炉衬测厚技术的定量化研究.docx
《炉衬测厚技术的定量化研究.docx》由会员分享,可在线阅读,更多相关《炉衬测厚技术的定量化研究.docx(11页珍藏版)》请在冰豆网上搜索。
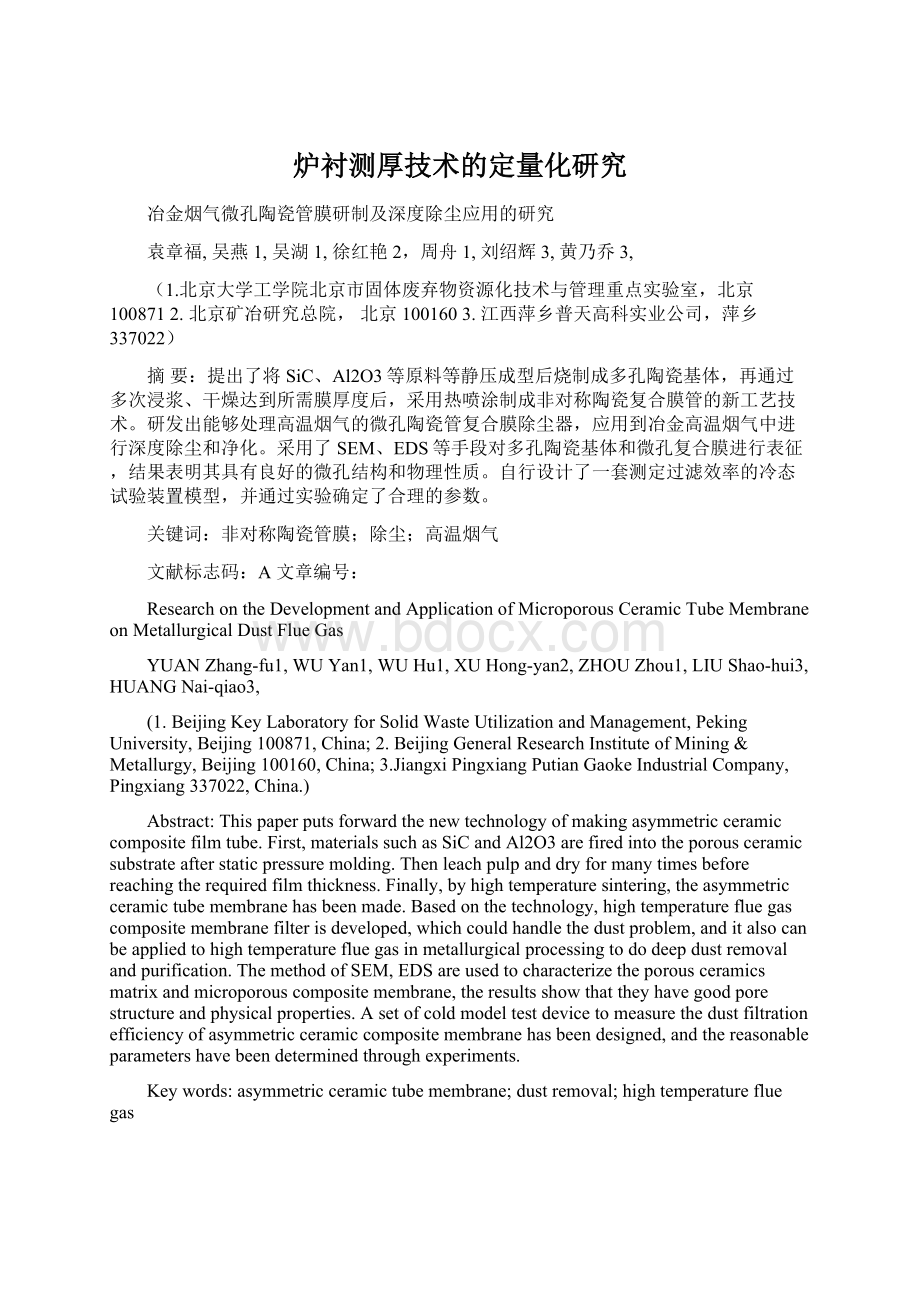
炉衬测厚技术的定量化研究
冶金烟气微孔陶瓷管膜研制及深度除尘应用的研究
袁章福,吴燕1,吴湖1,徐红艳2,周舟1,刘绍辉3,黄乃乔3,
(1.北京大学工学院北京市固体废弃物资源化技术与管理重点实验室,北京1008712.北京矿冶研究总院,北京1001603.江西萍乡普天高科实业公司,萍乡337022)
摘要:
提出了将SiC、Al2O3等原料等静压成型后烧制成多孔陶瓷基体,再通过多次浸浆、干燥达到所需膜厚度后,采用热喷涂制成非对称陶瓷复合膜管的新工艺技术。
研发出能够处理高温烟气的微孔陶瓷管复合膜除尘器,应用到冶金高温烟气中进行深度除尘和净化。
采用了SEM、EDS等手段对多孔陶瓷基体和微孔复合膜进行表征,结果表明其具有良好的微孔结构和物理性质。
自行设计了一套测定过滤效率的冷态试验装置模型,并通过实验确定了合理的参数。
关键词:
非对称陶瓷管膜;除尘;高温烟气
文献标志码:
A文章编号:
ResearchontheDevelopmentandApplicationofMicroporousCeramicTubeMembraneonMetallurgicalDustFlueGas
YUANZhang-fu1,WUYan1,WUHu1,XUHong-yan2,ZHOUZhou1,LIUShao-hui3,HUANGNai-qiao3,
(1.BeijingKeyLaboratoryforSolidWasteUtilizationandManagement,PekingUniversity,Beijing100871,China;2.BeijingGeneralResearchInstituteofMining&Metallurgy,Beijing100160,China;3.JiangxiPingxiangPutianGaokeIndustrialCompany,Pingxiang337022,China.)
Abstract:
Thispaperputsforwardthenewtechnologyofmakingasymmetricceramiccompositefilmtube.First,materialssuchasSiCandAl2O3arefiredintotheporousceramicsubstrateafterstaticpressuremolding.Thenleachpulpanddryformanytimesbeforereachingtherequiredfilmthickness.Finally,byhightemperaturesintering,theasymmetricceramictubemembranehasbeenmade.Basedonthetechnology,hightemperaturefluegascompositemembranefilterisdeveloped,whichcouldhandlethedustproblem,