零件分析与工艺规程的设计.docx
《零件分析与工艺规程的设计.docx》由会员分享,可在线阅读,更多相关《零件分析与工艺规程的设计.docx(10页珍藏版)》请在冰豆网上搜索。
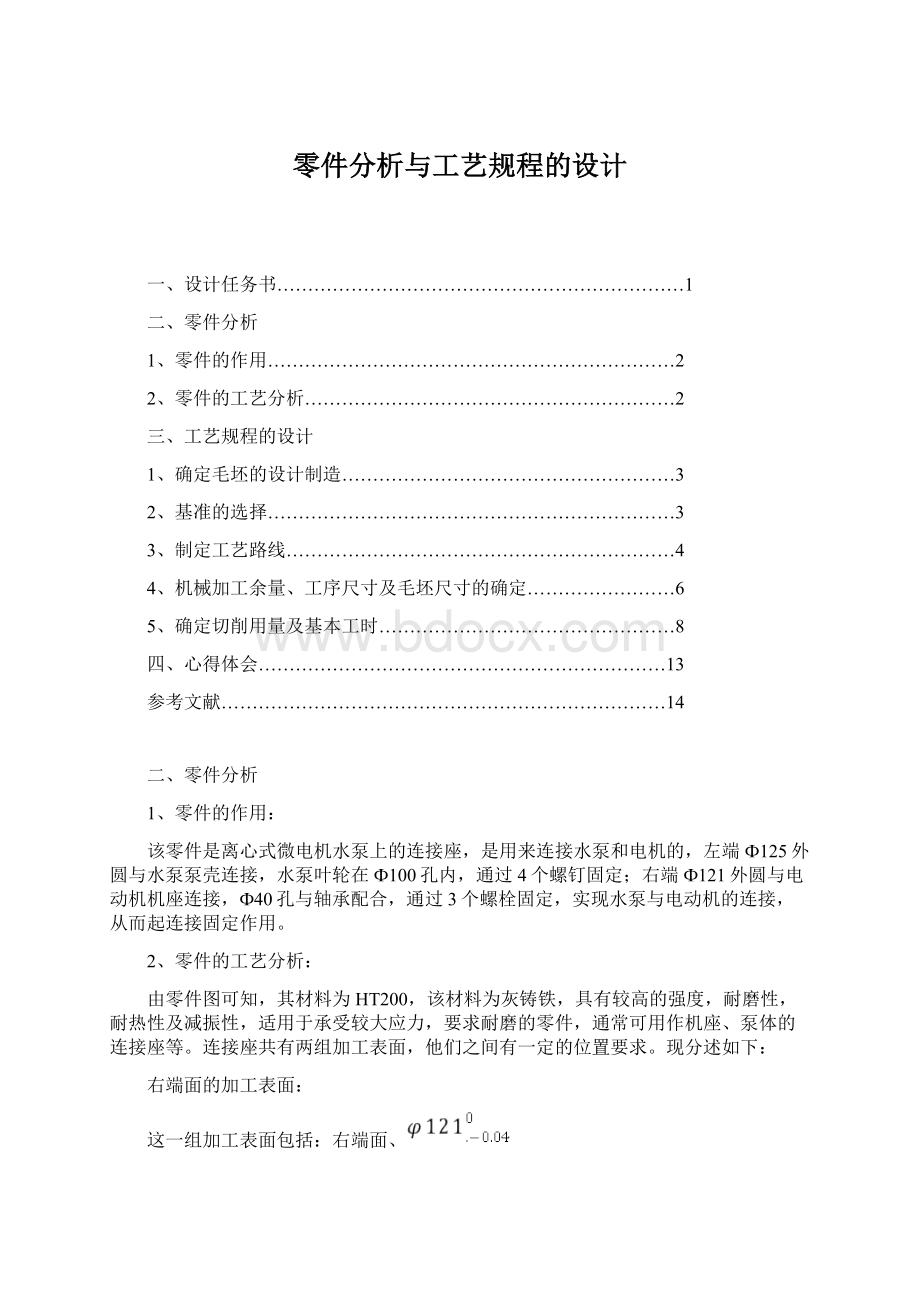
零件分析与工艺规程的设计
一、设计任务书…………………………………………………………1
二、零件分析
1、零件的作用…………………………………………………………2
2、零件的工艺分析……………………………………………………2
三、工艺规程的设计
1、确定毛坯的设计制造………………………………………………3
2、基准的选择…………………………………………………………3
3、制定工艺路线………………………………………………………4
4、机械加工余量、工序尺寸及毛坯尺寸的确定……………………6
5、确定切削用量及基本工时…………………………………………8
四、心得体会…………………………………………………………13
参考文献………………………………………………………………14
二、零件分析
1、零件的作用:
该零件是离心式微电机水泵上的连接座,是用来连接水泵和电机的,左端Ф125外圆与水泵泵壳连接,水泵叶轮在Ф100孔内,通过4个螺钉固定;右端Ф121外圆与电动机机座连接,Ф40孔与轴承配合,通过3个螺栓固定,实现水泵与电动机的连接,从而起连接固定作用。
2、零件的工艺分析:
由零件图可知,其材料为HT200,该材料为灰铸铁,具有较高的强度,耐磨性,耐热性及减振性,适用于承受较大应力,要求耐磨的零件,通常可用作机座、泵体的连接座等。
连接座共有两组加工表面,他们之间有一定的位置要求。
现分述如下:
右端面的加工表面:
这一组加工表面包括:
右端面、
的外圆,粗糙度为3.2、6.3;外径为Ф50、内径为
的小凸台,粗糙度为3.2,带有倒角;Ф32的小凹槽,粗糙度为25;钻17.5的中心孔,钻Ф7的通孔。
其加工工序采取先粗车——半精车——精车。
其中Ф17.5、
的孔或内圆直接在车床上进行粗镗——半精镗,
的内圆的半精镗的基础上再精镗就可以了。
左端的加工表面:
这一组加工表面包括:
左端面,
外圆粗糙度为3.2,
内圆,倒角,钻通孔Ф7,钻孔并攻丝。
端面有6.3的粗糙度要求,
的内圆孔有25的粗糙度要求。
采用的工序为粗车——半精车——精车。
孔加工为钻孔—扩钻—扩孔。
该零件上的主要加工面是
的孔,
的外圆和
的外圆。
孔的尺寸精度直接影响连接座与轴承的配合精度,
的尺寸精度直接影响连接座与水泵的接触精度和密封性,
的尺寸精度直接影响连接座与电机的接触精度和密封性。
由参考文献【1】中有关和孔加工的经济加工精度及机床能达到的位置精度可知,上要求是可以达到的。
零件的结构工艺性也是可行的。
三、工艺规程的设计
1、确定毛坯的设计制造:
零件的材料为HT200,应采用铸件,由于零件为中批生产,其轮廓尺寸也不大。
故可采用铸造成型。
这对提高生产率,保证加工质量也是有利的。
2、基准的选择:
基面选择是工艺规程设计中的重要工作之一。
基面选择得正确与合理可以使加工质量得到保证,生产率得以提高。
否则,加工工艺过程中回问题百出,更有甚者,还会造成零件的大批报废,是生产无法正常进行。
