火力发电厂凝汽器化学清洗及成膜导则全解.docx
《火力发电厂凝汽器化学清洗及成膜导则全解.docx》由会员分享,可在线阅读,更多相关《火力发电厂凝汽器化学清洗及成膜导则全解.docx(15页珍藏版)》请在冰豆网上搜索。
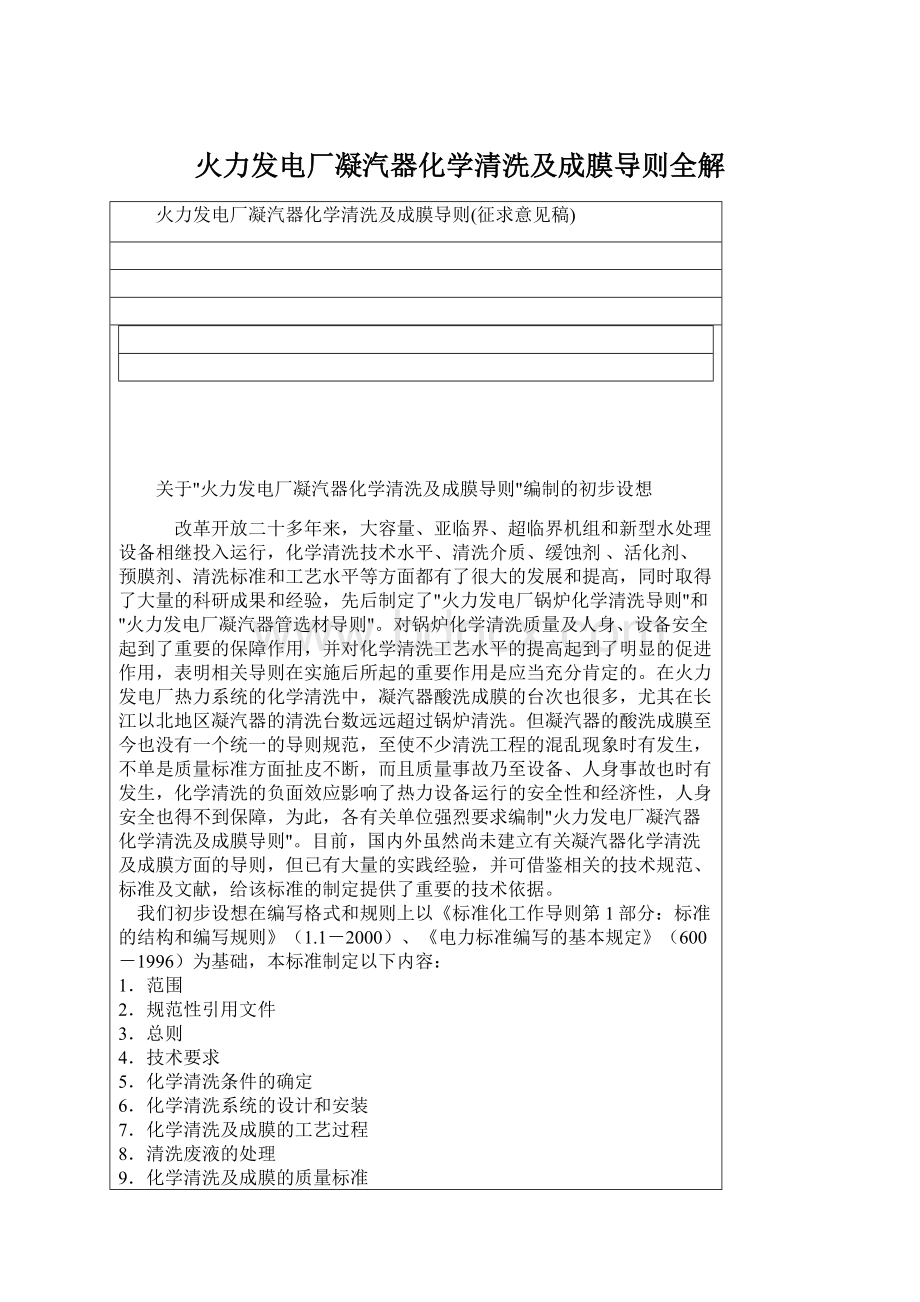
火力发电厂凝汽器化学清洗及成膜导则全解
火力发电厂凝汽器化学清洗及成膜导则(征求意见稿)
关于"火力发电厂凝汽器化学清洗及成膜导则"编制的初步设想
改革开放二十多年来,大容量、亚临界、超临界机组和新型水处理设备相继投入运行,化学清洗技术水平、清洗介质、缓蚀剂、活化剂、预膜剂、清洗标准和工艺水平等方面都有了很大的发展和提高,同时取得了大量的科研成果和经验,先后制定了"火力发电厂锅炉化学清洗导则"和"火力发电厂凝汽器管选材导则"。
对锅炉化学清洗质量及人身、设备安全起到了重要的保障作用,并对化学清洗工艺水平的提高起到了明显的促进作用,表明相关导则在实施后所起的重要作用是应当充分肯定的。
在火力发电厂热力系统的化学清洗中,凝汽器酸洗成膜的台次也很多,尤其在长江以北地区凝汽器的清洗台数远远超过锅炉清洗。
但凝汽器的酸洗成膜至今也没有一个统一的导则规范,至使不少清洗工程的混乱现象时有发生,不单是质量标准方面扯皮不断,而且质量事故乃至设备、人身事故也时有发生,化学清洗的负面效应影响了热力设备运行的安全性和经济性,人身安全也得不到保障,为此,各有关单位强烈要求编制"火力发电厂凝汽器化学清洗及成膜导则"。
目前,国内外虽然尚未建立有关凝汽器化学清洗及成膜方面的导则,但已有大量的实践经验,并可借鉴相关的技术规范、标准及文献,给该标准的制定提供了重要的技术依据。
我们初步设想在编写格式和规则上以《标准化工作导则第1部分:
标准的结构和编写规则》(1.1-2000)、《电力标准编写的基本规定》(600-1996)为基础,本标准制定以下内容:
1.范围
2.规范性引用文件
3.总则
4.技术要求
5.化学清洗条件的确定
6.化学清洗系统的设计和安装
7.化学清洗及成膜的工艺过程
8.清洗废液的处理
9.化学清洗及成膜的质量标准
10.化学清洗中的化学监督
11.安全保证体系
--为确保清洗质量,明确了承担火电厂凝汽器化学清洗单位,应经资质审查合格后才能负责凝汽器化学清洗工作,严禁无证清洗,并应健全质量体系,完善各项管理制度。
--参考了国内外(美国)有关化学清洗质量控制腐蚀速度的标准。
--由于水处理技术有了很大的发展,循环水增加了水质稳定剂的药剂处理、胶球处理和成膜处理。
提高了管材的耐蚀性,使凝汽器管的泄漏率有所减少,给水质量有了明显的提高。
又由于我国北方地区水资源短缺,循环水浓缩倍率成倍增加,使金属内表面结垢速率上升,凝汽器管的酸洗周期缩短。
因此,运行机组凝汽器管的清洗间隔时间主要根据换热管上沉积的垢量和凝汽器的端差决定。
--本导则准备增设清洗工艺的不同使用条件相关条款。
--准备增设可供选择的清洗介质、缓蚀剂、活化剂和预膜剂的品种,并补充产品质量标准和验收方法。
--推荐新的清洗工艺和成膜工艺技术。
--准备增设清洗范围及系统;清洗及成膜的质量控制标准;对不同材质凝汽器选择相适宜的清洗介质、缓蚀剂、活化剂和预膜剂;选择科学合理的清洗工艺和成膜工艺。
--准备增设并指明哪些附录是规范性附录,哪些是资料性附录。
--本标准由电力行业电厂化学标准化技术委员会提出。
--本标准由西安协力动力化学有限责任公司归口。
--标准的起草单位:
西安协力动力化学有限责任公司、国电热工研究院、北京电力建设公司;
--本标准的主要起草人:
杨振乾、张全根、陈洁、陈子华。
--本标准委托西安协力动力化学有限责任公司负责解释。
上述编写大纲内容供大家讨论,主要目的是抛砖引玉,看看内容是否再增加或删减,谢谢!
