QSB+01快速反应.pptx
《QSB+01快速反应.pptx》由会员分享,可在线阅读,更多相关《QSB+01快速反应.pptx(80页珍藏版)》请在冰豆网上搜索。
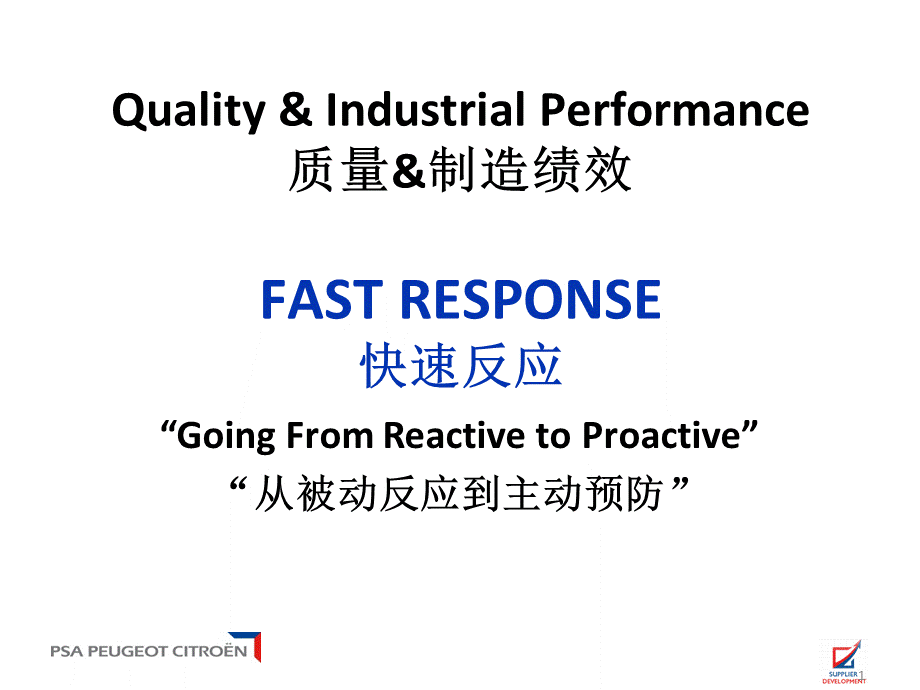
Quality&IndustrialPerformance质量&制造绩效FASTRESPONSE快速反应,1,GlobalPurchasingandSupplyChain,“GoingFromReactivetoProactive”“从被动反应到主动预防”,目的:
及时处理质量缺陷外部/内部定义应遵守的流程定义显示重要信息的方法,作为目视化管理工具,扫一眼就能了解状态通过系统性方法在问题响应时使用准则定义为操作人员提供快速反应的方法,范围:
装配区生产操作发货/收货所有操作其他支持部门,职责:
责任归属业务经理所有情况下的应变计划,介绍,2,快速反应,Benefits益处,提高质量指标降低PPM,保修费用消除问题解决报告,增加客户满意度。
为问题解决(大问题和小问题)提供(简单、普遍的)系统性方法和质量问题交流。
确保每个问题都有指定负责人。
为持续改善提供支持。
落实经验总结的记录。
防止重复性错误,减少资源浪费。
激励组织内部所有相关人员。
建立人人善于解决问题、推动持续改善的文化。
问题是积极改善的机会。
快速反应是一个这样的系统:
对重大外部/内部质量问题的反应进行标准化。
通过对所有问题使用标准记录格式,逐步培养问题解决原则意识。
通过每日会议促进沟通和知识分享。
使用显示重要信息的目视化方法促进关闭。
从客户向上游传递问题鉴定,尽快解决内部问题。
3,快速反应,4,本要素要求一览表,快速反应会查什么?
