黑曲霉生产纤维素酶工艺设计.docx
《黑曲霉生产纤维素酶工艺设计.docx》由会员分享,可在线阅读,更多相关《黑曲霉生产纤维素酶工艺设计.docx(41页珍藏版)》请在冰豆网上搜索。
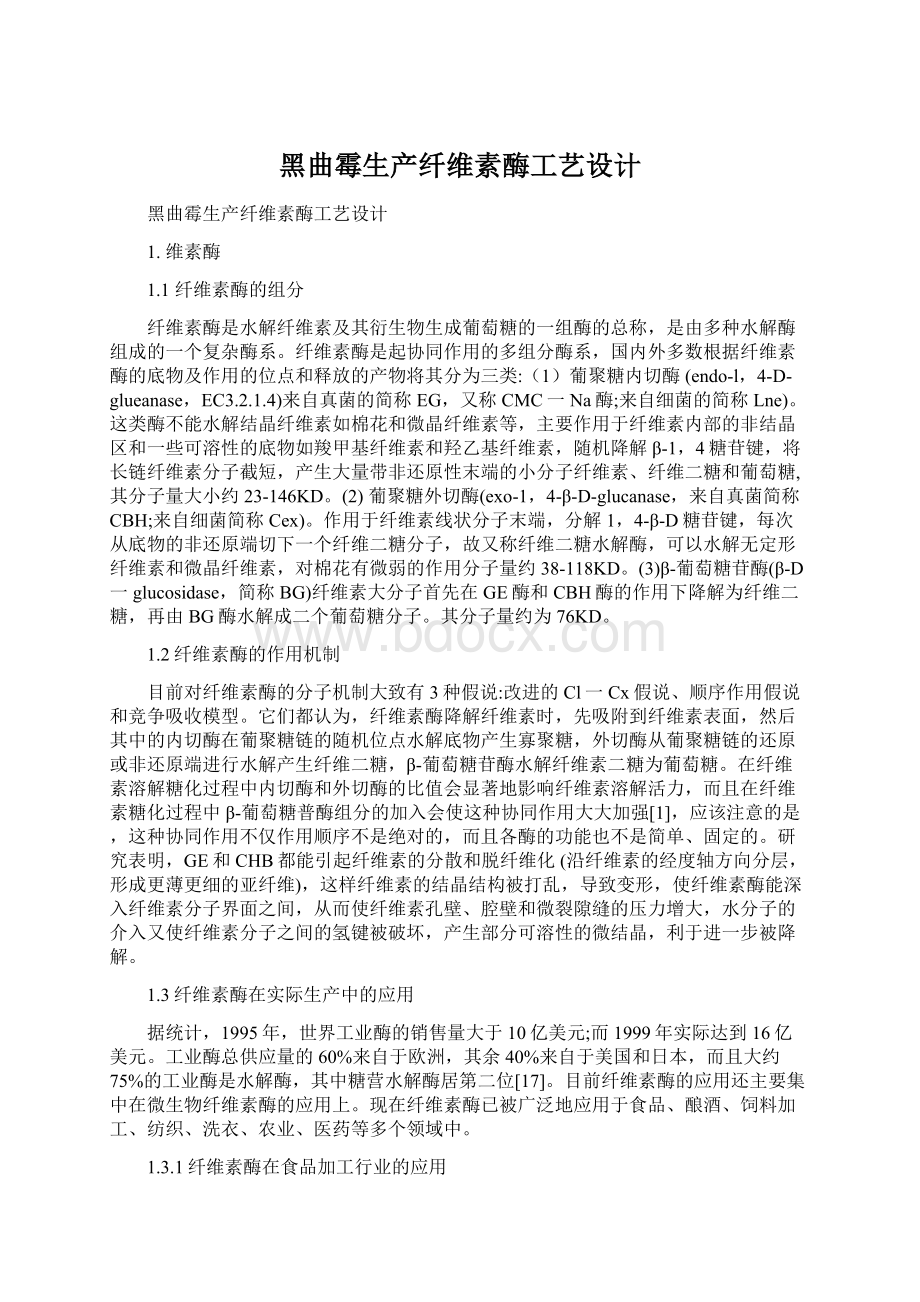
黑曲霉生产纤维素酶工艺设计
黑曲霉生产纤维素酶工艺设计
1.维素酶
1.1纤维素酶的组分
纤维素酶是水解纤维素及其衍生物生成葡萄糖的一组酶的总称,是由多种水解酶组成的一个复杂酶系。
纤维素酶是起协同作用的多组分酶系,国内外多数根据纤维素酶的底物及作用的位点和释放的产物将其分为三类:
(1)葡聚糖内切酶(endo-l,4-D-glueanase,EC3.2.1.4)来自真菌的简称EG,又称CMC一Na酶;来自细菌的简称Lne)。
这类酶不能水解结晶纤维素如棉花和微晶纤维素等,主要作用于纤维素内部的非结晶区和一些可溶性的底物如羧甲基纤维素和羟乙基纤维素,随机降解β-1,4糖苷键,将长链纤维素分子截短,产生大量带非还原性末端的小分子纤维素、纤维二糖和葡萄糖,其分子量大小约23-146KD。
(2)葡聚糖外切酶(exo-1,4-β-D-glucanase,来自真菌简称CBH;来自细菌简称Cex)。
作用于纤维素线状分子末端,分解1,4-β-D糖苷键,每次从底物的非还原端切下一个纤维二糖分子,故又称纤维二糖水解酶,可以水解无定形纤维素和微晶纤维素,对棉花有微弱的作用分子量约38-118KD。
(3)β-葡萄糖苷酶(β-D一glucosidase,简称BG)纤维素大分子首先在GE酶和CBH酶的作用下降解为纤维二糖,再由BG酶水解成二个葡萄糖分子。
其分子量约为76KD。
1.2纤维素酶的作用机制
目前对纤维素酶的分子机制大致有3种假说:
改进的Cl一Cx假说、顺序作用假说和竞争吸收模型。
它们都认为,纤维素酶降解纤维素时,先吸附到纤维素表面,然后其中的内切酶在葡聚糖链的随机位点水解底物产生寡聚糖,外切酶从葡聚糖链的还原或非还原端进行水解产生纤维二糖,β-葡萄糖苷酶水解纤维素二糖为葡萄糖。
在纤维素溶解糖化过程中内切酶和外切酶的比值会显著地影响纤维素溶解活力,而且在纤维素糖化过程中β-葡萄糖普酶组分的加入会使这种协同作用大大加强[1],应该注意的是,这种协同作用不仅作用顺序不是绝对的,而且各酶的功能也不是简单、固定的。
研究表明,GE和CHB都能引起纤维素的分散和脱纤维化(沿纤维素的经度轴方向分层,形成更薄更细的亚纤维),这样纤维素的结晶结构被打乱,导致变形,使纤维素酶能深入纤维素分子界面之间,从而使纤维素孔壁、腔壁和微裂隙缝的压力增大,水分子的介入又使纤维素分子之间的氢键被破坏,产生部分可溶性的微结晶,利于进一步被降解。
1.3纤维素酶在实际生产中的应用
据统计,1995年,世界工业酶的销售量大于10亿美元;而1999年实际达到16亿美元。
