塑料仪表盖注塑模具设计.docx
《塑料仪表盖注塑模具设计.docx》由会员分享,可在线阅读,更多相关《塑料仪表盖注塑模具设计.docx(36页珍藏版)》请在冰豆网上搜索。
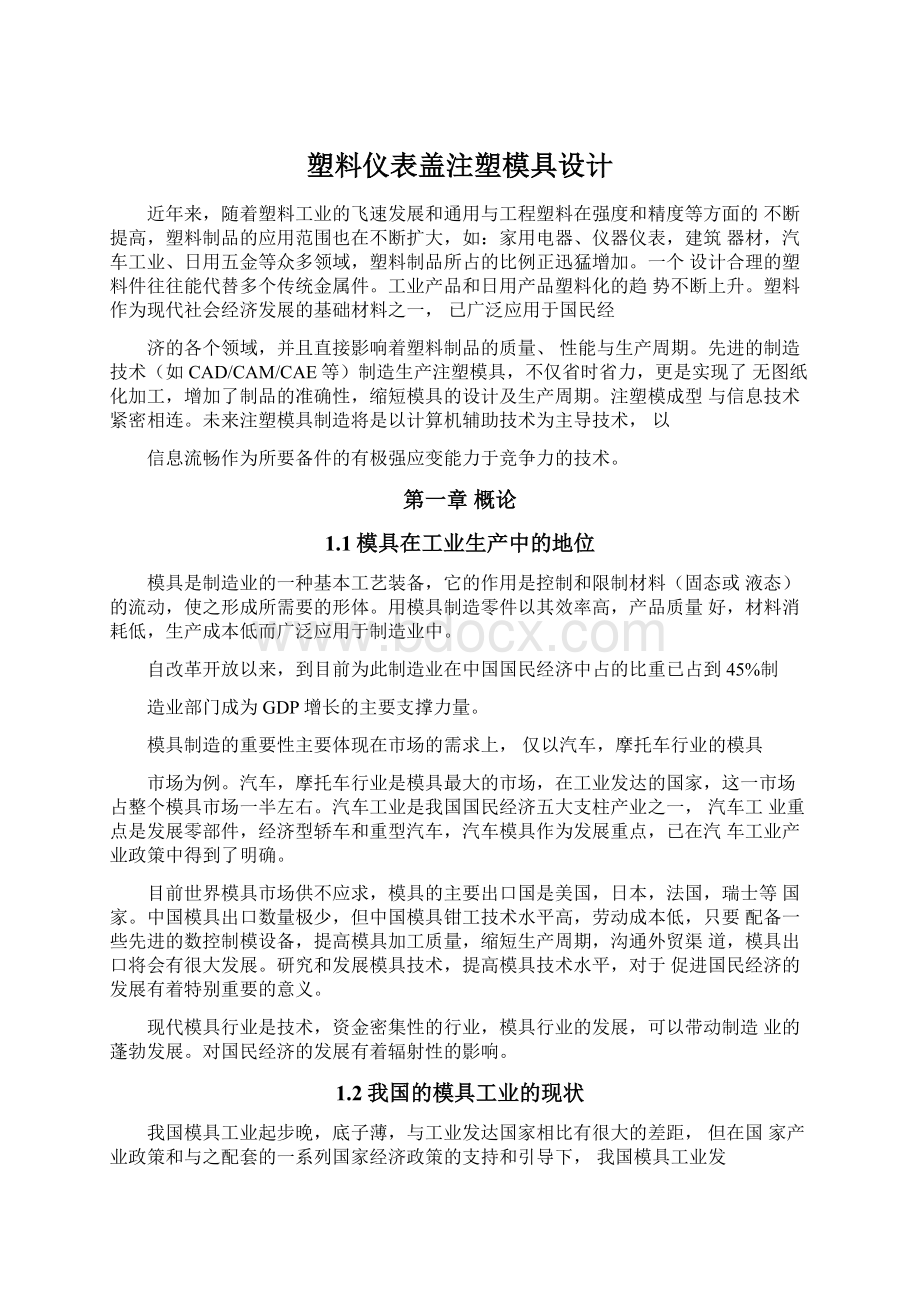
塑料仪表盖注塑模具设计
近年来,随着塑料工业的飞速发展和通用与工程塑料在强度和精度等方面的不断提高,塑料制品的应用范围也在不断扩大,如:
家用电器、仪器仪表,建筑器材,汽车工业、日用五金等众多领域,塑料制品所占的比例正迅猛增加。
一个设计合理的塑料件往往能代替多个传统金属件。
工业产品和日用产品塑料化的趋势不断上升。
塑料作为现代社会经济发展的基础材料之一,已广泛应用于国民经
济的各个领域,并且直接影响着塑料制品的质量、性能与生产周期。
先进的制造技术(如CAD/CAM/CAE等)制造生产注塑模具,不仅省时省力,更是实现了无图纸化加工,增加了制品的准确性,缩短模具的设计及生产周期。
注塑模成型与信息技术紧密相连。
未来注塑模具制造将是以计算机辅助技术为主导技术,以
信息流畅作为所要备件的有极强应变能力于竞争力的技术。
第一章概论
1.1模具在工业生产中的地位
模具是制造业的一种基本工艺装备,它的作用是控制和限制材料(固态或液态)的流动,使之形成所需要的形体。
用模具制造零件以其效率高,产品质量好,材料消耗低,生产成本低而广泛应用于制造业中。
自改革开放以来,到目前为此制造业在中国国民经济中占的比重已占到45%制
造业部门成为GDP增长的主要支撑力量。
模具制造的重要性主要体现在市场的需求上,仅以汽车,摩托车行业的模具
市场为例。
汽车,摩托车行业是模具最大的市场,在工业发达的国家,这一市场占整个模具市场一半左右。
汽车工业是我国国民经济五大支柱产业之一,汽车工业重点是发展零部件,经济型轿车和重型汽车,汽车模具作为发展重点,已在汽车工业产业政策中得到了明确。
目前世界模具市场供不应求,模具的主要出口国是美国,日本,法国,瑞士等国家。
中国模具出口数量极少,但中国模具钳工技术水平高,劳动成本低,只要配备一些先进的数控制模设备,提高模具加工质量,缩短生产周期,沟通外贸渠道,模具出口将会有很大发展。
研究和发展模具技术,提高模具技术水平,对于促进国民经济的发展有着特别重要的意义。
现代模具行业是技术,资金密集性的行业,模具行业的发展,可以带动制造业的蓬勃发展。
对国民经济的发展有着辐射性的影响。
1.2我国的模具工业的现状
我国模具工业起步晚,底子薄,与工业发达国家相比有很大的差距,但在国家产业政策和与之配套的一系列国家经济政策的支持和引导下,我国模具工业发
迅速。
据统计,我国(未包括香港、台湾、澳门)现有模具生产厂近2万家,从
业人员约50万人,九五”期间的年增长率为13%,2000年总产值为270亿元,占世界总量的5%。
但从总体上看,自产自用占主导地位,商品化模具仅为1/3
左右,国内模具生产仍供不应求,特别是精密、大型、复杂、长寿命模具,仍主要依赖进口。
目前,就整个模具市场来看,进口模具约占市场总量的20%左右,其中,中高档模具进口比例达40%。
