浅谈制动系统的正向设计word文档.docx
《浅谈制动系统的正向设计word文档.docx》由会员分享,可在线阅读,更多相关《浅谈制动系统的正向设计word文档.docx(9页珍藏版)》请在冰豆网上搜索。
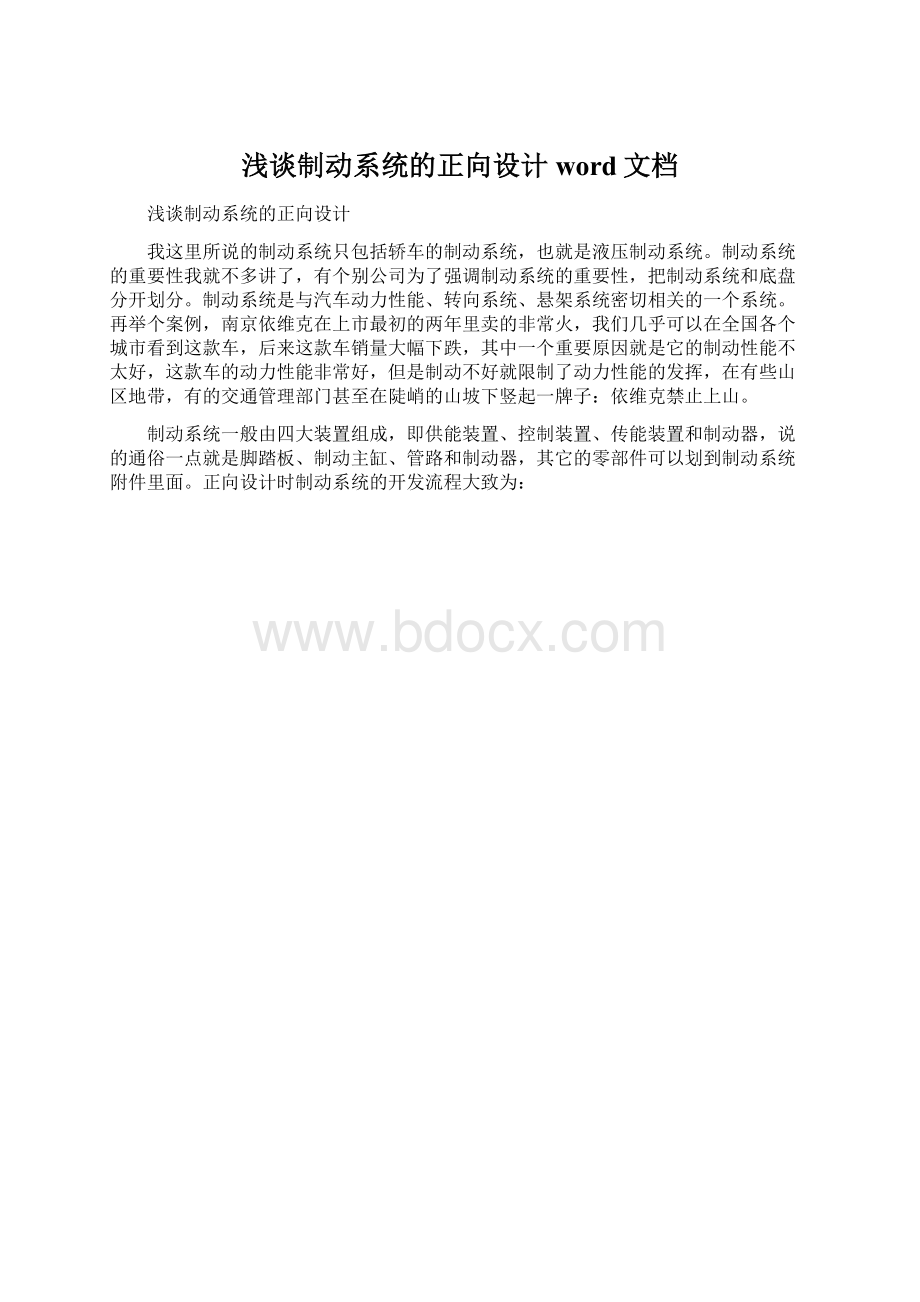
浅谈制动系统的正向设计word文档
浅谈制动系统的正向设计
我这里所说的制动系统只包括轿车的制动系统,也就是液压制动系统。
制动系统的重要性我就不多讲了,有个别公司为了强调制动系统的重要性,把制动系统和底盘分开划分。
制动系统是与汽车动力性能、转向系统、悬架系统密切相关的一个系统。
再举个案例,南京依维克在上市最初的两年里卖的非常火,我们几乎可以在全国各个城市看到这款车,后来这款车销量大幅下跌,其中一个重要原因就是它的制动性能不太好,这款车的动力性能非常好,但是制动不好就限制了动力性能的发挥,在有些山区地带,有的交通管理部门甚至在陡峭的山坡下竖起一牌子:
依维克禁止上山。
制动系统一般由四大装置组成,即供能装置、控制装置、传能装置和制动器,说的通俗一点就是脚踏板、制动主缸、管路和制动器,其它的零部件可以划到制动系统附件里面。
正向设计时制动系统的开发流程大致为:
Y
关于制动系统的计算,有太多的资料和书籍讲述这方面的知识,我也就不多说了。
我今天提一下咱们81的制动系统,我一直认为咱们81制动系统的同步附着系数计算有误,关于同步附着系数的概念,汽车理论是这样定义的:
理想的前后制动力分配曲线和实际的前后制动力分配曲线交点处的附着系数为同步附着系数,也就是常说的I曲线和ß线的交点,理论上来讲,满载的I曲线永远在空在的I曲线上面,也就是满载的同步附着系数永远比空载的同步附着系数大。
但是咱们81的满载同步附着系数比空载的要小,所以我认为81的制动系统计算结果有误。
但是这并不代表咱们81制动系统方案有误,因为81的制动系统是逆向开发的,逆向做的方案和计算报告联系并不大,这也是逆向设计的优点。
如果是正向设计,计算报告错的话,制动系统方案一定是错的。
下面讲一些具体的方案设计,首先从踏板开始:
踏板机构涉及到人体工程学,既要满足操纵性能的要求,又要满足人体运动学原理,给人以操纵的方便性和舒适性,这就要求许多相关尺寸有相应范围规定,力求适合于绝大多数人对操纵性的需求
相关的尺寸及规定
1,离合器踏板左侧边缘至R点的距离C=>>100
2,制动踏板右侧边缘至R点的距离D=>>100
3,制动踏板右侧至油门踏板左侧距离E=>>60
4,离合踏板左侧边缘至踏板垫右侧G=>>60
制动踏板右侧边缘至通道距离H=>>137