5,GlobalPurchasingandSupplyChain,快速反应,问题识别在快速反应会准备阶段,在一天开始时,部门应识别出过去24小时的重大问题,包括:
外部问题:
用户关注的问题(问题解决报告,用户抱怨,用户电话,保修)供应商问题(在会上作问题汇报时应提前通知供应商)内部问题:
检验工位发现的问题过程分层审核中发现的体系问题停线问题其他内部质量问题(出货审核,遏制行动)防错装置故障所有重大质量问题都在快速反应板上进行跟踪。
6,快速反应,生产问题:
生产计划vs实际产量:
严重偏差会影响向用户发运健康与安全:
所有安全相关事件事故侥幸未发生的事故没必要在快速反应板上对生产和安全相关问题进行跟踪,但需要行动和后续跟进。
组织架构QRQC会的责任人为生产部门/质量部门,由质量、工程、维护部门和支持人员提供支持。
每天举行,回顾部门收集的重大问题。
有些厂可能每班举行一次。
是交流会,而不是问题解决会。
10-20分钟的站立会议,在生产现场召开。
每个问题都需记录在实际问题解决报告(PPSR)中。
会上固定使用此结构进行报告,保证会议在预定时间内完成。
供应商应在报告最初遏制阶段、问题根源和纠正措施更新时使用标准的问题解决格式。
7,快速反应,职责工厂经理或者指定的生产负责人需要:
确保快速反应过程有效且得到保持指定一名推进人或多人联合推进快速反应会上,现场管理层需要:
为未分配的问题指定一名负责人。
确保与会者提供合适的支持。
为状态为红色的问题明确行动方案和责任人。
未关闭问题需明确下次报告日期。
8,快速反应会示例,快速反应,审核员必须参加快速反应会!
在审核之前安排好相应的快速反应会和日程时间。
如果因供应商原因导致无法参加快速反应会,得0分。
9,GlobalPurchasingandSupplyChain,快速反应,审核员注意事项,是否由生产部门主持并有跨职能的人员参加主持人如何控制FR会议(时间控制在10-20分钟,聚焦于主题,不要深入到细节)环境适宜(每个人可以听见和看见会议)问题是如何汇报的,问题跟踪的查什么?
10,GlobalPurchasingandSupplyChain,快速反应,职责负责人应在会前将新问题更新到看板上(如果是供应商问题,组织与供应商联络)责任人负责保证所有问题及时得到解决和关闭,通过下列手段:
会下多功能小组进行回顾更新快速反应看板的关闭条件和状态栏向小组成员或关键联络人分配更新任务以下每个阶段责任人都需要将改善情况报告给小组:
明确问题,遏制分析根本原因(5-Why)长期/短期纠正措施验证纠正措施,经验总结,11,快速反应,每个问题(内部、用户和供应商)都需记录在实际问题解决报告(PPSR)中。
会上固定使用此结构进行报告,保证会议在预定时间内完成。
供应商应在报告最初遏制阶段、问题根源和纠正措施更新时使用标准的问题解决方式。
12,问题解决报告格式,12,快速反应,13,板可以不同但内容必须相符,14,看板可以是可擦白板,张贴板,或者投影的EXCEL表等,快速反应跟踪板示例,快速反应,回顾要点:
责任归属、关闭条件、总体状态、下次报告日期,为优化目视化管理,看板形式运用于会议区(例,4x8可擦白板,张贴板等),红色和黄色状态包括预计变成绿色的目标日期,GlobalPurchasingandSupplyChain,15,快速反应跟踪板,(,快速反应,ABC公司-质量快速反应跟踪板,16,GlobalPurchasingandSupplyChain,17,关闭条件,状态,问题解决过程的每个关键步骤都应明确关闭条件(核心6步)。
另外,需记录使用过程分层审核进行纠正措施验证,使用防错验证防止问题再现,以及制度化经验总结的关键要素。
典型关闭条件,责任人需在快速反应会上回顾每个关闭条件(管理层批准关闭/绿色状态),17,快速反应,GlobalPurchasingandSupplyChain,18,每个关闭条件都应明确期限,以正确标注问题的红黄绿状态。
当问题刚打开时默认为黄色,直到到期(红色),或完成(绿色)。
在上面的例子里,问题打开时的日期是1月21日。
24小时内实现遏制。
7天内查明根本原因。
纠正措施没能在14天内实施,因此2月14日到期时(本应完成,变成绿色)状态为红色。
这类红色状态应该在行动/状态栏中详细解释,说明下一步方案。
Guideline指导原则,18,关闭条件,状态,快速反应,GlobalPurchasingandSupplyChain,19,总体状态为红色、黄色或绿色单个问题的最差步骤颜色列在下方,预计关闭日期应以30天作为目标。
最长为40天。
