高炉鼓风机试车方案讲诉.docx
《高炉鼓风机试车方案讲诉.docx》由会员分享,可在线阅读,更多相关《高炉鼓风机试车方案讲诉.docx(16页珍藏版)》请在冰豆网上搜索。
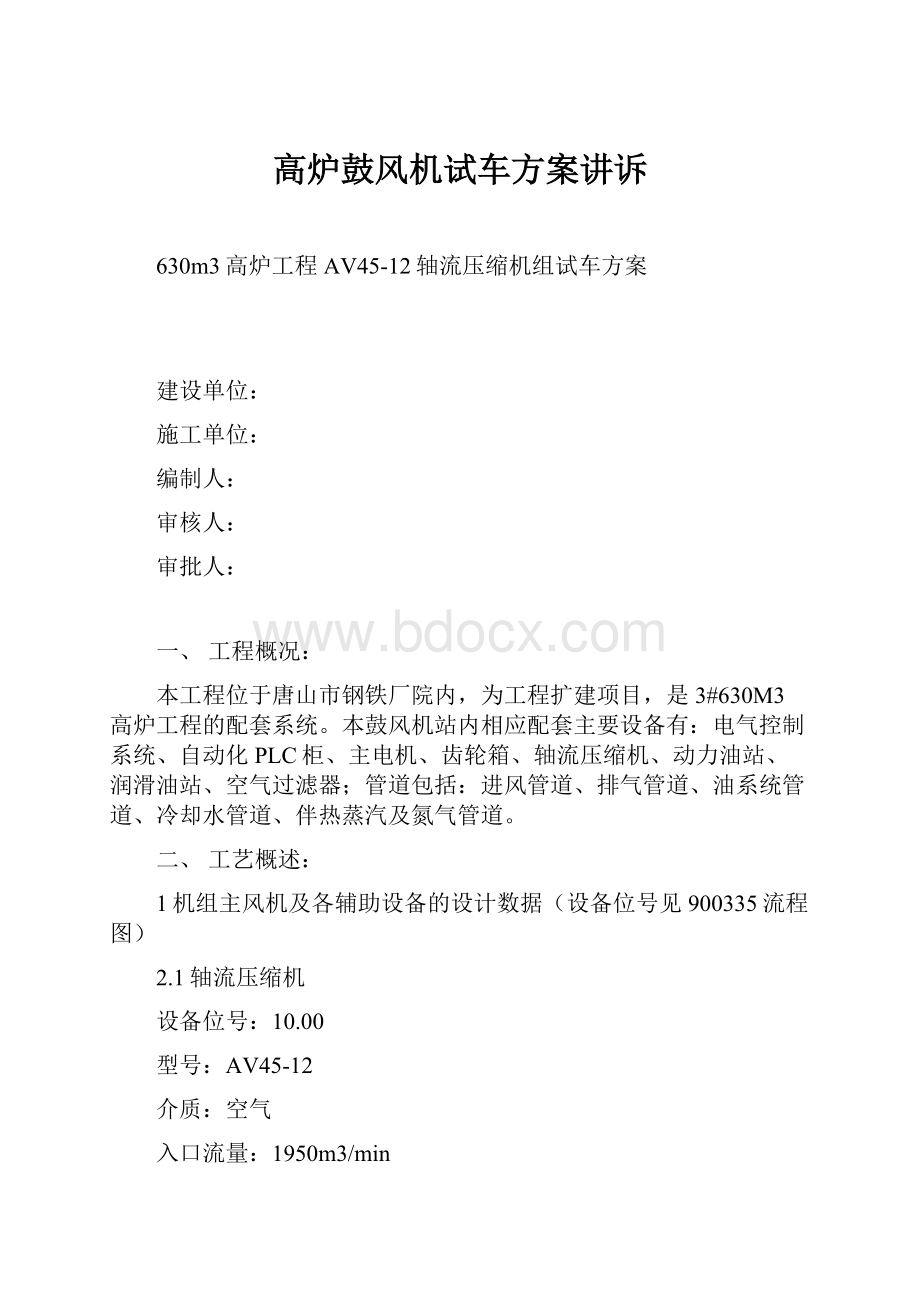
高炉鼓风机试车方案讲诉
630m3高炉工程AV45-12轴流压缩机组试车方案
建设单位:
施工单位:
编制人:
审核人:
审批人:
一、工程概况:
本工程位于唐山市钢铁厂院内,为工程扩建项目,是3#630M3高炉工程的配套系统。
本鼓风机站内相应配套主要设备有:
电气控制系统、自动化PLC柜、主电机、齿轮箱、轴流压缩机、动力油站、润滑油站、空气过滤器;管道包括:
进风管道、排气管道、油系统管道、冷却水管道、伴热蒸汽及氮气管道。
二、工艺概述:
1机组主风机及各辅助设备的设计数据(设备位号见900335流程图)
2.1轴流压缩机
设备位号:
10.00
型号:
AV45-12
介质:
空气
入口流量:
1950m3/min
进气压力:
0.0994Mpa(A)
排气压力:
0.37Mpa(A)
工作转速:
7150r/min
轴功率:
6044Kw
主轴旋转方向:
从进气端看顺时针
设备制造商:
陕西鼓风机(集团)有限公司
2.2齿轮箱
设备位号:
50.00
传递功率:
8000Kw
速比:
4.815
盘车装置:
电动盘车
盘车电机:
380v/15Kw
盘车转速:
73rpm
齿轮形式:
平行轴双斜齿
齿型:
渐开线硬齿面
设机组工艺概述:
备制造商:
西安陕鼓动力股份有限公司/郑州机械研究所
2.3电动机
设备位号:
40.00
额定功率:
8000Kw
额定电压:
10000v
额定转速:
1490rpm
额定电流:
524A
传递效率:
96.7%
冷却方式:
上水冷
绝缘等级:
F级
2.4动力油站
图号:
87020CK
型号:
DYZ33-16
输出油压:
12Mpa
输出流量:
33/min
过滤精度:
5μm
油牌号:
30#透平油
油箱容积:
500L
油泵:
恒压变量轴向柱塞泵
油泵电机:
型号:
Y160L-4B35功率:
15KW
蓄能器规格:
16*2L
冷油器型号:
2LQFW-AIF耗水量3T/h
2.5润滑油站
图号:
87005
容量:
6300L
电动泵型号:
流量:
648L/min
压力:
0.5Mpa(G)
功率:
11*2KW
转速:
1450r/min
双联滤油器过滤精度:
20μm
双联滤油器冷却水量:
80*2T/h
冷却面积:
100*2m2
三、组试车方案的编制依据:
⒈设计施工图纸;
⒉机组设备说明书及有关技术文件;
⒊施工组织设计及方案;
⒋各分项,分部工程的施工技术资料及记录;
⒌《机械设备安装工程施工及验收通用规范》。
四、机组试车前应确认的条件:
⒈机组及其附装置,各管路均应全部施工完毕。