2002年5月15日
—
引 言
由于我国水资源短缺,循环水浓缩倍率增加较快,加剧了凝汽器铜管的结垢和腐蚀,从而缩短了凝汽器化学清洗及成膜的周期,目前国内凝汽器化学清洗及成膜的机组每年在百台以上。
国内虽开展此项工作己有四十余年,至今国内仍无统一的技术规范和质量标准,其间由化学清洗引起的凝汽器质量人身事故也时有发生,严重影响了热力设备运行的安全性和经济性。
为此,有必要制定"火力发电厂凝汽器化学清洗及成膜导则"。
目 次
前言
引言
1 范围
2 规范性引用文件
3. 总则
4. 技术要求
5. 化学清洗条件的确定
6. 化学清洗系统的设计与安装
7. 化学清洗工艺过程
8. 清洗废液处理
9. 化学清洗成膜质量指标
10. 化学清洗中的化学监瞀
11. 安全保证体系
附录A(标准的附录)化学清洗中的测试方法
附录B(标准的附录)清洗用药品(包括酸、碱、缓蚀剂、活化剂、予膜剂)的产品质量标准和检验方法
附录C(资料性附录)各种牌号凝汽器管的主要成分及杂质含量对照表
中华人民共和国电力行业标准
火力发电厂凝汽器化学清洗及成膜导则 ×××-200×
1. 范围
本标准规定了火力发电厂凝汽器化学清洗及成膜的技术要求、工艺、质量指标和试验方法。
本标准适用于铜及其合金、钛及其合金、不锈钢制成的凝汽器管和管板。
在其表面主要是结有钙镁水垢、硅垢、泥砂和污泥的化学清洗及成膜。
2. 规范性引用文件
下列标准所包含的条文,通过在本标准中引用而构成为本标准的条文。
本标准出版时,所示版本均为有效。
所有标准都会被修订,使用本标准的各方应探讨使用下列标准最新版本的可能性。
B600-1997钛和钛合金表面除鳞与清洗标准
A380-1999不锈钢零件、设备及系统的清洗和除锈
12145-1999火力发电机组蒸汽动力设备水汽质量
8978-1996污水综合排放标准
3935.1-1996标准化和有关领域的通用术语第1部分:
基本术语
20001.4标准编写规则第1部分:
化学分析方法(78-2--2:
)
794-2001火力发电厂锅炉化学清洗导则
712-2000火力发电厂凝汽器管选材导则
561-1995火力发电厂水汽化学监督导则
523-1993盐酸酸洗缓蚀剂应用性能评价指标及浸泡腐蚀试验方法
2387-1992工业设备化学清洗质量标准
3. 总则
3.1 凝汽器的化学清洗及成膜,是使热交换面内表面清洁、防止热交换面因腐蚀和结垢引起事故的必要措施,同时也是提高凝汽器真空度、提高热交换率、改善水汽品质的有效措施之一。
3.2 承担火电厂凝汽器化学清洗单位,应具备相应的资质,严禁无证清洗。
3.3 凝汽器的化学清洗及成膜,应由专业技术人员制定清洗方案和措施,经技术负责人或有关领导审核、批准。
清洗过程中应有技术部门进行清洗过程的质量监督,清洗结束后,由甲、乙双方技术人员对清洗质量进行检查、评定。
3.4 负责清洗的单位应对参加化学清洗人员进行技术和安全教育培训,使其熟悉清洗系统,掌握安全操作程序。
3.5 清洗范围
3.5.1 新建亚临界机组宜进行凝汽器的清洗成膜,其范围包括凝汽器管的水侧和水室。
