浅论数控机床加工精度.docx
《浅论数控机床加工精度.docx》由会员分享,可在线阅读,更多相关《浅论数控机床加工精度.docx(17页珍藏版)》请在冰豆网上搜索。
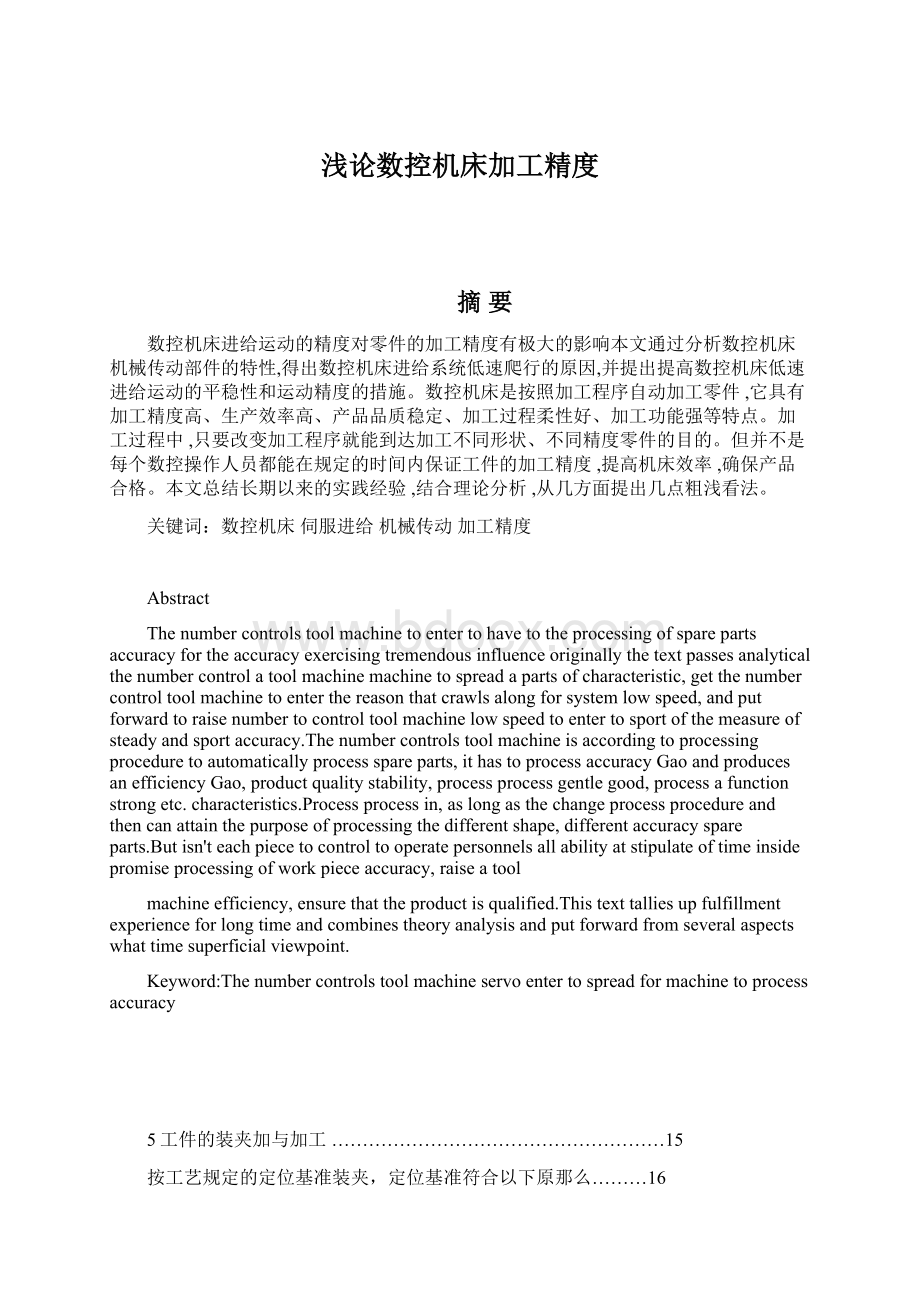
浅论数控机床加工精度
摘要
数控机床进给运动的精度对零件的加工精度有极大的影响本文通过分析数控机床机械传动部件的特性,得出数控机床进给系统低速爬行的原因,并提出提高数控机床低速进给运动的平稳性和运动精度的措施。
数控机床是按照加工程序自动加工零件,它具有加工精度高、生产效率高、产品品质稳定、加工过程柔性好、加工功能强等特点。
加工过程中,只要改变加工程序就能到达加工不同形状、不同精度零件的目的。
但并不是每个数控操作人员都能在规定的时间内保证工件的加工精度,提高机床效率,确保产品合格。
本文总结长期以来的实践经验,结合理论分析,从几方面提出几点粗浅看法。
关键词:
数控机床伺服进给机械传动加工精度
Abstract
Thenumbercontrolstoolmachinetoentertohavetotheprocessingofsparepartsaccuracyfortheaccuracyexercisingtremendousinfluenceoriginallythetextpassesanalyticalthenumbercontrolatoolmachinemachinetospreadapartsofcharacteristic,getthenumbercontroltoolmachinetoenterthereasonthatcrawlsalongforsystemlowspeed,andputforwardtoraisenumbertocontroltoolmachinelowspeedtoentertosportofthemeasureofsteadyandsportaccuracy.Thenumbercontrolstoolmachineisaccordingtoprocessingproceduretoautomaticallyprocessspareparts,ithastoprocessaccuracyGaoandproducesanefficiencyGao,productqualitystability,processprocessgentlegood,processafunctionstrongetc.characteristics.Processprocessin,aslongasthechangeprocessprocedureandthencanattainthepurposeofprocessingthedifferentshape,differentaccuracyspareparts.Butisn'teachpiecetocontroltooperatepersonnelsallabilityatstipulateoftimeinsidepromiseprocessingofworkpieceaccuracy,raiseatool
