PVD工艺.docx
《PVD工艺.docx》由会员分享,可在线阅读,更多相关《PVD工艺.docx(19页珍藏版)》请在冰豆网上搜索。
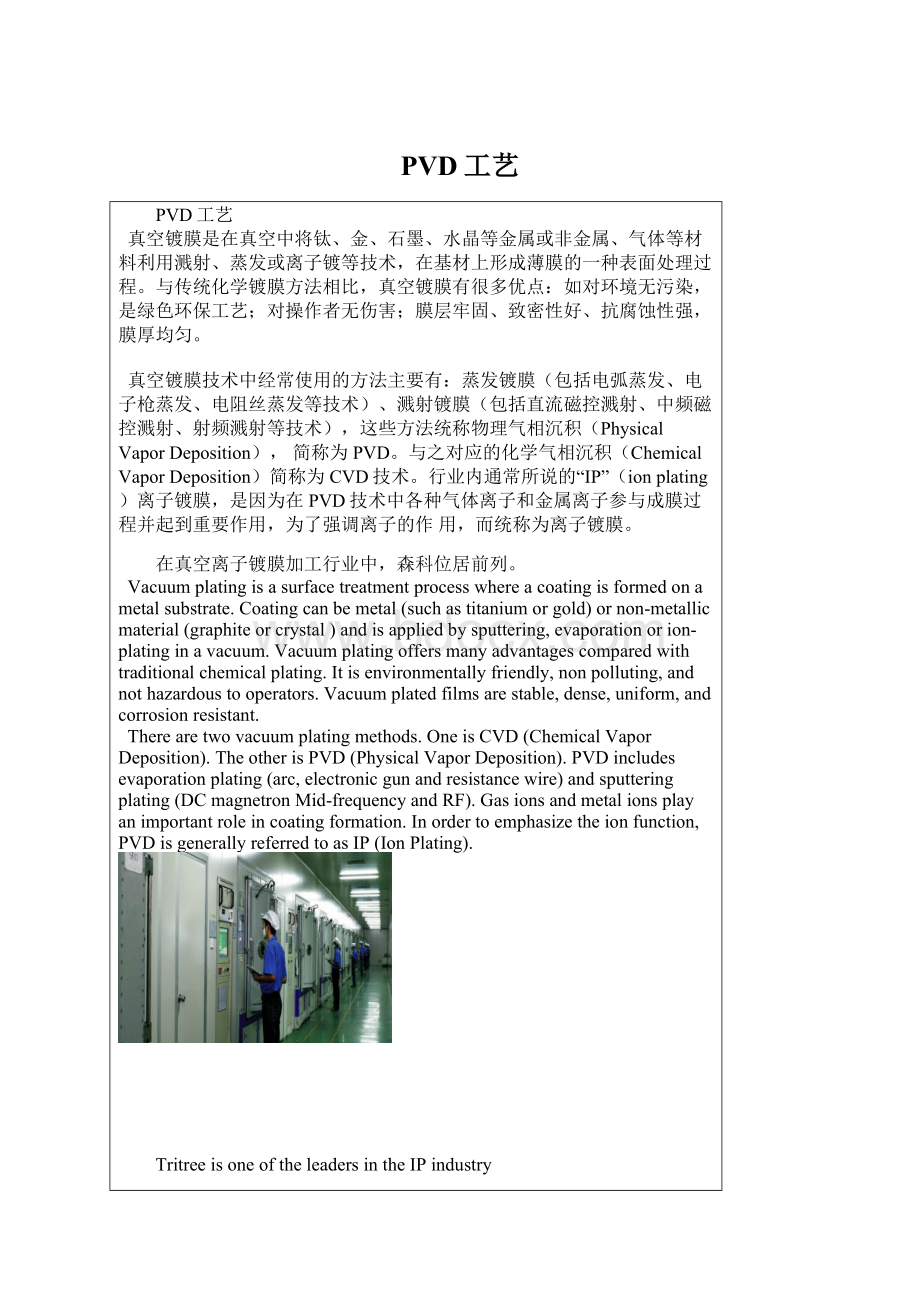
PVD工艺
PVD工艺
真空镀膜是在真空中将钛、金、石墨、水晶等金属或非金属、气体等材料利用溅射、蒸发或离子镀等技术,在基材上形成薄膜的一种表面处理过程。
与传统化学镀膜方法相比,真空镀膜有很多优点:
如对环境无污染,是绿色环保工艺;对操作者无伤害;膜层牢固、致密性好、抗腐蚀性强,膜厚均匀。
真空镀膜技术中经常使用的方法主要有:
蒸发镀膜(包括电弧蒸发、电子枪蒸发、电阻丝蒸发等技术)、溅射镀膜(包括直流磁控溅射、中频磁控溅射、射频溅射等技术),这些方法统称物理气相沉积(PhysicalVaporDeposition),简称为PVD。
与之对应的化学气相沉积(ChemicalVaporDeposition)简称为CVD技术。
行业内通常所说的“IP”(ionplating)离子镀膜,是因为在PVD技术中各种气体离子和金属离子参与成膜过程并起到重要作用,为了强调离子的作用,而统称为离子镀膜。
在真空离子镀膜加工行业中,森科位居前列。
Vacuumplatingisasurfacetreatmentprocesswhereacoatingisformedonametalsubstrate.Coatingcanbemetal(suchastitaniumorgold)ornon-metallicmaterial(graphiteorcrystal)andisappliedbysputtering,evaporationorion-platinginavacuum.Vacuumplatingoffersmanyadvantagescomparedwithtraditionalchemicalplating.Itisenvironmentallyfriendly,nonpolluting,andnothazardoustooperators.Vacuumplatedfilmsarestable,dense,uniform,andcorrosionresistant.
Therearetwovacuumplatingmethods.OneisCVD(ChemicalVaporDeposition).TheotherisPVD(PhysicalVaporDeposition).PVDincludesevaporationplating(arc,electronicgunandresistancewire)andsputteringplating(DCmagnetronMid-frequencyandRF).Gasionsandmetalionsplayanimportantroleincoatingformation.Inordertoemphasizetheionfunction,PVDisgenerallyreferredtoasIP(IonPlating).