因此,近年来我国模具发展的重点放在精密、大型、复杂、长寿命模具上,并取得了可喜的成绩,模具进口量下降,模具技术和水平也有长足的进步。
目前,我国的模具正处在告诉增长时期,尤其是塑料模具近年来发展相当快,2002年已猛增到140亿元左右。
当前国内塑料模具市场以塑料模具需求量最大,其中发展重点为工程塑料模具,这是与工程塑料的快速发展分不开的。
预测塑料建材件模具需求量将增长较快。
但是,我们国家的模具产业并不是完美的。
虽然我国模具总量目前已达到相当规模,模具水平也有很大提高,但设计制造水平总体上落后于德、美、日、法、意等工业发达国家许多。
当前存在的问题和差距主要表现在以下几方面:
(1)总量供不应求
国内模具自配率只有70%左右。
其中低档模具供过于求,中高档模具自配率只有50流右。
(2)企业组织结构、产品结构、技术结构和进出口结构均不合理
我国模具生产厂中多数是自产自配的工模具车间(分厂),自产自配比例高达60%左右,而国外模具超过70%属商品模具。
专业模具厂大多是“大而全”、“小而全”的组织形式,而国外大多是“小而专”、“小而精”。
国内大型、精密、复杂、长寿命的模具占总量比例不足30%而国外在50%以上。
2004
年,模具进出口之比为3.7:
1,进出口相抵后的净进口额达13.2亿美元,为世界模具净进口量最大的国家。
(3)模具产品水平大大低于国际水平,生产周期却高于国际水平
产品水平低主要表现在模具的精度、型腔表面粗糙度、寿命及结构等方面。
(4)开发能力较差,经济效益欠佳
我国模具企业技术人员比例低,水平较低,且不重视产品开发,在市场中经常处于被动地位。
我国每个模具职工平均年创造产值约合1万美元,国外模具工业发达国家大多是15〜20万美元,有的高达25〜30万美元,与之相对的是我国相当一部分模具企业还沿用过去作坊式管理,真正实现现代化企业管理的企业较少。
造成上述差距的原因很多,除了历史上模具作为产品长期未得到应有的重视,以及多数国有企业机制不能适应市场经济之外,还有下列几个原因:
1国家对模具工业的政策支持力度还不够
虽然国家已经明确颁布了模具行业的产业政策,但配套政策少,执行力度弱。
目前享受模具产品增值税的企业全国只有185家,大多数企业仍旧税负过重。
模具企业进行技术改造引进设备要缴纳相当数量的税金,影响技术进步,而
且民营企业贷款十分困难。
2人才严重不足,科研开发及技术攻关投入太少
模具行业是技术、资金、劳动密集的产业,随着时代的进步和技术的发展,掌握并且熟练运用新技术的人才异常短缺,高级模具钳工及企业管理人才也非常紧张。
由于模具企业效益欠佳及对科研开发和技术攻关重视不够,科研单位
和大专院校的眼睛盯着创收,导致模具行业在科研开发和技术攻关方面投入太少,致使模具技术发展步伐不大,进展不快。
3工艺装备水平低,且配套性不好,利用率低
近年来我国机床行业进步较快,已能提供比较成套的高精度加工设备,但与国外装备相比,仍有较大差距。
虽然国内许多企业已引进许多国外先进设备,但总体的装备水平比国外许多企业低很多。
由于体制和资金等方面的原因,引进
设备不配套,设备与附件不配套现象十分普遍,设备利用率低的问题长期得不到较妥善的解决。
4专业化、标准化、商品化程度低,协作能力差