anditalsocanbeappliedtohightemperaturefluegasinmetallurgicalprocessingtododeepdustremovalandpurification.ThemethodofSEM,EDSareusedtocharacterizetheporousceramicsmatrixandmicroporouscompositemembrane,theresultsshowthattheyhavegoodporestructureandphysicalproperties.Asetofcoldmodeltestdevicetomeasurethedustfiltrationefficiencyofasymmetricceramiccompositemembranehasbeendesigned,andthereasonableparametershavebeendeterminedthroughexperiments.
Keywords:
asymmetricceramictubemembrane;dustremoval;hightemperaturefluegas
据国家环境保护部2010年中国环境状况公报统计,2010年我国烟尘排放量达830×104t,工业粉尘排放量达449×104t。
这些高温含尘气体的直接排放,不仅会造成严重的环境污染,还会造成大量热能的不必要浪费。
国外从20世纪70年代就开展了对高温气体除尘技术的开发研究工作。
早期,美国能源部开展以无机膜过滤介质为主的高温气体过滤除尘技术的开发,德、日、英等发达国家也都开展了类似的研究工作[1]。
上世纪90年代中期,高温气体除尘技术取得很大进展。
首先是一批先进的高性能无机膜过滤材料的开发为高温气体过滤除尘技术的工业化应用奠定了基础。
其次,高温除尘工艺技术的提高,如系统高温密封和过滤元件试样自保护密封技术,过滤元件试样再生技术,气体在线检测技术以及系统自动控制技术等,也都大大推动了高温气体过滤除尘技术的工业化应用[2-3]。
许多国家都开展了对高温陶瓷过滤材料技术研究工作,其中包括过滤管材质选择、结构设计、成型和制备工艺、高温性能和高温相结构、过滤管的综合性能测试和技术评价及经济可靠性分析等。
国外如德国Schumacher公司生产的SiC-A12O3双层试管式滤管,表层孔径为10~20μm,耐温达1000℃[4]。
美国CeraMem公司研制的多孔陶瓷膜过滤器,其面积/体积比达到500m2/m3,可直接安装在烟气道中滤去99%的烟尘[5]。
美国西屋公司开发的交叉流式无机膜过滤器,在加利福尼亚Montebelfo的Texaco汽化炉上做了8000h的示范实验,该气化炉的工作压力为1.0~3.0MPa,气体温度为650~900℃[6],结果表明交叉流式过滤器极易在角部断裂并在过滤体中形成纵向裂缝。
美国DupuntLanxide公司生产的PRD-66型试管式陶瓷过滤器外表面涂有炭化硅砂粒的强化尼龙纤维丝缠绕,内表面是渗透率较高的炭化硅刚性能架,除尘效率达99%以上。
日本研制的蜂房式过滤器一般由多铝红柱石或堇青石制成,除尘效率达99%,耐温400℃。
日本Asahi公司生产的均质堇青石陶瓷滤管,孔径为40~60μm,耐温达1000℃,抗热冲击性较好[7-8]。
