预分解窑系统结皮的主要因素及预防措施.docx
《预分解窑系统结皮的主要因素及预防措施.docx》由会员分享,可在线阅读,更多相关《预分解窑系统结皮的主要因素及预防措施.docx(24页珍藏版)》请在冰豆网上搜索。
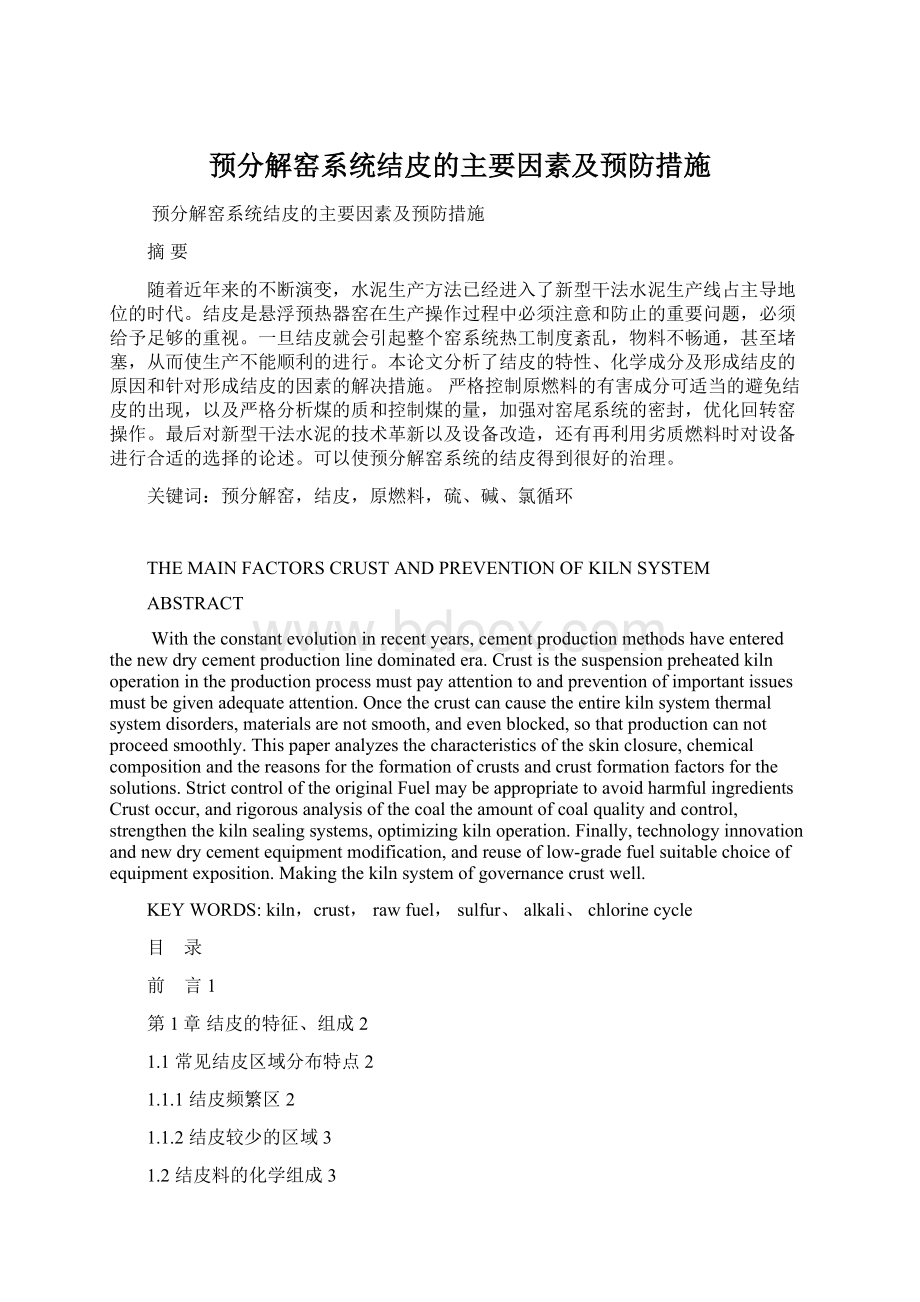
预分解窑系统结皮的主要因素及预防措施
预分解窑系统结皮的主要因素及预防措施
摘要
随着近年来的不断演变,水泥生产方法已经进入了新型干法水泥生产线占主导地位的时代。
结皮是悬浮预热器窑在生产操作过程中必须注意和防止的重要问题,必须给予足够的重视。
一旦结皮就会引起整个窑系统热工制度紊乱,物料不畅通,甚至堵塞,从而使生产不能顺利的进行。
本论文分析了结皮的特性、化学成分及形成结皮的原因和针对形成结皮的因素的解决措施。
严格控制原燃料的有害成分可适当的避免结皮的出现,以及严格分析煤的质和控制煤的量,加强对窑尾系统的密封,优化回转窑操作。
最后对新型干法水泥的技术革新以及设备改造,还有再利用劣质燃料时对设备进行合适的选择的论述。
可以使预分解窑系统的结皮得到很好的治理。
关键词:
预分解窑,结皮,原燃料,硫、碱、氯循环
THEMAINFACTORSCRUSTANDPREVENTIONOFKILNSYSTEM
ABSTRACT
Withtheconstantevolutioninrecentyears,cementproductionmethodshaveenteredthenewdrycementproductionlinedominatedera.Crustisthesuspensionpreheatedkilnoperationintheproductionprocessmustpayattentiontoandpreventionofimportantissuesmustbegivenadequateattention.Oncethecrustcancausetheentirekilnsystemthermalsystemdisorders,materialsarenotsmooth,andevenblocked,sothatproductioncannotproceedsmoothly.Thispaperanalyzesthecharacteristicsoftheskinclosure,chemicalcompositionandthereasonsfortheformationofcrustsandcrustformationfactorsforthesolutions.StrictcontroloftheoriginalFuelmaybeappropriatetoavoidharmfulingredientsCrustoccur,andrigorousanalysisofthecoaltheamountofcoalqualityandcontrol,strengthenthekilnsealingsystems,optimizingkilnoperation.Finally,technologyinnovationandnewdrycementequipmentmodification,andreuseoflow-gradefuelsuitablechoiceofequipmentexposition.Makingthekilnsystemofgovernancecrustwell.