由于长期以来受“大而全”“小而全”影响,模具专业化水平低,专业分工不细致,商品化程度低。
目前国内每年生产的模具,商品模具只占40%左
右,其余为自产自用。
模具企业之间协作不畅,难以完成较大规模的模具成套任务。
模具标准化水平低,模具标准件使用覆盖率低也对模具质量、成本有较大影响,特别是对模具制造周期有很大影响。
5模具材料及模具相关技术落后
模具材料性能、质量和品种问题往往会影响模具质量、寿命及成本,国产模具钢与国外进口钢材相比有较大差距。
塑料、板材、设备性能差,也直接影响模具水平的提高。
1.3我国模具行业的发展趋势⑴
1模具日趋化。
2模具的精度将越来越高。
10年前精密模具的精度一般为5微米,现已达到2-3微米。
1微米精度的模具也将上市。
3多功能复合模具将进一步发展。
4热流道模具在塑料模具中的比重将逐渐提高。
5随着塑料成型工艺的不段发展与改进,气辅模具及适应高压注塑成型等工艺的模具也将随之发展。
6标准件的应用将日益广泛。
模具标准化及模具标准件的应用将极大地影响模具制造周期,还能提高模具的质量和就降低模具制造成本。
7快速经济模具的前景十分广阔。
8随着车辆和电机等产品向轻量化发展,压铸模的比例将不断提高。
同时对压铸模的寿命和复杂程度也将提出越来越高的要求。
9以塑代钢、以塑代木的进程一步加快,塑料模具的比例将不断增大。
由于机械零件的复杂程度和精度的不断提高,对塑料模具的要求也越来越高。
10模具技术含量将不断提高。
第二章仪表盖的结构设计
2.1设计要求
表2-1零件尺寸要求
单位:
mm
材
料
尺寸序号
A
B
C
D
E
F
G
H
I
ABS
90
80
50
4
4
72
9
6
54
2.2塑件成型工艺的可行性分析及修改说明
产品的可行性分析主要包括:
产品尺寸精度分析;脱模斜度检测;塑件厚度及其均匀性检测;圆角设计。
塑件的修正:
对于塑件的精度、壁厚、拔模斜度、圆角等不合理之处加以更正说明,在不影响使用的前提下提出合理可行性的更正措施,以利于工业生产。
2.2.1塑件材料及产品精度分析
该塑件选用ABS塑料。
ABS(丙烯腈一丁二烯一苯乙烯共聚物)综合性能较好、吸湿性强,含水量应小于0.3%,成型前必须进行充分干燥;有较高的冲击强度、收缩率在0.3%-0.8%范围内,流动性较差,应选较高的料温和模温,但料温过高易分解,所以料温应选择在210C—260C。
塑件要求表面光洁,模温应选25C—70C。
选用螺杆式注塑机,注射压力为50—100Mp。
ABS具有良好的成型加工性,制品表面光洁度高,且具有良好的涂装性和染色性,可电镀成多种色泽。
ABS的成型特性:
成型温度:
200-240C干燥条件:
80-90C2小时
(1)无定形料,流动性中等,吸湿大,必须充分干燥,表面要求光泽的塑件须长时间预热干燥80-90度,3小时。
(2)宜取高料温,高模温,但料温过高易分解(分解温度为>270C)。
对精度较高的塑件,模温宜取50-60度;对高光泽.耐热塑件,模温宜取60〜80C。
(3)如需解决夹水纹,需提高材料的流动性,采取高料温、高模温,或者改变入水位等方法。
(4)如成形耐热级或阻燃级材料,生产3-7天后模具表面会残存塑料分解物,导致模具表面发亮,需对模具及时进行清理,同时模具表面需增加排气位置。
