百菌清实用工艺操作法12ISO.docx
《百菌清实用工艺操作法12ISO.docx》由会员分享,可在线阅读,更多相关《百菌清实用工艺操作法12ISO.docx(28页珍藏版)》请在冰豆网上搜索。
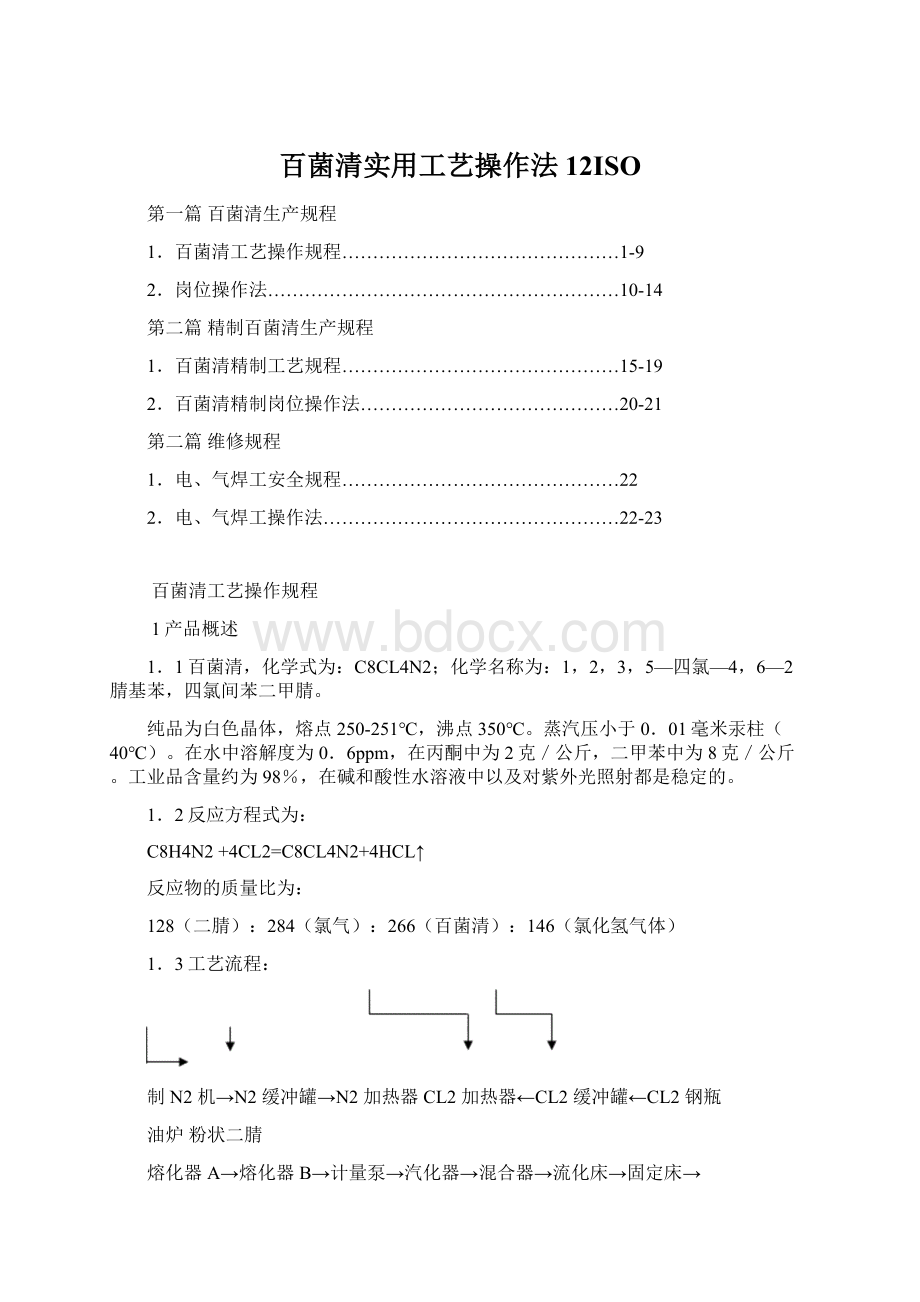
百菌清实用工艺操作法12ISO
第一篇百菌清生产规程
1.百菌清工艺操作规程………………………………………1-9
2.岗位操作法…………………………………………………10-14
第二篇精制百菌清生产规程
1.百菌清精制工艺规程………………………………………15-19
2.百菌清精制岗位操作法……………………………………20-21
第二篇维修规程
1.电、气焊工安全规程………………………………………22
2.电、气焊工操作法…………………………………………22-23
百菌清工艺操作规程
1产品概述
1.1百菌清,化学式为:
C8CL4N2;化学名称为:
1,2,3,5—四氯—4,6—2腈基苯,四氯间苯二甲腈。
纯品为白色晶体,熔点250-251℃,沸点350℃。
蒸汽压小于0.01毫米汞柱(40℃)。
在水中溶解度为0.6ppm,在丙酮中为2克/公斤,二甲苯中为8克/公斤。
工业品含量约为98%,在碱和酸性水溶液中以及对紫外光照射都是稳定的。
1.2反应方程式为:
C8H4N2+4CL2=C8CL4N2+4HCL↑
反应物的质量比为:
128(二腈):
284(氯气):
266(百菌清):
146(氯化氢气体)
1.3工艺流程:
制N2机→N2缓冲罐→N2加热器CL2加热器←CL2缓冲罐←CL2钢瓶
油炉粉状二腈
熔化器A→熔化器B→计量泵→汽化器→混合器→流化床→固定床→
捕集器→吸收塔→风机→循环喷淋池
百菌清盐酸漂液灰浆泵←灰浆←石灰
2工艺控制条件
2.1物料配比
间苯二甲腈100kg/hr;氮气90m3/h;氯气50-60m3/hr;
2.2工艺参数控制
2.2.1固定床前部系统压力在0.02—0.2Mpa,固定床下部测压点为微负压;
2.2.2油炉温度为:
≤295C;系统油温在255℃-275℃;
2.2.3熔化器A、B温度为160℃-190℃;
2.2.4计量泵温度为165℃-180℃;
2.2.5汽化器温度为240℃-270℃;
2.2.6氮气压力0.3±0.02Mpa;
2.2.7氮气加热器温度>200℃;
2.2.8氯气压力0.3±0.02Mpa;
2.2.9氯气加热器温度≥150℃;
2.2.10流化床反应温度265℃-310℃;
2.2.11捕集器温度<160℃;
3岗位操作
3.1开车前准备
3.1.1检查系统中各设备及连接管道、仪表、阀门等部位是否具备开车条件;
3.1.2检查二腈、液氯的储备,及辅助原材料氮气、导热油、催化剂等储备情况;
3.1.3开车前将给定催化剂均匀地加入固定床列管中,保证无架桥情况;
3.1.4打油前再次检查系统中设备、油路管道的密封性,及各油阀、保温大球阀,尾气阀门等开关要求;
3.1.5通知油炉人员把准备好的导热油注入系统循环,待高位槽油液位压差表高液位显示时,油炉人员迅速关闭低位槽进油阀门,打开系统回油路阀门,系统油进入正常循环状态,油炉点火提温,升温过程按给定要求;
