熟料质量控制及煅烧方面的影响因素整理精品范本.docx
《熟料质量控制及煅烧方面的影响因素整理精品范本.docx》由会员分享,可在线阅读,更多相关《熟料质量控制及煅烧方面的影响因素整理精品范本.docx(8页珍藏版)》请在冰豆网上搜索。
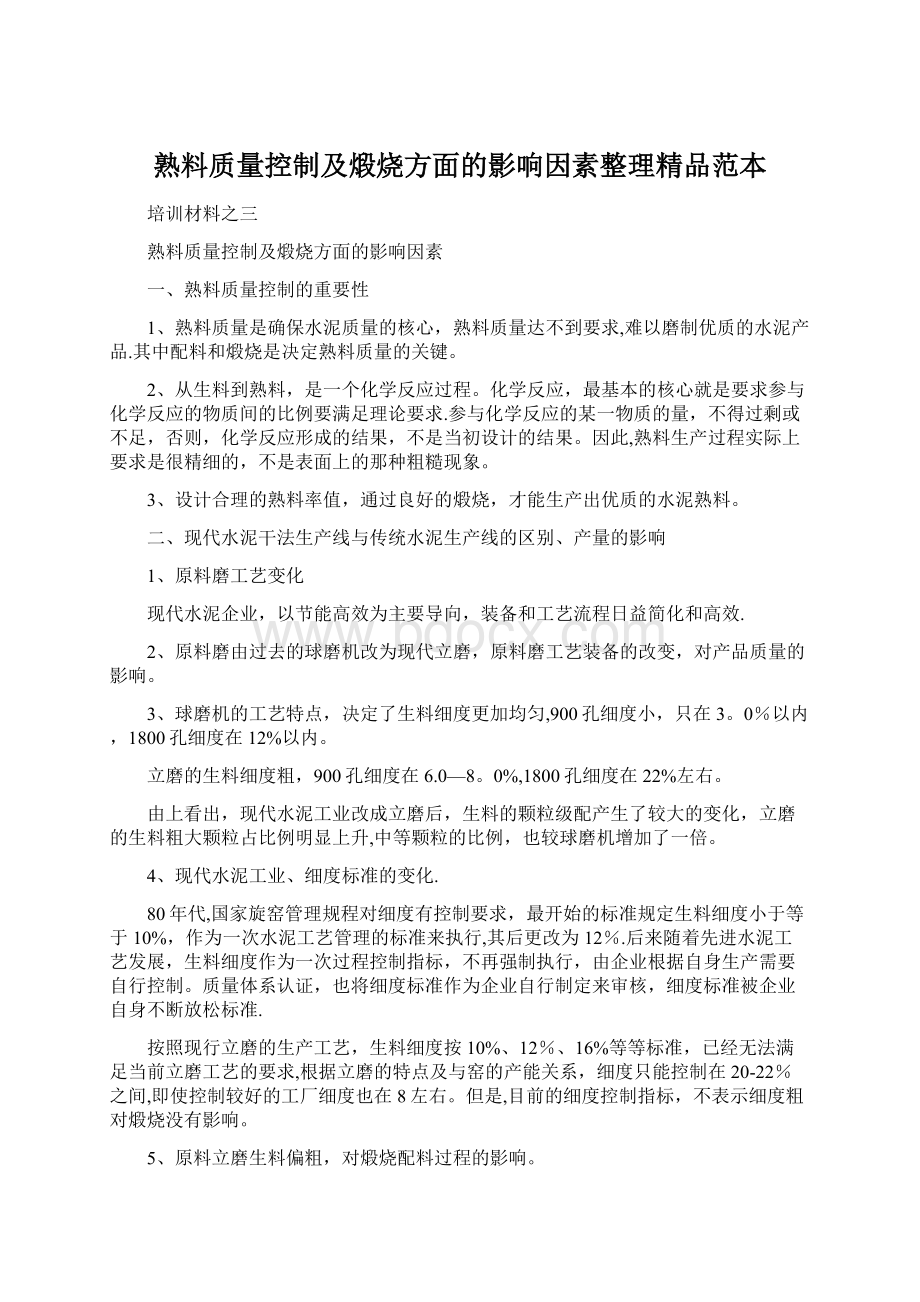
熟料质量控制及煅烧方面的影响因素整理精品范本
培训材料之三
熟料质量控制及煅烧方面的影响因素
一、熟料质量控制的重要性
1、熟料质量是确保水泥质量的核心,熟料质量达不到要求,难以磨制优质的水泥产品.其中配料和煅烧是决定熟料质量的关键。
2、从生料到熟料,是一个化学反应过程。
化学反应,最基本的核心就是要求参与化学反应的物质间的比例要满足理论要求.参与化学反应的某一物质的量,不得过剩或不足,否则,化学反应形成的结果,不是当初设计的结果。
因此,熟料生产过程实际上要求是很精细的,不是表面上的那种粗糙现象。
3、设计合理的熟料率值,通过良好的煅烧,才能生产出优质的水泥熟料。
二、现代水泥干法生产线与传统水泥生产线的区别、产量的影响
1、原料磨工艺变化
现代水泥企业,以节能高效为主要导向,装备和工艺流程日益简化和高效.