为减少凝汽器管的结垢和腐蚀有的厂在新机安装后对闭式循环水系统先用磷酸三钠或高效除油剂进行除油清洗,再用盐酸清洗除去表面残碳膜,最后进行成膜处理,提高合金管的耐蚀性能。
3.5.2 运行机组凝汽器清洗的确定
在机组大修或小修前应观察凝汽器的端差和真空度。
当出现异常(端差>8℃)时,应安排抽管检查凝汽器管外壁有无腐蚀或磨损减簿;内壁结垢、粘泥及腐蚀程度。
当内壁结垢>0.5㎜,腐蚀或磨损减簿>0.02㎜时,该设备为三类设备应安排水冲洗,在部分换管后进行化学清洗和成膜处理。
3.6 化学清洗的方式为循环清洗。
3.7 酸洗液中应添加与其相匹配的缓蚀剂和还原剂,如有必要还应添加其它助剂。
清洗的质量指标应符合本标准9.1~9.5。
3.8 凝汽器化学清洗的水源、电源、压缩空气气源应充足安全可靠。
3.9 工作人员在化学清洗过程中应严格遵守安全规程,严格执行化学清洗安全措施,确保人身、设备安全。
根据国家劳动保护法的有关规定和实际需要,参加化学清洗人员应享有劳动保健的待遇。
4. 技术要求
4.1 在制订化学清洗施工方案及现场清洗措施时,除应符合相关的标准外,还应符合与设备相关的技术条件或规范,以及用户和施工方共同签定的其它技术要求。
4.2 化学清洗前应隔离易受清洗液损害的部件和其它配件。
4.3 化学清洗后设备内的有害残液、残渣应清除干净,并应符合相应的标准。
4.4 设备清洗后的质量应符合本标准9.1~9.5。
4.5 化学清洗产生的废液应进行处理,并应符合表5标准规定的要求后,才允许排放。
5. 化学清洗条件的确定
5.1 化学清洗工艺的选择,应根据垢的成份,凝汽器设备的构造、材质,通过小型试验选用合理的清洗介质并确定清洗工艺。
清洗介质的确定应在保证清洗效果、缓蚀效果的前提下,综合考虑其经济性及环保要求等因素。
5.2 用于化学清洗的药剂应有产品合格证(单一的化学试剂除外),并通过有关药剂的质量检验,其结果应符合附录B的要求。
5.3 清洗介质的选择见表1。
5.4 为减少清洗液对金属的腐蚀,清洗液的最大浓度应由试验确定。
5.5 为尽量减小清洗介质对被清洗设备的腐蚀,必须选择合适的酸洗缓蚀剂。
可供选用的部分国产商品缓蚀剂的品种、质量标准和检验方法见附录B和523-93。
5.6 酸液的流速应在该缓蚀剂所允许的范围内,凝汽器酸洗一般采用循环酸洗。
维持冷凝管中酸液的流速为0.15~0.25,酸洗后冲洗流速应大于酸洗流速。
5.7 在酸洗时,酸液温度最低温度应在10℃以上。
无机酸的清洗温度应控制为室温,有机酸的清洗温度一般<65℃。
5.8 当酸洗液中3+浓度≥50时,可采用半开半闭酸洗或在酸洗液中添加还原剂如抗坏血酸钠等,不得用废酸液清洗凝汽器。
5.9 奥氏体钢清洗时,选用的清洗介质、缓蚀剂不应含有易产生晶间腐蚀的敏感离子-、F-和S,同时还应做金相试验观察其有无晶间腐蚀。
表1 清洗介质的选择
6. 化学清洗系统的设计和安装
6.1 化学清洗系统应根据凝汽器设备结构、热力系统、清洗介质、清洗方式、水垢的分布状况、汽机辅属车间和环境及清洗范围等具体情况进行设计。
6.2 清洗系统的设计要求