3.1.6将流化床上部手孔打开,通氮气,加流化床催化剂,赶水。
3.2催化剂内水汽处理
3.2.1油炉提温,使两床温度缓慢上升,两床上部手孔打开,通氮气把催化剂中的大量水分除掉。
在一定时间后,将两床手孔关闭,进行抽真空继续赶水,待水除净后方可通氯气活化;
3.2.2两床同时整换催化剂赶水时间在9-12小时,若部分更换规定床催化剂,赶水时间在7-10小时,赶水具体步骤按车间规定进行。
分段赶水时间表(例)
两床催化剂整换
150℃
200℃
250℃
255℃
2h
2—4h
2—4h
1—2h
部分更换固定床催化剂
150℃
200℃
250℃
255℃
2h
2h
2—4h
1—2h
3.3催化剂活化
3.3.1净除催化剂内部的水份后,固定床下封头以后系统保持微负压,两床温度保持车间规定温度,开始通氯气活化;
3.3.2活化条件:
氯气通30-45m3/hr;氮气通80-90m3/hr;活化时间根据两床反应温度变化而定,当床内温度显示由低温到高温再到低温(260℃—305℃—270℃),活化过程结束。
附--相关工艺通知单----催化剂具体处理过程(例):
B.加CAT、赶水、活化、开计量泵全过程
一、赶水(12小时)
1.系统打油提温,当温度到150℃时,加流化床催化剂KG进口-1型,保温4小时;
2.系统由150℃向200℃提温,提温和保温时间共计4小时;
注意:
①当温度提到200℃,打上两床赶水孔,抽真空赶水;
②加刘化床催化剂后,通氮气80m3/h(赶水期间);
3、系统由200℃向255℃提温,提温和保温时间共计4小时;
此时,赶水结束。
二、活化(9小时)
1.活化时间为9小时;
2.系统油温保持255℃;
3.活化期间,氯气通40m3/h,氮气通80m3/h;
三、投料
1.活化结束前4小时,投A-1料预熔;
2.开计量泵前,系统油温保持255℃;同时将氯气改通54m3/h(每瓶使用4小时25—30)分钟);氮气通90m3/h;
3.开计量泵前,二腈熔化温度要达到特定的温度;
4.开计量泵后,二腈进料速度为100kg/h;
5.操作人员要控制好进料速度;
6.记录人员、班长勤巡查,做详实记录;
7.出现异常情况,严格按车间规定进行调整。
工段长审核签名:
时间:
工艺技术员签名:
时间:
班长签名
开车过程
加流化床催化剂开始:
结束:
提温、赶水开始时间:
结束:
X流1最高:
X流2最高:
X流3最高:
通氯活化开始时间:
结束:
X流1最高:
X流2最高:
X流3最高:
开泵进料开始时间:
进料:
催化剂吸附期间:
X流1最高:
X流2最高:
X流3最高:
备注:
特殊情况补充及详细记录
3.4投料开车
3.4.1活化结束前4小时,操作人员按要求把二腈投到熔化器A内;
3.4.2操作人员控制熔化器A、B、计量泵的油阀开度,把温度控制在较适宜的点上,保证熔化器A二腈为液态;
3.4.3活化结束,计量泵进料后,根据系统反应状态,均衡物料配比,调整氯气、氮气的流量及系统的油温;
3.4.4,计量泵进料初6—10小时,为催化剂吸附过程,此期间没有料出(其温度变化如同活化期间);
3.4.5记录人员从赶水开始,详实记录温度、压力、流量等变动情况,发现问题及时反应,并积极做出补救处理措施;