施工记录及资料应齐全。
其中:
①设备(机组)的找正,精平,配合间隙,密封以及有关的几何精度经检验后确认合格。
②润滑油系统,动力油系统冲洗滤油精度达到试车条件。
(润滑油站滤油精度达到20um。
动力油站冲洗滤油精度为5um)。
系统检验合格。
③冷却水系统检验要求系统畅通,无跑冒滴漏。
④电气控制、仪表测量等控制操作系统检验合格。
⒉试车站需要的能源,油料,氮气,水,工机具,检测仪器,安全防护设备等均应到位,并符合试运转的条件。
1氮气0.4~0.6MPa。
2冷却水0.3~0.4MPa,温度≤25℃。
3电源供电。
电压:
10000V频率:
50HZ
4充氮工具。
5检验调试工具。
6消防器材。
⒊试车体制建设。
1成立AV45-12轴流压缩机组试车领导小组及试车作业班组:
试车领导小组:
组长:
项目总工:
副组长:
小组成员:
试车作业班组:
机械设备及工艺管线,电气仪表。
2参加试车运转的人员必须熟悉机组的工作原理与工艺原理,熟悉操作规程及试运转操作。
熟悉并领会试车方案。
3试车实行统一指挥。
定职,定责,定岗。
发现问题自己不能解决的应立即逐级汇报请示,不能擅自主张。
试车期间闲杂人员不得入内。
⒋试车须有下列单位到场检查指导:
1甲方现场代表。
2设计单位技术支持。
⒌机组的试车方案已经批准。
⒍机组及周围环境应清扫干净,不能有其它施工作业。
五、机组试运转的内容和步骤:
⒈电气控制系统及自动化的联锁模拟试验。
⒉润滑油系统,动力油系统的检查和联锁调试。
⒊主电机单机试运转。
⒋主电机带增速器试运转。
⒌机组各系统联动模拟试验。
6.机组无负荷试运转。
7.加载试验(机组防喘试验)。
六、机组启动前的检查与调试
⒈润滑油系统调试:
⑴油泵启动:
1油泵启动打开及进出口管线上的阀门应保证泵体内压力不于无限升高而泵体爆裂,并通过泵体。
最高处供注油用的螺塞在泵体内注满输送的润滑油,为泵体启动时提供必要的液体密封(油泵严禁干转)。
2点动,检查电动机的旋转方向。
⑵油泵启动后注意观察泵的运转情况和密封情况,并须保证泵的出口压力≤0.5MPa。
运转正常后,通过阀后压力调节阀调整润滑油站出口压力为0.25MPa。
油压正常后可进行压力控制器和温度控制器调整。
调整项目职锁报警值
冷油器出口油温>45℃
润滑油压力MPa<0.09开辅机,<0.06停机
油箱油位低于油箱面720mm
⑶检查油温:
1如低于20℃需进行加热。
加热时应启动辅助油泵。
打开阀前压力调节阀旁通管道上的截止阀。
关闭阀前压力调节阀的闸扳阀,油循环加热。
2在机组启动过程中,由于油温需经过一定时间才能稳定,因此要注意这段时间内的油温变化,并适当调节冷却水量,直达到稳定温度。
⑷GLL形双联冷却器的操作使用:
a.冷却器首次运行时,先打开位于冷却器筒体上部的放气阀,并打开冷油器进油阀(出油阀关闭),当有油溢出时,关闭进油阀。
