材料制备技术课程复习提纲.docx
《材料制备技术课程复习提纲.docx》由会员分享,可在线阅读,更多相关《材料制备技术课程复习提纲.docx(16页珍藏版)》请在冰豆网上搜索。
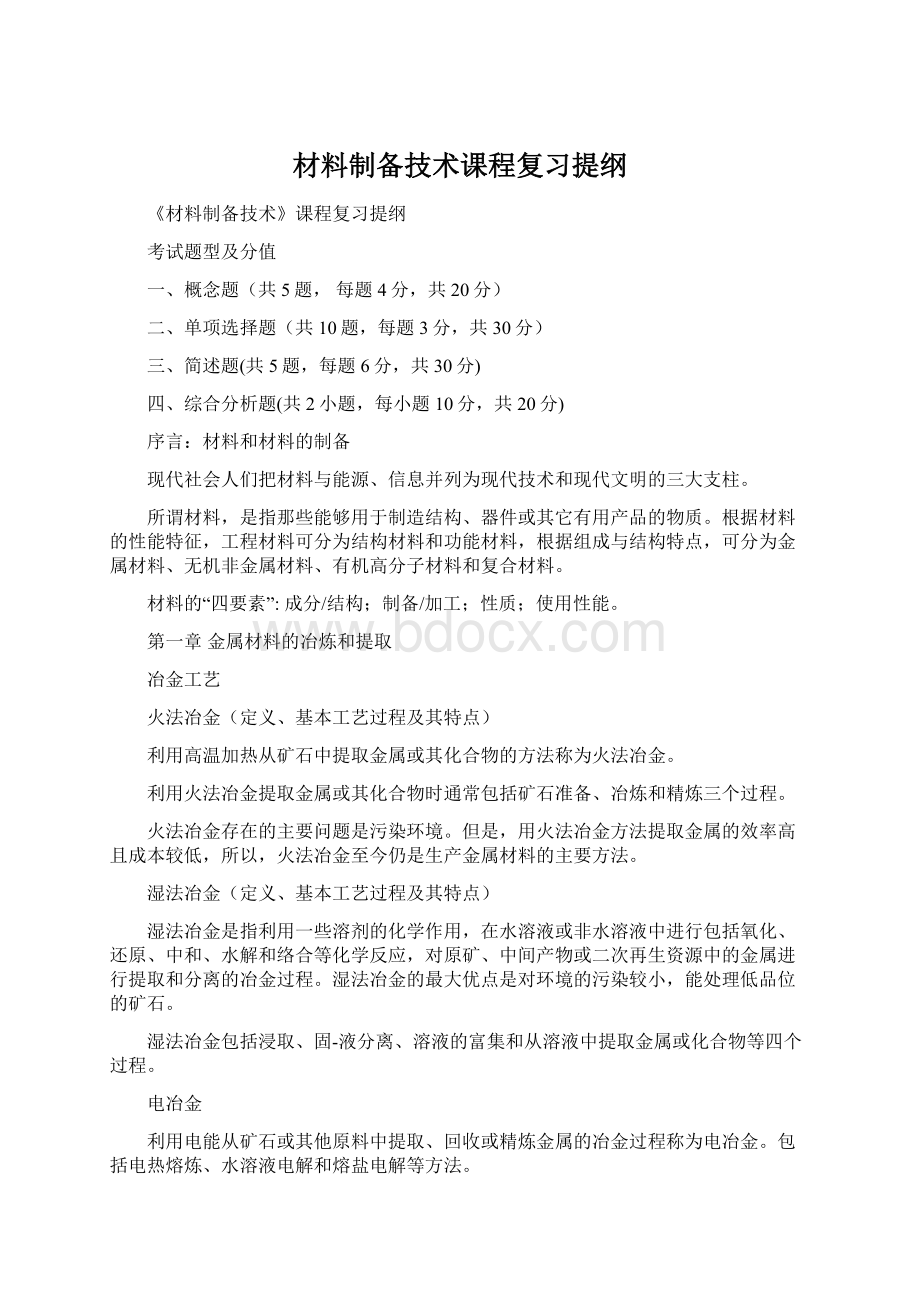
材料制备技术课程复习提纲
《材料制备技术》课程复习提纲
考试题型及分值
一、概念题(共5题,每题4分,共20分)
二、单项选择题(共10题,每题3分,共30分)
三、简述题(共5题,每题6分,共30分)
四、综合分析题(共2小题,每小题10分,共20分)
序言:
材料和材料的制备
现代社会人们把材料与能源、信息并列为现代技术和现代文明的三大支柱。
所谓材料,是指那些能够用于制造结构、器件或其它有用产品的物质。
根据材料的性能特征,工程材料可分为结构材料和功能材料,根据组成与结构特点,可分为金属材料、无机非金属材料、有机高分子材料和复合材料。
材料的“四要素”:
成分/结构;制备/加工;性质;使用性能。
第一章金属材料的冶炼和提取
冶金工艺
火法冶金(定义、基本工艺过程及其特点)
利用高温加热从矿石中提取金属或其化合物的方法称为火法冶金。
利用火法冶金提取金属或其化合物时通常包括矿石准备、冶炼和精炼三个过程。
火法冶金存在的主要问题是污染环境。
但是,用火法冶金方法提取金属的效率高且成本较低,所以,火法冶金至今仍是生产金属材料的主要方法。
湿法冶金(定义、基本工艺过程及其特点)
湿法冶金是指利用一些溶剂的化学作用,在水溶液或非水溶液中进行包括氧化、还原、中和、水解和络合等化学反应,对原矿、中间产物或二次再生资源中的金属进行提取和分离的冶金过程。
湿法冶金的最大优点是对环境的污染较小,能处理低品位的矿石。
湿法冶金包括浸取、固-液分离、溶液的富集和从溶液中提取金属或化合物等四个过程。
电冶金
利用电能从矿石或其他原料中提取、回收或精炼金属的冶金过程称为电冶金。
包括电热熔炼、水溶液电解和熔盐电解等方法。
水溶液电解:
利用电化学反应使金属从所含盐类的水溶液中析出的方法。
熔盐电解:
利用电化学反应使金属从所含盐类的熔体中析出的方法。
钢铁材料的制备
钢铁冶炼包括从开采铁矿石到使之变成可供加工制造零件所使用的钢材和铸造生铁为止的全过程。
一、生铁的冶炼
生铁是用铁矿石在高炉中经过一系列的物理化学反应过程冶炼出来的。
从矿石中提取铁过程称为炼铁,进行炼铁的炉子叫高炉。
从原料来说,除了铁矿石以外,还需要燃料和造渣用的熔剂。
金属冶炼时加入熔剂的主要目的是降低脉石熔点。
由于自然开采的铁矿石大小不均并含有脉石及砂粒等杂质,必须经过各种准备和预处理工作才能更经济、更合理地投入高炉进行生产。
常用的预处理方法有破碎、筛分、选矿、烧结和造块。
选矿的目的主要是为了提高矿石的品位。
铁矿石按其矿物组成主要分为四大类:
磁铁矿、赤铁矿、褐铁矿、菱铁矿。
高炉中配加焦炭的作用有作还原剂;燃烧后产生热量;作料柱骨架,起支撑料柱作用。