目前国内冶金行业各种对烟气粉尘过滤技术和装置,不具备针对细颗粒的高效捕集能力。
随着我国提高大气环境质量工作的推进,研究开发高效捕集烧结烟气中颗粒可以有效缓解冶金行业所面临的环保危机,同时也能够大幅度提高空气环境质量。
微孔陶瓷除尘器具有耐高温、耐腐蚀、耐清洗、机械强度大、结构稳定不变形和寿命长等突出优点,因而被认为是热粒子过滤材料的最佳选择。
本文提出将SiC、Al2O3等原料静压成型后烧制成多孔陶瓷基体,再通过多次浸浆,干燥达到所需要的膜厚度后,采用高温喷涂,制成非对称陶瓷复合膜管的新工艺技术。
然后,研发出能够处理高温烟气微孔陶瓷管复合膜除尘器,应用到冶金高温烟气中进行深度除尘和净化。
采用了SEM、EDS等手段对多孔陶瓷基体和微孔复合膜进行表征,结果表明其具有良好的微孔结构和物理性质。
1微孔陶瓷过滤管膜结构及生产制备
1.1微孔陶瓷过滤管膜结构
微孔陶瓷除尘器的核心部件是微孔陶瓷过滤管,这种多孔过滤材料采用SiC、海鲍石、氧化铝、氧化锆和稀土等原料按照一定的配比,在一定的温度下烧制而成,适应于高温高压且粉尘颗粒大于0.5μm的烟气。
其突出特点是具有优良的热和化学稳定性,工作温度可高达1000℃,耐压≤2.5MPa,并且在氧化还原等高温环境下具有很好的抗腐蚀性。
可去除高温烟尘中的99.5%以上的尘粒,净化的气体所含粒子载荷小于5mg/Nm3,符合国定规定的环保排放标准。
对于微滤膜,单层或多层陶瓷膜淀积在管状或平板状多孔支撑体上,形成了在垂直于支称体表面切面方向上孔径渐小的微结构,即所谓的孔梯度结构[9-11]。
支撑体的主要作用是为整个系统提供足够的机械强度,使陶瓷膜在具体分离应用中能够承受一定的压力梯度[12-13],为了保证低的渗透阻力,必然要求支撑体具有大的孔径、高的开孔隙率和渗透通量。
微孔陶瓷膜过滤管采用三层结构,内层为平均孔径较大的支撑膜,确保过滤管的强度,在支撑膜的外表面加上一层平均粒径较小的分离膜,以实现固体颗粒的表面过滤,中间为过渡连接层,确保支撑基体和表面膜的良好连接,见图1。
这种不对称的孔径成梯度变化的多层结构,就是其与传统的多孔陶瓷的不同之处。
形成微孔孔径梯度变化的目的是减少过滤时的压力损失,真正起过滤分离作用的是表面膜层。
这种多层的陶瓷功能膜过滤管就把深层过滤变成了表层过滤,在保证过滤精度的前提下,使得过滤阻力显著降低,孔径进一步减小,抗热震性也得到加强。
微孔陶瓷过滤管膜生产采用两步法,第一步采用等静压技术成形后,在约1400℃(Al2O3)或1850℃(SiC)下烧成管状微孔陶瓷支撑体,第二步首先制备Al2O3或SiC悬浮液,然后把微孔陶瓷过滤支撑体浸入悬浮液中,在毛细管力和粘性力的作用下形成涂层,经过浸浆,干燥烧结后得到多孔表面膜,通过反复浸浆,干燥达到所需要的膜厚度后,再采用等离子体技术进行高温喷涂,制成非对称陶瓷复合膜管(SiC/Al2O3,本文称为Al2O3陶瓷复合膜和Al2O3/SiC,本文称为SiC陶瓷复合膜)。
图1非对称陶瓷膜管的结构模型示意图
1.2微孔陶瓷过滤管支撑基体的制备