KEYWORDS:
kiln,crust,rawfuel,sulfur、alkali、chlorinecycle
目 录
前 言1
第1章结皮的特征、组成2
1.1常见结皮区域分布特点2
1.1.1结皮频繁区2
1.1.2结皮较少的区域3
1.2结皮料的化学组成3
1.3结皮的特征4
第2章结皮形成的因素6
2.1预分解系统中挥发性组分的循环富集6
2.1.1碱的循环富集9
2.1.2硫的循环与富集10
2.1.3氯的循环与富集11
2.2局部温度过高11
2.3操作不当13
第3章防止结皮的措施14
3.1控制原材料质量、减少有害成分14
3.1.1硫碱比的含量控制14
3.1.2氯含量的控制15
3.2避免局部高温16
3.2.1用煤量的控制16
3.2.2窑内通风量的控制16
3.2.3稳定喂料量16
3.3操作及设备方面16
第4章技术的革新及改造防结皮18
4.1分解炉用煤的高比控制18
4.2旁路放风19
4.3无烟煤20
4.3.1燃烧器的选择20
4.3.2预热预分解系统21
结论23
谢辞24
参考文献25
外文资料翻译27
前 言
近年来,新型干法水泥生产线在水泥行业中所占的比例越来越大,成为我国水泥工业的主要生产工艺形式。
但由于各地原燃材料的组分及煅烧工艺水平的差异,各厂煅烧过程中窑系统内结皮现象时有发生。
不仅影响产量和能耗,严重时还影响正常生产。
对结皮原因的分析研究是减少及正确处理结皮的科学依据,具有重要的意义。
在预分解窑生产中,由于挥发性有害成分在预热器系统中的循环富集,当生料及燃料中碱、氯、硫等有害成分含量较高时,容易造成预热器系统的结皮,影响窑系统的均衡稳定的生产。
因此要严格控制原燃料的有害成分。
再者就是局部高温它是形成结皮的关键因素,所以风、煤、料及其设备要适量适当。
还有就是操作方面的问题,定期检查,用压缩空气吹扫或用空气炮吹击,因此良好的操作员及巡检人员是必须的。
第1章结皮的特征、组成
新型干法窑的结皮会发生在预热系统的不同部位,因各结皮部位的物理化学环境是有区别的,因此结皮呈现出不同的特征和组成。
1.1常见结皮区域分布特点
新型干法水泥系统的结皮是指生产过程中预热器或分解炉的器壁被经它的气流携带的粉状物料黏附,并不断增厚,从而引起整个窑系统热工制度紊乱,物料不畅通,甚至堵塞,使生产难以维持的一种现象。
预分解系统包括预热器和分解炉两大部分。
预热器通常由4~5级旋风筒及相应连接管道构成,它们将生料由常温预热至800oC,然后进入分解炉。
物料中的碳酸钙分解后850oC.。
整个窑尾系统温度最高区域为窑尾烟室及烟道,通常在1050oC左右。
预热器排放的废气温度处于全系统最低温度区,通常在300~370oC,正常是为330oC左右。
整个窑尾系统从上到下温度逐渐上升。
物料进入预热器后,在任何部位都有可能结皮和黏附,但各部位结皮的频繁程度不同。
1.1.1结皮频繁区
预分解窑系统中最容易发生结皮的部位主要在窑尾烟室、下料斜坡、缩口、最下一级旋风筒下料管等部位。