6.2.1 清洗泵的选择,必须是大流量、低扬程(小于25㎜H2O柱)保证凝汽器冷凝管单管流速在0.1~0.25,清洗时还可防止凝汽器超压。
选择耐腐蚀的混流泵最经济实用。
6.2.2 清洗总管管径的选择以管内总流速小于4为准。
6.2.3 为在酸洗成膜中经常要进行系统的切换正反方向循环,故一般设计进出口管管径相同。
可将原排气门作为另一个排酸返回管,每个单元凝汽器排汽门管径300机组一般≥80,100机组一般≥50,即一进二出或三出以防憋压。
6.2.4 被清洗设备和临时系统接口处,要避免死区、盲肠,并尽量减少接口的数量。
6.2.5 清洗系统应尽量简化,便于操作,并能合理、有效地处理清洗废液。
6.2.6冲洗时,流速应明显高于清洗流速。
可采用清洗泵或循环水泵进行冲洗。
6.3 加酸方式
6.3.1 清洗回路充满水后,当加入缓蚀剂及其它助剂达到要求时,应继续循环均匀后,用浓酸泵或酸喷射器向清洗箱和清洗回路内加入浓酸,边循环,边配酸。
为防止瞬间产生大量二氧化碳气体集中溢出,应严格控制进出口酸度差小于0.6%。
6.3.2 采用半开半闭酸洗时,将浓酸和缓蚀剂按一定比例用浓酸泵打入正在运转的清洗泵出口或循环泵出口。
6.4 清洗系统的安装应满足下列要求
6.4.1 新建机组热力系统已安装完毕,并经水压试验合格。
对运行机组已停机并应与其它机组的共用系统解列。
6.4.2 安装临时系统时,管道内应先用手电筒检查,确认没有砂石和其它杂物。
按相应压力正式管道的质量要求,检查临时管道的焊接质量。
焊接部位应易于观察,焊接操作人员应持有压力容器焊工岗位合格证。
6.4.3 凝汽器汽侧灌水查漏前应将凝汽器两端的管板吹干,在检查时如发现冷凝管及管囗胀接处有泄漏,应及时作出明显标记,然后采取措施于以消除,并确认严密无泄漏。
6.4.4 酸洗前应在凝汽器水室内,将循环水进出口管口用钢板临时焊死封堵严密。
并在循环水入口阀门后加装一个临时排水管。
6.4.5 临时系统和所有正式设备连接须可靠无泄漏,启动清洗泵对系统应进行严密性试验。
打压试验压力为0.10~0.20,以防在清洗过程中酸液泄漏至循环水系统。
6.4.6 阀门在安装前必须研磨,更换法兰填料,并进行水压试验。
阀门及法兰填料,应采用耐酸、碱的防蚀材料。
6.4.7 清洗泵入口侧(或酸箱出口)应装滤网,滤网孔径应小于5,有效通流截面应大于入口管截面积的3倍。
为防止滤网堵塞可在清洗箱内加装1㎡以上的大滤网,在酸洗前大流量冲洗完毕后,将滤网拆除再进行酸洗。
6.4.8 化学清洗时,在清洗箱上应设液位计以便控制循环清洗时的流量调整。
6.4.9 临时系统中安装的温度、压力、流量表计及分析仪表,应经校验合格后方能使用。
不耐蚀的表计,应采取隔绝清洗液的措施。
6.4.10 临时设置的清洗箱、溶药箱,不宜布置在电缆沟附近。
清洗现场的道路应平整、畅通。
通道上的临时管道,如影响通行应设临时便桥,并有良好的照明和通讯设施。
6.4.11 不参加化学清洗的设备、系统应与化学清洗系统可靠地隔离。
6.4.12 系统安装过程中及安装完毕后应及时清除清洗系统和凝汽器水室内的砂石、焊渣和其它杂物。
6.4.13 临时系统的流程应考虑能正反方向循环。
7 化学清洗工艺过程