ABS的工艺特点:
ABS树脂ABS树脂是丙烯腈、聚丁二烯和苯乙烯三种单体共聚而成的。
其中丙烯腈使之有较高的硬度,表面光泽;聚丁二烯能增加韧性;苯乙烯则使加工性能良好。
因而ABS树脂具有综合性能较好,冲击韧度高,化学性能稳定,电性能好,与372有机玻璃的熔接性好,制成双色塑件,而且表面可以有镀层,适合制作一般塑件、件耐磨零件、传动零件等。
其成型工艺性如下:
(1)无定性料,吸湿大,不易分解,必须充分干燥,表面要求干燥的零件需长时间预热干燥。
(2)宜取高料温、高模温,但是要防止温度过高发生分解(分解温度大于250°C),对于精度要求高的塑件,模具温度宜取50°C〜60°C,对光泽耐热塑件,模温取60600C〜80600C
2.2.2脱模斜度设计
由于注塑件在开模冷却时会产生收缩,对型芯产生一个包紧力,所给标准塑件没有设置脱模斜度,使得塑件脱模困难,过大的推出力推出时易拉坏插伤塑件。
在不影响塑件使用的前提下,为了便于塑件脱模,在塑件的内外表面沿脱模方向设计一定的脱模斜度。
表2-2单边脱模斜度推荐值[3]
脱模咼度\mm
>18~30
>30~50
>50~80
续表2-2
ABS
145'
130'
115'
塑件内外表面的脱模高度为40mm,所以外表面脱模斜度取1°,内表面脱模斜度取1.5°。
2.2.3塑件壁厚分析
塑件壁厚对质量的影响[3]:
壁厚过小:
成型时流动阻力大,熔体难以充满型腔;
壁厚过大:
易产生气泡、缩孔、翘曲等缺陷;增加冷却时间,降低生产效率
最大壁厚
常用壁厚
最小壁厚
9
4
4
表2-3ABS的建议壁厚值
[3]
单位:
mm
分析结果:
壁厚均匀满足厚度要求且为常用壁厚,所以塑件壁厚合理。
2.2.4圆角设计
塑件除特殊要求的圆角之和塑件某些特殊部位如分型面、型芯和型腔配合处
不便作圆角,而只能采用尖角外,其余所以转角处均应尽采用圆角过度,因为制
件尖角处易产生应力集中,导致塑件制件破裂或失效;同时圆角过度使料流平滑绕过,大大改善了塑料的冲模特性;塑件设计成圆角,尤其是外圆角,使模具型腔对应部位也是圆角,增加了模具的坚固性。
通常塑件理想的内圆角半径应有壁厚的1/4以上[3]。
这里因塑件外圆角半径为4mm,塑件内圆角设为3mm。
2.3修正后的产品图
如图2-2所示
2-2修改后的塑件的工件图与零件图
第三章模具结构设计
3.1分型面位置的确定
分型面的选择原则⑴:
(1)便于塑件脱模,尽量使塑件开模时留在动模一侧。
(2)分型面应尽量选在塑件的最大截面处。
(3)有利于保证塑件的精度要求。
(4)有利于浇注系统、排气系统、冷却系统的设置和模具型腔的加工
(5)便于嵌件的安装。
确定结果:
分型面选在塑件的投影面最大的部位,如图3-1o
图3-1分型面的选择
3.2型腔数量和排列方式的确定
3.2.1型腔数量的确定
模具型腔数量的确定要综合考虑塑件的技术质量要求、产品的生产数量、塑
料的种类、塑件的形状、塑件的加工成本、注塑机的额定最设量和锁模力等因素。
单腔模具、多腔模各自的缺点和使用范围:
单型腔模具结构相对简单,设计自由度较大,成型塑件的形状和尺寸的一致性好,塑件精度较高;多型腔模具的结构复杂,生产效率高,分配到单个塑件上的成本低。
