热处理说明11.docx
《热处理说明11.docx》由会员分享,可在线阅读,更多相关《热处理说明11.docx(12页珍藏版)》请在冰豆网上搜索。
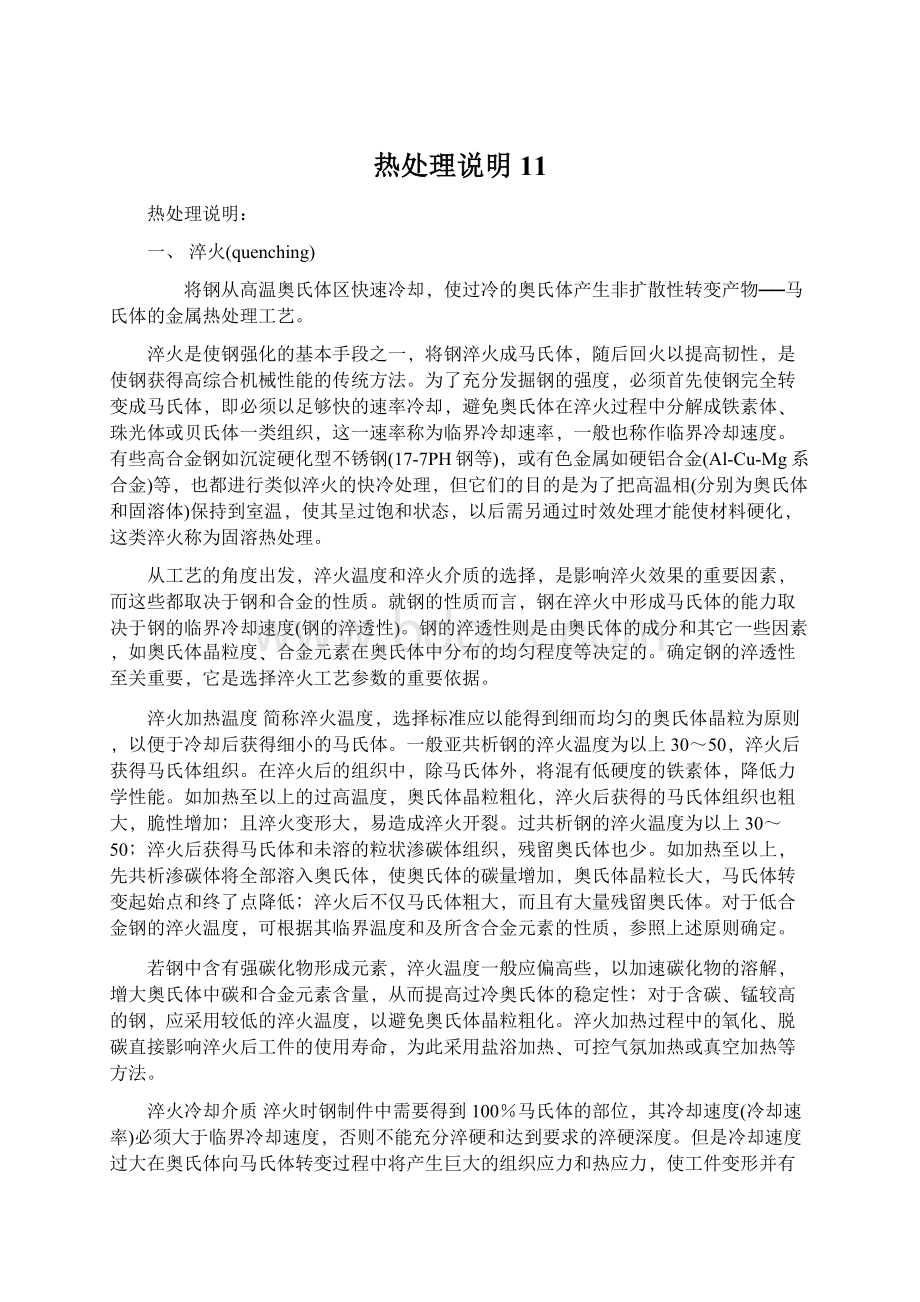
热处理说明11
热处理说明:
一、淬火(quenching)
将钢从高温奥氏体区快速冷却﹐使过冷的奥氏体产生非扩散性转变产物──马氏体的金属热处理工艺。
淬火是使钢强化的基本手段之一﹐将钢淬火成马氏体﹐随后回火以提高韧性﹐是使钢获得高综合机械性能的传统方法。
为了充分发掘钢的强度﹐必须首先使钢完全转变成马氏体﹐即必须以足够快的速率冷却﹐避免奥氏体在淬火过程中分解成铁素体﹑珠光体或贝氏体一类组织﹐这一速率称为临界冷却速率﹐一般也称作临界冷却速度。
有些高合金钢如沉淀硬化型不锈钢(17-7PH钢等)﹐或有色金属如硬铝合金(Al-Cu-Mg系合金)等﹐也都进行类似淬火的快冷处理﹐但它们的目的是为了把高温相(分别为奥氏体和固溶体)保持到室温﹐使其呈过饱和状态﹐以后需另通过时效处理才能使材料硬化﹐这类淬火称为固溶热处理。
从工艺的角度出发﹐淬火温度和淬火介质的选择﹐是影响淬火效果的重要因素﹐而这些都取决于钢和合金的性质。
就钢的性质而言﹐钢在淬火中形成马氏体的能力取决于钢的临界冷却速度(钢的淬透性)。
钢的淬透性则是由奥氏体的成分和其它一些因素﹐如奥氏体晶粒度﹑合金元素在奥氏体中分布的均匀程度等决定的。
确定钢的淬透性至关重要﹐它是选择淬火工艺参数的重要依据。
淬火加热温度简称淬火温度﹐选择标准应以能得到细而均匀的奥氏体晶粒为原则﹐以便于冷却后获得细小的马氏体。
一般亚共析钢的淬火温度为以上30~50﹐淬火后获得马氏体组织。
在淬火后的组织中﹐除马氏体外﹐将混有低硬度的铁素体﹐降低力学性能。
如加热至以上的过高温度﹐奥氏体晶粒粗化﹐淬火后获得的马氏体组织也粗大﹐脆性增加﹔且淬火变形大﹐易造成淬火开裂。
过共析钢的淬火温度为以上30~50﹔淬火后获得马氏体和未溶的粒状渗碳体组织﹐残留奥氏体也少。
如加热至以上﹐先共析渗碳体将全部溶入奥氏体﹐使奥氏体的碳量增加﹐奥氏体晶粒长大﹐马氏体转变起始点和终了点降低﹔淬火后不仅马氏体粗大﹐而且有大量残留奥氏体。
对于低合金钢的淬火温度﹐可根据其临界温度和及所含合金元素的性质﹐参照上述原则确定。
若钢中含有强碳化物形成元素﹐淬火温度一般应偏高些﹐以加速碳化物的溶解﹐增大奥氏体中碳和合金元素含量﹐从而提高过冷奥氏体的稳定性﹔对于含碳﹑锰较高的钢﹐应采用较低的淬火温度﹐以避免奥氏体晶粒粗化。
淬火加热过程中的氧化﹑脱碳直接影响淬火后工件的使用寿命﹐为此采用盐浴加热﹑可控气氛加热或真空加热等方法。
淬火冷却介质淬火时钢制件中需要得到100%马氏体的部位﹐其冷却速度(冷却速率)必须大于临界冷却速度﹐否则不能充分淬硬和达到要求的淬硬深度。
但是冷却速度过大在奥氏体向马氏体转变过程中将产生巨大的组织应力和热应力﹐使工件变形并有开裂的危险。
