PLC数控机床高数高精度检测系统.docx
《PLC数控机床高数高精度检测系统.docx》由会员分享,可在线阅读,更多相关《PLC数控机床高数高精度检测系统.docx(10页珍藏版)》请在冰豆网上搜索。
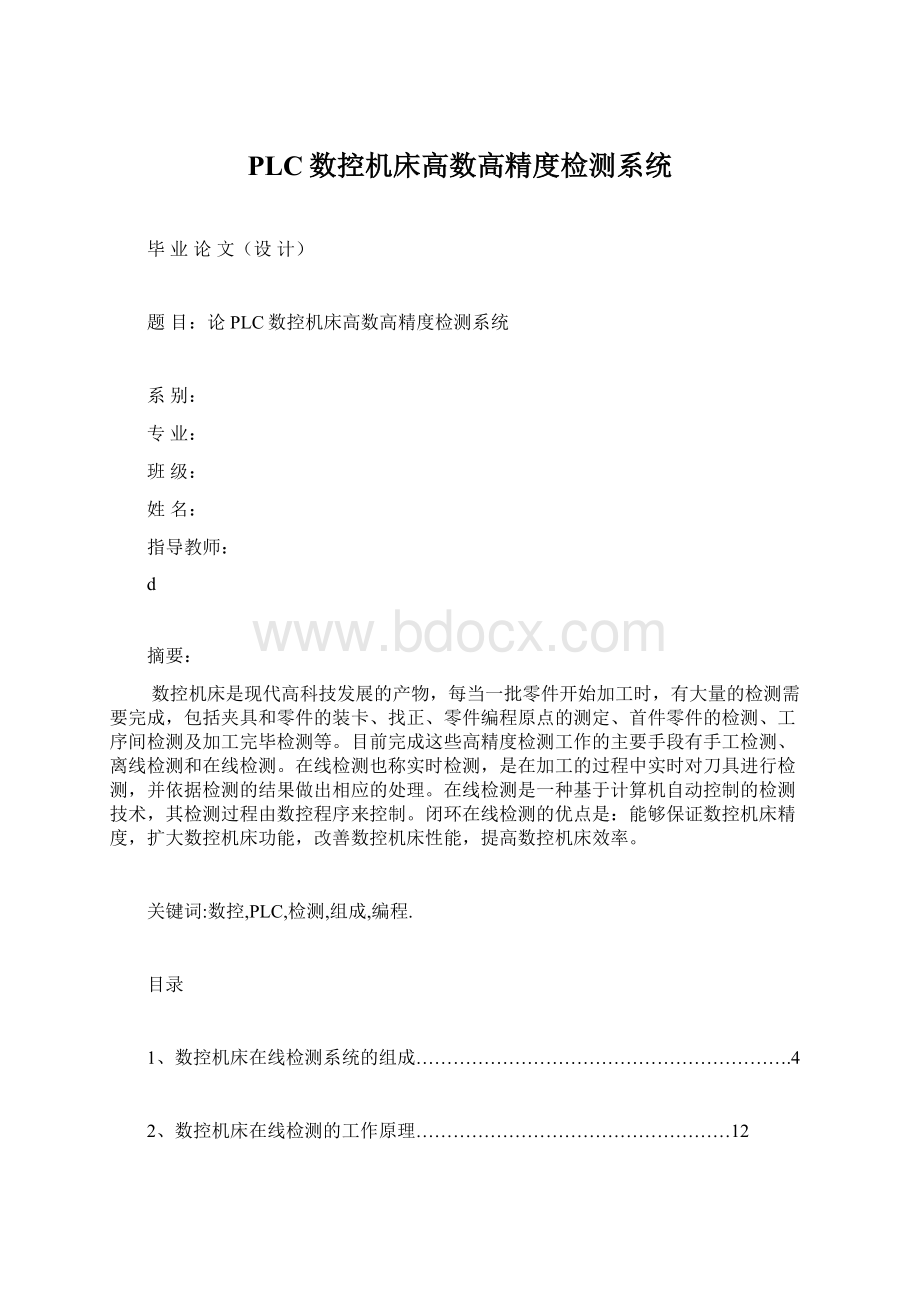
PLC数控机床高数高精度检测系统
毕业论文(设计)
题目:
论PLC数控机床高数高精度检测系统
系别:
专业:
班级:
姓名:
指导教师:
d
摘要:
数控机床是现代高科技发展的产物,每当一批零件开始加工时,有大量的检测需要完成,包括夹具和零件的装卡、找正、零件编程原点的测定、首件零件的检测、工序间检测及加工完毕检测等。
目前完成这些高精度检测工作的主要手段有手工检测、离线检测和在线检测。
在线检测也称实时检测,是在加工的过程中实时对刀具进行检测,并依据检测的结果做出相应的处理。
在线检测是一种基于计算机自动控制的检测技术,其检测过程由数控程序来控制。
闭环在线检测的优点是:
能够保证数控机床精度,扩大数控机床功能,改善数控机床性能,提高数控机床效率。
关键词:
数控,PLC,检测,组成,编程.