高炉冶炼的理化过程:
(1)燃料的燃烧
(2)铁的还原(3)铁的增碳(4)其它元素的还原(5)造渣
高炉炼铁中的炉渣:
矿石中的废料及燃料中的灰分与熔剂的熔合过程称为造渣,熔合后的产物就是渣。
高炉炉渣的来源:
炉料中不能被还原和部分未被还原的组分,以及某些化学反应产物如脱硫产物CaS,均进入炉渣。
炉渣的作用:
实现铁水与脉石分离;完成渣铁间的脱硫;调整铁水成分:
炼制钢铁,造碱性渣,铸造铁,造酸性渣;改善流动性,促进高炉顺行;保护高炉炉衬。
二、钢的冶炼
生铁含有较多的碳和硫、磷等有害杂质元素而强度低、塑性差。
需再经冶炼成钢后才能进行成型加工用于工程结构和制造机器零件。
炼钢的目的就是去除生铁中多余的碳和大量杂质元素,使其化学成分达到钢的标准。
炼钢过程的主要反应是碳的氧化。
1.炼钢的基本过程
(1)元素的氧化
(2)造渣脱磷和脱硫(3)脱氧及合金化
2.常用的炼钢方法:
碱性平炉炼钢,电弧炉炼钢,氧气顶吹转炉炼钢。
三.铸铁的熔制
高炉冶炼得到的铸造生铁是工程用铸铁材料的原材料,还需要通过重新熔炼进行合金化及变质处理使其成分、组织和性能满足要求。
常见的铸铁材料有普通灰铁、孕育铸铁、球墨铸铁、可锻铸铁和合金铸铁等。
除普通灰口铸铁铁水出炉后直接进行浇注外,绝大多数铸铁材料的铁水要在炉前进行变质处理。
主要方法和工艺有:
(1)孕育处理。
通过在出铁的过程中向铁水中加入预热的硅铁或硅钙孕育剂颗粒,
达到使铁水变质的目的。
(2)球化处理。
球化处理是生产球墨铸铁的关键技术,通过向铁水中加入球化剂使铁水凝固成为具有球状石墨组织的铸铁。
球化剂的主要成分是镁,此外,还加入稀土、硅和铁等辅助材料,以改变球化剂的熔点和有效作用时间。
处理方法多用包内冲入法。
铝的制备
铝在自然界中以氧化铝(Al2O3)形态存在,氧化铝主要存在于铝矾土、高岭石和矾土岩石中。
其中,铝矾土矿是炼铝的主要原料。
从中提取金属铝一般分为氧化铝的制备和氧化铝的电解两个步骤。
一.氧化铝的制备
制备氧化铝的方法主要有湿碱法和干碱法两种。
二.氧化铝的电解
从氧化铝中提取金属铝是通过熔盐电解法来实现的,用氟化铝、冰晶石(Na3AlF6)或其它氟化盐作为电解质,把其放入有碳素阳极和阴极所组成的电解槽中,然后通入直流电,使电解质发生一系列物理化学变化,结果在阴极得到液体铝,在阳极得到氧,它使碳阳极氧化而析出。
三。
铝合金的制备
纯铝的导电性好、塑性好,但机械性能差,除直接用作导电材料外,一般不用作结构材料。
要求具有较好机械性能的各种铝合金,是根据不同材料的成分和性能要求,在坩埚中将纯铝重熔并通过合金化处理后获得的。
根据成分和成形方法的不同可分为变形铝合金和铸造铝合金两大类。
1.铝合金的熔炼特点
⑴熔化时间长。
铝的熔化潜热大,比热大,黑度小。
与铁、铜相比较,熔化时消
耗热量多。
因而熔化速度慢,熔化时间长。
⑵易氧化。
在熔体表面形成的氧化铝薄膜虽然有保护作用,但氧化膜一旦破坏,氧
