PLC控制组合机床动力滑台液压系统设计.docx
《PLC控制组合机床动力滑台液压系统设计.docx》由会员分享,可在线阅读,更多相关《PLC控制组合机床动力滑台液压系统设计.docx(33页珍藏版)》请在冰豆网上搜索。
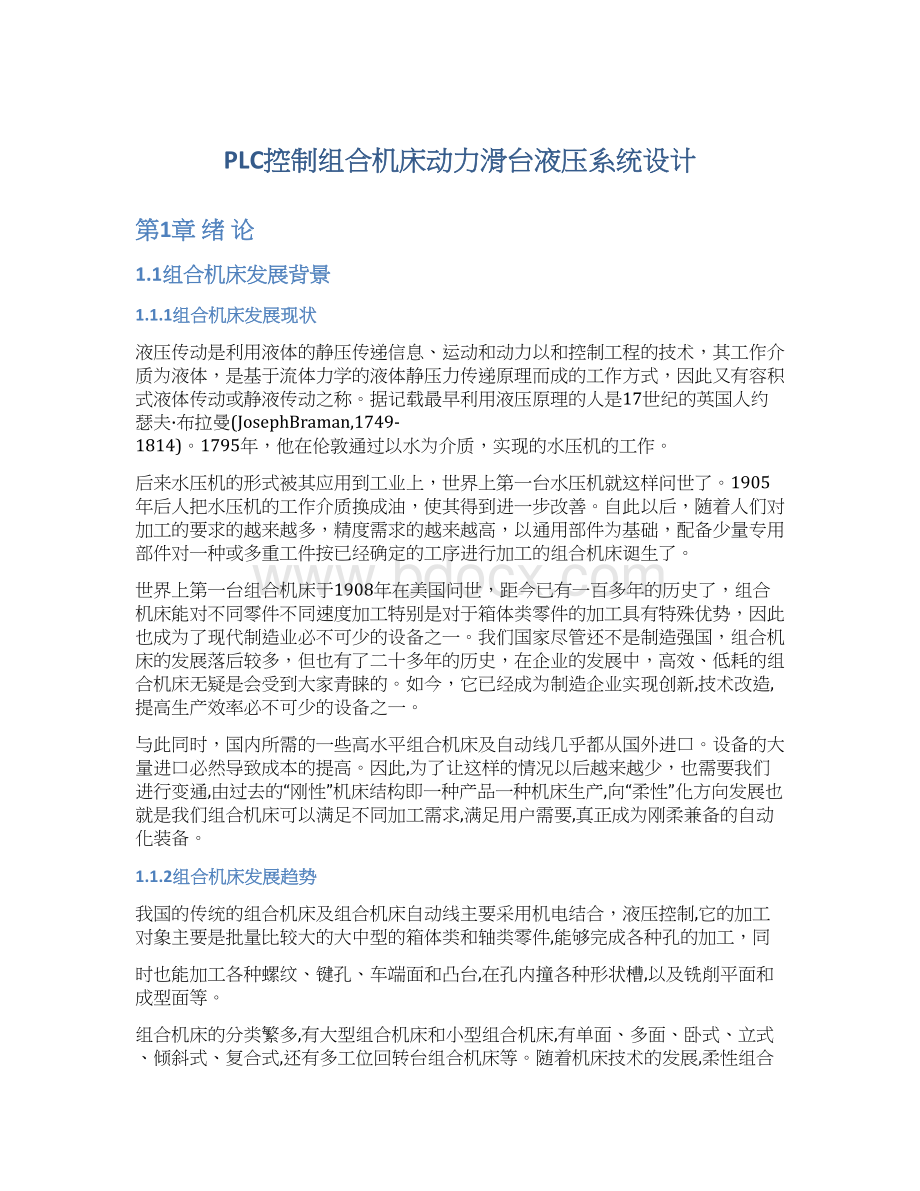
PLC控制组合机床动力滑台液压系统设计
第1章绪论
1.1组合机床发展背景
1.1.1组合机床发展现状
液压传动是利用液体的静压传递信息、运动和动力以和控制工程的技术,其工作介质为液体,是基于流体力学的液体静压力传递原理而成的工作方式,因此又有容积式液体传动或静液传动之称。
据记载最早利用液压原理的人是17世纪的英国人约瑟夫·布拉曼(JosephBraman,1749-1814)。
1795年,他在伦敦通过以水为介质,实现的水压机的工作。
后来水压机的形式被其应用到工业上,世界上第一台水压机就这样问世了。
1905年后人把水压机的工作介质换成油,使其得到进一步改善。
自此以后,随着人们对加工的要求的越来越多,精度需求的越来越高,以通用部件为基础,配备少量专用部件对一种或多重工件按已经确定的工序进行加工的组合机床诞生了。
世界上第一台组合机床于1908年在美国问世,距今已有一百多年的历史了,组合机床能对不同零件不同速度加工特别是对于箱体类零件的加工具有特殊优势,因此也成为了现代制造业必不可少的设备之一。
我们国家尽管还不是制造强国,组合机床的发展落后较多,但也有了二十多年的历史,在企业的发展中,高效、低耗的组合机床无疑是会受到大家青睐的。
如今,它已经成为制造企业实现创新,技术改造,提高生产效率必不可少的设备之一。
与此同时,国内所需的一些高水平组合机床及自动线几乎都从国外进口。
设备的大量进口必然导致成本的提高。
因此,为了让这样的情况以后越来越少,也需要我们进行变通,由过去的“刚性”机床结构即一种产品一种机床生产,向“柔性”化方向发展也就是我们组合机床可以满足不同加工需求,满足用户需要,真正成为刚柔兼备的自动化装备。
1.1.2组合机床发展趋势
我国的传统的组合机床及组合机床自动线主要采用机电结合,液压控制,它的加工对象主要是批量比较大的大中型的箱体类和轴类零件,能够完成各种孔的加工,同
时也能加工各种螺纹、键孔、车端面和凸台,在孔内撞各种形状槽,以及铣削平面和成型面等。
组合机床的分类繁多,有大型组合机床和小型组合机床,有单面、多面、卧式、立式、倾斜式、复合式,还有多工位回转台组合机床等。
随着机床技术的发展,柔性组合机床即可以根据不同加工要求变化的机床越来越受到人们的亲睐,它应用于多工位主轴箱、可换主轴箱、编码随行夹具和刀具的自动更换,配以PLC、数字控制等,能任意改变工作循环控制和驱动系统,同时也能灵活适应各种加工情况。
另外,近年来组合机床加工中心、数控组合机床、机床辅机等在组合机床中的发展也越来越快,占比逐渐大了起来。
