装配与划线基础知识1.docx
《装配与划线基础知识1.docx》由会员分享,可在线阅读,更多相关《装配与划线基础知识1.docx(15页珍藏版)》请在冰豆网上搜索。
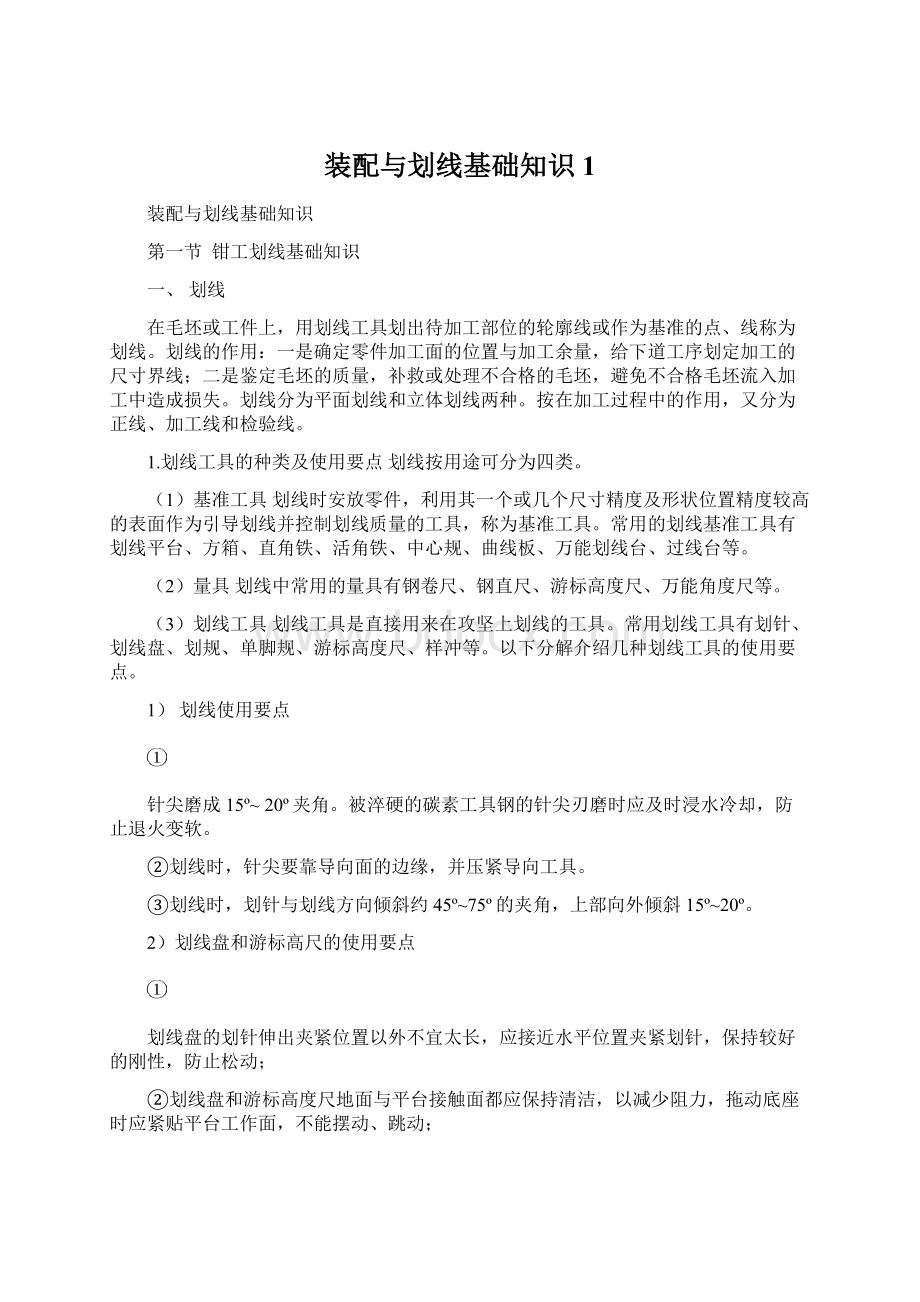
装配与划线基础知识1
装配与划线基础知识
第一节钳工划线基础知识
一、划线
在毛坯或工件上,用划线工具划出待加工部位的轮廓线或作为基准的点、线称为划线。
划线的作用:
一是确定零件加工面的位置与加工余量,给下道工序划定加工的尺寸界线;二是鉴定毛坯的质量,补救或处理不合格的毛坯,避免不合格毛坯流入加工中造成损失。
划线分为平面划线和立体划线两种。
按在加工过程中的作用,又分为正线、加工线和检验线。
1.划线工具的种类及使用要点划线按用途可分为四类。
(1)基准工具划线时安放零件,利用其一个或几个尺寸精度及形状位置精度较高的表面作为引导划线并控制划线质量的工具,称为基准工具。
常用的划线基准工具有划线平台、方箱、直角铁、活角铁、中心规、曲线板、万能划线台、过线台等。
(2)量具划线中常用的量具有钢卷尺、钢直尺、游标高度尺、万能角度尺等。
(3)划线工具划线工具是直接用来在攻坚上划线的工具。
常用划线工具有划针、划线盘、划规、单脚规、游标高度尺、样冲等。
以下分解介绍几种划线工具的使用要点。
1)划线使用要点
针尖磨成15º~20º夹角。
被淬硬的碳素工具钢的针尖刃磨时应及时浸水冷却,防止退火变软。
②划线时,针尖要靠导向面的边缘,并压紧导向工具。
③划线时,划针与划线方向倾斜约45º~75º的夹角,上部向外倾斜15º~20º。
2)划线盘和游标高尺的使用要点
划线盘的划针伸出夹紧位置以外不宜太长,应接近水平位置夹紧划针,保持较好的刚性,防止松动;
②划线盘和游标高度尺地面与平台接触面都应保持清洁,以减少阻力,拖动底座时应紧贴平台工作面,不能摆动、跳动;
③游标高度尺是精密划线工具,不得用于粗糙毛坯的划线;用完后应擦净,涂油装盒保管。
3)划规、单脚规使用要点
划规、单脚规使用时应施较大压力于旋转中心一脚,而施较轻压力于另一脚在零件表面划线;
②划线时两脚尖要保持在同一个平面上;
③单脚规使用时,弯脚离零件端面的距离始终保持一致。
4)样冲使用要点
样冲尖磨成45º~60º夹角,磨时防止过热退火;
②打样冲时冲尖对准线条正中;
③样冲眼间距视划线长短曲直而定,线条长而直则间距可大些,短而曲则间距可小些交叉、转折处必须打上样冲眼;
