1600mm板坯连铸机工艺技术操作规程.docx
《1600mm板坯连铸机工艺技术操作规程.docx》由会员分享,可在线阅读,更多相关《1600mm板坯连铸机工艺技术操作规程.docx(19页珍藏版)》请在冰豆网上搜索。
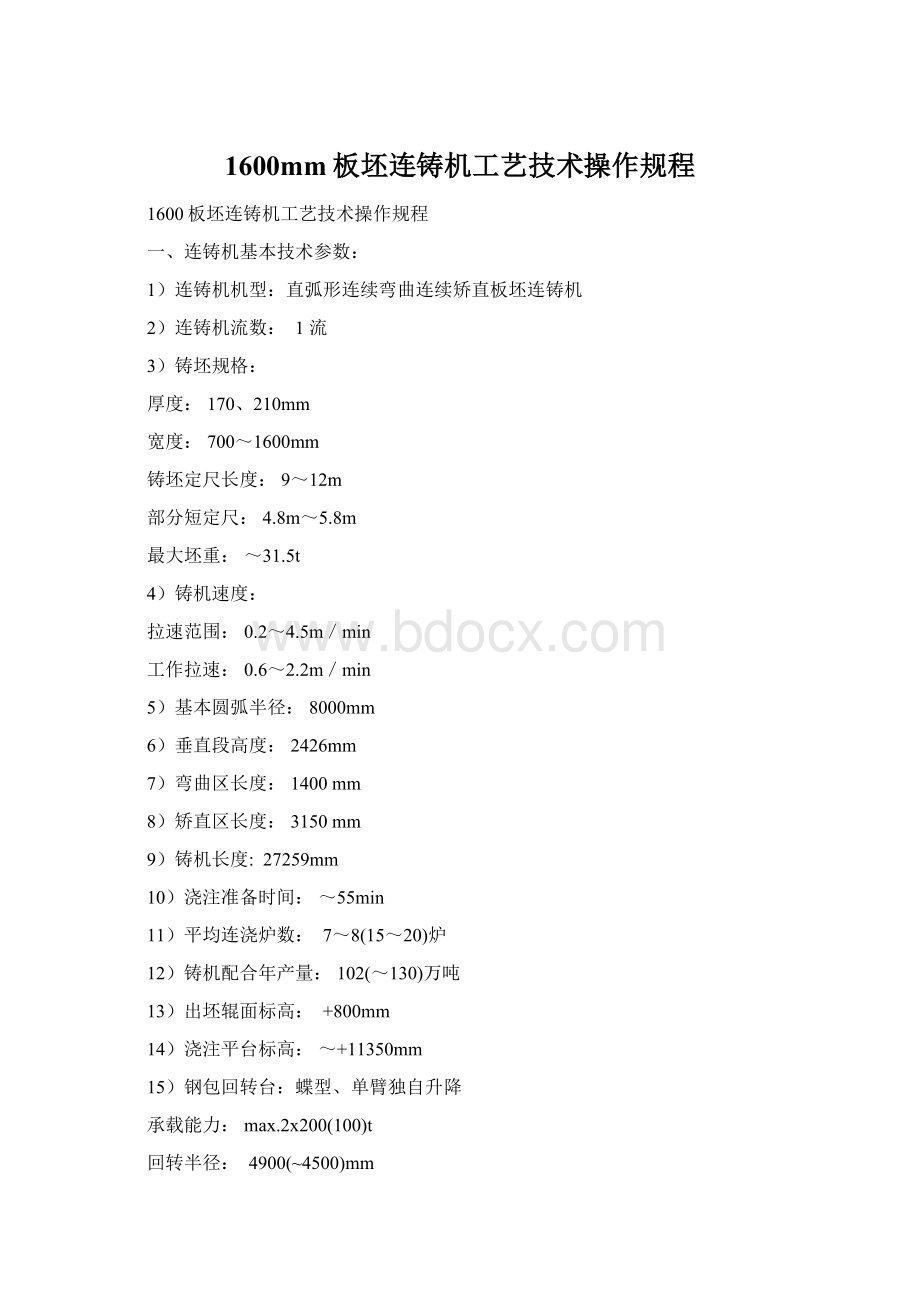
1600mm板坯连铸机工艺技术操作规程
1600板坯连铸机工艺技术操作规程
一、连铸机基本技术参数:
1)连铸机机型:
直弧形连续弯曲连续矫直板坯连铸机
2)连铸机流数:
1流
3)铸坯规格:
厚度:
170、210mm
宽度:
700~1600mm
铸坯定尺长度:
9~12m
部分短定尺:
4.8m~5.8m
最大坯重:
~31.5t
4)铸机速度:
拉速范围:
0.2~4.5m/min
工作拉速:
0.6~2.2m/min
5)基本圆弧半径:
8000mm
6)垂直段高度:
2426mm
7)弯曲区长度:
1400mm
8)矫直区长度:
3150mm
9)铸机长度:
27259mm
10)浇注准备时间:
~55min
11)平均连浇炉数:
7~8(15~20)炉
12)铸机配合年产量:
102(~130)万吨
13)出坯辊面标高:
+800mm
14)浇注平台标高:
~+11350mm
15)钢包回转台:
蝶型、单臂独自升降
承载能力:
max.2x200(100)t
回转半径:
4900(~4500)mm
升降行程:
800mm
该回转台可以适应60t和120t钢包的生产。
16)中间罐车:
半门型,
载重量:
~60t
17)中间罐:
矩形结构
中间罐容量:
正常30t/1000mm,
溢流35t/1100mm
18)钢流控制方式:
电动塞棒式;涡流液面检测
19)结晶器:
铜板材质:
CuCrZr
铜板长度:
900mm
足辊直径:
φ100mm;宽面1对,三节式;窄面4对
结晶器调宽:
手动调宽
20)结晶器振动装置
形式:
四连杆式振动装置
振幅:
0±5mm(可调)
振频:
0~200次/min
21)弯曲段(扇形0段)
辊子数量:
内、外弧各15个
22)弧形扇形段
扇形段个数:
5个
辊子数量:
每段内、外弧各7个
23)矫直扇形段
扇形段个数:
2个
辊子数量:
每段内、外弧各7个
24)水平扇形段
扇形段个数:
4个
辊子数量:
每段内、外弧各7个
25)脱引锭装置:
液压冲顶式
26)铸坯切割
自动火焰切割机:
切割行程:
~9m
27)窜动辊道:
窜动行程:
~600mm
28)引锭杆
引锭杆型式:
链式、下装、侧存放
引锭杆长度:
~11m
引锭杆厚度:
~160mm
引锭杆身宽度:
~1450mm
引锭杆头宽度:
700~1300mm
1250~1600mm
29)升降挡板:
1#机:
2个;2#机3个。
30)出坯辊道:
单独传动,成组控制,
31)辊道速度:
30m/min,部分变频
32)铸坯横移车:
运行速度:
0~100m/min
二、连铸车间金属工艺流程
钢包回转台
