模具制造工艺复习解析.docx
《模具制造工艺复习解析.docx》由会员分享,可在线阅读,更多相关《模具制造工艺复习解析.docx(9页珍藏版)》请在冰豆网上搜索。
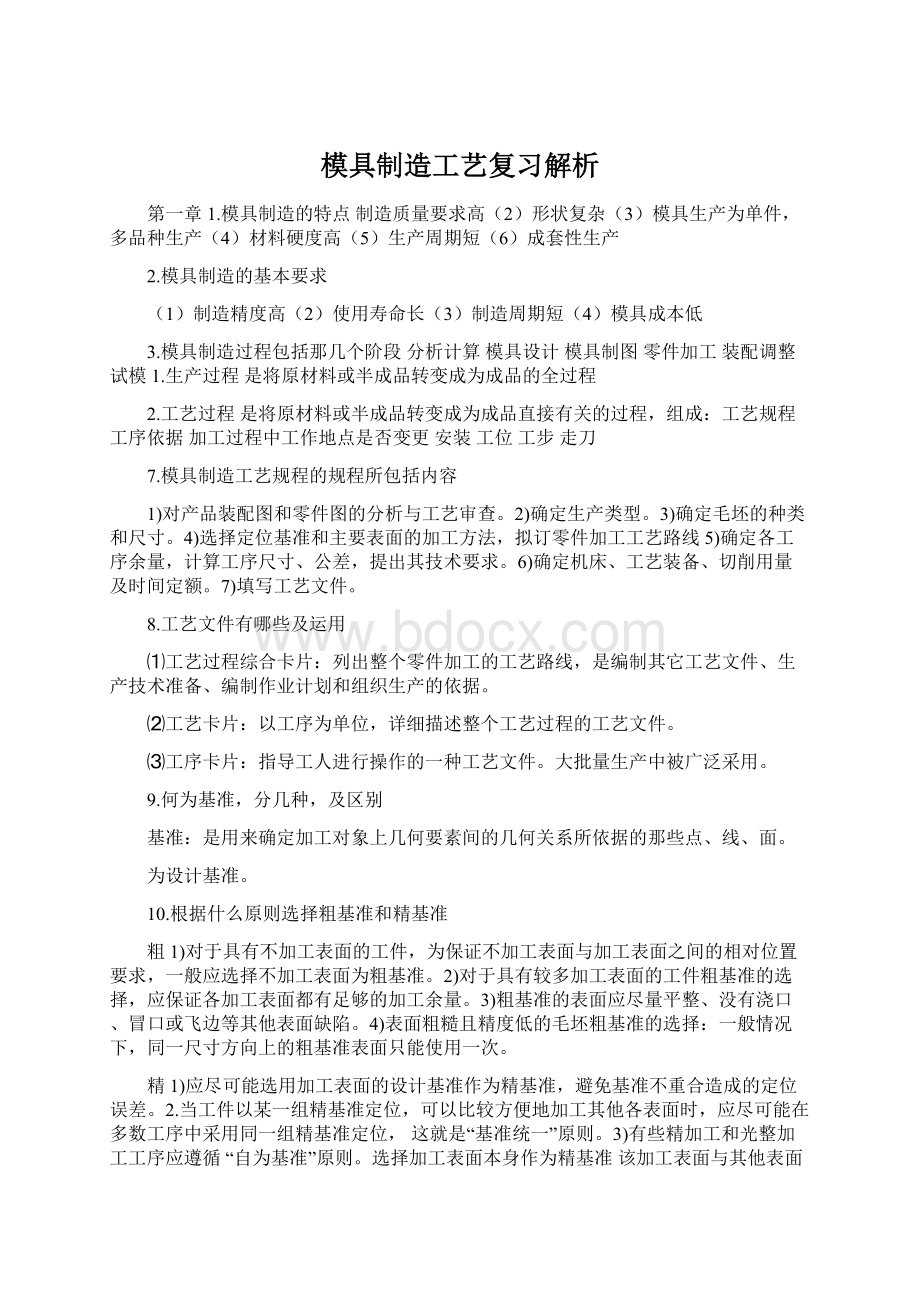
模具制造工艺复习解析
第一章1.模具制造的特点制造质量要求高
(2)形状复杂(3)模具生产为单件,多品种生产(4)材料硬度高(5)生产周期短(6)成套性生产
2.模具制造的基本要求
(1)制造精度高
(2)使用寿命长(3)制造周期短(4)模具成本低
3.模具制造过程包括那几个阶段分析计算模具设计模具制图零件加工装配调整试模1.生产过程是将原材料或半成品转变成为成品的全过程
2.工艺过程是将原材料或半成品转变成为成品直接有关的过程,组成:
工艺规程工序依据加工过程中工作地点是否变更安装工位工步走刀
7.模具制造工艺规程的规程所包括内容
1)对产品装配图和零件图的分析与工艺审查。
2)确定生产类型。
3)确定毛坯的种类和尺寸。
4)选择定位基准和主要表面的加工方法,拟订零件加工工艺路线5)确定各工序余量,计算工序尺寸、公差,提出其技术要求。
6)确定机床、工艺装备、切削用量及时间定额。
7)填写工艺文件。
8.工艺文件有哪些及运用
⑴工艺过程综合卡片:
列出整个零件加工的工艺路线,是编制其它工艺文件、生产技术准备、编制作业计划和组织生产的依据。
⑵工艺卡片:
以工序为单位,详细描述整个工艺过程的工艺文件。
⑶工序卡片:
指导工人进行操作的一种工艺文件。
大批量生产中被广泛采用。
9.何为基准,分几种,及区别
基准:
是用来确定加工对象上几何要素间的几何关系所依据的那些点、线、面。
为设计基准。
10.根据什么原则选择粗基准和精基准
粗1)对于具有不加工表面的工件,为保证不加工表面与加工表面之间的相对位置要求,一般应选择不加工表面为粗基准。
2)对于具有较多加工表面的工件粗基准的选择,应保证各加工表面都有足够的加工余量。
3)粗基准的表面应尽量平整、没有浇口、冒口或飞边等其他表面缺陷。
4)表面粗糙且精度低的毛坯粗基准的选择:
一般情况下,同一尺寸方向上的粗基准表面只能使用一次。
精1)应尽可能选用加工表面的设计基准作为精基准,避免基准不重合造成的定位误差。
2.当工件以某一组精基准定位,可以比较方便地加工其他各表面时,应尽可能在多数工序中采用同一组精基准定位,这就是“基准统一”原则。
3)有些精加工和光整加工工序应遵循“自为基准”原则。
选择加工表面本身作为精基准该加工表面与其他表面之间的位置精度由先行工序保证4)定位基准的选择应便于工件的安装与加工,并使夹具的结构简单。
预备热处理改善加工性能消除内应力为最终热处理做准备
退火正火细化晶粒均匀组织调质淬火加高温回火综合力学性能好粗加工后半精加工前
最终热处理淬火渗碳淬火回火氮化处理提高硬度耐磨性疲劳强度抗蚀
加工顺序的安排先粗后精先主后次基准先行先面后孔
加工余量确定方法经验估算法分析计算法查表修正法
第三章
1.车铣刨磨加工的特点
(1)车A、加工范围广,适应性强,可以加工钢、铸铁及其合金、铜、铝等有色金属和某些非金属材料。