为了解决上述矛盾﹐钢的合理的淬火冷却过程通常要求在珠光体转变区或贝氏体转变区等奥氏体最不稳定区域要快速冷却﹐以防止其分解﹐通过马氏体转变区域要较缓慢冷却﹐以减小奥氏体转变马氏体时出现的应力。
实际生产中可根据钢种的特性选择冷却介质﹐如碳钢的临界冷却速度大﹐应选用水﹑盐水等冷却能力较强的介质﹔合金钢的临界冷却速度小﹐可采用比较缓和的介质如油等。
由表内常用淬火介质的冷却速度可以看到﹐水在200~300区域的冷却速度过大﹐易于使钢淬裂﹔油在550~650区间的冷速过小﹐不易使淬透性小的钢淬硬。
近年来广泛研究采用冷却能力介于水和油之间的冷却介质﹐使高温区的冷却能力接近于水﹐低温区的冷却能力接近于油﹐如水玻璃﹑过饱和硝酸水溶液﹑聚乙烯醇溶液等。
钢的淬透性淬透性是钢的基本性质之一。
它不同于淬硬性﹐后者指马氏体的硬度值﹐主要决定于钢中含碳量。
淬透性的大小是用理想临界直径作为指标来衡量的﹐它是钢棒在冷却烈度(见后文)为∞的介质中冷却时﹐心部形成50%马氏体时的直径。
在其它淬火介质(如水﹑油等)中冷却时﹐所得到的临界直径均较为小。
其中50%马氏体转变量是为了便于测量而人为选定的﹐可通过金相检验和硬度测量确定。
马氏体含量不同时碳含量对淬火硬度的影响中的曲线表示硬化层中含有不同百分数的马氏体时的硬度值和含碳量的关系。
一定尺寸的圆棒淬火时﹐表面和心部的冷却速度不同。
很明显﹐淬透层的深度取决于临界冷却速度的大小﹐因而可通过加入合金元素来降低钢的临界冷却速度﹐使钢的淬透层深度增加。
最常用的确定钢的淬透性方法是顶端淬火试验。
顶端淬火试验或称Jominy试验﹐是一种测定淬透性的简便方法﹐在许多国家已标准化。
利用顶端淬火法测定淬透性曲线是用标准试样经适当奥氏体化后进行顶端淬火的示意图。
顶端淬火时冷却速度由淬火端沿试棒逐渐减小﹐组织和硬度随之相应地变化﹐由此得到的硬度变化曲线,称为淬透性曲线或Jominy曲线。
严格地说﹐这种曲线只对某一炉次的钢有效﹔对于某一定钢种来说﹐由于化学成分的差异(成分波动及偏析)﹑预先热处理工艺的差异(显微组织上的差异)﹐其淬透性曲线可在相当大的范围内波动﹐形成一个淬透性带(Jominy带)。
工业用钢的淬透性曲线几乎都已测定﹐并汇集成册供查阅参考。
根据Jominy试验结果﹐钢的淬透性大小可通过以下途径确定﹕
直接用试棒顶端至半马氏体区的距离。
用临界直径表示临界直径指钢在一定冷却介质(如油或水)中淬火时能淬透(中心形成50%马氏体)的最大直径﹐生产中常用以表示淬透性的大小﹐不同冷却介质下的临界直径(中心形成50%马氏体)为其示意图。
可以从不同直径的钢棒由试验得到﹐称格罗斯曼(Grossmann)法﹐也可在用顶端淬火试验得出后﹐利用由淬透性曲线换算为钢棒截面上淬透层深度的曲线查出的某种介质中淬火时的临界直径。
用理想临界直径表示临界直径虽然可以在规定介质条件下对钢的淬透性进行定量比较﹐但仍缺乏普遍意义﹐因为当淬火介质改变时﹐虽然钢的淬透性并不改变﹐但工件的淬透直径却发生变化。