样冲眼的深浅要视零件表面粗糙程度而定,表面光滑或薄壁零件样冲眼打得浅些,粗糙表面打得深些,精加工表面禁止打样冲眼。
(4)辅助工具辅助工具是划线中起支撑、调整、装夹等辅助作用的工具,常用的有千斤顶、V形架、C刑夹头、楔铁、定心架等。
2.划线涂料为使划出的线条清晰可见,划线前应在零件划线部位涂上已成薄而均匀的涂料。
常用划线涂料配方和应用见下表。
常用划线涂料配方和应用
名称
配制比例
应用场合
石灰水
稀糊状熟石灰水加适量骨胶或桃胶
大、中型铸件和锻件毛坯
蓝油
品紫(青莲、普鲁士蓝)2%~4%加漆片(洋干漆)3%~5%和91%~95%酒精混合而成
已加工表面
硫酸铜溶液
100g水中加1g~1.5g硫酸铜和少许硫酸
形状复杂的零件或已加工面
3.平面划线只要在零件一个表面上划线即能明确表示零件加工界线的称平面划线。
平面划线分几何划线法和样板划线法两种。
(1)几何划线法是根据零件图的要求,直接在毛坯上利用平面几何作图的基本方法划出加工界线的方法。
它的基本线条有平行线、垂直线、圆弧与直线或圆弧与圆弧的连接线、圆周等分线、角度等分线等,其划线方法都和平面几何作图方法一样,划线过程不再赘述。
(2)样板划线法是将根据零件尺寸和形状要求划好线并加工成形的样板,放置在毛坯合适的位置划出加工界线的方法。
它适用于平面形状复杂、批量大、精度要求一般的场合。
其优点是容易对正基准,价格哦哦那个余量留得均匀,生产效率高。
在拌料上用样板划线,可以合理排料,提高材料利用率。
4.立体划线立体划线是在零件的二个以上的表面划线。
立体划线的方法一般采用零件直接翻转法。
划线过程中涉及零件或毛坯的放置和找正、基准选择、借料等方面。
(1)零件或毛坯的放置立体划线时,零件或毛坯放置位置的合理选择十分重要。
这关系到划线的质量和划线效率。
一般较复杂的零件都要经过三次或三次以上的放置,才可能将全部划线划出,而其中特别要重视第一划线位置的选择。
其选择原则如下:
1)第一划线位置的选择原则优先选择如下表面:
零件上主要的孔、凸台中心线或重要的加工面。
相互关系最复杂及所划线条最多的一组尺寸线;零件中面积最大的一面。
2)第二划线位置的选择原则要使主要的孔、凸台的另一中心线在第二划线位置划出。
3)第三划线位置的选择通常选择与第一和第二划线位置相垂直的表面,盖面一般是次要的、面积最小的、线条相互关系较简单且线条较少的表面。
(2)划线基准的选择零件图上用来确定其它点、线、面位置的基准称设计基准,而划线中用来确定零件各部分尺寸、几何形状及相对位置的依据称划线基准。
