廉、与硫化氢反应速度快,硫容高等。
但相对其他吸附剂机械强度较差,且不易再生。
硫化反应过程中产生的CaS极易覆盖在吸附剂表面,阻碍了H2S气体向内部的进一步扩散,再生时容易产生大量的硫酸盐,这些都限制了它的使用。
但因为其价格低廉,所以在上世纪70年代国内外就开始对其进行研究。
&1『1等利用石灰石及白云石制备吸附剂,在固定床上进行硫化评价,结果表明CaCO3同硫化氢的反应必须在高于自身分解温度527℃的条件下进行,且反应较慢。
当温度达到950℃时,其分解产生的CaO能与H2S迅速反应。
Kamath等通过热重法重点研究了煅烧白云石制得的CaO与H2S的硫化反应动力学,并根据实验得到了相关动力学参数。
针对氧化钙吸附剂再生时易放热导致烧结和再生后吸附剂机械强度严重下降的问题,等率先提出利用1000-1100℃的空气气氛先把CaS氧化成CaS04,然后利用CO或H2等还原性气体再把CaS04还原为CaO,以此来促进O2的扩散,达到多次循环再生的目的。
该过程发生的反应式为:
CaS+2O2=CaSO4
CaSO4+CO=CaO+CO2+SO2
Van等利用SO2对硫化后的氧化钙吸附剂进行再生,取得良好的效果。
首先在600-700℃下利用SO2把CaS部分氧化为CaSO4和单质S,之后在1100-1200℃下将剩余的CaS与上步生成CaSO2反应得到CaO和SO2,这样多次进行硫化-氧化-再生循环。
.研究表明该法能有效提高氧化钙吸附剂的再生能力。
氧化铜吸附剂
热力学研究发现在127-927℃范围内,氧化铜与硫化氢之间有很强的亲和力,具备较高的脱硫效率,是一种高效的吸附剂。
但氧化铜自身比表面积较小,使用时需与其它载体配合使用,这也在一定程度上限制了它的使用范围。
闫波等使用一步沉淀法制备出纳米氧化铜吸附剂,研究发现其作为常温吸附剂使用具有较高的穿透硫容。
Kyotani等将氧化铜负载在酸性载体上(如二氧化硅、沸石等)制备出一种较单纯氧化铜吸附剂效果更好的吸附剂。
研究结果表明在硫化温度为600℃时,吸附剂中的铜几乎完全被使用,不但避免了烧结现象而且提高了脱硫精度及铜的使用效率。
Abbasian等在氧化铜吸附剂中加入Cr2O3,研究发现适量Cr2O3的加入能有效阻止Cu2O被还原为单质铜,且可将出口H2S浓度降至低于5ppmvoKyotani等利用SiO2负载氧化铜制备吸附剂,研究发现在还原性气氛中吸附剂的脱硫精度有所下降,这是因为氧化铜在此气氛下极易被还原成铜单质,造成部分铜的损失,且由于反应生成的CuS覆盖在吸附剂的表面,阻止了H2S分子的扩散导致出现烧结现象。
侯相林等[40]利用TPS分析发现相对其它金属氧化物,氧化铜的反应温度更低。
基于氧化铜的特点,为了提高其利用率,在使用时可通过对其进行改性或者与其他金属氧化物配合使用。
氧化锰吸附剂
氧化锰脱硫反应速率快且不易被还原为单质锰,具有良好的热稳定性,但其脱硫精度较低,一般只能把出口H2S的含量脱除到100-200ppm,在实际中一般不作为单一金属氧化物吸附剂使用,需和其它氧化物吸附剂复合使用。
Atakvl等将氧化锰负载在Y-Al2O3上制备吸附剂,实验结果表明当硫化温度为600℃时,出口尾气中H2S浓度能被脱除到很低的水平,且利于回收利用,可用水气气氛对其进行再生。
Wakker等在1998年研究了氧化锰和铝猛化合物的脱硫性能,研究发现对于锰系吸附剂,不同反应物对其硫化和还原性能有不同的影响。