(1)粗基准的选择:
对于一般零件以不加工表面作为粗基准是完全合理的。
而对有若干个不加工表面的工件,则应以与加工表面要求相对位置精度较高的不加工表面作粗基准。
根据这个基准选择原则,再结合零件,选择Ф50的外圆做为粗基准。
(2)精基准的选择:
精基准的选择主要应该考虑重合的问题在工艺过程中的具体选择。
当设计基准与工序基准不重合时,应该进行尺寸换算。
用自为基准原则,选择Ф125的外圆表面做为精基准。
3、制定工艺路线:
制定工艺路线的出发点,应当是使零件的几何形状、尺寸精度及位置精度等技术要求能得到合理的保证,在生产纲领已确定的情况下,可以考虑采用万能性机床配以专用夹具,并尽量使工序集中来提高生产率。
除此之外,还应当考虑经济效果,以便使生产成本尽量下降。
(1)工艺路线方案一:
1.粗车右端面
2.粗车、半精车、精车外圆Ф121
3.粗车、半精车右台阶面
4.粗车、半精车外圆Ф130
5.粗车端面Ф50
6.钻Ф17.5的通孔
7.粗镗、半精镗、精镗Ф40的内孔
8.粗镗Ф32的凹槽深1mm
9粗车左端面
10粗车、半精车、精车外圆Ф125
11粗车、半精车左台阶面
12.粗车、半精车外圆Ф138
13.粗车Ф95的内孔
14.粗车Ф100的内圆台阶
15钻3—Ф7的通孔
16钻6—Ф7的通孔,钻Ф4的孔深12mm攻螺纹M5深12mm
17粗磨、精磨Ф125h6的外圆,靠Ф138的大端面
18粗磨、精磨Ф121h7的外圆,靠Ф130的大端面
(2)工艺路线方案二:
1.粗车左端面
2.粗车、半精车、精车外圆Ф125
3.粗车、半精车左台阶面
4.粗车、半精车外圆Ф138
5.粗车Ф95的内孔6.粗车、半精车、精车Ф100的内圆台阶
6.粗车右端面
7.粗车、半精车、精车外圆Ф121
8.粗车、半精车右台阶面4.粗车、半精车外圆Ф130
9.粗车端面Ф50
10.钻Ф17.5的通孔
11.粗镗、半精镗、精镗Ф40的内孔
12.粗镗Ф32的凹槽深1mm
13钻3—Ф7的通孔
14钻6—Ф7的通孔,钻Ф4的孔深12mm攻螺纹M5深12mm
15粗磨、精磨Ф125h6的外圆,靠Ф138的大端面
16粗磨、精磨Ф121h7的外圆,靠Ф130的大端面
(3)工艺方案的比较与分析:
上述两个工艺方案的特点在于:
方案一早先加工右边Ф121h7的外圆,然后以此为基准加工左边。
方案二正好相反,在加工左边Ф125h6的外圆后,然后再以此为基准加工右边。
经比较可见,在先加工左边Ф125h6时更容易保证右边部分的位置精度。
两种方案均是将钻孔、攻螺纹和磨外圆面放在最后,这样有利于工序的集中,节省时间。
综合各方面因素,最后的加工路线确定工艺路线方案二。
(四)机械加工余量、工序尺寸及毛坯尺寸的确定
连接座零件材料为HT200,硬度190~210HB,生产类型为中批量,铸造毛坯。
据以上原始资料及加工路线,分别确定各家工表面的机械加工余量、工序尺寸及毛坯尺寸如下:
1.外圆凸耳表面(φ142mm、φ130mm所在表面)
考虑其零件外圆凸耳表面为非加工表面,所以外圆凸耳表面为铸造毛坯,没有粗糙度要求,因此直接铸造而成。
2.外表面和内表面圆弧(R5、R15所在的过渡圆弧)