长水口+吹氩保护→↓
中间罐及中间罐车
快换浸入式水口+吹氩保护浇铸→↓
结晶器液面自动检测→结晶器及结晶器振动
↓
弯曲段及扇形段
↓
拉坯矫直机
↓
脱引锭装置
↓
切前辊道
↓
火焰切割机及切割区辊道
↓
运输辊道及引锭杆侧存放装置
↓
升降挡板
↓
铸坯横移装置
↓
热送辊道
↓
热送热连轧机组入炉辊道
辊道吊下
图1-1 连铸车间工艺流程图
三、连铸中间罐维修工艺流程
中间罐维修分为热循环和冷循环两种。
其维修过程如下:
中间罐热循环:
连铸用过的中间罐,在钢水注完后,关闭中间罐的塞棒,并用吊车从中间罐车上取下,运至中间罐维修区的冷却台架。
经初步的风冷,取下塞棒,清除中间罐内部残存渣及钢壳、耐火涂层和废水口,翻掉废耐火材料,修补砌耐火材料,砌水口、砌耐火泥涂层、装塞棒、加热干燥各工序后待用。
中间罐冷循环:
从连铸作业线上吊下用过的中间罐,运至中间罐维修区的冷却台架上,冷却到常温后,拆下塞棒、拆除中间罐内全部残存渣及钢壳、耐火永久层和废水口,将罐体吊到中间罐倾翻台上翻掉罐内废耐火材料,吊到修砌台上重新砌筑耐火材料、水口、砌耐火泥涂层、装塞棒、加热干燥各工序后待用。
图1-2中间罐热修工艺流程框图
四、板坯连铸设备维修工艺流程
设备维修的工艺过程:
线上吊下―冷却清理―分解维修―组装对中―存放待用。
图1-4结晶器维修工艺流程框图
图1-5弯曲段维修工艺流程框图
图1-6扇形段维修工艺流程框图
五、板坯连铸工艺参数
(一)、连铸钢水的要求
连铸钢水要保证脱氧良好,成份、温度均匀,符合连铸要求。
钢组分类
钢组号
钢组定义
代表钢种
1
低碳钢([C]≤0.08%)
SPHC,SPHD
2
包晶钢(0.08%<[C]≤0.17%)
Q235B,SS400
3
中碳钢(0.17%<[C]≤0.30%)
20,Q255
4
低合金钢*
BM510L、X52
*用Nb、Zr、B、V、Ti、Ce等元素微合金化,或者[Al]%×[N]>0.0003%。
代表钢种
钢组
钢种
1
SPHC、SPHD、SPHC、SPCC、SPHT1、SPHT2、08AL、SPHE、08、StW22、SAPH370、SAPH310、BM330RCL、BM380RCL、SAE1006
2
Q195、Q215A、Q235A、Q235B、SS400、B级、Q235D
3
20G、20R、Q255
4
Q345B、SS490、BM510L、HP295、X42、SM400A、09CuPTiRe、16MnRE、SPA-H、SM490A、BM440L、X52、BM440QZR、X60、BM480QZR
1、成份
(1)、C元素
A、对于低C钢种,C元素含量应尽量避开包晶反应区的敏感范围。
B、同中包多炉连浇时必须是同钢种,各炉次之间(含量之间的差异应≤0.02%)
(2)、[Mn]、[Si]元素
A、在各类钢水成份的范围内,并满足钢水脱氧要求的前提下,调整[Mn]、[Si]元素的含量,保持[Mn]/[Si]≥3.0以改善钢水流动性。