2、原料磨由过去的球磨机改为现代立磨,原料磨工艺装备的改变,对产品质量的影响。
3、球磨机的工艺特点,决定了生料细度更加均匀,900孔细度小,只在3。
0%以内,1800孔细度在12%以内。
立磨的生料细度粗,900孔细度在6.0—8。
0%,1800孔细度在22%左右。
由上看出,现代水泥工业改成立磨后,生料的颗粒级配产生了较大的变化,立磨的生料粗大颗粒占比例明显上升,中等颗粒的比例,也较球磨机增加了一倍。
4、现代水泥工业、细度标准的变化.
80年代,国家旋窑管理规程对细度有控制要求,最开始的标准规定生料细度小于等于10%,作为一次水泥工艺管理的标准来执行,其后更改为12%.后来随着先进水泥工艺发展,生料细度作为一次过程控制指标,不再强制执行,由企业根据自身生产需要自行控制。
质量体系认证,也将细度标准作为企业自行制定来审核,细度标准被企业自身不断放松标准.
按照现行立磨的生产工艺,生料细度按10%、12%、16%等等标准,已经无法满足当前立磨工艺的要求,根据立磨的特点及与窑的产能关系,细度只能控制在20-22%之间,即使控制较好的工厂细度也在8左右。
但是,目前的细度控制指标,不表示细度粗对煅烧没有影响。
5、原料立磨生料偏粗,对煅烧配料过程的影响。
立磨工艺的使用,生料细度的变化,在配料过程中,已经有了明显的变化,并且对配料的稳定性,产生了较大的影响。
以原宁国水泥厂一线4000吨窑为例,原宁国水泥厂一线窑配套原料磨系统是球磨机,生料细度一直在10%以内,后来逐渐放宽到12%和16%.
最显著的区别在于原料磨停机后,出窑熟料KH下降,一般由0.89下降到0.86.这符合理论计算值,因为有煤灰掺入。
而我们现代水泥窑,使用立磨的系统,原料磨停机后,熟料KH由0.89上升到0。
91,不得不采用增加搭配煤的比例或其他手段来调整,这不仅是池州存在这个问题,所有的基地,都大致存在这个问题,给生产控制带来较大的麻烦增加了控制难度。
因为原料磨是要预检修的,运转率不可能跟窑一样达到92%.
6、立磨系统停机后,出窑熟料成份偏高的原因:
从理论上说,原料磨停机后,熟料成份应该下降,因为回灰中增加了煤灰的掺入量。
但实际结果是回灰成份很高,回灰中的生料KH达到1.2以上,原因在哪里?