根据设计的理论模型,要求支撑体层必须具有足够的机械强度和较高的孔隙率及较大的孔径,为此在配方选材上经过上千次的试验,确定选用刚玉砂为主要骨料,因为刚玉砂本身是经过1700℃高温煅烧的,其结构相当稳定,选用玻璃粉作低温度下熔剂,选用具有低膨胀系数的锂云母,滑石及少量高活性的稀土镧系元素作高温复合粘结剂,该高温熔剂不仅能提高支撑体的机械强度,还具有很好的热稳定性。
首先对碳化硅、氧化铝、氧化锆、稀土等添加剂原料进行预烧结和粉碎成颗粒后过筛,获得不同颗粒等级的骨料,加入造孔剂和粘结剂,等静压成型后烧成管状微孔陶瓷过滤基体,工艺流程见图2。
图2微孔陶瓷基体制备技术路线图
球磨时将各种原料分别装入球磨罐中干法球磨120min,料球比为1:
2。
为保证坯体在干燥过程中不变形、不开裂,实验中采用室温干燥的方法,干燥时间为1d。
造孔剂颗粒越大,颗粒堆积越疏松,越易于在烧成过程中留下更多空隙,就越利于滤料气孔率的提高[14-16]。
因此,实验中骨料和造孔剂采用不同的级配。
实验中采用常压烧结法[17],颗粒越细、比表面积就越大、表面能及界面能就越高、烧结活性也就越大,烧成温度因而也能够相对降低,本研究氧化铝陶瓷烧结温度为1400℃,碳化硅陶瓷为1850℃,烧结时间45min。
1.3非对称陶瓷膜的制备
采用浸浆方法制备微孔陶瓷过滤管的表面覆膜。
首先制备莫来石悬浮液(主要由粉料、溶剂、分散剂、粘结剂和增塑剂组成),然后把微孔陶瓷过滤基体浸入悬浮液中,在毛细管力和粘性力的作用下形成涂层,经过浸浆,干燥烧结后得到多孔表面膜,通过反复浸浆,干燥达到所需要的膜厚度后,再采用等离子体技术进行高温喷涂,制成非对称陶瓷过滤管膜。
具体工艺路线如图3所示。
图3膜制备工艺技术路线图
粉料主要是以一定粒径的a-Al2O3为骨料,添加一定量的复合熔剂配制而成。
为了进一步掌握颗粒大小及颗粒级配与产品技术性能的关系,做了一系列正交试验,由试验结果得出,粉料的粒径与膜孔径的关系在2.5~3倍之间,即制作1~2μm的微孔膜其粉料粒径应控制在2.5~6μm的范围。
选择膨胀系数较低的锂云母,滑石及少量的有较高活性的镧系元素,通过试验其用量控制在5%~8%。
膜的浸涂过程是制膜过程中的重要环节,关系到膜的厚度及其均匀性和膜的完整性。
在多孔支撑体上浸涂膜通常利用两种机理:
毛细过滤和薄膜形成机理。
通过试验,发现仅仅是毛细过滤机理形成的膜强度好,但孔隙率和孔径均匀性差,仅仅是薄膜机理形成的膜,膜的孔隙率和孔径均匀性好,但膜的机械强度和热稳定性较差。
所以先将多孔支撑体预处理,消除一部分毛细管力,同时利用两种机理涂膜。
浸涂好膜后的陶瓷膜过滤管经干燥后,再利用等离子高温热喷涂。
2微孔陶瓷管膜的表征
2.1Al2O3陶瓷和Al2O3多孔陶瓷复合膜的SEM与EDS分析
Al2O3多孔陶瓷及Al2O3多孔陶瓷复合膜的微观形貌如图4所示,(a)是50倍下Al2O3多孔陶瓷,(b)是50倍下Al2O3多孔陶瓷复合膜支撑体,(c)是50倍下Al2O3多孔陶瓷复合膜支撑体与膜连接处,(d)是200倍下Al2O3多孔陶瓷膜表面。
从图4中看出Al2O3多孔陶瓷由直径数百微米的球状颗粒堆积而成,其截面存在大量的三维贯通孔洞且为宏观孔洞,孔径大约为100~200μm,形状不规则,这些主要是颗粒堆积所形成的。
同时表面有形状规则的微观孔洞,且为闭合孔,孔径大约为十到几十微米之间,这些孔洞的来源大部分是造孔剂燃尽留下的孔洞。