目录
1、数控机床在线检测系统的组成…………………………………………………….4
2、数控机床在线检测的工作原理……………………………………………12
3、数控机床在线检测编程………………………………………………………….12
4、数控机床在线检测系统仿真………………………………………………….14
5、结束语……………………………………………………………………………………….15
6、参考资料…………………………………………………………………………………16
7、致谢…………………………………………………………………………………………18
1、数控机床在线检测系统的组成
数控机床在线检测系统分为两种,一种为直接调用基本宏程序,而不用计算机辅助;另一种则要自己开发宏程序库,借助于计算机辅助编程系统,随时生成检测程序,然后传输到数控系统中,系统结构如图1所示。
图1计算机辅助在线检测系统组成
d数控机床的在线检测系统由软件和硬件组成。
硬件部分通常由以下几部分组成:
(1)机床本体
机床本体是实现加工、检测的基础,其工作部件是实现所需基本运动的部件,它的传动部件的精度直接影响着加工、检测的精度。
(2)数控系统
目前数控机床一般都采用CNC数控系统,其主要特点是输入存储、数控加工、插补运算以及机床各种控制功能都通过程序来实现。
计算机与其他装置之间可通过接口设备联接,当控制对象或功能改变时,只需改变软件和接口。
CNC系统一般由中央处理存储器和输入输出接口组成,中央处理器又由存储器、运算器、控制器和总线组成。
(3)伺服系统
伺服系统是数控机床的重要组成部分,用以实现数控机床的进给位置伺服控制和主轴转速(或位置)伺服控制。
伺服系统的性能是决定机床加工精度、测量精度、表面质量和生产效率的主要因素。
(4)测量系统
测量系统有接触触发式测头、信号传输系统和数据采集系统组成,是数控机床在线检测系统的关键部分,直接影响着在线检测的精度。
其中关键部件为测头,使用测头可在加工过程中进行尺寸测量,根据测量结果自动修改加工程序,改善加工精度,使得数控机床既是加工设备,又兼具测量机的某种功能。
目前常用的雷尼绍测头,是英国雷尼绍公司的产品,如图2所示。
它们用于数控车床、加工中心,数控磨床、专机等大多数数控机床上。
测头按功能可分为工件检测测头和刀具测头;按信号传输方式可分为硬线连接式、感应式、光学式和无线电式;按接触形式可分为接触测量和非接触测量。
用户可根据机床的具体型号选择合适的配置。
图2雷尼绍RMP60无线电式测头
(5)计算机系统
在线检测系统利用计算机进行测量数据的采集和处理、检测数控程序的生成、检测过程的仿真及与数控机床通信等功能。
在线检测系统考虑到运行目前流行的Windows和CAD/CAM/CAPP/CAM以及VC++等软件,以及减少测量结果的分析和计算时间,一般采用Pentium级别以上的计算机。
另外数控系统是各类数控装备的核心,因此通过科技创新首先发展具有中国特色的新型数控系统,将是推动数控产业化进程的有效技术途径。
实践证明,10年来我们所走的PC数控道路是完全正确的。
PC机(包括工业PC)产量大、价格便宜,技术进步和性能提高很快,且可靠性高(工业PC主机的MTBF已达30年〔3〕)。
因此,以其作为数控系统的软硬件平台不但可以大幅度提高数控系统的性能价格比,而且还可充分利用通用微机已有软硬件资源和分享计算机领域的最新成果,如大容量存储器、高分辨率彩色显示器、多媒体信息交换、联网通讯等。