TritreeisoneoftheleadersintheIPindustry
PVD加工工艺流程
一、前处理工艺:
1.来料抽检2.电镀件过碱去油,清水清洗.4.过酸表面洁化,清水清洗5.丙酮+滑石粉清洗6.擦洗
二、上挂
三、PVD处理工艺:
1.烘烤:
80摄食度2.镀膜:
真空抽到4.5-2帕保持真空度2.8-1帕成膜
四、出炉
五、下挂
六、全检
PVD简介1.PVD的含义—PVD是英文PhysicalVaporDeposition的缩写,中文意思是“物理气相沉积”,是指在真空条件下,用物理的方法使材料沉积在被镀工件上的薄膜制备技术。
2.PVD镀膜和PVD镀膜机—PVD(物理气相沉积)镀膜技术主要分为三类,真空蒸发镀膜、真空溅射镀和真空离子镀膜。
对应于PVD技术的三个分类,相应的真空镀膜设备也就有真空蒸发镀膜机、真空溅射镀膜机和真空离子镀膜机这三种。
近十多年来,真空离子镀膜技术的发展是最快的,它已经成为当今最先进的表面处理方式之一。
我们通常所说的PVD镀膜,指的就是真空离子镀膜;通常所说的PVD镀膜机,指的也就是真空离子镀膜机。
3.PVD镀膜技术的原理—PVD镀膜(离子镀膜)技术,其具体原理是在真空条件下,采用低电压、大电流的电弧放电技术,利用气体放电使靶材蒸发并使被蒸发物质与气体都发生电离,利用电场的加速作用,使被蒸发物质及其反应产物沉积在工件上。
4.PVD镀膜膜层的特点—采用PVD镀膜技术镀出的膜层,具有高硬度、高耐磨性(低摩擦系数)、很好的耐腐蚀性和化学稳定性等特点,膜层的寿命更长;同时膜层能够大幅度提高工件的外观装饰性能。
5.PVD镀膜能够镀出的膜层种类—PVD镀膜技术是一种能够真正获得微米级镀层且无污染的环保型表面处理方法,它能够制备各种单一金属膜(如铝、钛、锆、铬等),氮化物膜(TiN、ZrN、CrN、TiAlN)和碳化物膜(TiC、TiCN),以及氧化物膜(如TiO等)。
6.PVD镀膜膜层的厚度—PVD镀膜膜层的厚度为微米级,厚度较薄,一般为0.3µm~5µm,其中装饰镀膜膜层的厚度一般为0.3µm~1µm,因此可以在几乎不影响工件原来尺寸的情况下提高工件表面的各种物理性能和化学性能,镀后不须再加工。
7.PVD镀膜能够镀出的膜层的颜色种类—PVD镀膜目前能够做出的膜层的颜色有深金黄色,浅金黄色,咖啡色,古铜色,灰色,黑色,灰黑色,七彩色等。
通过控制镀膜过程中的相关参数,可以控制镀出的颜色;镀膜结束后可以用相关的仪器对颜色进行测量,使颜色得以量化,以确定镀出的颜色是否满足要求。
8.PVD镀膜与传统化学电镀(水电镀)的异同—PVD镀膜与传统的化学电镀的相同点是,两者都属于表面处理的范畴,都是通过一定的方式使一种材料覆盖在另一种材料的表面。
两者的不同点是:
PVD镀膜膜层与工件表面的结合力更大,膜层的硬度更高,耐磨性和耐腐蚀性更好,膜层的性能也更稳定;PVD镀膜不会产生有毒或有污染的物质。