油门踏板右侧至通道的距离K=>>15
5,制动踏板宽度(机械变速/自动变速)L=>>50/100
6,离合器踏板宽度M=>>50
踏板垫宽度N=>>60
7,制动踏板下边缘至地毯上边缘的高度Q=145+8
8,油门踏板下边缘至地毯上边缘的高度O=>>110+10
9,离合器踏板下边缘至地毯上边缘的高度S=>>145+8
10,制动踏板,离合器踏板在最大行程时
至油门踏板参考点A的距离X=135
12,制动踏板至方向盘的下边缘L13=MIN590
离合器踏板至制动踏板0-10
13,油门踏板至制动踏板的高度差L52=大约50
咱们公司用的都是大众的踏板设计标准,他们编写的这个标准的数据大多来源于捷达轿车,其实大众的标准中的有的参数已经过时,比如制动踏板和离合踏板高度,现在的踏板高度一般都达不到145mm。
离合器踏板和制动踏板高度差也没有严格规定,宾法曾给我发过一个关于离合制动踏板高度的调查报告,当时他们调查了近20个车型,包括奔驰宝马阿尔法等车型,我印象中离合比制动高16mm的车都有,也有离合比制动低的。
在ABC三踏板布置时,首先确定的是A踏板,如何确定A踏板的位置取决于邢孔归,也就是有人机工程来定的,其次是制动踏板。
制动踏板和油门踏板的间距要求是大于60mm,我个人认为设计状态最好定为65mm,原因是制造偏差,一般的供应商能把这个间距误差控制在5mm左右,最好的供应商也只能把这个误差控制在2mm或者3mm,离合踏板相对于制动和油门,地位就低下得多,可以做成70,也可以设计成100,原因是离合是由左脚来控制的,而制动和油门是同一只脚,间隙太大换脚时容易踩空,间隙小时容易误踩
车型数据(mm)
a
b
c
d
e
f
g
h
I
适用范围
175~215
60~100
75~125
35~55
65±5
60以上
60以上
30~50
没有标准
支架总成
●支架根据结构及空间需求,设计成不同的形状,可以采用整体式或分离式(离合器踏板支架,制动踏板支架,油门踏板支架)再连接成总成。
●从目前来看,主要采取冲压成型或全塑件,铝合金压铸结构,在满足强度同时,尽可能减轻重量,以提高整车的经济性。
●对于安装各类开关的位置,设计支架时要考虑安装方便性,一般采用卡接形式,简单可靠。
●设计开关支架位置时,要考虑到开关的工作行程是靠踏板臂上下运动的来实现的。
所以设计位置时,首先要确定开关行程,协调开关同踏板臂的运动关系。
(制动灯开关,离合器开关等)
●踏板销轴是支架设计中关键部位,要满足踏板在自重作用下100%地自动回落,不用回位弹簧,以便降低成本。
其轴向间隙设计成最大0.5mm,径向间隙0.1mm.