machineefficiency,ensurethattheproductisqualified.Thistexttalliesupfulfillmentexperienceforlongtimeandcombinestheoryanalysisandputforwardfromseveralaspectswhattimesuperficialviewpoint.
Keyword:
Thenumbercontrolstoolmachineservoentertospreadformachinetoprocessaccuracy
5工件的装夹加与加工 ………………………………………………15
按工艺规定的定位基准装夹,定位基准符合以下原那么………16
………………………………………17
6测量工具正确使用方法……………………………………………19
常用测量工具的读数…………………………………………21
千分尺的读数……………………………………21
游标卡尺读数………………………………………22
引言
在开环进给系统中运动精度取决于系统各组成环节,特别是机械传动部件的精度;在闭环和半闭环进给系统中,位置检测装置的分辨力和分辨精度对运动精度有决定性的影响,但是机械传动部件的特性对运动精度也有一定的影响。
通常在开环进给系统中,设定的脉冲当量为0101时,实际的定位精度最好的情况也只能到达0102在闭环系统中,设定的脉冲当量(或称最小设定单位)一般为01001,实际上定位精度只能到达01003,当指令进给系统做单步进给(即每次移动01001时,开始一二个单步指令,进给部件并不动作,到第三个单步指令时才突跳一段距离,以后又如此重复"这些现象都是因为进给系统的低速爬行现象引起的,而低速爬行现象又决定于机械传动部件的特性。
数控机床是按照加工程序自动加工零件,它具有加工精度高、生产效率高、产品品质稳定、加工过程柔性好、加工功能强等特点。
加工过程中,只要改变加工程序就能到达加工不同形状、不同精度零件的目的。
但并不是每个数控操作人员都能在规定的时间内保证工件的加工精度,提高机床效率,确保产品合格。
本文总结长期以来的实践经验,结合理论分析,从以下几方面提出几点粗浅看法。
1速度爬行产生原因
速度爬行产生原因分析
对于数控机床进给系统产生爬行的原因,一般认为是由于机床运动部件之间润滑不好,导致机床工作台移动时静摩擦阻力增大;当电机驱动时,工作台不能向前运动,使滚珠丝杠产生弹性变形,把电机的能量贮存在变形上;电动机继续驱动,贮存的能量所产的弹性力大于静摩擦力时,机床工作台向前蠕动,周而复始地这样运动,产生了爬行的现象。
事实上这只是其中的一个原因,产生这类故障的原因还可能是机械进给传动链出现了故障,也可能是进给系统电气局部出现了问题,或者是系统参数设置不当的缘故,还可能是机械局部与电气局部的综合故障所造成。