氧化锰的最佳硫化温度为850℃。
Liang等利用浸渍法制备锰吸附剂,研究发现猛含量能影响吸附剂的孔容、表面积和硫容。
一定范围内,随着锰含量的提高硫容增加,而孔容和表面积则与之相反,同时发现该吸附剂活性组分中存在Mn2O3和Mn3O4的混合物。
Alonso等在950℃条件下制备了CuO/MnO不同比例的吸附剂,在固定床上进行硫化和再生性能的研究。
研究发现MnO与CuO之间的相互影响并不大,MnO的加入不能阻碍CuO被还原为铜单质,CuO亦不能阻止硫化锰在再生时被氧化成硫酸锰。
万晨等通过共沉淀法制备猛铜复合吸附剂,利用固定床进行硫化评价。
实验结果表明此吸附剂脱硫精度高且硫容较大,脱硫温度、空速等影响其反应活性,而与粒度无关。
侯相林等将MnO2负载在氧化铝上制备吸附剂,实验结果表明硫化过程中吸附剂活性的提高是因为Mn02被还原成MnO。
氧化铈吸附剂
除上述金属氧化物以外,近年来氧化铈也逐渐引起人们的关注,被成为第二代高温煤气吸附剂。
它最大的优点是硫化产物Ce2O2S2在再生时能和SO2快速发生反应,直接生成可回收利用的单质硫,且再生时不形成铈的硫酸盐,铈的挥发较少。
高春珍等[481以硝酸铈为原料,利用干混法制备出氧化铈吸附剂,在固定床反应器中考察煅烧温度和硫化温度的影响。
实验结果表明在600-800℃时,随着煅烧温度和硫化温度的升高,吸附剂的脱硫效率也随之升高;在800℃下,空速与脱硫效率的变化相反。
Zeng等人[49'5D]对氧化铈吸附剂进行了深入研究,研究发现在高温或强还原气氛条件下CeO2首先被还原成CeOn(n≤2),且该吸附剂在反复进行25次硫化-再生实验后,仍具有较好的脱硫活性,其机械强度几乎没有变化。
虽然氧化铈吸附剂的硫化温度较锌基吸附剂高,但氧化铈吸附剂可在强还原气氛下使用,克服了锌基吸附剂在这方面的缺点,且再生时能回收单质硫。
但氧化铈吸附剂脱硫精度不如氧化锌吸附剂高,所以在实际应用中常常将二者结合使用,优势互补。
可先利用Ce02吸附剂粗脱,脱除气体中绝大部分的硫化氢,之后再用氧化锌吸附剂进行精脱,把出口硫化氢的浓度脱除到一个符合生产要求的范围。
对各类单金属氧化物吸附剂的优缺点归纳总结,如表1-1所示。
复合金属氧化物吸附剂的研究
可将其优势归纳为以下几点[52]:
1)有效提高了脱硫效率;2)—定程度上提高了硫容;3)有效防止或降低了金属氧化物以金属游离态的形式挥发或流失;4)活性组分的分散度得到了改善;5)增强了吸附剂的机械强度和稳定性。
当在氧化物吸附剂中添加传递电子能力强的金属氧化物时,具有空轨道的H2S分子将易于接受电子,从而降低反应的活化能,增加反应的活性中心,提高吸附剂的低温活性[53]。
因此,将各种单金属氧化物复合改性是克服单一金属氧化物吸附剂缺点的一个有效手段。
铁酸锌吸附剂的硏究
Zn-Fe吸附剂的主要活性组分为铁酸锌,其由ZnO与Fe203形成,具有尖晶石结构,既减少了Zn的挥发,又大大的提高了硫容,集两者脱硫精度高、硫容大和反应速度快等优势。
极大的提高了单组分氧化锌或氧化铁吸附剂的脱硫性能。
Grindley等首先研制出了铁酸锌吸附剂,在800-850℃下焙烧粘结剂和等摩尔数的Fe2O3和ZnO,其硫化后产物可在空气/水蒸气气氛下进行再生。
Ahmed等研究了能影响铁酸锌吸附剂结构变化的条件,如煅烧温度、氧化物的含量等。