气进入融体,便很难除去。
⑶易吸气。
铝及铝合金的吸气能力较强(主要是吸氢的能力),使铸锭结晶时形成气
孔和疏松的倾向性很大。
⑷容易吸收各种杂质。
铝及铝合金中的—些合金化元素具有很高的化学活性,它们
不仅能直接吸收从铁坩埚和工具中溶解的铁,而且还能从炉衬的许多氧化物中和熔剂的许多氯盐中置换出铁、硅、锌等金属杂质。
2.铝合金的熔制工艺
铝合金是以电解铝,中间合金及低熔点纯金属为原材料,在电阻炉或反射炉中进行重熔和合金化制备的。
因为铝液在高温下极易吸气和氧化,所以熔炼的关键是除气和除渣,提高铝液的纯净度。
此外,对于铝硅系合金,浇注前还要进行变质处理。
精炼处理。
精炼的目的是除气除渣。
精炼方法很多,主要应用的有吹气精炼和氯盐精炼这两种方法。
吹气精炼是指通过向铝熔体直接吹入氩气或氮气等,使之与铝熔体中的气体和非金属夹杂物发生吸附作用,并在气泡上浮过程中将其带出液面,从而达到除气、除渣的目的。
氯盐精炼主要是利用氯盐与铝熔体的置换反应以及氯盐本身的挥发作用和热离解作用。
最常用是氯化锌,四氯化碳和六氯乙烷,与铝作用时生成的三氯化铝气体自铝液底部向上浮起的过程中起着和惰性气体精炼时相似的除气、除渣作用。
变质处理。
对于铸造铝硅合金等,因成分接近共晶点,为细化有害的初生硅和共晶硅,需要在浇注前对铝液进行变质处理。
常用的变质剂为氟化钠,氯化钠,氯化镁等组成的复合钠盐。
变质温度一般为720-730oC,以钟罩搅拌法压入铝液。
镁的制备
镁是地壳中埋藏量较多的金属之一(2.1%),仅次于A1和Fe而占第三位。
镁还大量储存在海水及盐湖水中。
生产镁的原矿石主要有菱镁矿、白云石、卤水和光卤石等。
一.金属镁的冶金和提取
镁的生产方法分为两大类,即氯化镁熔盐电解法和热还原法。
提取到的粗镁再经过溶剂精炼或升华精炼进行提纯。
1.熔盐电解法
根据原料的不同,熔盐电解法又可分为以菱镁矿为原料的无水氯化镁的电解法、以海水或盐卤为原料制取无水氯化镁的电解法以及低水料电解法。
2.热还原法
热还原法又分为硅热法、碳化物热法及炭热法,目前在工业上多用硅热法。
二.镁合金的制备
工程上应用的大多是镁合金材料,因此,需要对镁进行重熔和合金化以制备镁合金铸件或锭坯。
镁合金以铸造镁合金用量最大,且大多为以压铸方法生产。
在生产铸件和变形镁合金锭坯之前,镁通常是在软钢坩埚中进行重熔、精炼和合金化的。
1.配料及熔化
与铝合金一样,镁合金的配料也是根据合金成分的要求,以镁锭、中间合金纯金属等
通过计算进行的。
配料的过程中应注意元素的烧损和加料顺序。
在熔炼镁合金时必须使用适当的熔剂或惰性气体进行熔体保护。
目前常用的熔体保护方法有溶剂保护和气体保护。
(1)溶剂保护。
使用的熔剂为碱金属和碱土金属的氯化物和氟化物,以及某些不活泼的氧化物。
熔剂在熔体表面形成一层连续完整的覆盖层,隔绝空气,防止镁合金被进一步氧化。
此外,由于熔剂在精炼时对非金属夹杂物具有良好的润湿和吸附能力,还可以起到精炼净化的作用。
