散热器风扇气动噪声仿真研究.docx
《散热器风扇气动噪声仿真研究.docx》由会员分享,可在线阅读,更多相关《散热器风扇气动噪声仿真研究.docx(13页珍藏版)》请在冰豆网上搜索。
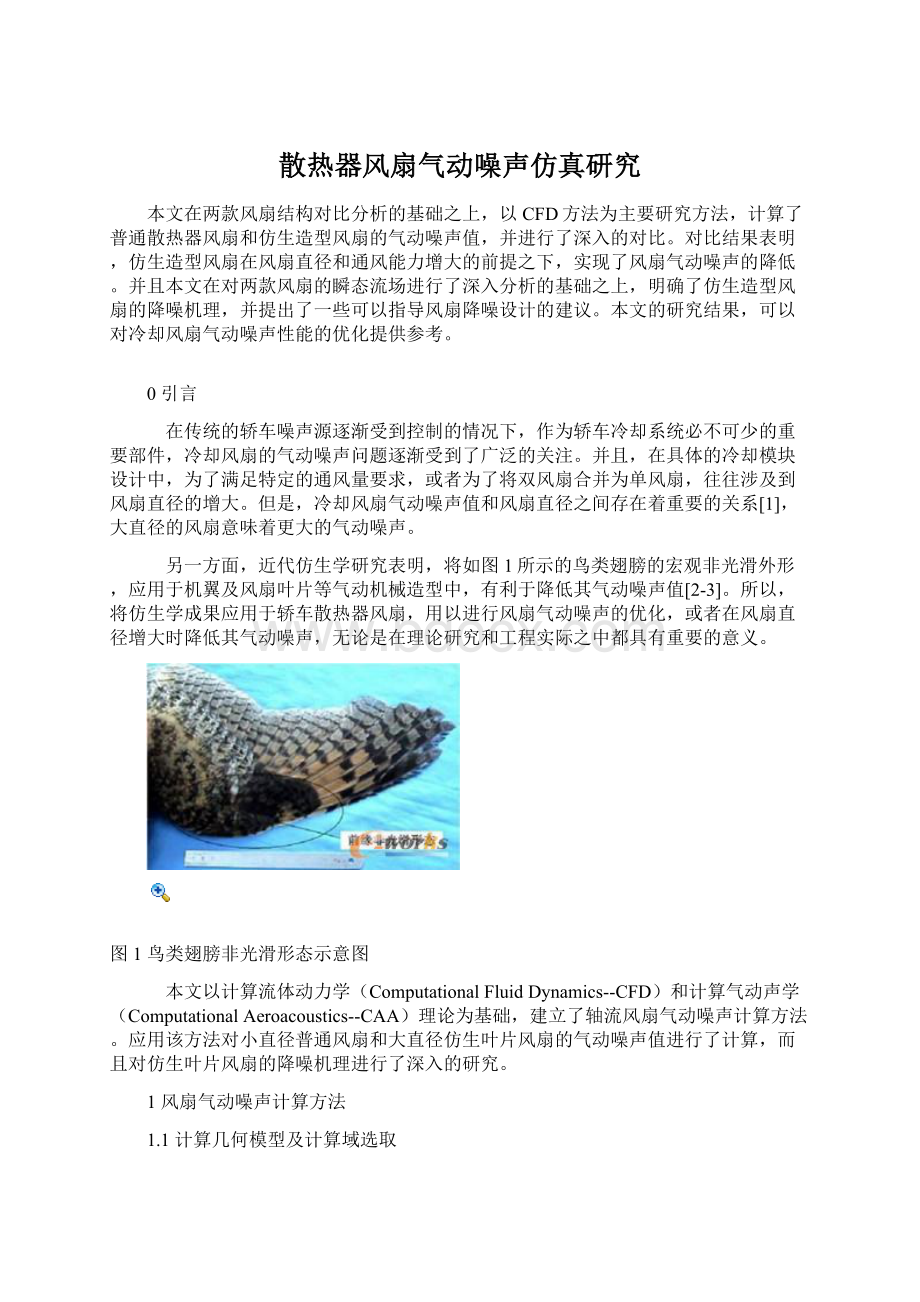
散热器风扇气动噪声仿真研究
本文在两款风扇结构对比分析的基础之上,以CFD方法为主要研究方法,计算了普通散热器风扇和仿生造型风扇的气动噪声值,并进行了深入的对比。
对比结果表明,仿生造型风扇在风扇直径和通风能力增大的前提之下,实现了风扇气动噪声的降低。
并且本文在对两款风扇的瞬态流场进行了深入分析的基础之上,明确了仿生造型风扇的降噪机理,并提出了一些可以指导风扇降噪设计的建议。
本文的研究结果,可以对冷却风扇气动噪声性能的优化提供参考。
0引言
在传统的轿车噪声源逐渐受到控制的情况下,作为轿车冷却系统必不可少的重要部件,冷却风扇的气动噪声问题逐渐受到了广泛的关注。
并且,在具体的冷却模块设计中,为了满足特定的通风量要求,或者为了将双风扇合并为单风扇,往往涉及到风扇直径的增大。
但是,冷却风扇气动噪声值和风扇直径之间存在着重要的关系[1],大直径的风扇意味着更大的气动噪声。
另一方面,近代仿生学研究表明,将如图1所示的鸟类翅膀的宏观非光滑外形,应用于机翼及风扇叶片等气动机械造型中,有利于降低其气动噪声值[2-3]。
所以,将仿生学成果应用于轿车散热器风扇,用以进行风扇气动噪声的优化,或者在风扇直径增大时降低其气动噪声,无论是在理论研究和工程实际之中都具有重要的意义。
图1鸟类翅膀非光滑形态示意图
本文以计算流体动力学(ComputationalFluidDynamics--CFD)和计算气动声学(ComputationalAeroacoustics--CAA)理论为基础,建立了轴流风扇气动噪声计算方法。
应用该方法对小直径普通风扇和大直径仿生叶片风扇的气动噪声值进行了计算,而且对仿生叶片风扇的降噪机理进行了深入的研究。
1风扇气动噪声计算方法
1.1计算几何模型及计算域选取
研究显示,轴流风扇的噪声源包括干涉噪声和自噪声两部分[4]。
其中,干涉噪声是指旋转叶片与固定部件之间的流体干涉,以及风扇上游部件导致的进口湍流产生的噪声;自噪声的主要噪声源为风扇叶片的气流分离、尾窝脱落和叶尖窝等。
针对轿车散热器风扇而言,如图2所示,散热器风扇由轮毂、叶片、和叶圈组成,叶圈与叶片固连在一起共同运动。
风扇外部有风扇框架,风扇框架上与叶圈相对应的部分为护风圈。
另外在散热器风扇上游存在发动机舱入口格栅、散热器、冷凝器等部件,风扇下游还有动力总成及其附件等结构。
所有这些结构,都会对散热器风扇的气动噪声值产生不同程度的影响。
图2散热器风扇结构示意图
但是,由于CAA计算需要耗费大量的计算资源,在现阶段无法实现散热器风扇在实车状态下的噪声值计算。
另外,作为仿生叶片风扇噪声的初步研究,忽略周边部件的影响,对于对比风扇本身的性能优劣和研究其降噪机理是有利的。
因此在本文的研究之中,主要考虑风扇本体的自噪声部分和叶圈、护风圈之间的干涉噪声。
计算域如图3所示,整个计算域为封闭的矩形空间,风扇几何模型包括轮毂、叶片、叶圈、护风圈和风扇支架,计算模型完整的保留风扇叶片和护风圈之间的特征。
图3风扇气动噪声计算域
1.2计算物理模型