图1机械传动机构的简化动力学模型数控机床进给系统的机械传动机构可以简化成如图1所示的动力学模型[3]"图中,B为传动部件的阻尼系数,K为传动刚度,为执行部件,m为执行部件的质量"设驱动件以等速+v1运动,经时间t后,从动件的位移为x,速度为x,
加速度&x,那么运动方程为:
m&x+B(&x-v1)-K(vt-x)+(F-Ax)=0
(1)
式中:
F-Ax为摩擦力,它由弹簧力F和随的速度
而变化的分量-Ax所组成,A为比例系数"
该方程的解为:
x=Bv1K+v1t-FK+e-NXt(C1Xt+C2Xt)
(2)
中:
N=B-AKm称为阻尼比,X=Km为角频率"
式
(2)中的C1!
C2可以根据初始条件:
t=0,x=0,x=$Fm来求得"这样有
x=Bv1K+v1t-FK+v1XeNXt[(2N-A)Xt-(1+N)Xt](3)
(4)
试中:
$F=F0-Fv,即静摩擦力F0与动摩擦力Fv
差;S1为动!
静柔度修正系数,取为1"
将式(3)对t微分,得速度和加速度为
x=v1{1-eNXt[Xt-(N-A)Xt]}(5)
&x=v1XeNXt[AXt-(1-AN)Xt](6)
从式(5)可以看出,执行部件的运动速度包括局部:
恒量v1和振动量v1eNXt[Xt(N-A)Xt]"振动分量小于恒定分量,x不会为零,如果阻尼足大,那么随着时间的延续,振动分量将衰减到零,这振动表现为过渡过程,一段时间以后,执行部件将主动件的速度作匀速运动,如图2()所示"当满足上述条件,那么执行部件的速度将会时快时慢,图2()所示,甚至会出现停顿,如图2()所
这便是所谓的爬行现象,使运动产生停顿,即当
=t1,x=0,&x=0时,由式(5)与式(6)得
eNXt[Xt1-(N-A)Xt1]=1(7)
AXt1-(1-AN)Xt1=0(8)
当N不大时,由式(7)可以求得A的近似值=4PN
Ac称为系统开始出现爬行现象临界运动均匀数"由式(4)可知,当$F!
K!
m等为一定果A为临界值Ac,那么速度v1就是产生爬行现象界速度vc
vc=$F4PNKm=N#$f4PNKm
中:
$f为静!
动摩擦系数之差,N=mg为正压力。
进给执行部件的定位运动在接近定位点时,要降速,这时的速度可能低于临界速度vc,由于爬象将使部件不能准确地停在定位点,因而出现定差。
当执行部件单步运动时,如果指令位移为X0动件的位移量),那么只有满足KX0EF0时,执行才能够克服静摩擦力F0运动,如系统的静摩擦,传动刚度K不大,那么一个微小的单步位移指传动链产生的弹性力缺乏以克服静摩擦力,执行是不会有位移响应的。
2提高进给运动精度采取的措施
根据前面的分析可知,要提高运动精度,应设法高进给运动的低速运动平稳性,可以采取的措施:
降低执行部件的质量,减少静动摩擦系数之,提高传动刚度K。
减少动静摩擦系数之差执行部件所受摩擦阻力主要来自导轨副,一般的滑动导轨副不仅!