研究发现焙烧温度低,则吸附剂的晶格紧缩;反之,温度高则较松弛。
即经高温焙烧制得的吸附剂其反应活性较低。
在高温和还原气氛下进行再生时,Fe203常常会被还原性气体还原成Fe304和FeO,两者结合形成的尖晶石结构使得吸附剂本身的机械强度下降。
许鸿雁等主要研究铁酸锌吸附剂的硫化及再生性能,实验结果表明铁酸锌吸附剂的最适硫化温度为350℃,且其机械强度在多次硫化-再生后不降反升,具有良好的抗磨损性。
Munusamy等在铁酸锌吸附剂中加入铜的氧化物,研究发现Cu2+能提高硫化反应的催化活性,而Zn2+起到增强反应稳定性的作用。
该吸附剂的硫化穿透时间能达到100h以上,表现出良好的稳定性和很高催化活性。
Woods等在制备铁酸锌吸附剂时加入2%的膨润土并考察不同的煅烧条件对其性能的影响,实验结果表明这样制备的吸附剂具有高强度和稳定性。
卢朝阳等[61]考察并研究了自制铁酸锌吸附剂的再生气氛,研究发现在650-700℃范围内,吸附剂几乎可以完全再生,且再生后的吸附剂其反应活性有所提高;其最佳的再生温度和再生气氛分别为600℃,2%02、48%N2和50%H20(g)。
Akyuritlu等在铁酸锌中加入适量V2O5制备出一种新吸附剂,研究发现吸附剂中锌的挥发量与V2O5的加入量存在一定关系,加入量越多,锌的挥发越少。
这进一步增强了吸附剂的循环稳定性;Zn-Fe-V吸附剂的脱硫能力优于单一氧化锌吸附剂。
为减少强还原性气氛下氧化锌的挥发量及避免再生时形成大量的硫酸盐,并稳定钛酸锌的尖晶石结构,Pineda等利用TiO2对其进行改性,研究发现镍的加入能有效阻
止铁酸锌的分解,增强其在还原气氛中的稳定性,提高自身的反应活性。
且在一定范围内随着镍含量的增加,吸附剂的表面积随之增大,推测其可能与本粒子的大小有一定关系。
Makoto[64]等考察了Sn02对MnZnFe204吸附剂脱硫性能的影响,研究发现SnCh能通过控制晶粒由离子空穴造成的反常生长,并通过增加密度来促进尖晶石结构的再生成,Sn4+与Fe2+可结合形成稳定的Sn4+-Fe2+离子对
钛酸锌吸附剂的研究
ZnO能与Ti02形成具有反尖晶石结构的复合物,其脱硫能力好、力学强度高、抗H2或CO还原能力强,能有效减少吸附剂中锌的挥发,提高了吸附剂的稳定性。
Ti02按晶型一般可分为锐钛矿、金红石和板钛矿三类。
其中板钛矿一般很少用到。
锐钛矿和金红石都具有钛氧八面体结构,二者的差异在于八面体的畸变程度和八面体间连接的方式不同。
常见的锌-钛复合氧化物如ZnTi03、Zn2Ti308和Zn2Ti04,它们都是反尖晶石结构,其中Zn2Ti04吸附剂的硫容最大。
Abbasian等制备了Ti/Zn摩尔比为5:
1的钛酸锌吸附剂,实验结果表明其使用寿命长,抗磨损性强,多次硫化实验后反应活性几乎没有变化。
Cole等考察了钛酸锌吸附剂的脱硫能力,研究发现在高温条件下Ti02具有防止锌单质挥发的作用,在硫化动力学上与氧化锌相似。
Makoto等[671研究了不同再生条件对钛酸锌吸附剂再生性能的影响。
发现少量水的存在,不但使Ti02能显著的促进ZnS与O2反应,而且也可以提高ZnS与H2O的反应速率。
当温度高于650℃时,吸附剂出现碎裂现象,反应活性受到影响。
等利用固定床对制备的钛酸锌吸附剂进行评价,结果发现在经过5次循环脱硫实验后,其稳定性几乎没有改变,但脱硫精度略逊于纯氧化锌吸附剂。