因此组合机床未来的发展趋势应该是会照着以下几个方面进行:
①更多的应用PLC与数控技术
目前组合机床生产厂家在通用部件和专用部件上都有不错的研究水平,因而在硬件基础够的情况下会着重考虑软件上的提高,例如在组合机床上不仅一般的动力部件可以应用数控和PLC技术,而且夹具的转位或转角、换箱装置的自动分度与定位也都可以应用此类技术,从而进一步提高了组合机床的工作可靠性和加工精度。
②更灵活多变的满足客户需求
在我国从制造大国向制造强国迈进的过程中,制造企业也会越来越发展迅速,因而产品要求也会越来越多样化,越来越精密。
面对不同的制造要求,我们的组合机床这时候就派上了用场,可以想象,在不久后的将来,这种具有柔性化,能灵活多变适应不同加工要求的组合机床,必定会是将来组合机床的发展趋势。
柔性加工自动线的出现既可以实现多品种加工要求,又能使机床配置更加灵活多变。
③进一步提高工序集中程度
国外为了减少机床数量,节省占地面积,对组合机床这种工序集中程度高的产品,继续采取各种措施,进一步提高工序集中程度。
如采用十字滑台、多坐标通用部件、移动主轴箱、双头铿孔车端面头等组成机床或在夹具部位设置刀库,通过换刀加工实现工序集中,从而可最大限度地发挥设备的效能,获取更好的经济效益。
在这些方面我国组合机床装备还有相当大的差距,因此我国组合机床技术装备高速度、高精度、柔性化、模块化、可调可变、任意加工性以及通信技术的应用将是今后的发展方向。
1.2液压技术和PLC在其中的应用
1.2.1液压技术在其中的应用
组合机床由系列化和标准化的通用部件为基础,配以专用部件对一种或多种的工件进行加工的机床,兼有万能机床和专用机床的有点。
通用部件通常占比较多,但专用部件也很重要,其中通用部件有动力箱、动力滑台、支撑件、输送部件。
而专用部件则包括主轴箱和夹具。
液压系统由于具有结构简单、多做灵活、操作方便、调速范围大、可无极连续调节等优点因而在组合机床中得到了广泛的应用。
其中动力滑台运动靠液压缸驱动,通过液压回路配合刀具进行不同的动作。
液压回路中运用到的各种液压技术包括回路设置,原件选用都会大大的影响动力滑台运动从而影响到刀具的运动、进给。
例如通过设置差动连接使活塞杆快速动作,选用电液换向阀使换向平稳等。
1.2.2PLC在本课题中的重要意义
在前不久,我国才提出了工业2.0的概念,而由于西方国家的已经在工业3.0的发展道路上,甚至德国已经提出了工业4.0的概念。
我国需要和国际社会接轨,因而现在可以说处在2.0与3.0并存的时代,这更要求了我们对机电一体化的运用。
为了提高生产效率、节省企业成本,同时也为了顺应时代发展,我们也应该将PLC和NC(数控技术)应用在现有的机床研究、应用中。
同时PLC也具有传统继电器所不具有的优点。
传继电器控制,一旦线路安装完成,则如要改变其控制功能非常复杂,费时费力,而采用PLC控制后,只要改变控制程序,不需对外部电路接线进行改动,即可适应不同的控制要求。