工业酶总供应量的60%来自于欧洲,其余40%来自于美国和日本,而且大约75%的工业酶是水解酶,其中糖营水解酶居第二位[17]。
目前纤维素酶的应用还主要集中在微生物纤维素酶的应用上。
现在纤维素酶已被广泛地应用于食品、酿酒、饲料加工、纺织、洗衣、农业、医药等多个领域中。
1.3.1纤维素酶在食品加工行业的应用
纤维素酶在食品加工行业应用极为广泛。
在果蔬加工行业中,纤维素酶用来软化植物组织。
和一般的加热蒸煮、酸碱处理等方法相比,采用纤维素酶处理可以避免营养物质特变是维生素的流逝。
采用纤维素酶水解法对海藻粉进行前处理可以提高海藻脂质的抽提率,充分获取海藻中的脂质资源,同时降低生产成本。
在油料作物加工中,传统的压榨法和有机溶剂法生产的油制品存在质量差产量点的缺点。
用纤维素酶代替有机溶剂进行加工,可以避免有机溶剂的残留,因而能提高产品质量;另外酶反应条件温和,可以避免剧烈条件对产品质量的影响,同时也降低了生产成本。
在酿酒行业中,原材料中纤维素含量很高,加入纤维素酶,使纤维素能转换为糖,原料利用率大大提高,且残渣相对锐减,不仅提高了产量,同时使残渣处理的工作量减少,极大的提高了经济效益。
1.3.2纤维素酶在饲料工业中的应用
由于家禽家畜一般难消化利用纤维素和半纤维素。
而在饲料中加入纤维素酶制剂后,使纤维素和半纤维素转化为易吸收利用的糖类,使饲料得以充分的利用,同时也避免纤维素和半纤维素在动物体内累积,促进动物的消化吸收。
1.3.3纤维素酶在纺织工业中的应用
近年来,人们通过微生物工程技术,利用纤维素酶对纺织品进行后处理。
因为纤维素酶能使麻、棉这类富含纤维素的物质表面剥离和纵向复合细胞间层侵蚀,使纤维梢丝束化或者脱落,因此,经纤维素酶处理过的织物比较蓬松、丰满、柔软、滑爽,且悬垂性好,吸湿性强,具有一定的丝光效果。
有效地提高了棉麻织物的服用性能及产品的档次。
1.3.4环境保护和纤维素废料处理
自然界和工农业生产中都有大量含纤维素的废物,如木屑、废纸等纤维滤渣,这些废料经理化方法处理后易于酶解[17],就可以用纤维素酶将其水解。
如利用纤维素酶处理秸杆、蔗渣等农业废料生产葡萄糖,再经过发酵可生产甲醇、乙醇等工业物质,这些不仅是重要的化工原料,还可以替代汽油等作为燃料解决日益紧张的能源问题。
1.3.5在医药中的应用
中草药所含成分十分复杂,既有有效成分,又有无效成分和有毒成分。
为了提高中草药的治疗效果,就要尽最大限度提取有效成分,去除无效成分及有毒成分。
因此,中草药提取对于提高中药制剂的内在质量和临床疗效最为重要。
但常用的提取方法(如煎煮法、回流法、浸渍法、渗流法等)在保留有效成分,去除无效成分方面,存在着有效成分损失大、周期长、工序多等缺点。
近年来,用于中药提取方面研究较多的是纤维素酶,该方法的应用,使得中草药提取既符合传统的中医理论,又能达到提高有效成分的收率和纯度的目的。
大部分的中药材的细胞壁是由纤维素构成,植物的有效成分往往包裹在细胞壁内,用纤维素酶酶解可以使植物细胞壁破坏,有利于有效成分的提取。