考虑到没用粗糙度要求和加工难度,因此采用直接铸造而成。
3.连接座左端面为高度方向的精基准,并且有粗糙度要求Ra6.3。
查《工艺设计课程设计指导书》(以下称《指导书》),确定加工余量为3mm。
其中分配如下:
粗车2mm
半精车1mm
4.连接座右端面加工粗基准,有粗糙度要求Ra12.5。
查《工艺设计课程设计指导书》(以下称《指导书》),确定加工余量为3mm。
其中分配如下:
粗车2mm
半精车1mm
5.连接座φ95内孔没有粗糙度要求,查《工艺设计课程设计指导书》(以下称《指导书》),确定加工余量为3mm。
其中分配如下:
粗车φ92内孔至φ94mm
半精车φ94内孔至φ95mm
6.φ40H6孔和φ17.5通孔以及φ32凹槽在同一轴线上,铸造时铸造出有余量的孔,再加工出相应的尺寸。
而且都有粗糙度要求φ40H6孔Ra3.2,φ32凹槽Ra25,φ17.5通孔Ra25,首先加工出φ17.5孔,再加工φ32凹槽,然后镗φ40H6孔。
其中分配如下:
钻17.5通孔
粗镗φ34孔至尺寸φ32mm深至28mm
半精镗φ32孔至φ38mm深至27mm
精镗φ38孔至尺寸φ40H6
7.φ50凸台,外圆没有粗糙度要求,端面粗糙度为25,外圆表面直接铸造得到,端面粗车就能达到粗糙度要求。
分配如下:
粗车φ50外圆端面至高27mm
8.3-φ7孔以及6-φ7孔都是凸耳通孔,并且粗糙度为Ra25,凸耳不厚。
因此直接铸造成实心,然后通过钻孔方式加工。
9.4-M5-7H为加工螺纹孔
左端面钻
孔,深度为12mm
在
孔基础上攻M5螺纹孔深度10mm
10.φ100H7内圆凸台,粗糙度为25。
加工分配如下:
粗车φ95内圆至φ98mm深7mm
半粗车φ97内圆至φ99mm深7mm
精车φ99内圆至φ100mm深7mm
11.其他尺寸直接铸造得到
由于本设计规定的零件为中批量生产,应该采用调整加工。
因此在计算最大、最小加工余量时应按调整法加工方式予以确认。
5、确定切削用量及基本工时:
(1)车左端面:
计算机床轴转速n=1000v/πd=398r/min
选机床主轴转速为400r/min,切削速度v=πdn/1000
切削速度:
得ν=3.12m/s,即187m/min
基本工时:
T=πDLZ/1000vfa=3.1min
(2)车左边φ125外圆:
切削速度v=πdn/1000=2.61m/s,即157m/min
基本工时:
T=πDLZ/1000vfa=14.1min
(3)车φ100内圆凸台:
计算机床轴转速n=1000v/πd=386r/min
选机床主轴转速为400r/min,切削速度v=πdn/1000
切削速度:
v=2.09m/s
基本工时:
T=7.1min
(4)车右端面
计算机床轴转速n=1000v/πd=375r/min
选机床主轴转速为400r/min,切削速度v=πdn/1000
切削速度:
v=2.88m/s
基本工时:
T=3.1min
(5)车φ50凸台
计算机床轴转速n=1000v/πd=398r/min
选机床主轴转速为400r/min,切削速度v=πdn/1000
切削速度:
v=2.88m/s
基本工时:
T=3.1min
(6)钻φ17.5通孔
确定进给量f=0.35~0.39mm/r