3.5酸吸收处理
3.5.1酸吸收原理为氯化氢气体溶于水得盐酸;
3.5.2开车前打开补水阀将一、二级酸贮罐水液位补至70-80cm;
3.5.3油炉温度提到200℃,尾气开风机抽负压,启动酸循环泵,同时把石墨热交换器的冷却水阀打开,检查酸泵运行情况、吸收塔的回流情况;
3.5.4从通氯开始,吸收塔开始喷淋吸收生产尾气;
3.5.5正常生产期间,每隔10—12小时,把一级酸贮罐内的盐酸打入指定的酸贮槽,把二级酸贮罐内的盐酸打入一级,并把二级酸贮罐补足水;
3.5.6正常生产期间要巡查酸漏点、泵运行及酸吸收状况。
3.6尾气吸收处理
3.6.1尾气吸收原理为氯气和石灰水中氢氧化钙反应,生成漂液,具体反应方程式为:
2Ca(OH)2+2CL2=Ca(CLO)2+CaCL2+2H2O
3.6.2开启化灰泵,使用高压水枪喷击熟石灰,石灰浆淌入化灰池,3、4、5、6号化一池,7、8号化2池;
3.6.3将化灰池内灰浆打入池循环;
3.6.4开启循环泵和喷淋泵;
3.6.5油炉温度提到200℃后,开启风机抽负压,从盐酸吸收塔出来的气体被真空抽到喷淋塔内,再次被吸收,注意吸收塔喷淋吸收效果;
3.6.6从喷淋塔出来的气体通入清水池吸收、排空。
3.7百菌清的捕集、出料及包装、入库
3.7.1正常生产期间,气态百菌清在捕集器内壁上冷却,结晶成固态(呈粉状);
3.7.2出料前,先开启出料柜引风机,相应打开准备切换使用的捕集器水阀;
3.7.3捕集器有2套,分别为N1,N2,如要使用N2,将此路固定床下部阀门及二捕出口球阀打开,保证无正压现象,相应关闭N1捕集器进出口阀门(注:
此系统作为备用系统,循环使用);
3.7.4出完料后,应清理两只捕集器之间的连接管道,然后打上手孔(注:
两路捕集器之间的物料管道必须每班清理);
3.7.5记录人员填好取样通知单,通知分析人员取样,取样必须是分析人员,并且合成人员在场;
3.7.6每袋原药规定为25±0.1kg,每袋内必须放批号单;
3.7.7经入库人员核对后,安排装卸人员分类码好后,入库时,必须有仓库保管员在场并随即办理入库手续;
附--应急停车、应急操作及停车后的启动程序
根据百菌清产品生产的特点,每间隔10天左右要停车1到2天更换催化剂,在生产期间暴露出来的问题在停车期间集中处理。
突发事故导致的应急停车主要表现为:
停电,设备内部漏油和设备漏氯气。
一、停电
1.氯气岗位人员迅速关闭液氯钢瓶阀和氯气汽化器前氯气阀;
2.记录人员迅速关闭氯气流量计上下阀门,同时把氮气流量由90m3/h调到20m3/h,10分钟后全部关闭;
3.合成人员关闭固定床下保温球阀,系统保持0.1MPa以下的压力,氮气保护催化剂防止系统温度上升;
4.油炉岗位用潮湿的煤炭向炉堂内压火,防止油盘管(炉堂)内导热油高温氧化;
5.来电后,油炉人员开启循环泵,导热油正常循环。
油炉点火提温到工艺要求的温度;
6.合成岗位开启各套系统油泵,保持系统导热油正常循环;
7.合成人员打开固定床下保温球阀,同时向系统通氮气90m3/h;
8.尾气岗位开引风机,酸吸收岗位开启酸泵;
9.氯气人员把缓冲罐压力调整到0.3MPa,通氯气30m3/h,30分钟后,
10.油温提到工艺要求后,合成人员开计量泵;