主要原因就是立磨生料的颗粒结构变化,大颗粒偏多,其中硅质材料,像砂岩,易磨性差,粗颗粒大部分是硅质材料。
在预热器系统产生颗粒分配。
粒大颗粒基本入窑内,而较细的颗粒出预热器被回收,这部分回灰主要是含钙较高的成份,其生料KH达1.2以上,导致磨长时间不开,窑内熟料成份越来越高。
曾经做过一个试验,生料KH1.05,将该生料通过0.08mm方孔筛进行筛余冲洗,将粗粉留下烘干化学分析,结果粗粉的生料KH只有0.80左右,这说明生料中不同的颗粒级配,其化学成份是有很大的差别的。
7、立磨系统对窑煅烧影响的调控方法:
立磨系统入窑生料经过预热器后,有分级现象,导致回灰成份偏高,如何控制好入窑生料成份稳定,保持出窑熟料率值稳定,最有效的方法是磨机长时间的预检修,必须事先与质量部门进行沟通,确定具体的停磨时间.质量控制采用提前三小时,对出磨生料成份进行预先调整,此期达到磨停后,入窑生料成份变化不大,满足出窑熟料率值要求,当然,提前控制几个小时,取决于均化库的料位,均化库料位越高,要求超前降生料的时间越长。
三、煤磨系统由球磨机改为立磨系统后,对熟料煅烧的影响
1、传统的水泥厂,煤磨系统是球磨机,煤粉细度基本在5%以下(1800孔)
而现代立磨系统,煤粉细度基本在12%左右,最显著的影响是煤粉细度变粗后,着火点温度要求高、火焰变长,要求煤质优良,否则不易煅烧,立磨无法使用劣质煤,只能用燃烧性能较好的。
优质煤挥发份在22%以上。
因此,后期新建的企业,煤磨选型又回归到球磨.但初期的立磨,确实对熟料质量的控制产生了较大的影响.
以上是从新型干法线装备方面的变化,来谈谈对熟料质量控制和煅烧的影响。
四、熟料质量管理需要掌握的要点
1、选择好适合的生、熟料率值
生熟料率值的选择,无非是为了控制好熟料的三天和二十八天强度,同时保证窑能够正常煅烧,有利于提高窑的产量。
因此,配料的目的是为了有效保证熟料的质量满足要求,还要保证窑能正常运行。
2、生、熟料率值如何选择设定
熟料中C3S和C3A是决定熟料三天强度的要要矿物,较高的熟料KH、较高的C3A含量,均能有效保证熟料三天强度达到30MPa以上,这在目前各水泥企业不是难点,控制方法比较统一,无非是熟料KH高了,窑烧不合格,熟料f—CaO高,熟料f—CaO一旦不合格,分析原因,可能比较复杂。
对于原材料比较正常,目前的水泥企业,熟料率值的经典值一般是下面这种配料方案:
SiO2Al2O3Fe2O3CaOMgO合计KHSMIM
21.955。
453。
4566。
21。
2598。
30.912.461。
57
大多数水泥企业与这个熟料方案大同小异,区别不大,这个配料方案的好处是,三天强度能达到30MPa以上,后期强度,在窑煅烧较好的前提下,也能达60MPa左右。
这是比较大众化的配料方案,一般原材料较好的企业,建议采用。
3、对于一些熟料后期强度低的工厂,熟料率值选型的难点
作为配料管理,率值的选择,三天强度不是难度,困难的是熟料后期强度。
熟料后期强度。
一些资源较好的企业。
后期强度不成问题,但一些资源较差的企业,遇到了很大的困难。
4、影响熟料后期强度的因素:
在熟料的矿物组成中,单一矿物的强度绝对值,C3A是最低的,虽然C3A早期强度高,但后期无增长,因此,C3A是熟料后期强度影响的矿物之一.MgO在熟料中也占有一定的含量,该物质对熟料后期强度无支持,且后期水泥膨胀,对熟料后期强度有破坏作用。
三是熟料矿物的晶体发育是否良好,是熟料后期强度能否均匀,稳定增长的关键.弄清楚了上述三个原因,在配料上可以针对自身原材料的特点和熟料后期强度情况,有针对性的调整,特别是原材料品质较差的企业,可以有效提高自身熟料的后期强度。
4、几个方面的误区:
1)硅酸率越高越好,硅酸率越高,后期强度越高
这是一个误区,硅酸率SM高一点,一般来讲,C3S、C2S含量要高一些,但是,还要考虑构成熟料后期强度的主要矿物的生存环境,其所在这种环境中的发育状况是否良好。
①举一个例子:
SiO2Al2O3Fe2O3CaOMgOKHSMIM28天强度
22.484.084。
3466。
610.790.9272。
670。
9452MPa
22.233.894.9366.411。
370。
9362。
520.7958MPa
这是一个Ⅱ/Ⅴ型熟料经典的例子,第一种方案生产了将近三个月,后期强度急骤下降,最低的只有51MPa,高的也只有54MPa,这个熟料,烟台三菱也生产了好长时间,烟台三菱的熟料SM更高,平均达到2.75以上,但是,后期强度只有51MPa左右,长期承受后期强度偏低的影响,最后不得不停止生产。
当然,烟台三菱不生产Ⅱ/Ⅴ型熟料也还有其他方面的原因,上面的例子反应出并不是硅酸率越高越好。
上面两种熟料后期强度的差别,主要不是矿物含量的率值引起的,而是熟料矿物生存发育的环境引起的,后一种配料方案所生产的熟料,内部结构更均匀,晶体发育匀齐均匀,而前一种熟料矿物晶体发育粗糙,早强高,后期强度增长小.