为了定量地表示冷却介质的冷却能力而引入了冷却烈度﹐静止水的烈度规定为1﹐以作为和其它淬火介质比较的标准﹔理想淬火介质(淬火时使热的试棒表面立即冷到介质温度)的值为无穷大﹔一些常用实际淬火介质的值分别为0.02~5不等。
这样﹐钢的淬透性可以简便地用理想临界直径加以表示和进行比较。
对于某一定成分的钢﹐表示一个圆柱形棒在理想淬火条件下﹐中心形成50%马氏体时的直径。
奥氏体晶粒度和化学成分对淬透性的影响奥氏体晶粒度和化学成分是影响淬透性最重要的两个因素。
钢的淬透性随奥氏体晶粒度增大和晶粒介面积减小而提高﹐这是因为可供铁素体和珠光体形核的位置减少﹐延缓了这些转变的速度。
钢中合金元素一般延缓奥氏体分解﹐使转变曲线(TTT曲线或CCT曲线)右移﹐从而提高淬透性。
为了定量估算它们的影响曾经提出一些计算方法﹐如格罗斯曼(M.A.Grossmann)和霍洛曼(J.H.Holloman)所提出的公式﹐经莫泽尔(A.Moser)和莱格特(A.Legat)改进后得到的计算理想临界直径的经验公式为﹕
=×2.21%Mn×1.40%Si×2.13%Cr×3.275%Mo×1.47%Ni
其中为基本临界直径﹐主要决定于奥氏体的含碳量和晶粒度﹐可由图10含碳量和晶粒度对基本临界直径的影响查出﹔列于各元素前面的数字是该元素含量(重量)为1%时的淬透性系数﹐数值越大﹐表示对淬透性的贡献越大。
这样的计算只能用作对淬透性的粗略估算。
淬透性和淬火工艺为了保证工件淬火时得到完全马氏体组织﹐一般来说要求选用的钢有足够的淬透性。
如淬透性不同的钢棒淬火并高温回火处理后的力学性能所示﹐完全淬透的钢高温回火后﹐其力学性能沿截面是均匀的﹔如因钢的淬透性低而使心部未能淬透﹐则心部的力学性能特别是冲击韧性较低。
对于给定成分的钢﹐选用烈度高的淬火介质可以更快地降低钢件表面温度﹐增大临界直径。
但这将增大温度梯度﹐引起工件翘曲变形﹐甚至开裂。
因此在实际淬火操作中往往需要采用较缓和的冷却介质﹐如油或空气流等。
这就要求钢有高的淬透性。
能在空气中冷却形成马氏体的钢称为空硬钢﹐如一些高合金模具钢。
对中等淬透性的钢已发展出各种间断淬火方法。
某些情况下并不要求工件完全淬透﹐如工具和有些机器部件往往希望高疲劳强度或耐磨的硬表面。
表面层淬成马氏体而心部不淬透使表面层中产生压应力﹐有利于防止疲劳裂纹的形成和阻止在表面所形成的疲劳源的扩展。
二、回火(tempering)
将经过淬火的工件重新加热到低于下临界温度的适当温度﹐保温一段时间后在空气或水﹑油等介质中冷却的金属热处理。
钢铁工件在淬火后具有以下特点﹕得到了马氏体﹑贝氏体﹑残余奥氏体(见钢铁显微组织)等不平衡(即不稳定)组织﹔存在较大内应力﹔力学性能不能满足要求。
因此﹐钢铁工件淬火后一般都要经过回火。