动摩擦系数大,而且差值也大"因此采用滚动导!
卸荷导轨静压导轨塑料导轨,精度要求特高数控机床如数控三坐标测量机,那么多采用气浮导。
另外在进给传动系统中,广泛采用滚珠丝杠螺母或静压丝杠螺母副也是为了减少$f。
提高传动系统的传动刚度进给系统中从服驱动装置到执行部件之间必定要经过由齿轮!
丝螺母副或蜗杆蜗轮副等组成的传动链"为提高其刚,应尽可能缩短传动链,适当加大传动轴的直径,强支承座的刚度。
此外,对轴承丝杠螺母副和丝本身进行预紧也可以提高传动刚度。
减小机床的热变形机床的热变形,特是数控机床的热变形,是影响加工精度的重要因引起机床热变形的热源主要是机床的内部热源,主电机!
进给电机发热,摩擦以及切削热等热变影响加工精度的原因,主要是由于热源分布不均,热源产生的热量不等,各处零部件的质量不均,形成各部位的温升不一致,从而产生不均匀的温度场和不均匀的热膨胀变形,以致影响刀具与工件相对位置的正确性。
2.2减少机床热变形及其影响的措施是:
减少机床内部发热量"主运动采用直流或交流调速电机,减少传动轴与传动齿轮的数量;采用低摩擦系数的导轨和轴承;液压系统中采用变量泵这样可以减少摩擦和能耗发热。
均衡温度场"主轴箱或主轴部件用强制润滑冷却,甚至采用制冷后的润滑油进行循环冷却;液压系统尤其是液压油泵站是一个热源,应放置在机床
之外,假设必须放在机床上时,应采取隔热或散热措施;切削过程中发热最大,要进行强制冷却,要自动及时排屑;对于发热大的部位,应加大散热面积或散热效果。
合理设计机床的结构及布局设计"热传导对称的结构,如数控卧式镗床,采用双柱对称结构时,热变形对主轴轴线变位的影响要小,如果用立柱主轴箱悬挂的结构形式,那么热变形对主轴影响要大结构设计时,应设法使热量比拟大的部位的热向热量小的部位传导或流动,使结构部件的各部位能够均热,也是减少热变形的有效措施。
进行热变形补偿"预测热变形的规律,建立变形的数学模型,或测定其变形的具体数值,存入数控装置的内存中,用以进行实时补偿校正"如传动丝杠的热伸长误差,导轨平行度和平直度的热变形误差等,都可以采用软件实时补偿来消除其影响。
保持工艺系统的热平衡"高精度的机床可安装在恒温车间,并在使用前进行预热,使机床到达热稳定后再进行加工,这是在使用时防止热变形影响的一种措施。
控制环境温度精密数控机床一般安装在恒温车间,其温度一般控制在2e以内。
3工件坐标系设定对加工精度的影响
因为数控机床通过坐标控制刀具进给。
每次操作完数控机床,机台一般不在零点位置上,当你下次操作机床的时候,如果不进行回零操作,那你程序中的坐标系反响在机床动作的时候就会出现偏差,即不能准确的建立机床坐标系。
通过机床回零操作,确定了机床零点,从而准确地建立机床坐标系,即相当于数控系统内部建立一个以机床零点为坐标原点的机床坐标系。
这样你程序中的坐标就可以准确的在机床的运动中表现出来。
其实无论是否提高机床加工精度,数控机床回零操作都是操作数控机床必须的一个步骤。
工件坐标系是编程人员在编写程序时,在工件上建立的坐标系,其原点即为工件原点(也称工件零点或编程原点)。
理论上是由编程人员任意设定的,但实际上,它是编程人员根据零件特点为了编程方便以及尺寸的直观性而设定的。
有个比拟方便的方法,就是用夹头对刀,我们知道夹头外径,刀具去碰了输入外径就可以,对内径时可以拿一量块用手压在夹头上对,同样输入夹头外径就可以了.如果有对刀器就方便多了,对刀器就相当于一个固定的对刀试切工件,刀具碰了就记录进去位置了.
