仓储运作管理2范文.docx
《仓储运作管理2范文.docx》由会员分享,可在线阅读,更多相关《仓储运作管理2范文.docx(16页珍藏版)》请在冰豆网上搜索。
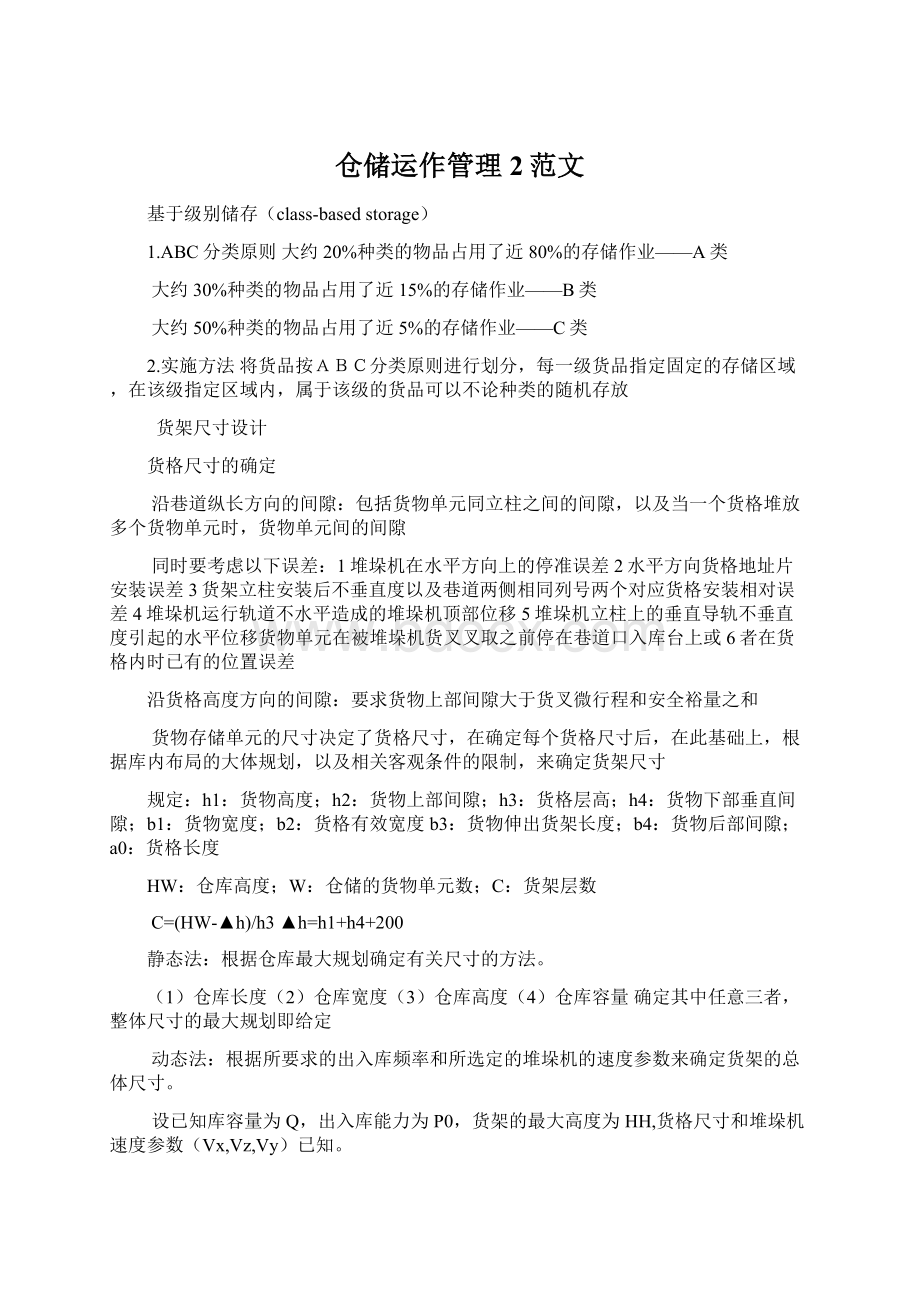
仓储运作管理2范文
基于级别储存(class-basedstorage)
1.ABC分类原则大约20%种类的物品占用了近80%的存储作业——A类
大约30%种类的物品占用了近15%的存储作业——B类
大约50%种类的物品占用了近5%的存储作业——C类
2.实施方法将货品按ABC分类原则进行划分,每一级货品指定固定的存储区域,在该级指定区域内,属于该级的货品可以不论种类的随机存放
货架尺寸设计
货格尺寸的确定
沿巷道纵长方向的间隙:
包括货物单元同立柱之间的间隙,以及当一个货格堆放多个货物单元时,货物单元间的间隙
同时要考虑以下误差:
1堆垛机在水平方向上的停准误差2水平方向货格地址片安装误差3货架立柱安装后不垂直度以及巷道两侧相同列号两个对应货格安装相对误差4堆垛机运行轨道不水平造成的堆垛机顶部位移5堆垛机立柱上的垂直导轨不垂直度引起的水平位移货物单元在被堆垛机货叉叉取之前停在巷道口入库台上或6者在货格内时已有的位置误差
沿货格高度方向的间隙:
要求货物上部间隙大于货叉微行程和安全裕量之和
货物存储单元的尺寸决定了货格尺寸,在确定每个货格尺寸后,在此基础上,根据库内布局的大体规划,以及相关客观条件的限制,来确定货架尺寸
规定:
h1:
货物高度;h2:
货物上部间隙;h3:
货格层高;h4:
货物下部垂直间隙;b1:
货物宽度;b2:
货格有效宽度b3:
货物伸出货架长度;b4:
货物后部间隙;a0:
货格长度
HW:
仓库高度;W:
仓储的货物单元数;C:
货架层数
C=(HW-▲h)/h3▲h=h1+h4+200
静态法:
根据仓库最大规划确定有关尺寸的方法。
(1)仓库长度
(2)仓库宽度(3)仓库高度(4)仓库容量确定其中任意三者,整体尺寸的最大规划即给定
动态法:
根据所要求的出入库频率和所选定的堆垛机的速度参数来确定货架的总体尺寸。
设已知库容量为Q,出入库能力为P0,货架的最大高度为HH,货格尺寸和堆垛机速度参数(Vx,Vz,Vy)已知。
要求
(1):
减少堆垛机的存取作业周期,提高堆垛机的作业效率,则:
H/L=Vx(max)/Vz(max)
(2):
保证货物出入库频率的条件下,实现巷道数最少的目标,以提高仓库单位的库容量,减少堆垛机的配备数量。
具体分析步骤
假定堆垛机采取单一作业方式
a)假定巷道数Gn=1,则货架列数LH=W/(2GnC)(其中W为货物单元数,C为货架层数)
b)根据货架层数C和列数LH,参考货格尺寸,计算货架长度L,高度H和货架系数H/L,根据堆垛机速度参数,计算堆垛机平均作业周期:
t0:
固定时间,例如控制信号的获取、转换时间等,是一个常数ty:
货叉作业的伸缩时间
ax:
堆垛机行走方向上的加速度ay:
堆垛机载货台的垂直运动加速度
Vx:
堆垛机行走方向速度Vz:
堆垛机载货台垂直方向加速度
L:
货架长度
c)计算仓库的出入库能力:
d)设P0为要达到的出入库能力,如果P小于P0,则试计算Gn=2的情况,重复以上几个步骤,知道P大于或等于P0为止。
存储区与作业区的衔接问题
叉车——出入库台式货架端部设置出入库台,由叉车在存储区与作业区间运送货物单元
AGV——出入库台式
叉车——积放式输送机利用积放式输送机平衡作业过程
AGV——积放式输送机
5.2库内装卸搬运系统设计
装卸搬运:
指在同一场所内将物品进行水平移动为主的物流作业
装卸(loadingandunloading):
指物品在指定地点以人力或机械装入运输设备或从运输设备卸下的活动
搬运(handling/carrying):
指在同一场所内将物品进行水平移动为主的物流作业
物料搬运活性分析活性系数物料的搬运难易程度称为活性。
散放0装箱1支垫2装车3移动4
活性系数的计算平均活性系数=活性系数总和/作业工序数
低于0.5,有效利用集装器具、手推车
0.5-1.3,有效利用动力搬运车、叉车
1.3-2.3,有效利用输送机,自动导引小车
2.3以上,从设备,方法方面进一步减少搬运工序数
物流基本流动模式:
直线型L型U型S型(避免流动路径的交叉)
装卸搬运方法是指搬运路线、装卸搬运设备和装卸搬运单元的总和。
我们分别讨论这三个方面的选择原则。
装卸搬运路线的选择:
直达型、渠道型、中心型
装卸搬运路线的选择
1.直达型直达型是指物料经由最近路线到达目的地,在直达型路线上,各种物料从起点到终点经过的路线最短,当物流量大,距离短或距离中等时,一般采用这种方式最经济,尤其是当物料有一定的特殊性而时间又比较紧迫的时候最为有利。
2.渠道型渠道型是指一些物料在预定路线上移动,同来自不同地点的其他物料一起运到同一终点,当物流量中等或少量,而距离为中等或较长时采用这种方式比较经济。
3.中心型中心型是指各种物料从起点移动到一个中心分拣处或分发地区,然后再运往终点,当物流量小而距离中等或较远时,这种方式比较经济
装卸搬运方法的选择
装卸搬运设备的配置与选择:
1、选择原则:
①根据作业性质和作业场合进行选择明确作业时单纯的装卸,还是单纯的搬运,还是装卸搬运兼顾,从而选择对应的设备②根据作业运动形式进行选择,运动形式主要分为水平、垂直、倾斜、多平面式③根据作业量进行选择④根据货物种类、性质进行选择⑤根据搬运距离进行选择
2.装卸搬运设备数量的配置
设备数量一般根据装卸作业量和设备作业能力确定
①作业量实际作业量,不是简单的物流量,这是因为货物包装状态不同,作业环节不同,装卸次数不同等等,实际作业量也可能不同②设备类型、性能③作业均衡性货物装卸搬运大都是多环节,多机联合作业,要保持作业的连续性和均衡性,各环节的设备数量,要按照各个环节的作业内容和特点,做到基本均衡,连续作业。