此外,以通用微机作为数控平台还可获得快速的技术进步,当PC机升级换代时,数控系统也可相应升级换代,从而长期保持技术上的优势,在竞争中立于不败之地。
目前,PC数控系统的体系结构有2种主要形式:
(1)专用数控加PC前端的复合式结构;
(2)通用PC加位控卡的递阶式结构。
另外还有一种正在发展的数字化分布式结构。
其方案是将由DSP等组成的数字式伺服通过以光缆等为介质的网络与数控装置连接起来,组成一完整的数控系统。
这种系统虽然性能很好,但由于开发和生产成本太高,近期难以被国内广大用户所接受。
我们认为,上述结构并不是符合中国国情的最好方案,适合中国国情的应是将所有数控功能全软件化的集成式结构,因为这种结构的硬件规模最小,不但有利于降低系统成本,而且更重要的是可以有效提高系统的可靠性。
几十年的经验表明,可靠性好坏是国产数控系统能否发展的关键。
虽然影响数控系统可靠性的因素很多,但过大的硬件规模和较低的硬件制造工艺水平往往对可靠性造成最大的威胁。
以往,国产数控系统在总体设计时由于种种原因的限制,不得不选用技术指标不太高的普通CPU,这样,为完成数控的复杂功能往往需要由多个CPU来组成系统,有时还需另加一些专用或通用硬件电路来实现数控系统的一些高实时性功能(如细插补、位置伺服控制等),从而造成系统硬件规模庞大。
对于数控系统这种批量不大的产品,在国内现有工艺条件下,很难从硬件制造的角度保证系统的可靠性,因而使得国产数控系统在生产现场的表现不佳,对国产数控系统的形象和声誉造成严重影响,使得不少用户现在还心有余悸。
因此,我们在开发新型数控系统时,应优先选用新型高性能CPU(如高主频的PentiumII、PentiumIII等)作为系统的运算和控制核心,并尽量用软件来实现数控的所有功能。
这样,可大幅度减小系统硬件的规模。
此外,还应在软件设计、电源设计、接插件设计与选用、接地与屏蔽设计和施工等方面采用强抗扰高可靠性设计与制造技术,从而全面提高系统的可靠性。
由于一个新型高性能CPU可以代替数十个普通CPU(如80286、80386等),因此,在基于高性能CPU的PC平台上不仅可以完成数控系统的基本功能(如信息处理、刀补计算、插补计算、加减速控制等)和开关量控制功能(内装PLC),而且还可以完成伺服控制功能。
这样,以前由DSP完成的数字化伺服控制功能(如位置控制、速度控制、矢量变换控制等)均可由PC中的CPU完成,从而实现内装式伺服控制,这不仅有效缩小了数控部分的硬件规模,而且还大幅度缩小了伺服控制部分硬件规模。
这种具有内装PLC和内装伺服控制的全软件化集成式数控系统,其硬件规模将达到最小化,整个数控系统除一个PC平台外,剩下的只有驱动机床运动的功率接口和反馈接口。
这既有效提高了系统可靠性,又消除了信息传递瓶颈,提高了系统性能,同时还可显著降低系统成本,使系统(包括电机)售价将可降至现有数控系统的一半左右。
显然,这种高性能、高可靠性、低成本的新型数控系统将具有极强的竞争力,有望为开创中国数控的新局面作出贡献。
此外,集成化PC数控系统还有一大优点,就是容易实现开放式结构。
这是因为,这种系统的硬件本身已经是完全开放的,构成开放式数控系统的工作完全在软件上,只要制定好标准和协议,从信息处理、轨迹插补、加减速控制、开关量控制到伺服控制都可以实现开放,从而可大大方便用户的使用。
