无缝钢管生产缺陷与预防.docx
《无缝钢管生产缺陷与预防.docx》由会员分享,可在线阅读,更多相关《无缝钢管生产缺陷与预防.docx(25页珍藏版)》请在冰豆网上搜索。
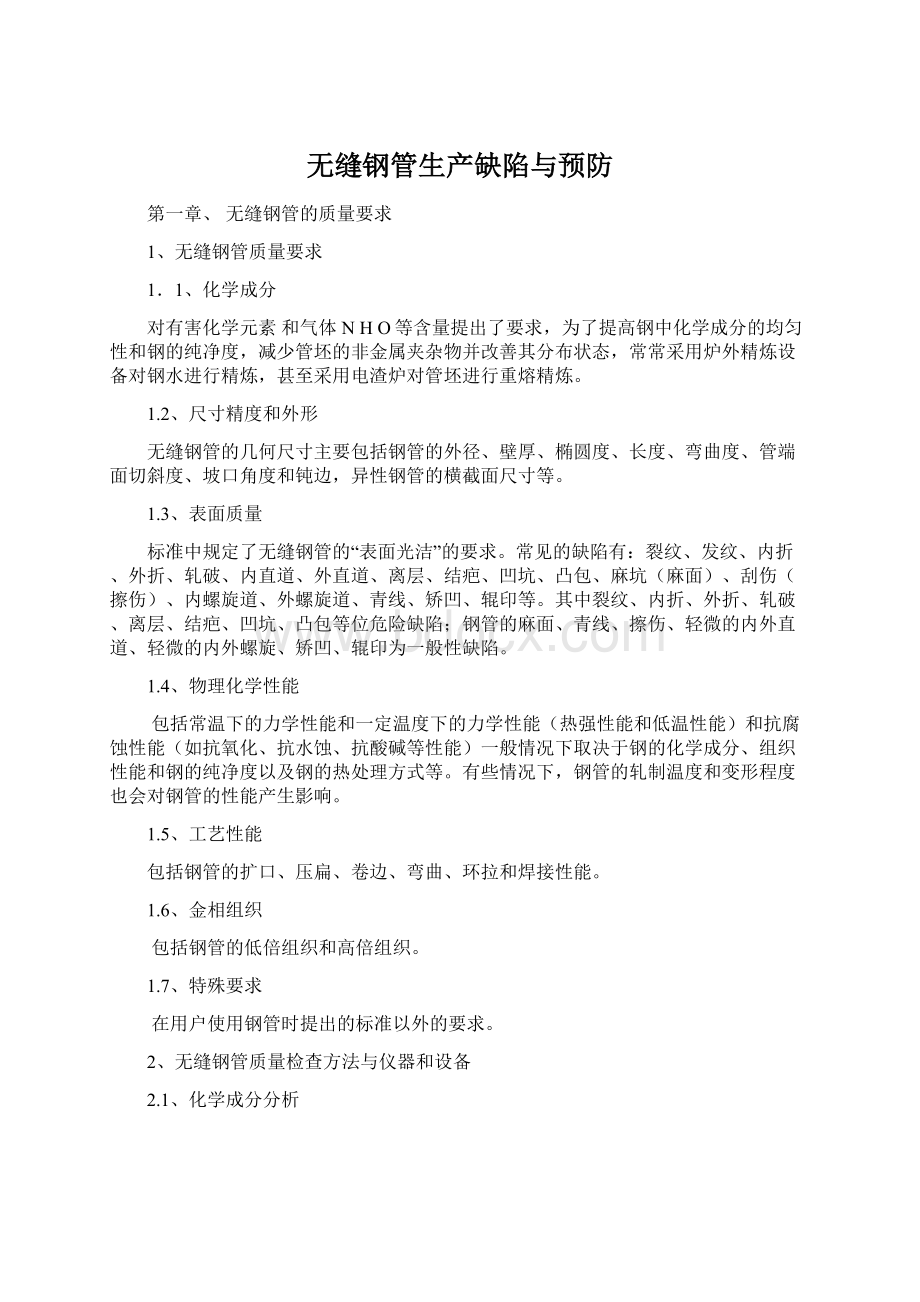
无缝钢管生产缺陷与预防
第一章、无缝钢管的质量要求
1、无缝钢管质量要求
1.1、化学成分
对有害化学元素和气体NHO等含量提出了要求,为了提高钢中化学成分的均匀性和钢的纯净度,减少管坯的非金属夹杂物并改善其分布状态,常常采用炉外精炼设备对钢水进行精炼,甚至采用电渣炉对管坯进行重熔精炼。
1.2、尺寸精度和外形
无缝钢管的几何尺寸主要包括钢管的外径、壁厚、椭圆度、长度、弯曲度、管端面切斜度、坡口角度和钝边,异性钢管的横截面尺寸等。
1.3、表面质量
标准中规定了无缝钢管的“表面光洁”的要求。
常见的缺陷有:
裂纹、发纹、内折、外折、轧破、内直道、外直道、离层、结疤、凹坑、凸包、麻坑(麻面)、刮伤(擦伤)、内螺旋道、外螺旋道、青线、矫凹、辊印等。
其中裂纹、内折、外折、轧破、离层、结疤、凹坑、凸包等位危险缺陷;钢管的麻面、青线、擦伤、轻微的内外直道、轻微的内外螺旋、矫凹、辊印为一般性缺陷。
1.4、物理化学性能
包括常温下的力学性能和一定温度下的力学性能(热强性能和低温性能)和抗腐蚀性能(如抗氧化、抗水蚀、抗酸碱等性能)一般情况下取决于钢的化学成分、组织性能和钢的纯净度以及钢的热处理方式等。
有些情况下,钢管的轧制温度和变形程度也会对钢管的性能产生影响。
1.5、工艺性能
包括钢管的扩口、压扁、卷边、弯曲、环拉和焊接性能。
1.6、金相组织
包括钢管的低倍组织和高倍组织。
1.7、特殊要求
在用户使用钢管时提出的标准以外的要求。
2、无缝钢管质量检查方法与仪器和设备
2.1、化学成分分析
可以采用仪器分析法和化学分析法。
用于化学分析的试样分熔炼试样、锭钻屑试样、管材试样。
熔炼试样一般采用仪器分析法、管材成品试样采用化学分析法和一起分析法。
常用的化学分析仪器主要是:
红外碳硫仪、直读光谱仪、X射线荧光光谱仪等。
2.2、尺寸及外形检测
检查内容主要包括:
壁厚、外径、长度、弯曲度、椭圆度、端口坡度及钝边角度和异形钢管横截面形状等。
2.3表面质量检测
人工肉眼检查和无损探伤检查。
无损检测的方法有很多如:
超声波探伤、涡流探伤、磁粉探伤、漏磁探伤、电磁超声波探伤和渗透探伤等。
每种方法各有优缺点:
适合检测钢管表面或者近表面:
涡流探伤、磁粉探伤、漏磁探伤、渗透探伤。
其中渗透探伤仅限于钢管表面开口缺陷的检查。
磁粉探伤、漏磁探伤、涡流探伤仅仅限于铁磁性材料检查。
涡流探伤对点状缺陷比较敏感,其他探伤对裂纹敏感。
而超声波探伤对对钢管表面检测反应比较迅速,对钢管内部定性分析尚存在一定的困难,并且超声波检查还受到钢管的形状和晶粒度的限制。
2.4化学性能检测
