汽化器传热设计计算.docx
《汽化器传热设计计算.docx》由会员分享,可在线阅读,更多相关《汽化器传热设计计算.docx(24页珍藏版)》请在冰豆网上搜索。
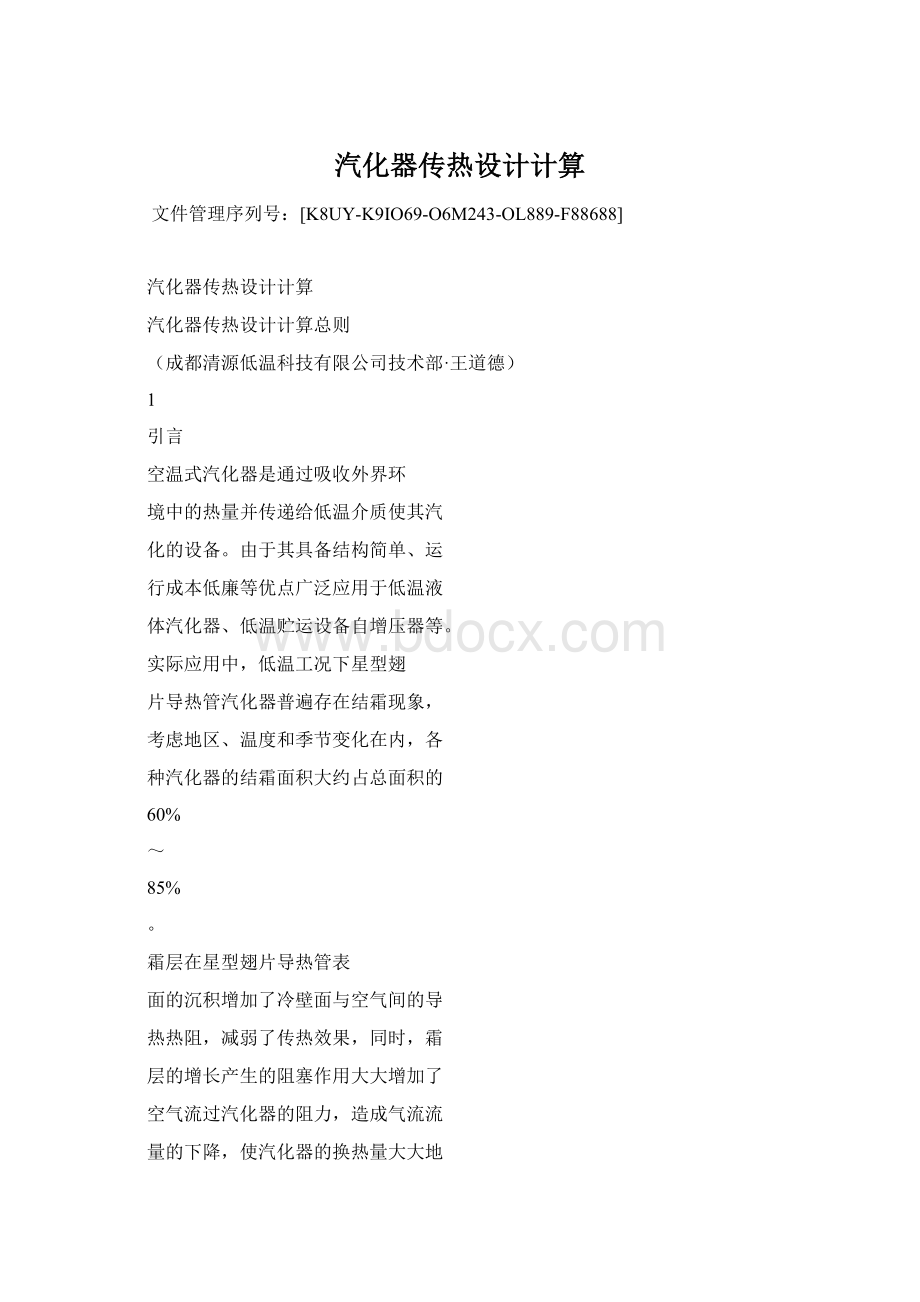
汽化器传热设计计算
文件管理序列号:
[K8UY-K9IO69-O6M243-OL889-F88688]
汽化器传热设计计算
汽化器传热设计计算总则
(成都清源低温科技有限公司技术部·王道德)
1
引言
空温式汽化器是通过吸收外界环
境中的热量并传递给低温介质使其汽
化的设备。
由于其具备结构简单、运
行成本低廉等优点广泛应用于低温液
体汽化器、低温贮运设备自增压器等。
实际应用中,低温工况下星型翅
片导热管汽化器普遍存在结霜现象,
考虑地区、温度和季节变化在内,各
种汽化器的结霜面积大约占总面积的
60%
~
85%
。
霜层在星型翅片导热管表
面的沉积增加了冷壁面与空气间的导
热热阻,减弱了传热效果,同时,霜
层的增长产生的阻塞作用大大增加了
空气流过汽化器的阻力,造成气流流
量的下降,使汽化器的换热量大大地
减少。
以往的空温式汽化器都是依据
现有的相关经验来进行设计制造的,
并且忽略了星型翅片导热管在结霜工
况下对传热性能的影响,实际应用偏
差较大,有些汽化量不足,影响生产,
过大则造成不必要的浪费。
因此如何
合理设计空温式汽化器,方便工程应
用是当前急需解决的问题。
国内文献
对此进行过不少的理论分析与实验研
究,目前仍未得出一个比较实用且相
对精确的关联式。
本文探讨这些问题
在于为空温式汽化器的设计计算提供
参考依据。
图
1
空温式汽化器结构示意图
2
传热量的计算
由热力学相关知识可知,汽化器
管内工作介质的压力在临界压力以
上,温度低于临界温度时为液体,高
于临界温度时为气体;在临界压力和
临界温度以下时,有一相变的气
—
液
两相区,温度高于压力对应的饱和温
度时为气体,低于饱和温度时为过冷
液体。
如果压力高于临界压力,它的
换热特点是分为预热段(临界温度以
下)和蒸发段(临界温度以上)两个
区段,没有两相共存的汽化阶段。
因
此,介质的压力和温度决定汽化器的
设计方案,不同的流态传热特性有很
大差别,需分别考虑、计算。
本文选定的空温式汽化器为
LNG
高压汽化器,
LNG
进口温度为
-162
℃,
工作压力为
25MPa
。
所以,
