浅析电解铝生产节能降耗措施.docx
《浅析电解铝生产节能降耗措施.docx》由会员分享,可在线阅读,更多相关《浅析电解铝生产节能降耗措施.docx(8页珍藏版)》请在冰豆网上搜索。
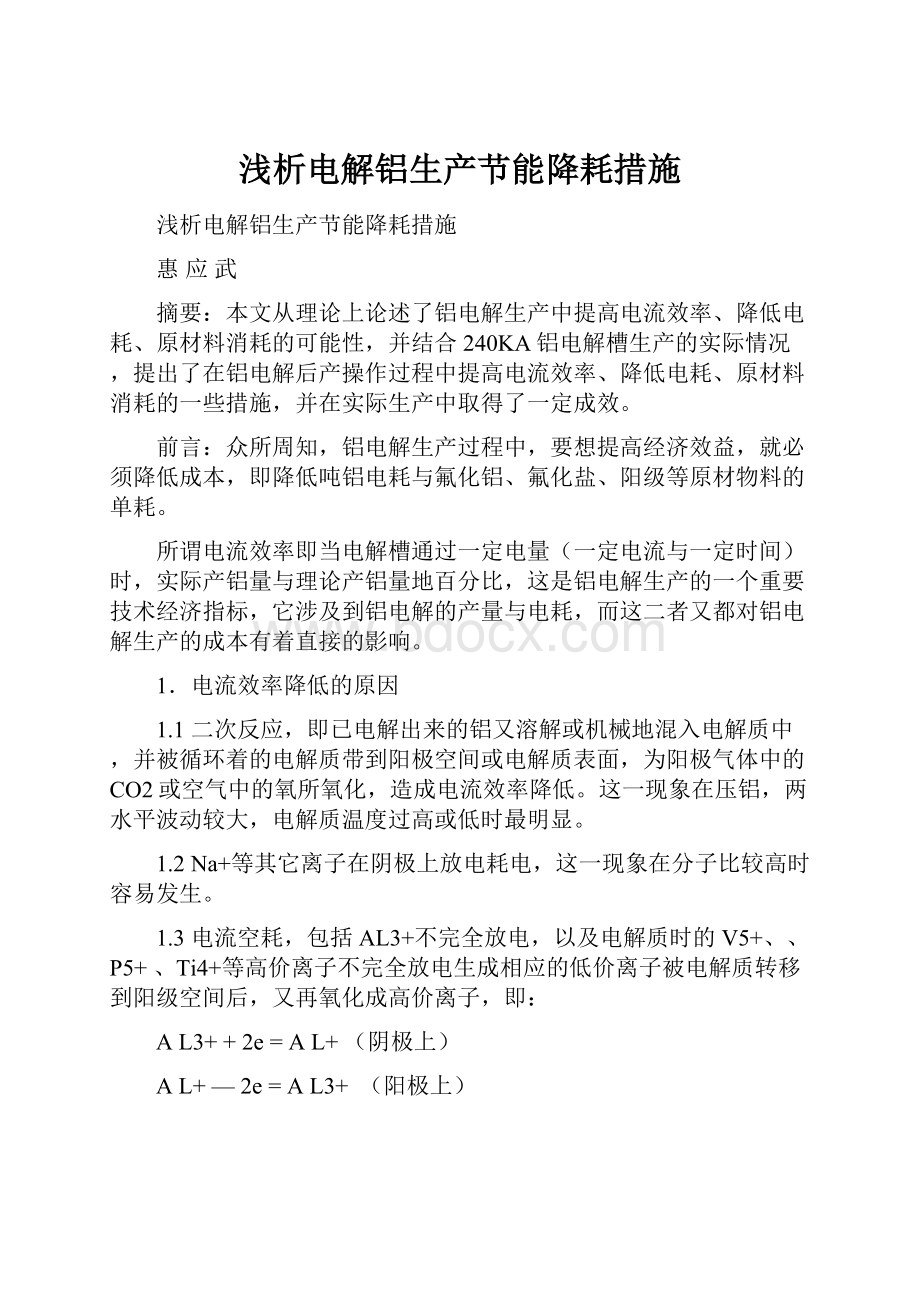
浅析电解铝生产节能降耗措施
浅析电解铝生产节能降耗措施
惠应武
摘要:
本文从理论上论述了铝电解生产中提高电流效率、降低电耗、原材料消耗的可能性,并结合240KA铝电解槽生产的实际情况,提出了在铝电解后产操作过程中提高电流效率、降低电耗、原材料消耗的一些措施,并在实际生产中取得了一定成效。
前言:
众所周知,铝电解生产过程中,要想提高经济效益,就必须降低成本,即降低吨铝电耗与氟化铝、氟化盐、阳级等原材物料的单耗。
所谓电流效率即当电解槽通过一定电量(一定电流与一定时间)时,实际产铝量与理论产铝量地百分比,这是铝电解生产的一个重要技术经济指标,它涉及到铝电解的产量与电耗,而这二者又都对铝电解生产的成本有着直接的影响。
1.电流效率降低的原因
1.1二次反应,即已电解出来的铝又溶解或机械地混入电解质中,并被循环着的电解质带到阳极空间或电解质表面,为阳极气体中的CO2或空气中的氧所氧化,造成电流效率降低。
这一现象在压铝,两水平波动较大,电解质温度过高或低时最明显。
1.2Na+等其它离子在阴极上放电耗电,这一现象在分子比较高时容易发生。
1.3电流空耗,包括AL3+不完全放电,以及电解质时的V5+、、P5+、Ti4+等高价离子不完全放电生成相应的低价离子被电解质转移到阳级空间后,又再氧化成高价离子,即:
AL3++2e=AL+(阴极上)
AL+—2e=AL3+(阳极上)
如此循环,造成电流空耗。
这种现象在阴极表面的电子密度(即电流密度)较小时,如AE过多,炉温过高、化炉膛时,或整流所突然限电时比较明显。
1.3.2漏电
通常是炉帮结壳熔化,并且电解质面上有大量炭渣时发生,即电流有可能连接槽壳与格子板之间,及铁渣箱体与槽壳接触等均可造成漏电损失。
在上述这些造成电流效率降低的原因当中原铝二次反应是电流效率降低的主要原因。
2.提高电流效率的措施
既然电流效率降低的主要原因是熔解铝的再氧化(二次反应)损失,那么提高电流效率的措施可以从控制铝损失过程中探索。
首先铝熔解,即已电解出的原铝通过铝液(阴极)与电解质之间扩散层扩散到电解质中去的过程,根据{邱竹贤《铝电解》冶金工业出版社1988}推出来的公式:
η(电流效率)=[1—KZF(COˊ—Cˊ)D/δD阳]×100
(1)
可得出,凡是能够减小扩散系数D与铝的溶解度COˊ及增加阴极电流密度D阴与扩散层厚度δ的所有因素,均可使电流效率η提高,反之则降低。
2.1电解质温度
电解质温度正常与否,对电解槽电流效率等工作指标有着决定性的影响,根据我厂实践中的多次测量表明,电解质温度每升高10℃,电流效率大约降低1—2%,这是因为随着电解质温度的降低:
①靠近阴极(铝液)的电解质中溶解铝的速度降低。
即COˊ减小。
②动粘度增大,阴极气体体积减小,从而使扩散层厚度增加,即η增加。
③扩散系数(D)减小。
由
(1)式可知,电流效率η增大。
但是,电解质温度过低也是不利的,它使电解质发粘,致使铝珠与电解质分离困难,反而易于铝的损失,使电流效率降低。
在一定的条件下有一个最适宜的温度,高于此或低于此电流效率都会降低,如图1所示。
240KA大面四点进电中间下料槽的铝电解生产,当电解质的温度控制在950—960℃为最佳,电流效率可达90%以上。
在操作管理过程中,必须供料正常,严格控制突发AE,并及时熄灭正常AE,平时要加强保温工作,防止温度大起大落,适时适量补充冰晶石,添加A1F3,以期平稳保持两水平,保持一定的分子比,即把电解质温度控制在950—960℃之间。
温度℃
图1η随温度变化曲线
2.2极距
极距是指炭阳极与阴极(铝液)之间的距离,极距增大,电解质搅拌强度将减弱,因为相同的阳极气体量所搅拌的两极间的液体量增加,搅拌减弱,则使扩散层厚度(δ)增加,使用使铝损失减少,电流效率提高。
反之,极距过度缩短将使电流效率急剧下降,这是由于阳极上气体直接接触铝液面而造成铝液的直接氧化损失所致。
但极距超过某一限度,电流效率变化不大,多次测量表明:
45mm的极距最适合240KA电解槽生产。
因此,不能企图以提高极距的方式来取得高电流效率,如图2所示。
而相反,应是力求使极距保持在实际所能允许的最小值,否则随着极距增加,不但不能提高电流效率,反而使槽电压徒然升高,加大电耗、最终还是不利于降低产品成本。
实践证明,采用45mm左右的极距可以取得90%以上的电流效率。
在实际生产操作过程中,必须严格电压管理,电压一经设定,就不要随便频繁变更,更不要随便手动调整电压;另外,AE时,一定要保证工序质量,一定要严格使用兜尺设置好每一块新极之极距,壁免极距大起大落。
100%
极距(L)
图2η随极距变化曲线
2.3电解质成分
2.3.1CR(即NaF/AIF3之重量比)
当CR小于1.5,有过剩AIF3时,电流效率开始提高,这是由于此时铝液与电解质之间界面张力(δ)增大,有利于分散于电解质中的铝珠汇集,且铝的溶解度减小的缘故。
同时在酚性电解质中,Na+的放电及铝自电解质中取代钠的反应减弱。
即:
Na++AL=3Na+2+AL3+减弱。
但电解质过酸,又使生成低价氟化铝反应增强,增加铝的损失,即:
2AL+AIF3=3AIF增强
因此,铝电解生产一般采用弱酸性电解质,其分子比(CR)在1.25~1.35之间。
要保持住一定的分子比(CR)。
平时操作时要严格控制阳极效应系数,以及AE持续时间,保持规整的炉膛,避免炉温升高,加速AIF3的挥发损失,从而提高CR。
观察电解质液颜色大致判断及定期取电解质试样分析结果,适当补充添加ALF,使电解CR稳定地保持在1.2~1.30之间。
2.3.2AI2O3浓度