在我国现有的机床中有一部分仍采用传统的继电器-接触器控制方式,这些机床触点多、线路复杂,使用多年后,故障多、维修量大、维护不便、可靠性差,严重影响了正常的生产。
还有一些旧机床虽然还能正常工作,但其精度、效率、自动化程度已不能满足当前生产工艺要求。
对这些机床进行改造势在必行,改造既是企业资源的再利用,走持续化发展的需要,也是满足企业新生产工艺,提高经济效益的需要。
1解决方案利用PLC对旧机床控制系统进行改造是一种行之有效的手段。
采用PLC进行控制后,机床控制电路的接线量大大减少,故障率大大降低,提高了设备运行的稳定性和使用率,增强了可靠性,减小了维修,维护工作强度。
当机床加工程序发生变化时,只需要修改PLC的程序就可以进行新的加工,更改较方便,有助于提升机床的应用。
由于具有通信功能,采用可编程控制器进行机床改造后,可以与其他智能设备联网通信,在今后的进一步技术改造升级中,可根据需要联入工厂自动化网络中。
2改造过程、步骤及应用实例
(1)深入了解原有机床的工作过程,分析整理其控制的基本方式、完成的动作时序和条件关系,以及相关的保护和联锁控制,尽可能地与实际操作人员充分交流,了解是否需要对现有机床的控制操作加以改进,提高精度、可操作性和安全性等;如有需要,在后续的设计中予以实现。
(2)根据分析整理的结果,确定所需要的用户输入P输出设备。
由于是对旧机床的改造,在保证完成工艺要求的前提下,最大限度地使用原有机床的输入P输出设备,如:
按钮、行程开关、接触器、电磁阀等,以降低改造成本。
(3)PLC机型选择。
根据输入P输出设备的数量与类型,确定所需的IPO点数。
确定IPO点数时,应留有20%左右的裕量,以适应今后的生产工艺变化,为系统改造留有余地。
由IPO点数,利用一条经验公式:
总内存字数=(开关量输入点数+开关量输出点数)×10+模拟量点数×150来估算内存容量。
在估算出内存字数后,再留25%的裕量。
据此,选择合适的机型。
(4)设计并编制IPO分配表,绘制IPO接线图。
应注意到:
同类型的输入点或输出点应尽量集中在一起,连续分配。
(5)进行程序设计。
可借鉴机床原有继电器控制电路图,加以修改和完善。
完成程序设计后,应进行模拟调试。
(6)模拟调试后,进行现场系统调试。
调试中出现的问题逐一排除,直至调试成功。
最后还应进行技术资料整理、归档。
图1IPO接线图下面是对某锯片切割机的数控改造过程,机床的各控制过程如下:
(1)主轴电机的控制。
起动,停止;
(2)进给电机控制。
工作台纵向进给到与锯片相切的位置,之后工作台横向快速进给锯片,完成后工作台慢速移动后退,其间锯片主工作台变速旋转一个锯齿的角度,两运动同时进行插补出一个锯齿圆弧;(3)冷却泵电机的起动控制以及相关的保护、联锁控制,工作台的各运动方向的超程保护,各运动方向的联锁控制等。
确定所需的用户输入P输出设备。
根据设备的硬件条件分析出,面板上有6个按钮需占6个数字输入口,一个BCD拨码开关占用4个输入口,一条直线光栅尺占用3个输入口,一个三位状态旋钮占2个输入口,执行元件为3个步进电机和2个异步电机,其中3个步进电机共需8个数字输出口,砂轮主电机和冷却泵各需1个输出口,报警指示灯和上电指示灯各需1个输出口。
为保证安全起见,热继电器不接入输入端,而直接接在PLC的输出端;合计输入点数15点,输出点数12点。
考虑到要留有20%左右的裕量,所以IPO点数要在30个点以上。