1.4纤维素酶的分离纯化
基本用于分离蛋白质的方法都可以用来分离纤维素酶。
纤维素酶常用的分离纯化方法有:
有机试剂沉法、盐析法、电泳法、离子交换层析法、分子筛层析法等。
无水乙醇和丙酮是最常用来沉淀的有机溶剂,沉淀再经离心分离、风干,即得到较纯的酶制剂。
盐析常用的试剂为硫酸按,操作简单,缺点是存在酶活的损失,且除盐困难[15]。
电泳法和离子交换法都是依据物质的酸碱性、极差的差异,通过离子间的交换吸附实现组分分离的方法,缺点是当杂质与所要分离的物质具有相类似的极差时,难以分离出杂质。
分子筛层析是利用具有一定孔径的分子筛对物质按分子大小进行分离,方法简便,缺点是当杂质和所分离物质分子大小接近时,达不到分离的目的。
除了以上常用的分离方法外,双水相萃取技术、色谱技术也应用于纤维素酶的分离。
双相萃取技术又称水溶液两相分配技术,分离过程温和,酶不易被破坏,且不需要苛刻的条件[16]。
纤维素酶本身就是一个多组分的酶系统,实际生产中又不可避免得引入一些杂质,因此,要得到纯组分的纤维素酶,往往需要多种分离手段联合应用才能实现。
2.产生纤维素酶的微生物
纤维素酶的来源很广泛,真菌,细菌,放线菌等均有能产生纤维素酶。
细菌有纤维粘菌(CytoPHaga)和纤维杆菌(Cellulomonas)等。
放线菌主要有玫瑰色放线菌(A.Roseus)和纤维放线菌(A.Cellulase),链霉属放线菌等。
不同微生物合成的纤维素酶在组成上有显著的差异,对纤维素的酶解能力也不大相同。
放线菌的纤维素酶产量极低,研究很少。
细菌的产量也不高,主要是葡聚糖内切酶,且大多数对结晶纤维素没有活性,所产生酶是胞内酶或吸附在菌壁上,很少能分泌到细胞外,增加提取纯化难度,在工业上很少应用。
目前国内外最主要的还是利用真菌来发酵产纤维素酶。
真菌具有产酶的诸多优点:
产生纤维素酶为胞外酶,便于酶的分离和提取;产酶效率高,且产生纤维素酶的酶系结构较为合理;同时可产生许多半纤维素酶、果胶酶、淀粉酶等。
真菌纤维素酶主要有木霉(Trichoderm)青霉(penicillium)、曲霉(Aspergillus)以及腐质霉(Humicola)等。
其中研究得比较深和透彻的是木霉属(Trichoderma)和曲霉(Aspergillus),绿色木霉和黑曲霉被公认是产纤维素酶最稳定和无毒安全的菌种,且其产生的是胞外酶对研究纤维素酶的性质以及分离纯化等都比较方便。
2.1绿色木酶简介
绿色木霉(Trichodermaviride)为腐生菌,主要存在于朽木、枯枝、落叶、土壤、有机肥、植物残体和空气中。
其分生抱子通过空气传播。
菌株在马铃薯一葡萄糖琼脂培养基上广铺,最初为白色致密的基质菌丝,而后出现棉絮状气生菌丝,并形成密实产抱丛束区,常排成同心轮纹。
深黄绿色至深蓝绿色的产抱区,菌落反面无色,老的培养基散发一股椰子气味,菌丝透明,壁光滑,有隔,分枝繁复,直径1.5~12μm,透明。