窑尾烟室区,该区域温度范围为1000~1200oC(正常窑尾烟室温度为1050oC左右)在此区域的结皮料通常较坚实、多孔,几乎所有新型干法窑在此区域都有结皮,常常对生产造成较大影响;再就是下料斜坡缩口和最下一级旋风筒下料管部位,此区域温度通常在820~900oC之间,此区域结皮外观特征视具体情况有较大变化,但以硬块结皮居多,此区域结皮对煤的燃烧特性极为敏感,当煤燃烧不充分时,其结皮频度高,严重时会造成最下一级旋风筒下料管大量结皮,严重影响生产。
1.1.2结皮较少的区域
分解炉壁、最下一级旋风筒内壁及次一级旋风筒下料管的区域,此区域的温度范围通常在750~870oC。
在此区域结皮频度较窑尾烟室及烟道稍低,分解炉及最下一级旋风筒中的结皮大多为较为松的层状料块,偶尔也会有较硬的料块出现。
次末级以上的旋风筒结皮一般不常见,但C2、C3预热器中轻微结皮时有发生,其结皮料通常为密实料块,层状结构,其形成温度通常在600~800oC之间。
1.2结皮料的化学组成
预分解系统结皮是影响新型干法水泥窑正常生产的常见问题。
为了综合利用资源、实现水泥生产的可持续发展,会更多使用含硫、碱、氯等成分较高的原燃料,这些情况下结皮问题将更加突出。
造成预分解系统结皮的原因很多:
由于机械故障、漏风、操作不当引起的结皮;由于窑和分解炉中煤粉因燃烧不完全而跑到预热器中继续燃烧,引起局部高温使物料熔融而造成的结皮;由于碱、氯、硫等挥发性物质循环富集,在分解预热系
统冷却融结而引起的结皮堵塞等。
后一种碱、氯、硫等引起的结皮,需通过放风排除部分有害物质来避免,但放风使熟料烧成热耗增加,排除物还需要处理。
关于碱、氯、硫等引起的结皮,一般认为是湿液薄膜表面张力作用下的熔融粘结,以及作用于表面上的吸力造成的表面粘结及纤维状或网状物质的[7]交织作用造成的粘结。
粘结的根源是K2SO4-CaSO4-KCl等多组分低共熔融体,它们与分解炉内的粉尘一起构成粘聚性物质。
国内外对碱、氯、硫等挥发物在预分解系统内的循环及其引发结皮、堵塞的机理进行过大量研究.分解炉内的粉尘包括从预热器下来的生料及随气流由窑内带入的粉尘。
关于哪些粉尘容易与融体形成结皮的研究报道不多。
据统计,结皮物质中K2O、Na2O、SO3、Cl-等形成融体的物质含量只占少部分,平均只有16%.左右,最低只有5.77%。
这样少的融体要将粉料粘结起来形成厚厚的结皮,显然融体的性质、融体与粉料的粘结特性、融体的温度等起着决定作用。
表1-1列举了一些从实际生产线获取的结皮料的化学组成。
融体的组成复杂多变,即使对简化了的融体(R2O-SO3-Cl-CaO单一或复合体系)性质的研究也不多见。
在分解炉内运行的粉料有:
CaCO3、CaO、Fe2O3、MgO、Al2O3、SiO2和粉煤灰以及由回转窑出来的少量熟料矿物C2S等,研究融体与这些粉体之间的粘结特性及其对结皮堵塞的影响,对于弄清结皮堵塞机理、防止结皮堵塞的发生、进一步提高系统的技术经济效益具有理论和实际意义。
表1-1结皮料的化学组成
1.3结皮的特征
预热分解系统不同部位的物理化学环境的不同。
形成的结皮特征也不尽相同。
肖成平[8]根据结皮的坚硬程度不同,粗略地将结皮划分为质地比较疏松的结皮和质地比较坚硬的结皮。
李建料归为三个基本类型,即密实的粉饼状料块、疏松多孔状结皮料和较硬的结皮料。
预分解窑中出现的其他各种结皮可以看作是这三种典型结皮料的组合或过渡形式。
(1)密实粉料块形成温度一般小于800℃,宏观看烧结程度较低,外观类似于经加压形成的粉饼:
微观上。
其物料颗粒之间呈较紧密堆积状态,偶尔也有颗粒间的小部分粘接。
颗粒形貌无明显变形。
无“织粘结”形成。
(2)疏松结皮的最大特点是由一种多孔的强不高的层状物料所构成。
其形成温度范围约为850-1000℃之间,通常显暗黄或浅棕色。
外观上。
其率高但孔径细小;显微镜下观察到,疏松结皮具有明显的液相粘接特征。
物料颗粒首先在液相的作用下形成球状或不规则的小粒团,小粒团之间又被液相相互粘接,组成一个多孔的结构。
(3)硬块结皮主要生长在1200℃的区,由致密的料团或熟料的“飞砂”经液相的粘结构成。
硬块结皮内多孔,但孔径较疏松结皮大多颜色一般较深;显微镜下观察到的硬块结皮特征和疏松结皮的差不多。
但硬块结皮的粒团比疏松结皮的更大,粒团之间的液相更加明显,粘结也更稳固此外物料还有一定的烧结,并已有大量新的熟料矿物析晶。
第2章结皮形成的因素
以前国内外学者对结皮研究的结果均得出了一致的看法:
原料、燃料中的挥发组分(如K2O、Na2O、NaCl、KCl、SO3等)。
在烧成过程中形成循环富集,在预热系统中冷凝下来,对预热结皮其促进作用。
而刘朝宗等经过实验得出:
生料煅烧所用的煤质差、灰分高是引起结皮的重要因素。
煤灰在局部时间局部料流参入不均改变了物料的化学组成、液相性质和液相量,使预热器过早出现微细熔体,粘附其余生料粉形成结皮,并不是由于挥发分所引起的。
陈全德、曹辰等曾将国内外学者所提出的造成预分解系统结皮的原因归纳为:
原料中挥发成分(K2O、Na2O、S、Cl-)含量过高,生料成分波动,喂料不均,火焰不当,预热器温度过高,燃料不完全燃烧,窑尾及预热器系统漏风,翻板阀不良等。
关于结皮的原因,H.Rumpf认为是湿液薄膜表面张力作用下的熔融粘结,作用在表面上的吸力造成的表明粘结及纤维状或网状物质的交织作用造成的粘结。
由于窑气中的碱、硫、氯等有害组分在窑尾及预热器和分解炉中冷凝时,会使最低共融温度降低,因此窑气中的碱、硫、氯等凝聚时,会以熔态的形式沉淀下来,并于入窑物料和窑内粉尘一起构成粘聚性物质,而这种物质在生料颗粒上形成液相物质薄膜,会阻碍生料颗粒的流动,从而造成结皮甚至堵塞。
总之造成结皮的因素很多,原因也较复杂,因此必须从原燃材料、机械设备、热工技术、操作方法和管理维护等各方面进行分析和探讨。
2.1预分解系统中挥发性组分的循环富集
挥发组分的循环富集主要体现在碱、硫、氯三种物质的循环富集。
在预分解窑系统中,挥发性组分(氯、碱、硫等)的循环和富聚分为内循环和外循环两个过程,内循环是挥发性组分在窑内高温带从生料及燃料中挥发,到达窑系统较低温度区域时,随即冷凝在温度较低的生料上,并随着生料沉集一起进入窑内,形成的一个在预热器和窑之间的循环和富集的过程。
而外循环是指凝聚在生料中的挥发性组分,随未被预热器收集的生料一起排出预热器系统,这部分粉尘在收尘器被收集重新入窑,这个循环是在窑外单独进行的,故称之为外循环。
这两个循环的起源是挥发性组分在窑内高温带挥发,最后由窑尾收尘器将含有挥发性组分的粉尘收集。
下面以珠江水泥有限公司生产线成套引进丹麦Smidth公司的生产设备为例。
2007年3月12日由于结皮堵塞而停窑以下为当日样品。
窑的规格为φ4.75mx75m,带有双系列(窑列和炉列)五级悬浮预热器,分解炉为FLS喷腾式分解炉。