LNG
在星
型翅片导热管内吸热经液相、气相两
种相变过程,不考虑气液两相区汽化
阶段。
图
2
星型翅片导热管结构示意图
按照热力学第一定律,汽化器的
汽化过程中吸收的总热量,有如下关
系式:
n
Q
Q
h
h
m
Q
g
l
in
out
(1)
Q
为星型翅片导热管在单位时间内的
传热量——
KJ/s
m
为单位时间内汽化液体质量——
Kg
h
out
为汽化器出口气体焓值——
KJ/kg
h
in
为汽化器进口液体焓值——
KJ/kg
Q
l
为单排星型翅片导热管液相区单位
时间内的传热量——
KJ/s
Q
g
为单排星型翅片导热管气相区单位
时间内的传热量——
KJ/s
n
为星型翅片导热管的排数
3
传热系数的确定
空温式汽化器管内流动着低温液
体,液体吸热产生相变。
同时星型翅
片导热管表面温度低于周围环境空气
的露点温度,星型翅片导热管表面结
霜,不同相区霜层厚度不同,导热热
阻也不同。
汽化器从开启到正常运行
传热与热阻要经历非稳态和稳态两个
阶段:
在非稳态阶段霜开始形成时表
面粗糙度增大,引起传热面积增大,
同时气体流速也增大,稳态工作时,
汽化器表面的霜层厚度要比非稳态时
的大,而且随着霜层厚度的增大翅片
间的空气流道不断减小,增大了空气
流通阻力进而增大传热热阻。
因此,
汽化器工作时相同的产气量在稳态传
热时需要的传热面积要大,作为计算
的上限值,而非稳态不考虑结霜的传
热面积作为计算的下限值。
低温工质的传热过程十分复杂,
本文对计算过程进行了适当的简化。
(1)
沿管程分为两段:
单相液体对
流换热区、单相气体对流换热区;
(2)
各相区采用均相模型;
(3)
传热管壁仅考虑径向导热
。
总传热系数按照下式确定:
0
4
4
2
2
1
1
1
1
1
1
f
R
K
(2)
其中,总传热系数中构成值
由下
式推导而得出:
3
3
0
3
3
3
0
2
)
1
(
2
)
tanh(
b
m
mh
mh
R
f
为污垢热阻——
m
2
·
K/W
1
为星型翅片导热管壁厚——
m
1
为星型翅片导热管导热系数——
W/(m·
K)
2
为霜层厚度——
m
2
为霜的导热系数——
W/(m·
K)
3
为翅片厚度——
m
3
为翅片导热系数——
W/(m·
K)
3
为不锈钢内衬厚度——
m
4
为不锈钢导热系数——
W/(m·
K)
为翅片的总效率
0