B、多炉连浇时,各炉次之间钢水中元素[Mn]、[Si]含量的差异应尽量≤0.20%
(3)、[S]元素
钢中[S]元素含量应控制在≤0.02%,并在钢水成份规格范围内要求[Mn]、[S]元素的含量保持[Mn]/[S]>25以提高铸坯的高温塑性。
(4)、[P]元素
钢中[P]元素含量应控制在≤0.03%。
(5)、某些对[C]、[S]、[P]以及气体含量有特殊要求的钢种其控制标准另行规定。
2、温度
(1)要求液相线温度的确定
钢水液相线温度按下式计算:
TL=1536.6-90C%-8Si%-5Mn%-30P%-25S%-3Al%-1.55Cr%-4Ni%-2Mo%-18Ti%-80N%-5Cu%
各成份采用各钢种元素成份上、下限的中央值,只有上限值的取上限值。
(2)连铸钢水目标过热度控制
T上台=TL+(60~80)℃
T中包=TL+(10~30)℃
(1)、供连铸第一炉T上台比正常供钢温度高20℃,第二、三炉按供钢温度上限控制。
(2)、从钢包吹氩结束到该炉钢包开浇,时间控制在20分钟以内;上台镇静时间控制在15分钟以内。
(二)结晶器及结晶器振动
1、结晶器铜板的使用标准
(1)结晶器上端内外弧宽边长度之差≤2mm;
(2)铜板厚度最大刨除量为10mm;
(3)铜板相对厚度差≤3mm;
(4)窄面磨损≤3mm;
(5)铜板平直度(或弧度)≤0.5mm;
(6)宽度弯曲≤10mm;窄面弯曲≤1.0mm;
(7)角部间隙≤0.3mm;
2、结晶器表面使用标准
(1)结晶器上部,长度方向距上口450mm内处,裂纹(或划痕)要求:
宽≤2.0mm、长≤10mm、深≤0.5mm、条数≤2;
(2)结晶器下部,长度方向距上口450mm以外处裂纹(或划痕)要求:
宽≤2.0mm、长≤50mm、深≤0.5mm、条数≤2;
(3)弯月面处镀层大面积龟裂,面积≤30×30mm2;
(4)弯月面处镀层脱落,面积为0;
3、结晶器窄面锥度使用标准
结晶器窄面锥度与目标值相差≤±0.1%;
4、结晶器铜板清洗标准
(1)连铸结晶器水箱每8个月酸洗一次;
(2)结晶器背板需要每月拆洗一次;
(3)铜板通钢量12万吨酸洗一次。
5、结晶器偏振
(1)内外弧方向偏振≤0.2mm;
(2)两窄面方向偏振≤0.5mm;
6、结晶器锥度设定
为保证板坯宽度外形尺寸误差符合标准要求,按照不同的钢组线收缩系数进行结晶器上口宽度计算,下口宽度按照各钢组锥度标准进行确定,偏差±0.2mm;单侧锥度允许偏差±0.3mm,实际锥度利用锥度仪检测。
具体见下表:
铸坯宽度
结晶器下口宽
结晶器上口宽
单侧锥度
锥度
(mm)
(B)
(A)
(A—B)/2
(%/m)
700
707.0
714.07
3.535
1.10
750
757.5
765.07
3.787
1.10
800
808.0
816.08
4.040
1.10
850
858.5
867.08
4.292
1.10
900
909.0
918.09
4.545
1.10
950
959.5