排气是很重要的,因为空气在冷却器内会使传热效果降低。
打开冷却器回水盖气接口上的阀,然后打开冷却水的进水阀,当有水溢出时,关闭进水阀,关闭排气阀(出水阀始终关闭)。
此时水和油成静止状态,经热交换,温度差逐渐减小。
b.打开冷却器出水阀,再慢慢打开冷却水进水阀,使冷却水流动;同时打开出油阀,再逐渐打开进油阀,使油也处于流动状态。
然后根据冷却器出油口双金属温度计所示的油温,不断调节冷却水的进口阀,直到测出所需的油温。
c.在起用冷却器时,切忌快速打开冷却器进水阀门。
因为冷却水大量流过冷却器时,会使换热管表面形成一层导热性很差的“过冷层”,以后即使大量的水流过冷却器,还是起不到良好的冷却效果。
d.双联冷却器采用并联的结构布置,用切换阀来选择他们的使用和备用。
在需要换向时,必须先把三通换向阀上的旁通阀,即压力平衡开关打开,让油逐渐通到换向阀的另侧,这样能减小换向时的阻力及消除液后冲击。
待两侧压力平衡后打开切换阀,同时,打开备用冷却器的所有排气口和冷却水的进出口阀门,但必须注意不能立即切换还在工作的那支冷却器(可先将阀芯处于三通阀的中位,令两只冷油器同时工作),同样通过调节冷却水进口阀,测得所需油温后,即可将阀芯完全切换至另一端。
⑸切换油路及更换滤芯操作:
双联滤有器主要技术参数为:
工作压力:
≤2.5MPa;
初始压差:
≤0.01MPa;
报警压差:
≤0.15MPa;
当使用滤罐的滤芯被污物堵塞,且出油口压差达到规定值时压差发讯器发出讯号,这时必须更换滤芯,切换油。
更换滤芯的操作步骤如下:
1切换油路
第一步:
注油。
在转动切换阀扳手之前,必须使装有新滤芯的备用滤罐充满油液,首先须打开平衡阀,使油液缓缓流进备用油罐。
第二步:
放气。
在注油的同时,应该打开备用油罐顶部的放气阀,以便油液进入滤罐时顺利排出空气。
第三步:
切换。
打开平衡阀约10分钟,当放气口有连续油液冒出时,表明该滤罐已注满油液,立即拧紧放气阀,至此备用滤罐已处于切换状态,转动切换扳手90度即实现了油路切换。
再关闭平衡阀(当扳手朝左边扳表示右边滤罐工作,反之亦然)。
2更换滤芯:
第一步:
将内部装有脏滤芯的滤罐(备用滤罐)放油口的放油阀打开,同时打开该滤罐顶部的放气阀。
放出油罐洁净腔里的油液,当放油口不再有油液流出时,再打开排污阀,将滤罐的污油全部放掉。
第二步:
拆掉该滤罐上盖的连接螺栓,旋紧起盖螺钉,则上盖离开罐体。
此时,可方便的将上盖逆时针转动而离开滤罐体。
第三步:
拧开固紧滤芯的压紧螺母,拿掉压板。
此时,即可顺着中空导柱将滤芯取出。
第四步:
分别用手隔着包装塑料袋拿着新滤芯顺着中空导柱套入,然后盖上压板,拧紧压紧螺母,新滤芯即已换装到位。
第五步:
顺时针转回上盖,旋松起盖螺钉,上盖即重落滤罐体上。
装上并拧紧连接螺栓。
旋紧排污螺塞,关闭放油阀。
至此,该滤罐已处于备用状态。
⑹压力阀组调节