9.PVD镀膜技术目前主要应用的行业—PVD镀膜技术的应用主要分为两大类:
装饰镀膜和工具镀膜。
装饰镀的目的主要是为了改善工件的外观装饰性能和色泽同时使工件更耐磨耐腐蚀延长其使用寿命;这方面主要应用五金行业的各个领域,如门窗五金、锁具、卫浴五金等行业。
工具镀的目的主要是为了提高工件的表面硬度和耐磨性,降低表面的摩擦系数,提高工件的使用寿命;这方面主要应用在各种刀剪、车削刀具(如车刀、刨刀、铣刀、钻头等等)、各种五金工具(如螺丝刀、钳子等)、各种模具等产品中。
10.PVD镀膜(离子镀膜)技术的主要特点和优势—和真空蒸发镀膜真空溅射镀膜相比较,PVD离子镀膜具有如下优点:
1.膜层与工件表面的结合力强,更加持久和耐磨2.离子的绕射性能好,能够镀形状复杂的工件3.膜层沉积速率快,生产效率高4.可镀膜层种类广泛5.膜层性能稳定、安全性高(获得FDA认证,可植入人体)
PVD清洗剂PVD是指在真空条件下,采用低电压、大电流的电弧放电技术,利用气体放电使靶材蒸发并使被蒸发物质与气体都发生电离,利用电场的加速作用,使被蒸发物质及其反应产物沉积在工件上。
PVD技术出现于二十世纪七十年代末,制备的薄膜具有高硬度、低摩擦系数、很好的耐磨性和化学稳定性等优点。
PVD工艺对环境无不利影响,符合现代绿色制造的发展方向。
目前PVD涂层技术已普遍应用于硬质合金立铣刀、钻头、阶梯钻、油孔钻、铰刀、丝锥、可转位铣刀片、异形刀具、焊接刀具等的涂层处理。
PVD在广度上的普及应用及深度上的持续发展要求其设备、工艺及清洗剂等专用物料具有高稳定性、适应性和可靠性。
作为环保型工业清洗剂的专家和引领者,山之风致力于为PVD提供全方位多品种的系列清洗剂,产品涵盖PVD全过程
推荐PVD清洗剂:
WIN-91WIN-92、WIN-136;
WIN-91:
本品是一种多功能高效水基清洗剂,含有多种表面活性剂、助剂,缓蚀剂。
清洗能力强,配合超声波使用只需稀释5%~7%使用即可,本品主要用于清洗不锈钢工件上冲压油、切削油及抛光蜡的清洗,特别用于PVD前工件的精密清洗。
WIN-92:
本品是一种多功能高效水基清洗剂,含有多种表面活性剂、碱性助剂,渗透剂,除油能力强。
可清洗各类机器及配零件上的油污、抛光蜡、指印,特别适用于PVD前工件的精洗。
WIN-93:
本品是采用金属表面处理技术中最新配方,根据用户需要而推出的,具有良好的中和金属表面的碱性残留物、溶解油脂的能力,且使用方便安全,对大部份金属材料和饰面都没有影响,是PVD前优良清洗中和剂,主要用于PVD前工件精洗中的碱性中和,使漂洗更容易,工件表面更洁净
PVDPVD(PhysicalVaporDeposition),指利用物理过程实现物质转移,将原子或分子由源转移到基材表面上的过程。
它的作用是可以是某些有特殊性能(强度高、耐磨性、散热性、耐腐性等)的微粒喷涂在性能较低的母体上,使得母体具有更好的性能!