常温或者一定温度下的力学性能实验(拉伸实验、韧性实验、硬度试验),液压试验以及腐蚀试验(晶间腐蚀试验、抗氢开裂实验、抗硫化物应力开裂实验)。
2.5钢管工艺性能试验
包括压扁实验、环拉实验、扩口和卷边实验、弯曲实验。
2.6金相分析
包括低倍和高倍检查。
2.7石油专用管螺纹参数检测
包括接箍纹检测、管体螺纹检测以及管体与接箍拧紧后的检测。
第二章、管坯质量缺陷其及预防
连铸圆管坯一般采用立式连铸机、弧形连铸机和水平连铸机生产。
立式连铸机和弧形连铸机的生产的管坯的直径较大,而水平连铸机的生产的员管坯规格较小。
连铸生产管坯的优点如下:
a、工艺简化
b、收得率高
c、生产条件改善
d、节约能源
2.1、管坯标准简介
包括《连铸管坯标准》和《轧制管坯标准》
2.2、管坯缺陷的检查和清理
缺陷检查:
一般采用肉眼检查。
对表面质量要求比较高,而且氧化铁皮比较厚的氧化铁皮比较厚的管坯,检查前可以采用酸洗或者喷丸处理将管坯表面氧化铁皮去除,是表面缺陷裸露出来,便于目视检查。
目视检查室最常用的,但是其可靠性查。
还可以采用磁感应探伤的方法检查管坯表面及表层的缺陷。
电磁感应探伤的方法有很多,比如有:
干荧光磁粉探伤法、涡流探伤法、电磁探伤法。
管坯的低倍组织检查一般采用硫印法和酸浸法。
硫印检验是用相纸显示试样上的硫偏析。
它可以显示管坯中的裂纹、偏析、低倍组织、夹杂分布。
酸浸法是选用不同的腐蚀药、剂,对管坯缺陷和钢基体进行浸蚀由于管坯缺陷和钢基体的浸蚀程度不同,使原本难以鉴别的细小尺寸的管坯缺陷都可以显示出来。
缺陷的清理:
火焰清理、风铲清理、手动砂轮清理和自动砂轮清理、车削和砂带清理
2.3、管坯的外形形状缺陷
管坯的直径椭圆度超差、钢锭尺寸超差和端面切斜度超差等。
2.4、管坯的表面质量缺陷
常见的表面缺陷有:
表面裂纹、结疤、气孔(针眼)、重皮、凹坑、沟槽、耳子等。
连铸圆管坯纵向裂纹的原因如下:
a、水口和结晶器不对中而产生的偏流对管坯凝固坯壳的冲刷;
b、保护渣融化不良,液渣层过后活过薄,导致渣膜薄厚不均,使管坯凝固壳过薄;
c、结晶器液面振动;
d、钢中的SP含量,S>0.02>0.017%时,钢的高温强度和塑性明显降低,管坯表面发生纵裂的趋势增大;
e、钢中的C含量,在0.12-0.17%时,管坯的表面发生纵裂的倾向增大;
防止连铸圆管坯产生表面纵裂纹的措施主要有以下几个方面:
a)保证水口和结晶器对中;
b)结晶器波面振动要在±10以内;
c)确保合适的浸入式水口插入度;
d)采用合适的结晶器锥度;
e)结晶器与二次冷却区上部对弧要准;
f)选择性能优异的保护渣;
g)采用热顶结晶器。
管坯横裂纹位于铸坯内弧表面振痕的波谷处,通常是隐藏看不见的。
横裂纹产生的原因大体包括以下几个方面:
a)振痕太深是连铸管坯横裂纹的发源地
b)钢中的含量增加,促使质点()在晶界沉淀,诱发连铸圆管坯横裂纹产生。
c)连铸管坯在脆性温度900-700°C时矫直