因此,选用西门子公司S7-200系列226型号的PLC,其输入点数24点,输出点数16点,IPO总点数40点;编制IPO分配表(见表1),绘制IPO接线图(见图1);借助机床原有的继电器控制电路图,进行程序设计,编写STL结构化程序语言;模拟调试及现场系统调试,完成技术资料的归档。
表1IPO分配表输入输出I0.0BCD拨码开关1位Q0.0W轴CP端I0.1BCD拨码开关2位Q0.1X轴PY轴CP端I0.2BCD拨码开关3位Q0.2W轴DIR端I0.3BCD拨码开关4位Q0.3W轴FREE端I0.4启动Q0.4X轴DIR端I0.5暂停Q0.5X轴FREE端I0.6光栅尺A相输入Q0.6Y轴DIR端I0.7光栅尺B相输入Q0.7Y轴FREE端I1.0光栅尺Z相复位Q1.0主电机继电器I1.1锯片直径输入确定Q1.1冷却泵继电器I1.2砂轮直径输入确定Q1.2报警指示灯I1.3三位状态旋钮输入1Q1.3上电指示灯I1.4三位状态旋钮输入2I1.5冷却泵启动I1.6急停3改造后效果可实现加工的柔性自动化,效率比传统锯片机提高5~6倍。
加工的锯齿精度高,尺寸分散度小,提高了锯齿的强度。
拥有自动报警、自动监控、补偿等多种自我调节功能,可实现长时间无人看管加工。
由于锯片采用的是某新型合金钢,齿磨损后修补的成本很高,采用该锯片机以后,为工厂节省了可观的维修成本,真正提高了工厂的效益。
4结语利用PLC对传统机床进行数控化改造,能够有效地解决复杂、精密和小批多变的零件加工问题,满足高质量、高效益和多品种、小批量的柔性生产方式的要求,适应各种机械产品迅速更新换代的需要,同时为企业节省了大量的设备改造成本,提高了企业的经济效益和社会效益,提升了企业的产品竞争力,使企业更容易在竞争激烈的市场环境里生存与发展.
2、数控机床在线检测的工作原理
实现数控机床的在线检测时,首先要在计算机辅助编程系统上自动生成检测主程序,将检测主程序由通信接口传输给数控机床,通过G31跳步指令,使测头按程序规定路径运动,当测球接触工件时发出触发信号,通过测头与数控系统的专用接口将触发信号传到转换器,并将触发信号转换后传给机床的控制系统,该点的坐标被记录下来。
信号被接收后,机床停止运动,测量点的坐标通过通信接口传回计算机,然后进行下一个测量动作。
上位机通过监测CNC系统返回的测量值,可对系统测量结果进行计算补偿及可视化等各项数据处理工作。
测量典型几何形状时检测路径的步骤为:
确定零件的待测形状特征几何要素;
确定零件的待测精度特征;
根据测量的形状特征几何要素和精度特征,确定检测点数及分布;
根据测点数及分布形式建立数学计算公式;
确定检测零件的工件坐标系;
根据检测条件确定检测路径。
3、数控机床在线检测编程
在线检测技术的关键主要体现在检测程序的编制上,检侧程序编制质量的优劣直接影响到检测效果。
目前检测软件有商业化软件和自主开发的软件。
商业化软件如英国DELCAM公司新版本的PowerInspect,是一款开放的检测软件,不受测量设备的限制,既可以在线检测,也可以脱机检测。
不仅提供在线检测的功能,还能够在检测前针对读取的CAD模型进行检测路径的编程工作,并进行检测的仿真。
随后可以把编制好的程序传输给CNC检测设备,进行自动检测。
又如雷尼绍公司基于PC机的在机检测软件OMV(onmachineverification),该软件专为数控机床配用系统而编写,主要应用于:
根据原始CAD数据,检测样件、复杂零件及大型零件、多工序零件以及模具。
自主开发软件的编程方式有:
基于C、C++、VC++、VB、Delphi开发平台的在线检测编程和基于CAD开发平台的在线检测编程。
基于VC++语言的在线检测编程结构框图如图3所示。
图3基于VC++语言的在线检测系统结构框图
检测部分主要模块的功能如下:
(1)测量主程序自动生成模块:
主要完成零件待测信息的输入,生成检测主程序。
(2)误差补偿模块:
对测量过程中所产生的误差进行补偿,提高测量精度。
(3)通信模块:
完成主程序与被调用宏程序的发送及测量点坐标信息的接收。
(4)测量宏程序模块:
实现宏程序的管理和内部调用。
主模块要实现对宏程序的查找、增添、修改及删除等操作。
(5)数据处理模块:
对测量点坐标进行补偿,完成各种尺寸及精度计算。
通过打开测量结果数据文件,获得测量点坐标信息,经过相应的运算过程最终得到所测值。
基于CAD开发平台的在线检测自动编程是采用AutoCAD作为系统集成开发平台,并采用ObjectARY作为二次开发工具,开发该系统可弥补CAD/CAM系统所欠缺的功能,实现检测程序的图形化编制,即CAD在线检测。
4、数控机床在线检测系统仿真
目前数控机床在线检测借鉴于CAD/CAM技术的发展思路可开发相应的在线检测仿真系统。
仿真系统以图形化的方式再现数控机床在线检测过程,可形象直观地对检测路径规划进行检查,提前发现宏程序编制中的错误,以避免在真实检测过程中对在线检测系统所造成的破坏。
以VC++作为系统开发工具,OpenGL作为三维场景开发工具,按照面向对象的程序设计思想开发数控机床在线检测仿真系统的过程是:
(1)虚拟检测环境的建立
采用OpenGL标准进行图形处理工作。
OpenGL是一个图形硬件的软件接口,利用它可进行几何建模、图形变换、渲染、光照、材质等多种操作,大部分对于图形的底层处理工作都由一些专门的函数来处理。
(2)检测信息的提取
在线检测仿真系统,必须在仿真过程中,如实地反映测量宏程序的每一条语句,即利用测量宏程序驱动检测仿真过程的进程。
因而该仿真系统应具备完整的检测信息提取能力,能实现对测量程序的语法检查,能实现相关的计算与判断,最为重要的是能够提取出测头的运动轨迹,以驱动测头的检测仿真。
(3)虚拟测头的驱动
在线检测系统是利用测头与待测物体的碰撞来确定接触点的位置信息的,因而检测仿真必须逼真的再现这一过程,这也是整个仿真系统的核心问题。
为保证测头可靠地撞击上待测物体,应使测头检测运动的最远行程大于测头到实际接触点位置的距离,即实际接触点位于测量起始点与测头最远行程点之间的直线段上。
5、结束语
将检测技术融于数控加工的内容之中,采用在线测量的方式,能使操作者及时发现工件存在的问题,并反馈给数控系统。
据抽样调查,目前我国因产品质量问题,如废品、次品、返修品等,所造成的经济损失约为产值的10%~15%,而在线测量技术应用于数控系统,其最直接的经济效益就在在于既节省了工时又提高了测量精度。
而且由于利用了机床数控系统的功能,又使得数控系统能及时得到检测系统所反馈的信息,从而能及时修正系统误差和随机误差,以改变机床的运动参数,更好地保证加工质量,促进加工测量一体化的发展。
可以预见,在线测量技术在数控机床中的应用未来具有广阔的前景。
参考资料:
1、章昌南,我国工业自动化市场现状分析报告,上海电气自动化设计研究院,资料来源:
工控网,2002。