B、可以加工单一轴线的零件,也可以加工曲轴、偏心轮或盘形凸轮等多轴线的零件。
C、生产率高;刀具简单,其制造、刃磨和安装都比较方便。
1.常用的装夹方法
(1)三爪卡盘装夹:
适用于短轴类、套类、盘类零件,位置精度在0.1mm。
(2)四爪卡盘装夹:
适用于短轴类、套类、盘类、异形零件,位置精度在0.03mm。
(3)一夹一顶装夹:
适用于中长轴类零件,位置精度在0.05mm。
(4)两顶尖装夹:
适用于中长轴类零件,位置精度在0.03mm
仿形车削是采用仿形装置使车刀在纵向走刀的同时,又按预定的轨迹横向走刀,通过纵向走刀和横向走刀的复合运动,从而完成模具零件的复杂旋转曲面的内外形加工。
(2)铣
(1)生产率较高
(2)铣削过程不平稳(3)刀齿散热较好靠模和仿形销选择
)靠模材料:
非金属材料:
如木材、石膏、树脂
金属材料:
钢、铸铁、铜合金、铝合金
仿形触头直径D与铣刀直径d的关系:
D=d+2(Z+e)
式中:
d—铣刀直径
e—仿形触头偏移修正量,精仿时,e=0.05~0.1mm
Z—加工后修正余量:
Z>0,留有半精加工或精加工余量;Z=0,精加工成型;Z<0,改变型腔尺寸
(3)刨
(1)刨削特别适合于加工狭长平面。
(2)刨床结构简单,调整和操作都较方便;刨刀为单刃刀具,制造和刃磨较容易,价格低廉。
所以,刨削生产成本较低。
(3)由于刨削主运动是直线往复运动,刀具切入和切离工件时有冲击负载,因此,限制了切削速度的提高,此外,还存在空行程损失,因此刨削生产效率较低。
(4)刨削的加工精度通常为IT9~IT7,表面粗糙度值为12.5~1.6;采用宽刃刨刀精刨时,加工精度可达IT6,表面粗糙度值Ra为0.8~0.2µm。
(4)磨1)具有很高的加工精度和很小的表面粗糙度值。
加工精度通常可达IT6~IT5,表面粗糙度值一般为Ra0.8~0.01μm。
2)砂轮磨料具有很高的硬度和耐热性,因此,能够磨削一些硬度很高的金属和非金属材料,如淬火钢、硬质合金、陶瓷材料等。
这些材料用一般的车、铣等很难加工。
3)磨削速度大,磨削时磨削区温度可高达800~1000℃左右,这容易引起零件的变形和组织的变化。
所以在磨削过程中,需进行充分的冷却,以降低磨削温度。
4)砂轮在磨削时具有“自锐作用”。
在磨削力的作用下会部分磨钝的磨粒能自动崩碎脱落,从而形成新切削刃口,从而使砂轮保持良好的磨削性能。
粗磨用颗粒较粗的砂轮,以提高生产效率;精磨用颗粒直径较小的砂轮,以减小已加工表面粗糙度值。
◆当工件材料软,塑性大,磨削面积大时,采用粗粒度,以免堵塞砂轮烧伤工件。
◆成形磨削和高速磨削时应选用细粒度砂轮。
砂轮硬度选择原则:
1.磨削硬材,选软砂轮;磨削软材,选硬砂轮;
2.磨导热性差的材料,不易散热,选软砂轮以免工件烧伤;
3.砂轮与工件接触面积大时,选较软的砂轮;
4.成形磨精磨时,选硬砂轮;粗磨时选较软的砂轮。
(5)镗镗削加工是利用镗刀对已有孔、孔系进行再加工的方法。
特别适合于箱体、支架、杠杆等零件上的单个孔或孔系的加工
第四章
1.数控机床加工的特点1)加工精度高