969.09
4.797
1.10
1000
1010.0
1019.64
4.818
1.05
1050
1060.5
1070.62
5.059
1.05
1100
1111.0
1121.60
5.300
1.05
1150
1161.5
1172.58
5.540
1.05
1200
1212.0
1223.56
5.781
1.05
1250
1262.5
1274.54
6.022
1.05
1300
1313.0
1325.53
6.263
1.05
1350
1363.5
1375.88
6.191
1.00
1400
1414.0
1426.84
6.421
1.00
1430
1444.3
1457.42
6.558
1.00
1450
1464.5
1477.80
6.650
1.00
1500
1515.0
1528.76
6.879
1.00
1550
1565.5
1579.72
7.109
1.00
1600
1616.0
1630.68
7.338
1.00
在每次更换结晶器及浇次间隙,对结晶器锥度进行的检查测定,不符合要求的需在线调整或更换结晶器。
7、结晶器水量设定
(1).水质
序号
名称
软水系统(结晶器冷却水)
1
PH值
8.5~8.9
2
总硬度
Max.350ppm
3
碳酸钙碱度
200ppm
4
侵蚀性CO2
none
5
电导率
Max.1200mμs/cm
6
硫酸盐
250ppm
7
氯化物
100ppm
8
沉积和悬浮物
20ppm
9
总溶解固体
600ppm
10
油/油脂
5ppm
(2).水量计算根据结晶器水槽来计算的:
结晶器水流量设定如下表所示
钢组
面
结晶器水流量(l/min)
设定值
下限值(*)
钢组1、3
宽面
3600
2350
窄面
650
430
钢组2、4
宽面
3000
2350
窄面
550
430
警告:
超出该范围停止浇注
结晶器进出水温度要求:
结晶器进水温度≤40℃
结晶器宽面进出水温差≤10℃
结晶器窄面进出水温差≤10℃
(3).结晶器进水总管压力≥0.8MPa
8、振动参数
1、振幅:
s=±3、±4
2、振动频率:
f=0~200次/min
3、振动曲线为正弦曲线
f振频(次/min)Vc拉速(m/min)
振动方程:
ε=(
)×100%Tn=
arccos(
)
f:
振频(次/min)s:
振幅(mm)
Vc:
拉速(m/min)Tn:
负滑脱时间(s)ε:
负滑脱率(%)
振动参数列表如下,负滑脱不变,负滑脱时间大于0.10秒
(三)二次冷却参数
1、各钢种二冷水强度设定的原则
钢组分类
钢组号
钢组定义
二冷强度
1
低碳钢([C]≤0.08%)
强冷
2
包晶钢(0.08%<[C]≤0.17%)
弱冷
3
中碳钢(0.17%<[C]≤0.30%)
中冷
4
低合金钢
弱冷
2、二冷喷嘴选型
扇形段号
喷嘴型号
喷嘴数量
扇形段号
喷嘴型号
喷嘴数量
足辊
9525
42
矫直6段