PVD基本方法:
真空蒸发、溅射1.PVD简介PVD是英文PhysicalVaporDeposition(物理气相沉积)的缩写,是指在真空条件下,采用低电压、大电流的电弧放电技术,利用气体放电使靶材蒸发并使被蒸发物质与气体都发生电离,利用电场的加速作用,使被蒸发物质及其反应产物沉积在工件上。
2.PVD技术的发展PVD技术出现于二十世纪七十年代末,制备的薄膜具有高硬度、低摩擦系数、很好的耐磨性和化学稳定性等优点。
最初在高速钢刀具领域的成功应用引起了世界各国制造业的高度重视,人们在开发高性能、高可靠性涂层设备的同时,也在硬质合金、陶瓷类刀具中进行了更加深入的涂层应用研究。
与CVD工艺相比,PVD工艺处理温度低,在600℃以下时对刀具材料的抗弯强度无影响;薄膜内部应力状态为压应力,更适于对硬质合金精密复杂刀具的涂层;PVD工艺对环境无不利影响,符合现代绿色制造的发展方向。
目前PVD涂层技术已普遍应用于硬质合金立铣刀、钻头、阶梯钻、油孔钻、铰刀、丝锥、可转位铣刀片、异形刀具、焊接刀具等的涂层处理。
PVD技术不仅提高了薄膜与刀具基体材料的结合强度,涂层成分也由第一代的TiN发展为TiC、TiCN、ZrN、CrN、MoS2、TiAlN、TiAlCN、TiN-AlN、CNx、DLC和ta-C等多元复合涂层。
3.涂层的PVD技术增强型磁控阴极弧:
阴极弧技术是在真空条件下,通过低电压和高电流将靶材离化成离子状态,从而完成薄膜材料的沉积。
增强型磁控阴极弧利用电磁场的共同作用,将靶材表面的电弧加以有效地控制,使材料的离化率更高,薄膜性能更加优异。
过滤阴极弧:
过滤阴极电弧(FCA)配有高效的电磁过滤系统,可将离子源产生的等离子体中的宏观粒子、离子团过滤干净,经过磁过滤后沉积粒子的离化率为100%,并且可以过滤掉大颗粒,因此制备的薄膜非常致密和平整光滑,具有抗腐蚀性能好,与机体的结合力很强。
磁控溅射:
在真空环境下,通过电压和磁场的共同作用,以被离化的惰性气体离子对靶材进行轰击,致使靶材以离子、原子或分子的形式被弹出并沉积在基件上形成薄膜。
根据使用的电离电源的不同,导体和非导体材料均可作为靶材被溅射。
离子束DLC:
碳氢气体在离子源中被离化成等离子体,在电磁场的共同作用下,离子源释放出碳离子。
离子束能量通过调整加在等离子体上的电压来控制。
碳氢离子束被引到基片上,沉积速度与离子电流密度成正比。
星弧涂层的离子束源采用高电压,因而离子能量更大,使得薄膜与基片结合力很好;离子电流更大,使得DLC膜的沉积速度更快。
离子束技术的主要优点在于可沉积超薄及多层结构,工艺控制精度可达几个埃,并可将工艺过程中的颗料污染所带来的缺陷降至最小。
4,补充物理气向沉积技术*PVD介绍物理气相沉积具有金属汽化的特点,与不同的气体发应形成一种薄膜涂层。
今天所使用的大多数PVD方法是电弧和溅射沉积涂层。
这两种过程需要在高度真空条件下进行。
Ionbond阴极电弧PVD涂层技术在20世纪70年代后期由前苏联发明,如今,绝大多数的刀模具涂层使用电弧沉积技术。
工艺温度典型的PVD涂层加工温度在250℃—450℃之间,但在有些情况下依据应用领域和涂层的质量,PVD涂层温度可低于70℃或高于600℃进行涂层。
涂层适用的典型零件PVD适合对绝大多数刀具模具和部件进行沉积涂层,应用领域包括刀具和成型模具,耐磨部件,医疗装置和装饰产品。
材料包括钢质,硬质合金和经电镀的塑料。
典型涂层类型涂层类型有TiN,ALTIN,TiALN,CrN,CrCN,TiCN和ZrN,复合涂层包括TiALYN或W—C:
H/DLC涂层厚度一般2~5um,但在有些情况下,涂层薄至0.5um,厚至15um装载容量。
涂层种类和厚度决定工艺时间,一般工艺时间为3~6小时。
加工过程优点适合多种材质,涂层多样化减少工艺时间,提高生产率较低的涂层温度,零件尺寸变形小对工艺环境无污染图示:
电镀diàndù(Electroplating)电镀的概述:
利用电解作用使金属或其它材料制件的表面附着一层金属膜的工艺。
可以起到防止腐蚀,提高耐磨性、导电性、反光性及增进美观等作用
电镀的主要用途是什么?