方便快捷,节省成本。
有全套CAD/CAXA图纸以及外文翻译,有需要的同学联系Q1197053443
第2章液压系统设计
2.1设计内容和方案确定
2.1.1设计内容
专用立式组合机床动力滑台液压系统的工作动作循环为:
快进—工进—快退—原位停止。
切削总力为28000N,要求为快进、快退的速度为6m/min,工进的速度为50mm/min,动力滑台的质量1500kg快速行程为100mm.工进行程为50mm,动力滑台往复加减速时间为0.05s。
动力滑台用平面导轨,静摩擦系数0.2;动摩擦系数为0.1。
可在动力滑台任意位置停止.
2.1.2液压传动方案确定
通过查阅资料得到了YT4543液压动力滑台液压系统的工作原理图如图2.1所示:
1、执行元件的选择
根据加工要求,刀具旋转由机械传动来实现;主轴头导轨中心线方向的“快进-工进-快退-停止”工作循环拟采用液压传动方式来实现。
故拟选定液压缸作执行机构。
图2.1YT4543液压原理图
2、回路选择
①快速运动回路
为了实现快速运动,有两个方案可供选择:
1>双泵供油2>差动连接。
在这里选择差动连接的方式,仅仅通过一个行程阀和一个单向阀就可以使回油路的液压油再次回到进油路实现快速运动,故沿用YT4543差动连接的方式,用元件少,节省成本,快速运动性能好,提高效率。
②调速回路
节流调速回路的工作原理是通过改变回路中流量控制元件(节流阀和调速阀)通流截面的大小来控制流入执行元件或自执行元件流出的流量,以调节其运动速度。
根据流量阀在回路中的位置不同,分为进油节流调速、回油节流调速和旁路节流调速三种回路。
在本次设计中,选择进油路节流调速回路。
③换向回路
根据系统设计平稳性需要,选择三位五通电液换向阀作为换向回路关键部件。
首先,为了满足系统需要的换向和在停止时的卸荷功能因而选用五通阀,三个工作机位能保证进油,回油以及中位停止的顺利运行。
同时电液换向阀的平稳性也作为选择时的一个考虑重点。
④平衡回路
考虑到本次设计是立式组合机床的动力滑台液压系统设计,因此要考虑到液压缸的一个平衡问题,为了使液压缸平衡问题得到解决,在回油路设置一个如图2平衡回路,平衡重力带来的相关问题。
图2.2
3.液压原理图和电磁铁动作顺序表
根据上一步所选的各种回路,配以必要的安全设置如背压阀、压力表等,组成了如下图2.3的初步确定的液压原理图。
图2.3液压原理图
1.油箱2.滤油器3.变量泵4、9、12.单向阀5.电液换向阀6.背压阀7.顺序阀8.压力表10.调速阀11.压力继电器13.行程阀14.液压缸15.调压阀
电磁铁和行程阀动作顺序表2.1
动作
1YA
2YA
行程阀
快进
+
-
-
工进
+
-
+
快退
-
+
+
停止
-
-
-
考虑到本次设计的组合机床主要是用于孔的加工,对于位置的要求比较高,因此设置了一个压力继电器,当滑台与死挡铁接触后,压力继电器收到信号即使三位五通电磁换向阀5的换向。
