甲醇制氢操作规程范文.docx
《甲醇制氢操作规程范文.docx》由会员分享,可在线阅读,更多相关《甲醇制氢操作规程范文.docx(17页珍藏版)》请在冰豆网上搜索。
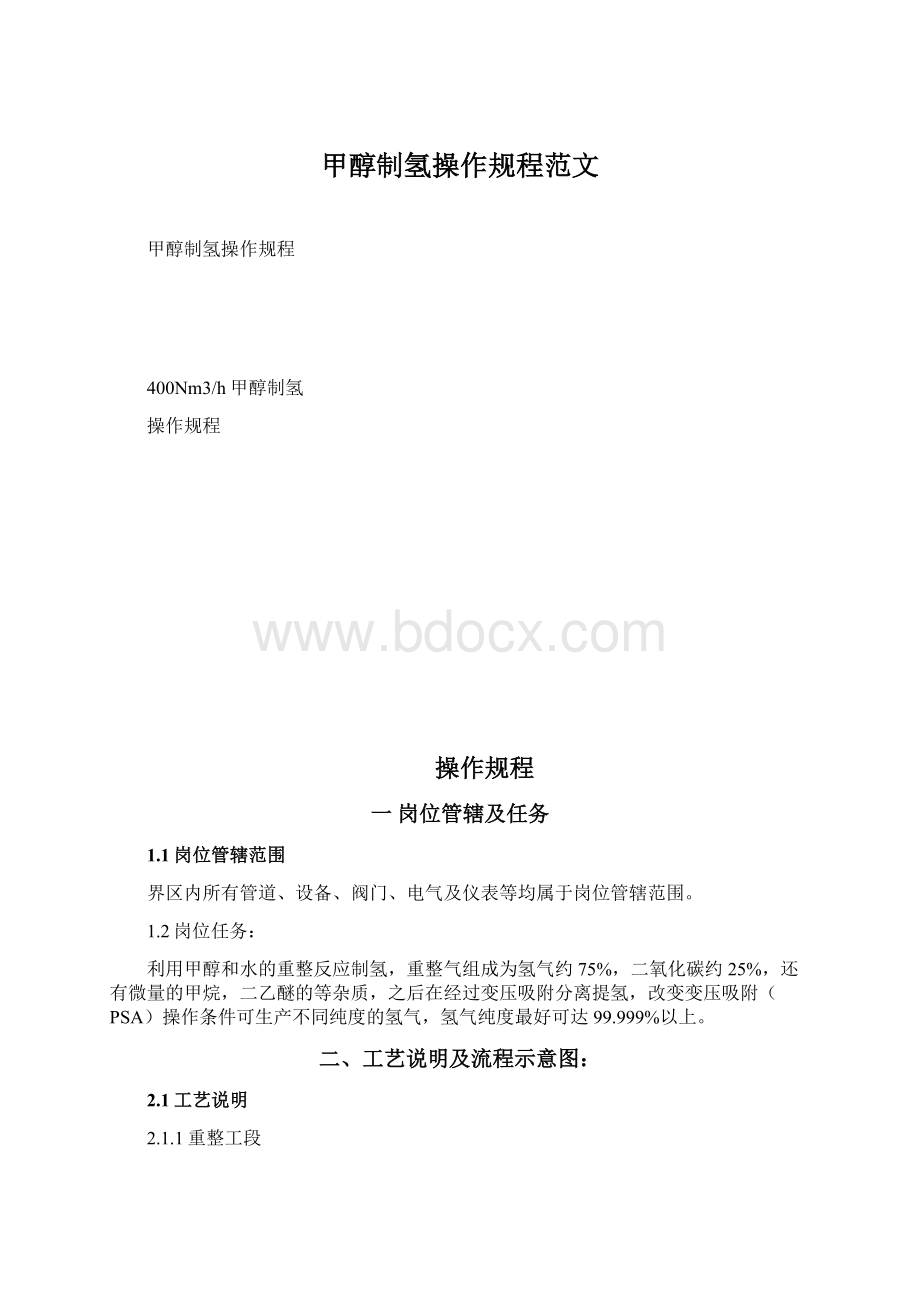
甲醇制氢操作规程范文
甲醇制氢操作规程
400Nm3/h甲醇制氢
操作规程
操作规程
一岗位管辖及任务
1.1岗位管辖范围
界区内所有管道、设备、阀门、电气及仪表等均属于岗位管辖范围。
1.2岗位任务:
利用甲醇和水的重整反应制氢,重整气组成为氢气约75%,二氧化碳约25%,还有微量的甲烷,二乙醚的等杂质,之后在经过变压吸附分离提氢,改变变压吸附(PSA)操作条件可生产不同纯度的氢气,氢气纯度最好可达99.999%以上。
二、工艺说明及流程示意图:
2.1工艺说明
2.1.1重整工段
甲醇进入界区后直接进入混配罐中,经过液位控制甲醇进料量,无离子水进入界区后直接进入混配罐中,经过控制液位控制无离子水进料量,两台混配罐一台陪料,一台使用。
混配罐内甲醇、水混合液体能维持一个班八小时的工作用量。
混配罐中的混合液经计量泵输送到换热器中。
本工艺现场配备三台计量泵,其中一台输送混合液体,一台给水洗塔输送无离子水,另一台备用,三台泵型号、结构完全相同,开二备一。
甲醇、水混合液体进入换热器与由反应器出来的重整气进行换热,换热后混合液温度由室温升至140℃,并呈现部分气化的气液胶着状态,然后接着进入气化过热器,被过热器下部管壳内高温导热油加热气化,气化后的甲醇、水混合蒸气经过气化过热器上部列管被管壳中的高温导热油进一步加热到240~300℃范围内,然后进入反应器中。
进入反应器的甲醇、水混合蒸气由上而下经过催化剂床层,在催化剂的作用下发生甲醇、水蒸气重整反应,生成产物为二氧化碳和氢气—重整气。
由反应器出来的重整气进入换热器中与原料甲醇、水液体进行换热,完成热量交换后,重整气的温度由240~300℃降为160℃左右,然后进入水冷却器进一步冷却至室温,经冷却后的重整气由下而上进入水洗塔,与由上喷淋而下的无离子水逆向流动,在填料表面充分接触,重整气中携带的未反应的甲醇蒸气被无离子水洗掉,然后进入气液分离器、缓冲罐后送往变压吸附系统进行氢气提纯。
水冷器中的冷凝液经过排污阀利用自重流入水洗塔,水洗塔喷淋的无离子水进行洗涤,当水洗塔的液位不断升高至液位计上限时,排液电磁阀将打开,将液体排至无离子水储罐,当水洗塔中液位低至液位计控制下限时,电磁阀将关闭,依此将液位保持在上下限范围内。
2.1.2吸附工段
本项目中所采用的复合吸附剂具有发达的内孔、丰富的比表面积,对氢气之外的杂质组分吸附容量大,与氢气分离得彻底,吸附饱和后的吸附剂采用真空解析的方式得到再生。
本变压吸附系统采用五塔流程。
每个吸附塔在一次循环均需要经历吸附(A)、一次降压(1ED)、二次降压(2ED)、三次降压(3ED)、逆向放压(D)、真空解析(V)、一次升压(1ER)、二次升压(2ER)三次升压(3ER)以及最终升压(FR)等十个步骤。