1、提高金属制品或者零件的耐蚀性能。
例如钢铁制品或者零件表面镀锌。
2、提高金属制品的防护-装饰性能。
例如钢铁制品表面镀铜、镀镍镀铬等。
3、修复金属零件尺寸。
例如轴、齿轮等重要机械零件使用后磨损,可采用镀铁、镀铬等祸福其尺寸。
4、电镀还可赋予某种制品或零件某种特殊的功能。
例如镀硬铬可提高其耐磨性能等。
电镀的概念
就是利用电解原理在某些金属表面上镀上一薄层其它金属或合金的过程。
电镀时,镀层金属做阳极,被氧化成阳离子进入电镀液;待镀的金属制品做阴极,镀层金属的阳离子在金属表面被还原形成镀层。
为排除其它阳离子的干扰,且使镀层均匀、牢固,需用含镀层金属阳离子的溶液做电镀液,以保持镀层金属阳离子的浓度不变。
电镀的目的是在基材上镀上金属镀层,改变基材表面性质或尺寸.电镀能增强金属的抗腐蚀性(镀层金属多采用耐腐蚀的金属)、增加硬度、防止磨耗、提高导电性、润滑性、耐热性、和表面美观。
电镀作用
利用电解作用在机械制品上沉积出附着良好的、但性能和基体材料不同的金属覆层的技术。
电镀层比热浸层均匀,一般都较薄,从几个微米到几十微米不等。
通过电镀,可以在机械制品上获得装饰保护性和各种功能性的表面层,还可以修复磨损和加工失误的工件。
镀层大多是单一金属或合金,如钛靶、锌、镉、金或黄铜、青铜等;也有弥散层,如镍-碳化硅、镍-氟化石墨等;还有覆合层,如钢上的铜-镍-铬层、钢上的银-铟层等。
电镀的基体材料除铁基的铸铁、钢和不锈钢外,还有非铁金属,如ABS塑料、聚丙烯、聚砜和酚醛塑料,但塑料电镀前,必须经过特殊的活化和敏化处理必须经过特殊的活化和敏化处理必须
电镀原理
在盛有电镀液的镀槽中,经过清理和特殊预处理的待镀件作为阴极,用镀覆金属制成阳极,两极分别与直流电源的负极和正极联接。
电镀液由含有镀覆金属的化合物、导电的盐类、缓冲剂、pH调节剂和添加剂等的水溶液组成。
通电后,电镀液中的金属离子,在电位差的作用下移动到阴极上形成镀层。
阳极的金属形成金属离子进入电镀液,以保持被镀覆的金属离子的浓度[1]。
在有些情况下,如镀铬,是采用铅、铅锑合金制成的不溶性阳极,它只起传递电子、导通电流的作用。
电解液中的铬离子浓度,需依靠定期地向镀液中加入铬化合物来维持。
电镀时,阳极材料的质量、电镀液的成分、温度、电流密度、通电时间、搅拌强度、析出的杂质、电源波形等都会影响镀层的质量,需要适时进行控制
电镀方式
电镀分为挂镀、滚镀、连续镀和刷镀等方式,主要与待镀件的尺寸和批量有关。
挂镀适用于一般尺寸的制品,如汽车的保险杠,自行车的车把等。
滚镀适用于小件,如紧固件、垫圈、销子等。
连续镀适用于成批生产的线材和带材。
刷镀适用于局部镀或修复。
电镀液有酸性的、碱性的和加有铬合剂的酸性及中性溶液,无论采用何种镀覆方式,与待镀制品和镀液接触的镀槽、吊挂具等应具有一定程度的通用性。
镀层分类
镀层分为装饰保护性镀层和功能性镀层两类。
装饰保护性镀层装饰保护性镀层装饰保护性镀层装饰保护性镀层主要是在铁金属、非铁金属及塑料上的镀铬层,特别是钢的铜-镍-铬层,锌及钢上的镍-铬层。
为了节约镍,人们已能在钢上镀铜-镍/铁-高硫镍-镍/铁-低固分镍-铬层。