2、动力油站系统调试:
在动力油系统冲洗完后,应将冲洗油排出,将油箱内沉淀的杂质清理干净并更换滤油器滤芯,再加入新油作为工作油。
为保证系统的清洁度,新油必须经过,过滤精度不低于5μm的滤油机过滤后再加入油箱。
2.1、安装完毕后应先进行低负荷运转,低负荷运转压力为1-2MPa。
时间为30分钟,再进行满负荷运转,满负荷压力为125MPa时间为15分钟。
满负荷运转时,泵壳温度一般比油温高10~15℃,但当入口油温达65℃时,泵壳的最高温度不应超过75~80℃。
当泵的压力、噪声、振动以及其它各元件工作均无异常时,即可投入正式作用。
2.2、各参数的正常值与各元件和仪表的调整值。
序号
测点
额定值
作用
1
油站出口油压力
12MPa~12.5MPa
正常值
2
油箱内油温
45℃~50℃
正常值
3
油箱内充油液位
距箱顶100mm
正常值
4
蓄能器内充氮压力
6.4MPa
正常值
5
油泵的工作压力
12~12.5MPa
正常值
6
溢流阀开启压力
13.5MPa
保护泵
7
溢流截止阀开启压力
140MPa
保护蓄能器
8
试验管路处压力继电器动作压力
11MPa
启动备用泵
9
供油管处压力继电器动作压力
9MPa
发停机信号
10
滤油器差压发讯装置动作差压
0.35MPa
切换滤油器
11
温度控制器动作温度
20℃开、25℃关
控制电加热器
12
温度控制器动作温度
55℃
发报警信号
13
液压控制器动作液位
距箱顶350mm
发报警信号
以上各调整值(除蓄能器充氮气压力、油箱内充油液位外)。
出厂前均为已调整好,为可靠起见,用户在投入使用前以上各值进行较核。
不符的应重新调整。
2.3、调试前的确认
2.3.1启动前应检查油箱液位及阀门是否在正确位置上。
2.3.2当油温低于20℃时应将电加热器投入,待油温升到20℃时方可启动油泵。
油温升至45℃时投入冷却水。
2.3.3蓄能器充氮气压力的检查
在开始工作的最初一个月每星期检查一次,以后每月检查一次,对正在运行的蓄能器进行检查前应先按下述方法对备用蓄能器进行检查。
确认合格后,将备用蓄能器投入,然后再检查。
检查时,先关闭蓄能器进口溢流截止阀上的球形截止阀,再缓慢的打开放油阀。
将蓄能器内的油缓慢放回油箱,同时观察溢流截止阀上的压力表,起初压力下降缓慢,当降到某一压力时突然下降至零,这个压力就是充氮压力。
也可以利用充氮工具在蓄能器充气阀处检查。
但每检查一次须放掉一点氮气,检查后关闭放油阀缓慢打开球形截止阀。
2.3.4当滤油器的差压达到0.35MPa,差压发讯装置发生信号时,说明滤芯已污染,应立即切换备用滤油器工作,将堵塞的滤芯拆下,清洗滤油器壳体部后换上新滤芯。
3、机组起动前的准备工作
3.1自控、电控系统信号的检验,报警及安全保护系统的检验,应确认所有系统安全可靠,并符合有关自控、电控操作图纸设计意图和工艺要求。