11.进料后,合成人员调整捕集器负压,这时正常生产;
二、设备内部漏导热油
1.合成岗位出料发现料中有黑色块状物料或有恶臭味,系统的温度超出正常的反应温度,此种条件判断为漏油;
2.班长通知相关岗位人员做好停车准备工作。
3.加料人员停计量泵;
4.氯气岗位人员关闭氯气钢瓶阀和氯气汽化器前氯气阀,并且做好对缓冲罐内氯气的置换工作;
5.记录人员关闭氯气流量计处氯气阀门,同时把氮气由90m3/h调整为110m3/h,对系统进行保护;
6.通知油炉人员把相关的回往低位槽的油阀打开;
7.通知油炉人员关闭相关的油循环泵;
8.合成岗位人员对相关系统进行回油;
9.停车后检查处理,更换催化剂,重新开车。
三、氯气泄露
若系统中出现漏氯影响正常生产的因素,由班长通知协调各岗位进行停车处理
1.氯气岗位缓冲罐、管道等腐蚀漏氯气停车处理:
a.合成加料岗位人员停计量泵;
b.氯气岗位人员关闭氯气钢瓶阀和氯气汽化器前氯气阀;
c.合成岗位记录人员关闭相应系统的氯气阀门,继续向系统内通氮气20m3/h;
d.通知尾气岗位人员做好氯气置换准备工作,氯气岗位人员做好对氯气缓冲罐中的氯气置换。
e.氯气缓冲罐置换为零,再向缓冲罐内部通氮气置换,罐内部或管道经检测无氯气,开始进行处理;
f.将漏点处理后进行试压,经检查,处理完好,通知各岗位准备开车生产;
g.氯气岗位人员将氯气钢瓶阀打开,把缓冲罐压力调整到0.3MPa,通氯气30m3/h,30分钟后;
h.油温提到工艺要求后,合成人员开计量泵;
i.进料后,合成人员调整捕集器负压,这时正常生产
2.合成岗位系统设备腐蚀漏氯气停车处理:
a.合成加料岗位人员停计量泵;
b.氯气岗位人员关闭氯气钢瓶阀氯气汽化器前氯气阀;
c.合成岗位记录人员关闭相应系统的氯气阀门,继续向系统内通氮气;
d.维修处理过程中要把氮气阀门完全关闭,系统保持微负压;
e.办理相关手续后,开始处理;
f.将漏点处理后进行试压,经检查,处理完好,通知各岗位准备开车生产;
g.氯气岗位人员将氯气钢瓶阀打开,把缓冲罐压力调整到0.3MPa,记录人员先开氮气阀门,通90m3/h,再通氯气30m3/h,30分钟后准备开计量泵;
h.油温调整到工艺要求后,合成人员开计量泵;
i.正常进料后,记录人员把氯气由30m3/h调整到正常要求,合成人员调整捕集器负压,这时正常生产
百菌清更换催化剂操作规程
1.六氯上升或含量过低,需停车更换催化剂,先停止向熔化器A内加料,待熔化器内二腈打完,停计量泵,待床内部二腈反应完(流花床1温度低于270℃),关闭氯气钢瓶阀,待氯气缓冲罐内压力小于0.1Mpa,停止向系统内部通氯,并打开尾气真空阀,将缓冲罐内氯气置换完;同时关闭固定床物料阀门,通氮气(0.2Mpa),排汽化器内渣,然后切换油路阀门,开鼓风机对系统油降温,待流1温度降到180℃以下,回系统油,停氮气,放流化床催化剂,待系统中的导热油回尽,开始检修。
2.清理熔化器A、B
2.1待熔化器A、B内油回尽,看熔化器A、B的温度是否低于100℃,然后将熔化器A、B的热电阻拿出来放好,方可进行拆卸;
2.2拆熔化器A、B时,将熔化器A、B的进出口油阀关闭;
2.3拆下熔化器A底部桶体(根据残渣多少而定);
2.4待熔化器A下部桶体拆下时,将桶休内残渣清理干净;