立体划线的每一划线位置都有一个划线基准,而且划线往往是在这一划线位置开始。
它的选择原则是:
1)尽量与设计基准重合。
2)对称形状的零件、应以对称中心线为划线基准。
3)有孔或凸台的零件、应以主要孔或凸台的中线为划线基准。
4)未加工的毛坯件,应以主要的、面积较大的不加工面为划线基准。
5)加工过的零件,应以加工后的较大表面作划线基准。
(3)零件或毛坯的找正找正是利用划线工具使零件或毛坯上有关表面与基准面(如划线平台)之间调整到合适的位置。
零件找正是依据零件选择划线基准的要求进行的。
零件的划线基准又是通过找正的途径来最后确定它在零件上的准确位置。
所以零件和毛坯的找正和划线基准选择原则是一致的。
(4)零件的借料借料即通过试划和调整,将各部位的加工余量在允许的范围内重新分配,使各加工表面都有足够的加工余量,从而消除铸件或锻件毛坯尺寸、形状和位置上的某些误差和缺陷。
对一般较复杂的工件,往往是要经过多次试划,才能最后确定合理的借料方案。
它的一般步骤是:
1)测量毛坯或零件各部分尺寸,找出偏移部位和偏移量。
2)合理分配各部位加工余量,确定借料方向和大小,划出基准线。
3)以基准线为依据,按图划出其余各线。
4)检查各加工表面加工余量,若发现余量不足,则应调整各部位加工余量,重新划线。
(5)立体划线的步骤了解以上要求和原则后,立体划线步骤如下:
1)看清图样,详细了解零件加工工艺过程,并确定需要划线的部位;明确零件及其划线的有关部分的作用和要求;判定零件划线的次数和,每次划线的位置范围。
2)选定划线基准,确定装夹位置和装夹方法。
3)检查毛坯的误差情况,并确定是否需要借料,如需借料,则应初步确定借料的方向与距离,然后在划线部位涂上涂料。
4)找正。
5)划线。
6)详细检查划线的准确性和是否有漏划线条。
7)在划好的线条上打出样冲眼。
第二节复杂零件的划线
一、基本概念
根据图样和实物要求,在毛坯或工件上,用划线工具划出待加工部位的轮廓线作为基准点、线的操作称为划线。
(一)、按加工中的作用,划线可分为加工线,证明线和找正线3种。
划线按照用途分,有以下三种:
线按照用途分,有以下三种
1.在板料、条料上划落料线。
供气割、电焊、剪切、锯开和加工用。
2.在铸、锻毛坯件上划线,用以确定加工面的位置和孔的中心,供粗加工用。
以划线来校正加工余量,对某些由于铸造、锻造中存在的缺陷,经划线确定是否可以补救。
3.在半成品上划线,用以确定精加工表面及孔的位置,保证加工质量.