HPZ3.5-90B30-850
14
0#段
HPZ5.8-115B14
46
HPZ5.6-110B30-770
14
0#段
HPZ4.5-95B14
90
矫直7段
HPZ5.6-110B30-770
14
HPZ3.5-90B30-870
14
弧形1段
HPZ6.6-110B30-690
14
水平8段
HPZ5.6-110B30-770
14
弧形2段
HPZ6.6-110B30-600
42
水平9段
HPZ3.5-90B30-870
14
弧形3段
HPZ5.6-110B30-730
28
水平10段
3/8PZ31110B1
56
弧形4段
HPZ6.6-110B30-640
28
水平11段
PZ9700B16A2(手调)
56
弧形5段
HPZ3.5-90B30-730
28
辊道
3/8PZ59110B1
68
3、二次冷却水表选择:
比水量按0.6~0.9/1.2L/KG选择
(四)、浇铸参数
1、中间包钢水重量控制范围:
(1)、当中间包钢水重量达8~10t时或大包开浇大于60秒后,中包进行开浇。
(2)、浇注时根据中包温度检测,设定中包内钢水量
A、开浇时,钢水重量为8~10t
B、浇注正常时时,中包内钢水量25~30t,在长时间浇注时,中包内钢水量应控制在上限。
(3)、更换中间包时,一旦中间包钢水重量到达8~10t或塞棒部位钢液深度为300±50mm,关闭塞棒,严禁结晶器内下渣。
2、钢包、中间包测温
(1)、钢包测温要求
以钢包出精练炉或吹氩站的温度为基准。
上台温度可进行确认,
(2)、中间包内钢水温度测定要求
中间包钢水温度测定基准为4次/炉,每次测温间隔不得超过10分钟。
正常
1)钢包浇注后5分钟以内
2)钢包浇注了钢水的1/4时
3)钢包浇注了钢水的1/2时
4)钢包浇注了钢水的3/4时
非正常
下述场合,根据机长判断多测
1)中包更换前后
2)低温等异常时
3)与前次测温值相差10℃以上时
(3)、温度计异常时处理:
测温前后差值大时或温度值显示不稳定时通知仪表值班人员进行温度计的校正。
(4)、了解钢包降温情况,对非正常周转包要加强大、中包的保温工作,以免浇注后期低温。
3、连续浇注炉号划分
连铸板坯相邻炉号的划分方法:
以大包钢水注入中间罐时,中间罐注入结晶器的钢水即作为下炉的开始;根据钢水实际重量、浇注断面、定尺长度计算该炉铸坯支数,并在相应铸坯上标明炉号、铸机号、钢种。
4、起步时间和起步拉速的设定:
(1)中间包塞棒开~浇注开始的保持时间,根据每100mm板坯宽度4秒出苗时间原则
进行计算,最短出苗时间不得小于28秒。
(2)各断面起步拉速统一设定为0.3m/min。
5、浇铸速度的设定
实际生产中,机长要根据铸机状况、铸坯质量情况、生产节奏、钢水情况等综合因素,合理控制浇注速度,并努力保持恒拉速,以保证铸坯质量,获取最佳生产能力,生产组织中浇注速度参考下表(按每炉出坯量120吨计算)。
钢种类别
宽度×厚度(mm)
工作拉速(mm/min)
最大拉速(mm/min)
