年产100万吨连铸坯的全连铸转炉炼钢车间工艺的设计.docx
《年产100万吨连铸坯的全连铸转炉炼钢车间工艺的设计.docx》由会员分享,可在线阅读,更多相关《年产100万吨连铸坯的全连铸转炉炼钢车间工艺的设计.docx(93页珍藏版)》请在冰豆网上搜索。
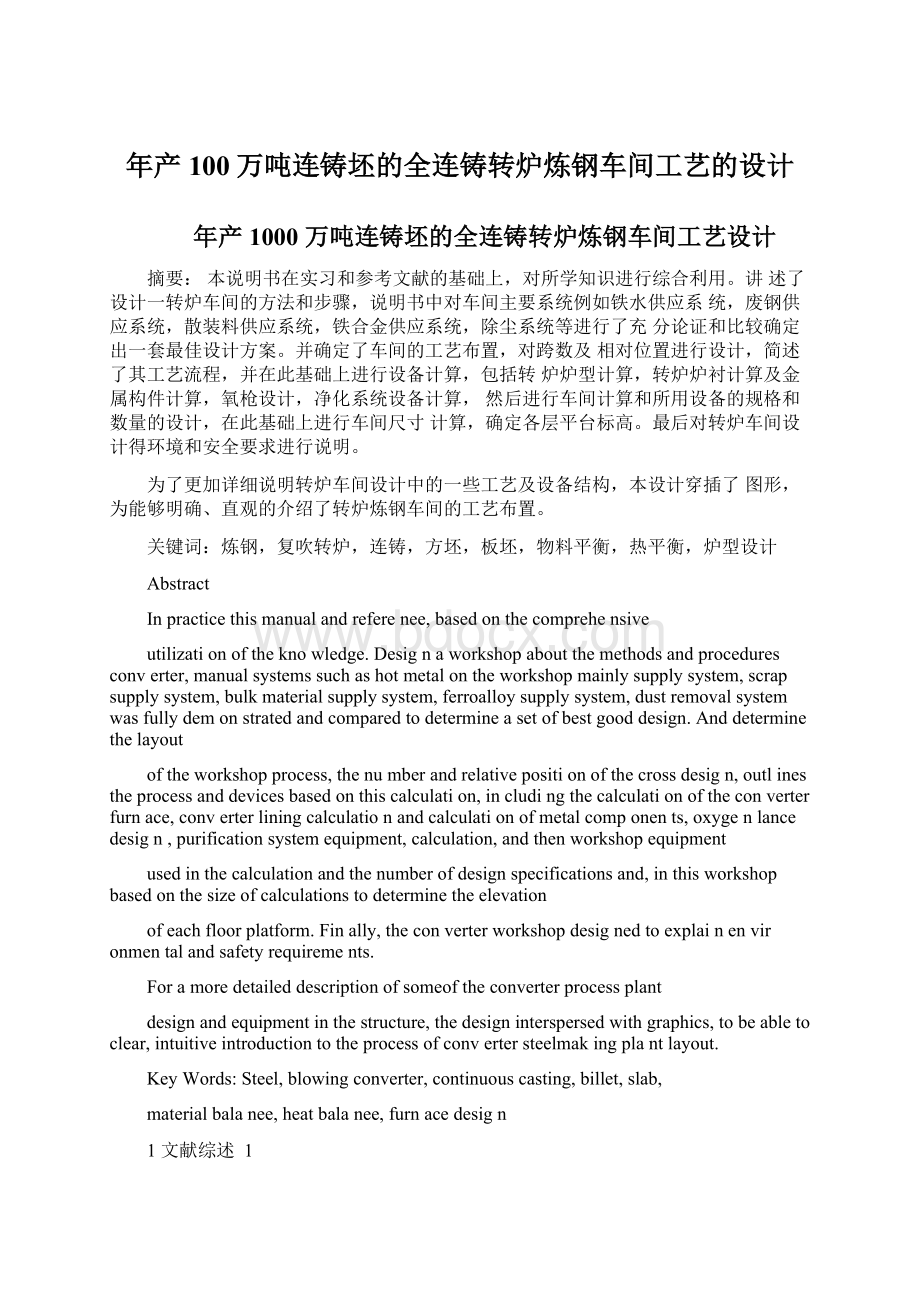
年产100万吨连铸坯的全连铸转炉炼钢车间工艺的设计
年产1000万吨连铸坯的全连铸转炉炼钢车间工艺设计
摘要:
本说明书在实习和参考文献的基础上,对所学知识进行综合利用。
讲述了设计一转炉车间的方法和步骤,说明书中对车间主要系统例如铁水供应系统,废钢供应系统,散装料供应系统,铁合金供应系统,除尘系统等进行了充分论证和比较确定出一套最佳设计方案。
并确定了车间的工艺布置,对跨数及相对位置进行设计,简述了其工艺流程,并在此基础上进行设备计算,包括转炉炉型计算,转炉炉衬计算及金属构件计算,氧枪设计,净化系统设备计算,然后进行车间计算和所用设备的规格和数量的设计,在此基础上进行车间尺寸计算,确定各层平台标高。
最后对转炉车间设计得环境和安全要求进行说明。
为了更加详细说明转炉车间设计中的一些工艺及设备结构,本设计穿插了图形,为能够明确、直观的介绍了转炉炼钢车间的工艺布置。
关键词:
炼钢,复吹转炉,连铸,方坯,板坯,物料平衡,热平衡,炉型设计
Abstract
Inpracticethismanualandreferenee,basedonthecomprehensive
utilizationoftheknowledge.Designaworkshopaboutthemethodsandproceduresconverter,manualsystemssuchashotmetalontheworkshopmainlysupplysystem,scrapsupplysystem,bulkmaterialsupplysystem,ferroalloysupplysystem,dustremovalsystemwasfullydemonstratedandcomparedtodetermineasetofbestgooddesign.Anddeterminethelayout
oftheworkshopprocess,thenumberandrelativepositionofthecrossdesign,outlinestheprocessanddevicesbasedonthiscalculation,includingthecalculationoftheconverterfurnace,converterliningcalculationandcalculationofmetalcomponents,oxygenlancedesign,purificationsystemequipment,calculation,andthenworkshopequipment
usedinthecalculationandthenumberofdesignspecificationsand,inthisworkshopbasedonthesizeofcalculationstodeterminetheelevation
ofeachfloorplatform.Finally,theconverterworkshopdesignedtoexplainenvironmentalandsafetyrequirements.