④作业时间在一定设备条件下,作业量越大,作业时间越长,而设备数量增加,可以缩短作业时间,但时间缩短是由限度的,过度通过增加设备数量来缩短时间,反而会导致作业效率的下降,最为明显的,通道资源被多台设备要求占用时,就会出现堵塞。
⑤作业条件在确定设备数量时,要充分考虑作业面积的大小,尽量避免设备作业时的相互干扰
此外,设备运行速度与地形条件、道路情况有关
3.装卸搬运设备的配套设备的配套直接关系到前后作业的相互衔接
①装卸搬运设备在作业区的衔接(设备应相互联系,相互补充,相互衔接)②设备在数量上、吨位上配套(也就是使各作业环节的设备作业能力匹配)③在作业时间上协调(尽量使各环节在作业时间上具有一致性,使整个流程连续进行)④设备周边辅助设备配套
物料搬运的单元化与标准化物料实行单元化改变了物料散放的状态,提高了搬运活性系数,易于搬运,同时也改变了堆放条件,提高空间利用率。
同时实施标准化能合理、充分的利用搬运设备、设施,提高生产率和经济效益
单元化:
将状态和大小不同的物品,集装成一个实体单元,以便于一次拣起和移动,也叫集装单元化或单元负荷
单元化的作用:
1集包装、装卸、搬运、运输、储存为一个系统,实现总体优化2便于实现装卸搬运作业机械化,减轻工人劳动强度,提高工作效率3减少货物变换环节4减少气候条件等的影响
标准化:
指物品包装与集装单元尺寸(例如托盘的尺寸)要符合一定的标准模数,仓库货架、运输车辆、搬运机械也要根据标准模数决定其主要性能参数
物料控制系统
物料搬运是:
用正确的方法,以正确的成本,按正确的程序,在正确的时间,将正确的物料,以正确的数量,运送到正确的地点
物料搬运系统具有五个维度:
移动、数量、时间、空间和控制。
移动物料产生了时间和空间效用,正确的数量、时间和空间离不开精确的控制。
物料控制系统的例子
条形码编码设计:
条码需要携带物种信息,包括托盘号、零件号、批号、设备进入顺序号以及数量。
托盘号:
托盘号用来表示托盘,整个作业过程中托盘号不变零件号:
零件号反映的是在装配图中零件是用来装配哪一种产品以及零件所在的产品部件、装配图中零件的标号批号:
包括批序号和批中编号,批序号表示的是零件的批次,批中编号则标识零件在该批中的序号设备进入顺序号:
表示了零件所要经过的工艺步骤的顺序
一般条码分为三段:
固定段、可更换段和菜单段
固定段:
标识托盘号,始终不变。
托盘分为三类,包括加工托盘、储运托盘和检测托盘
可更换段:
包括零件号、批号、设备进入顺序号。
物品入库,由特定托盘集装时,对应插入到托盘的夹持器中,当托盘上货物转移时,随物品一起转移到下一个托盘上
菜单段:
标识托盘上的工件的数量
装卸搬运系统分析与设计
装卸搬运系统设计通常采用缪瑟提出的SHA法SHA法一般包括四个阶段:
第一阶段:
外部衔接指对已确定系统边界的物流系统,研究物流输入与输出系统的情况,包括物料输入输出系统的方式、频率以及输入输出系统的条件(例如时间、道路及周围情况)等统计资料
HA法的输入资料仍然是PQRST分析结果要对物料分行分类,分析物料的可运性,在搬运过程中的一些限制条件(工艺要求、环保等)。