4.2润滑油系统的检验应遵循有关润滑油系统操作说明书详细地检验其是否完全满足轴流压缩机组运转的要求。
4.3原动机(电动机)应按照其制造厂提供的说明书详细地检验其是否完全满足运转的要求。
4.4所有附属设备(如供水系统、配电系统、气路系统等)都应该处于正常工作状态。
4.5检查下列各项:
a、轴流压缩机静叶必须关闭到最小启动角(第一级静叶为14°)。
b、防喘震阀(即放空阀)必须100%的全开。
c、逆止阀(即止回阀)必须100%的关闭。
七、机组试运转:
1试车前的准备
低压配电设备在试车前应全部整定和校验完毕。
按要求将润滑油系统投入,调节进油阀门管路压力为0.15MPa。
2电动机空负荷试车
电动机与齿轮箱之间联轴器切断开,护罩连接紧固,试车详见电动机说明书。
记录启动电流、电压、轴承温度、定子温度等。
3电机带齿轮箱的试车
联结电动机和齿轮箱间联轴器及护罩,风机与齿轮箱联轴器护罩,手动盘车检查盘车啮合情况,电动盘车检查机械安装情况并检查盘车脱开情况。
主要检测设备机械运转情况如轴承温度、齿轮箱的轻负荷机械运转等,在试车时检查盘车装置的运行及脱开动作是否可靠。
4机组试运转
(1)、联接齿轮箱与压缩机之间的联轴器及护罩。
(2)、将机组的监测、保护系统和自动控制系统投入。
(3)、按4.1条要求投入润滑油系统,并观察机各单机轴承及各润滑点和高位油箱供油畅通,并至少做一次备用油泵启动试验。
(4)、按4.2条要求投入动力油系统。
注意:
必须按要求先进行低负荷运转30分钟,然后逐渐增加负荷,为蓄能器充油,使一台工作,一台备用,并做静叶的静态调节试验。
步骤如下:
按自控系统要求改变静叶调节电流信号,使静叶从22°旋转到79°。
关掉动力油站电动油泵,当油压降低到9MPa时,自控系统发出紧急停机信号,这时伺服马达应在蓄能器的作用下使静叶关到22°。
按上述要求试验后,重新投入动力油系统,并至少做一次备用油泵启动试验。
(5)、手动盘车装置,认真检查各单机,有无异常声音,调整油路阀门使阀
(6)、启动机组
(7)、检查检测系统是否运行正常。
(8)、检查离润滑油站最远处轴承的进油压力,轴承入口处的表压力应大于或等于0.6Kgf/cm2。
(9)检查冷油器出口油温,温度指示表应指示在40℃。
(10)、检查所有轴承(包括径向轴承和止推轴承)的温度,必须低于轴承工作温度的允许值。
(11)、根据电动机制造厂提供的说明书中规定的检验项目检查电动机的运行状态,所有检查结果应满足制造厂说明书的要求。
(12)、检查轴流压缩机机组轴系中各单机主轴的振动,其振动值必须满足设计要求。
(13)、检查轴流压缩机机组轴系中各单机主轴的轴位移,其轴向位移值必须低于有关说明书中规定的报警值。
(14)、加载过程