Foramoredetaileddescriptionofsomeoftheconverterprocessplant
designandequipmentinthestructure,thedesigninterspersedwithgraphics,tobeabletoclear,intuitiveintroductiontotheprocessofconvertersteelmakingplantlayout.
KeyWords:
Steel,blowingconverter,continuouscasting,billet,slab,
materialbalanee,heatbalanee,furnacedesign
1文献综述1
1.1国外炼钢技术的发展1
1.2钢铁工业在国民经济中的地位和作用2
1.3现代转炉炼钢工艺流程3
1.4我国氧气转炉炼钢技术展望4
1.4.1转炉大型化和流程优化4
1.4.2转炉高效化4
1.4.3钢水洁净化5
1.4.4控制模型化5
1.4.5资源综合利用化6
1.5现代转炉炼钢技术存在的问题6
2转炉炼钢厂设计方案7
2.1转炉车间组成7
2.2转炉座数、容量和车间生产能力的确定7
2.2.1转炉座数7
2.2.2车间生产能力的确定7
2.3主要钢种的选择9
2.4工艺流程9
2.5原料方案10
2.5.1铁水的供应10
2.5.2废钢的供应10
2.5.3散装料的供应11
2.5.4铁合金的供应12
2.6主厂房工艺布置12
2.6.1原料跨的布置12
2.6.2炉子跨的布置13
2.6.3精炼跨的布置14
3物料平衡与热平衡计算15
3.1物料平衡15
3.1.1计算所需原始数据15
3.1.2物料平衡基本项目16
3.1.3计算步骤16
3.2热平衡计算25
3.2.1计算所需原始数据25
3.2.2计算步骤26
4顶底复吹转炉炉型设计31
4.1炉型选择31
4.2原始条件31
4.3主要参数的确定32
4.4炉衬各层填充材料选择36
5生产工艺设计37
5.1炼钢原料37
5.1.1铁水37
5.1.2废钢37
5.1.3铁合金37
5.1.4石灰38
5.1.5萤石38
5.1.6生白云石38
5.1.7其他38
5.2装料制度39
5.3供氧制度39
5.3.1转炉炉膛内氧气射流的特性39
5.3.2氧气射流对转炉熔池的作用40
5.3.3顶吹氧气转炉的氧枪操作41
5.4造渣制度41
5.4.1炉渣碱度的控制与石灰加入量的确定41
5.4.2影响石灰熔解速度的因素42
5.4.3炉渣粘度的控制42
5.4.4炉渣氧化性的控制43
5.4.5泡沫渣及其控制44
5.4.6放渣及留渣操作45
5.5温度制度45
5.5.1出钢温度的确定45
5.5.2冷却剂及其加入量的确定46
5.6终点控制和出钢48
5.7脱氧制度和合金化48
5.7.1顶吹氧气转炉炼钢的脱氧方法48
5.7.2合金化的一般原理49
6转炉炉体金属构件设计51
6.1炉壳设计51
6.2支撑装置设计51
6.3倾动机构的设计53
7氧气转炉供氧系统设计54
7.1氧气的供应54
7.1.1转炉炼钢车间需氧量计算54
7.1.2制氧机能力的选择55
7.2氧枪设计55
7.2.1喷头类型与选择55
7.2.2喷头设计55
7.3氧枪枪身设计57
7.3.1枪身各层尺寸的确定57
7.3.2氧枪长度的确定59
7.4转炉底部供气构件设计59
7.4.1底气种类59
7.4.2底气用量59
7.4.3供气构件60
7.4.4底吹元件布置60
8转炉车间烟气净化与回收61