物料分类的基本方法包括是:
固体、液体还是气体;是单独件、包装件还是散装物料
严格来说任何物料类别都可以按照其物理特性来进行分类,同时数量也特别重要,物料是大量(要求物流速度较快),还是少量(常属于“特殊订货”),搬运大量的物品和少量的物品一般是不一样的。
时间方面的各项因素也需要在进行物料种类划分时被考虑到(一般急件运输成本高,而且要求采用不同的物流方法,而且时间方面的因素决定了物流节拍)。
物料特征表:
要对物料分行分类,分析物料的可运性,在搬运过程中的一些限制条件(工艺要求、环保等),物料装卸搬运的一个关键的内容是要对物料的移动进行详细分析,要分析路线的起点、终点、移动的距离,计算出物流量、运输工作量,一般采用的移动分析方法有流程分析法、起讫点分析法
物料装卸搬运的一个关键的内容是要对物料的移动进行详细分析,要分析路线的起点、终点、移动的距离,计算出物流量、运输工作量,一般采用的移动分析方法有流程分析法、起讫点分析法。
流程分析法:
每次只观察一类物料,并跟随它沿着整个过程收集资料,然后编制出流程图,当物料品种单一或较少的时候,常采用此法
起讫点分析法:
又可分为搬运路线分析法和区域进出分析法
搬运路线分析法:
通过观察每项移动的起讫点来收集资料,编制搬运路线一览表,每次分析一条路线呢,收集该路线上移动的各类物料或各种产品的有关资料,每条路线编制一个搬运路线表
区域进出分析法:
每次对一个区域进行观察,收集这个区域运进运出的所有物料的资料,每个区域要编制一个物料进出图
第二阶段:
总体搬运方案与总体区划设计确定基本物流模式、作业单位、部门或区域的相互关系及外形,对物流线路、搬运设备及容器类型作出初步决策
第三阶段:
编制详细搬运方案
确定详细的物料搬运方法,拟采用的具体方式,设备容器等
第四阶段:
方案实施
案例:
沼律电机厂要验收并压接厂外制造的线圈。
交来的线圈每件重量达10—40千克。
搬运困难,尤其是女工,而且也不安全,因此决定研究改进物料搬运。
该作业的工艺过程为:
卡车交货—称重—压接—检验—下一道工序。
工序虽然简单,但搬运量大,经过分析发现:
搬运共三次,总距离30米,即把线圈搬到工作台或台秤上,再从台秤上卸下各三次,中间还有2次停滞。
其中搬运工序分析如图1所示:
仓库规模的确定一家小型的化学公司,道格拉斯比耶尔,计划在美国西海岸建造一个仓库,该仓库的平均需求预测如下表1所示。
该仓库每月库存周转率将保持为3次/月,总库容中50%为巷道,为了应对未来可能发生的库容需求变化,仅有70%库容被利用,一组普通化学产品平均每磅占用0.5立方英尺的库容,在货架上可堆码16英尺高。
改仓库连同设备在内的造价为30美元/平方英尺,折旧期限为20年,运营成本为每磅0.05美元,总库容的年固定成本为3美元/平方英尺。
租借库容的租金为每月0.1美元/磅。
出入库的搬运费用为0.07美元/磅,问需要建立多大规模的仓库?