作用回火的作用在于﹕提高组织稳定性﹐使工件在使用过程中不再发生组织转变﹐从而使工件几何尺寸和性能保持稳定﹔消除内应力﹐以便改善工件的使用性能并稳定工件几何尺寸﹔调整钢铁的力学性能以满足使用要求。
回火之所以具有这些作用﹐是因为温度升高时﹐原子活动能力增强﹐钢铁中的铁﹑碳和其它合金元素的原子可以较快地进行扩散﹐实现原子的重新排列组合﹐从而使不稳定的不平衡组织逐步转变为稳定的平衡组织。
内应力的消除还与温度升高时金属强度降低有关。
一般钢铁回火时﹐硬度和强度下降﹐塑性提高。
回火温度越高﹐这些力学性能的变化越大。
有些合金元素含量较高的合金钢﹐在某一温度范围回火时﹐会析出一些颗粒细小的金属化合物﹐使强度和硬度上升。
这种现象称为二次硬化。
要求用途不同的工件应在不同温度下回火﹐以满足使用中的要求。
刀具﹑轴承﹑渗碳淬火零件﹑表面淬火零件通常在250℃以下进行低温回火。
低温回火后硬度变化不大﹐内应力减小﹐韧性稍有提高。
弹簧在350~500℃下中温回火﹐可获得较高的弹性和必要的韧性。
中碳结构钢制作的零件通常在500~600℃进行高温回火﹐以获得适宜的强度与韧性的良好配合﹐淬火加高温回火的热处理工艺总称为调质。
钢在300℃左右回火时﹐常使其脆性增大﹐这种现象称为第一类回火脆性。
一般不应在这个温度区间回火。
某些中碳合金结构钢在高温回火后﹐如果缓慢冷至室温﹐也易于变脆。
这种现象称为第二类回火脆性。
在钢中加入钼﹐或回火时在油或水中冷却﹐都可以防止第二类回火脆性。
将第二类回火脆性的钢重新加热至原来的回火温度﹐便可以消除这种脆性。
三、退火(annealing)
将金属缓慢加热到一定温度﹐保持足够时间﹐然后以适宜速度冷却(通常是缓慢冷却﹐有时是控制冷却)的一种金属热处理工艺。
目的是使经过铸造﹑锻轧﹑焊接或切削加工的材料或工件软化﹐改善塑性和韧性﹐使化学成分均匀化﹐去除残余应力﹐或得到预期的物理性能。
退火工艺随目的之不同而有多种﹐如重结晶退火﹑等温退火﹑均匀化退火﹑球化退火﹑去除应力退火﹑再结晶退火﹐以及稳定化退火﹑磁场退火等等。
退火的一个最主要工艺参数是最高加热温度(退火温度)﹐大多数合金的退火加热温度的选择是以该合金系的相图为基础的﹐如碳素钢以铁碳平衡图为基础。
各种钢(包括碳素钢及合金钢)的退火温度﹐视具体退火目的的不同而在各该钢种的以上﹑以上或以下的某一温度。
各种非铁合金的退火温度则在各该合金的固相线温度以下﹑固溶度线温度以上或以下的某一温度。
重结晶退火应用于平衡加热和冷却时有固态相变(重结晶)发生的合金。
其退火温度为各该合金的相变温度区间以上或以内的某一温度。
加热和冷却都是缓慢的。
合金于加热和冷却过程中各发生一次相变重结晶﹐故称为重结晶退火﹐常被简称为退火。
这种退火方法﹐相当普遍地应用于钢。
钢的重结晶退火工艺是﹕缓慢加热到(亚共析钢)或(共析钢或过共析钢)以上30~50﹐保持适当时间﹐然后缓慢冷却下来。