3.1工件坐标系时一般应遵循如下原那么:
尽可能将工件原点选择在工艺定位基准上,这样有利于加工精度的提高;
尽量将工件原点选择在零件的尺寸基准上,这样便于坐标值的计算,减少错误率(当尺寸基准与工艺基准不重合时,那么要考虑由基准不重合产生的误差);
尽量选在精度较高的工件外表上,以提高被加工零件的加工精度;
对于对称零件,应设在对称中心上,一般零件应设在工件轮廓某一角上,且Z轴方向上原点一般设在工件外表;
对于卧式加工中心最好把工件原点设在回转中心上,即设置在工作台回转中心与Z轴连线的适当位置上;
应将刀具起点和编程原点设在同一处,这样可以简化程序,便于计算,提高加工精度;对一般零件,仅按上述原那么确定工件坐标系,即能保证其加工精度。
但对于复杂、特殊零件,就要综合考虑各种因素对加工精度的影响。
3.3 在立式加工中心上加工畸形工件根据畸形工件的结构特点,往往在一个零件上要选择两个或两个以上的坐标系,这时就要根据零件的形状特征、夹紧方式及各加工部位的精度上下等因素综合考虑:
建立几个坐标系;
先加工哪个坐标系的哪个外表才能提高整个零件的加工精度;
坐标系间定位尺寸的精度对各部位加工精度的影响(某些定位基准可能不在工件上)。
3.4在卧式加工中心上加工箱体类零件根据箱体类零件的结构特点,不仅除上下底面之外的四个侧面需要分别建立四个定位坐标系,而且每一侧面上有时还需建立几个坐标系,这时就必须考虑各加工精度如何保证。
如:
机床回转中心坐标精度对零件相对两侧面坐标系的建立来说,它直接影响两相对侧面通孔的同轴度;
每一侧面上几个坐标系建立时,加工工序的设计对加工精度的影响;
以底面为基准的的装夹精度,直接影响孔轴线相对端面的垂直度;
基准底面精度对孔的中心高精度的影响。
当然,零件结构不同,精度要求不同,坐标系的建立也不一样,不管何种情况都应详细分析优先选用哪一原那么或同时兼顾哪几项原那么,才能有利于保证零件加工精度、提高工作效率,降低加工本钱。
4如何提高数控机床的加工精度
目前数控机床位置精度的检验通常采用国际标准ISO230-2或国家标准GB10931-89等。
同一台机床,由于采用的标准不同,所得到的位置精度也不相同,因此在选择数控机床的精度指标时,也要注意它所采用的标准。
数控机床的位置标准通常指各数控轴的反向偏差和定位精度。
对于这二者的测定和补偿是提高加工精度的必要途径。
效率、质量是先进制造技术的主体。
高速、高精加工技术可极大地提高效率,提高产品的质量和档次,缩短生产周期和提高市场竞争能力。
为此日本先端技术研究会将其列为5大现代制造技术之一,国际生产工程学会〔cirp〕将其确定为21世纪的中心研究方向之一。
在加工精度方面,近10年来,普通级数控机床的加工精度已由10μm提高到5μm,精密级加工中心那么从3~5μm,提高到1~1.5μm,并且超精密加工精度已开始进入纳米级(0.01μm)。
因为数控机床通过坐标控制刀具进给。
每次操作完数控机床,机台一般不在零点位置上,当你下次操作机床的时候,如果不进行回零操作,那你程序中的坐标系反响在机床动作的时候就会出现偏差,即不能准确的建立机床坐标系。
通过机床回零操作,确定了机床零点,从而准确地建立机床坐标系,即相当于数控系统内部建立一个以机床零点为坐标原点的机床坐标系。
这样你程序中的坐标就可以准确的在机床的运动中表现出来。
其实无论是否提高机床加工精度,数控机床回零操作都是操作数控机床必须的一个步骤