溶剂保护法操作简单,效果可靠,但溶剂易在浇注时卷入金属液造成铸件的熔剂夹渣。
1.气体保护。
对镁合金溶液具有保护作用的气体有SO2,CO2,SF6和惰性气体等。
现在最常用的保护气体是SF6、CO2与空气的混合气体。
气体保护与溶剂保护相比,可以避免造成熔剂夹渣并改善生产环境,但不具有精炼作用,而且SF6是严重污染大气的气体。
2.精炼
精炼的目的是除去镁熔液中的氧化镁等夹杂物,使熔体净化。
现在使用的主要的精炼剂是MgCl2。
通过强烈搅拌使熔融的MgCl2进入金属液中,由于其密度低而上浮,在上浮的时候吸附并携带悬浮于镁液中的氧化镁等非金属夹杂物,从而达到净化熔体的目的。
3.除气
镁合金在熔化中吸收的气体主要是氢气,因氢在镁中的固溶度较高(平均每100克约30
毫升),所以并不像对铝合金的影响那么严重,氢的主要来源是潮湿的熔剂或经过腐蚀的废金属铸锭,因比如果对这些材料采取适当的预防措施就可以降低氢量。
常用氯气进行除气,最佳的除气温度是725—750oC。
4.变质处理
变质处理的目的是为了使晶粒细化,提高性能。
对于镁铝系合金常用碳变质或熔体过热变质法,而对于镁锌系及镁稀土系合金则应该用锆变质。
目前,国内外对镁合金变质剂和变质方法的研究很多,不断出现新的成果。
5.浇注和制锭
由于镁合金易于氧化的特性,在浇注铸锭和铸件的过程中,应该对镁合金熔
液进行保护。
常用撒硫磺粉和硼酸的混合物或用气体保护。
此外,应尽可能采用低的浇注温度并保持平稳充型。
第二章铸造技术
铸造是指将金属、合金或复合材料熔化成为液体(熔体),浇注于具有特定型腔的铸型中凝固成形的一种金属材料成形方法。
铸造法是制备金属及合金的锭坯和零件毛坯的主要方法之一。
几乎所有的合金锭坯都是通过铸造制备的。
因为工艺灵活和成本较低,在许多机械产品中,铸件占整机质量的比例很高。
目前,砂型铸造仍是最主要的铸造方法。
此外,还有许多特种铸造方法,如熔模铸造、金属型铸造、压力铸造、低压铸造、离心铸造、壳型铸造、陶瓷型铸造等。
它们的铸型用砂较少或不用砂,采用特殊工艺装备。
可获得表面更光洁、尺才更精确、机械性能更高的铸件。
第一节铸件成形基本原理
铸造是液态金属充填铸型型腔并在其中凝固和冷却的过程。
液态金属的流动特性和凝固收缩特性直接影响着铸件的形成。
同时,液态金属的流动特性和凝固收缩特性也是衡量其铸造性能的重要依据。
一.金属的充型能力
液态金属填充铸型的过程简称为充型。
液态金属充填铸型型腔,获得形状完整、轮廓清晰铸件的能力称为金属的充型能力。
金属的充型能力和金属的流动性、浇注条件以及铸型等因素密切相关。
金属的充型能力和金属的流动性、浇注条件以及铸型等因素密切相关纯金属和共晶成分的合金在恒定温度下结晶时,液态合金从表面逐层向中心凝固,由于液固相界面光滑,对液态金属流动的阻力小,流动性好。
