多产品多阶段制造系统仿真与分析教学提纲.docx
《多产品多阶段制造系统仿真与分析教学提纲.docx》由会员分享,可在线阅读,更多相关《多产品多阶段制造系统仿真与分析教学提纲.docx(15页珍藏版)》请在冰豆网上搜索。
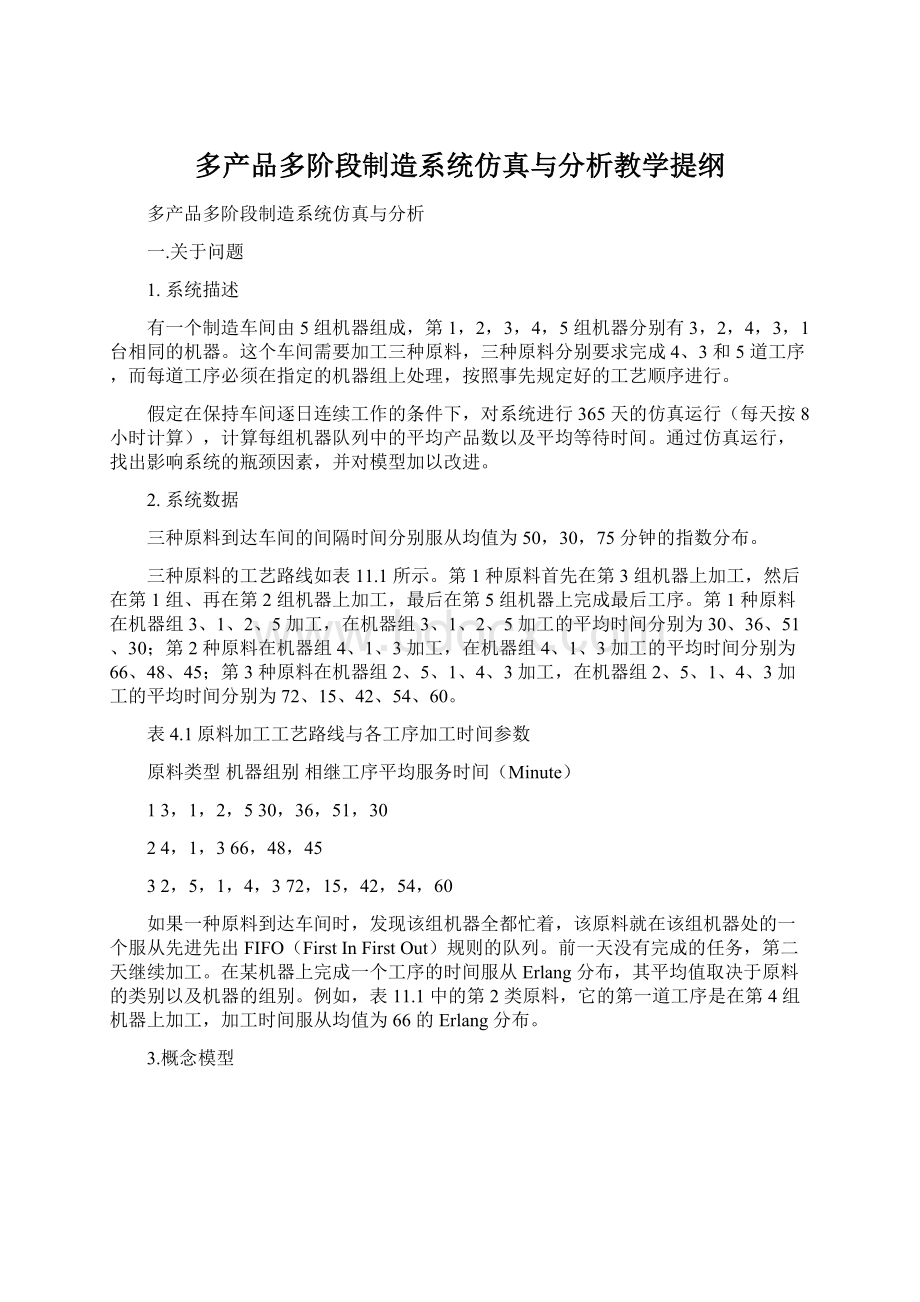
多产品多阶段制造系统仿真与分析教学提纲
多产品多阶段制造系统仿真与分析
一.关于问题
1.系统描述
有一个制造车间由5组机器组成,第1,2,3,4,5组机器分别有3,2,4,3,1台相同的机器。
这个车间需要加工三种原料,三种原料分别要求完成4、3和5道工序,而每道工序必须在指定的机器组上处理,按照事先规定好的工艺顺序进行。
假定在保持车间逐日连续工作的条件下,对系统进行365天的仿真运行(每天按8小时计算),计算每组机器队列中的平均产品数以及平均等待时间。
通过仿真运行,找出影响系统的瓶颈因素,并对模型加以改进。
2.系统数据
三种原料到达车间的间隔时间分别服从均值为50,30,75分钟的指数分布。
三种原料的工艺路线如表11.1所示。
第1种原料首先在第3组机器上加工,然后在第1组、再在第2组机器上加工,最后在第5组机器上完成最后工序。
第1种原料在机器组3、1、2、5加工,在机器组3、1、2、5加工的平均时间分别为30、36、51、30;第2种原料在机器组4、1、3加工,在机器组4、1、3加工的平均时间分别为66、48、45;第3种原料在机器组2、5、1、4、3加工,在机器组2、5、1、4、3加工的平均时间分别为72、15、42、54、60。
表4.1原料加工工艺路线与各工序加工时间参数
原料类型机器组别相继工序平均服务时间(Minute)
13,1,2,530,36,51,30
24,1,366,48,45
32,5,1,4,372,15,42,54,60
如果一种原料到达车间时,发现该组机器全都忙着,该原料就在该组机器处的一个服从先进先出FIFO(FirstInFirstOut)规则的队列。
前一天没有完成的任务,第二天继续加工。
在某机器上完成一个工序的时间服从Erlang分布,其平均值取决于原料的类别以及机器的组别。
例如,表11.1中的第2类原料,它的第一道工序是在第4组机器上加工,加工时间服从均值为66的Erlang分布。
3.概念模型
2.建立Flexsim模型
1.生成实体
从左边的实体库中拖动实体到模型(建模)视窗中。
具体操作是,点击并按住实体库中的实体,然后将它拖动到模型中想要放置的位置,放开鼠标键即可。
其中发生器代表三种不同产品的出发点,暂存区代表产品的临时存放区,处理器代表机器,吸收器代表成品库。
由于受临时实体数量的限制,该方案中一个处理器代表一组机器。
如图1所示。
图1
2.连接端口
要连接一个实体的输出端口至另一个实体的输入端口,按住键盘上的“A”键,然后点击第一个实体并按住鼠标左键,拖动鼠标到下一个实体然后放开鼠标键。
将会看到拖动出一条黄色连线,放开鼠标键时,会出现一条黑色的连线。