在数控机床上,由于各坐标轴进给传动链上驱动部件(如伺服电动机、伺服液压马达和步进电动机等)的反向死区、各机械运动传动副的反向间隙等误差的存在,造成各坐标轴在由正向运动转为反向运动时形成反向偏差,通常也称反向间隙或失动量。
对于采用半闭环伺服系统的数控机床,反向偏差的存在就会影响到机床的定位精度和重复定位精度,从而影响产品的加工精度。
如在G01切削运动时,反向偏差会影响插补运动的精度,假设偏差过大就会造成“圆不够圆,方不够方〞的情形;而在G00快速定位运动中,反向偏差影响机床的定位精度,使得钻孔、镗孔等孔加工时各孔间的位置精度降低。
同时,随着设备投入运行时间的增长,反向偏差还会随因磨损造成运动副间隙的逐渐增大而增加,因此需要定期对机床各坐标轴的反向偏差进行测定和补偿。
反向偏差的测定方法:
在所测量坐标轴的行程内,预先向正向或反向移动一个距离并以此停止位置为基准,再在同一方向给予一定移动指令值,使之移动一段距离,然后再往相反方向移动相同的距离,测量停止位置与基准位置之差。
在靠近行程的中点及两端的三个位置分别进行屡次测定(一般为七次),求出各个位置上的平均值,以所得平均值中的最大值为反向偏差测量值。
在测量时一定要先移动一段距离,否那么不能得到正确的反向偏差值。
测量直线运动轴的反向偏差时,测量工具通常采有千分表或百分表,假设条件允许,可使用双频激光干预仪进行测量。
当采用千分表或百分表进行测量时,需要注意的是表座和表杆不要伸出过高过长,因为测量时由于悬臂较长,表座易受力移动,造成计数不准,补偿值也就不真实了。
假设采用编程法实现测量,那么能使测量过程变得更便捷更精确。
例如,在三坐标立式机床上测量X轴的反向偏差,可先将表压住主轴的圆柱外表,然后运行如下程序进行测量:
N10G91G01X50F1000;工作台右移
N20X-50;工作台左移,消除传动间隙
N30G04X5;暂停以便观察
N40Z50;Z轴抬高让开
N50X-50:
工作台左移
N60X50:
工作台右移复位
N70Z-50:
Z轴复位
N80G04X5:
暂停以便观察
N90M99;
需要注意的是,在工作台不同的运行速度下所测出的结果会有所不同。
一般情况下,低速的测出值要比高速的大,特别是在机床轴负荷和运动阻力较大时。
低速运动时工作台运动速度较低,不易发生过冲超程(相对“反向间隙〞),因此测出值较大;在高速时,由于工作台速度较高,容易发生过冲超程,测得值偏小。
回转运动轴反向偏差量的测量方法与直线轴相同,只是用于检测的仪器不同而已。
国产数控机床,定位精度有不少>,但没有补偿功能。
对这类机床,在某些场合下,可用编程法实现单向定位,去除反向间隙,在机械局部不变的情况下,只要低速单向定位到达插补起始点,然后再开始插补加工。
插补进给中遇反向时,给反向间隙值再正式插补,即可提高插补加工的精度,根本上可以保证零件的公差要求。
对于其他类别的数控机床,通常数控装置内存中设有假设干个地址,专供存储各轴的反向间隙值。
当机床的某个轴被指令改变运动方向时,数控装置会自动读取该轴的反向间隙值,对坐标位移指令值进行补偿、修正,使机床准确地定位在指令位置上,消除或减小反向偏差对机床精度的不利影响。
一般数控系统只有单一的反向间隙补偿值可供使用,为了兼顾高、低速的运动精度,除了要在机械上做得更好以外,只能将在快速运动时测得的反向偏差值作为补偿值输入,因此难以做到平衡、兼顾快速定位精度和切削时的插补精度。