图4所示为典型轴流风扇的噪声频谱,由图可见,轴流风扇的气动噪声可以归结为两种,即叶片通过频率噪声(BladePassingFrequency--BPF)和宽频噪声(BroadbandNoise)。
其中,BPF噪声是由于风扇叶片与空气相对运动过程中,大范围的流场变化引起的。
BPF噪声分布在由风扇叶片数量和风扇转速共同决定的一些离散的频率点上。
同时,由气流的小范围扰动引起的宽频噪声,分布在很宽的频率范围之内。
图4典型的轴流风扇噪声频谱
研究显示,首先假设叶片周围的宏观流场变化是产生BPF噪声的主要原因,之后采用RANS方法(Reynolds-AveragedNavier-Stokes--RANS)计算风扇瞬态流场,从而预测叶片表面的静压波动,最后结合声类比理论预测风扇远场噪音,此种噪声预测方法是合理的[5]。
因此,在本文的风扇BPF噪声计算中,应用k-ε湍流模型进行风扇瞬态流场的计算,并应用滑移网格方法模拟风扇叶片的转动,之后应用FW-H(FfowcsWilliams-Hawkings--FW-H)噪声模型进行噪声值的预测。
为了更加精确地预测宽频噪声值,在风扇宽频噪声的计算过程中,瞬态流场计算采用DES(DetachedEddySimulation)方法,计算域同BPF噪声计算域相同,相对于BPF噪声计算网格在宽频噪声计算网格在附面层内进行了细化。
2两款风扇气动噪声值对比
2.1两款风扇尺寸及结构
本文用于计算的两款风扇如图5所示。
分别为大直径仿生叶片风扇A和小直径普通叶片风扇B。
两款风扇叶片数量都为7片,相对于B风扇,A风扇直径增大了1.23倍,轮毂直径增大了1.16倍,A风扇除轮毂和护风圈面积之外的有效通风面积增加了1.51倍。
为保证噪声值计算结果的可对比性,两款风扇框架的形状都为规则的正方形,并且正方形的边长均为风扇叶圈直径的1.5倍,如图6所示。
图5风扇本体尺寸参数对比
图6风扇框架及护风圈形状示意图
两款风扇的护风圈形状有所不同,A风扇护风圈形状为锯齿形,B风扇护风圈形状为光滑的圆形。
护风圈形状的不同,将直接导致两款风扇叶圈与护风圈之间的间隙的差别,并进一步影响叶圈与护风圈之间的干涉噪声。
因此,在两款风扇的计算模型中,完整的保留了护风圈形状特征。
图5风扇本体尺寸参数对比图6风扇框架及护风圈形状示意图图7风扇叶片形状对比两款风扇单片叶片形状如图7所示,A风扇叶片前缘存在两个明显的凹陷,这是典型的基于鸟类翅膀的宏观非光滑结构;相比之下B风扇的叶片形状更加简单规则。
另一方面,两款风扇叶片的截面都为翼型截面,但是A风扇的叶片更薄。
图7风扇叶片形状对比
2.2风扇BPF噪声对比
计算过程中共设置了四个噪声监测点,分别用于BPF噪声和宽频噪声值的检测。
如图8所示,四个检测点分别为point1风扇中心轴上游0.5m;point2风扇中心轴下游0.5m;point3风扇中心轴下游1.5m;point4风扇下游轴向0.8m向计算域上部偏移0.8m的位置。
图9所示为两款风扇BPF噪声计算值,在point4的监测结果,共计算了1800rpm和2500rpm两种工况。
在图9之中,共对比了两款风扇第1--5个BPF频率点处,噪声值的相对大小。
计算结果表明,在1800rpm转速情况下,A风扇在第1、第3和第5BPF频率点处,噪声值均低于B风扇;在第2和第4BPF频率点处,两款风扇噪声值基本相当。