按照问题中不同产品的产品的加工流程,依次连接各实体。
如图2所示。
图2
3.定义发生器
在模型中,共有3个发生器实体,每个发生器对应一类原料,也就是说,一个Source生成一类原料。
第一类原料的到达间隔时间服从均值为50分钟的指数分布。
我们双击对应于第一类原料的那个发生器实体,打开其参数视窗。
保留其到达方式的默认选项“按时间间隔到达”,并且在到达时间间隔中选择指数分布,但是我们需要修改其参数,因此单击右侧的
按钮,出现参数修改视窗。
把尺度参数修改成50,其它按其默认值。
如图3所示。
图3
同样地,我们可以修改第二类原料和第三类原料的Source,使得其生成实体的到达间隔时间分别服从均值为30分钟和75分钟的指数分布。
三类原料进入系统后,为了方便各机器组能区分开不同的原料,我们需要给这三类原料相对应的实体不同的实体类型。
同时为了能在后续的仿真运行中更好的观察系统的行为和变化,可以赋予三类原料不同的颜色,方便我们直接从视觉上观察不同原料的加工状态。
这里我们简单将三类原料用红、黄、蓝三种颜色区分,其中第一类原料黑色,第二类原料红色,第三类原料黄色。
再次打开第一个发生器的参数视窗,选择发生触发器标签。
我们可以在生成流动实体时设置其类型,在其将要离开发生器时赋予颜色,这需要定义创建触发和离开触发选项。
首先我们来设置其实体类型。
单击创建触发下拉菜单,选择设置实体类型选项。
再打开其参数修改视窗,将其类型值改为1。
如图4所示。
图4
单击确定,关闭该参数修改窗口。
单击离开触发下拉菜单,选择设置实体颜色选项。
再打开其参数修改视窗,将其颜色改为黑色(black)。
如图5所示。
图5
单击确认,再以类似的方法定义发生器二和发生器三。
4.定义处理器
首先我们来定义机器的加工时间。
由问题可知,不同类型的原料在机器1上的加工时间不同,分别为均值是36分钟、48分钟、42分钟的Erlang分布。
由于方案中使用一个处理器代表一组机器,所以相应的加工时间也要缩短。
比如案例中有3台机器一,所以加工时间应变为均值是12分钟、16分钟、14分钟的Erlang分布。
双击第一类处理器,打开其参数窗口,单击处理时间选项的下拉菜单,选择“按临时实体类型(间接)”,打开其参数修改窗口,可以看到,可以针对不同的实体类型定义不同的加工时间。
按题意修改加工时间,如图6所示。
图6
接下来,定义机器的输出端口。
第1类原料从机器组1流向机器组2,第2类原料从机器组1流向机器组3,第2类原料从机器组1流向机器组4。
首先,查看一下机器组1的输出端口,右键单击机器,打开其属性窗口,选择常规标签。
单击OutputPorts,右侧将出现该机器输出端口所连接实体的列表。
可以看出,端口一是暂存区5,端口二是暂存区6,端口三是暂存区7,如图7所示。
图7
根据题意,产品一流向端口1,产品二流向端口2,产品三流向端口3。
打开该机器的参数窗口,选择临时实体流标签。
通过修改送往端口选项可以控制从该机器流出的实体所通过的输出端口。