②再举一个普通熟料因配料方案细微差别引起的熟料后期强度变化:
SiO2Al2O3Fe2O3CaOMgOKHSMIM28天强度
22.205。
203.3565。
901.480。
902.601。
5553MPa
22.104。
853.6565.951.500。
912.601.3260MPa
以上两种配料方案,同样的原料同样的窑同样的煤,熟料中MgO含量相当,熟料f-CaO都合格,在1。
0以内,但熟料后期强度差异较大,差异非常大.单从熟料SM,看不出有多大差别,实际差别很大。
2)误区二:
熟料SM低,后期强度更高
这是不对的,熟料低SM,例如:
熟料SM值2.3左右,后期强度高,只适合较少数原材料特别好的企业,这类企业熟料MgO低,一般在0。
5左右,熟料有效成份很高,而且出窑熟料中晶体发育均匀,否则,一般原料不是很优秀的企业,是不能采用这个配料方案的.
以上的例子,应该对一些石灰石品质差,后期强度长期偏低的企业有些帮助,但要真正控制好熟料的质量,必须是一有个恰当的配料方案,好的煅烧过程,熟料晶体发育均匀缺一不可。
五、新建基地熟料f—CaO的控制及原因分析
新建基地熟料f—CaO控制是个难点,一是新建基地物流不稳,原料磨开停频繁,有堵料现象,二是从质量人员到窑工艺操作,新人多,达不到操作要求,一些是明显的成分波动,比较直观,一些是成份在控制范围,出窑熟料游离氧化钙持续不合格,原因不明,比较困惑,这是新建基地的一个难点,建议从如下几个方面去查找原因,同时不断提高质量控制人员对工艺质量的专业渗透,完善自己的综合技能.
1、检查生料成份是否合理
检查生料成份是否在控制范围内,先要校准荧光仪。
荧光仪一般来说,还是经较准确的,一般在煤质没有大的变化前提下,熟料结果不会漂移,但要注意铁质材料的影响,比喻,用铁矿石、铁粉,再换成复杂的钢渣,一般生、熟料检量线就要校正,防止出现误差.
对于出窑熟料f-CaO不合格,如果成份不在控制范围,明显是配料原因引起的,应尽快调整出磨生料成份.
2、检查窑工艺系统问题
质量管理和窑工艺管理密不可分,在质量控制指标都在范围内的前提下,要及时查找窑工艺和窑操作问题,具体有以下几个方面:
1)检查煤秤喂煤量是否波动
质量主管要多去中控室,检查喂煤曲线是否有较大的波动,如果煤秤波动造成f—CaO不合格,可以暂时排出其他原因。
2)检查中控至操作画面中,篦冷机二次风温
正常窑的煅烧,二次风温应在1100C左右,在工况较好的前提下,二次风温能达到1200C。
3)检查两个五级筒溜管温度
溜管温度是生料入窑前预分解是否有效的标记,一般不要低于865C(这是比较好一点的窑),检查两个五级筒溜管温度是否有较大的温差,不正常的窑,温差大。
4)检查筒扫,看窑内是否结圈或窑皮过厚过长现象
正常窑筒扫温度在22米之前,一般在320C左右,有较小的波动,往后是过渡带,温度在380-400C左右。
隐轮带和大牙轮处外,筒体温度不应该低,否则就有结圈,造成通风不良,窑应减产运行。
5)检查窑头和分解炉喂煤量是否到位或过量
分解炉喂煤检查起来比较直观,可以通过五级筒溜管温度来判断,溜管温度偏低,说明分解炉喂煤不足,预分解差,窑难烧。
窑头煤的判断相对复杂一些,只要窑内没有还原气氛,在f-CaO不合格情况下,窑头可以加煤,如果窑内有还原气氛,加煤熟料f-CaO会更高。
检查窑头煤是否准确,一是看气体分析仪显示的CO含量,但是气体分析仪显示的含量是预热器出口气体,对窑内的判断不是很明显,因为预热器有漏风,建议去看熟料,取整块熟料