厚垣抱子间生于菌丝中顶生于短侧枝上,多数为球形,极少为椭圆形,透明,壁光滑,直径可达14μm,通常在基底菌丝中产生.分生抱子梗的特征同属的特征。
小梗瓶形或锥形,基部稍窄,中部较宽,从中部以上变窄成长颈,近于直或中部弯曲,8~14×2.5~4.5μm,分生抱子大多为球形,直径25~4.5μm,少数抱子为短倒卵形,4~5×3.5~4μm,抱壁具明显的小扰状突起,在显微镜下单个抱子淡绿色。
在分生抱子梗分枝上聚成的孢子头8~9林μm。
绿色木霉生产纤维素酶产量比较高,可以通过物理或化学诱变获得高产菌株,能够稳定地用于生产;该霉菌要求的生长环境粗放,适应性较强,易于控制,便于管理;绿色木霉产生的纤维素酶稳定性比较好,培养和控制比较容易;该霉菌分泌的纤维素酶是胞外酶,易于分离纯化;另外,绿色木霉及其代谢物安全无毒,不会对操作人员和环境造成不良的影响。
因此,绿色木霉是目前用于纤维素酶生产的最普遍的菌种之一。
2.2黑曲霉简介
黑曲霉是半知菌亚门,丝孢纲,丝孢目,丛梗孢科,曲霉属的一种常见真菌(曹澍泽等,1992)。
广泛分布于植物性产品、籽实和土壤中,可生产淀粉酶、酸性蛋白酶、纤维素酶、果胶酶、单宁酶、葡萄糖氧化酶、柠檬酸、葡糖酸和没食子酸等,是一种重要的发酵工业菌种。
目前,国内外对纤维素酶的研究多集中于木霉。
但是木霉毒性嫌疑大,在食品发酵工业和饲料工业中的应用受到限制,而黑曲霉被认为是不会产生毒素的纤维素酶产生菌。
现已被许多国家批准作为食品用酶制剂生产菌,国外已实现黑曲霉酶制剂商品的工业化生产[3]
3.生产纤维素酶的工艺介绍
纤维素酶的生产主要有固体发酵和液体发酵两种方法,生产原料有麸皮、秸秆粉、废纸、玉米粉和无机盐等。
3.1纤维素酶的发酵工艺
3.1.1固态发酵
随着固体发酵生产线的相继建成投产,以及市场竞争对低成本高产出的迫切需求,固体发酵已日益受到注目。
固态发酵是指利用不溶性原料作为固体支持物和营养物质,体系无自由流动液体,在其上进行的任何发酵过程[4]。
固态发酵历史悠久,应用广泛,是人类利用微生物生产产品历史最悠久的技术之一。
自20世纪90年代以来,随着能源危机和环境问题的日益严重,人们重新开始审视固体发酵的优点,并不断在原料、工艺和设备等方面进行大量深入的研究,使固态发酵在酶制剂领域取得了长足的进展[5]。
其工艺流程如下
斜面试管→小三角瓶培养→大三角瓶培养→种子罐培养
↓
原料→粉碎→配料→混合—蒸煮灭菌→冷却接种
(稻草等)(麸皮、营养盐等)↓
成品←包装←干燥←过滤←盐析←浓缩←过滤←浸提←固体发酵
3.1.2液体发酵
液体发酵法是将玉米秸杆粉碎至20目以下进行灭菌处理,送入发酵釜内发酵,同时加入纤维素酶菌种,发酵时间约70h,温度低于60℃。
采用无菌空气从釜底通入进行通气搅拌,发酵完的物料经压滤机压滤,超滤浓缩和喷雾干燥后制得纤维素酶产品。
其生产工艺流程下图所示。