d)二次冷却强度过大
防止连铸圆管坯产生表面横裂纹大方法如下:
a)结晶器采用高频率、小振幅的以减小铸内弧的振痕深度;
b)二次冷却区采用平稳的弱冷却制度,以确保矫直时连铸管坯的表面温度大于900°C;
c)确保结晶器的液面稳定;
d)采用润滑性能良好、黏度较低的保护渣。
连铸圆管坯的表面网状裂纹只有在酸洗完后才可以看的见其产生原因如下:
a)高温铸坯吸收了结晶器的铜,而铜变成液体之后在沿奥氏体晶界渗透;
b)表面铁皮的选择性氧化使钢中的残余元素()残留在管坯表面并沿晶界渗透而形成裂纹;
防止连铸圆管坯的表面网状裂纹产生方法:
a)结晶器表面镀铬或以增强其表面硬度
b)采用合适的二次冷却水量
c)控制钢中的残余元素
d)控制值
结疤和重皮缺陷
管坯的结疤和重皮缺陷是指管坯表面未与基体金属完全结合的金属片层。
钢锭和轧制圆坯的结疤和重皮缺陷相比连铸坯较多,主要是由于皮下气泡、非金属夹杂物的连铸坯或钢锭经轧制后皮下气泡和非金属夹杂物不但没有焊合,反被轧破而与基体金属分开造成的。
严重的结疤和重皮缺陷会导致钢管表面无规律分布的片状外折。
一般是比较大,但是深度不是很深,可以通过修磨将其清除。
管坯气孔
一般比较小,常常是因为钢液在浇铸过程中皮下气泡破裂在管坯的表面形成的一些小孔。
钢锭和连铸坯上的气孔比连铸坯多。
气孔一旦存在,即表明钢中的气体含量比较高。
管坯的凹坑和沟槽
存在于管坯的表面,连铸圆管坯的凹坑和沟槽的产生存在以下两方面的原因:
a)铸坯在结晶过程中产生的,与结晶器的锥度太大和二冷区的不均匀冷却有关;
b)铸坯在没有完全冷却时,管坯表面收到机械碰撞或者划伤造成的。
轧制圆管坯的凹坑和沟槽主要是由于轧制变形工具盒运输工具造成的。
凹坑呈点状分布,沟槽呈纵向连续或断续分布。
管坯的耳子
钢锭和连铸圆坯的“耳子”并不突出。
只有轧制圆坯才会出现“耳子”。
带有“耳子”的管坯在斜轧穿孔过程中极易造成毛管表面的螺旋状外折。
当采用多边形圆钢锭时就相当于钢锭表面存在多根“耳子”,穿孔毛管也会产生螺旋状外折。
2.5、管坯的低倍组织缺陷
连铸圆管坯低倍组织主要由三个区组成:
靠外表层的等轴细晶区、像树枝状的晶体组成的柱状晶区、中心是粗大的的等轴晶区
连铸圆坯的低倍组织缺陷对管坯的加工性能、力学性能和钢管质量产生很大的影响。
常见的低倍组织缺陷有:
管坯皮下气泡、疏松、缩孔、皮下裂纹、中心裂纹、组织偏析等。
管坯的皮下气泡:
存在连铸坯表面的附近,形态为椭圆形。
一般认为钢水脱氧不足是管坯皮下气泡产生的主要原因。
一般需要对保护渣、铁合金、钢包、中间包进行烘烤、注流采用保护浇注。
对于要求更高的钢种,还要采用炉外精炼的方法对钢水进行脱气。
存在皮下气泡的连铸圆管坯,在加热炉加热时气泡内表面会被氧化,轧后无法焊合就会形成钢管表面缺陷。
管坯皮下裂纹:
存在于连铸圆管坯和的柱状晶区和表面细晶区的过渡附近。
距离管坯表面3-10范围内。