五个吸附塔在执行程序的时间安排上相互错开,构成一个闭路循环,以保证原料连续输入和产品不断输出。
整个过程由工控机控制25个气动阀自动切换实现。
现以A塔为例说明,A塔按照5-1-2/V方式运行时在一次循环周期内各工艺步骤的工艺过程如下:
1.吸附(A)
程控阀开启,重整气在1.5MPa下进入A塔,重整气中除氢气以外的其它组分被吸附剂吸附,未被吸附的H2流出吸附塔。
当吸附剂吸附前沿移动到接近吸附剂塔顶末端时,程控阀关闭,停止原料气进入和产品气输出。
此时吸附塔中吸附剂前沿依然留有一段未吸附杂质的吸附剂,目的:
防止杂质组分穿透吸附床层流入产品中,降低产品气的纯度。
过程压力:
1.5MPa吸附时间:
~360S
2.第一次降压平衡(1ED),简称一次降压
吸附塔A吸附步骤停止后,开启程控阀,使A塔与刚结束一次升压步骤的塔出口端相连,实行A塔第一次压力降和塔的第二次升压,均压过程中吸附塔A的吸附前沿朝出口端方向推进,但仍未到其出口端。
俩塔均压后,两塔压力相等,稳定在1.12MPa,均压完毕,回收了A塔死空间中纯氢气。
过程压力:
由1.50MPa下降到1.12MPa
步骤执行时间:
~60S
3.第二次降压平衡(2ED),简称二次降压
吸附塔A第一次降压平衡步骤停止后,开启程控阀,使A塔与已结束逆向放压步骤的塔出口端相连,实行A塔的第二次压力降和向放压步骤的塔的第一次升压,均压过程中吸附塔A的吸附前沿继续朝出口端方向推进,但仍未到其出口端。
均压后,两塔压力相等,压力为0.60MPa,均压完毕,关闭程控阀,再次回收了A塔死空间的氢气。
过程压力:
由1.12MPa下降到0.74MPa
3.第三次降压平衡(3ED),简称三次降压
吸附塔A第一次降压平衡步骤停止后,开启程控阀,使A塔与已结束逆向放压步骤的塔出口端相连,实行A塔的第三次压力降和塔的第一次升压,均压过程中吸附塔A的吸附前沿继续朝出口端方向推进,但仍未到其出口端。
均压后,两塔压力相等,压力为0.36MPa,均压完毕,关闭程控阀,再次回收了A塔死空间的氢气。
过程压力:
由0.74MPa下降到0.36MPa
步骤执行时间:
~60S
4.逆向放压
开启程控阀使A塔内剩余气体直接经过消声阻火器放入大气。
过程压力:
由0.36MPa下降到0.00MPa
步骤执行时间:
~60S
5真空解析
逆向放压结束后,对A塔进行抽真空解析至-0.08MPAG。
6.第一次升压平衡(1ER),简称一次升压
关闭程控阀HS201A停止抽空;开启程控阀,利用塔二次降压平衡后的气体,对A塔进行一次升压平衡,均压后两塔压力稳定在0.36MPa,此时回收了B塔死空间的纯氢气,同时A塔完成一次升压和塔的第二次降压。
过程压力:
由0.00MPa上升到0.36MPa
步骤执行时间:
~60S
7.第二次升压平衡(2ER),简称二次升压