(二)划线按复杂程度又可分为两种
1.平面划线,也可叫简单划线,在工件的一个表面上划线后,即能明确表面加工界线的操作叫平面划线。
如在法兰端面上划占孔加工线。
2.立体划线,也可叫复杂划线,是在毛坯工件几个不同的表面或彼此成不同角度的各个表面进行划线的操作叫立体划线。
(三)划线的作用
1.通常情况下,一些比较复杂的工件毛坯和半成品,在进入精耕细作粗精加工时,常需凭借划线作为校正的依据。
2.通过划线,可以检查毛坯是否与图纸要求一致。
3.利用划线校正加工余量,来补救坯件上存在的某些局部缺陷。
4.及早发现和剔除一些无法校正加工余量的坯件,以免浪费后道工序的加工工时。
(四)划线注意事项:
1.划线前必须研究图纸上的视图,尺寸、形位公差和技术要求,综合工件的加工工艺和设计要求进行分析,力求按设计基准划线。
2.合理选定第一划线位置,以提高划线质量和简化划线过程。
尽量选择划线面积较大且平行於划线平台的表面为第一划线位置或者尽量选择精度要求较高的或主要加工面的加工线为第一划线位置线。
3.划重型轴特别注意工件锻造缺陷。
挠性轴(L/d>15)注意工件弯曲。
4.复杂零件一般划三个方向的十字线及检查线。
5.斜孔及斜面必须把线引到斜面上去。
6.对畸形大形工件合理选择支承点,使工件的重心与专用划线夹具的组合重心落在支承面内,否则加支承点。
7.按划线基准(一般为设计基准)进行划线时可能出现某些平面、孔等加工余量不足,为挽救毛坯,在允许的条件下将各部分加工余量重新分配,保证各加工处仍有一定的加工余量,这就是借料。
为保证加工余量,可能出现几次借料。
二、划线基准及其选择
划线时,决定工件其他的点、线、面的位置所依据的点、线和面,称为划线的基准。
这个基准一般同设准备重合。
在零件几何形状特殊时,可临时增加工艺基准为划线基准。
基准的选择要以保证零件的精度,使加工余量分配合理,简化划线工序为原则。
一般按下列三种不同情况来选定。
1、以两个互成直角的外平面(或直角)为基准。
划线前,先加工好两个基准边,并互成直角,划线的一切尺寸,都以这两个边作基准划出其他的线。
2、以一个底平面和一条中心线为基准如图9-9所示。
划线前,先将底平面加工好,然后划出中心线,再划其他的加工线。
三、以两条中心线作基准如图9-10所示。
先根据毛坯轮廓划出两条中心线,然后再依据中心线划其他的加工线。
第三节装配知识
一、装配基本知识
1.装配工艺过程装配是按照一定的技术要求,将若干零件装成一个组件或部件,或将若干零件、部件装成一个机械的工艺过程。
装配过程是机械制造生产过程中重要的也是最后的一个环节。
机械产品的质量必须由装配最终来保证。
机械产品结果后和装配工艺性是保证装配质量的前提条件,装配工艺过程的管理与控制则是保证装配质量的必要条件。
装配工艺过程包括装配、调整、监测和试验等工作,其工作量在机械制造总工作量中所占的比重较大。
产品的结构越复杂、精度与其它的技术条件越高,装配工艺过程也就越复杂,装配工作量也越大。
产品的装配工艺过程由以下四部分组成:
(1)装配前的准备工作包括:
研究和熟悉装配图,了解产品的结构、零件的作用以及相互的连接关系;确定装配的方法、顺序、准备所需的工具;对零件进行清理和清洗;对某些零件进行修配、密封性试验或平衡工作等。
(2)装配工作通常分为部装和总装。
部装是把各个零件装配成一个完整的机构的过程。
总装是把零件和部件装配成最总产品的过程。
(3)调整、精度检验和试车调整是指调节零件或机构的相对位置、配合间隙和结构松紧等,如轴承间隙、齿轮啮合的相对位置、摩擦离合器松紧的调整。
精度检验包括工作精度检验和几何精度检验(有的机器则不需要做这项工作)。
试车是机器装配后,按设计要求进行的运转试验,包括运转灵活性、工作时温升、密封性、转速、功率、振动和噪声等。
(4)喷漆、涂油和装箱。
2.装配办法为了保证装配的精度要求,机械制造中常采用以下四种装配方法之一完成装配工作。
(1)互换装配法在装配时各配合零件不经修配、选择或调整即可达到装配精度的方法称为互换装配法。
互换装配法的特点是:
装配简单,生产率高;便于组织流水作业;维修时更换零件方便。
但这种方法对零件的加工精度要求较高,制造费用将随之增大。
因此仅在配合精度要求不太高或产品批量较大时采用。
(2)分组装配法在成批或大量生产中,将产品各配合副的令济南按实测尺寸分组,然后按相应的组分别进行装配。
在相应组进行装配时,无需再选择的装配方法,称为分组装配法。
分组装配法的特点是:
经分组后在装配,提高了装配精度;零件的制造公差可适当放大,降低了成本;要增加零件的测量分组工作,并需加强管理。
(3)调整装配法在装配时,根据装配实际的需要,改变产品中可调整零件的相对位置称为调整装配法。
调整装配法的特点是;零件不需任何修配即能达到很高的装配精度;可进行定期调整,故容易回复精度,这对容易磨损或因温度变换而需改变尺寸位置的结构是很有利的;调整件日容易降低配合副的连接刚度和位置精度,在装配时必须十分注意。
(4)修配装配法在装配时,根据装配的实际需要,在某一零件上去除少量预留修配量,以达到装配精度的方法,称为修配装配法。
修配装配法的特点是:
零件的加工精度可大大降低;无需采用高精度的加工设备,而又能得到很高的装配精度;但这种方法使装配工作复杂化,仅适宜于在单件生产、小批生产中采用。
3.装配工作的要点要保证装配产品的质量,必须按照规定的装配技术要求去操作。
不同产品的装配技术要求虽不尽相同,但在装配过程有许多工作要点是必须共同遵守的。
(1)做好零件的清理和清洗工作。
清理工作包括去除残留的型砂、铁锈、切屑等。
零件上的油污、铁锈或附着的切屑,可以用柴油、煤油或汽油作为洗涤液进行清洗,然后用压缩空气吹干。
(2)相配表面在配合或连接前,一般都需加润滑剂。
(3)相配零件的配合尺寸要准确,装配时对于某些较重要的配合尺寸应进行复验或抽验。
(4)做到边装配边检查。
当所装配的产品较复杂时,每装完一部分就应检查是否符合要求。
在对螺纹连接件进行紧固的过程中,还应注意对其他有关零部件的影响。
(5)试车时的事前检查和启动过程的监视是很必要的,例如检查装配工作的完整性、各连接部分的准确性和可靠性、活动件运动的灵活性、润滑系统的正常性等。