只要此裂纹不贯通到外表面,就不会被氧化,在轧制压力的作用下会焊合。
一般不会产生严重的表面质量。
中间裂纹和中心裂纹:
存在于连铸圆坯的柱状晶区,一般来讲中间裂纹的方向和柱状晶的方向是一致的。
有研究表明,连铸管坯的中间裂纹和中心裂纹是造成无缝钢管内折的主要原因。
穿孔时,管坯再由轧辊和导向工具所组成椭圆孔型中受到反复拉压应力的作用,其中间裂纹或中心裂纹得到扩张或氧化,由此而会产生钢管内折。
连铸圆坯的中心裂纹或者中间裂纹扩张以后而形成的钢管内折,一般较深,常常会造成钢管废品。
(其形成机理比较复杂,详情请看《无缝钢管缺陷与预防》-40页)
管坯的疏松与缩孔:
存在于管坯中心的部分的等轴晶区内。
管坯疏松是因为铸坯在凝固的过程中的超前的晶粒作用,液态金属运动基于向凝固方向冷却产生收缩受到阻碍,或者是管坯液态部分下沉的晶粒妨碍铸坯的补缩形成的。
当疏松达到一定程度的时候,铸坯就会出现缩孔。
其分布状态为在管坯中不连续分布。
分布密度比较均匀、弥散度较高的连铸管坯中心疏松,对斜轧穿孔过程不但没有危害,反而是有利的。
北京科技大学朱景清教授通过实验已经证明该点。
并且,在顶头鼻部前端有一个5的金属带,此金属将开裂的管坯中心与顶头分开,从而避免了内折和裂纹的缺陷。
管坯的偏心:
包括组织偏析、成分偏析和结晶区域偏析等。
存在穿晶的连铸管坯必须报废,绝对不允许投放轧管。
2.6、管坯的显微组织缺陷
一般来讲,管坯标准没有对管坯的标准进行规定,但是对于有特殊要求的合金钢管、高合金钢管管坯的显微组织则有相应的要求。
这些要求只要是体现在管坯的成分、管坯的成分和组织均匀性以及非金属夹杂物的含量和分布形态上。
当管坯中含有、、、等有害元素时,由于这些元素几乎完全不溶于结晶区的晶内分布上在晶界上,管坯加热到一定的温度后,这些比钢熔点低得多的元素就先期开始熔化,从而削弱了晶粒间的联系,在管坯热变形时就容易产生金属破裂,从而产生大量的质量缺陷。
当管坯的成分和组织不均匀并且产生严重的偏析时,会使钢管出现严重的带状组织,从而严重影响钢管的力学性能和耐蚀性能。
管坯的夹杂物含量太多,特别是呈簇状分布并形成大型夹杂物之后,不仅会严重影响钢管的性能,而且可能会使钢管在生产过程中产生裂纹。
钢中的有害元素,往往是因为冶炼技术或者成本的原因使其很难在钢水中去除。
电炉炼钢时,废钢的有害元素往往会更高。
钢的冶炼一般采用精料的方针。
管坯的成分和偏析往往是因为钢水的冶炼时间不够(往往使用完全电炉炼钢时更加突出)或者是因为钢水的搅拌效果不好。
当冶炼合金钢的时候,尤其是冶炼高合金钢,可以将铁合金先在工频炉中熔化,再将其加入到精炼炉而不是直接将铁合金加入到精炼炉。
可以缩短钢水在精炼炉中的冶炼时间,又有利于钢水的成分均匀化。
管坯的非金属夹杂物是不可避免的。
它是钢中的铁和氧、硫、氮等作用形成的化合物;也有可能是炼钢和浇注是混入的耐火材料碎片。
、、、、、等的氧化物。