单型腔模具宜用于大型或精度要求较高的塑件的注塑成型,多型腔模具特别使用于精度要求不是很高、结构较易冲型的中小型塑件的大批生产。
型腔数量的确定:
因本次设计的塑料罩类零件的精度要求不高;注塑用塑料
ABS型性能良好;塑件属小型塑件。
综合塑件的尺寸,考虑到模具制造费用、设备运转费用低一些,这里初步拟定采用一模四腔的模具成型。
322产品布局
型腔排列形式采用矩形对称布局,如图3-2所。
图3-2型腔排列方式
第四章注塑机型号的选择
4.1注塑成型工艺简介
注塑成型是利用塑料的可挤压性与可模塑性,首先将松散的粒状或粉状成型物料从注塑机的料斗送入高温的机筒内加热熔融塑化,使之成为粘流状态熔体,然后在柱塞或螺杆的高压推动下,以很大的流速通过机筒前端的喷嘴注射进入温度较低的闭合模具中,经过一段时间的保压冷却以后,开启模具便可以从模腔中脱出具有一定形状和尺寸的塑料制件。
一般分为三个阶段的工作。
A
图4-1注塑成型压力一时间曲线
(1)物料准备成型前应对物料的外观色泽、颗粒情况、有无杂质等进行检验,并测试其热稳定性、流动性和收缩率等指标。
对于吸湿性强的塑料,应根据
注射成型工艺允许的含水量进行适当的预热干燥,若有嵌件,还要知道嵌件的热膨胀系数,对模具进行适当的预热,以避免收缩应力和裂纹,有的塑料制品还需要选用脱模剂,以利于脱模。
(2)注塑过程塑料在料筒内经过加热达到流动状态后,进入模腔内的流动
可分为注射、保压、倒流和冷却四个阶段,注塑过程可以用如图所示3-1所示。
图中to代表螺杆或柱塞开始注射熔体的时刻;当模腔充满熔体(t=t1)时,熔体压力迅速上升,达到最大值Po。
从时间t1到t2,塑料仍处于螺杆(或柱塞)的压力下,熔体会继续流入模腔内以弥补因冷却收缩而产生的空隙。
由于塑料仍在流动,
而温度又在不断下降,定向分子(分子链的一端在模腔壁固化,另一端沿流动方向排列)容易被凝结,所以这一阶段是大分子定向形成的主要阶段。
这一阶段的
时间越长,分子定向的程度越高。
从螺杆开始后退到结束(时间从t2到tj,由于模腔内的压力比流道内高,会发生熔体倒流,从而使模腔内的压力迅速下降。
倒流一直进行到浇口处熔体凝结时为止。
其中,塑料凝结时的压力和温度是决定塑料制件平均收缩率的重要因素。
(3)制件后处理由于成型过程中塑料熔体在温度和压力下的变形流动非常复杂,再加上流动前塑化不均匀以及充模后冷却速度不同,制件内经常出现不均
匀的结晶、取向和收缩,导致制件内产生相应的结晶、取向和收缩应力,脱模后除引起时效变形外,还会使制件的力学性能,光学性能及表观质量变坏,严重时会开裂。
故有的塑件需要进行后处理,常用的后处理方法有退火和调湿两种。
退火是为了消除或降低制件成型后的残余应力,此外,退火还可以对制件进行解除取向,并降低制件硬度和提高韧性,温度一般在塑件使用温度以上的10~20度至热变形温度以下10~20度之间;调湿处理是一种调整制件含水量的后处理工序,主要用于吸湿性很强、而且又容易氧化的聚酰胺等塑料制件。
调湿处理所用的加热介质一般为沸水或醋酸钾溶液(沸点为121C,加热温度为100〜121C),保温时间与制件厚度有关,通常取2〜9小时。