通过加热过程中发生的珠光体(或者还有先共析的铁素体或渗碳体)转变为奥氏体(第一回相变重结晶)以及冷却过程中发生的与此相反的第二回相变重结晶﹐形成晶粒较细﹑片层较厚﹑组织均匀的珠光体(或者还有先共析铁素体或渗碳体)﹐退火温度在以上(亚共析钢)使钢发生完全的重结晶者﹐称为完全退火﹐退火温度在与之间(亚共析钢)或与之间(过共析钢)﹐使钢发生部分的重结晶者﹐称为不完全退火。
前者主要用于亚共析钢的铸件﹑锻轧件﹑焊件﹐以消除组织缺陷(如魏氏组织﹑带状组织等)﹐使组织变细和变均匀﹐以提高钢件的塑性和韧性。
后者主要用于中碳和高碳钢及低合金结构钢的锻轧件。
此种锻﹑轧件若锻﹑轧后的冷却速度较大时﹐形成的珠光体较细﹑硬度较高﹔若停锻﹑停轧温度过低﹐钢件中还有大的内应力。
此时可用不完全退火代替完全退火﹐使珠光体发生重结晶﹐晶粒变细﹐同时也降低硬度﹐消除内应力﹐改善被切削性。
此外﹐退火温度在与之间的过共析钢球化退火﹐也是不完全退火。
重结晶退火也用于非铁合金﹐例如钛合金于加热和冷却时发生同素异构转变﹐低温为相(密排六方结构)﹐高温为相(体心立方结构)﹐其中间是“+”两相区﹐即相变温度区间。
为了得到接近平衡的室温稳定组织和细化晶粒﹐也进行重结晶退火﹐即缓慢加热到高于相变温度区间不多的温度﹐保温适当时间﹐使合金转变为相的细小晶粒﹔然后缓慢冷却下来﹐使相再转变为相或+两相的细小晶粒。
等温退火应用于钢和某些非铁合金如钛合金的一种控制冷却的退火方法。
对钢来说﹐是缓慢加热到(亚共析钢)或(共析钢和过共析钢)以上不多的温度﹐保温一段时间﹐使钢奥氏体化﹐然后迅速移入温度在以下不多的另一炉内﹐等温保持直到奥氏体全部转变为片层状珠光体(亚共析钢还有先共析铁素体﹔过共析钢还有先共析渗碳体)为止﹐最后以任意速度冷却下来(通常是出炉在空气中冷却)。
等温保持的大致温度范围在所处理钢种的等温转变图上至珠光体转变鼻尖温度这一区间之内﹔具体温度和时间﹐主要根据退火后所要求的硬度来确定。
等温温度不可过低或过高﹐过低则退火后硬度偏高﹔过高则等温保持时间需要延长。
钢的等温退火的目的﹐与重结晶退火基本相同﹐但工艺操作和所需设备都比较复杂﹐所以通常主要是应用于过冷奥氏体在珠光体型相变温度区间转变相当缓慢的合金钢。
后者若采用重结晶退火方法﹐往往需要数十小时﹐很不经济﹔采用等温退火则能大大缩短生产周期﹐并能使整个工件获得更为均匀的组织和性能。
等温退火也可在钢的热加工的不同阶段来用﹐例如﹐若让空冷淬硬性合金钢由高温空冷到室温时﹐当心部转变为马氏体之时﹐在已发生了马氏体相变的外层就会出现裂纹﹔若将该类钢的热钢锭或钢坯在冷却过程中放入700左右的等温炉内﹐保持等温直到珠光体相变完成后﹐再出炉空冷﹐则可免生裂纹。
含相稳定化元素较高的钛合金﹐其相相当稳定﹐容易被过冷。
过冷的相﹐其等温转变动力学曲线与钢的过冷奥氏体等温转变图相似。
为了缩短重结晶退火的生产周期并获得更细﹑更均匀的组织﹐亦可采用等温退火。
均匀化退火亦称扩散退火。
应用于钢及非铁合金(如锡青铜﹑硅青铜﹑白铜﹑镁合金等)的铸锭或铸件的一种退火方法。