(2)自动化程度高和生产率高(3)适应性强4)有利于生产管理现代化(5)减轻劳动强度,改善劳动条件6)成本高
2.Nc数控技术cnc计算机数控
3.与普通机床的区别能加工普通机床难以加工的复杂型面按预先编写的零件加工程序自动加工加工精度可以通过软件进行校正和补偿生产效率可提高2.3倍一般使用通用夹具可实现一机多用减少在制数量劳动强度成本核算和生产精度安排
4.组成控制介质数控装置伺服系统机床本体
5.图样程序数控装置伺服机构机床本体工件
第五章
特种加工是直接利用电能、化学能、光能和声能对工件进行加工,以达到一定的形状尺寸和表面粗糙度要求。
电火花加工的原理是基于工具电极与工件电极(正极与负极)之间脉冲性火花放电时的电腐蚀现象来对工件进行加工,以达到一定形状、尺寸和表面粗糙度要求
要利用电腐蚀现象来加工金属材料,必须具备以下条件
1)足够的火花放电强度。
2)脉冲放电。
3)停歇时间。
4)放电间隙。
5)极间液体介质。
与机械加工相比,有如下特点:
1)材料:
由于脉冲放电的能量密度很高,可以加工任何硬、脆、韧及高熔点的导电材料。
2)切削力:
不存在明显的宏观作用力。
加工时,工具电极与工件不接触,而且工具材料也不必比工件硬。
这不仅有助于工具电极的制造,而且也有利于包括小孔、窄槽在内的各种复杂精密模具的加工,并能在淬火之后进行。
3)热影响区也很小。
脉冲放电的持续时间短,放电时所产生的热量传散范围小。
4)粗、中、精及精微加工可在一台设备上完成。
脉冲参数能在一个较大范围内调节,故可以在同一台机床上连续进行。
精加工时的精度能控制其误差小于±0.01mm,表面粗糙度为Ra0.63~1.25um;
精微加工时的精度可达0.002~0.004mm,表面粗糙度为Ra0.04~0.16um。
5)便于实现自动化。
直接利用电能进行加工
电火花成形加工的速度,是指在一定的条件下,单位时间内工件被蚀除的体积V或质量m。
极性效应
在电火花加工过程中,无论是正极还是负极,都会受到不同程度的电腐蚀。
即使是正负两极材料相同(如用钢电极加工钢工件),也往往会出现正负两极的蚀除速度不一样。
这种由于极性不同而发生蚀除速度不一样的现象叫做极性效应。
极性效应产生的原因:
正负两极表面分别受到电子和正离子的轰击而蚀除金属。
负离子(电子)的质量,容易获得很高的加速度和速度,很快奔向正极,并轰击正极表面而蚀除金属。
而正离子则因质量和惯性较大,起动较慢,到达负极的速度低,能量小。
小间隙加工,正极蚀除速度大。
窄脉冲精加工正极性
在电火花成形加工时,工作液的作用是:
①介电作用。
工作液一般都具有一定的介电能力,有助于产生脉冲式的火花放电,形成放电通道,放电结束之后又能恢复极间绝缘状态。
②压缩放电通道,提高火花放电能量密度。
帮助电蚀产物的抛出和排除。
④冷却工具与工件和极间放电通道余热。
影响电火花成形加工精度的因素很多,主要有机床本身的制造精度、工具电极制造精度、工具与工件的装夹定位误差以及仿形加工过程所产生的放电间隙、电极损耗等。
1.斜度,圆角出现的原因