在2500rpm转速情况下,A风扇在第1、第4和第5BPF频率点处,噪声值均低于B风扇;在第2BPF频率点处,A风扇噪声高于B风扇;第3BPF频率点处,两款风扇噪声值相当。
总体评价,相对于B风扇,A风扇在叶圈直径扩大了1.23倍的情况下,实现了BPF噪声的降低。
图8噪声监测点位置示意图
图9两款风扇point4监测点BPF噪声计算结果
2.3风扇宽频噪声对比
图10所示为两款风扇在2500rpm转速工况下,宽频噪声计算结果。
对比各监测点噪声值可知,在1000HZ左右,两款风扇噪声值相当,在高频区域A风扇噪声高于B风扇噪声值。
总体评价,对A风扇宽频噪声较B风扇略有增加。
众所周知,对于冷却风扇而言,BPF噪声值大小比宽频噪声值大小更加重要。
结合BPF噪声和宽频噪声的计算结果分析,可知A风扇在风扇直径增加的情况下,总体噪声值低于B风扇,说明A风扇的仿生叶片形状实现了气动噪声值的降低。
3仿生叶片风扇降噪机理
从基础研究的角度出发,目前大部分轴流风扇气动噪声的研究,是针对无叶圈结构的风扇进行的,对于具有叶圈结构的轴流风扇噪声源的研究比较少见。
因此,以下本文将参考无叶圈轴流风扇的研究成果,并结合具有叶圈的轴流风扇的结构特殊性,对本文中所涉及的大直径仿生叶片风扇降噪机理进行研究。
图10两款风扇各监测点宽频噪声计算结果
根据AtsushiNashimoto等人对无叶圈汽车散热器风扇的研究结果[6],散热器风扇首位的噪声源分布在叶片前缘的吸力面,此处发生了流动的分离和再附着;第二位的噪声源为叶片尾缘附近由于页尖窝和尾窝脱落产生的噪声,如图11所示。
因此,在本文的研究之中,将分别从叶片前缘气流分离、叶片尾窝和叶尖窝三个方面考察A风扇的降噪机理。
3.1叶片前缘气流分离
图12所示为两款风扇叶片吸力面静压云图,由图可知,A风扇在叶片前缘上部靠近叶圈的区域压力梯度更加平缓。
并且在A风扇叶片前缘的第二个凹陷位置处,相对于B风扇叶片的相同位置,气流分离得到了明显的抑制。
为进一步对比两款风扇叶片前缘气流分离情况,截取了位于风扇叶片顶端的周向截面总压云图,如图13所示。
分析图13可以发现,A风扇在叶片前缘吸力面位置的负压区域明显的低于B风扇。
结合以上分析可以说明,A风扇的仿生造型有效的减小了叶片前缘吸力面的气流分离,这种改善作用在叶片顶端区域表现的尤为明显。
图11轴流风扇噪声源示意图
图12风扇叶片吸力面压力云图
图13风扇圆周截面总压云图
3.2叶片尾窝
图14所示,为两款风扇在不同风扇位置的径向截面的窝量云图。
由图可知,A风扇叶片尾窝区域明显的比B风扇小,并且在风扇叶片下游靠近叶圈的位置表现的最为明显。
可以初步推测,A风扇在叶片仿生造型以及护风圈锯齿形结构的共同作用之下,有效的抑制了叶片顶端漩涡的产生,并且有效的减小了叶片尾窝,这些改进对降低风扇气动噪声都是有利的。
图14风扇径向截面窝量云图
3.3风扇叶尖窝
为了分析两款风扇叶片顶端部位在风扇叶片、叶圈和护风圈的共同作用下的复杂流场,特别提取了两款风扇不同径向截面的叶片顶端位置的速度矢量图,如图15所示。
由图可知,对于具有叶圈结构的风扇而言,风扇叶片顶端的页尖窝首先产生于叶圈上游的主流分离区域,之后随主流和风扇叶片的推动作用向下游发展。
两款风扇所不同的是,B风扇叶圈与护风圈之间间隙的回流更加明显。
B风扇叶尖窝在离开叶圈时,受到了风扇外侧回流的影响,使得叶尖窝在紧贴护风圈的下游位置得到了进一步的加强,之后才逐渐耗散。