将铸锭或铸件加热到各该合金的固相线温度以下的某一较高温度﹐长时间保温﹐然后缓慢冷却下来。
均匀化退火是使合金中的元素发生固态扩散﹐来减轻化学成分不均匀性(偏析)﹐主要是减轻晶粒尺度内的化学成分不均匀性(晶内偏析或称枝晶偏析)。
均匀化退火温度所以如此之高﹐是为了加快合金元素扩散﹐尽可能缩短保温时间。
合金钢的均匀化退火温度远高于﹐通常是1050~1200。
非铁合金锭进行均匀化退火的温度一般是“0.95×固相线温度(K)”﹐均匀化退火因加热温度高﹐保温时间长﹐所以热能消耗量大。
球化退火只应用于钢的一种退火方法。
将钢加热到稍低于或稍高于的温度或者使温度在上下周期变化﹐然后缓冷下来。
目的在于使珠光体内的片状渗碳体以及先共析渗碳体都变为球粒状﹐均匀分布于铁素体基体中(这种组织称为球化珠光体)。
具有这种组织的中碳钢和高碳钢硬度低﹑被切削性好﹑冷形变能力大。
对工具钢来说﹐这种组织是淬火前最好的原始组织。
球化退火的具体工艺有﹕普通(缓冷)球化退火﹐缓冷适用于多数钢种﹐尤其是装炉量大时﹐操作比较方便﹐但生产周期长﹔等温球化退火﹐适用于多数钢种﹐特别是难于球化的钢以及球化质量要求高的钢(如滚动轴承钢)﹔其生产周期比普通球化退火短﹐不过需要有能够控制共析转变前冷却速率的炉子﹔周期球化退火﹐适用于原始组织为片层状珠光体组织的钢﹐其生产周期也比普通球化退火短﹐不过在设备装炉量大的条件下﹐很难按控制要求改变温度﹐故在生产中未广泛采用﹔低温球化退火﹐适用于经过冷形变加工的钢以及淬火硬化过的钢(后者通常称为高温软化回火)﹔形变球化退火﹐形变加工对球化有加速作用﹐将形变加工与球化结合起来﹐可缩短球化时间。
它适用于冷﹑热形变成形的钢件和钢材(如带材
再结晶退火应用于经过冷变形加工的金属及合金的一种退火方法。
目的为使金属内部组织变为细小的等轴晶粒﹐消除形变硬化﹐恢复金属或合金的塑性和形变能力(回复和再结晶)。
若欲保持金属或合金表面光亮﹐则可在可控气氛的炉中或真空炉中进行再结晶退火。
去除应力退火铸﹑锻﹑焊件在冷却时由于各部位冷却速度不同而产生内应力﹐金属及合金在冷变形加工中以及工件在切削加工过程中也产生内应力。
若内应力较大而未及时予以去除﹐常导致工件变形甚至形成裂纹。
去除应力退火是将工件缓慢加热到较低温度(例如﹐灰口铸铁是500~550﹐钢是500~650)﹐保温一段时间﹐使金属内部发生弛豫﹐然后缓冷下来。
应该指出﹐去除应力退火并不能将内应力完全去除﹐而只是部分去除﹐从而消除它的有害作用。
还有一些专用退火方法﹐如不锈耐酸钢稳定化退火﹔软磁合金磁场退火﹔硅钢片氢气退火﹔可锻铸铁可锻化退火等
热处理设备
※电热炉
电热炉可使用金属发热体或非金属发热体来产生热源,其构造简单,用途十分广泛是它的主要特色,可广泛应用于退火、正常化、淬火、回火、渗碳及渗碳氮化等。
主要的金属发热体包括Ni-Cr电热线(最常见,最高用至1200℃)、Mo-Si合金及W、Mo等纯金属;非金属发热体包括SiC(最常见,最高可加热至1600℃)、LaCrO3及石墨棒(真空或保护气氛下可加热至2000℃)。