斜度电火花加工时侧面产生斜度,使上端尺寸大而底端尺寸小。
这是由于“二次放电”和电极损耗而产生的。
,由于电蚀产物的混入而使极间实际距离减小或是极间工作液介电性能降低,而再次发生脉冲放电现象,使间隙扩大。
在进行深度加工时,上面入口处加工的时间长,产生二次放电的机会多,间隙扩大量也大;而接近底端的侧面,因加工时间短,二次放电的机会少,间隙扩大量也小,因而加工时侧面会产生斜度。
工具电极损耗也会产生斜度。
因为工具电极的下端加工时间长,绝对损耗量大,而上端加工时间短,绝对损耗量使电极形成一个有斜度的锥形电极。
而冲裁模凹模的加工,斜度是有用的。
圆角电火花加工时,工具电极上的尖角和凹角,很难精确地复制在工件上,而是形成一个小圆角。
这是因为当工具电极为凹角时,工件上对应的尖角处放电蚀除的机率大,容易遭受腐蚀而形成圆角。
充分利用极性效应:
1)电火花成形加工必须采用单向脉冲电源。
否则,采用正负双向脉冲电源将相互抵消其极性效应的作用。
2)正确选择加工极性3)用导热性好、熔点高的材料作工具电极,以利于降低工具电极耗损。
4)正确脉冲放电能量,合理选用脉冲放电持续时间(即脉宽ton)。
电火花线切割加工原理与电火花成形加工的原理相同,都是基于电极间脉冲放电时的电火花腐蚀原理:
极间液体介质被击穿以后形成火花放电,以实现尺寸加工的目的。
所不同的是,电火花线切割加工是用连续移动的电极丝作为工具,工件则按预定的轨迹进行运动而“切割”出所需的复杂零件电火花线切割加工只能加工以直线为母线的曲面,而不能加工任意空间曲面。
线切割加工工艺流程下料→锻造→退火→刨平面→磨平面→划线→铣漏料孔→孔加工→淬火→磨平面→线切割
坯料的准备工艺参数的选择工件的装夹与调整电极丝的选择和调整
2.电火花线切割加工特点,运用范围
特点没有复杂的电极、工件材料被蚀除的量很少、能够方便地加工各种复杂的精密零件加工精度高、多使用精规准
运用范围1)加工冲模,包括大、中、小型冲模的凸模、凹模、固定板、卸料板等。
2)加工粉末冶金模、镶拼型腔模、拉丝模、波纹板成形模、冷拔模等。
3)加工样板、成形刀具、电火花成形加工电极等。
4)加工微细孔、槽、窄缝等,如异形孔、喷丝板、射流元件、激光器件等的微孔窄缝以及微型零件。
5)加工和切割稀有贵重金属材料等。
超声波加工原理利用工具端面作超声(16~25kHz)振动,使工作液中的悬浮磨粒对工件表面撞击抛磨来实现加工。
,特点,运用范围特点
1.适于加工各种硬脆材料,特别是非金属材料,如陶瓷、玻璃及各种半导体材料。
2.宏观切削力小,不易引起变形和烧伤,适于加工薄壁、窄缝、低刚度零件。
3.加工精度高,表面质量好。
4.加工机床及工具简单。
5.生产率比电火花、电解加工等低。
应用:
主要用于对硬脆材料加工圆孔、型孔、套料/微细孔,对电火花加工后的各种模具进行抛/磨光整加工等。
电解加工是利用金属在电解液中的“电化学阳极溶解”来加工工件的。
。
特点电解加工与其他加工方法相比较,具有如下优点:
1)材料适应性广。
电解加工与被加工材料的硬度、强度、韧性等无关,故可加工任何金属材料。