现取f=0.36mm/r
查的切削速度为ν=18m/s
ns=
=
=327r/min
又查得nw=195r/min
故实际切削速度为:
ν=
=
=10.07m/min
钻削长度为l=5mm
切削工时tm=
=
=4.2s
(7)镗φ40H6孔
切削用量取
f=(1.2~1.8)钻=(1.2~1.8)×0.36=0.432~0.648mm/r
取f=0.60mm/r
nw=400r/min切削速度v=8m/min
钻6—φ7孔
f=(1.2~1.8)×0.6=0.72~1.08mm/r
取f=0.9mm/r
ν=(
~
)ν钻=4~6m/min
则主轴转速为n=34~51.6r/min,按机床说明书取nw=68r/min
ν=
=
=3.84m/min
钻削长度为l=8mm
切削工时tm=
=
=0.13min
(8)钻3—φ7孔
f=(1.2~1.8)×0.6=0.72~1.08mm/r
取f=0.9mm/r
ν=(
~
)ν钻=4~6m/min
则主轴转速为n=34~51.6r/min,按机床说明书取nw=68r/min
ν=
=
=3.84m/min
钻削长度为l=10mm
切削工时tm=
=
=0.16min
(9)钻φ4孔深度12mm(以扩孔参数计算)
钻削长度为l=12mm
切削工时tm=
=
=0.1min
(10)磨φ125外圆面
磨削余量0.5mm,磨削速度v=35m/s
(11)磨φ121外圆面
磨削余量0.5mm,磨削速度v=35m/s
(12)其余工时根据实际情况而定。
四、心得体会
经过三周的机械制造工艺与装配设计,从工艺工装设计中我了解了我所设计的机械加工工艺流程,学习了和了解了机械加工的基本过程。
其目的在于通过实习使学生获得基本生产的感性知识,理论联系实际,扩大知识面;同时专业实习又是锻炼和培养学生业务能力及素质的重要渠道,也是学生接触社会、了解产业状况、了解国情的一个重要途径,逐步实现由学生到社会的转变,培养我们初步担任技术工作的能力;体验企业工作的内容和方法。
这些实际知识,对我们学习乃至以后的工作,都是十分必要的基础。
机械制造装备设计是我们在学完了大学的全部基础课,专业基础课以及专业课后进行的。
这是我们在进行毕业设计之前对所学的各科课程一次深入的综合性总复习,也是一次理论联系实际的训练。
因此,他在我们的大学四年生活中占有重要的地位。
就我个人而言,这次课程设计我学习各种的基本工艺知识,初步分析解决简单工艺问题的能力。
我希望通过这次课程设计对自己未来将从事的工作进一步适应性的训练,希望自己在设计中能锻炼自己的分析问题、解决问题、查资料的能力,为以后的工作打下良好的基础。
参考文献
1、倪小丹、杨继荣、熊运昌主编《机械制造技术基础》北京,清华大学出版社,2007
2、倪森寿主编《机械制造工艺与装配习题集与课程设计指导书》北京,化学工业出版社,2003
3、吴拓、方琼珊主编《机械制造工艺与机床夹具课程设计指导书》北京,机械工艺出版社,2005
4、王启平主编《机械制造工艺学》哈尔滨,哈尔滨工业大学出版1999
5、《机床夹具设计手册》上海,上海科学技术出版社,第二版,1987
6、《互换性与技术测量基础》胡凤兰主编,高等教育出版社,2010