8.1转炉烟气与烟尘61
8.1.1烟气的特征61
8.1.2烟尘的特征61
8.2烟气净化方案选择62
8.2.1炉口附近烟气处理方法62
8.2.2转炉烟气净化方法62
8.3烟气净化系统63
8.4烟气净化回收系统主要设备63
8.4.1烟罩63
8.4.2静电除尘器64
8.4.3煤气柜64
车间主要设备的选择66
9.1原料跨66
9.1.1混铁车的设计66
9.1.2废钢料斗的计算68
9.2转炉跨68
9.2.1钢包68
9.2.2渣罐数量的确定69
9.3精炼跨70
9.4连铸跨71
941板坯的生产:
(尺寸为170mM1500mm)71
942方坯的生产:
(尺寸为150mM150mm)74
9.4.3其它工艺参数的确定76
9.4.4中间包主要工艺参数的确定76
9.4.5结晶器的有关参数77
9.4.6车间起重机的选择78
10主厂房工艺布置79
10.1原料跨间的布置79
10.2转炉跨间的布置82
10.2.1炉子跨的布置82
10.2.2转炉跨各平台的确定84
10.3连铸设备的布置89
11总劳动定员表93
1炼钢工序93
2连铸工序94
3燃气95
4给排水95
5热力96
6通风96
7电气96
8精炼工序96
9机修97
10检化室97
12主要技术经济指标98
致谢99
1文献综述
1.1国外炼钢技术的发展
世界近代炼钢工业首先诞生于欧洲,机器的大量发明和广泛应用,是炼钢成为最基本的工业材料,对钢铁的数量和质量的需求越来越高。
首先公布转炉炼钢法的是英国发明家亨利•贝塞麦,1965年,亨利•贝塞麦在英国科学协会发表演讲,宣布其发明了底吹酸性空气转炉炼钢法,也因此此法生产率高、成本低的炼钢方法,成为冶金史上的一大创举,从此开创了大规模炼钢的新时代。
回顾氧气转炉炼钢的发展,可分为以下三个时期。
(1)转炉大型化时期(1950~1970):
以转炉大型化技术为核心,逐步完善了转炉炼钢工艺和设备。
先后开发出大型化转炉设计技术、0G法除尘与煤气回收技术、计算机静态与副枪动态控制技术、镁碳砖综合砌筑与喷补挂渣等护炉工艺技术。
(2)转炉复合吹炼时期(1970~1990):
这一时期,由于连铸技术的迅速发展,出现了全连铸的炼钢车间。
对转炉炼钢的稳定性和终点控制的准确性提出了更高的要求。
为了改善转炉吹炼后期钢-渣反应远离平衡,实现稳定吹炼的目标,综合顶吹、底吹转炉的优点,研究开发出各种顶低复合吹炼工艺技术,在世界上迅速推广
(3)转炉综合优化时期(1990年以后):
在这一时期,由于社会对纯净钢
的生产需求日益增加。
迫切需要建立起一种全新的、能大规模廉价生产纯净钢的生产体制。
围绕纯净钢生产,研究开发出铁水“三脱”预处理、高效转炉生产、全自动吹炼控制与溅渣护炉等重大新工艺技术。
降低了生产成本、大幅提高了生产效率。
1.2钢铁工业在国民经济中的地位和作用
钢铁工业是国民经济的支柱产业,是国民经济中的主导产业。
而钢铁材料是用途最广泛的金属材料,人类使用的金属中,钢铁占90%以上。
人们生活离不开钢铁,人们从事生产或其他活动所用的工具和设施也都要使用钢铁材料。
钢铁产量往往是衡量一个国家工业化水平和生产能力的重要标志,钢铁的质量和品种对国民经济的其他工业部门产品的质量,都有着极大的影响。
世界经济发展到今天,钢铁作为最重要的基础材料之一的地位依然未受到根本性的影响,而且,在可预见的范围内,这个地位也不会因世界新技术和新材料的进步而消弱。
纵观世界主要发达国家的经济发展史,不难看出钢铁材料工业的发展在美国、前苏联、日本、英国、德国、法国等国家的经济发展中都起到了决定性作用。