2.5打开熔化器B上盖,将残渣清理干净;
2.6清理干净后将垫子放好,将熔化器A、B装好,将螺栓带死。
3.清理汽化器
3.1清理汽化器前,先将汽化器进山口油阀关闭;
3.2拆下汽化器下封头,将汽化器下封头放到地面上进行清理;
3.3如汽化器桶体里或四壁有二腈残渣,用铁钎将四壁残渣清理干净;
3.4清理干净后,将金属缠绕垫放好,将汽化器下封头装好,把封头螺栓紧死。
4.清理混合器
4.1打开混合器下部盲板,将混合器内杂质清理掉,清理之后将盲板打上。
5更换流化床催化剂与检修流化床下封头
5.l打开流化床下封头盲板将流化床cat放出;
5.2放完催化剂后,用大锤轻击法兰口,将封头内的cat全部落下;
5.3如流化床的催化剂结焦在盘管上时,将流化床下封头拆头进行清理。
清理时,不要将U型管破坏,在清理流化床下封头时也随即检查U型管被腐蚀情况;
5.4清理干净后,将石棉垫放好,将封头装好,将螺栓紧死。
6.更换固定床cat或更换部分固定床cat
6.1如固定床cat需要全部更换的,先将固定床上封头拆下,再拆固定床下封头;
6.2当固定床下封头拆下时,用大锤轻击固定床底部法兰口,让固定床列管内的cat自由落下;
6.3如固定床内的cat结焦过硬,用铁钎或电锤将列管内的cat钻出,使用电锤时一定要注意,以防将列管损坏;
6.4当列管内cat放完后,然后从固定床上封头逐一对列管进行检查,看列管内是否有cat结焦在列管壁,如有,可用钢管将列管内cat刷洗干净后,将下封头装好;
6.5装新的活性炭时,待活性炭装满后,用大锤轻振几下,让列管内cat落实,以防造成装空管现象;
6.6使用大锤振过后,将下封头装好,将上下封头螺栓紧死。
7.清理尾气管道和热交换器
7.1拆下尾气管道,用铁棍或铁钎将管道内百菌清清理干净;
7.2如果管道内物体过硬,可使用火烤(塑料管除外);
7.3清理干净后,将尾气管道连接好;
7.4清理交换器时,一定要轻击,轻敲,不要将设备损坏。
清理后用清水将石墨管冲洗干净后,方可进行安装。
8.清理捕集器
8.1进入捕集器时,必须在停车的情况下方可进入;
8.2进入捕集器前先将人孔及手孔打开,抽负压,保持风道畅通;
8.3入捕集器前,先佩带劳保用品,并且在清理捕集器时必须有二人以上进行临护;
8.4用小铲将捕集器内壁清理干净,即可打死人孔和手孔;
9.尾气岗位检修
9.1尾气处理是百菌清生产的辅助岗位,检修频率随着百菌清生产周期的变化而变化。
9.2尾气岗位检修时,操作人员应将循环池中的漂液打入漂液池,而后停电机;如不合格,停电机,须将灰乳池中半成品通过池底部的胶木球阀放走;
9.3操作人员根据喷淋管、吸收塔堵塞情况,拆塔清理或用清水冲刷;
9.4操作人员可使用铁锹,小铲等工具下池将池中灰垢进行清理;
9.5每次清理结束后,操作人员须向循环池内放半池水,打循环置换半小时后,放掉,重复2次;
9.6检修期间,操作人员应协调电工人员和维修人员对电机、风机进行重点保养和维护。
9.7具体检修的内容应根据生产情况及车间的检修方案进行。
10.检修时各班组一定要按照车间所给定的具体检修计划执行;
11.检修期间所拆下的螺栓螺帽等零配件收拾整齐,以备使用,检修完后,将卫生打扫干净;