与镀铬层相似的锡/镍镀层,可用于分析天平、化学泵、阀和流量测量仪表上。
功能性镀层这种镀层种类很多,如:
①提高与轴颈的相容性和嵌入性的滑动轴承罩镀层,铅-锡,铅-铜-锡,铅-铟等复合镀层;②用于耐磨的中、高速柴油机活塞环上的硬铬镀层,这种镀层也可用在塑料模具上,具有不粘模具和使用寿命长的特点;③在大型人字齿轮的滑动面上镀铜,可防止滑动面早期拉毛;④用于防止钢铁基体遭受大气腐蚀的镀锌;⑤防止渗氮的铜锡镀层;⑥用于收音机、电视机制造中钎焊并防止钢与铝间的原电池腐蚀的锡-锌镀层。
适用于修复和制造的工程镀层,有铬、银、铜等,它们的厚度都比较大,硬铬层可以厚达300微米。
常用表面处理工艺流程常用表面处理工艺流程常用表面处理工艺流程常用表面处理工艺流程
(1)钢铁件电镀锌工艺流程┌酸性镀锌除油→除锈→│→纯化→干燥└碱性镀锌
(2)钢铁件常温发黑工艺流程┌浸脱水防锈油││烘干除油→除锈→常温发黑→│浸肥皂液——→浸锭子油或机油││└浸封闭剂(3)钢铁件磷化工艺流程除油→除锈→表调→磷化→涂装(4)ABS/PC塑料电镀工艺流程除油→亲水→预粗化(PC≥50%)→粗化→中和→整面→活化→解胶→化学沉镍→镀焦铜→镀酸铜→镀半亮镍→镀高硫镍→镀亮镍→镀封→镀铬(5)PCB电镀工艺流程除油→粗化→预浸→活化→解胶→化学沉铜→镀铜→酸性除油→微蚀→镀低应力镍→镀亮镍→镀金→干燥(6)钢铁件多层电镀工艺流程除油→除锈→镀氰化铜→镀酸铜→镀半亮镍→镀高硫镍→镀亮镍→镍封→镀铬(7)钢铁件前处理(打磨件、非打磨件)工艺流程1、打磨件→除蜡→热浸除油→电解除油→酸蚀→非它电镀2、非打磨件→热浸除油→电解除油→酸蚀→其它电镀(8)锌合金件镀前处理工艺流程除蜡→热浸除油→电解除油→酸蚀→镀碱铜→镀酸铜或焦磷酸铜→其它电镀(9)铝及其合金镀前处理工艺流程除蜡→热浸除油→电解除油→酸蚀除垢→化学沉锌→浸酸→二次沉新→镀碱铜或镍→其它电镀除蜡→热浸除油→电解除油→酸蚀除垢→铝铬化→干燥→喷沫或喷粉→烘干或粗化→成品除蜡→热浸除油→电解除油→酸蚀除垢→阳极氧化→染色→封闭→干燥→成品(10)铁件镀铬工艺流程:
除蜡→热浸除油→阴极→阳极→电解除油→弱酸浸蚀→预镀碱铜→酸性光亮铜(选择)→光亮镍→镀铬或其它除蜡→热浸除油→阴极→阳极→电解除油→弱酸浸蚀→半光亮镍→高硫镍→光亮镍→镍封(选择)→镀铬(11)锌合金镀铬工艺流程除蜡→热浸除油→阴极电解除油→浸酸→碱性光亮铜→焦磷酸铜(选择性)→酸性光亮铜(选择性)→光亮镍→镀铬(12)电叻架及染色工艺流程前处理或电镀→纯水洗(2-3次)→预浸→电叻架→回收→纯水洗(2-3次)→烘干→成品不锈钢镀光亮镍工艺流程:
有机溶剂除油→化学除油→水洗→阴极电解活化→闪镀镍→水洗→活化→水洗→镀光亮镍→水洗→钝化→水洗→水洗→热水洗→甩干→烘干→验收。
不锈钢上的光亮镍层是微带黄光的银白色金属,它的硬度比铜、锌、锡、镉、金、银等要高,但低于铬和铑金属。
光亮镍在空气中具有很高的化学稳定性,对碱有较好的稳定性。
不锈钢上通过运用光亮剂,可不经抛光直接镀取光亮镍,以提高表面的硬度、耐磨性和整平性,在外观上使不锈钢与其他镀镍件外观一致,并且避免不锈钢与其他光亮镍之间产生接触电位差的腐蚀。