混合仓库空间策略的成本计算表
库存控制
库存:
invebtory,指存储的一系列物料
存货:
stock,存货通常在不同的领域有不同的含义,在通常情况下它可以和库存互换使用
SKU:
stockkeepingunit,存货单项,库存中的每一个单项都代表着众多存货中某一种特有的存货种类。
保有库存的原因:
设置库存的原因和我们设置仓储这一作业环节的原因基本是一致的,简单来说可以用一句话来解释:
低成本协调供需在时间、空间上的矛盾(这句话包含的内容很多,例如对销售形成支持,支持生产等等)
反对保有库存的原因
库存相关成本采购成本(procurementcoats)
通常采购成本包括人员成本、订单处理成本、运输成本(有时包括到运到价中)、产品购买价格等等。
如果是首次采购,还包括一系列的例如需求描述、供应商选择、质量检测、谈判等相关费用
库存持有成本(carryingcosts)
空间成本:
占用存储空间而支付的费用(包括该仓库的运营成本、仓库投资等)
资金成本:
占用资金而导致的成本(占持有成本的80%,也是最具主观性的一种成本)
库存服务成本:
保险、库存税(中国通常没有设置)
库存风险成本:
与产品变质、短少、破损或报废相关的费用,也包括例如技术进步等外部因素造成的风险成本
缺货成本(out-of-stockcosts)
难以准确衡量
客户所订的货物无法由指定的仓库供货时,即产生缺货成本
失销成本:
客户选择取消订单,由此发生的成本
保留订单成本:
客户选择等待,由此发生的成本
库存会掩饰企业经营中存在的问题,库存作为一种缓冲,会使企业在经营中组织生产、营销等方面缺乏动力去积极改进,发现存在的错误
5.1概述服务水平(servicelevel)
定义:
描述现有存货满足需求的能力(也就是不发生缺货的能力)
按量计算的服务水平:
服务水平=1-(每年产品缺货件数的期望值)÷(年需求总量)
①订单完全履行能力:
订单通常可能包括多种商品,只有对每一种商品的订货都得到完全的满足才能成为订单完全履行,通常采用概率来描述这一能力水平②加权平均履行概率(weightedaveragefillrate,WAFR)
例:
某公司有三种产品,客户按不同的品种组合进行采购,根据给定的历史数据统计分析得到如下数据:
SL1=0.95SL2=0.90SL3=0.80
按订购周期计算的服务水平
即给定一定时间内不发生缺货的概率,通常称为订购周期内的现货供应概率
P{M实<M库}
例:
博登食品公司在其仓库中存有柠檬汁系列产品,博登曾经在仓库中存放相当多的这种产品,可以保证该产品在4年内都不会缺货,此时,该产品的服务水平超过99%,虽然这是公司销量很高的产品,但问题在于是否有必要将库存水平定到如此高的水平。
根据公司的一般经验,服务水平每变化1%,毛收入就变化0.1%。
仓库每周向零售店补货,所以客户服务水平可以定义为补货提前期内仓库有存货的概率。
销售毛利是每箱0.55美元,每年经仓库销售的量均值为59904箱,每箱标准成本是5.38美元,年持有成本率估计为25%,补货提前期是一周,平均每周的销量为1152箱,标准差为350箱。
(边际分析的基本思路即当收入的变化量(△R)等于成本变化量(△C)时可以得到最优服务水平。
)
△R=销售毛利×销售反应系数×年销量=0.55×0.001×59904=32.95美元
表示服务水平每变化1%,年收入变化32.95美元
△C=年库存持有成本×标准产品成本×订单周期内需求的标准差×△Z
=0.25×5.38×350×△Z=470.75△Z(Z表示正态偏差,△Z表示Z的变化量)
§5.2独立需求库存控制模型
1再订货点法基本思想:
假设需求持续耗用库存,当有效库存水平下降到低于或等于某一给定值(再订货点,ROP)时,发出订单,订货量为一固定值Q。
连续盘点
有效库存水平:
实际在库数量+在途库存-已收订单未出库量缺货发生在提前期内
预留ROP水平的库存是为了满足提前期内的需求
、Q*=
由经济订货批量(EOQ)模型给出D:
单位时间内的需求均值S:
每订单成本I:
库存持有成本率C:
产品单位成本
ROP给定服务水平,即现货供应概率SL(servicelevel)
则:
最优的ROP满足P﹛MLT≤ROP*﹜=SL
例1:
给定服务水平为0.875,年需求量的均值为18000单位/年,每订购一次的采购成本为2000元,每单位库存每年的库存持有成本为50元,提前期为1天,给定提前期内需求量的概率分布如下表,求Q﹡和ROP﹡。
例2:
拜尔斯产品公司经销一种名为尖端连杆的产品,相关数据如下:
产品月需求量满足均值D为11107个,标准差为Sd为3099个的正态分布,补货提前期为1.5个月,产品单价为0.11美元/个,订单成本为10美元/订单,单位库存持有成本率为20%每年,规定提前期内的现货供应概率为0.75,求Q﹡和ROP﹡
2定期订货法
单一产品的定期订货法库存控制
基本思想:
间隔固定的时间盘点库存,发出订单,订单订货量为设定的最高库存水平减去盘点时的有效库存水平缺货发生时间:
T+LT
设置最高库存水平的目的:
在一定程度上满足T+LT时间段内的需求
M*:
P﹛MT+LT≤M*﹜=SLT*:
由经济订货批量给出
例1:
拜尔斯产品公司经销一种名为尖端连杆的产品,相关数据如下:
产品月需求量满足均值D为11107个,标准差为Sd为3099个的正态分布,补货提前期为1.5个月,产品单价为0.11美元/个,订单成本为10美元/订单,单位库存持有成本率为20%每年,规定提前期内的现货供应概率为0.75,求T﹡和M﹡
T*=Q*/D=11008/11107≈0.991≈1个月
(T*+LT)内需求的标准差:
Sd’=Sd(T*+LT)1/2=3099×(0.991+1.5)1/2≈4891
又因为P=0.75
所以:
M*=D(T*+LT)+Z×Sd’=11107×(0.991+1.5)+0.67×4891≈30945
平均库存水平:
AIL=DT*/2+Z×Sd’=8780
3联合订货
联合采购周期
某企业对来自同一供应商的两种产品进行联合订货,现有数据如下表:
其中Z0.7=0.67Z0.75=0.52
联合订货时间间隔:
T*=(2×(30+10+10)÷(0.3/365)÷(150×25+75×50))1/2≈4.03≈4天
(Sd’)A=(Sd)A×(T*+LTA)=7×(4+14)1/2=29.70
(Sd’)B=(Sd)B×(T*+LTB)=11×(4+14)1/2=46.67
M*A=25×(4+14)+0.52×29.70≈465M*B=50×(4+14)+0.67×46.67≈931
4按需存储
基本思想:
对某种产品的需求速率进行预测,预测值乘以一个代表盘点周期、补货提前期以及包含需求预测和提前期不确定性的时间增量因子,从而得到目标值,订购量为目标值减去有效库存
例:
某大型保险公司的材料管理员每个月要对职员需要的办公纸进行预测,某月,复印纸的使用量预计为2000令,库存纪录显示现有存货750令,没有在途货物,也没有保留订单的货物,向纸张经销商订货后一周才能收到货物,而材料管理员希望手中有相当于一周需求量的额外存货作为安全库存。
解:
一个月四周,意味着所订的货物量要满足四周的需求,对该月需求量的预计值为2000令,为了防止缺货的发生,要设置安全库存,并要考虑提前期,作适当的调整。
盘点周期:
4周提前期:
1周安全库存:
1周求和:
6周