19,关闭条件,状态,快速反应,部门收集过去24小时的重大问题.,每日快速反应会将问题分配到责任人。
会下责任人用问题解决过程采取纠正措施和防止问题再现。
负责人应确保其负责的问题符合关闭条件,包括经验总结。
就问题解决过程的结果进行交流。
快速反应跟踪板上关闭标准栏标为绿色。
在快速反应跟踪板上对问题进行跟踪。
责任人需在快速反应会上做周期性更新和回顾。
快速反应过程的关键步骤,20,GlobalPurchasingandSupplyChain,快速反应,21,GlobalPurchasingandSupplyChain,快速反应,审核员注意事项,审核之前,检查最近的客户抱怨,聚焦于未关闭的抱怨FR会议之前,询问是否有内部重大问题检查展板,是否包含上述的内外部问题跟踪一个快速反应跟踪展板上的问题,检查其处理过程是否包含核心步骤,确认行动是否落实&所有文件记录是否更新检查几个步骤的状态,根据时间期限判断状态其评价是否合理。
检查几个N/A(不适用)步骤,判断其是否不适用。
生产中快速反应查什么?
22,GlobalPurchasingandSupplyChain,快速反应,23,GlobalPurchasingandSupplyChain,操作工问题快速反应运用Andon系统对操作工进行支持,防止操作工试图自行解决而导致重大问题,例如:
安全问题质量决定(例:
判断不合格品OK)未经许可的返工/返修偏离标准作业,产生新的失效模式,等根据生产线的复杂程度可采取不同的解决方案,要保证快速及时的沟通,操作人员不会独自面对识别出的问题。
快速反应,操作工快速反应:
目的,防止缺陷出现或传递到下个流程,面对工序或经验问题时求助优先启动问题处理过程管理和支持团队,实地考察问题,采取行动,交流操作信息,GlobalPurchasingandSupplyChain,24,快速反应,操作工快速反应:
角色和职责,小组成员角色遵守标准化作业程序主动留心非标准化状况如果发现非常规问题或缺陷无法立即纠正,拉动灯绳(或用无线电、信号旗等其他手段寻求支持),继续完成工作循环,直到得到支持。
按要求解决问题并修复,支持小组领导者,小组领导者角色留意小组成员的求助(例:
听到音乐,在看板上寻找信息)。
立即赶往求助现场,进行调查和支持。
听取问题描述,对问题负责。
立即开始纠正问题。
在小组成员支持下开始解决问题(当确定纠正方案时重拉灯绳,重置Andon系统)。
如果问题得不到快速解决,向团队领导者寻求支持。
操作工快速反应:
角色和职责,GlobalPurchasingandSupplyChain,25,快速反应,团队领导者角色如果小组领导者无法纠正问题,向其提供支持,尽快使生产线恢复运转。
如有需要,寻求额外的支持(例:
维护、质量、生产、工程等)。
与小组领导者共同确保根本原因得到明确,应对策略得到实施。
监控停工期,识别问题区域,利用所有可用资源消除问题。
图表显示的是组织内部的支持跨度。
倒三角结构的重要意义在于小组成员位于顶部,由下面的整个组织支持着。
当小组成员需要援助时,他寻求支持,小组领导者提供支持。
复杂问题中,小组领导者向团队领导者寻求支持,支持就这样下达。
操作工快速反应:
角色和职责,GlobalPurchasingandSupplyChain,26,快速反应,TeamMember小组成员,TeamLeader小组领导者,GroupLeader团队领导者,Mgr经理,Needshelp需要援助,Support支持,Support支持,Support支持,CallSupport寻求支持,Decision决策,Decision决策,Decision决策,27,(Example),快速反应,班组之间信息流,确保所有班组之间交流途径的通畅;避免面对相同问题时班组间可能的交流不畅;在问题解决行动中管理和支持团队。
GlobalPurchasingandSupplyChain,28,快速反应,交流的内容-建议所有在班组发生的重大问题必须记录在班组记录中。
例如:
防错验证失效停线启动遏制临时替代流程,等如果有一个以上班组,所有会对下一班产生影响的信息需通过班长面对面讨论进行交流。
班组记录用于根本原因分析:
被动:
当生产出不合格零件时在过程中检查哪里出错,明确断点。
主动:
领导者每天检验为解决问题所采取的行动,如有需要,启动升级。
29,审核员注意项,快速反应,-询问操作人员怎样才能向上升级他们的问题-有Andon或者类似的系统,是否适用-验证Andon的功能和是否满足要求(灯光告示板,灯,声音信号是否可用,支持人员是否迅速到达)-参与换班,检查班组记录簿和信息共享情况。
问题解决查什么?