其它成分的合金均在一定温度范围内逐步凝固,由于有初生树枝状晶体使固液界面粗糙,阻碍合金液的继续流动,因此,具有一定结晶温度范围的合金流动性较差,且结晶温度范围越大,流动性越差。
实际应用的合金材料中,为了保证材料具有高的机械性能,绝大多数合金都不是纯金属或共晶成分,因此,必须从浇注条件上保证充型能力。
2.浇注条件(了解)
⑴浇注温度。
浇注温度对充型能力有决定性的影响。
浇注温度越高,液态金属的粘度就越小,液态金属在铸型中保持流动能力的时间就越长,故充型能力也越强。
反之,则充型能力越差。
所以,液态金属在浇注是一般都要求一定的过热度。
⑵浇注压力。
液态金属在流动方向上所受的压力愈大,充型速度越快,充型能力就愈好。
压力铸造、挤压铸造和半固态铸造就是利用这一原理。
⑶铸型条件。
铸型的温度越高、导热系数越小、蓄热系数越小则液态金属的充型能力越好。
但是对凝固速度和合金的组织和性能会产生不利的影响。
此外,充型能力还受到铸件结构(如铸件的薄厚、大小和复杂程度等的影响。
二.铸件的凝固与收缩
1.凝固过程。
金属液注入铸型后,按照传热学基本规律,与铸型型腔表面相接触的金属液将首先冷却结晶转变为固态。
此时,金属形态由已结晶的外层固相区、未结晶的心部液相区以及两者之间的两相区(即凝固区)组成。
随着热量不断从铸件中心向铸型传递,铸件内部温度不断降低,凝固区不断向液相区延伸,固相区不断扩大,直至液相全部消失为止。
2.凝固方式
根据凝固区的宽窄,铸件的凝固方式可分为如下三种:
(注意识图)
(1)逐层凝固:
纯金属或共晶成分合金在凝固中因不存在液、固两相并存的凝固区,故断面上外层的固体和内层的液体由一条界线(凝固前沿)清楚地分开。
随着温度的下降,固体层不断加厚,液体层不断减少,直到铸件的中心。
(2)糊状凝固:
如果合金的结晶温度范围很宽,且铸件截面上温度变化小,则在凝固的某段时间内铸件表面不存在固相层,液、固共存的凝固区贯穿整个断面。
(3)中间凝固:
大多数合金的凝固介于逐层凝固和糊状凝固之间,称为中间凝固方式。
影响铸件凝固方式的主要因素包括:
(1)合金的结晶温度范围:
合金的结晶温度范围愈小,液固两相并存的凝固区域愈窄,愈倾向于逐层凝固。
(2)铸件的温度梯度:
铸件凝固时内外层之间的温度差越大,则其对应的凝固区域越窄,愈倾向于逐层凝固。
2.铸件的收缩
合金从浇注、凝固到冷却至室温的过程中,其体积或尺寸缩减的现象称为收缩。
收缩是金属的物理本性。
合金的收缩为铸造生产带来许多困难,是多种铸造缺陷产生的根源。
铸件形成过程中三个阶段的收缩:
(1)液态收缩。
从浇注温度到凝固开始温度间产生的收缩。
(2)凝固收缩。
从凝固开始温度到凝固终止温度间产生的收缩。
(3)固态收缩。
从凝固终止到室温间产生的收缩。
铸造质量控制:
缩孔和疏松。
金属液在铸型中冷却和凝固时,若液态收缩和凝固收缩所缩减的容积得不到补充,则在铸件的厚大部位等最后凝固部位将形成一些孔洞。
其中,在铸件中集中分布且尺寸较大的孔洞称为缩孔,分散且尺寸较小的孔洞称为缩松(疏松)。