同样的,我们是根据实体类型来区分输出端口的,单击送往端口下拉菜单,选择“按临时实体类型(间接)”选项。
打开其参数修改窗口,对应不同的实体类型,设置好不同的端口。
如图8所示。
图8
按照类似的方法,定义其它组的处理器。
5.定义暂存区
暂存区用来存放等待加工的原料,采用先进先出策略,而且暂存区没有容量限制,也就是说,只要是加工完了而又无法立即开始下一阶段加工的原料都可以存放在暂存区中。
Flexsim中,暂存区实体的默认出入规则就是先进先出,因此不需要设置。
但是其默认最大容量是10,由于我们不知道在模型运行过程中可能需要的容量是多少,因此我们将其最大容量改为一个大值.双击暂存区,打开其参数窗口,将最大容量一栏的值改为10000。
单击确定,关闭窗口。
对模型中所有的暂存区作相同的设置。
如图9所示。
图9
6.模型运行
该案例中需对系统进行365天的仿真运行(每天按8小时计算),计算每组机器队列中的平均产品数以及平均等待时间。
通过仿真运行,找出影响系统的瓶颈因素,对模型加以改进。
注意,在模型中,我们假设单位时间长度是1分钟,因此,需要运行的总时间长度是365×8×60=175200单位时间。
单击编译按钮,对模型进行编译。
编译完成后,单击重置按钮,重置模型。
最后单击运行按钮,开始仿真。
仿真进行过程中,可以看到黑、红、黄三种不同颜色的原料从系统中流过,经过不同机器组的加工,最后离开系统。
如图10所示。
当仿真运行到175200单位时间的时候,停止运行。
图10
7.数据分析
首先来查看机器组一的统计数据。
打开其机器组一前的暂存区属性窗口,选择统计标签。
该页面的内容一栏统计了暂存区内存放的待加工产品数量信息,而停留时间一栏统计了待加工产品在暂存区内等待时间信息。
图11是机器组11的暂存区的统计数据。
图11
再打开机器组一的处理器的属性窗口,选择统计标签中的状态分页,便可以看到该处理器的工作率和空闲率。
如图12所示。
图12
根据不同机器组的统计信息,我们可以得出各机器组处等待加工的产品的数量和等待时间以及工作率,如表1所示。
表1各机器组统计数据
机器组数
1
2
3
4
5
平均等待时间(分)
55.05
603.92
5.69
321.8
4.42
平均等待数量
3.6
19.68
0.37
14.81
0.14
工作率
94.3%
96.9%
71.1%
95.8%
78.1%
除此之外,还可以生成统计报表得到以上数据。
按住键盘“Shift”键然后用鼠标拖动一个选择框包围要报告的实体。
当一个实体被选中时,在它周围将显示一个红色方框。
选择了想要进行报告的实体后,选择菜单选项“统计>标准报告”。
选择了此选项后,将会看到StandardReportSetup(标准报告设置)视窗。
如图13所示。
图13
按生成报告可以生成一个基本报告,如图14所示。
图14
由表一可以发现,机器组2的暂存区中等待加工的产品数量大、等待时间长,我们可以认为这是整个加工系统的瓶颈,如果要提高整体产出率,那么首先需要对机器组2的进行改善。