30,GlobalPurchasingandSupplyChain,快速反应,问题解决,31,GlobalPurchasingandSupplyChain,31,问题是什么?
是指现状和用户期望之间的差距。
定义为现行标准或期望与现实状况之间的不符合。
.组织应该定义问题解决的过程,包括用于识别和消除根本问题的记录工具。
快速反应,Standard标准,Discrepancy不符合,Actual现状,LEVEL级别,TIME时间,问题是提高的种子!
问题是积极的机会!
如果没问题出现,那就出岔子了!
问题解决,32,快速反应,问题解决基本原则,摒弃先入为主的思维。
不要回应没有数据的问题。
拆分问题。
看异常状况和问题发现点的第一手信息。
对正在发生的问题有了全面了解后再开展原因分析。
标准是什么?
将所发生的事与应该发生的事进行对比。
建立原因/影响间的联系。
一直问“为什么?
”直到发现了根本原因,能阻止问题重现。
问题解决,33,快速反应,定义:
一个结构化过程,识别、分析和消除因现实状况和标准预期不符合带来的问题,阻止根本原因再现。
运用多功能小组方法。
P,D,C,A,34,GlobalPurchasingandSupplyChain,34,问题解决,快速反应,问题解决过程-核心6步,问题描述(最初印象),问题定义,遏制问题发现点持续时间断点(转效点),了解情况,根源调查,根本原因,应对策略,跟踪,标准化,重大/模糊问题用户看见什么拆分问题问题各个部分,遏制,问题在哪里发生?
标准是什么,持续多久?
100%检查,防止忽视,技术性根本原因调查7-Diamonds,5Why,原因/影响深度挖掘系统为何失效?
应对策略开发/试运行?
/实施,验证应对策略数据,分层审核,交叉重读,STEP1:
定义STEP2:
遏制STEP3:
根本原因STEP4:
纠正措施STEP5:
措施验证STEP6:
横向展开与标准化,35,35,问题解决,谁来进行问题解决?
Stability稳定性,参与度,参与的人越多,就能解决越多的问题,创造越稳定的环境。
环境变得越稳定,越多的人就能参与到问题解决中来。
每个人,People,快速反应,问题描述(最初印象)说明发生的问题(四要素样4W)人及设备、时间、地点、发现了什么5W2H(WHATWHENWHEREWHOWHYHOWHOWMUCH),Step1-问题定义,根据你的理解对问题做一个宏观模糊的描述。
36,36,问题解决,快速反应,ProblemDescription问题描述(InitialproblemPerception)(最初印象),了解情况,第1步-问题,问题描述-按特性定义情况(拆分问题)标准(应该发生什么?
)偏差(发生了什么?
)时间(持续多久?
)频率(多少次?
),37,GlobalPurchasingandSupplyChain,37,问题解决,FASTRESPONSE快速反应,了解情况,ProblemDescription问题描述(InitialproblemPerception)(最初印象),ProblemDefinition问题定义,Process3IsthePointofCause!
过程3是问题发现点!
亲自去看;问题发现点。
问题出在哪里?
第2步-遏制问题,38,GlobalPurchasingandSupplyChain,38,问题解决,快速反应,不可见,不可见,可见,可见,可见,可见,了解情况,产品流方向,调查方向,ProblemDescription问题描述(InitialproblemPerception)(最初印象),ProblemDefinition问题定义,ContainmentLocatePointofCause遏制确定问题发现点,PoC问题发现点,第2步-遏制问题,一旦明确了问题发现点,小组需要运用不合格品程序来确定:
遏制缺陷的最佳方法。
持续了多久?