Law等利用ZnO和Ti02的混合楽液经干燥和焙烧后制备出钛酸锌吸附剂,研究发现其热稳定性和脱硫率比单一氧化锌吸附剂明显提高。
等使用四氧化三钴对钛酸锌吸附剂进行改性,研究发现钴是该吸附剂的活性组分之一,其能有效阻止Zn的外逃运动,显著减少了锌的挥发损失;镍可以在一定程度上降低硫化温度,使得吸附剂的适用温区更广;当吸附剂中C03O4的质量分数为25%,硫化温度为480℃时,其脱硫能力最强,稳定性最好。
邓一英等考察了钛酸锌吸附剂的最佳再生温度。
实验结果表明700℃是其最佳再生温度,在低于700℃条件下吸附剂再生不完全,反应活性下降。
其它复合吸附剂的研究
Postan等研究了La2O3对ZnO-Ti02吸附剂脱硫及再生性能的影响。
研究发现因La3+离子半径较Zn2+和Ti4+的离子半径大,所以加入LazCb的ZnO-Ti02吸附剂在多次硫化-再生循环后,本身很少出现破缝现象,但在再生过程中会产生些许La的硫化物。
Andersor等制备了以ZrzOs或Y-AI2O3为载体的氧化锌吸附剂,实验结果表明这两种载体对提高单一氧化锌吸附剂的机械强度和反应速率都有很大作用,但在高温条件下阻碍锌的流失作用甚微。
Garcia等研究了铜锰复合氧化物吸附剂的硫化性能。
实验结果表明该吸附剂反应活性主要受铜含量的影响,含量高时容易导致吸附剂烧结。
为保证其具有良好的脱硫能力及减少再生时硫酸盐的出现,选择700℃为最佳硫化温度,800℃为最适再生温度。
Maria等考察了复合铜的CeCb吸附剂,研究发现在CeO2吸附剂中加入铜后能适应更低的硫化温度,还原反应速度得到了一定的提高,甚至在低于200℃时吸附剂仍具有良好的活性。
实验表明铜的最近比例为5%。
Akit利用一种名为Core-in-shell的模型研究了鈣基吸附剂的机械强度。
依据该模型采用含质量分数40%的石灰石小球为内核,nim厚度的铝酸水泥做外壳,制备吸附剂。
在固定床上进行硫化评价,实验结果表明该吸附剂具有好的机械性能和强的脱硫能力,其最佳硫化温度为920℃,但再生后反应活性与脱硫能力都有所下降。
通过以CaS04为内核,AI2O3和CaO混合物为外壳的吸附剂比较,发现小球状吸附剂的机械强度主要受外壳厚度的影响。
Slimane等考察了锰-铜-铝复合氧化物吸附剂在中高温模拟煤气中的脱硫性能。
实验结果表明该吸附剂脱硫效率高、硫容大、抗磨损性能高,具有良好的脱硫能力,对H2S有很好的脱除效果,经其脱除后尾气浓度在1ppmv以下,是一种优秀的中高温吸附剂。
葛晓华重点研究了Fe-Ce复合氧化物吸附剂,研究发现该吸附剂的脱硫性能主要受反应过程中还原反应的影响。
其可能原因是还原时一个或几个还原态易与H2S结合。
同时还发现Si02的加入能有效地提高F8C2S953吸附剂的脱硫能力,但对F7C3S953吸附剂则起到了相反的作用。
氧化铝只对F7C3A953吸附剂的脱硫性能有影响,对F8C2S953吸附剂则起促进作用。
综上所述归纳常见复合吸附剂的特点如表1-2所示。
该脱硫剂主要应用于半水煤气脱硫,变换气脱硫,焦炉煤气脱硫,硫化氢脱出,
PDS-4最新高效脱硫催化剂
PDS-4脱硫催化剂是气液相催化氧化剂。
适用于所含硫化氢、硫醇、二硫化碳、羰基硫等液体、气体的脱硫。
广泛用于半水煤气、天然气、焦炉气、城市煤气、液化石油气、汽油、石脑油等。
目前国内使用的催化剂有十几种之多,其中具有代表性的是:
ADA、MSQ、MQ、FQ,对苯二酚、KCA栲胶等。
但上述催化剂尚不能满足某些工艺要求,也存在一些缺点,如不能脱有机硫、总脱硫效率低、泡沫硫不易分离、堵塞设备、适应性小等。
PDS-4脱硫催化剂是总结我厂生产的PDS在脱硫工艺中存在的问题而开发的新产品。
可在原工艺条件不变的基础上改换上述脱硫催化剂为我厂的PDS-4脱硫催化剂。
PDS-4脱硫催化剂脱硫全面,能脱除无机硫,也可脱除5g/Nm3以上高硫。
PDS-4不腐蚀设备、不堵塞设备、能清除设备的沉积硫,该催化剂无毒、无污染、使用方便,广泛用于化肥厂、煤油厂、煤气厂、制碱厂等。
PDS-4脱硫催化剂脱无机硫效率达95-98%,脱有机硫效率达50-80%。
PDS-4脱硫催化剂系酞菁类金属有机化合物,是以多种金属离子为中心的一大类有机金属化合物的总称。
该类化合物具有特定颜色,在酸碱性介质中不发生分释,热稳定性好,水溶性好、无毒、对硫化物具有很强的催化氧化作用。
二、PDS-4脱硫催化剂作用机理可分四步
1、在碱溶淮中将溶液的O2吸附而活化;
2、当遇到H2S等含硫化合物时,将硫化物吸附到高活性的大离子微观表面。
这时硫化物的分解和氧的分释将形成新化合物分子,在常温常压下,便由原来的吸携活化氧将含硫化合物氧化,产物为硫和多硫化物,同时也有硫代硫酸盐或二硫化物形成;3、新产物从活性大离子的微观表面上解析离去;
4、此时脱硫液中活性大离子(既酞菁类有机金属化合物)经重新携氧而再生,只要活性离子保留在催化液中不被其物质浮获或溢出系统外,催化剂使用寿命是相当长久的。
三、技术指标
性能:
能脱5g/Nm3以下硫化氢气体外观:
灰蓝色粉沫密度:
(g/Cm3)有效成份(%)>95水不溶物(%)≤四、使用方法及注意事项1、以氨水为吸收剂时最好不要用含有消泡剂的碳化氨水,以防止干扰硫泡沫的浮选分离。
2、催化剂可以单独使用,也可与MSQ配合使用。
但必须分别溶解,用新鲜碱液或贫液将催化剂溶解后要通入少量空气,预活化2-4小时,然后每班均匀补加入脱硫液中。
3、第一次配制脱硫液时,按脱硫液体积和所处理的气体中H2S含量高低而定,一般加入量按15-20g/m3来计算。
正常生产时,催化剂平均的消耗量为。
若溶液损失较大或有机硫含量较高时,要适当多补充一些。
PDS-4脱硫催化剂是气液相催化氧化剂。
适用于所含硫化氢、硫醇、二硫化碳、羰基硫等液体、气体的脱硫。
广泛用于半水煤气、天然气、焦炉气、城市煤气、液化石油气、汽油、石脑油等。
目前国内使用的催化剂有十几种之多,其中具有代表性的是:
ADA、MSQ、MQ、FQ,对苯二酚、KCA栲胶等。
但上述催化剂尚不能满足某些工艺要求,也存在一些缺点,如不能脱有机硫、总脱硫效率低、泡沫硫不易分离、堵塞设备、适应性小等。
PDS-4脱硫催化剂是总结我厂生产的PDS在脱硫工艺中存在的问题而开发的新产品。
可在原工艺条件不变的基础上改换上述脱硫催化剂为我厂的PDS-4脱硫催化剂。
PDS-4脱硫催化剂脱硫全面,能脱除无机硫,也可脱除5g/Nm3以上高硫。
PDS-4不腐蚀设备、不堵塞设备、能清除设备的沉积硫,该催化剂无毒、无污染、使用方便,广泛用于化肥厂、煤油厂、煤气厂、制碱厂等。
PDS-4脱硫催化剂脱无机硫效率达95-98%,脱有机硫效率达50-80%。
PDS-4脱硫催化剂系酞菁类金属有机化合物,是以多种金属离子为中心的一大类有机金属化合物的总称。
