防错.docx
《防错.docx》由会员分享,可在线阅读,更多相关《防错.docx(20页珍藏版)》请在冰豆网上搜索。
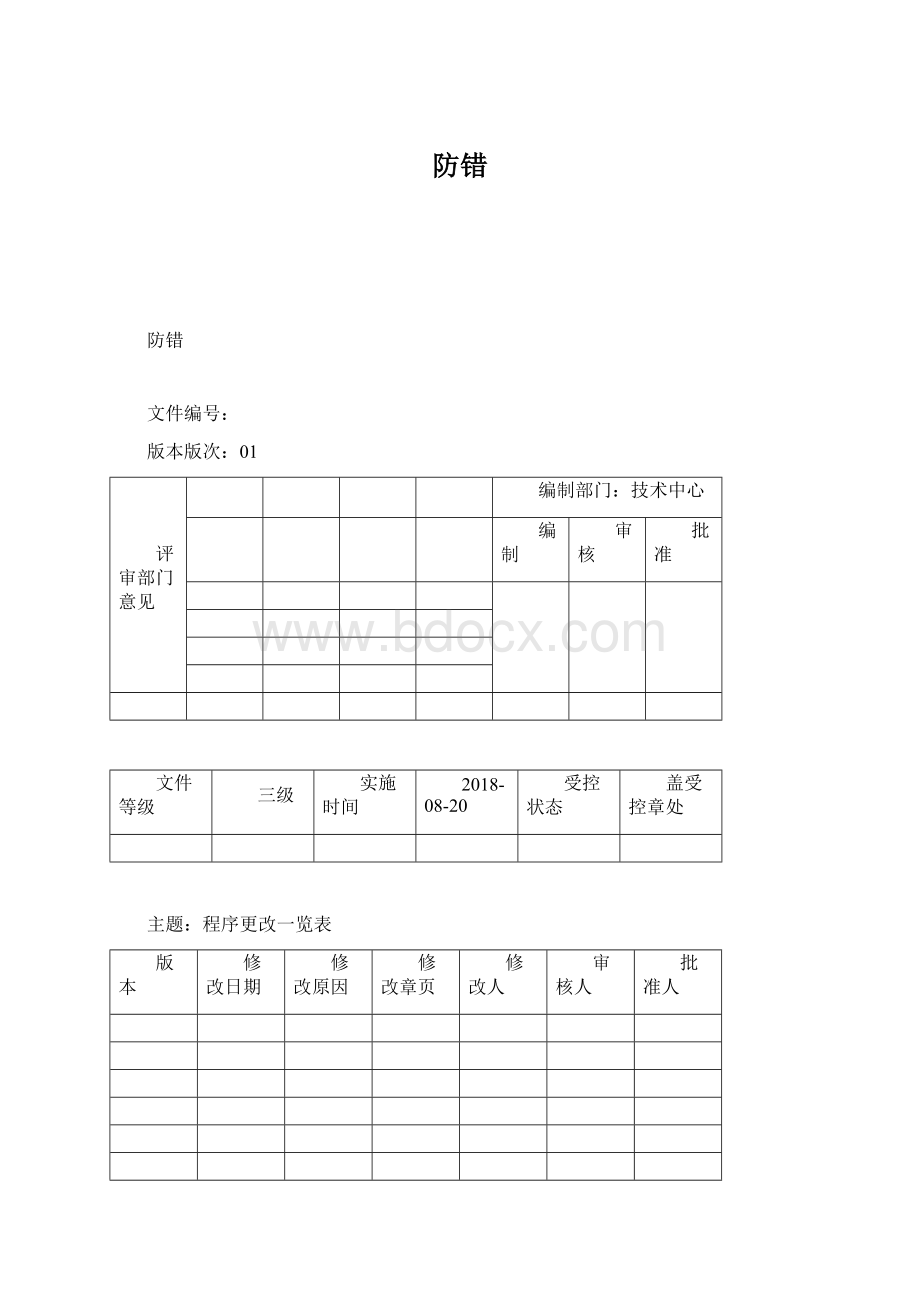
防错
防错
文件编号:
版本版次:
01
评审部门意见
编制部门:
技术中心
编制
审核
批准
文件等级
三级
实施时间
2018-08-20
受控状态
盖受控章处
主题:
程序更改一览表
版本
修改日期
修改原因
修改章页
修改人
审核人
批准人
1目的
从预防的角度出发,使用装置或方法使作业者在作业过程中直接可以明显发现缺陷或即使操作失误后也不会产生缺陷的预防措施,避免作业过程中出现缺陷,提升产品品质,实现零缺陷生产。
2适用范围
适用于新产品设计开发阶段的防错考虑、现有制造过程的防错控制、策划和实施纠正/预防措施的防错。
3定义
防错:
为防止制造不合格产品而进行的产品和制造过程的设计及开发。
防错的思路体现在以下五个方面:
●消除:
消除可能的失误,通过产品和制造过程的重新设计,加入防错方法,是防错设计原则中的最好方法。
●替代:
用更可靠的过程代替目前的过程以减低失误,通过运用机器人技术或自动化生产。
●简化:
使作业更容易完成,通过合并生产步骤,实施工程改善。
●检测:
在缺陷流入下工序前对其进行检测并剔除。
●减少:
将失误影响降至最低,采用保险丝进行过载保护等。
挑战件:
具有已知规范、经校准并且可追溯到标准的零件,其预期结果(通过或不通过)用于确认防错装置或检具(如通止规)的功能性。
临时替代方案:
也称备用方案,是指防错装置失效后,在保证质量的前提下,为保证正常生产而采取的临时替代措施,如100%的人工检测;使用其他替代性的检验工具等。
4职责
4.1技术部负责在产品和过程的设计和开发阶段(包括设计变更)组织项目小组成员进行防错设计。
4.2质管部负责制造现场的防错装置首次验证和挑战件的确定及定期校准。
4.3设备部负责防错装置的制作。
4.4各车间主管负责本区域防错装置的日常管理
4.5各班组长负责本区域防错装置日常点检。
5防错分类
5.1概念性分类
5.1.1定性的防错:
通过图像识别技术,光电、限位、接近开关的逻辑控制技术等来完成防错。
比如:
及时摄片比较、传感器感应检测、加工孔红外线探测、硬靠山、硬探头探测、光栅防错、夹具防错等。
5.1.2定量的防错:
:
通过测量探头感应或经过气电转换的测量技术(气体流量转换成电量)来达到防错的目的,如:
位移传感器、BTS刀具长度检测(CNC加工中心刀具检测可防止错误长度的刀具安装在刀库中,防止加工过程中的断刀现象)、泄漏测试、随线检具直径测量、扭矩控制(螺栓固定的拧紧程度均通过扭矩枪来控制)。
5.1.3颤动功能的防错:
:
通过颤动机的颤动,使零件随着不断的颤动并输送至判别零件的方向正确与否方向处,只有零件处于正确的位置方向时,才能进入轨道;位置方向错误的零件则掉入零件颤动料箱里,从而达到预防零件的进给方向错误,避免工件报废的目的。
5.2防错的标准规范
种类
说明
A:
100%检验
该操作或后续操作存在100%检验,检验是机械的和/或过程
B:
探测和转移
存在有效的设备,能从正常的工艺流程中探测并转移不合格品。
必须证明从合格品中隔离开的不合格品得到标识和控制。
i>预防
通过有效的夹具、控制运行参数等,使不合格品不能被生产。
例如控制产品的夹具方向、根据产品特征进行正确的产品挑选等
C:
极限样品
i>极限样品一定不能通过