2)能以简单的直线进给运动,一次加工出复杂的型腔、型孔(如锻模、叶片等)。
3)生产率较高,约为电火花加工的5~10倍。
4)加工表面质量好,无毛刺和变质层。
5)加工过程中阴极工具在理论上不会损耗。
电解加工的局限性在于:
1)不易达到较高的加工精度和加工稳定性,也难以加工出棱角,一般圆角半径都大于0.2mm。
2)电解加工设备投资大,占地面积大;设备的锈蚀也严重;单件小批量生产时成本比较高。
3)电解产物必须进行妥善处理,否则将污染环境。
电解加工的应用于深孔扩孔、内孔来复线(膛线)以及内齿轮和叶片加工等,同时在模具制造行业也得到广泛应用,主要有锻模型腔加工、硬质合金拉丝模穿孔以及模具电解抛光等。
分类电火花穿孔成型加工,电火花线切割,电火花磨削和镗削,电火花同步共轭回转加工,电火花高速小孔加工,电火花表面强化与刻字
第八章
1.快速成型技术的基本原理配
它采用离散堆积成型原理,根据三维CAD模型,对不同的工艺要求,按一定厚度进行分层,将三维数字模型变成厚度很薄的二维平面模型,再将数据进行一定的处理,输入加工参数,产生数控代码,在数控系统控制下以平面加工方式连续加工出每个薄层,并使之黏结而成型。
4.快速成型特点
(1)快速性
(2)自由性(3)高度柔性:
(4)设计制造一体化(5)材料的广泛性(6).技术的高度集成性
代号SL(光固化)SLS(选择性激光烧结)LOM(切纸叠层)FDM(熔融挤丝3DP(三维打印)
第六章
模具零件工艺过程制定的步骤工艺分析毛坯选择表面加工方案确定工艺路线制定确定工序余量尺寸制定零件工艺过程
主要表面加工方案Ra0.4µm
粗车—半精车—粗磨—精磨¢32h6Ra0.1µm
粗车—半精车—磨削—精磨—研磨
外圆粗车—半精车—粗磨—精磨
内孔钻—粗镗—精镗—粗磨—精磨—研磨
钻—粗镗—半精镗—精镗
粗刨/铣—半精刨/铣—粗磨
下料—锻造—退火—铣六面—磨六面—划线/作螺纹孔/漏料孔/穿丝孔—热处理—线切割内外形—研磨内外形
复习题
1.电火花加工参数有哪些,影响加工速度因素有哪些,各自产生什么影响
电参数脉冲宽度能量大极性效应强峰值电流击穿电压
①正比于单脉冲能量和脉冲放电频率;
②用矩形波脉冲加工时,加工速度正比于脉冲电流幅值Im和脉冲放电持续时间ton,亦即正比于平均放电电流。
2.特种加工使用范围,材料对象。
特种加工可以加工任何硬度、强度、韧性、脆性的金属或非金属材料,且专长于难加工的材料及复杂零件的加工问题,同时,有些方法还可以用于进行超精加工、镜面光整加工和纳米级加工。
3,快速成型技术优缺点
优点利用快速成形技术可对产品设计进行迅速评价、修改,并自动快速地将设计转化为具有相应结构和功能的原型产品或直接制造出零部件,从而大大缩短新产品的开发周期,降低产品的开发成本,使企业能够快速响应市场需求,提高产品的市场竞争力和企业的综合竞争力。
3.加工孔的加工方法有,区别
钻、扩、铰、镗、车
钻孔一般要占机械加工厂切削加工总量的30%左右。
钻削的精度较低,表面较粗糙,生产效率也比较低。
扩孔除了可用做高和较高的孔的预加工外,还由于其加工质量比钻孔高,可用于一些要求不高的孔的最终加工。