缩孔和疏松都使铸件的机械性能降低,疏松还是造成铸件渗漏的重要原因。
因此,缩孔和疏松都属于铸造缺陷,必须根据技术要求在制备过程中采取适当的工艺措施予以防止。
在实际铸件的生产中,通常采用顺序凝固的原则来避免铸件产生缩孔、疏松缺陷。
所谓顺序凝固是指通过在铸件上可能出现缩孔的厚大部位安置冒口等工艺措施,使铸件上远离冒口的部位先凝固,而后是靠近冒口的部位凝固,最后是冒口本身凝固。
按照这样的凝固方式,先凝固区域的收缩由后凝固部位的金属液来补充,后凝固部位的收缩由冒口中的金属液来补充,从而使铸件各个部位的收缩都能得到补充,而将缩孔移至冒口之中。
冒口为铸件上多余的部分,在铸件清理时将其去除。
为了实现顺序凝固,在安放冒口的同时.还可以在铸件的某些厚大部位放置冷铁,以加大局部区域的凝固速度。
(2)铸造应力、裂纹和变形。
在铸件的固态收缩阶段会引起铸造应力。
按其形成原因,可分为机械应力、热应力和相变应力。
铸造应力是引起铸件变形的根本原因.当铸造应力过大时,还易在应力集中部位产生裂纹。
3.合金的偏析及吸气性
铸件各部分化学成分不均匀的现象称偏析。
它影响铸件性能和质量,必须减少和防止。
合金中总会吸入一定量的气体,且随温度升高其含量增加。
若凝固前气体来不及排除,铸件将产生气孔。
气孔的存在减小了铸件的承载面积,并是应力集中源,显著降低了铸件的机械性能和气密性。
铸件可能出现的几类气孔及形成:
①侵入性气孔:
指在浇注过程中铸型和型芯受热产生的气体及型腔中的空气侵入金属液中所形成的气孔,其数量少、体积大,常出现于铸件上表面或靠近型芯的表面处。
②析出性气孔:
指溶解于合金液中的气体在冷凝过程中,因气体的溶解度下降而析出,在铸件中产生的气孔,主要是氢气孔和氮气孔。
③反应性气孔:
指浇入铸型的金属液与铸型材料、冷铁和熔渣反应以及金属液内部某些成分之间进行化学反应所产生的气孔。
三.铸锭的宏观组织及控制
铸锭及铸件的组织,包括晶粒的形状、大小和分布状况以及溶质的重新分布形式等,对于它们的性能尤其是机械性能有很大的影响。
液态金属在铸型内凝固时,根据液态金属所含溶质的种类与铸型的材料、大小、熔化及浇注温度、浇注方法等等能够得到不同的凝固组织。
一般来说,工业上的铸锭和铸件凝固后的宏观组织具有三个晶体形态不同的区域
典型铸锭凝固后的断面宏观组织:
(1)激冷区。
紧邻型壁的一个外壳层,它是由无规则排列的细小等轴晶粒组成的。
(2)柱状晶区。
它是由垂直于型壁,彼此平行的柱状晶粒所组成的。
(3)等轴晶区。
它是处于铸锭(件)的中心区域,由等轴晶粒所组成的。
这中心区域的性质是各向同性的。
等轴晶区中晶粒尺寸往往比激冷区的大得多。
这三个区域的大小随凝固条件的不同而变化。
一般而言,激冷区较薄,只有数个毫米厚,其余二个区域比较厚。
当液态金属刚一注入时,型壁接触部分的液体受到剧烈的冷却,获得很大的过冷度,加之型壁对形核又有利,于是在紧邻型壁的那部分液体中就产生了大量的晶核。