工艺流程如图2-1
生产工艺流程图2-1
样品名称
图2-2窑内物料挥发性组分(氯、硫、碱)含量分布
注:
Y68、Y72、Y75三个点的数值出现异常,这是由于取样时混入窑
上升烟道处理下来的结皮料造成的,将其从分布曲线图中剔处
样品名称
图2-3A列旋风筒物料挥发性组分(氯、硫、碱)含量分布
样品名称
图2-4B列旋风筒物料挥发性组分(氯、硫、碱)含量分布
2.1.1碱的循环富集
碱的来源。
碱主要来源于原料,尤其是粘土。
微量的碱能降低物料的最低共熔温度,增加液相量,对熟料性能不会造成太大的影响。
物料在煅烧过程中,苛性碱、氯化碱首先挥发,碱的碳酸盐和硫酸盐次之,而存在于长石、云母、伊利石中的碱要在较高的温度下才能挥发[9]。
这一观点解释了B3~B1的碱含量变化幅度(0.3786%~0.3481%)与A3~A1的碱含量变化幅度(0.6409%~0.4557%)不一致的原因温度较低,在分解炉内出现挥发的物质主要是苛性碱和氯化碱,及部分的碳酸碱和硫酸碱,而固溶在长石、云母、伊利石等矿物晶格中的碱要在接近烧成带(如Y32)附近才挥发出来。
因此,A列烟气中的碱含量较B列高,可提供给A列物料吸收的碱较B列多。
挥发的碱除一部分排人大气外,大部分在随烟气运行过程中冷凝在温度较低的物料上,重新人窑,形成了碱的循环。
图2-2碱含量的变化趋势显示,碱在窑内高温带不断地挥发;图2-3碱含量的变化趋势又显示,碱在A系列被C5A和C4A被大量吸收,因此,碱的内循环区间为窑内高温带与C4A之间的区域。
从图2-4可以看出,B5~B3碱含量的变化趋势接近一直线,B3-B1基本不变化,这一方面说明碱在C5B~C4B间产生物理循环,另一方面说明碱在C5B和C4B的被吸收效应几乎相同。
Na20的冷凝率较低,而K20的冷凝率高达89%-97%珠江水泥有限公司生料中的钾含量较高,为钠含量的几倍,因此,窑系统碱的循环主要体现为钾的循环。
2.1.2硫的循环与富集
硫的来源。
燃料中带入的硫通常较原料中多。
使用较多的燃料是煤。
煤中通常含有C、H、O、N、S等元素。
煤中的硫通常有三种存在形式:
有机硫、硫化物中的硫、硫酸盐中的硫。
存在于硫酸盐中的硫不具有可燃性,在高温下,一部分会分解生成含硫化合物,而大部分留在灰分中。
因此在一般的水泥生产中,燃料中带入的硫通常比原料中的多,含硫化合物最终都会被氧化成三氧化硫,分布在熟料、窑皮、结皮、烟气和窑灰中。
从图2-2和图2-3可以看出,窑内硫的富集和循环情况与碱基本相似。
图2-4中B5~B3硫的变化趋势与碱的有点不一样,硫的变化B5~B4的斜率大于B4~B3的斜率,说明硫在C5B的被吸收效应比C4B明显。
要解决硫的富集问题,一方面要从源头上严格控制原燃料中的硫含量,另一方面要设法将硫固溶在熟料的晶格结构中,随熟料退出循环。
进入熟料中的硫,对熟料的形成有强化作用。
三氧化硫可以降低熟料形成时液相的黏度,增加液相数量,有利于硅酸三钙的形成。
珠江水泥有限公司窑系统上升烟道的结皮主要是由硫引起的,结皮中含硫量特别高,达43%.水泥生料自身具有一定的固硫能力,水泥生料的固硫行为主要有两种方式[9]:
一是水泥生料中富含的SiO2、AI2O3与燃煤固硫过程中的部分CaO、CaSO4在高温下反应生成了耐高温的硫硅酸钙、硫铝酸钙,使固硫产物不再以高温稳定性差的活性硫酸钙的形式存在;二是铁铝酸盐的存在使硅酸盐化合物很容易在高温下产生熔融,并以液态形式相互融合,使硅酸盐矿物有更多机会将硫酸盐的表面包裹,以更好的抑制其高温分解,使得三氧化硫的析出量减少。
肖佩林等研究表明[10]:
在钙基固硫剂中加入SrCO3后,能形成稳定产物SrSO4,同时能促进稳定矿物3CaO·3A1203·CaSO4的生成。
程军对Ba固硫剂时固硫反应的固硫特性进行了试验研究[11]:
Ba化合物的固硫效果明显优于钙化合物,在相同试验条件下,BaCO3的固硫效率几乎是CaCO3的4倍,原因在于BaSO4在l580℃下不会分解,高温稳定性比CaSO4要好得多。
因此,若生料中引入含Sr和Ba元素的组分,对减少硫在窑内的挥发和循环是有利的。
2.1.3氯的循环与富集
氯的来源。
氯主要来自水溶性碱的氯化物,即通常以KCl、NaCl的形式存在于原料内。
图2-2氯离子的变化趋势显示,回转窑后20m曲线的斜率变化最大,表明氯离子在回转窑后20m大回量挥发;图2-3氯离子的变化趋势显示,A5-A4的斜率变化最大,表明氯离子在A列C5A大量凝聚。
这两个图说明氯离子除遵循挥发性组分的循环规律外,还在回转窑后20m至A列C,。
间形成一个小循环。
从图2-4可以看出,氯离子变化B5~B4的斜率比B4-B3的斜率小,说明氯在B列C相的被吸收效应比C5B明显。
氯离子的大量存在会对水泥的性能产生影响,严重时会导致钢筋锈蚀,影响钢筋混凝土的结构稳定性。
然而,在生产中又希望熟料能多带出一些氯离子,减缓氯在窑系统中的循环和富集。
带入氯离子的除生料原料外,还有燃料煤。
有资料显示,煤中的氯主要以有机形式存在,在燃烧和热解过程中主要以氯化氢的形式释放。
何杰等人曾将兖州的烟煤在900℃下加热45min后,发现其中的氯全部释放。
窑内的温度高于900℃,虽然物料在窑内停留时间可能少于45min但从理论上分析物料中的氯应当全部释放。
然而,从图2-2氯离子的变化趋势可以看出,出窑熟料中仍含有部分氯,且从12m处到窑口基本上保持稳定。
熟料中的氯究竟以何种形式存在于熟料中,是以固溶体的形式固溶于晶体的晶格中,还是以包裹体的形式包含在玻璃相中,或者以其他方式存在于熟料中,这些值得我们进一步研究,研究的结果将直接影响到日后的灰渣煅烧。
2.2局部温度过高
局部温度过高,这是形成结皮的关键因素。
系统中如果产生局部高温,一方面促进生料和燃料中有害组分的挥发及冷凝循环,并使内循环发生的区域进一步扩大;另一方面也可能使液相提前出现,使生料粘附在衬料的内壁形成结皮。
肖成平等将热力学中表面张力与接触角之问的关系理论,即cosθ=[γ(s-g)-γ(l-s)]/γ(l-g),表面张力随温度的升高而下降。
应用于结皮的研究之中:
如果窑内局部温度偏高,则使出现熔体表面的张力下降,即γ(l-g)降低,由cosθ=[γ(s-g)-γ(l-s)]/γ(l-g)知道,熔体的表面张力下降必然导致cosθ增大,接触角减小,这就使得出现的熔体更容易在生料或衬料表面铺展开来,就更易形成结皮。
产生局部高温的原因,主要有以下几个因素:
①煤粉的不完全燃烧。
窑头或分解炉中的煤粉由于多种原因不能完全燃烧时,就可能到达窑尾或低级旋风系统中去燃烧,从而产生局部高温,这也是产生局部高温最主要的原因。