Al2O3多孔陶瓷复合膜表面则由直径数微米到数十微米的不规则颗粒堆积而成,从图4中可看出孔径大约为5~15μm,孔径分布窄,而孔径分布越窄,膜的抗堵塞性能越好,从而有效地减少膜污染,提高膜的分离效率和分离效果。
Al2O3多孔陶瓷复合膜SiC膜层厚约为100μm左右,Al2O3多孔陶瓷复合膜与支撑体连接良好。
图4Al2O3多孔陶瓷及Al2O3多孔陶瓷膜的微观形貌
从Al2O3多孔陶瓷EDS结果和表面Al元素分布可知,样品含有C,O,Mg,Al,Si,K,Ca,Fe等元素。
定量分析结果发现,Al元素占阳离子原子百分比达到90%以上,而其他阳离子的存在一方面是因为原料本身含有,另一方面是因为造孔剂、粘结剂等的加入所带来。
Al元素面分布分析发现Al分布较为均匀且多在球体上,也间接说明了造孔剂和粘结剂等的加入带来了其他阳离子。
从Al2O3多孔陶瓷复合膜支撑体EDS结果和表面Al元素分布可知,样品含有C,O,Mg,Al,Si,K,Ca,Fe等元素。
定量分析结果发现,Al元素占阳离子原子百分比达到90%以上,Si元素则达到了5%左右,而其他阳离子的存在一方面是因为原料本身含有,另一方面是因为造孔剂、粘结剂等的加入所带来。
Al元素面分布分析发现Al分布较为均匀且多在球体上,也间接说明了造孔剂和粘结剂等的加入带来了其他阳离子。
2.2SiC陶瓷和SiC多孔陶瓷复合膜的SEM与EDS分析
SiC多孔陶瓷及SiC多孔陶瓷复合膜的微观形貌如图5所示,(a)是50倍下SiC多孔陶瓷,(b)是50倍下SiC多孔陶瓷复合膜支撑体,(c)是50倍下SiC多孔陶瓷复合膜支撑体与膜连接处,(d)是300倍下SiC多孔陶瓷复合膜表面。
从图5中看出SiC多孔陶瓷由直径数百微米的不规则颗粒堆积而成,其截面存在大量的三维贯通孔洞且为宏观孔洞,孔径大约为50~100μm,形状不规则,这些主要是颗粒堆积所形成的。
同时表面有形状规则的微观孔洞,且为闭合孔,孔径大约为十到几十微米之间,这些孔洞的来源大部分是造孔剂燃尽留下的孔洞。
SiC多孔陶瓷复合膜表面则由直径数微米到数十微米的不规则颗粒堆积而成,由图5知孔径大约为5~15μm,孔径分布窄。
SiC多孔陶瓷复合膜Al2O3膜层厚约为80~100μm,Al2O3多孔陶瓷复合膜与支撑体连接良好。
图5SiC多孔陶瓷及SiC多孔陶瓷复合膜的微观形貌
SiC多孔陶瓷EDS结果和表面Si元素分布可知,样品含有C,O,Al,Si,K,Ca,Fe等元素。
定量分析结果发现,Si元素占阳离子原子百分比达到90%以上,而其他阳离子的存在一方面是因为原料本身含有,另一方面是因为造孔剂、粘结剂等的加入所带来。
Si元素面分布分析发现Si分布较为均匀。
SiC多孔陶瓷复合膜支撑体与膜连接处EDS结果和表面Si元素分布可知,样品含有C,O,Al,Si,K,Ca,Fe等元素。
定量分析结果发现,Si元素占阳离子原子百分比达到90%以上,Al元素则达到了5%左右,而其他阳离子的存在一方面是因为原料本身含有的,另一方面是因为造孔剂、粘结剂等的加入所带来,同时由于膜层较薄,对于总体Si元素含量影响不大。
Al元素面分布分析发现Al分布较为均匀且多在SiC颗粒上,膜上的分布较少,一方面说明了造孔剂和粘结剂等的加入带来了其他阳离子,另一方面也说明了Al2O3膜上有较少的Si元素,只有较少的喷涂过程中混熔的一些Si元素。