不锈钢镀光亮镍的溶液中光亮剂的近年来发展很快,品种很多。
归纳起来,光亮剂的发展经历了四个年代。
第一代的也是最原始的产品为糖精加丁炔二醇。
可以镀取整平性很高的光亮镍。
其运用兴盛于20世纪六七十年代。
但由于丁炔二醇在镀镍槽中的不稳定性,寿命较短,有机杂质积累很快,需要经常处理镍槽,于是,通过环氧氯丙烷或环氧丙烷与丁炔二醇结枝,合成了第二代镀镍光亮剂,如BE、791光亮剂,情况有所好转,BE和791保留有炔基,后来又进步将吡啶基聚合上去,形成了第三代产品,出光速度更快,光亮剂用量更少了,使用寿命更长了。
现在又进一步运用镀镍光亮剂中间体多种组合构成新型光亮剂已发展到第四代产品了。
它的使用量更少,出光速度更快,处理周期更长,深镀能力更强了。
不锈钢镀光亮镍工艺流程:
有机溶剂除油→化学除油(氧氧化钠40g/L,碳酸钠30g/L,磷酸三钠50g/L,OP-乳化剂3mL/L,温度80~90℃,时间30min)→水洗→阴极电解活化(盐酸水溶液1+1,室温,Dk1~3A/dm2,时间5min,阳极布包碳精板)→闪镀镍(氯化镍180~220g/L,盐酸120g/L,室温,电流密度4A/dm2,时间5~lOmin,阳极镍板)→水洗→活化[硫酸5%(V),时间5s]→水洗→镀光亮镍(时间5~lOmin,或按厚度所需时间)→水洗→钝化(重铬酸钾1s0g/L,重铬酸钠150g/L,硫酸30~50mL/L,室温,时间20~25s)→水洗→水洗→热水洗→甩干→烘干→验收。
[编辑本段编辑本段编辑本段编辑本段]电镀的过程基本如下电镀的过程基本如下电镀的过程基本如下电镀的过程基本如下1把镀层金属接在阳极2把镀件接在阴极3阴阳极以镀上去的金属的正离子组成的电解质溶液相连4通以直流电的电源后,阳极的金属会进行氧化反应(失去电子),溶液中的正离子则在阴极被还原(得到电子)成原子并积聚在负极表层。
电镀后被电镀物件的美观性和电流大小有关系,电流越小,被电镀的物件便会越美观;反之则会出现一些不平整的形状。
电镀的主要用途包括防止金属氧化(如锈蚀)以及进行装饰。
不少硬币的外层亦为电镀。
电镀产生的污水(如失去效用的电解质)是水污染的重要来源。
电镀专业术语
3镀覆方法术语3.1化学钝化将制件放在含有氧化剂的溶液中处理,使表面形成一层很薄的钝态保护膜的过程。
3.2化学氧化通过化学处理使金属表面形成氧化膜的过程。
3.3电化学氧化在一定电解液中以金属制件为阳极,经电解,于制件表面形成一层具有防护性,装饰性或其它功能氧化膜的过程。
3.4电镀利用电解原理,使金属或合金沉积在制件表面,形成均匀、致密、结合力良好的金属层的过程。
3.5转化膜对金属进行化学或电化学处理所形成的含有该金属之化合物的表面膜层。
3.6钢铁发蓝(钢铁化学氧化)将钢铁制件在空气中加热或浸入氧化性的溶液中,使之于表面形成通常为蓝(黑)色的薄氧化膜的过程。
3.7冲击电流电流过程中通过的瞬时大电流。
3.8光亮电镀在适当条件下,从镀槽中直接得到具有光泽镀层的电镀。
3.9合金电镀在电流作用下,使两种或两种以上金属(也包括非金属元素)共沉积