机器启动后,应立即观察主要工作参数和运动件是否正常运动。
主要工作参数包括润滑油压力、温度、振动和噪声等。
只有当启动阶段指标正常、稳定,才能进行试运转。
二、固定连接的装配知识
1.螺纹连接的预紧、防松及其装配螺纹连接是一种可拆的固定连接,它具有结构简单、连接可靠、装拆方便等优点,因而在机械中应用极为普遍。
(1)螺纹连接的预紧螺纹连接为了达到紧固且可靠的目的,必须保证螺纹之间具有一定的摩擦力矩,此摩擦力矩是由施加拧紧力矩后产生的,即螺纹之间产生了一定的预紧力。
螺纹连接的力矩一般由装配者按经验控制,但对于重要的螺纹连接,则由设计人员确定力矩。
螺纹装配连接时,拧紧力矩应适宜。
(2)螺纹连接的装配与防松装配前要仔细清理工件表面,锐边倒角并检查是否与图样相符。
旋紧的次序要合理。
一般用手旋紧后,再使用扳手旋紧。
拧紧力矩必须适当,在没有规定拧紧力矩和专用工具的条件下,全凭经验而定。
过大的拧紧力矩常常造成螺杆断裂、螺纹滑牙和机件变形;而郭襄的拧紧力矩同样会因连接紧固性不足,造成设备及人身事故。
由于拧紧力矩的大小由多方面因素所决定,对于不同材料和螺纹直径在一般情况下采用呆扳手来拧紧螺母是比较合理的。
它的柄长与开口尺寸保持了适宜的比例,拧紧力矩不会产生过于悬殊的出入。
2.键连接的类型及其装配键是用于连接传动件,并能传递转矩的一种标准件。
按结构特点和用途不同,分为松键连接、紧键连接和花键连接三种。
(1)松键连接的装配松键连接应用最广泛。
它又分为普通平键、半圆键、导向平键三种。
其特点是只承受力矩而不能承受轴向力。
(2)紧键连接的装配紧键又称楔键,其上表面亵渎一般为1:
100.装配时要使键的上下工作表面和轴槽、轮毂槽的底部贴紧,而两侧面应有间隙。
键的斜度一定要吻合,可用涂色法检查接触情况。
若接触不好,可用锉刀或刮刀修整键槽。
钩头键安装后,钩头和套件端面,必须留有一定距离,供修理调整时拆卸用。
(3)花键连接的装配装配前应按图样公差和技术条件检查相配件。
套件热处理变形后,可用花键推刀修整,也可用涂色法修整,花键连接分固定连接和滑动连接两种:
固定连接稍有过盈,可用铜棒轻轻敲入,过盈量较大时,则应将套件加热至80℃~120℃后进行热装;滑动连接应滑动自如,灵活无阻滞,在拥有转动套件时不应感觉有间隙。
3.销连接的类型及其装配销连接在机构中除起到连接作用外,还可起定位作用。
按销子的结构形式,分为圆柱销、圆锥销。
开口销等几种。
其装配要点如下:
(1)圆柱销的装配圆柱销按配合性质有间隙配合、过度配合和过盈配合,按使用场合不同有一定差别,使用时要按规定选用。
(2)圆锥销的装配圆锥具有1:
50的锥度。
锥孔铰削时宜用销子试配,以手推入80%~85%的锥销长度即可。
锥销紧实后,销的大端应露出工件平面(一般为稍大于倒角尺)。
(3)开口销的装配开口销打入孔中后,将小端开口扳开,防止振动时脱出。
4.过盈连接的类型及其装配过盈连接是依靠包容件(孔)和被包容件(轴)配合后的过盈值达到紧固连接的。
装配后,轴的直径被压缩,孔的直径被胀大。