斜面试管→小三角瓶培养→大三角瓶培养→种子罐培养
↓
原料→粉碎→配料→混合→蒸煮灭菌→冷却接种
(稻草等)(麸皮、营养盐等)↓
成品←包装←喷雾干燥←超滤浓缩←压滤←液体深层发酵
此法具有原料利用率高、生产条件易控制、劳动强度小、产品质量稳定、不易染菌、生产效率高等特点,但缺点是动力消耗大、设备要求高。
目前,应用于生产纤维素酶的菌种主要是木霉、黑曲霉和变异青霉等,其中木霉应用最广泛。
纤维素酶的生产和其它酶制剂一样,可采用液体培养(包括液体浅盘培养和深层通气培养)和固体培养(包括固体浅盘培养和厚层通风培养)两种。
美国在原有的液体培养方法的基础上发展出了流加培养法、分批发酵法、连续发酵法、二次发酵法以及细胞循环法等等[6]。
从现有的研究结果来看,纤维素酶的生产以固态发酵居多,而且较为经济合理。
其原因主要有以下几个方面:
(1)固态发酵能耗低,一般不需搅拌,只需通入少量低压无菌空气。
液态发酵的通气量比固态发酵大得多,而且进气压力也较高。
另外培养液粘度大,氧的传质困难,需要消耗大量的动力做搅拌功;
(2)固态发酵原料及培养条件比较粗放,成本较低;
(3)固态发酵设备投资少,后处理简单,基本无污染。
液态发酵设备投资大,技术要求高,需要排放大量污水。
(4)大量的实验表明,由于丝状真菌的菌丝体在固态发酵中能够很好地与纤维质原料结合,因此,固态发酵的酶活要比液态发酵高。
当然,固态发酵也存在着一些不足:
机械化程度低,劳动强度大;产品质量不稳定,重复性差等。
3.2工艺条件对纤维素酶活性的影响
3.2.1原料的影响
微生物生长需要从外界获得营养物质,这些物质包括碳源,氮源,无机盐,生长因子和水分。
作为发酵培养基的原料必须提供微生物生长所需的全部营养物质,才能保证生长发酵过程的实现。
常用的碳源有玉米芯,鼓皮,秸秆,稻草粉,可溶性淀粉等;常用的氮源有硝酸按,硫酸按,酵母膏,尿素,蛋白陈等。
杨盛等分别以玉米芯鼓皮比例为2:
1-6:
1,采用绿色木酶与黑曲霉混合发酵,实验结果表明在玉米芯与鼓皮比例为4:
1时酶活最高,而且鼓皮比例越高酶活越低,以此推断出鼓皮只能作为添加碳源,加入过多会对纤维素酶的形成产生抑制,加入越多,抑制越强。
以鼓皮和玉米芯为碳源,酵母膏为氮源,研究发现,当碳氮比为5:
1时,酶活最高[7]。
原料营养物质的结构对微生物生长同样存在影响,对营养物质的结构进行有效的改造往往能提高整个微生物生长发酵过程的效率。
通常的预处理方法包括物理法、化学法、生物法及上述方法的综合利用[8]。
预处理提高发酵效率的同时也引入了新的工序,因此应从经济效益出发,选择合理的预处理方法。
许宪松等研究发现,将稻壳通过300W的微波处理7min候发酵,可以得到最高的酶活。
但以单位能耗产生的德酶活增加量记,以处理5min时产生的酶活增加量为最高[9]。
3.2.2温度的影响
各种菌种都有其相适应的生长温度。