●为了提高寿命,轴上涂以油脂.但,目前采取更为先进的技术,在衬套上涂以聚四氟乙稀薄膜,它含有石墨等润滑材料,不再涂油脂
ABC三个踏板分管三个独立的系统,也各有各的特性,油门踏板行程比较小,一般为60左右,踏板力在30N左右,踏板面曲率和角度要求比较高,有的油门踏板除了在运动过程中围绕安装点公转,踏板垫本身也自转,就是为了踩起来更舒适。
制动踏板杠杆比曾变小的趋势,真空助力器膜片直径曾变大趋势。
以前的杠杆比一般在3.5到4.65之间,现在的一般在3左右,离合的踏板行程在三个踏板中是最大的,杠杆比也比较大,在4到5之间的比较多。
由于离合的行程一般都比制动踏板大,所以在设计时,离合踏板面与地板的角度要比制动小,是为了离合踏板在踩到底的时候脚掌和小腿的角度变化不是太大。
真空助力气部分:
真空助力器从膜片数量上分单膜片和双膜片两种,根据布置的需要来选择相应规格的助力器。
单膜片助力器常用规格有6、7、8、9、10、11英寸的,双膜片的有7+8、8+9、8+8等组合。
做制动系统设计时,真空助力器基本上都是选型件,最重要的是和根据制动系统需要设计它的性能参数。
真空助力器是对踏板感觉影响非常大的一个件,关键参数有始动力,跳跃值,助力比和最大助力点,在这里需要纠正的是很多同事都认为助力器的助力比越大越好,其实不然。
比如说9英寸的助力器助力比设为7.5,对踏板的影响是助力范围小,刹车来的急,一旦真空度降低较多后,助力器失效非常明显,第二是小助力器大助力比对助力器的寿命影响非常大。
常用的制动主缸分为补偿孔式和中心阀式两种,补偿孔价格便宜,技术含量比较低,和非ABS制动系统对应,中心阀用在ABS车上(也可用在非ABS车上),制动主缸常用的规格有20.64\22.22\23.81\25.4。
储液罐的设计
材料:
PP(聚丙烯)
单腔失效容积的确定:
(1)计算方法:
制动主缸单腔活塞行程×活塞截面积×(3-5),
(2)要求:
单腔失效容积要保证汽车倾斜45°时还能有3-5次制动,
●制动储液罐最小容积的确定:
单腔失效容积是制动储液罐最小容积确定时的一个很重要的参数,根据经验公式,制动储液罐的最小容积一般是单腔失效容积的2-3倍,
●制动储液罐最大容积的确定:
制动储液罐的最大容积一般是单腔失效容积的3-5倍,
●制动储液罐的报警装置:
采用液压制动的机动车,其储液罐的加注口必须易于接近,从结构设计上必须保证在不打开容器的条件下就能很容易地检查液面。
若不能满足此条件,则必须安装制动液面过低报警装置。
现在储液罐不管透明不透明基本上都有报警装置,只有极个别的车没有最低液面报警,如捷达。
●设计制动储液罐应该注意的一些事项:
1,在制动储液罐最小容积已经确定的前提下,加注口的位置毫无疑问是首先要考虑的
2,储液罐重心尽量和制动主缸进油口在一个平面内,防止极限工况下,制动储液罐上下摇摆太厉害,从制动主缸中脱开
3,和主缸的连接方式.若是储液罐容积较小,而且重心和储液罐出油口基本在一个平面内,可以不考虑其他的辅助连接方式.相反,则必须考虑.