这些国家和地区钢铁工业的迅速发展和壮大对于推动其汽车、造船、机械、电器等工业的发展和经济的腾飞都发挥了至关重要的作用。
美国钢铁工业曾在20世纪70-80年代遭到来自日本为主的国外进口材料的冲击而受到重创,钢铁产品生产能力急剧下降,但经过十几年的改造和重建,终于在20世纪90年代中期恢复到其原有的钢铁生产规模,为其维持世界强国地位继续发挥着重要作用。
由此可见钢铁工业在国民经济的重要作用,并且钢铁工业在整个国家的发展中都起着举足轻重的作用。
1.3现代转炉炼钢工艺流程
现在钢铁联合企业是一个庞大而复杂的综合生产部门。
在这个钢铁联合企业中,钢铁材料的生产包括采矿、选矿、烧结(球团)、焦化、炼铁、炼钢和各种轧钢等过程。
由于各种钢材质量主要决定于炼钢工艺过程和设备,所以炼钢成为钢铁工业生产流程中的中心环节。
目前主要的炼钢方式是转炉炼钢,我国现在转炉钢占总钢产量的比例已经超过80%,并接近90%。
过去钢铁冶炼的工艺流程基本是铁水一炼钢炉(转炉、电炉、平炉)T浇铸(模铸、连铸)-轧钢的模式,这样的模式由于缺少铁水的预处理、炉外精炼工艺,只能冶炼普通钢种,难以冶炼优质特种高性能钢材,平炉由于其炉渣碱度低,脱磷、脱硫效果差,限制了钢材质量的提高,随着工业和科学技术的发展,对钢材质量和性能提出了更高的要求,迫使人们开发冶炼更多品种的钢材,从而推动了炼钢技术的不断发展。
转炉冶炼采用铁水预处理、炉外精炼工艺后,钢的质量大大提高,转炉钢品种增加,转炉不仅能冶炼普通钢种,而且能冶炼高级优质钢种,甚至能冶炼包括不锈钢在内的特种钢,这为转炉炼钢的发展提供了广阔的空间
传统的钢水浇铸一直以模铸为主,不仅生产效率低、工人劳动强度大、车
间环境恶劣,而且金属损失大、回收率低、难以浇铸大型钢锭。
采用连铸后,
情况大为改观,生产效率和金属回收率大为提高,工人劳动强度降低,实现了浇铸过程的完全自动化,近十年中炼钢连铸比不断提高,许多大型钢铁企业均已实现了全连铸。
高炉一铁水预处理一转炉顶低复合吹炼一炉外精炼一连铸连轧,已成为大型现代化钢铁企业钢铁生产模式。
而高炉一铁水预处理一转炉顶低复合吹炼一RH真空精炼一连铸连轧-铸坯热送一直接轧制,则是现在转炉炼钢生产的最佳工艺流程。
1.4我国氧气转炉炼钢技术展望
1.4.1转炉大型化和流程优化
中国《钢铁产业发展政策》明确规定新建转炉必须>120t。
一方面将全力
推进转炉大型化的进程,加快淘汰落后的小转炉,另一方面则将更理性地研究转炉大型化的合理炉容问题。
段瑞钰院士呼吁研究钢铁联合企业各工序的界面技术,树立转炉设计动态有序地理顺衔接匹配关系,做到全流程优化的思路,反对各工序能力简单叠加的设计方法。
1.4.2转炉高效化
为了提高转炉作业率,减低生产成本,如何进一步缩短转炉冶炼周期一直
是各钢厂研究的课题。
其中,转炉采用“三脱”铁水少渣冶炼,纯吹炼时间可
以缩短3~5min,采用直接出钢技术可以缩短转炉停吹到出钢的镇静时间2~3min
日本住友金属和歌山新炼钢厂通过改造,铁水全部采用KR搅拌法脱硫,经过专用脱磷转炉进行全量铁水脱磷处理,然后,再到脱碳转炉进行脱碳升温。
脱磷转炉和脱碳转炉冶炼转炉只有20min,其中纯吹氧时间只有9min,2座公称容量210t脱碳转炉(2吹1)年产400万t以上,实现了转炉高效化。
1.4.3钢水洁净化
用户对钢材质量要求的不断提高促使炼钢技术的发展,其中纯净钢生产技
术越来越受到钢厂的重视。