由于材料的弹性变形,在包容件和被包容件配合面产生压力。
工作时,依靠此压力产生摩擦力来传递转矩、轴向力。
过盈俩节的结构简单,对中性好,承载能力强,还可避免零件由于有键槽等原因而削弱强度。
但配合面加工精度要求较高,装配工作有时也不甚方便,需要采用加热或专用设备工具等。
过盈连接常见形式有两种,即圆柱面过盈连接和圆锥面过盈连接,最广泛应用的是圆柱面过盈连接。
过盈连接的装配过盈连接的装配方法很多,依据结构形式、过盈大小、材料、批量等因素有锤击法、螺旋压力机装配、气动杠杆压力装配、油压机装配等方法,还有热胀配合法(紅套)和冷缩法。
5管道连接的类型和装配
(1)管道连接的类型管道是由管、管接头、法兰盘和衬垫等零件组成的,并与机械上的流体通道相连,以保证水、气体或液体等流体流动或能量传递。
管按材料的不同,有钢管、铜管、橡胶管、尼龙管等。
管接头按结构形式不同,有螺纹管接头、法兰式管接头,卡套式管接头、球形管接头和扩口薄壁管接头等多种
(2)管道连接的装配
1)保证足够的密封性采用管道连接时,管在连接以前常需进行密封性试验(水压试验或气压试验),以保证管子没有破损和泄漏现象。
为了嘉庆密封性,使用螺纹管接头时,在螺纹处还需加以填料,如白漆加麻丝或聚四氟乙烯薄膜等。
用法兰盘连接时,须在接合面之间垫以衬垫,如石棉板、橡胶或软金属等。
2)保证压力损失最小采用管道连接时,管道的通流界面足够大,长度应尽量短且管壁要光滑。
管道方向的急剧变化和界面的突然改变都会造成压力损失,必须尽可能避免。
3)法兰盘连接连接时,两法兰盘端面必须与管的轴心线垂直。
4)球型管接头的连接当采用球型管接头连接时,如管道流体压力较高,应将管接头的密封球面(或锥面)进行研配。
涂色检查时,其接触面宽度应不小于1mm,以保证足够的密封性。
三、带传动机构的装配
带传动机构是将传动带紧紧地套在两个带轮上,利用带与带轮之间的摩擦力来传递运动和动力。
同齿轮传动相比,它具有传动平稳、噪声低、结构简单、制造容易、可过载保护及适应两轴中心距较大场合等优点。
但它传动比不准确(同步齿形带传动除外)、传动效率低且容易磨损。
按带的断面形状不同,带传动分为平带传动、V带传动、圆形带传动和同步齿形带传动。
(一)、带传动机构的装配技术要求
(1)带轮安装要正确,其径向圆跳动量和端面圆跳动量应控制在规定范围内。
(2)两带轮中间平面应重合,一般倾斜角应小于1°。
(3)带轮工作面表面粗糙度值大小要适带轮工作面表面粗糙度值大小要适,一般为Ra1.6。
(4)带的张紧力要适当,且调整方便。
(二)、带与带轮的装配
1.带轮的装配
带轮孔与轴为过渡配合,有少量过盈,同轴度较高,并且用紧固件作周向和轴向固定。
2.V带的安装
安装v带时,先将其套在小带轮轮槽中,然后套在大轮上,边转动大轮,边用一字旋具将带拨入带轮槽中。
(三)、张紧力的控制与调整
带传动是摩擦传动,适当的张紧力是保证带传动正常工作的重要因素。
张紧力不足,张紧力不足,带将在带轮上打滑,使带急剧磨损;张紧力过大,则会使带寿命缩短,轴与轴承上作用力增大。
1.张紧力的检查.