金属夹杂物的存在会导致金属塑性变差,使钢在加工时变形不一致或者导致钢管开裂。
钢中的非金属夹杂物的包括内生非金属夹杂物和外来非金属夹杂物。
内生的非金属夹杂物是钢水脱氧、二次氧化或者钢液冷却和凝固过程中造成的。
主要有以下三个来源
a)加入脱氧剂后形成的脱氧产物,裸露的钢液被大气氧化和被耐火材料氧化而生成的二次氧化物;
b)来源耐火材料的夹杂物,它是由于耐火材料渣线或者内衬受到化学腐蚀或者机械侵蚀而生成的产物;
c)卷渣产生的夹杂物,它是因为渣-钢界面上的钢水流速较大以及渣的乳化而使液态的渣滴入钢液中。
抑制钢液漩涡的方法:
a)优化钢水出口的挡渣结构;
b)在钢水出口附近插入挡板;
c)临时关闭钢水出口,可以有效抑制漩涡;
d)吹起,可以延迟钢液漩涡的产生
防止钢水的二次氧化主要是控制炉渣对钢水的二次氧化;控制气氛防止钢水的二次氧化;看着耐火材料对钢水的二次氧化等。
采用钢包精炼技术和中间包冶金技术可以减少钢中的非金属夹杂。
所有的钢包精炼炉,均具有去除非金属夹杂的功能。
其主要功能是通过脱气减少钢水的二次氧化,并且在精炼过程中有足够的时间使钢液中的非金属夹杂上浮进入渣中。
第三章、管坯加热缺陷及其预防
热轧无缝钢管,从管坯到产品钢管一般需要两次加热,即管坯穿孔前加热和轧后荒管在定径前的加热;生产冷轧(拔)钢管时,需要采用中间退火来消除残余应力;对于一些特殊要求的钢管,为了提高钢管的力学性能和改善钢管组织及工艺性能,还要对其进行热处理。
常见的管坯(钢管)加热缺陷有管坯加热不均、氧化、脱碳、加热裂纹、过热过烧。
3.1、加热炉炉型及其特点
穿孔前的管坯加热,其目的是提高钢的塑性;降低钢的变形抗力;为轧管提供良好的金相组织。
管坯加热炉主要有环形加热炉、步进式加热炉、斜底式加热炉和车底式加热炉。
定径前的荒管再加热,其目的在于升高和均匀荒管的温度,提高钢的塑性,控制其金相组织,为荒管定径创造有利条件,并保证钢管的力学性能。
常见的加热炉有步进式再加热炉、连续式辊底式再加热炉、斜底式在加热炉、电感式再加热炉。
冷轧(拔)的再加热主要是为了消除加工硬化,降低变形抗力。
常见的退火热处理采用的加热炉主要是步进式加热炉、车底式加热炉、连续式辊底加热炉。
在无缝钢管生产中,环形加热炉和步进式加热炉目前应用最为广泛;电感应式加热炉也正在发展;斜底式加热炉因为加热质量不高,劳动强度大而趋于淘汰。
连续式辊底加热炉主要使用在冷轧(拔)钢管的热处理;车底式加热炉适用于批量较小,加热及保温时间较长的合金厚壁钢管的热处理;保护气体连续式辊底式加热炉主要是应用于钢管表面要求无氧化的成品钢管的热处理和冷轧(拔)过程中酸洗工序的退火处理。
环形加热炉的优缺点:
a)可加热异性坯料;
b)加热能力强,并且能适应多种规格的坯料加热,有利于无缝钢管的组织生产;
c)可根据需要改变坯料在炉内的分布;
d)坯料静止在炉底,装出料开门小,密封性好,金属损伤小;
e)坯料三面加热,热效率高,管坯的加热速度快且质量好;