宝钢从20世纪90年代初期就开始研究纯净钢生产技术,经过十几年开发,目前已拥有完善的纯净钢炼钢技术。
采用该技术生产的纯净管线钢和IF钢在不同阶段达到的纯净度水平在2004年进行的批量超纯净管线钢生产试验中S、P、ONH元素的总含量最小达到7110-6。
除了对钢
水杂质元素控制外,还要对钢水的夹杂物进行控制,特别是氧化物夹杂。
复吹转炉可以明显降低转炉终点游离氧含量,减少氧化物夹杂的生产。
因此,转炉复吹技术的开发和应用,对于从源头上减少夹杂物有着重要作用。
1.4.4控制模型化
中国钢铁产品的质量稳定性不够,其原因有很多,但转炉靠工人操作引起
波动大是其主要原因。
随着计算机技术的迅猛发展,炼钢模型的开发和利用不断进步。
目前,中国大部分转炉实现了模型控制。
转炉模型主要有转炉静态和动态模型、转炉自动吹炼模型、转炉合金模型等。
模型的应用对生产操作的稳定、提高劳动生产率、减少质量波动等起着促进作用。
因此,有必要继续优化、完善冶金模型,进一步提高模型控制精度,全面推进大、中型转炉的全自动不倒炉炼钢技术,进行智能型转炉炼钢。
1.4.5资源综合利用化
改变原有炼钢过程产生大量废弃物的概念,将炼钢过程产生的液态、固态和气态的物质定义为炼钢过程副产品加以利用。
1.5现代转炉炼钢技术存在的问题
现代转炉炼钢技术普遍存在的问题主要是随着社会对洁净钢的生产需求日益提高,迫切需要建立起一种全新的、能大规模廉价生产纯净钢的生产体系。
因此,如何降低生产成本、能耗,生产出大量的纯净钢以达到社会的需求是当前必须解决的问题。
2转炉炼钢厂设计方案
2.1转炉车间组成
现代氧气转炉炼钢车间一般由以下几个部分组成:
主厂房(包括炉子跨、原料跨、炉外精炼及钢包转运跨、浇铸系统各跨间);铁水预处理站及铁水倒罐间;废钢堆场与配料间;铁合金仓库及散装源料储存运输设施;中间渣场;耐火材料仓库;一、二次烟气净化设施及煤气回收设施;水处理设施;分析检测及计算机监控设施;备品备件库、机修间;生产必须的生活福利设施;水、电、气(氧气、氩气、氮气、压缩空气)等的供应设施。
车间的主要生产操作都集中在主厂房内进行,主厂房也包括原料跨、炉子跨和浇铸跨。
2.2转炉座数、容量和车间生产能力的确定
2.2.1转炉座数
转炉座数的确定与采用的吹炼制度有关,也与转炉的寿命有关。
由于现代的转炉炼钢都采用“溅渣护炉”操作,从而大大的提高了转炉的寿命,现代转炉寿命已经可以达到10.000~20.000炉,因此,本设计采用“三吹三”制度(即三个转炉都同时进行吹炼工作)完全能够保持生产的顺利进行。
2.2.2车间生产能力的确定
(1)计算年出钢炉数
每一座转炉的年出钢次数N为:
N1440365Ti
式中T1每炉钢的平均冶炼时间,min,参照表2-1,
本设计中取每炉钢平均冶炼时间为42min;
1440一天的时间换算为分钟,min/d;
365――一年的日历天数,d/a;
——转炉作业率,本设计取87%
则每一座转炉的年出钢次数N为:
N144036587%4210887(炉)
表2-1氧气转炉平均冶炼时间
—公称容积/t
15—
30
50—
100〜120
150
200
250
300
平均供氧时
12〜14
14〜15
15〜16
16〜18
18〜19
19〜20
20〜21
21~22
平均冶炼时
25〜28
28〜30
30〜33
33〜36
36〜38
38〜40
40〜42
42〜45
(2)计算转炉公称容量
转炉车间年产钢水量:
W=nNQ
式中:
W转炉车间年产钢水量;
n――车间经常吹炼炉子座数;
Q――转炉公称容量,t;