2.3陶瓷膜的孔隙率计算
采用BX51M型金相显微镜测孔隙率,100倍视野下SiC陶瓷(左)和Al2O3陶瓷(右)的金相显微镜图见图6,实验测得的孔隙率结果见表2。
图6100倍视野下SiC陶瓷(左)和Al2O3陶瓷(右)的金相显微镜图
由表1知,Al2O3陶瓷和Al2O3陶瓷复合膜的孔隙率要略低于SiC陶瓷和SiC陶瓷复合膜,是因为SiC熔点较高,烧结时流动性没有Al2O3好,粘结程度略低于Al2O3,因此成品孔隙率略高于Al2O3。
总体来看,所有成品陶瓷以及陶瓷复合膜的孔隙率都超过了30%,陶瓷管膜孔径大小在5~15μm,完全可以满足高温烟气过滤的净化过程。
表1样品孔隙率测定结果
样品
SiC陶瓷
SiC陶瓷复合膜
Al2O3陶瓷
Al2O3陶瓷复合膜
孔隙率/%
38.2%~40.7%
39.5%~43.2%
32.2%~37.4%
35.5%~36.5%
3微孔陶瓷管膜过滤性能的冷态模拟
根据高温陶瓷过滤器的运行和控制原理,设计了一套冷态模拟实验装置(如图7所示),实验采用的主要设备由动力系统、加料系统、过滤器系统、脉冲反吹系统、流量计、颗粒物分析仪和压差计等构成。
实验采用的工艺流程:
空气经粉尘加料器加入一定量的固体杂质粒子后形成一定浓度的含尘气体,然后通过高压风机进入过滤系统的过滤室中,经过高温陶瓷过滤管过滤后的洁净气体排入大气。
当过滤进行一段时间后,陶瓷过滤管外表面上灰尘滤饼增厚,过滤阻力增加,这时开启脉冲电磁阀将高压气体反向通入陶瓷过滤管,以清除陶瓷过滤管外表面积沉的灰饼,使陶瓷过滤管清洗再生,继续进行过滤,聚积到过滤室底部的灰饼,经由底部闸阀定期排除。
实验过程中压力降采用压差计控制和测量,过滤流量采用流量计测定,过滤前后的粉尘浓度采用颗粒物测定仪测定。
1:
动力系统;2:
加料系统;3:
颗粒物分析仪;4:
流量计;5:
脉冲反吹系统;6:
压差计;7:
陶瓷管复合膜;8:
过滤系统;9:
排气口
图7陶瓷过滤管的冷态除尘模拟实验装置图
实验结果表明,孔径较小非对称陶瓷管复合膜材料的渗透率比均质多孔陶瓷材料小,但是减少的不多,主要是因为膜层厚度只有100μm左右,相对于支撑体厚度小得多。
因此,陶瓷管复合膜材料的渗透率下降的不多,说明其具有较好的渗透率以及过滤阻力小等优点。
随时间的延长,膜表面及膜孔被不断污染和堵塞,使粉尘的传递增加了新的阻力,渗透率随之降低。
此外还可看出,粉尘浓度较低时,本研究制备的非对称陶瓷管复合膜具有较高的渗透率,并且随着过滤时间的推移,渗透率基本保持不变,说明膜孔径基本没有发生堵塞现象。
在过滤速度3.0cm/s、粉尘浓度2.5g/Nm3左右的条件下,随着过滤时间的延长,Al2O3陶瓷管复合膜和SiC陶瓷管复合膜的过滤阻力逐渐增大,但是增大的趋势很缓慢,25min内过滤阻力不超过1000Pa,说明在粉尘浓度不大的条件下非对称陶瓷管复合膜具有较好的透气性能。
当粉尘浓度增加时,随着过滤时间的延长,各过滤管过滤阻力均有不同程度的提高,并且过滤阻力的增大明显加快。
由于Al2O3陶瓷管复合膜的渗透率比SiC陶瓷管复合膜大,因此,条件相当的情况下,Al2O3陶瓷管复合膜的过滤阻力会更小。