4.2注塑成型工艺条件
ABS的注射工艺参数
1注射机类型:
螺杆式。
2喷嘴形式:
通用式
3料筒温度(t/C);后段150〜170;
中段180〜190;
前段200〜210。
4喷嘴温度(t/C):
180〜190.
5模具温度(t/C):
50〜60。
6注射压力(MPa):
60〜100。
7保压压力(MPa:
40〜60。
8成型时间(Ts):
注射20〜90;高压0〜5;
成型周期15~30;冷却5~15
注:
螺杆带止回环。
9后处理:
方法——红外线烘箱
温度(70)
时间(0.3――1)
红外线灯、烘箱;
温度(t/C)――70;
时间(Th)——2〜4。
表4-1ABS的主要技术指标[4]
密度p/(g/cm3)
1.13~1.14
拉伸弹性模量E/GPa
1.8X103
比体积u/(dm3/kg-1)
0.86~0.98
抗弯强度/MPa
80
吸水率24h/pfr100
0.2〜0.4
拉伸强度MPa
35~49
收缩率s
0.3〜0.8
硬度HR
62~86
熔点t/C
130〜160
体积电阻系数V/(cm)
1015
弯曲弹性模量Gpa
50
热变形温度t/C
65~98
4.3按预选型腔数选择注塑机
4.3.1注塑机的初步选择原则
1)ms,m
2)FFm
式中ms0最大注塑量(g或cm3)
F――注塑机的额定锁模力(N)
Fm――注塑所需的锁模力(N)
m一次注塑所需塑料量(g或cm3)
(1)注塑量的计算
m$m
其中mi――成型单个塑件所需的塑料量(g或cm3)
n――型腔个数
1.6――折算系数(将浇注系统的塑料量折算成0.6ng)
塑件体积V仁71.40cm3
塑件质量M仁pXV=78.54g
由于尺寸此次设计的模具采用的是一模四腔,所以塑件的总体积和总质量分别为
V=4V1=4X71.40=285.60cm3
M=4M仁4X78.54=314.6g
所以Vso》V=1.6X285.60=457.0cm3
Mso>M=1.6X314.6=503.4g
(2)锁模力计算
FFm
Fm1.35nAp型(4-2)
式中A――单个塑件在分型面上的投影面积(mm2)
n――型腔个数
1.35――将浇注系统在分型面上的投影面积折算成0.35nA
p型——塑料熔体对型腔的平均压力(MPa)
投影面积A1=6358.5mm2
根据查参考文献[2]表2-2取p型=35MPa
6
所以Fm=1.35X4X6358.5X10X40X106=1202KN
Ms0=503.4g
F>1202KN4.3.2注塑机型号的选择
由上面计算得到的m和Fm值来选择注塑机,注塑机的最大注射量(额定注
射量G)和额定锁模力F应满足
G>m=629.25g
式中一一注塑机最大注射量的利用系数一般取0.8
F>1202KN
初步选择SZ-400/1600型注塑机
表4-2LY240型(卧式)注塑机主要参数[4]
最大注射容量/cmB
799
拉杆内间距/mm
560560
螺杆直径/mm
65
开模行程/mm
500
注射压力/MPa
153
最大模具厚度/mm
520
注射速率/(g/s)
187
最小模具厚度/mm
220
塑化能力/(g/s)