其次,机器组3的工作率较低,也需要得到改善。
机器组1及4也许要一定的改善。
3.改善及结论
1.改善方案
由上面可知道,需要对整个车间的加工流水线系统进行改善,以使其到达一个平衡,确保各机器组的工作效率及缩短等待时间。
根据上面数据,首先对机器组2,3进行改善,机器组2的等待时间最长,说明机器不过用,在此增加一台2机器,由原来2台增为3台。
另外机器组3的工作率过低,说明生产能力过剩,在此减少一台机器3,由原来4台减为3台。
所以各机器的数量有一定变动,如表2所示。
表2改进后各机器组数量
机器组数
1
2
3
4
5
数量
3
3
3
3
1
接着来平衡流水线,由于方案中有一个处理器代表一组机器,根据问题中各机器的生产能力,再由各机器组的台数,转换成下表。
如表3所示。
表3各产品流程及相应时间
产品
生产流程
1
3
1
2
5
时间
10
12
17
30
2
4
1
3
时间
22
16
15
3
2
5
1
4
3
时间
24
15
14
18
20
假设分别生产一个产品1、产品2及产品3,各机器所需时间如下:
机器一:
12+16+14=42
机器二:
17+24=41
机器三:
10+15+20=45
机器四:
22+18=40
机器五;30+15=45
由上可知,各机器组的生产节拍在40到45左右,然而三种原料到达车间的间隔时间分别服从均值为50,30,75分钟的指数分布,所以导致流水线的不平衡。
我们可以改变的三种原料到达车间的间隔时间,以改变这种不平衡的现象。
考虑到机器的最大节拍为45,以及机器的工作率不可能为100%,我们把三种原料到达车间的间隔时间都改为服从均值为48分钟的指数分布。
首先修改模型中发生器的到达时间间隔,如图15所示。
图15
由于机器组2,3的数量有改变,所以相应的处理时间也需改变,如图16所示。
处理器3的数据也按类似方法改变。
图16
最后运行模型175200分钟,按上面数据分析中的方法打开各机器组暂存区及处理器的属性,得到各机器组处等待加工的产品的数量和等待时间以及工作率。
如表4所示。
表4改进后各机器组统计数据
机器组数
1
2
3
4
5
平均等待时间(分)
30.17
45.81
63.66
37.11
74.94
平均等待数量
1.85
1.88
3.91
1.52
3.08
工作率
86.0%
84.2%
92.2%
81.9%
92.4%
表1改进前各机器组统计数据
机器组数
1
2
3
4
5
平均等待时间(分)
55.05
603.92
5.69
321.8
4.42
平均等待数量
3.6
19.68
0.37
14.81
0.14
工作率
94.3%
96.9%
71.1%
95.8%
78.1%
2.结论
对比改进前后的统计数据,虽然存在个别机器组的等待时间变长及工作率降低的现象出现,但整个车间机器组的等待时间及等待数量相对平衡,不存在机器组与机器组间差别很大的现象,还有就是整体的工作率得到提高。
所以说,改进的方案是有效的,它使整个车间流水线系统变得更加平衡,效率更加高。