一次升压结束后,开启程控阀,利用塔一次降压平衡后的气体,对A塔进行二次升压平衡,均压后两塔压力稳定在0.74MPa,此时回收了C塔死空间的纯氢气,完成对A塔的二次升压和C塔的第一次降压。
过程压力:
由036MPa上升到0.74MPa
步骤执行时间:
~60S
7.第三次升压平衡(3ER),简称三次升压
一次升压结束后,开启程控阀,利用塔一次降压平衡后的气体,对A塔进行三次升压平衡,均压后两塔压力稳定在1.12MPa,此时回收了C塔死空间的纯氢气,完成对A塔的二次升压和C塔的第一次降压。
过程压力:
由0.74MPa上升到1.12MPa
步骤执行时间:
~60S
8.最终充压
二次升压结束后,开启程控阀对A塔进行四次升压,均压后A塔压力稳定在1.5MPa。
过程压力:
由1.12MPa上升到1.5MPa
步骤执行时间:
~60S
这一步骤完成后,A塔完成一个完整的吸附、均压、再生过程,紧接着便进行下一次循环。
过程叙述中的步骤执行时间及过程压力是说明性的,装置在实际运行中根据原料气流量、组成和压力的变化将随时对时间和压力进行调整。
其它四个塔的操作步骤与A塔相同,只是在时间上相互错开,同一时间内各塔依据吸附时序执行着不同步骤。
2.2流程示意图
见附件
三岗位工艺指标:
3.1温度指标:
1.换热器160℃
2.气体过热器280℃~300℃
3.反应器270℃~290℃
4水冷器30℃
3.2流量指标:
1.无离子水中间罐:
1.86m3/h
2.混配罐:
4.14m3/h
3.换热器:
0.69m3/h
4.气体过热器:
606.83Nm3/h
5.反应器774.50Nm3/h
6.冷冻换热器675.58Nm3/h
7.缓冲罐578.53Nm3/h
8.吸附塔出口400.00Nm3/h
9.真空缓冲罐400.00Nm3/h
3.3压力指标:
MPa
1.换热器出口压力:
1.5
2.气化过热器出口压力:
1.48
3.反应器出口压力:
1.44
4.水冷器出口压力:
1.38
5.缓冲罐出口压力:
1.34
6.吸附塔进口压力:
1.32
7.吸附塔出口压力:
1.20
3.4液位:
1.水冷器:
2.气液分离器:
3.5分析指标
采用氢气分析仪对产品氢气进行在线分析,并与阀门连锁,当氢气纯度合格时经过氢气储罐,不合格时放空,分析仪取样装置和鉴定器装在现场,检测数据远传只控制室仪表盘上的显示器,产品氢气纯度由仪表盘上读出。
四:
装置启动初次开车及停车后的再启动
4.1管道的试漏、保压
在装置安装完毕后,对整个装置进行吹扫,将管道中残留的粉尘、焊渣吹扫干净,注意:
要分段吹扫,不要将废物吹进设备、罐体中。
吹扫完毕进行亲密性试验,实验方法:
为节省开支,可先用空压机将净化后(除油、除水)的压缩空气冲入系统,先将压力预升至1.0MPa,然后用瓶装空气或氮气继续升压至1.5MPa,冲压完毕,将所有进出气口分住保压,24小时压降小于0.05MPa视为合格。
4.2催化剂的装填