该类化合物具有特定颜色,在酸碱性介质中不发生分释,热稳定性好,水溶性好、无毒、对硫化物具有很强的催化氧化作用。
PDS-4脱硫催化剂作用机理可分四步
1、在碱溶淮中将溶液的O2吸附而活化;
2、当遇到H2S等含硫化合物时,将硫化物吸附到高活性的大离子微观表面。
这时硫化物的分解和氧的分释将形成新化合物分子,在常温常压下,便由原来的吸携活化氧将含硫化合物氧化,产物为硫和多硫化物,同时也有硫代硫酸盐或二硫化物形成;3、新产物从活性大离子的微观表面上解析离去;
4、此时脱硫液中活性大离子(既酞菁类有机金属化合物)经重新携氧而再生,只要活性离子保留在催化液中不被其物质浮获或溢出系统外,催化剂使用寿命是相当长久的。
技术指标性能:
能脱5g/Nm3以下硫化氢气体外观:
灰蓝色粉沫密度:
(g/Cm3)有效成份(%)>95水不溶物(%)≤使用方法及注意事项
1、以氨水为吸收剂时最好不要用含有消泡剂的碳化氨水,以防止干扰硫泡沫的浮选分离。
2、催化剂可以单独使用,也可与MSQ配合使用。
但必须分别溶解,用新鲜碱液或贫液将催化剂溶解后要通入少量空气,预活化2-4小时,然后每班均匀补加入脱硫液中.
3、第一次配制脱硫液时,按脱硫液体积和所处理的气体中H2S含量高低而定,一般加入量按15-20g/m3来计算。
正常生产时,催化剂平均的消耗量为。
若溶液损失较大或有机硫含量较高时,要适当多补充一些
钴催化剂
以双核聚酞菁钴为主要成份的复合型脱硫剂,它具有特定颜色,无毒、无味对硫化物有很强的催化氧化活性。
它主要应用于半水煤气、城市煤气、天燃气、焦炉气以及其它工业废气中的硫化氢的脱除,同时可以脱除有机硫,可以取代传统的ADA法,栲胶法等常用的脱硫剂,亦是酞菁钴类脱硫剂的换代产品,本产品使用工艺操作简单,不改变原工艺流程和设备,并且具有脱硫效率高,用量少,再生好,不堵塔,不腐蚀设备的特点。
氧化铁脱硫剂
一用途
主要用于半水煤气、水煤气、焦炉气、天然气、沼气、石油化工及化肥生产中变换气、CO2再生气等气体中的H2S的脱除。
二、主要理化指标
型号
MT-1型
MT-2型
粒度(mm)
φ(5-6)×(5-15)
φ(5-6)×(5-15)
侧压强度(N/cm)
≥40
≥50
堆密度(kg/L)
饱和硫容(%)
≥50
≥70
操作条件及注意事项1、空速:
500-1500h-1,以500-1000h-1为宜2、温度:
10-80℃3、压力:
常压Mpa4、湿度:
脱H2S时,湿度越大越好,最好为接近饱和水汽,但严禁带水进床层。
5、开车:
开车前系统应先用原料气置换,并应逐渐升压,然后转入正常生产。
6、再生或更换脱硫剂时,采用惰性气体置换可燃气体成份,降至爆炸极限以下,再生时从塔底通入空气,空速5-50h-1,再生初期要低空速,塔内温度要控制在110℃以下,如超过110℃,可暂停通入空气,温度降至100℃以下时,可继续通入空气再生,当床层温度不升,进出口的氧含量基本相等即可结束再生。
更换脱硫剂时,不可打工塔底卸料口放出脱硫剂,为安全起见,应适当喷水冷却。
1KC-2改性活性炭脱硫剂是在常温常压及微量氧存在下,将硫化氢氧化成元素硫,元素硫吸附在KC-2脱硫剂中;KT-310脱硫原理是有机硫在微量水存在下水解为无机硫,无机硫再与氧化锌反应,要求反应温度在80-110,压力的条件下。
由此可见,该脱硫剂反应条件苛刻,反应过程复杂。
2新型高效脱硫剂是一种以