为空气对流换热系数——
W/(m
2
·
K)
1
为管内流体对流换热系数——
W/(m
2
·
K)
b
为翅片宽度——
m
h
为翅片高度——
m
β
为肋化系数
因为铝和不锈钢的导热系数远大
于管外空气自然对流换热系数,因此,
在
实
际
设
计
过
程
中
将
(2)
式
中
的
4
4
1
1
和
项略去,最后得到如下公式:
0
2
2
1
1
1
1
f
R
K
(3)
3.1
空气侧对流换热系数
0
的确定
由于结霜后翅片表面粗
糙度增
加,一般的,空气与霜层之间的换热
系数α
0
=(1.2
~
1.3)
α
w
,α
w
为汽化
器未结霜时的外表面换热系数。
空温
式汽化器都采用星型星型翅片导热
管,对于星型星型翅片导热管可按空
气对平壁的自然对流换热准则方程式
来求解α
w
。
层流
(Ra=Gr·
Pr=2×
10
4
~
8×
10
9
)
:
4
/
1
Pr)
(
54
.
0
Gr
Nu
(4)
紊流
(Ra=Gr·
Pr=8×
10
9
~
8×
10
11
)
:
3
/
1
Pr)
(
54
.
0
Gr
Nu
(5)
其中格拉晓夫准数
Gr
由下式确
定:
2
3
Tl
g
Gr
(6)
Ra
为瑞利数
Pr
为普朗特数
Nu
为努谢尔特数
β为体胀系数——
1/K
g
为重力加速度——
m/s
2
下载文档到电脑,查找使用更方便
1下载券8人已下载
还剩2页未读,继续阅读
定制HR最喜欢的简历
l
为星型翅片导热管长度——
m
Δ
T
为流体和管壁间温度差——
K
为空气的导热系数—
W/(m·
K)
由式
(7)
求得星型翅片导热管未结
霜时外表面对流换热系数:
l
Nu
w
(7)
3.2
霜层导热系数λ
2
的计算
研究表明霜层导热系数主要取决
于密度,但也取决于霜层的微观结构,
它是霜层结构、霜层内温度梯度引起
水蒸气扩散及凝华潜热释放和霜表面
粗糙度引起涡流效应相互作用的结
果。
目前应用最广泛的是:
Yonko
和
SepSy
提出的导热系数关联式:
λ
2
=0.02422+7.214×
10
-4
ρ
fr
+1.1797×
10
-6
ρ
fr
2
(8)
ρ
fr
为霜的密度——
Kg/m
3
,
霜的密
度
ρ
fr
主要与霜层表面温度
T
fr
和风速
u
fr
有关。
霜层密度由下式确定:
r
u
r
T
f
f
fr
25
340
455
.