据{邱竹贤《铝电解》冶金工业出版社1988}所述,在冰晶石——ALO熔体中,在5%(重量)AI2O3时,电流效率最低,大于或小于此电流效率均能升高,大型预焙槽生产,采用AI2O3浓度:
2.5~3.0%较适宜。
采用的2~3%AI2O3浓度进行生产,并且采用一次NB/5分钟,下料量7.21kg/次,AEB每次下料100kg左右的加料制度,在避开电流效率最低时AI2O3浓度的同时,又能有效地防止AI2O3浓度过高,避免形成炉底沉淀,或结晶壳,降低电流效率。
要保持一定的AI2O3浓度的前提条件是自动供料系统必须能正常供料,在这个先决条件下,电解生产现场管理,操作必须严格遵守NB、AEB制度,不得无故调整NB间隔和AE间隔,也不得无故手动NB、AEB。
2.4电流密度
2.4.1阴极电流密度
当电流强度不变,阴极面积即铝液面积发生变化(炉中”伸腿”收缩或长大)时,或者阳极面积不变,电流强度改变,阴极电流密度都会改变。
为了取得较高电流效率,阴极电流密度不能过高,也不能过低,因为阴极电流密度过低时,由于单位阴极面积上的电子密度过小,AI3+产生不完全放电:
AI3++2e=AI+
阴极电流密度过高时,则发生Na+大量放电,两者都会造成电流无谓的消耗,从而降低了电流密度。
因而阴极电流密度有一个对应最高电流密度的临界值—临界阴极电流密度。
而临界阴极电流密度又与铝电解生产中的电解质温度及极距有关,温度升高或极距缩小时,阴极电流密度均增大。
因此阴极电流密度与炉膛形状有直接的关系,生产实践表明,规整的炉膛,即炉底干净,侧部又能形成一定的炉帮,且伸腿既不长大也不收缩,刚好在阳极投影线之外,就能保持一定的阴极电流密度。
而生产操作中控制好AE系数,AE时间,保持一定的两水平、防止电解质温度大起大落;保持一定的电解质万分,平稳CR、CaF2%;不要随便手动调整电压,保持供料正常,不要无故手动NB、AEB,就能形成规整的炉膛。
2.4.2阳极电流密度
电流强度不变,加宽阳极,或阳极面积不变,电流强度波动均可使阳极电流密度改变。
阳极电流密度增大晨,阳极气体的析出量增加,对电解质液搅拌加强,使溶解金属的扩散系数增大(δ减小),二次反应加快,电流效率将降低;阳极电流密度减小时,阳极气体的析出排出的速度减弱,搅拌减小时,电流效率提高,但阳极电流密度保持过小,则系列电流强度也将变小,不利于强化生产,最终电流效率也无法保证。
因此,在系列电流设计值240KA的前提下,保持阳极电流密度为0.72A/cm²。
要使阳极电流密度稳定,在生产操作过程中必须严格AC工序质量,严格使用兜尺设置好新极极距,尽可能使所有阳极底掌保持在同一个平面上,并采取必要的措施(如划线、拧紧卡具等),防止新极下滑,加足极上AI2O3,以加强保温,使新极很快达到满负荷,从而可以避免阳极电流密度波动。
2.5铝液水平