对于FANUC0i、FANUC18i等数控系统,有用于快速运动(G00)和低速切削进给运动(G01)的两种反向间隙补偿可供选用。
根据进给方式的不同,数控系统自动选择使用不同的补偿值,完成较高精度的加工。
将G01切削进给运动测得的反向间隙值A输入参数NO11851(G01的测试速度可根据常用的切削进给速度及机床特性来决定),将G00测得的反向间隙值B输入参数NO11852。
需要注意的是,假设要数控系统执行分别指定的反向间隙补偿,应将参数号码1800的第四位(RBK)设定为1;假设RBK设定为0,那么不执行分别指定的反向间隙补偿。
G02、G03、JOG与G01使用相同的补偿值。
4.5定位精度
数控机床的定位精度是指所测量的机床运动部件在数控系统控制下运动所能到达的位置精度,是数控机床有别于普通机床的一项重要精度,它与机床的几何精度共同对机床切削精度产生重要的影响,尤其对孔隙加工中的孔距误差具有决定性的影响。
一台数控机床可以从它所能到达的定位精度判出它的加工精度,所以对数控机床的定位精度进行检测和补偿是保证加工质量的必要途径。
精度的测定
目前多采用双频激光干预仪对机床检测和处理分析,利用激光干预测量原理,以激光实时波长为测量基准,所以提高了测试精度及增强了适用范围。
检测方法如下:
A.双频激光干预仪;
B.需要测量的机床坐标轴方向上安装光学测量装置;
C.激光头,使测量轴线与机床移动轴线共线或平行,即将光路预调准直;
D.光预热后输入测量参数;
E.定的测量程序运动机床进行测量;
F.处理及结果输出。
精度的补偿
假设测得数控机床的定位误差超出误差允许范围,那么必须对机床进行误差补偿。
常用方法是计算出螺距误差补偿表,手动输入机床CNC系统,从而消除定位误差,由于数控机床三轴或四轴补偿点可能有几百上千点,所以手动补偿需要花费较多时间,并且容易出错。
现在通过RS232接口将计算机与机床CNC控制器联接起来,用VB编写的自动校准软件控制激光干预仪与数控机床同步工作,实现对数控机床定位精度的自动检测及自动螺距误差补偿,其补偿方法如下:
〔1〕CNC控制系统中的已有补偿参数;
〔2〕算机产生进行逐点定位精度测量的机床CNC程序,并传送给CNC系统;
〔3〕动测量各点的定位误差;
〔4〕定的补偿点产生一组新的补偿参数,并传送给CNC系统,螺距自动补偿完成;
〔5〕进行精度验证。
根据数控机床各轴的精度状况,利用螺距误差自动补偿功能和反向间隙补偿功能,合理地选择分配各轴补偿点,使数控机床到达最正确精度状态,并大大提高了检测机床定位精度的效率。
定位精度是数控机床的一个重要指标。
尽管在用户购选时可以尽量挑选精度高误差小的机床,但是随着设备投入使用时间越长,设备磨损越厉害,造成机床的定位误差越来越大,这对加工和生产的零件有着致命的影响。
采用以上方法对机床各坐标轴的反向偏差、定位精度进行准确测量和补偿,可以很好地减小或消除反向偏差对机床精度的不利影响,提高机床的定位精度,使机床处于最正确精度状态,从而保证零件的加工质量。
5工件的装夹
操作者必须在熟悉产品图样、工艺文件和工艺装备的根底上从事作业生产,防止盲目生产造成零件报废;
在机床工作台面上安装夹具时,要擦净其定位基准面,并找正加工要求的相对位置;
工件装夹前应将其定位面、夹紧面,夹具的定位