a当轴流压缩机转速达到额定工作转速,即轴流压缩机进入“安全运行”,这时轴流压缩机静叶关闭到最小启动角(第一级静叶角μ=14°),防喘振阀处于100%的全开,逆止阀处于100%的关闭状态,如果排气管道上设有截止阀(即主闸阀)的话,也应处于100%的关闭状态。
b打开第一级静叶角度到最小运行角(角μ=22°),此动作的完成由有关手动按钮来完成。
注意;打开第一级静叶角度到最小运行角μ所需时间必须控制逻辑监护,如果所需时间超过3秒钟,则机组立即被切换进入“安全运行”角度。
绝对不允许轴流压缩机在第一级静叶角度为μ与最小运行角μ间运转。
c将轴流压缩机的防喘振阀由手动控制状态转换为自动控制状态。
当然,也可以在手动状态下操作。
d逐渐打开轴流压缩机静叶,流量也随之增加,若防喘振阀处于自动控制状态的话,防喘振阀将缓慢地自动关闭,轴流压缩机排气管道上的逆止阀将随着排气压力的增加而打开。
e当轴流压缩机的流量和排气压力达到所期望的值时,将流量控制器转换到自动控制状态。
f机组的综合检查项目
润滑油压力冷油器出口的油温.
径向轴承的温度止推轴承温度
轴振动值轴向位移
电动机的综合检查项目(根据电动机制造厂提供的说明书)
齿轮箱的综合检查项目(根据齿轮箱制造厂提供的说明书)
附助设备的综合检查项目(根据总成说明书)
g当机组进入正常运行,则开始日常监测并记录在工作薄上。
h由于在试车阶段压缩机空气不送往工艺系统,而是通过放空阀放空,所以这时静叶的开度由手操器控制。
i在确定机组正常后,连续运行72小时,每小时检查一次轴承温度,轴振动,轴位移,润滑油系统,动力油系统的各项检测指标均不得超过表一中给出的正常值范围。
压缩机的性能测试可在此阶段进行。
5、停机
按正常停机按钮。
自控系统有以下停机动作。
(1)、轴流压缩机静叶从工作角度到22°
(2)、主电机跳闸。
(3)、轴流压缩机放空阀全开。
按动正常停机按钮后,应记录下机组的惰走时间。
待机组停稳后手动盘车。
停止动力油系统工作。
润滑油系统和盘车只有在确认机组已经完全冷却下来或各轴承温度均降至40℃以下才能停止工作。
6、停机后的检查
检查各仪表、阀门、压缩机静叶等的复位情况。
对运行期间曾出现的故障部位应认真检查并彻底排除。
7、机组的正常运转
7.1机组运行前的检查
(1)对机组周围的环境做全面清扫,保持机组周围清洁干净。
(2)检查机组各单机地脚螺栓是否紧固,各支撑面预留热膨胀间隙应符合各单机要求。
(3)投入自、电控系统,将电、气源送入各仪表、控制器、调节器、变送器等。
如发现有异常或出现报警信号应查找原因并排除之。
(4)认真检查工艺管线。
尤其是轴流压缩机入口及出口管线的安装情况,特别是应检查膨胀节是否满足安装要求。
8、安全运行
轴流压缩机出现逆流和工艺系统出现装置第流量时,自控系统便会发出安装运行信号,信号发出后有以下动作:
(1)静叶角度关闭到22°
(2)压缩机放空阀开
(3)压缩机出口逆止阀关
(4)向中心控制室送出安全运行工艺联锁信号