大多数霉菌生长最适宜的温度为25一30℃,在0℃以下,生长缓慢甚至处于休眠状态,而温度过高时会使其生长繁殖受抑制甚至死亡。
王仪明等在不同的温度下利用绿色木霉固态发酵,结果显示在35℃时酶活最高,产Cl酶活力最大为2.38U/mg,产CMC酶活力最大为1.97U/
mg,FPA酶活力最大为0.47U/mg,产β-葡萄糖营酶活力最大为0.32u/mg[10]。
混菌发酵中存在多种菌种,其生长产酶的适宜温度又不尽相同。
因此必须通过实验,选择合适的温度,使各菌种之间得以协调,达到互相补充互相促进的目的。
有的菌种在不同的生长阶段所需的事宜温度也不同,以至于需要采用变温培养。
刘薇等采用串珠霉与链霉菌混合发酵,通过4种方案考查温度对混菌发酵的影响:
第1组:
始终28℃;第2组:
始终37℃;第3组:
先37℃发酵绪论4d,再28℃发酵Zd;第4组:
先28℃发酵4d,再37℃发酵2d。
均在发酵第6d测酶活。
结果显示第3组方案的酶活最高:
CMC酶、FPA酶和pG酶酶活分别为3162IU/mL、1151IU/mL、2148lU/mL[11]。
3.2.3pH值的影响
和温度一样,微生物生长有其适宜的酸碱环境。
细菌生长环境的pH值为6.5-7.5,放线菌适宜生长的pH值为7.5-8.0,酵母菌和霉菌的适宜pH值大约为6.0-6.5。
pH过高过低都会抑制微生物的生长繁殖,超过一定范围甚至能导致微生物死亡。
邝哲师等利用玉米秸秆和玉米芯为原料,采用里氏木霉固态发酵的方法考察其发酵条件,结果表明,在自然pH值(pH=5.5-6.0)和弱酸的环境下(pH=4.5-5.5)时,产纤维素酶滤纸酶活较高,达到3200~3500U/mL的水平;而在偏碱(pH=7.0-7.5)的环境下,产纤维素酶滤纸酶活较低,为2500~2800U/ml[12]。
林捷等以木薯渣为原料,设计正交试验考察初始pH值,培养温度,培养基装量,接种量对纤维素分解菌混合发酵产酶的影响,通过极差分析显示,初始pH对产酶的影响最大[13]。
3.2.4水分的影响
水分是微生物生长不可或缺的物质。
而在固态发酵中,水分的量是有限的。
选择合适的水分比例,在固态发酵中显得尤为重要。
由于固体发酵是好氧发酵,水分过多,会影响透气性,使培养基内部散热难,且易造成杂菌污染,制曲发酵困难,产品酶活力下降。
水分过小,则可能会满足不了菌种生长的需要,造成产酶活力低下。
刘海德等通过实验对纤维素酶菌与蛋白酶菌混合培养的条件进行优化,结果显示在培养基含水量为40%-50%时,酶活较低,纤维素酶活为4930U/g,木聚糖酶活为4013U/g;在培养基含水量为51%-55%时,酶活力大幅度提高,纤维素酶活为7946U/g,木聚糖酶活为4054U/g;而当培养基含水量上升到60%时,酶活力略有下降,纤维素酶活为7761U/g,木聚糖酶活为3896U/g。
培养基含水量的选取和原料纤维素的含水量有关。
张冬艳等通过研究发现以麦秸为原料时,料水比1:
1.5的条件下产酶活力最高,而玉米秸产最高酶活的料水比为1:
2,酒糟产最高酶活的料水比为1:
1[14]。
4.存在问题
纤维素酶的工业化生产技术在我国尚属起步阶段,市售产品均为粗制酶,而精制酶基本上依靠进口。
造成这一现象主要是因为纤维素酶发酵菌种活力不高,发酵后处理技术不够成熟。
纤维素酶生产过程中浓缩工艺前承浸提工艺,后接溶剂提取工艺,是重要的生产环节。
如果生产产品为液体酶,则生产工艺将直接至浓缩环节结束。
因此,浓缩技术已成为影响我国纤维素酶精制的原因之一。
5.改进办法
5.1浓缩方式的选择
在浓缩工艺设计中,以下2个基本问题值得我们重视:
(1)由于酶浸提液中纤维素酶的摩尔分数仅为8‰~9‰,而要从如此低浓度的混合物中分离出纯纤维素酶,则需要消耗较大的能量。
因此,必须寻找一种操作可行且能耗较低的浓缩方式来浓缩纤维素酶浸提液,以减少浓缩过程的能耗。
(2)由于酶是一种具有高度催化活性的特殊蛋白质,在浓缩操作中,还必须严格防止酶的变性失活,以最大限度地提高产品收率。
目前,酶液的浓缩方法主要有3种:
试剂浓缩、减压浓缩法和超滤浓缩法。
试剂浓缩工艺可用聚乙二醇(PEG)吸收酶液中的水分,该法简便、效率高,但试剂价格较贵,作为工业化生产因成本问题则不予考虑;减压蒸发浓缩法采用减压装置使待浓缩酶液在一定的真空度和温度下进行,对酶液等热敏性物质,减压装置多采用离心薄膜蒸发器和刮板式蒸发器;超滤浓缩法是在常温、无相变时的浓缩过程,在加压条件下,将浓缩液通过一层只允许水分子等小分子选择性透过的微孔超滤膜,而酶大分子被滞留,从而达到酶液浓缩的目的。
5.2超滤工艺
5.2.1超滤浓缩原理及影响因素
超滤膜具有不对称结构(称为不对称膜)。
表面为活性层,起过滤作用,孔隙直径约为100nm,厚度为012~015Lm;底部为支撑层,起支持活性层的作用,孔隙直径为011~110Lm,厚度为50~100Lm。
由于活性层很薄,流体阻力较小且不易使孔道阻塞,因而,颗粒就被截留在膜的表面。
膜分离实质是由于物质通过膜的传递速度的不同而得到分离。
超滤过程是一种以压力为推动力的膜分离技术,溶质或悬浮物料按粒径大小不同进行分离,比膜孔小的物质和溶剂(水)一起透过膜,而较大的物质则被截留。
能否采用超滤浓缩工艺,与膜
的特性(空隙度、圆柱形孔道直径、厚度)、操作条件(膜两侧压力差、温度)、溶液性质(浓度、黏度、pH)等均有直接关系。
此外,对于生物高分子酶,会因强力搅拌或高速冲刷而使酶活力损失[3-4],故只能根据酶的特性适当控制流速。
5.2.2工业化生产纤维素酶使用超滤浓缩的可行性
超滤浓缩在常温或略偏低温且无相变的情况下进行,操作压力为低压(约0125MPa),对热敏性物质的影响很小,可保证酶不易失活。
影响超滤浓缩的压力、温度、pH、流体剪力等均可以通过适当的工艺流程设计和操作控制来满足生产要求,防止对酶活力的影响。