f)加热炉可以排空;
g)机械化自动化程度高;
h)占地面积大,炉底面积利用较差
步进式加热炉优缺点:
a)产量大
b)设备结构简单紧凑,机械化程度高,劳动条件好,维护检修方便;
c)坯料四面加热,加热质量好,加热效率高,加热时间短
d)密封性好,坯料表面氧化少,烧损少;
e)占地面积少
f)投资大
g)设备故障多维修费用高
斜底式加热炉优缺点:
a)结构简单,占地面积少,基建速度快;
b)投资费用比环形加热炉和步进式加热炉少很多;
c)机械化程度低,劳动强度大;
d)产量低;
e)管坯加热温度不均匀,热效率低;
f)金属烧损大
辊底式加热炉的优缺点:
a)占地面积小;
b)钢管加热质量好,不易发生表面氧化;
c)家热效率高;
d)设备结构简单,维护量小,劳动强度低;
e)密封性差;
f)炉辊容易弯曲;
g)钢管端头容易碰撞炉辊;
3.2、管坯加热缺陷及其预防
影响加热质量的因素包括加热温度、加热速度、加热和保温时间以及炉内气氛等。
制定管坯加热的依据是奥氏体化动力学曲线。
管坯的加热温度对管坯加热质量的影响主要体现为加热温度过低、过高或者加热不均。
加热温度太低时会增大金属的变形抗力,降低金属的塑性。
特别是当管坯加热温度不能保证钢的金相组织完全转化为奥氏体晶粒时,管坯在热轧过程中,产生裂纹的趋势会大大增加。
管坯在高温下加热时,管坯表面会发生严重的氧化、脱碳甚至产生过热或者过烧。
管坯过热主要是管坯加热温度过高,或者在较高的加热温度下加热时间过长而造成奥氏体晶粒过分粗大所致的缺陷。
当管坯加热到固相线温度附近时,使奥氏体晶界发生氧化甚至晶界局部熔化,管坯便产生了过烧。
管坯过烧,在加热过程中是一种十分严重的缺陷。
过热的管坯穿孔毛管会产生大量的内折;而过烧的管坯会使钢管报废。
一般情况下,管坯过烧是一种极不正常的现象,可能是因为设备失灵或者操作不当造成的。
对此应该予以高度重视。
管坯的加热不均匀(俗称阴阳面)。
产生的主要原因是加热的时间主要是保温时间不够,或者是加热炉的烧嘴布置和和火焰调整不当所致。
加热不均匀的管坯穿孔出来的毛管会产生壁厚不均,不均匀的程度比较严重时,穿孔出来的毛管会看到螺旋状的“黑带”。
制定管坯的加热工艺参数时,为了确定各个钢种的最佳的加热温度,应在铁-碳相图的指导下,遵循以下基本原则:
a)保证必须把管坯加热到临界温度以上,以便得到均匀一致的奥氏体组织;
b)应保障管坯在单一的奥氏体区内完成穿孔变形,荒管的终轧温度最好在850°C左右;
c)管坯的加热温度不能太靠近固相线(最好低100-150°C),以防止晶界氧化,出现过热或者过烧;
d)减少管坯的氧化,防止管坯的表面严重脱碳,应注意调节加热炉内的气氛;
在制定管坯的加热工艺参数时,还应该考虑以下因素的影响:
a)管坯的化学成分和原始组织;
b)管坯的尺寸和大小;
c)加热炉的形式和加热介质;
d)加热炉的装陆方式和装炉量
管坯的加热速度:
管坯的加热速度与管坯的热裂纹大产生有密切的关系,当管坯入炉后,若加热炉的温度过高或者管坯在加热炉中加热的速度过快时,则管坯易产生热裂纹。
加热裂纹既处在于管坯的表面,也有可能存在于管坯的内部,当有带有加热裂纹的管坯进行穿孔时,容易在毛管的内外表面形成裂纹或者折叠。
由于合金钢的热传导系数较低,合金钢管坯产生热裂倾向性更高,为此应该降低加热速度。
管坯加热裂纹还与管坯的尺寸有关系。
管坯直径越大,越易产生裂纹。
因此,在加热较大直径的管坯时候,当管坯处于较低的温度时,应该使用较低的加热速度。
管坯的加热时间和保温时间:
;
为了减少加热时间和保温时间不合理造成的管坯加热质量的缺陷,管坯的加热应该遵循以下原则:
a)确保管坯加热均匀,并全部转化为奥氏体;
b)碳化物应溶于奥氏体晶粒中;
c)奥氏体晶粒不能粗大,不能出现混晶;
d)加热管坯不能产生过热或者过烧
总而言之,为了提高管坯加热质量,预防管坯的加热缺陷,在制定加热工艺参数时,一般遵循以下几个基本要求:
a)加热温度准确,以保证管坯在最好的穿孔工艺性能;
b)加热温度均匀,力求管坯沿纵向很横向的加热温度差不得大于10°C;
c)金属烧损少。
在加热过程中应防止管坯产生过氧化、表面裂纹、粘结等;
d)加热制度合理,应做好加热温度、加热速度和加热时间合理配合,以防止管坯产生过热或者过烧。
在实际操作过程中,为了实现以上的基本要求,应当注意一下几个基本问题:
a)按照铁-碳相图来确定管坯的加热温度
b)注意调节炉内气氛,均热段要保持弱还原性火焰,根据燃气的发热值合理调节燃气和空气的空燃比
c)在保证管坯不产生加热裂纹的前提下,采用高温短时快速加热;
d)对于加热时间和保温时间,综合考虑加热氧化、脱碳和温度均匀性的要求。
3.3、荒管加热缺陷及其预防
轧管机轧后的荒管,一般不能保证温度的均匀一致,也难以保证荒管的终轧温度要求,因此需要在定径前进行再加热。
本文重点介绍电感式荒管再加热炉。
电感应式荒管在加热炉由高频供电系统、感应线圈、电容器、冷却水系统、电器控制系统和仪表检测系统等六部分构成。
荒管通过带电感应线圈时加热。
与传统的步进式加热炉相比,基建投资减少70%,能耗和维修费用也比较低。
荒管的加热时间不超过30s。
属于特快速加热,荒管加热后的晶粒很细,综合力学性能会得到显著改善,其次加热过程中没有烧损,有效的提高了钢管的成材率。
(详见书70页)
荒管再加热过程中的主要质量缺陷包括,荒管的加热不均、加热温度太高或者太低、金相组织不合理、表面严重氧化和脱碳、过热或者过烧,以及管体在加热炉内的机械擦伤。
3.4、钢管热处理缺陷及其预防
金属材料热处理分为整体热处理、表面热处理和化学热处理。
钢管热处理一般采用整体热处理。
一般都经过加热、保温、冷却等基本过程,这些过程中都有可能产生缺陷。
钢管的热处理缺陷主要包括钢管组织性能不合格、尺寸超标以及表面裂纹、擦伤、严重氧化、脱碳、过热、过烧等。