型壁表面随着激冷区的形成逐渐变热,对液态金属的冷却作用减缓。
达时只有处于结晶前沿的那层液体金属才是过冷的,才可以进行凝固,但是由于此层液态金属过冷度很小,所以一般不会产生新的晶核,而是以激冷区内壁上原有的晶粒为基础进行长大。
同时,由于散热是沿着垂直于型壁的方向进行的,而凝固时每个晶粒的成长又受到其四周正在成长的晶体的限制,因此结晶只能沿着垂直于型壁的方向由外向里生长,结果就形成了彼此平行的柱状晶区。
随着柱状晶的发展,型壁温度进一步升高,散热愈来愈慢,而成长着的柱状晶前沿的温度又由于结晶潜热的放出而有所升高。
这样整个截面的温度逐渐变为均匀。
当剩余液态金属都过冷到熔点以下时,就会在整个残留的液态金属中同时出现晶核而进行凝固。
在这种情况下,由于冷却较慢,过冷度不大,形成的晶核也不会很多,所以铸锭及铸件的中心区就形成了比较粗大的等轴晶粒。
2.铸锭组织的控制
一般而言,铸锭(件)表面激冷区比较薄,它对铸锭(件)的机械性能不发生决定性的影响。
铸锭的性能主要取决于柱状晶区和等轴晶区的比例。
控制铸态组织就是控制铸锭(件)中等轴晶区和柱状晶区的相对比例。
一般在铸锭和铸件上都希望获得细小的等轴晶组织,主要有以下几种工艺途径。
(1)增加形核的机率。
(2)抑制晶体的长大。
(3)使正在生长的枝晶产生“颈缩”。
(4)促使颈缩的晶体脱离模壁或枝晶干。
(5)使熔断破碎的晶体不被重新熔化。
凝固组织形态的控制主要是晶粒形态和相结构的控制。
相结构在很大程度上取决于合金的成分,而晶粒形态及其尺寸则是由凝固过程决定的。
晶粒形态的控制主要是通过形核过程的控制实现的。
促进形核的方法包括浇注过程控制方法、化学方法、物理方法、机械方法、传热条件控制方法等。
砂型铸造的特点及应用
砂型铸造的设备简单、投资小,生产成本低、不受铸件材质、尺寸、质量和生产批量的限制,几乎所有的铸件都可以采用砂型铸造。
造型工作量大,铸件尺寸精度和表面质量差,易产生铸造缺陷,机械性能差。
第三节.特种铸造
在砂型铸造的基础上,通过改变铸型材料、浇注方法或凝固条件等而产生的其他铸造方法。
通常把这些有别于砂型铸造的其他铸造方法统称为特种铸造。
常见的特种铸造方法有金属型铸造、熔模铸造、陶瓷型铸造、压力铸造、低压铸造、离心铸造、连续铸造和消失模铸造等。
每一种特种铸造方法都能在提高铸件质量、提高劳动生产率、降低成本和改善劳动条件等方面,表现出其特殊的优越性,因此成为铸造技术不可缺少的重要组成部分。
一.金属型铸造
金属型铸造是指利用金属材料(例如铸铁)制成铸型或型芯,在重力条件下将熔融金属浇入铸型中制造铸件的一种铸造方法。
由于一套金属型可以重复使用数百次甚至数万次,故金属型铸造又称为永久型铸造。
1.金属型铸造的特点及其应用。
金属型可以连续重复使用,生产效率高,劳动条件好。
铸件质量稳定,尺寸精度较高,表面粗糙度较低。
铸件晶粒细化、组织致密,使机械性能明显提高。