12.待所有要检修部位检修完后,对整个生产系统再进行巡检(油路安装,阀门开关等),确保无误后,系统打油提温,紧封头丝,加流化床催化剂,进行一次开车。
具体检修安排须下达工艺通知单(以下例为通知单中A检修部分,B部分催化剂处理、开车附在工艺规程后)
附--相关工艺通知单----停车换X6--1套催化剂(2007.11.07.X)
A.更换催化剂过程
一、停车原因
催化剂活性降低,收率下降,故决定停车整换催化剂。
二、停车前工作安排
1.停止加料,停计量泵,继续汽化系统内二腈,90分钟后关闭流量计处氯气阀门,排汽化器渣((KG、颜色、稠、稀);继续通氯气1小时(油温提到260℃),关闭液氯钢瓶处阀门,待压力降到0.1Mpa以下,置换氯气缓冲罐余氯;
2.切换系统旁路,开鼓风机对系统油降温;
3.降温期间,当班人员检查系统漏点,做标记,同时拆除固定床上、下封头,固定床到流化床间物料管道,流化床下封头,汽化器与混合器连接管道,汽化器下封头封头等接头连接部位保温棉,同时出1到4捕料;放流化床催化剂;待系统油温降到180℃时,关鼓风机,回系统油;
三、停车后工作安排
1.拆固定床上、下封头,清理催化剂,检查列管、赶水孔有无漏点,装KG催化剂进口-14型,装上下封头(清理固定床到流化床之间物料管道);
2.拆流化床下封头,拆清旋风,清理四壁、下封头(检查测温点、油盘管、上部赶水),装,保证密封性良好;
3.拆、清、装汽化器下封头(清理N2进汽化器管道,渣过秤KG);
4.拆、清、装汽化器到混合器物料管道(渣过秤KG);
5.清理混合器(清理CL2加热器到混合器之间管道,渣过秤KG);
6.拆、清一、二级旋风(清理旋风贮罐粉尘,过秤粉尘+=KG);
7.拆、清尾气管道;
8.清理X1—1、X1—2、X2—1、X2—2(过秤KG),X1—3、X1—4、X2—3、X2—4(过秤KG)捕集器;
9.清洗2个流量计,清理流化床压力表;
10.清理捕集器废气吸收池;
11.尾气清理7#、8#喷淋塔(扒球清理检查)、循环池;
工段长审核签名:
时间:
工艺技术员签名:
时间:
班次工作量
应注意事项
拆、清、装内容及时间
需要补充的内容:
清理固下1-1物料大球阀;拆固下2-1物料大球阀修理
百菌清岗位操作法
1加料岗位操作法
1.1加料前先将熔化器的进出口油阀打开,使熔化器A、B预热,待熔化A内加热到150℃后,开启加料引风机准备加料;
1.2向熔化器A内投料,待熔化器内用测量杆能测量到液体二腈为止;
1.3待开车之后,按照车间所给定的指标进行投料(正常100KG/H);
1.4待二腈加完后,立即将熔化器上盖打上,停引风机;
1.5加料人员在当班期间,所投的物料和领用情况必需跟下一班交接清楚
1.6注意事项:
1.6.1在正常投料时,当打开加料口上盖时,操作要迅速,以防止熔化器内气体喷出伤人,加料过程中,面部要尽量靠后,不能直接对加料口,防止熔化器内气体喷出烫伤面部。
1.6.2加料人员在测量熔化器内二腈的余量时,要待测量棒上的二睛凝固冷却后再测量。
1.6.3熔化器A、B的温度要严格按照工艺指标控制,如发现设备滴、漏现象应立即进行处理,不能处理的应向上反应。
2出料岗位操作法
2.1先将备用系统上的三捕球阀打开,再将备用系统上的物料阀门打开;