1PC机用于工业控制,《ControlEngineeringChina》专题,2003.6。
2、刘鑫,工业PC及其应用,《石油化工控制系统及仪表自动化》,中国石化出版社,2003.8。
3、2002年工业控制系统专家座谈会纪要,中国仪器仪表协会,资料来源:
工控网,2002.11。
4、王立奉,DCS系统的发展及应用,《石油化工控制系统及仪表自动化》,中国石化出版社,2003.8。
5、阳宪惠,现场总线的发展动态,清华大学自动化系,资料来源:
凌华科技,2003。
6、彭可等,现场总线技术及控制系统,中南大学,资料来源:
中国智能建筑服务网,2003.8。
7、刘向杰等,现场总线控制系统的现状与发展,电力研究院,资料来源:
电力系统自动化时代,2003。
8、王立奉,现场总线控制系统,《石油化工控制系统及仪表自动化》,中国石化出版社,2003.8。
9、陆廷杰,致高管沙龙开幕词,资料来源:
东方电子集成网,2002.9。
10、赵伟,网络化—测量技术与仪器发展的新趋势,清华大学,资料来源:
中国分析仪器网,2003.6。
11、数控系统与数控机床技术发展趋势,863CIMS专题组,资料来源:
武汉制造业生产力中心,2002.7。
12、中国数控机床现状分析,机械工业景气监测中心,资料来源:
中国工业电器网,2003.9。
13、冯冬芹等,无线局域网应用于工业控制系统研究,浙江大学工业控制技术国家重点实验室,2003。
14、颜瑛,无线局域网在工业控制中的应用,资料来源:
新浪网,2003.6。
15、涂博文,过程建模、在线优化及先进控制,《石油化工控制系统及仪表自动化》,中国石化出版社,2003.8。
致谢:
五月维夏,山有嘉卉。
初春的绿城早已艳阳朝天,花满枝头,欣欣向荣。
在这个美好的季节里,我在电脑上敲出了最后一个字,心中涌现的不是想象已久的欢欣,却是难以言喻的失落。
是的,随着论文的终结,意味着我生命中最纯美的学生时代即将结束,尽管百般不舍,这一天终究会在熙熙攘攘的喧嚣中决绝的来临。
三年寒窗,所收获的不仅仅是愈加丰厚的知识,更重要的是在阅读、实践中所培养的思维方式、表达能力和广阔视野。
很庆幸这些年来我遇到了许多恩师益友,无论在学习上、生活上还是工作上都给予了我无私的帮助和热心的照顾,让我在诸多方面都有所成长。
感恩之情难以用语言量度,谨以最朴实的话语致以最崇高的敬意。
感谢我的恩师。
三年来,老师对我的学习和研究都非常严格,并给予了悉心的指导,使我受益菲浅。
从恩师身上我体味到了丰富的学养、严谨的作风、求实的态度,勤奋的精神,这都成为了我不断前行的动力和标杆。
同时还感谢三年来帮助和教育过我的老师们,一路走来,从你们的身上我收获无数,却无以回报,谨此一并表达我的谢意。
还要感谢我的父母,给予我生命并竭尽全力给予了我接受教育的机会,养育之恩没齿难忘;感谢我的伴侣雷德坤,无论在精神还是在物质上都给予我莫大的支持;感谢我的同窗好友李静,在我最困难的时候总能给予我安慰和鼓励,让我重拾信心。
还有许多人,也许他们只是我生命中匆匆的过客,但他们对我的支持和帮助依然在我记忆中留底了深刻的印象。
在此无法一一罗列,但对他们,我始终心怀感激。
学生时代,岁月妥贴,时光绵长。
最后,我以《瓦尔登湖》里的一句话结束我的论文,并以此作为未来乘风破浪的心灵脚注:
使我们视而不见的光亮,对于我们就是黑暗。
但我们清醒时,曙光才会破晓。
来日方长,太阳只是颗启明星。
以此为记。