查找最近已知合格件的数据,找出问题的特征。
保证操作人员注意到变化、异常条件和时限。
创建遏制工作表,检查在时限内的所有问题原料都得到控制。
明确其他区域或用户是否受到了问题影响,如有影响达到什么程度。
39,GlobalPurchasingandSupplyChain,39,问题解决,快速反应,40,GlobalPurchasingandSupplyChain,Step3识别根本原因,问题解决,有好几种工具可用于问题解决和查找根本问题。
它们的使用基于过程复杂程度、失效模式类型、适用度、功能,以及测定关键特性参数(特性或可变数据)时失效的系统。
(Example),快速反应,流程图,鱼骨图,Pareto分布图,柱状图,运行图,分布图,控制图,图画,(Example),作为根本原因启动步骤,GM使用7diamond过程作为对内部质量问题的及时反应。
起初4步用于快速确定是否存在非标准化条件(特殊原因)。
这将防止问题解决统计技术的过度使用。
7,Step3识别根本原因,ProblemSolving问题解决,41,FASTRESPONSE快速反应,问题识别开始问询,负责人,过程正确?
工具正确?
零件正确?
零件质量?
生产部门1,生产部门2,生产部门3,相关的工程技术/供应商质量保证/供应商4,是否需要技术支持?
要进行工艺更改吗?
要进行产品更改吗?
不确定,极端复杂问题,责任方,车辆装配工艺5,产品开发6,统计工程7,钻石法14步用来判断生产部门是否严格按照设计内容执行制造工艺.钻石法1-4步评价过程的稳定性.一旦问题已被定义,第一反应即立即执行1-4步初次调查应在发现问题的区域执行.如果调查发现问题的原因在上游,应在上游也展开调查工作.如果制造过程完全按照设计进行而问题仍然存在时,应使用统计工程的方法帮助分析问题.,42,Step3识别根本原因,问题解决ProblemSolving,快速反应,正确的过程,是否张贴了正确的作业指导书?
是否执行标准化作业?
(如适用)是否符合相关加工文件,如图纸等?
是否按照规定的要求及频次使用检具进行检查?
不同班次的生产是否一致?
操作者是否理解产品规范,标准的内容?
操作者是否固定?
是否有很多轮岗员工?
操作者是否经过足够的培训?
目视辅助工具(样件、图片等)是否正确?
操作者是否了解其工位的质量要点?
操作者是否知道有问题时,如何沟通以得到帮助?
以下原因是否会导致问题的发生?
1,ProblemSolving,(Example),快速反应,43,(所有班次)是否使用正确的工具和夹具?
工具是否按照规定要求设定?
工具是否在校验有效期内?
不同的班次是否使用了相同的工具?
工具是否磨损?
工具与夹具是否具有保护装置以防损坏?
工位是否有防错装置?
工具或防错装置是否有效?
工位布局是否有利于操作者完成作业?
预防性维护是否按时完成?
(检查记录)工具的功能是否正确?
正确的工具,以下原因是否会导致问题的发生?
2,ProblemSolving,(Example),快速反应,44,零件的流动路线是否正确?
是否使用正确的零件?
零件存放位置是否正确?
料盒上的零件号与存放位置标识是否一致?
是否需要防错?
现有防错装置是否正常工作?
正确的零件,以下原因是否会导致问题的发生?
3,ProblemSolving,(Example),快速反应,45,质量部门负责确认零件是否发生变化以及零件的整体质量水平:
供应商质量数据CMM三座标测量工装夹具检查单个零件目检批次零件目检如果发现零件质量(不符合规范)是导致问题发生的根本原因,那么质量部门应将问题通知生产部门及供应商,并与生产部门或供应商一起验证纠正措施是否有效.,零件质量,4,ProblemSolving,(Example),快速反应,46,对钻石1-4步骤“NO”的回答,进行5-Why分析。
找到原因后,一直问“为什么”直到发现真正的根本原因(5Whys)。
Step3识别根本原因,47,快速反应,问题解决,5WHY问题解决工具,为什么机器人停了?