而就溶质分子大小来看,纤维素酶中的C1、Cx酶的相对分子质量为45000~75000,相当于球形直径为350~760nm,而超滤适用阻截溶质的相对分子质量为500~300000,溶质直径相当于100~4800nm,纤维素酶分子恰在超滤膜的切割范围之内。
就工业化生产而言,超滤具有能耗低、生产成本低等特点,适合于生产酶制剂。
因此,只要选择合适的膜及其膜组件,采用超滤法浓缩纤维素酶浸提液应当是完全可行的。
5.2.3超滤组件的选用
目前应用在酶制剂浓缩工艺上的超滤组件主要有外压管式、卷式和中空纤维式3种。
通过对过滤膜表面积、操作难易程度和价格等方面的比较,设计选用中空纤维式超滤组件。
中空纤维超滤装置的特点是运用成束(千根以上)坚实的中空纤维,每根纤维内腔直径为012mm。
这些纤维是由惰性的非离子聚合物制成,具有独特的多向异性的结构,故有非常高的流率和抗阻塞性能,当介质以轴流形式通过管腔时,将会在超滤膜面上形成剪切力。
因此,在截留溶质分子的同时,可以将浓差极化降到最低限度。
目前用于超滤过程的膜材料主要有:
醋酸纤维(CA)、聚砜(PS)、聚氯乙烯(PVC)、聚丙烯腈(PAN)和聚砜酰胺(PSA)等。
从膜的耐温、纯水透过量、酶液透过量、使用寿命以及强度等多方面综合考虑,宜选用聚砜酰胺膜。
5.2.4工艺流程设计
超滤膜及其组件确定后,根据超滤膜浓缩的原理、影响因素以及酶的生物特性,为保证酶活力的前提下最大限度地提高碱性纤维素酶的收率,在工艺流程设计中从以下方面采取了一定措施:
(1)采用低温超滤以减少酶失活,选用具有冷却装置的循环罐;
(2)将料液预过滤以除去较大的粒子,减少膜的负荷及减轻污染,同时设置清洗设施;
(3)为避免经过泵的剪切力使酶失活,选用剪切力低的泵代替离心泵,如采用工业软管泵等;
(4)配置稀碱和醋酸罐,以便调节酶液pH,避免pH对酶的阻流率和活性的影响;
(5)在管道配置方面,酶液循环管口需由上部向下插入循环罐液面,避免产生泡沫而引起酶的界面失活。
2.产品方案及工艺流程
2.1产品与产量的确定
产品方案明细表
产品名称
年产量/t
日产量/t
全年生产天数/d
酒精工业用酶
250
0.758
330
饲料添加酶
250
0.758
330
2.2工艺流程
2.2.1原辅料及菌种
(1)原料:
玉米秸秆、麦麸
(2)辅料:
酵母膏、木质纤维、蛋白胨、(NH4)2SO4、泡敌、CaCl2·2H2O、Tween-80、KH2PO4
(3)菌种:
黑曲霉
2.2.2工艺流程图
2.2.3操作要点
(一)菌种培养
(1)菌种及菌种保存
一般选用的菌种为黑曲霉,发酵周期为90h左右,纤维素酶产量高且稳定性好,产生的纤维素酶为胞外产物,容易分离纯化。
一般黑曲霉菌种用马铃薯琼脂(PDA)培养基保藏。
(2)菌种活化[5]
马铃薯琼脂(PDA)培养基灭菌冷却至30℃左右时,在无菌条件下将保藏的原菌接种到培养基中,在28~30℃的恒温培养箱中培养72h,取出后于0~4℃保存备用。
(3)