7.1 化学清洗前,除按6.4的要求完成临时系统安装后还应完成下列准备工作。
7.1.1 清洗前应根据冷凝管的材质及抽管检查和小型试验结果确定清洗方案。
抽管部位为空抽区、低温和高温区各一根,以了解垢的性质、垢量以及垢下基体金属腐蚀状况。
7.1.2 清洗前必须采用高压水枪、压缩空气或机械方法将凝汽器内部己堵塞的管子进行冲通,如管内有沉积的淤泥应冲洗于净,否则会影响酸与管内表面垢物的接触影响清洗效果。
7.1.3 清洗前的小型摸拟试验,取带垢样管放入酸液中进行清洗,清洗液在配制时,应考虑系统清洗的容积、面积、垢量以及金属铁离子增大的影响,所得数据才有参考性。
7.1.4 贮、供水量应能满足化学清洗和冲洗的用水需要。
清洗用水可采用澄清工业水,清洗用水量可参照表2。
表2 化学清洗用水量表
7.1.5 废液处理的设施应安装完毕,并能有效地处理废液。
7.1.6 化学清洗的药品应经纯度检验确证无误,并按技术方案的要求备足各种药品及化验仪器、腐蚀指示管等。
7.2 化学清洗工艺
7.2.1 化学清洗的工艺步骤,一般是:
凝汽器两端的管板吹干,汽测灌除盐水查漏并对水测热交换管进行水压查漏和堵漏→临时系统水冲洗→碱洗(热交换管中含油或微生物含量高时,应进行碱洗)→碱洗后水冲洗→酸洗→酸洗后的水冲洗→压缩空气人工吹球→加碱和活化剂进行中和处理→水冲洗→预膜→水室冲洗、通风于燥→查漏、抽管检查。
其清洗工艺的主要控制条件见表3。
7.2.2 清洗工艺的确定
7.2.2.1 被清洗的热交换管抽管检查,经酸洗后发现管内腐蚀己十分严重或出现严重点蚀时,应进行探伤检查确认,将此类管更换或堵死后再进行酸洗。
7.2.2.2 为减少3+对清洗腐蚀速度的影响,当3+>0.01%时,应在清洗介质中添加适量还原剂或采用半开半闭的方式将3+的高峰排除。
7.2.2.3 为提高予膜效果可在成膜过程中用除油压缩空气适量添加氧量。
7.2.3 汽侧灌水和水侧水压试验
7.2.3.1 用高压水冲洗清除凝汽器管内的污泥、砂石等污脏物。
7.2.3.2 在凝汽器汽测灌水实验前两端的管板必须充分干燥。
7.2.3.3 对于无奥氏体钢部件的设备,可用过滤后的澄清水或工业水进行水冲洗,水冲洗流速应为0.3。
冲洗终点以出水澄清无杂物为准。
7.2.4 酸洗
7.2.4.1 循环酸洗时,缓蚀剂可在浓酸液注入前加入清洗系统,也可与酸液同时加入清洗系统,酸洗工艺的控制条件见表3。
7.2.4.2 凝汽器清洗时,配酸过程应缓速持续进行,避免瞬间过高浓度进入,加酸前半小时进出口浓度差<0.6%,最好加酸持续时间为1.5h~2.0h。
并根据泡沫多少加入消泡剂,根据3+分析结果加入3+还原剂,使3+<0.01%。
7.2.4.3 若注酸后在2h内酸液浓度<1.5%应补加酸使其酸度为3.0%左右与此同时适量补加缓蚀剂。
通常在4h左右可完成酸洗,垢量多时可在6h内完成酸洗。
7.2.4.4 凝汽器监视管段可以分别放入清洗箱和水室,并使监视管内流速与被清洗凝汽器管内流速相近。
7.2.4.5 如酸液浓度连续半小时稳定不降低,说明垢己基本除去,可提前结束酸洗,减小腐蚀。
7.2.5 水冲洗