煤粉的不完全燃烧可能由下列因素引起:
燃料用煤灰分大。
煤灰含量高,说明煤质差,热值低,可燃性差,容易引起窑煤、炉煤的不完全燃烧;设备超负荷运转。
由于回转窑或分解炉的容量是有一定限度的,喂料量及喂煤量的过分加大将不利于生料和煤粉的悬浮分散,同时使得煤粉的燃烧空间变小而不利于煤粉的完全燃烧;分解炉结构不合理。
②喂料量的波动。
由于投料装置或人为因素导致喂料量不均匀,料流上下波动不稳定,就会打乱预热器、分解炉和窑的正常工作。
再加上操作上具有滞后的弱点,跟不上喂料的变化,加减煤不及时,甚至在出现断料时也不能及时减煤,因此很容易因料少而出现系统局部高温,造成结皮。
③回灰对结皮的影响。
回灰也叫做窑灰,是电收尘、增湿塔收集下来的物料。
由于回灰量小,在生料均化库中不容易被混合均匀,从而造成人窑生料成分的波动,影响窑热工制度的稳定性;再则由于回灰中含有一定量的有害组分,它的重新人窑必然加剧挥发组分的循环富集,这样引起结皮。
④预热器漏进冷风对结皮的影响。
当预热器漏进冷风时,则物料温度和分解率都降低,为维持生产,系统排风必须加大,因而废气量增大,飞扬粉尘增加,循环负荷加大,导致人窑生料温度下降,能耗上升。
当预热器漏进冷风与热物料接触,很容易使热物料冷凝,粘附在系统的内壁而产生结皮。
此外,被带到窑尾或预热器中的煤粉遇到新鲜冷风,燃烧速度加快,产生局部高温而形成结皮。
此外,石灰石中MgO也是结皮的一个因素,随着MgO含量的上升,经过回归分析,预热器出口温度上升;出口气体中氧气含量下降,说明交换效率下降,分解炉内存在煤粉的不完全燃烧,同时窑尾的负压随着MgO含量的上升而下降,说明窑内通风不良,窑尾易于结皮[12]。
2.3操作不当
操作上,过高的强调入窑分解率,分解炉用煤量过大;窑前三通道调整不当导致火焰形成不好;投料不及时或下料量与窑速不同步;窑尾风机下降必然导风量控制不当等都容易引起结皮[11]。
众所周知,长期以来窑尾结皮一直是众多预分解窑生产线的一大难题。
为了缓解结皮,一方面要控制原燃料有害元素的带入量,另一方面得减少有害元素在高温带的挥发以增加出窑熟料有害元素的带出量。
本文以国内普遍的硫过剩为例。
硫的挥发系数随窑内O2量增加而降低。
窑内硫挥发量主要来CaSO4的热分解:
CaSo4≒CaO+SO2+1/2O2这是一个可逆反应。
在温度一定的条件下,当O2量增加时,反应利于向左进行,CaO、SO2减少,CaSO4增加,否则反之。
国外实验室对不同O2量的SO2测定认为:
02量4%左右是抑制热生料中SO2挥发的关键点,当O2量大于4%左右后,生料中S02释放明显地大幅下降;且随02量的进一步增加,生料中S02释放量继续下降[13]。
窑内存在不完全燃烧时,部分煤粉落在料面上,硫酸盐与C作用,生成SO2:
K2SO4+C→K20+SO2+CO
CaSO4+C→Ca0+SO2+CO
这是SO2挥发量增加的又—途径。
另外,烧成带温度提高及烧成带物料停留时间增加,SO2挥发量均会随之增加。
以上情况的种种组合使熟料携带出窑的硫酸盐量变化范围颇宽。
而窑尾烟气中SO2浓度过高,致结皮加剧,影响窑内通风,还原气氛更浓,SO2挥更多。
第3章防止结皮的措施
3.1控制原材料质量、减少有害成分
众所周知,生料(包括燃料)中挥发性有害组分钾、钠、氯、硫进入窑系统后,它们在高温下挥发