Afuseintherobothasblown机器人的保险丝断了。
为什么保险丝断了?
Circuitsoverloaded电路过载。
为什么电路过载?
Thebearingshavedamagedoneanotherandlockedup轴承互相损毁,然后锁止了。
为什么轴承互相损毁?
Therewasinsufficientlubricationinthebearings轴承间润滑不足。
为什么轴承间润滑不足?
Theoilpumpontherobotisnotcirculatingsufficientoil.机器人油泵循环油量不足。
为什么油泵循环油量不足?
Pumpintakeiscloggedwithmetalshavings.油泵进口被金属屑堵住了。
为什么进口被金属屑堵住了?
Nofilteronthepumpintake.油泵进口没有过滤器。
为什么油泵进口没有过滤器?
Thepumpwasnotdesignedwithafilter.油泵设计就没有过滤器。
48,快速反应,问题解决,Step3识别根本原因,根源调查,5Whys是找到根本原因的工具。
我们处理问题时做出的初步结论常常就是直接原因。
直接原因有可能是其他原因导致的,依此类推。
如果能理解这个原因链条,我们就可以找到根本原因消除问题。
一直问为什么,直到发现根本原因!
49,Step3识别根本原因,问题解决,快速反应,ProblemDescription问题描述(InitialproblemPerception)(最初印象),ProblemDefinition问题定义,LocatePointofCause,确定问题发现点,PoC问题发现点,DirectCause直接原因,Cause原因,Cause原因,Cause原因,根本原因,根源调查,(Example),(Example),如果钻石1-4回答“YES”,进入原因影响头脑风暴,对钻石1-4提的问题,每个“NO”的回答都要求用5-Why探寻,1-4,50,实用问题解决表(1-3步),快速反应,深度挖掘分析/工作表,5Whys在找到技术性根本原因后,确定系统为什么失效。
一直问“为什么”知道真实的根本原因都得到明确。
预测为什么规划过程没能预测到失效?
预防-为什么生产过程没能阻止缺陷?
保护(流出)-为什么质量过程没能保护用户(GM)遭遇缺陷?
(Example),51,51,快速反应,Step4实施纠正措施,头脑风暴,想出可行的解决方案,并选出最有效,成本最优的方案。
决定是否需要试运行来确定和测试建议方案,检验它是否有效且无负面影响。
决定方案所需要的步骤和行动。
识别出实施方案对所有利益相关者的断点(转效点)。
GlobalPurchasingandSupplyChain,52,52,问题解决,快速反应,ProblemDescription问题描述(InitialproblemPerception)(最初印象),ProblemDefinition问题定义,LocatePointofCause,确定问题发现点,PoC问题发现点,DirectCause直接原因,Cause原因,Cause原因,Cause原因,根本原因,Countermeasure应对策略,跟踪和检查,实施分层审核来检验体系的更改得到了贯彻,按预期运行通过测量和数据检验效果。
建立检验周期(持续时间/日期)。
确定由谁跟踪。
确定标准化流程及方法。
去除遏制中多余的工作。
Step5验证措施(检验行动效果),53,53,问题解决,(Example),快速反应,ProblemDescription问题描述(InitialproblemPerception)(最初印象),ProblemDefinition问题定义,LocatePointofCause,确定问题发现点,PoC问题发现点,DirectCause直接原因,Cause原因,Cause原因,Cause原因,根本原因,Countermeasure应对策略,FollowUp跟踪,识别存在或产生潜在失效模式的类似产品和过程。
把失效模式和纠正措施加入到经验总结数据库中。
将问题解决报告副本发送给其他部门/工厂。
在整个组织内部实施解决方案。
更新必要的文件:
PFMEA过程失效模式和效果分析ControlPlan控制计划ErrorProofingVerification防错验证StandardizedWork标准化作业OperatorInstructions操作人员培训文件,Step6横向展开及标准化,54,Why?
Why?
54,问题解决,快速反应,ProblemDescription问题描述(InitialproblemPerception)(最初印象),ProblemDefin