钢管的热处理工艺特点:
第一道工序是加热:
一种是临界点1或者3以下的加热;另一种是临界点1或者3以上的加热。
第一种主要是稳定钢的组织和消除钢管的残余应力,第二种主要是将钢奥氏体化。
第二道工序是保温:
目的是均匀钢管的加热温度,以得到合理的加热组织。
第三道工序是冷却:
冷却过程是钢管热处理的关键工序,他决定钢管在冷却后的金相组织和力学性能。
在实际生产过程中所采用的钢管冷却方式是多种多样的。
经常采用的冷却方式有炉冷、空冷、油冷、聚合物冷、水冷。
根据不同的钢管加热温度,结合不同的钢管冷却速度,分为正火、退火、回火、淬火及其他工艺。
正火:
细化奥氏体晶粒,均匀内部组织和改变残余应力状态,提高钢管的综合性能。
减轻钢管在变形过程中的所形成的带状组织和混晶(但是不能消除因钢中的偏析和夹杂物等造成的带状组织);消除过共析钢中的网状碳化物,有利于球化退火;用作中碳钢及合金结构钢管淬火前的预处理,以细化晶粒使组织均匀,减少淬火工序所产生的钢管缺陷;对于低碳钢和低合金钢钢管用以替代退火,改善钢管的切削性能;也可以作为要求不高的普通钢管的最终热处理。
退火:
分为再结晶退火、完全退火、等温退火、球化退火和消除残余应力退火。
一般高碳、低合金和合金钢钢管,需要通过退火降低其硬度和强度,提高塑性,消除内应力和组织不均,细化结晶组织,以利于钢管的机加工和为钢管的最终热处理奠定基础。
回火;一般分为低温回火(150-250°C)、中温回火(350-500°C)、和高温回火(500-650°C)。
提高钢管的塑性和韧性;使钢管获得良好的综合力学性能,降低或者消除钢管在淬火时所产生的残余应力以及稳定钢管尺寸,使钢管在使用过程中不发生变化。
回火一般采用空冷,为防止钢管重新产生内应力,应该缓慢冷却;对于高温回火脆性的钢管,回火后应采用快速冷却,如油冷。
淬火:
将金属材料加热到奥氏体3线以上30-50°C,保温一段时间后使钢管快速冷却而得到马氏或者贝氏体的工艺过程。
钢管淬火后会产生热应力和组织应力,一般可通过回火消除和改善。
淬火和回火结合(调质)能使钢材的综合性能得到大幅提高。
其他工艺还有,固溶处理和保护气体热处理等。
热处理缺陷及其预防
钢管组织性能不合格:
钢管奥氏体化之后,根据其不同的碳含量和不同的冷却速度,可以得到珠光体组织、贝氏体组织、马氏体组织。
如果热处理工艺控制不当就可能产生魏氏组织。
魏氏组织是一种过热组织。
对钢管的综合性能有不良影响(该组织在高温持久性能方面比较优异),会使钢管常温强度降低、脆性增加。
较轻的魏氏组织可以采用适当温度的正火来消除,而程度较重的魏氏组织可以用二次正火来消除。
第一次正火温度较高,第二次正火温度较低。
同时还起到细化晶粒的作用。
过冷奥氏体转变曲线()和过冷奥氏体连续冷却转变曲线()是制定热处理冷却速度的重要依据。
钢管尺寸不合格
钢管经热处理后,在某些情况下其尺寸会发生明显变化而出现超差,包括钢