4.2.2再将上一班次使用过的系统关闭,应先关闭物料阀,再关闭三捕球阀,方可准备进行出料;
2.3打开手孔,用大锤轻击捕集器四壁,让物料自由落下;
2.4待料出完,换三捕布袋,清理系统连接管道,将手孔打上;
2.5待料冷却后方可进行装袋,装完后,将风机关闭。
2.6安全注意事项:
6.1当班人员必须穿戴好劳保用品,严格执行操作规程,不得擅自更改。
2.6.2出料前检查捕集器内是否正压,如正压不可进行出料。
2.6.3拆卸捕集器下部手孔时,如负压过高不可用手直接掀起,
应使用撬棍以防伤人。
2.6.4装料时应检查料中是否有杂质如铁块、螺丝,螺帽等。
3记录岗位操作法
3.1记录人员当班时必须穿好工作服,戴好工作手套,离开工作室要戴好安全帽;
3.2记录人员必须按照规定时间进行记录检查;
3.3记录人员发现温度、压力、流量等不正常时,能处理自己处理,不能处理的及时向班长或车间报告;
3.4记录人员人员必须按照事实的情况记录,不得有错记、漏记、涂改、臆造、瞒报等现象;
3.5记录人员应加强巡检力度,经常检查流量计进出口阀门的压盖,防止漏气;
3.6记录人员在上下班前,一定要要严格按照“五交”及“五不交”制度。
4油炉岗位操作法
4.1准备工作
4.1.1认真学习油路的工作过程。
4.1.2掌握油路系统的流程及正常生产时,系统中各阀门的控制情况。
4.1.3检查所有传动、循环系统是否畅通,仪表是否正常,各阀门开启是否正确。
4.1.4检查炉排箱,出渣机、除尘器是否清理干净。
4.1.5鼓风机、引风机及各阀门调节是否正常。
4.1.6导热油、引火材料和煤是否准备齐全。
4.2启动
4.2.1再次检查各阀门开关是否正确。
4.2.2关闭系统油流经热油泵阀门,打开热油泵出口阀门,启动系统热油循环泵,向系统打油,待低液位灯熄灭后,切换阀门,启动油炉热油循环泵,使油系统成循环状态。
4.2.3向煤斗内加煤。
4.2.4打开炉门,将引燃物置于炉排上。
4.2.5调节煤闸板高度,控制煤层厚度70/90mm,启动引风机、鼓风机,保持炉膛内微负压。
4.3运行
4.3.l点燃引燃物,正常运行时,炉膛内火焰呈亮黄色,无黑烟,出渣无煤。
4.3.2油炉出口温度应控制在250-280℃,进口压力控制在0.4-0.8MPa,并做好运行记录。
4.3.3应巡回检查有关部分是否处于良好状态、各部分振动、冷却、润滑是否正常。
4.3.4应保持和合成岗位及时联系。
4.4停炉
4.4.1将煤闸板摇上,炉排走快档,迅速将炉膛内燃煤走完。
4.4.2切换系统油路,开鼓风机对系统油进行降温。
4.4.3油炉油温降到180℃,停油炉循环泵。
4.4.3待流化床1温度降下180℃以下时,停系统热油循环泵,打开放油阀,将系统内导热油全部放入储油槽。
4.5注意事项
4.5.1正常运行过程中,若压差或油温过高,注意切换系统旁路。
4.5.2正常工作时,高位槽内导热油保持高液位。
低位槽内导热油保持低液位。
4.5.3每天应对油泵等机械的润滑点注油。
4.5.4紧急停炉时应压火,不能用水冲洗炉膛。
5入库岗位操作法
5.1入库人员抽查原料是否够称,将质检科发放的合格证放入袋中,将外袋口扎好。
5.2根据要求把产品运到仓库或叫车间,必须分批码放整齐,不得乱堆乱放,防止码放不牢百