48
推出行程/mm
150
螺杆转速/(r/min)
10〜170
锁模形式
双曲肘
锁模力/kN
2400
喷嘴
球半径SR/mm
14
定位孔直径/mm
120
孔直径/mm
5
4.3.3注塑机参数校核
(1)塑化能力M(g/s)校核
(4-3)
塑化能力必需满足M>m=16.78g.s<<48.01g/st
式中m——一次注塑所需塑料量
t――成型周期,取30s
校核结果:
注塑机的塑化能力满足要求
(2)注射压力Fe校核
Fe>KF0=1.3X117=152.1MPav153MFa
Fe――注塑机的额定注塑压力(MPa)
P。
一一塑件成型时所需要的注射力(MPa)
k――注塑压力安全系数,一般取k=1.25~1.4
因成型时塑料熔体对型腔的平均压力P型一般是注射压力Po的30%~65%,
P0=P型/0.65~P型/0.3=53.8MPa~116.7MPa,取Po=117MPa
校核结果:
注塑机的注射压力不满足要求
(3)锁模力校核
F>koFm=1.2X1202=1442.4KNV2400KN(4-5)
式中k。
——锁模力安全系数,一般取k。
1.1~1.2
校核结果:
注塑机的锁模力满足要求
通过校核可知,所选注塑机符合要求。
第五章模具设计
5.1模架的选择
模具的大小主要取决于塑件的大小和结构,对于模具而言,在保证足够强度和刚度的条件下,结构越紧凑越好。
为节约模具钢材和便于热处理,根据产品的外形尺寸,可以确定镶件(模仁)的外形尺寸,确定镶件的尺寸后,就可以大致确定模架的大小。
5.1.1模仁尺寸的确定
单个塑件在分型面上的投影面积为6358.5mm2,
5-1模仁的外型尺寸
根据上图模仁的外型尺寸可取300mmx300mm,上下模仁的高度分别为90mm和40mm,模架外形尺寸长x宽x高=500mmx500mmx516mm。
(选用龙记细水口的CI型)图5-2所示
图5-2模架类型
5.1.2注塑机的再次校核与确定
(1)注塑机安装尺寸的校核
拉杆间距校核:
模架的板面尺寸500x500,
所选注塑机的拉杆间距为560x560,拉杆宽度>模具宽度,拉杆间距合格;
模具高度校核:
模具高度516>最小模具厚度220,校核合格;
开模行程校核:
开模行程H是指从模具中取出塑件所需的最小开合距离,它必须小于注塑机的动模板的最大行程S。
因选注塑机是双曲肘结构(即开模行程与模具厚度无关)且是单分型面注射模,所以模具开模行程H=60(顶出行程)+166.1
(浇注系统凝料高度)+(8~10)=234.1~236.1<500注塑机移模行程S)合格。
综合以上各项校核可知LY240型(卧式)注塑机的各项参数均合格。
结论:
通过各项校核,确定选择LY240型(卧式)注塑机。
5.2浇注系统的设计
浇注系统控制着塑件在注塑成型过程中充模和补料两个重要阶段,对塑件质量关系极大。
浇注系统是指从注塑机喷嘴进入模具开始,到型腔入口为此的那一段流道,对于多型腔模具,浇注系统包括主流道、分流道、浇口、冷料井。
如
5-3图所示
图5-3浇注系统的组成
521主流道设计
紧接注塑机喷嘴,与注塑机喷嘴在同一直线上,主流道形状一般为圆形和圆
锥形,为便于冷料流