※燃烧炉
燃烧炉使用气体燃料或液体燃料作为加热源,热处理温度可达800℃至1200℃之间。
常见的气体燃料包括天然气、液化石油气及瓦斯等;液体燃料则包括重油、灯油及轻油等。
燃烧炉的热对流效果很好,特别是低温加热之均匀性甚佳;但燃烧炉容易产生燃烧噪音、尘粒、硫氧化物及氮氧化物等环境污染物,则是它的主要缺点。
※盐浴炉
盐浴炉设备便宜,加热速度快,处理件表面氧化程度低,适合小型工件热处理用。
若配合适当的盐裕,可应用于淬火加热、渗碳、渗氮、渗硫等表面处理。
常用的盐浴种类包括
(1)使用于200℃至500℃的低温盐主要以硝酸盐或亚硝酸盐;
(2)使用在450℃至950℃间的中温盐,主要以氯化钠、氯化钙及碳酸钠的混合盐;(3)使用在950℃至1250℃温度范围的高温盐则大多以氯化钡盐为主。
※气氛炉
气氛炉系在气密的炉体内,通入适当的气氛进行各项辉面热处理、渗碳、渗碳氮化及烧结等处理。
此类炉具可分为分批式及连续式两大类,加热形式则使用电热、油或燃气在加热管内燃烧以进行间接式加热。
※真空炉
在真空中加热工件进行各项热处理之炉具称为真空炉,一般的真空度在10-2至10-4mmHg左右,经由真空炉热处理之工件,可防止钢材表面氧化、脱碳,具有较佳的表面质量。
具有冷却装置的真空炉,可在非活性气体中冷却或淬火油中进行油淬火,但随着工件体积的增大,使得热处理成本会大幅增加。
※高周波热处理装置
高周波热处理装置主要是利用感应电流在工件必要的表面部分加热,并进行必要的淬火、回火等热处理程序,以获得表面硬度大而工件心部韧性佳的表面特性。
装置主要包括高频产生器、加热线圈及工件运动夹持机构。
感应加热的加热效率甚高,能在极短的时间内加热至高温,并获得极佳的硬化层;唯此种热处理技术会受到工件形状的影响较大,并不是每个工件都适用高周波热处理技术。
※流动床
流动床体的基本原理系利用流动的固体微粒(如氧化铝粉、砂粒)进行加热或冷却,它具有高传热速率(加热速度约为一般热辐射传导的8倍)及表面清洁作用等双重优点,可使用于正常化、退火、淬火、沃斯回火及麻回火等热处理程序。
※钢铁之热处理
※均质退火处理
简称均质化处理(Homogenization),系利用在高温进行长时间加热,使内部的化学成分充分扩散,因此又称为『扩散退火』。
加热温度会因钢材种类有所差异,大钢锭通常在1200℃至1300℃之间进行均质化处理,高碳钢在1100℃至1200℃之间,而一般锻造或轧延之钢材则在1000℃至1200℃间进行此项热处理。
※完全退火处理
完全退火处理系将亚共析钢加热至Ac3温度以上30~50℃、过共析钢加热至Ac1温度以上50℃左右的温度范围,在该温度保持足够时间,使成为沃斯田体单相组织(亚共析钢)或沃斯田体加上雪明碳体混合组织后,在进行炉冷使钢材软化,以得到钢材最佳之延展性及微细晶粒组织。
※球化退火处理