N——每一座转炉年出钢炉数;
n――连铸坯收得率,本设计取98%
因此,转炉公称容量为:
960000031088798%299.92(吨)
参照表2-2,本设计中取转炉公称容量为300吨。
采用“三吹三”制度不考虑转炉精炼收得率,验算连铸钢坯年产量:
W钢坯=31088730098%=9602712t>9600000t
所以,本设计所选转炉符合产量要求。
表2-2氧气转炉公称容量系列
转炉公称容量/t
20(15)
30
50
100
120
150
200
250
300
取大出钢量/t
30(20)
36
60
120
150
180
220
275
320
钢包容量/t
30(20)
40
60
120
150
180
220
275
320
浇铸吊车起重量/t
63/16
80/20
100/32
180/63/20
225/63/20
280/80/20
360/100/20
400/100/20
450/100/20
2.3主要钢种的选择
钢种:
普碳钢,低合金钢
产品规格:
方坯,板坯
2.4工艺流程
根据设计任务书的要求以及现代连铸技术的发展趋势,确定本设计方案的
基本工艺流程如图2-1所示
连诵坯
I钢旦回转呂|一~[KEh~「lf炉|一~}鶴炼詞旦1~
图2-1炼钢车间工艺流程图
2.5原料方案
2.5.1铁水的供应
铁水是转炉炼钢主要原料,高炉铁水采用混铁车运输,经预处理后转运兑
入转炉。
2.5.2废钢的供应
废钢主要靠外购,部分本厂返分废钢。
生铁本厂供给,作冷却剂加入
废钢要求:
(1)表面清洁少锈、无油污、无泥沙
(2)废钢中不得有铅、锡、砷等有色金属
(3)废钢中硫、磷含量要低
(4)外形尺寸要合格,不能过大
(5)废钢中不得有密封容器、易燃易爆物品和毒品
废钢管理要求:
(1)入场后,分类存放
(2)清除处理,清除油污、泥沙等杂质和有色金属、毒品
(3)使外形尺寸合格
炼钢车间,在原料跨一端单独设废钢间,按每炉需用量装入废钢,料斗送到炉前。
废钢一次一斗装入。
2.5.3散装料的供应
散装料包括:
石灰、白云石、萤石、铁矿石、焦炭等。
供应系统包括散装堆场,地下料仓,由地下料仓送往主厂房的运料设施,转炉上方高位料仓,称量和向转炉加料的设施。
为了保证转炉正常生产,应设散装料堆场,尽可能靠近转炉。
各种料储量按20天考虑。
在靠近主厂房附近设置地下料仓,它兼有部分储存和转运作用。
地下料仓为地下式,便于火车或汽车或运输带自动卸料。
地下料仓量按3天考虑。
从地下料仓向高位仓供料采用全胶带运输。
往各高位料仓布料采用可逆活动胶带运输机。
运输能力按每日工作一个班(约7h)考虑。
设置高位料仓起临时储料的作用,并利用重力方式向转炉及时可靠的供料,保证转炉正常生产。
高位料仓沿炉子跨纵向布置,三座转炉共用一套高位料仓,这样可以相互支持供料,并避免由于转炉停炉后料仓内剩余石灰的粉化。
散装料的用途如下:
(1)石灰:
主要是造渣材料。
石灰极易潮湿,故在入炉前须烘烤,以提高石灰的活性,有利于冶炼。
(2)萤石:
用于稀释炉渣,提高炉渣的活性。
(3)白云石:
用于提高炉渣的碱度,减小对炉衬的侵蚀。
(4)铁矿石:
用作冷却剂。
2.5.4铁合金的供应铁合金的供应一般由炼钢厂的铁合金车间,铁合金料仓及称量和输送设施等几部分组成。
铁合金主要用来调整钢液的成分、温度并进行合金化处理。
其主要作用如下:
(1)硅铁:
用于合金化,也作脱氧剂。
(2)锰铁:
用于合金化,也作脱氧剂。
根据碳含量可分为中碳、低碳、高碳锰铁,锰铁中碳含量越低,磷含量越低