当含尘气体中粉尘含量越大,陶瓷管复合膜对粉尘的过滤效率越高;Al2O3陶瓷管复合膜和SiC陶瓷管复合膜在不同操作条件下对实验气体中的粉尘粒子都具有非常好的去除效果,其粉尘过滤效率均达到98%以上,最高可达到99.8%以上。
从实验结果可以看出,本项目研究的陶瓷管复合膜管用于含尘气体净化具有非常好的再生效果,在粉尘浓度不超过10.0g/Nm3时,经过短暂周期循环后,其初始压降始终维持在一个较小的压力范围,且反吹周期内的最高压降也始终小于2000Pa。
这一试验结果表明:
非对称陶瓷管复合膜在该工艺操作条件下可以满足长周期稳定运行的条件。
由于非对称陶瓷管复合膜从分离膜层到多孔陶瓷支撑体,其孔径由小逐渐增大,这样一旦粉尘微粒穿过表面陶瓷过滤膜层后,也能通过多孔陶瓷支撑体,减少了非对称陶瓷管复合膜被堵塞的机率,延长了非对称陶瓷管复合膜的使用寿命。
而且,当非对称陶瓷管复合膜再生时,从多孔陶瓷支撑体、过渡层到分离膜层,孔径由大逐渐变小,有利于非对称陶瓷管复合膜的清洗再生。
4微孔陶瓷管膜除尘器的应用
微孔陶瓷管膜除尘器主要由微孔陶瓷过滤管膜、自动控制系统及钢结构三部份组成,具体除尘器装备结构图见图8。
研制不同烟气流量条件下微孔陶瓷管膜除尘器高效除尘的结构优化,控制除尘器阻力,使之可适用于不同类型、不同烟气量和不同含尘量的有色金属与冶金窑炉冶炼行业。
微孔陶瓷除尘器包括支架、检修孔上箱体、烟气入口、净气出口、灰斗、灰斗下面的螺旋输送机及排尘阀、排尘阀下面的排灰口等,其特征在于,在上箱体内装有80~800根孔径为0.5~50μm的微孔陶瓷过滤管,微孔陶瓷过滤管下方与烟气入口连通,微孔陶瓷过滤管的上方与净气出口连通。
使用微孔陶瓷过滤管过滤,具有除尘效率高、耐高温高湿、容易清洗、耐腐蚀、安装方便、使用寿命长等优点。
开发基于微孔陶瓷管膜除尘技术的过程控制程序使之既能现场控制又能远程控制,并开发工程化仿真系统,以确保新技术推广过程中的标准化操作和培训,加速新技术推广应用。
特别是核心部件微孔陶瓷过滤管膜可根据介质的情况进行制作,反冲容易,再生速度较快,节省了清灰能耗和延长了微孔陶瓷过滤管膜的使用寿命。
并采用硫化器取代传统的震动器,显著节约运行能源,减少设备的机械震动,提高了设备的可靠性,反冲清灰的效果也更加明显,有效防止了粉尘滞留,解决了烟气中含较多低熔点烟尘微粒高温下极易粘结的问题。
利用微孔陶瓷管膜除尘器的优点,通过处理粉尘收集技术与余热利用回收耦合技术,从高温烟气余能的本征特性出发,通过改性提升余热品质,最终实现除尘与高温余热高效转化一体化的目标。
图8除尘器装备结构图
5结论
(1)微孔陶瓷膜过滤管采用不对称的孔径成梯度变化的三层结构,内层为平均孔径较大的支撑膜,中间为过渡连接层,确保支撑基体和表面膜的良好连接,外层是真正起过滤分离作用的表面膜层。
(2)提出了将SiC、Al2O3等原料等静压成型后烧制成多孔陶瓷基体,再通过多次浸浆,干燥达到所需要的膜厚度后,采用高温喷涂,制成非对称陶瓷复合膜管的新工艺技术。
(3)通过SEM表征发现Al2O3多孔陶瓷孔径大约为100~150μm,形状不规则Al2O3多孔陶瓷复合膜孔径大约为5~15μm,Al2O3多孔陶瓷复合膜SiC膜层厚约为100μm左右,Al2O3多孔陶瓷复合膜与支撑体连接良好。
SiC多孔陶瓷孔径大约为50~200μm