球化退火主要的目的,是希望藉由热处理使钢铁材料内部的层状或网状碳化物凝聚成为球状,使改善钢材之切削性能及加工塑性,特别是高碳的工具钢更是需要此种退火处理。
常见的球化退火处理包括:
(1)在钢材A1温度的上方、下方反复加热、冷却数次,使A1变态所析出的雪明碳铁,继续附着成长在上述球化的碳化物上;
(2)加热至钢材A3或Acm温度上方,始碳化物完全固溶于沃斯田体后急冷,再依上述方法进行球化处理。
使碳化物球化,尚可增加钢材的淬火后韧性、防止淬裂,亦可改善钢材的淬火回火后机械性质、提高钢材的使用寿命。
※软化退火处理
软化退火热处理的热处理程序是将工件加热到600℃至650℃范围内(A1温度下方),维持一段时间之后空冷,其主要目的在于使以加工硬化的工件再度软化、回复原先之韧性,以便能再进一步加工。
此种热处理方法常在冷加工过程反复实施,故又称之为制程退火。
大部分金属在冷加工后,材料强度、硬度会随着加工量渐增而变大,也因此导致材料延性降低、材质变脆,若需要再进一步加工时,须先经软化退火热处理才能继续加工。
※弛力退火处理
弛力退火热处理主要的目的,在于清除因锻造、铸造、机械加工或焊接所产生的残留应力,这种残存应力常导致工件强度降低、经久变形,并对材料韧性、延展性有不良影响,因此弛力退火热处理对于尺寸经度要求严格的工件、有安全顾虑的机械构件事非常重要的。
弛力退火的热处理程序系将工件加热到A1点以下的适当温度,保持一段时间(不需像软化退火热处理那么久)后,徐缓冷却至室温。
特别需要注意的是,加热时的速度要缓慢,尤其是大型对象或形状复杂的工件更要特别注意,否则弛力退火的成效会大打折扣。
※正常化处理
正常化热处理有两个重要的功用,一是使工件结晶粒微细化而改善材料机械性质;另一个目的是调节轧延或铸造组织中碳化物的大小或分布状态,以利后续热处理时碳化物容易固溶于材质,以便提升材料切削性,并使材质均匀化。
正常化热处理的热处理程序,系将工件加热至A3(亚共析钢)或Acm(过共析钢)点温度以上30℃至60℃的高温(此即为正常化温度)保持一段时间,材质成为均匀沃斯田体后,静置于空气中使之冷却。
正常化时间的估算,可以每25mm厚度持温30分钟来估算需持温时间。
正常化热处理又可分为二段正常化、恒温正常化及二次正常化等多种改良式正常化热处理。
※淬火处理
淬火处理的主要目的是将钢材急速冷却以便获得硬度极大的麻田散体组织。
钢的淬火处理有三个要件,缺一不可,分别是:
(1)在沃斯田体区域内加热一段时间(即沃斯田体化);
(2)冷却时要能避开Ar’(波来体)变态;及(3)使钢材产生麻田散体或变韧体而硬化。
淬火处理可分为两个程序来实施,一是加热;一是冷却。
通常加热温度又称为淬火温度或沃斯田体化温度,依热处理钢材的不同而有所差异。
亚共析钢的淬火温度在Ac3温度以上30℃至60℃范围内,共析钢及过共析钢的淬火温度则是加热至Ac1温度以上30℃至60℃温度范围内。
冷却时要分两个阶段来冷却,钢从加热炉取