(1)在带与带轮两切点的中心,用弹簧秤垂直于皮带加一载荷,通过测量产生的挠度y来检查张紧力的来检查张紧力的大小。
(2)可根据经验判断张紧力是否合适。
2.张紧力的调整
传动带工作一定时间后将发生塑性变形,使张紧力减小。
为能正常地进行传动,在带传动机构中都有调整张紧力的装置,其原理是靠改变两带轮的中心距来调整张紧力。
当两带轮的中心距不可改变时,可使用张紧轮张紧。
四、链传动机构的装配
链传动机构是由两个链轮和连接它们的链条组成,通过链条与链轮的啮合来传递运动和动力。
链传动的传递功率大,传递效率高,能保证准确的平均传动比,适合于在低速、重载和高温条件以及尘土飞扬、淋水、淋油等不良环境中工作,但安装维护要求较高,无过载保护作用。
链传动机构按工作性质的不同,可分为传动链、起重链和牵引链3种。
(一)、链传动机构装配的技术要求
(1)链轮的两轴线必须平行其允差为沿轴长方向0.5mm/m。
(2)两链轮的中心平面应重合轴向偏移量不能太大,一般当两轮中心距小于500mm时,轴向偏移量应在1mm以下,两轮中心距大于500mm时,应在2mm以下。
(3)链轮的跳动量跳动量可用划针盘或百分表进行检验。
(4)链条的下垂度要适当
(二)、链传动机构的装配
链传动机构的装配内容包括:
链轮与轴的装配、两链轮相对位置的调整,链条的安装和链条张紧力的调整。
链轮与轴的配合为过渡配合。
装配后应检查链轮的跳动,检查两轴线平行度和轴向偏移量。
五、齿轮传动机构的装配
齿轮传动是机械中最常见的传动方式之一,它依靠轮齿间的啮合来传递运动和扭矩。
齿轮传动具有能保证准确的传动比、传递的功率和速度范围大、传动效率高、使用寿命长、结构紧凑、体积小等优点,它的缺点是传动时噪声大、易冲击振动、不宜远距离传动、制造成本高。
(一)、齿轮传动的装配技术要求
(1)齿轮孔与轴的配合要适当,能满足使用要求。
空套齿轮在轴上不得有晃动现象;滑移齿轮不应有咬死或阻滞现象;固定齿轮不得有偏心或歪斜现象。
定齿轮不得有偏心或歪斜现象。
(2)保证齿轮有准确的安装中心距和适当的齿侧问隙。
齿侧间隙是指齿轮非工作表面法线方向距离。
侧隙过小,齿轮传动不灵活,热胀时会卡齿,加剧磨损;侧隙过大,则易产生冲击、振动。
(3)保证齿面有一定的接触面积和正确的接触位置。
(4)在变速机构中应保证齿轮准确的定位,其错位量不得超过规定值。
(5)对转速较高的大齿轮,一般应在装配到轴上后再作动平衡检查,以免振动过大。
(二)、圆柱齿轮传动机构的装配
圆柱齿轮的装配一般分两步进行:
先将齿轮装在轴上,再把齿轮轴组件装入箱体。
1.齿轮与轴的装配
在轴上空套或滑移的齿轮与轴的配合为间隙配合,装配前应检查孔与轴的加工尺寸是否符合配合要求。
2.齿轮轴装入箱体
齿轮啮合质量的好坏,齿轮啮合质量的好坏,除了齿轮本身的制造精度外,箱体孔的尺寸精度、形位精度也对其有直接的影响,其有直接的影响,所以在齿轮轴组件装入箱体应对箱体进行检查。
装前对箱体检查包括:
1)孔距相互啮合的一对齿轮的安装中心距是影响齿侧间隙的主要因素。
2)孔系(轴系)平行度的检验孔系平行度影响齿轮的啮合位置和面积。
检验方法如图7-响齿轮的啮合位置和面积。
3)孔轴线与基面距离尺寸精度和平行度的检验
4)孔中心线与端面垂直度的检验
5)孔中心线同轴度的检验
机器修理后的装配,一般对箱体不作检验;但箱体磨损严重或大修理后,应对箱体孔进行检验,检验合格后方可进行装配。
3.齿轮啮合质量的检验
齿轮轴组件装入箱体后,应对齿轮啮