铰孔是应用较为普遍的孔的精加工方法之一,一般加工精度可达IT9-IT7,表面粗糙度度值Ra为0.4~1.6.镗削使用的刀具——镗刀。
一般镗孔精度可达IT7~IT9,精镗可达到IT6,粗糙度为Ra0.8~1.6μm。
除浮动镗削外,镗孔能纠正孔的直线度误差,获得高的位置精度,特别适合于箱体、支架、杠杆等零件上的单个孔或孔系的加工。
车削加工精度一般为IT8~IT7,表面粗糙度为Ra6.3~1.6μm;精车时,加工精度可达IT6~IT5,粗糙度可达Ra0.4~0.1μm。
4.车铣刨刀,砂轮,钻头刀具各自的特点(硬度,耐热,耐磨
1.刀具材料的基本要求
高硬度HRC60以上,高于工件1.3~1.5倍。
耐磨性通常情况下材料硬度高时,耐磨性也高。
强度和韧性材料硬度越高,其抗弯强度和冲击韧性就越低。
耐热性刀具材料的高温硬度是衡量刀具材料切削性能重要指标。
工艺性便于制造和使用
磨:
粗磨用颗粒较粗的砂轮,以提高生产效率;精磨用颗粒直径较小的砂轮,以减小已加工表面粗糙度值。
当工件材料软,塑性大,磨削面积大时,采用粗粒度,以免堵塞砂轮烧伤工件。
成形磨削和高速磨削时应选用细粒度砂轮。
1.磨削硬材,选软砂轮;磨削软材,选硬砂轮;2.磨导热性差的材料,不易散热,选软砂轮以免工件烧伤;3.砂轮与工件接触面积大时,选较软的砂轮;4.成形磨精磨时,选硬砂轮;粗磨时选较软的砂轮。
5.特种加工针对的材料对象
6.工序和工步怎么划分
1工序是工艺规程的基本单元;工序是指一个(或一组)工人,在一个固定的工作点(如机床或钳工台),对一个(或同时几个)工件所连续完成的那部分工艺过程。
划分依据:
零件在加工过程中工作地点(或机床)是否发生变更。
(2)工步在一个工序内,当加工表面、切削工具和切削用量中的转速与进给量均不变时,所完成的那部分工序称为工步。
电火花参数制定方法
7.刨削与铣削区别刨削与铣削加工的比较:
加工质量大致相当,经粗、精加工之后均可达到中等精度。
生产率一般刨削低于铣削。
加工范围刨削不如铣削广泛。
工时成本刨削低于铣削。
刨削不如铣削应用广泛。
8.什么叫特种加工,仿形加工,成型加工,快速加工
特种加工是直接利用电能、化学能、光能和声能对工件进行加工,以达到一定的形状尺寸和表面粗糙度要求。
仿形铣削以事先制成的靠模为依据,加工时触头对靠模表面施加一定的压力,并且沿其表面上移动,通过仿形机构,使刀具作同步仿形动作,从而在模具零件上加工出与靠模相同的型面。
快速成形就是由三维转换成二维(用软件将三维模型离散化),再由二维到三维(材料堆积)的工作过程。
成型加工:
成型车削加工是采用成型车刀的仿形车削方式对具有特殊型面的模具零件进行加工,即工件形状由成行车刀保证。
镗的方法,两种镗刀工艺特点
1.单刃镗刀工艺特点
(1)结构简单,有较大的灵活性和较强的适应性。
(2)可以校正底孔轴线的偏斜和位置误差。
(3)镗杆刚性差,切削用量小,生产效率低。
2.浮动镗刀工艺特点
(1)镗刀片径向浮动,加工精度高。
(2)镗刀片有修光刃,表面加工质量高。
3)镗刀片两切削刃同时工作,生产效率高。