4.2.1催化剂装填的准备工作
1.合成塔壳程和汽包水试压及蒸煮合格后,降至常温。
2.已清除合成塔内的堵塞物,用钢刷将内部除锈并清扫干净。
以免对催化剂在生产过程中的活性、选择性和寿命产生影响,特别是容易生成各种副产物特别是高级烃(如石蜡等),对生产的正常运行造成很大的影响。
3.合成循环回路吹扫完毕。
4.打开合成塔上下人孔盖,进入塔内仔细检查是否清理干净,催化剂支承框上的不锈钢丝网是否完好。
5.准备好装填氧化铝瓷球和催化剂所需工具:
6.将Φ25和Φ10两种氧化铝瓷球送至现场,搬运到合成塔匡架平台上,在平台上放一块篷布,其上放一块塑料布。
将氧化铝瓷球开桶倒出检查,把破碎的捡出来。
7.新反应器和旧反应器的装填方法一样,均按以下方案进行。
4.2.2装填惰性瓷球
1.低压安全照明灯应接到塔内,以便入塔人员工作。
2.操作人员必须将身上携带的小刀、硬币、钢笔等易脱落物品取下,并穿戴特别防尘连体式工作服、手套、安全帽后方能进入合成塔内工作。
3.按预计装填高度在合成塔下封头内划好Φ25瓷球的装填高度线。
4.由两名操作人员从合成气出口锥帽人孔进入下封头,在合成塔底部装填Φ25瓷球至与底部人孔口下边缘平齐,用扒具扒平。
将人孔用螺丝把好。
5.从锥帽顶盖处装入Φ25瓷球,并用扒具扒平。
测量出剩余空间的高度,计算好剩余空间的体积及所Φ25的瓷球量。
6.清理出所有工具和物品后,封好顶盖。
7.从上人孔进入合成塔上管板,从换热管内按计算量补装Φ25瓷球。
补装时应按反应管排布规律依次缓慢、均匀装填,防止瓷球在列管内架桥。
8.从上管板补装瓷球的过程中,应不断用探绳测量各个部位瓷球装填高度,使各部位瓷球装填高度尽可能相等(尽量控制装填高度差在10mm以内)。
9.瓷球最终装填至与下管板齐平或下管板上50mm处。
4.2.3催化剂的装填
1.在干净的地上放置两张篷布,在篷布上用孔径2×2筛子将催化剂开经过筛,除去其中的触媒灰和碎粒。
最好是将催化剂经过一倾斜筛子的方式进行过筛,在过筛过程中要放止踩碎催化剂。
2.过筛后的催化剂分装于10~15L的小袋子中,用吊车吊至合成塔上部人孔平台。
3.催化剂装填高度为上管板上200mm,在合成塔内画好此装填高度线。
4.根据合成塔直径大小确定进入合成塔装填催化剂的人数,入塔装填催化剂的人员必须佩戴过滤式防尘口罩和防尘镜,不可携带易脱落物品进入合成塔内。
5.操作人员进入上管板负责装填催化剂的过程中必须有人在人孔附近监护和联系工作。
6.反应器内的操作人员应按照列管排列顺序,将催化剂缓慢、均匀地装入列管内。
一定要控制装填速度,防止催化剂架桥。
装填过程中,要经常将管板上的催化剂扫入反应管中,并依次将每根催化剂管都装至离上管口约5~10mm。
防止操作人员踩碎催化剂。
7.继续在上管板上装一层高度为大约200mm左右的催化剂,以弥补催化剂还原后的体积收缩。
8.最后在催化剂上再铺Φ10耐火瓷球高100mm。
9.经有关人员检