有全套CAD/CAXA图纸以及外文翻译,有需要的同学联系Q1197053443
2.2工况分析
2.2.1动力分析
为了让动力滑台按照需要进行匀速运动,其所受的的总负载应该要和液压缸所给的驱动力互相平衡,此时加速度为0,动力滑台实现匀速运动。
因此需要对动力滑台主要负载进行分析,其主要承受载荷包括工作负载、惯性负载和机械摩擦阻力。
①工作负载Fw
对于金属切削机床液压系统,沿缸轴向切削为工作负载Fw
∴Fw=28000N(式2-1)
②惯性负载Fm
最大惯性负载取决于移动部件的最大质量和最大加速度,其中最大加速度可通过工作台最大移动速度和加速时间进行计算。
已知往复加减速时间最大为,工作台最大移动速度即快进和快退速度为,
已知
因此惯性负载为:
∴
=300N(式2-2)
③摩擦负载
最主要存在摩擦的地方在于工作台,因而工作台与滑台产生的机械摩擦阻力是摩擦负载的主要组成部分,分为静摩擦阻力和动摩擦阻力(g=9.8m/)。
静摩擦阻力
=
×N=2940N(式2-3)
动摩擦阻力
=
×N=1470N(式2-4)
取液压系统机械效率为0.9,因此可以列出工工作阶段所受外力负载
外力负载表2.2
工况
负载组成
负载值F(N)
液压缸推力F`=F/0.9
快进
1470
1633
工进
19470
32744
快退
1470
1633
启动
2940
3267
加速
1770
1967
2.2.2速度和负载循环图
根据计算后表2.2中的数据可以绘制出本次设计中液压系统的负载循环图如图2.4所示。
由图2.4能够看出,当动力滑台处于工进状态的时候,负载力是最大的,达到了32744N,而在快进和加速等阶段负载力比较小。
因而根据计算所得数据,可得出如2.5所示的动力滑台液压系统速度循环图。
有全套CAD/CAXA图纸以及外文翻译,有需要的同学联系Q1197053443
速度循环图图2.4负载循环图图2.5
2.3液压缸主要参数计算
2.3.1确定液压缸主要尺寸
①初选液压缸工作压力
由负载循环图2.5可知在系统工作是,工进阶段是负载最大的时候,可达到32744N,因此选择液压缸工作压力为3.5Mpa。
②确定液压缸主要尺寸
由于工作进给速度与快进差别相差比较大,快退和快进速度却一样,所以在液压缸选用时选择了单缸采用差动连接的方式,通常利用差动液压缸活塞杆较粗、可以在活塞杆中设置通油孔的优势条件,故而选择活塞杆固定,而液压缸缸体随滑台运动的常用安装方法。
在这种情况下,可知液压缸应设计成无杆腔的工作面积为有杆腔的二倍,所以活塞杆直接为缸筒直径的倍。
同时考虑到组合机床多对于孔类零件进行加工,当孔被加工完成时,负载会突然不再,为了避免液压缸突然前冲,因此液压缸的回油腔设置背压,同理快退时也取相同背压。
而由于快进时同样不可避免的存在着压降,同时要求有杆腔压力必须大于无杆腔,估算时取。
因此由可以推导出无杆腔有效作用面积可计算为
=F/(
-