4,由于制动储液罐的开发周期较长,而且模具几乎没有改动的余地,所以在车型开发期间要尽可能早的确定制动储液罐的方案
制动管路:
制动管路材质
轿车一般都采用刚性管,刚性管以前采用无缝钢管、单层焊接钢管和铜管,现已为双层卷焊钢管所取代。
按照GB11611-1989《汽车液压制动系金属管、内外螺纹管接头和软管端部接头》的规定,汽车液压制动系所用的双层卷焊钢管的规格列于下表:
外径D1(mm)
(未经表面处理)
管外径D1(mm)
(最大)
(经表面处理)
爆破压力
(Mpa)
(最小)
质量
(kg/m)
基本尺寸
极限偏差
基本尺寸
极限偏差
4.75
±0.07
0.7
±0.07
4.87
110
0.07
6.00
6.12
85
0.09
8.00
8.12
67.5
0.12
10.00
10.12
55
0.16
由于制动管大部分位于底盘下方,使用环境恶劣,对其表面防腐和保护要非常严格。
目前普遍采用镀锌25um、铬酸盐钝化、涂覆聚氟乙烯(PVF)15um的表面防腐层,同时在关键部位套装双层热收缩管,以防石击或摩擦损坏。
布置设计基本要求
a.最小间隙要求
与不动件
与动件
与转向机中间轴
与排气管
5
15
25
51
b、工艺要求
在设计布置的过程中需要留意的是在国内制动管中心线倒角半径均为15mm,两个倒角之间距离最小不能小于10mm,另外就是制动管两端为了考虑装配,应该预留至少一个制动管螺母高度那么长的距离,也就是16mm,如下图所示
c.设计要求
●在装配的时候需要有足够的工具空间,满足装配人机工程
●制动管必须用制动管夹可靠固定,不允许与其它部件有干涉
●没有固定点的管夹在制动管上的固定点需要能够易于识别
●三通必须与车身固定
●管夹之间距离不超过300mm
在满足使用要求的同时,兼顾美观
设计管路前首先要先布置管嘉,管夹根据安装形式大致分为两种,第一种是与焊接螺栓配合,第二种是与孔配合,一般情况下不推荐使用第二种形式,因为这样需要车身开孔,降低了车身强度,并且容易导致灰尘和雨水进入车身
设计制动管路时我个人喜欢用CATIA或者PRO-E做然后备份,因为管路在设计过程中的改动非常频繁,需要不断的改拐点更新数模,最好是在增加、删除或者替换某个拐点后管路数模能够自动更新,这样就节省了很大的工作量。
关于汽车制动管路的布置形式,汽车工程手册上提到了五种不同的布置形式,分别是:
II型、X型,HI型、LL型和HH型。
以前的轿车用II型和X型的比较多,现在比较流行的X型和H型,II在轿车上逐渐淘汰,比如夏利最早是II型管路布置,现在已经改成了X型,H型的在非承载式车身的的SUV上用的比较多,比如帕杰罗,路霸。
用X型还是用H型是由悬家系统的主销偏距决定的,当主销偏距为负的时候用X型,主销偏距为正用H型。
原因是X型布置在单回路失效时前轮的制动力是不均衡的,虽然X型的在单回路时效时汽车还保持一定的转向能力和抗侧滑能力,但是制动力的不均衡对汽车的方向稳定性有不良影响,主销负偏距可以对此有所缓解。
以前曾经和马显讨论过R08的管路布置形式,后来我查了一下R08的注销偏距是负12点多,所以R08的管路布置是X型的。
制动软管的设计
●液压制动软管总成由制动软管和制动软管接头组成,制动软管与软管接头之间是永久性联接,该连接是靠接头部分相对于软管压皱或冷挤变形来实现的。
●在设计制动软管的长度时要综合考虑车轮跳动的上下两个极限位置,转向轮还应该考虑转向的极限位置。
长度要适中,不能太短,否则在车轮跳动或车轮转向时会造成软管脱落;也不能太长,如果太长会导致软管的膨胀过大,影响制动性能。
数摸设计时首先确定制动软管的上安装点,制动软管的长度要大于上下两个固定点的直线距离加上车论的下跳极限,在此基础上软管尽可能短。
如果软管两端的接头都是卡接形式的,还需要考虑软管固定支架上U行孔的角度,否则有可能会导致软管装车后扭曲变形或者和周围边界干涉。
●因为在汽车行驶的过程中,制动软管的位置随着车轮位置的变化而变化,所以在容易与其它部件干涉或容易刮伤的软管处加上档圈或护簧等保护装置
比例阀的设计
双腔阀总成配用于微型车,是汽车制动系统中的压力调节装置,安装于制动系统的制动主缸和后轮分泵之间的制动管路中,用于调节后轮分泵的制动液压,从而充分发挥制动效能,提高汽车制动过程中的可靠性和安全性。
双腔阀总成配用于微型车,感载比例阀总成合用于任何车辆。
(注:
素材和资料部分来自网络,供参考。
请预览后才下载,期待你的好评与关注!
)