0
(9)
空温式汽化器在工作过程中都会
结霜,前几排管子的结霜一般较严重,
而后几排管子的结霜相对较轻。
在相
同的换热面积的情况下,星型翅片导
热管间距越大、管排数越少、表面结
霜速度就越慢,但是管排数减少会影
响汽化器的紧凑性。
因此,空温式汽
化器要充分考虑其结构的合理性,在
对汽化器的体积要求不是很严格的情
况下,可以适当增大星型翅片导热管
间距、减少管排数来减少结霜。
3.3
管内流体对流换热系数
α
1
计算
由流体的物性参数求得雷诺数
D
Re
,判断流体是层流还是湍
流,然后根据流态计算流动摩擦系数。
因为,管内流体采用分区计算的方法,
所以计算参数也应按相应流态选取;
摩擦系数
f
决定于壁表面的粗糙度
Ks
和
Re
。
层流时:
认为粗糙度对于换热的
影响可忽略,摩擦系数仅与雷诺数有
关,由下式确定:
Re
64
f
(10)
湍流时:
由相关表中查得粗糙度
后,由式
(11)
或简化式
(12)
、
(13
)
计算
湍流摩擦系数,对于已有的实际设备,
可以用实验的方法测出流体进出口的
压力降,根据压力降和磨擦系数之间
的关系式
(14)
求出湍流摩擦系数。
对流
换热系数的关联式如式
(16)
所示。
2
74
.
1
Re
lg
2
Ks
f
(11)
25
.
0
Re
316
.
0
5000
Re
3000
f
,
(12)
2
.
0
Re
184
.
0
5000
Re
f
,
(13)
2
2
m
u
D
l
f
p
(14)
8
Pr
3
/
2
f
St
(15)
p
m
c
u
St
1
(16)
D
为管段的直径——
m
ρ
为密度——
kg/m
3
v
为体积流速——
m
3
/s
μ
为动力黏度——
pa·
s
c
p
为比定压热容——
KJ/(kg·
K)
u
m
为流体的截面平均流度——
m/s
St
为斯坦顿数
Pr
为普朗特数
4
传热面积计算
Q=(K
l
A
1
ΔT
1
+K
g
A
g
ΔT
g
)n=[(h
c
-h
in
)+(h
out
-h
c
)]m
(17)
K
l
、
K
g
分别表示液相区和气相区的换
热系数
——
W/(m
2
·
K)
A
l
、
A
g
分别表示液相区和气相区的换
热面积——
m
2
hc
为
LNG
在临界点处的焓——
KJ/kg
由式
(17)
可以求得总的传热面积。
由于采用分区计算,
ΔT
分别取进出口
温度与临界温度的差值。
5
结束语
(1)
对于汽化压力高于介质临界压力的
星型翅片导热管汽化器,可分为
2
个
传热区进行计算,即单相液体对流换
热区和单相气体对流换热区。
这样不
仅使模型更接近实际情况,使设计更
加合理准确,也便于工程计算。
(2)
对于汽化压力低于介质的临界压力
的星型翅片导热管汽化器也可以采用
分区计算的方法,将其分为单相液体
对流换热区、气液两相对流换热区和
单相气体对流换热区
3
个传热区进行
计算
.
(3)
低温工况下星型翅片导热管汽化器
表面容易发生结霜现象,为了提高星
型翅片导热管汽化器的换热效率,可
以对汽化器定期除霜,或采用多组汽
化器切换使用的方法来减少结霜对星
型翅片导热管汽化器正常运行的影
响。
阅读已结束,如果下载本文需要使用