低碳钢
210×1250
170×1250
1.6
1.8
2.0
2.2
包晶钢
210×1250
170×1250
1.4
1.6
1.8
2.0
中碳钢
210×1250
170×1250
1.2
1.3
1.6
1.7
低合金钢
210×1250
170×1250
1.4
1.5
1.8
1.9
异常情况下的拉速控制:
(1)当发现液面变动20mm以上时(急剧变动)必须急减速到0.6m/min以下
(2)操作工感觉塞棒动作异常时,必须急减速到0.6m/min以下
(3)开浇有溢钢倾向时,如果出苗时间>40秒,可以开始拉坯,拉速设定在0.3~0.6m/min否则关盲板终浇。
清除挂钢,引锭杆倒送,将坯头吊出。
(4)漏钢后,维持当前拉速,或将拉速设定到0.6~1.0m/min。
如果铸坯拉不动,则按滞坯处理。
(5)钢水节奏紧张时,以钢水供应周期进行控速,最低拉速≥0.6m/min。
(6)出尾坯开始时,铸速0.3m/min。
坯尾出结晶器之后,以0.15m/min逐渐加大拉速到正常拉速(<1.4m/min),直至拉完板坯。
6、结晶器液面的设定
(1)、钢液面的目标值:
为了延长浸入式水口的使用寿命,可将液面目标值制定为两个阶段,通常限制在距上口100mm及70mm
(2)、在浇注开始后的增速终了后,液面在目标值附近稳定后,可以实施液面自动控制。
(3)、在中间包、浸入式水口更换、铁板插入等的非稳定作业前,以及浇注终了前,终止液面自动控制,切换为人工控制。
(4)、当由于检测器不良,控制参数不恰当等引起的液面控制精度不良时,终止液面自动控制,切换为人工控制。
(5)、一旦中间包液态钢水重量小于15t,立即关闭结晶器液面自动控制系统。
(6)、液面自动控制时,钢液面波动值<±3mm;人工控制时,钢液面波动值<±10mm。
7、结晶器保护渣
(1)、正常浇铸时,不让保护渣中断,边观察钢液面保护渣覆盖情况边投入,保护渣的加入原则是,少加、勤加、均匀加入,保持黑渣操作
(2)、保护渣消耗量为0.4~0.8Kg/t.s;液渣层厚度为7~12mm,烧结层和原渣层总厚控制在20~30mm为宜
(3)、分钢种使用专用保护渣。
注意:
不管任何原因保护渣均需在使用时开封,防止受潮。
8、结晶器保护渣换渣要求:
保护渣表面含有大量夹杂物及消耗量低时,需进行换渣操作。
原则上,保护渣换渣时拉速在Vc=0.6m/min以下时进行
(1)、中间包开浇或更换后、浸入式水口更换后
(2)、塞棒急剧开关后
(3)、熔融层异常时:
熔融层厚度小于5mm,大于25mm时
(4)、消耗量异常<0.4Kg/t钢时
9、引锭头准备
为了覆盖所有的板坯断面尺寸,准备了两种厚度的引锭头各两个:
(1)用于断面700~1250mm
(2)用于断面1220~1600mm
(3)这两种不同的断面,分别由两种引锭头接加不同的垫块。
不同断面的引锭头,分别接加不同的垫块,引锭头宽度要比结晶器下口宽度(计划浇注断面)小10~20mm。