极限样品一定不能被防错系统接受,属于不合格品,有明确的不同于正品的区分标识。
所有检验系统必须具有100%拒收极限样品(需要有连续有效的实验证明)
极限样品的确认可以发生在停线事件或快速的交接班检验
ii>尺寸极限样品
极限样品应当被标识并整合进《挑战件清单》,样品必须通过可以追溯的系统验证
iii>验证样品
样品用于证明产品或产品特征或方向的存在或符合。
零件(或零件特征)嵌入设备时设备确定他们存在;零件(或零件特征)移除时设备确定他们“不存在”。
D:
缺陷确认
i>过程步骤
如果缺陷产生,过程必须停止直到工厂指定人员重新启动
如果有缺陷自动识别的装置,则不需要过程停止
ii>可听或可视的报警启动
缺陷产生有信号产生,停止生产或自动拒收产品并向操作员发生信号
E:
根本原因解决程序
当防错设备或方法不能达到预期的效果,功能失效时,须有有效的根本原因解决程序(8D、鱼骨图等)或偏离批准。
F:
现场过程文件
必须具有定义防错装置如何运转的程序,这些程序能够表明如何处理可疑产品和不合格品
G:
定义和计划维护
对防错装置的维护须有明确的定义以及定期的维护计划
H:
交接班检查
必须规定使用极限样品对在使用中的防错设备的验证频率,并展示证据,最低要求在过程开始和每次交接班时执行
6防错验证
6.1防错验证评估
种类
表述
评估分值(10)
A:
100%自动检测
必须所有产品进行检测,不能被绕过
1
B:
产品探测
预防缺陷产品被制造
2
C:
极限样品
设备必须证明通过使用极限样品,100%拒收
1
D:
过程步骤和信号,带有由授权人要求的重启
探测到缺陷时产生信号,或过程停止或自动拒收产品并向操作工发生信号
1
E:
根本原因解决
有有效的解决程序
1
F:
过程文件
文件必须描述临时措施,根本原因解决,如何验证防错装置
2
G:
预防性维护
有文件说明防错装置的维护以及维护计划
1
H:
交接班检查
防错装置适当的功能性检查的频率
1
6.2防错接受标准
分类
绿色
黄色
红色
防错装置种类
得分分值
有措施计划
0分,没有措施计划
装置总分值
达到5.1中的分值
除了E、G其余每个种类均达到分值要求或达到每个种类分值中的至少1分
未达到接受标准,
7流程
工作流程
责任部门
工作内容
记录
技术部
质管部
7.1防错策划
7.1.1在新产品设计开发的初期,技术部应依据类似产品的经验(以往产品不合格报告、顾客反馈和投诉、服务中反馈的信息、市场调研的信息、管理评审提供的信息、质量管理体系审核中收集产品存在的问题的信息、过往问题数据库)、同类厂家的设立情况等来考虑防错装置的设计。
原则上包括但不限于以下几方面应考虑设立防错装置:
a涉及安全、性能方面的; b风险系数和严重度高的;
c左右件及相似件的防错; d安全特性和重要特殊特性优先考虑防错装置的使用;
7.1.2批量等阶段,根据客诉及生产反馈的问题,根据需要制定防错计划,输出防错清单。
7.1.3所有在设计和设计验证阶段输出的防错应整合到控制计划中,并在批量生产阶段被严格执行,同时对其可靠性进行确认。
7.1.4技术部根据PFMEA的设计输出,以及制造现场防错装置的设立,形成产品和过程《防错装置清单》。
清单内容包括:
a.防错装置的工位;b.防错内容;c.防错方法;d.防错结果;e.验证方法;f.验证频次;g.纠正方法;h.临时替代方案。
临时替代方案管理应包括:
a.100%人工检验;
b.100%检查过的特性进行可视化标识(在产品标签上说明);