启动两台泵用工业水进行大流量冲洗,也可采用间隙水冲洗。
冲洗流速应≥酸洗流速,冲洗至≥4.3。
7.2.6 人工吹球
清洗后热交换管内存在部分污泥,为保证预膜质量。
水冲洗结束后,用无油压缩空气进行吹球,每管不少于2个胶球,清除管内污泥,同时清除水室及管道内沉积的污泥。
7.2.7 中和
7.2.7.1 系统充满水,建立循环后加入和预膜活化剂,循环中和6h~8h后排放,使铜管活化表面进入钝化状态形成2O后排放,再通工业水冲洗至≤9.0。
7.2.7 予膜
7.2.7.1 冲洗吹球结束后,再上水冲洗排放至清水。
采用表4的工艺成膜。
表3 凝汽器清洗预膜工艺及控制标准
表4 凝汽预膜工艺条件
7.2.7.2 为了获得高质量的防腐膜,达到均匀致密应每隔8~12h切换系统一次(正反方向各循环2~4次)。
此外,每次倒向后先提高流速运转0.5h,再转入正常流速运行。
7.2.7.3 预膜至预定时间后排空预膜液。
7.2.8 冲洗干燥
系统进工业水,循环冲洗至水清且>7为合格。
将水排空,打开人孔,用工业通风机进行强力通风干燥。
7.2.9 查漏、抽管1~2根评定酸洗和预膜效果。
8. 清洗废液的处理
8.1 凝汽器化学清洗废液的排放必须符合8978的规定,其中主要的有关指标和最高允许排放浓度如表5。
表5 污水综合排放标准(第二类污染物最高容许排放浓度)
8.2 严禁排放未经处理的酸、碱液及其它有害废液,也不得采用渗坑、渗井和漫流的方式排放。
火电厂应设存放和处理废液有足够容量的处理装置。
8.3 清洗废液可排入冲灰沟或化学中和池经处理后排放,具体方法可参见794-2001。
9 化学清洗成膜质量指标
9.1 清洗后的金属表面应清洁,基本上无残留硬垢。
9.2 用试验腐蚀指示管段测量大型酸洗的金属平均腐蚀速度应<2(m2·h),小型试验腐蚀速度应≤0.5(m2·h),总腐蚀量应<202,与洗前管样比较无点蚀和脱锌现象(原始管样已发生脱锌现象除外)。
9.3 除垢率≥90%为合格,除垢率≥95%为优良。
9.4 凝汽器化学清洗后,机组启动未发生因酸洗引起的管子泄漏造成停机。
9.5 抽管检查膜质均匀致密,且有一定的厚度。
用1.0盐酸滴溶检查其耐蚀性>35S为优良、20~35S为合格、<20S为不合格。
10. 化学清洗中的化学监督
10.1 化学清洗前检查并确认化学清洗用药品的质量、数量,监视管段和腐蚀指示管。
腐蚀指示管应放入清洗箱和凝汽器水室内。
10.2 化学清洗中应监督加药、化验,控制各清洗阶段介质的浓度、温度、流量、压力等重要清洗参数。
10.3 化学清洗用药品质量和检定方法,详见附录B。
10.4 根据化验数据和监视管内表面的除垢情况判断清洗终点。
10.4.1 排酸浓度不低于2.5%(常温下盐酸浓度低于2.5%反应变得很缓慢)。
10.4.2 进出口酸浓度接近维持1h。
10.4.3 进出口酸液无泡沫产生。
10.5 化学分析项目与监视点
10.5.1 凝汽器化学清洗时的监视点布置见图1,清洗液的测试方法见附录A。
10.5.2 化学清洗过程中测试项目及终点,见表6。
表6 化学清洗的测试项目及终点
11 安全保证体系