但金属型的制造成本高,不透气且无退让性,易造成铸件浇不足或开裂。
受铸型限制,采用金属型铸造时合金的熔点不宜太高,铸件的形状和壁厚等有一定局限性。
金属型铸造主要适用于制备铸锭及大批量生产的有色合金铸件,例如铝合金活塞、汽缸体和油泵壳体,铜合金轴瓦和轴套等。
二.熔模铸造
熔模铸造是指利用易熔材料(例如蜡)制成模型,并在模型表面粘结一定厚度的耐火材料,然后加热将模型熔失再将金属液充满型腔的一种铸造方法。
这种铸造方法比砂型铸造所获得的铸件尺寸精度和表面质量高,因此又称为熔模精密铸造。
熔模铸造工艺过程的主要工序包括蜡模制造、制壳、脱蜡、焙烧和浇注等。
a.可获得尺寸精确高、表面光洁的铸件。
b.可铸造出形状复杂的铸件。
c.不受铸造合金种类的限制。
三.压力铸造
压力铸造简称压铸,是指将液态或半液态合金浇入压铸机的压室内,使之在高压和高速下充填型腔,并在高压下成形和结晶而获得铸件的一种铸造技术。
压力铸造是在压铸机上进行的。
压铸所用的铸型称为压铸模。
为了获得高质量的压铸件,压铸模具型腔部位应具有很高的尺寸精度和表面质量。
压铸最大的特点是生产效率高,铸件质量好。
但只适合用于大批量生产的有色合金中小铸件。
四.离心铸造
将液态金属浇入高速旋转的铸型中,使金属在离心力的作用下填充铸型并凝固成形的铸造方法称为离心铸造。
离心铸造主要用于生产圆筒形铸件。
离心铸造机分为立式和卧式两种。
立式离心铸造机上的铸型绕垂直轴旋转,主要用于生产高度小于直径的圆环类铸件。
卧式离心铸造机上的铸型绕水平轴旋转,主要用于生产长度大于直径的套类或管类铸件。
五.连续铸造
连续铸造是将熔融金属液连续不断地浇入到被称为结晶器的特殊金属型中,凝固的铸件不断从结晶器的另一端被引出,从而获得任意长度的等截面铸锭或铸件的铸造方法。
连续铸造时,金属的冷却速度快,组织致密,机械性能好,不用造型和浇注系统,大大简化了工艺和提高了生产效率。
连续铸造是目前生产钢材、铝材铸锭和铸铁管的主要方法。
第三章半固态铸造
当剧烈搅拌正在凝固的金属或合金时,虽然在凝固过程中随着温度的下降合金中的固体组分不断增加,甚至增加到40-60%以至更高时,这种合金仍然象糊状浆料一样具有很好的流动性,仍可以用压铸等铸造方法成形。
合金在半凝固状态下表现的这种类似液体可以流动的、带有粘性的特性,称为流变性,它是半固态流变铸造的理论基础。
半固态铸造是介于液态成形和固态成形之间的一种金属成形方法。
现已发展了流变铸造和触变铸造两种方法。
1.半固态铸造的原理
半固态铸造的工艺原理是将合金熔化后,待它冷却到液相线温度以下时,对合金进行搅拌,在搅拌力的作用下,合金中析出的树枝状晶被破坏,并在周围金属液的摩擦熔融作用下,晶粒和破碎的枝晶小块形成近似球状的颗粒,分布在整个液态金属中。
这时合金即使固态组分达40%-60%,仍然像糊状的悬浮液,具有一定的流动性。
而在剪切力较小或为零时,它又具有固体性质,可以进行搬运储存。
利用这一原理,