c.保持应用临时替代方案时的相关记录,以便于追溯;
d.临时替代方案由技术部、质管部、生产评审确认。
临时替代方案下生产的零件应能确保所生产的不合格零件不流入下道工序;
e.临时替代方案必须在防错标识牌(见附件1)红色的一面简单而清晰的描述;
f.防错装置失效后所采取的措施应在《防错功能检查表》中记录。
防错装置清单
防错计划表
N
技术部
7.2防错方案设计
技术部根据防错计划进行防错方案设计,防错方案包括:
防错内容、防错方法、验证方法、验证频次、临时代替方案、防错设计方案、方案预算成本、方案实施计划。
防错方案
技术部
质管部
设备部
Y
生产车间
7.3防错方案评审
7.3.1技术部组织相关部门人员及专家进行防错方案的评审,方案通过后进行方案实施应用;方案未通过,重新进行方案设计。
7.3.2方案评审内容应包含防错内容、防错方法、验证方法、验证频次、临时代替方案、防错设计方案、方案预算成本、方案实施计划。
评审报告
方案实施计划
设备部
采购部
技术部
质管部
7.4防错制造
7.4.1防错装置的制造、采购
7.4.2挑战件制作,挑战件由技术部设计、质管部选取并确认。
防错实体
N
技术部
质管部
生产车间
Y
设备部
7.5防错验证、评审
7.5.1防错装置制作完成后投入生产使用,首次使用,需要对防错装置进行验证,首次验证填写《防错状态评估表》,并对防错装置按防错接受标准进行进行打分评估。
7.5.2验证及通过后并且符合防错接受标准后,移交车间使用。
7.5.3验证未通过,技术部组织分析原因,制定整改计划,整改合格后移交车间使用。
防错状态评估表
防错验证评估表
生产车间
质管部
技术部
设备部
7.6防错实施、维护
7.6.1每条生产线悬挂防错清单,防错要求目视化。
7.6.2在新产品进行首次量产时,质管部应对防错装置清单中的所有防错装置进行一次验证,确保防错装置都应用到了相应的生产工位上面,同时确保防错装置有效。
7.5.3防错装置验证的通用做法是使用挑战件来证明不符合的操作或者不合格的产品能够被探测到。
7.5.4挑战件必须:
a由技术部设计、质管部选取并确认;
b正确标识(挑战件上必须标明零件名称和其应用的设备、模具、工装);
c与正常生产的零件清晰地区分(用油漆笔标识、张贴标签);
d应进行定置定位,并做好防锈工作,存放于防错装置附近的位置,方便操作者存取,有环境要求的,应按要求予以保存;
e质管部应建立《挑战件清单》,对状态、位置、有效期等进行管理。
f质管部应每6个月对挑战件进行校验,以确保其满足防
错的要求。
7.5.5生产车间应依据《防错装置清单》对各工序和工位的防错进行标识,标识卡(见附件1)应包含防错编号、防错功能、临时替代方案内容等信息,并悬挂在防错工位位置。
7.5.6每个操作者应按有防错工序的《作业指导书》的要求,经过防错的培训。
培训包括防错装置的使用和失效后的应急措施。
7.5.7有防错工序的《作业指导书》应体现防错的要求包括临时代替方案,以图文并茂的方式,识别要素和顺序。
7.5.8为了防止防错装置因磨损、失效、移位,操作者应对本工位的防错装置进行至少每天一次的验证,一般是在首件检查、模具或工装更换和设备维修后。
必要时,应通知质管部安排人员使用防错挑战件检查防错装置是否有效。
当过程能力CPK<1.33时,提高验证频次至每班1次或每班2次。
7.5.9防错装置应纳入《防错功能检查表》中检查防错结果。
防错验证合格后方能继续生产,操作者点检验证后作好记录,并将防