11.1 化学清洗中的安全防范工作,应设专人负责安全监督保障工作,制定安全措施,并检查落实措施的执行情况,确保人身与设备安全。
11.2 安全注意事项
11.2.1 各清洗单位都须根据本单位具体情况制定切实可行的安全操作规程。
清洗前,有关工作人员必须学习并熟悉清洗的安全操作规程、了解所使用的各种药剂的特性及灼伤急救方法,并做好自身的保护。
清洗工作人员需经演习和考试合格后方可参加清洗工作。
参加化学清洗的人员应佩带专用符号,与清洗无关的人员不得进入清洗现场。
11.2.2 清洗现场必须备有消防通讯设备、安全灯、充足的照明、急救药品和劳保用品,常用的急救备用药品见11.8,现场应有"注意安全"、"严禁明火"、"有毒危险"、"请勿靠近"等安全警示牌。
11.3 化学清洗系统的安全检查应符合下述要求
11.3.1 与化学清洗无关的仪表及管道应隔绝;
11.3.2 临时安装的管道与清洗系统图应相符;
11.3.3 对影响安全的扶梯、孔洞、沟盖板、脚手架,要做妥善处理;
11.3.4 清洗系统所有管道焊接应可靠,所有法兰垫片、阀门及水泵的盘根均应严密耐腐蚀,应设防溅装置,防备漏泄时酸液四溅,还应备有毛毡、胶皮垫、塑料布、胶带和专用卡子以便漏酸时抢修。
11.3.5 酸泵、取样点、化验站和监视管附近须设专用水源及石灰粉。
11.4 清洗时,禁止在清洗系统上进行明火作业和其它工作。
在加药场地严禁吸烟,清洗过程中,应有专人值班,定时巡回检查,随时检修清洗设备的缺陷。
11.5 搬运浓酸、浓碱时,应使用专用工具,禁止肩扛、手抱。
直接接触苛性碱或酸的人员和检修人员,应穿戴专用的防护用品。
尤其在配酸(包括使用氢氟酸或氟化物)及加碱液时应注意戴好防护眼镜或防毒面具。
11.6 在配碱地点应备有自来水、毛巾、药棉和浓度为0.2%硼酸溶液。
11.7 酸液泄漏的处理:
11.7.1 酸液漏到地面上应用石灰中和。
11.7.2 溅于衣服上,应先用大量清水冲洗,然后用23%碳酸钠溶液中和,最后再用水冲洗。
11.7.3 酸液溅到皮肤上,应立即用清水冲洗,再用23%重碳酸钠溶液清洗,最后涂上一层凡士林。
11.7.4 酸液溅入眼睛里,应立即用大量清水冲洗,再用0.5%的碳酸氢钠溶液冲洗并立即送医务室急救。
11.7.5 氢氟酸一旦溅于皮肤上,应用饱和石灰水冲洗。
11.8 清洗过程中,应备有急救药品
11.8.1 0.2%硼酸溶液、0.5%碳酸氢钠溶液、23%重碳酸钠和碳酸钠溶液各5L、凡士林250g和饱和石灰水50L。
11.8.2 氢氟酸灼伤急救用药:
11.8.2.1 药膏的配方为由乳酸钙(或葡萄糖酸钙)20g,氧化镁20g,甘油15g,水44g和盐酸普鲁卡因1g混合而成。
11.8.2.2 静脉注射用的含10%葡萄糖酸钙或10%氧化钙溶液10的针管30~40支。
含10%碘化钠溶液5~10的针管10支。
11.8.2.3 可拉明、咖啡因或止痛片药片。
11.9 易燃、易爆有毒的化学药品在存放、运输、使用过程中应遵守有关的安全规定。
11.10 禁止向水泥沟内排放废酸液,在向除灰系统内排酸时应有相应的技术措施。
排酸时间应与冲灰时间错开,排