(4)引锭头停止位置规定为离结晶器下口1000mm,然后再点动到引锭头距结晶器铜板上口650~600mm的位置。
10、铸坯成品取样标准
(1)、中包样
●大包钢水注入中间包钢水量达1/3时(第一个试样为成品样)
●大包钢水注入中间包钢水量达2/3时(第二个试样为保留样)
●取样器插入中包液面内200mm左右,插入停留时间为3~5秒。
(2)、钢坯样
●根据炉号划分,该炉铸坯走到切割位置时,利用割样副枪切割试样(低倍分析用);或对该炉铸坯作出记号,铸坯下线后,人工割样(化验成份用)
●试样厚度为80~200mm
11、中间包有关气体吹入标准
为了防止钢包与中间包之间的空气氧化、中间包与结晶器之间水口接合部空气的吸入,浸入式水口内壁夹杂物的粘着,为了促进结晶器内夹杂物上浮等,长水口与钢包下水口之间、中间包上水口与浸入式水口之间,必须进行Ar封;中间包塞棒、中间包上水口必须进行吹Ar操作。
(1)、对象钢种:
全钢种
(2)、吹入气体种类:
Ar气
(3)、(水口+塞棒+氩封)氩气总量≤20(L/min)
(4)、吹入气体流量的判断原则
在浇注过程中,要根据结晶器液面状况和钢流量变化合理调节氩气流量,即根据钢种、断面、拉速、中包钢水温度、中包钢水液面高度、结晶器液面高度等情况的变化合理微调氩气流量。
中包吹氩量必须控制在合适的范围内,以结晶器液面稳定、钢水不裸露,不骚动为原则;以调整到结晶器液面呈微小波浪型为最佳。
(五)切割、出坯
1、切割机的参数
结构形式:
龙门架式
割枪数量:
4把(其中切割试样2把)
切割范围:
宽度700-1600mm
厚度:
170~210mm
介质要求:
霞普气
热值:
20000kcal/Nm3
压力:
~0.02Mpa
氧气:
压力:
1.2-1.5Mpa
纯度:
99.5%
压缩空气:
压力:
0.4-0.6Mpa.
铸坯长度:
9~12m(正常)4.8~5.8m(少量)
割枪运行速度:
快速:
3000mm/min
切割:
350~500mm/min
切割行程:
~9000mm
切割机走行速度:
2.5~24m/min
割缝宽度≤8mm
主、副枪距离80~250mm(可调)
点火:
用引燃火苗自动点火
切割粒化方式:
粒化水
2、板坯定尺的确定:
L热=L冷×X+S
L热………………定尺长度,
L冷………………冷坯长度
S………………割缝宽度
X………………收缩系数,碳钢(收缩系数1.018)
铸坯热定尺的确定主要考虑的是铸坯的热收缩,而铸坯的热收缩要受钢种、铸坯表面温度、拉速等因素的影响,因此,在实际生产中需根据现场确认后适时调整。
3、铸坯管理
(1)执行按炉送钢制度,同钢种、同炉号、同规格的板坯应尽量堆放在一个垛位。
合格品、废品、待处理品、处理后的合格品都应按规定区域堆放,并标识清楚。
(2)板坯标识按(炉号-铸机流号-第几支坯-钢种)在每支铸坯的一个侧面标清。
(3)散落的铸坯及处理后的非定尺坯还需在板坯的上表面标明该板坯的(宽度×长度)。
第二炼钢厂
二〇一〇年四月二十一日