M*=2000÷4×5+2000÷4×1=2000×6/4=3000
6/4称为增量因子订购量:
Q=3000-750=2250
5最低最高库存控制
基本思想:
按固定间隔盘点库存,当有效库存水平下降到等于或者小于再订货点时,发出订单,否则不发出订单,订单订货量为最高库存水平减去有效库存水平。
M*=ROP+QEOQQ*=M*-I
强制联合订货
A、B、C三种产品由同一供应商供货,假定A达到订货条件,B、C在这时即使没有达到订货条件也可以发出订单,同时:
需求波动较大情况下的修正
当标准差大于或者等于需求均值的时候,认为有必要修正最低最高库存模型
考虑到两次库存记录更新之间,需求波动大的产品可能会出现较大的产品需求,使库存水平出现明显下降,导致缺货情况失控,此时需要认为的抬高ROP来调整订单发出时间。
调整方法:
ROPnew=ROP+预计短缺量
预计短缺量一般可以设置为库存记录更新间隔期内的平均需求量
注意:
订单订货量的计算方法不变,仍取原ROP
6多产品、多渠道的库存管理
基本思想:
尽管可以将库存管理问题看做是多个单一产品、单一存储点的问题,但也可以用一种总体的方法集中考虑几个重要的经济问题,例如以整车方式运输、或以经济批量生产。
例题:
某制造商生产饭店、医院、洗车厂、制造商、学校使用的清洁化工品,其200多类产品750多个品种销售到全国各地,产品储存在约40个仓库中,但并非每个仓库都储存所有产品,公司生产的肥皂类产品年销量达到2.2亿美元,其中70%通过仓储系统进行分拨,该工厂开发了自动化的库存管理系统,以期按下图所示的方法来控制库存水平。
P46
库存总量控制集中型和分散型的库存系统库存周转率ABC产品分类
案例:
ACME是一家在美国东北部生产和销售电子设备的公司,目前的销售系统将东北区域划分为两个市场,每个市场都设有一个仓库,一个仓库位于新泽西的帕里梅斯,另一个位于马萨诸塞洲的牛顿,顾客(一般指零售商)向仓库直接订货,在目前的销售系统中,每个顾客被分配到其中一个市场并向相应的仓库订货。
仓库向位于芝加哥的一家制造工厂订货,制造工厂到每个仓库的交货提前期大约为一周,制造工厂具有足够的生产能力来满足任何仓库的订单。
目前的销售系统提供97%的服务水平,也就是说每个仓库实施的库存策略是经过设计的,其缺货概率为3%,未得到满足的订单被竞争对手夺走,因此缺货不能用将来的存货来满足。
现行的销售系统是7年前设计的,公司新上任的首席执行官决定修改目前的物流和销售系统。
ACME的仓库处理约1500种产品,向东北约10000个客户提供服务。
ACME公司正在考虑如下的方案策略:
用位于帕里梅斯和牛顿之间的一个仓库代替现有的两个仓库,并且首席执行官坚持认为不管采用什么物流策略都必须维持同样的97%的服务水平。
分析该方案的可行性,以下三个表所提供的是关于两种产品A、B的历史数据,以此作为决策的数据资料
产品A的历史数据
周12345678
马萨诸塞洲3345373855301858
新泽西4635414026481855
总计79807878817836113
产品B的历史数据
周12345678
马萨诸塞洲02300130
新泽西24003100
总计26303230
统计项产品平均需求需求的标准差
马萨诸塞洲A39.313.2
马萨诸塞洲B1.1251.36
新泽西A38.612.0
新泽西B1.251.58
总计A77.920.71
总计B2.3751.9
库存周转率
库存周转率=某库存成本下的年销售额÷平均库存投资
库存周转率通常被用来在总体上衡量库存控制在经济方面的效率
ABC产品分类
将产品划分为有限的几类,然后针对每类产品使用不同的库存管理方法,利用此方法的关键在于分类原则的把握