而A风扇受护风圈外部锯齿形结构的影响,回流能量大大降低,因此叶尖窝在离开随动护风圈区域之后漩涡能量没有被加强。
基于以上分析可以发现,与普通风扇主要由于页顶回流产生的叶尖窝不同,具有叶圈结构的风扇叶尖窝是由叶圈入口的气流分离和出口的气流回流共同作用产生的,叶尖窝产生的最初始的原因为叶圈入口的气流分离。
图15两款风扇不同位置径向截面速度矢量图
因此,初步假设叶圈入口圆角的形状,为影响叶尖窝大小的主要风扇结构参数之一。
为了验证此想法,在A风扇模型基础之上,制作了无叶圈入口圆角的风扇模型(如图16所示),并进行了瞬态流场的计算。
图16风扇径向截面速度矢量图
图17风扇流场窝量为3000的等势面
如图16所示,为原始A风扇和无叶圈圆角的A风扇瞬态流场径向截面速度矢量图。
从图中可以发现没有护风圈入口圆角的计算模型,入口气流分离更加明显,并且叶尖窝更加粗大。
这一点从图17中所示的窝量=3000的等势面图片中,可以更加明显的体现出来。
由此可见,在风扇设计过程中,需要特别注意随动护风圈入口圆角的形状和大小,以降低叶尖窝能量,从而进一步降低风扇气动噪声值。
4结论
本文应用数值计算方法,分别计算了大直径仿生叶片风扇和小直径普通叶片风扇的气动噪声值,并深入研究了仿生叶片风扇的降噪机理。
所得研究结论如下:
(1)以鸟类翅膀的宏观非光滑结构为基础,通过对风扇叶片形状和护风圈形状的调整,可以实现在风扇直径增大的同时降低风扇气动噪声;
(2)通过调整风扇叶片形状,可以减小风扇叶片前缘的气流分离和尾窝脱落,这些改进有利于降低风扇气动噪声值,在具体的改进过程之中应主要关注叶片顶端位置;
(3)通过在风扇护风圈上设置锯齿形结构,可以有效的降低叶圈与护风圈之间的回流能量,从而减小风扇的叶尖窝。
(4)对于具有叶圈结构的轴流风扇而言,位于叶圈前缘的气流分离是叶尖窝的初始成因,优化相应部位的圆角形状和大小,有利于降低叶尖窝能量,并进一步降低风扇气动噪声值。
参考文献
[1]JeonghanLee,KyungookNam.DevelopmentofLow-NoiseCoolingFanUsingUnevenFanBladeSpacing[J].SAEinternational.2008-01-0569
[2]孙少明,徐成宇,任露泉等.轴流风机仿生叶片降噪试验研究及机理分析[J].吉林工业大学学报(工学版).2009,39
(2);
[3]基于信鸽体表的减租降噪功能表面耦合仿生.吉林大学博士学位论文.张春华,200812;
[4]AsukaSoya.StudyontheFanNoiseReductionforAutomotiveRadiatorCoolingFans[J].SAEinternational.2005-01-0601
[5]空调器室外机轴流风机系统内部复杂流动及其气动声学研究.上海交通大学博士学位论文.田杰,200902
[6]AtsushiNashimoto,TsuneoAkuto,YuichiNagaseetc.DetectionofAerodynamicNoiseSourcesoveraRotatingRadiatorFanBladeforAutomobile[J].SAEInternational.2007-01-0545
[7]傅立敏.汽车空气动力学[M].机械工业出版社,1997