在铝电解生产过程中,阳极下部总是会有一些多余的热量产生,这就使阳极下部较侧部温度为高,二次反应加快,从而影响电流效率的提高,这时,如果槽内铝液水平较高时,则可较快地使这部分多余的热量疏导出去(铝液导热性好),从而减少这个温度差,提高了电流效率。
但铝液水平过高也是不利的,因为这不仅使炉膛炉温偏低,炉膛过深,阴极电流密度增大,降低电流效率,而且传热量加大、热损失过大、也使电耗增加。
实践证明,保持17—18cm的铝水平可以得90%以上的电流效率。
因此,必须严格按规程下指示量,实施TAP作出时一定要严格按指示量出准,坚决杜绝在这台槽多出了,再在另一台槽少出的“互补”现象,同时尽量不要压铝,以免造成铝液水平波动。
3.降低电耗措施
3.1工业电解槽的电耗分配
完成铝电解生产中的反应:
AI2O3+2C=2AI+CO2+CO
必须要供给以下五部分的热量:
第一部分:
用来补偿反应过程的自由能变所消耗的能量。
第二部分:
用来补偿反应过程的束缚能所消耗的能量。
第三部分:
用来补偿反应物(AI2O3、C)由温度t1(室温)升高到电解温度(t3)的热焓变化所消耗的能量。
第四部分:
电解槽外部线路上的电能损失。
以上第一至第三部分的电能消耗为保持电解槽在所要求条件下,连续而稳定地进行生产,理论上所应付出的最低电能,是必不少的;第五部分的电能消耗与工程设计、施工有关。
因而只有第四部分的电能消耗直接与铝电解生产操作有关,我们在生产操作过程中只有努力降低这部分的电能消耗,才能有效地降低电耗。
3.2降低电耗的因素
电耗只取决于电解槽平均电压及电流效率两个因素:
w=2980/V平/r(KWh/TAC)
式中:
W—电耗(KWh/TAI)
r—小数表示的电流效率
由上式可见,凡能降低平均电压与提高电流效率的各种因素,都是降低电耗的因素。
①设r=0。
90
V平由4.16V升高到4.17V
则△W=2980/V平2—V平1/r
=2980/001/0.90
=33.11KWh/TAl
即电耗增加33.11KWh/TAl
②设V平=4.16V不变,当r自0.90增加到0.91,即电流效率增加1%时:
△w=2980/V2–r/r1r2
=151.4KWh/TAI
即电流效率提高了1%可降低电耗151.4KWh/TAI
③当V平=4.16不变,r自0.90增加到0.89时,△w=2980×4.16/–0.01/0.90(0.90–0.01)
=–155KWh/TAI
即当电流效率降低1%时,增加电耗155KWh/TAI
④如果在160KA系列(按每区33台槽计算)每台槽降低0.001V(1mv)则全年可节电:
Ivt=160×0.001×10³×33×365×24×10‐³
=46253KWh
若以全厂246台运行计算,则全年可节电:
Ivt=160×0.001×10³×246×365×24×1013
=344794KWh
3.3降低电耗的具体措施
提高电流效率的措施,前已论述、现从降低平均电太,即从生产技术上论述降低电耗的具体措施。
根据测试数据见表1