上述工况轴流压缩机仍在额定转速下运转称之为“安全运行”,当压缩机逆流消除后,按动存储器复位按钮,这时自控系统使流量调节器先投入,压缩机放空阀组投入自动,压缩机出口逆止阀开,又向工艺系统供风。
9、紧急停机
14.1联锁紧急停机项目包括以下内容
(1)、轴流压缩机轴位移≥0.6mm
(2)、润滑油总管最远点处润滑油压力≤0.08MPa
(3)、动力油压力≤9MPa
(4)、压缩机持续逆流
(5)来自中心控制室的工艺事故信号
(6)手动紧急停机
(7)电动机故障跳闸
11、手动紧急停机
手动紧急停机主要是在机组出现紧急报警,而且事故又无法排除。
这时工艺系统应迅速做好紧急停机准备,特别应注意紧急报警时,机组已处于危险的边缘,如果工艺系统仍然勉强继续开车,就可以使机组损坏而带来不可估量的损失。
紧急报警内容详见附表一。
12、紧急停机联锁发出后机组有以下动作:
(1)、轴流压缩机静叶从工作角度关闭到22°
(2)压缩机放空阀开
(3)压缩机出口止回阀关
(4)主电动机跳闸
(5)向中心控制室送出工艺系统紧急停机联锁信号
13、紧急停机后的处理和正常停机相同
当各轴承回油温度降至室温下先停盘车装置,然后停止润滑油站工作。
注:
如果紧急停机是由于停电引起的,则应进行人工手动盘车,每半小时盘动180°,直到各轴承温度降至40°为止。
14、正常停机
14.1正常停机前的准备
逐渐减少轴流压缩机负荷,使静叶工作角度V逐渐关闭到最小角度22°
用手操作器将轴流压缩机放空阀缓慢打开,逐步使主风机从工艺系统中切除出来。
14.2正常停机按钮
按正常停机按钮后,机组有如下动作
(1)压缩机静叶关小到22°
(2)压缩机放空阀开,出口逆止阀关
(3)向中心控制室发出停机联锁信号
(4)电动机跳闸
14.3、正常停机后的处理详见7.4
八、安全要求及保证措施
1、首先建立施工现场安全保证体系,项目经理对工程项目施工的安全负全面责任,其他相应负责人员亦应配备齐全,严格执行国家及企业的有关规范管理制度保证安全生产;
2、电、气焊工施工前要检查自己的施工用具是否完好,否则不得施工。
3、各工种施工人员要熟悉本工种安全操作规程,现场施工应坚守工作岗位,严禁酒后操作,禁止现场打闹。
4、现场用电须坚持“三相五线制”,由专职电工专人操作。
照明、施工用电分开,定期检查,禁止带病作业。
5、现场施工一定要遵守甲方厂规厂纪,按操作规程作业。
6、现场施工的孔、洞、沟应采取临时措施,必须加盖板,临时使用的梯子,平台要做到牢固可靠。
平台要设围栏,确保安全。
7、设备在未停稳前,不得用手、脚或物件强行制动;
8、设备在运转中不得进行修理。
如须修理应切断电源,并设专人保护电源,待设备停止运转后,方可允许修理,修理期间并设专人保护;
9、应设置操作区域,并挂警示牌,非试车人员不许入内;
10、非试车人员不得随意开动和关闭阀门;
11、试车必须有专人指挥操作,任何人不得私自进行违章操作;