车工实训教学情境设计方案1229003024.docx
《车工实训教学情境设计方案1229003024.docx》由会员分享,可在线阅读,更多相关《车工实训教学情境设计方案1229003024.docx(24页珍藏版)》请在冰豆网上搜索。
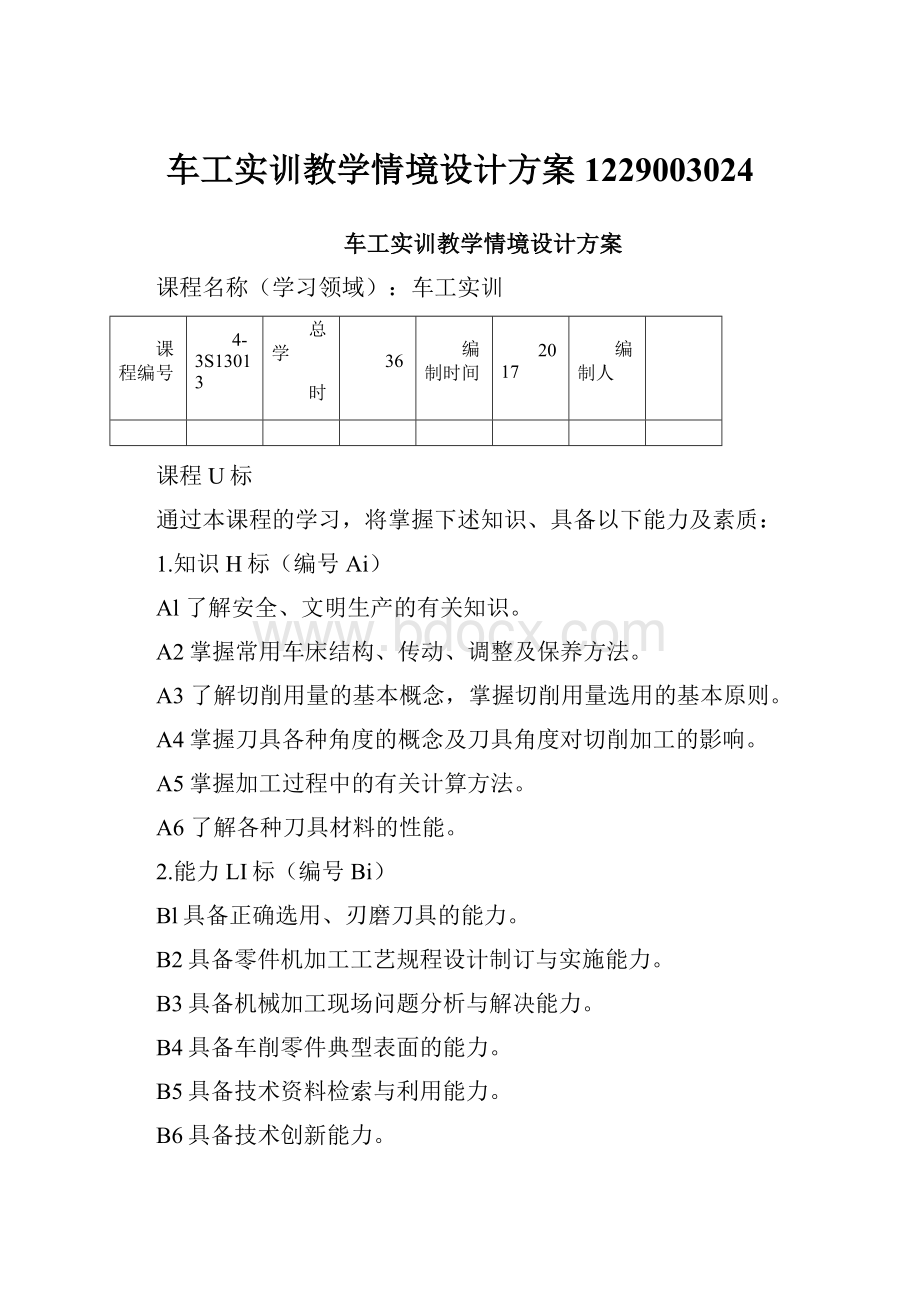
车工实训教学情境设计方案1229003024
车工实训教学情境设计方案
课程名称(学习领域):
车工实训
课程编号
4-3S13013
总学
时
36
编制时间
2017
编制人
课程U标
通过本课程的学习,将掌握下述知识、具备以下能力及素质:
1.知识H标(编号Ai)
Al了解安全、文明生产的有关知识。
A2掌握常用车床结构、传动、调整及保养方法。
A3了解切削用量的基本概念,掌握切削用量选用的基本原则。
A4掌握刀具各种角度的概念及刀具角度对切削加工的影响。
A5掌握加工过程中的有关计算方法。
A6了解各种刀具材料的性能。
2.能力LI标(编号Bi)
Bl具备正确选用、刃磨刀具的能力。
B2具备零件机加工工艺规程设计制订与实施能力。
B3具备机械加工现场问题分析与解决能力。
B4具备车削零件典型表面的能力。
B5具备技术资料检索与利用能力。
B6具备技术创新能力。
3.素质□标(编号Ci)
Cl培养有强烈的事业心、高度的责任感和正直的品质。
C2培养讲诚信,遵守职业道德与法规。
C3培养团队合作精神。
C4培养安全与文明生产意识。
C5培养继续学习能力。
课程内容
1.安全与文明生产。
2.车床结构、用途及日常保养。
3.车刀认识及刃磨。
4.三爪及四爪卡盘装卸工件。
5.轴类零件的加工。
6.套类、盘类零件的加工。
7.螺纹加工。
8.综合练习
项目编号
内容
学时数
项目一
安全与文明生产
项目二
车床结构、用途及日常保养
项目三
车刀认识及刃磨
项目四
三爪及四爪卡盘装卸工件
项目五
轴类零件的加工
项目六
螺纹加r.
教学组织形式与方法:
按照“理论实践一体化”教学模式组织教学过程。
以岗位定能力,能力分解为知识、技能和素质(态度),运用岗位职能需求、项LI支撑、任务驱动的教学过程设计方法,实施工学结合的课程模式改革。
整合实训条件,开展项目驱动、任务引领型理论实践一体化教学活动。
实施场所:
实训车间
课程考核方式:
基于本课程工学结合、“理实一体化”教学特点,建立职业化的综合考评体系,对学生专业能力进行全面、客观、公正地评价。
1.工作过程考核(每一任务完成后进行一次过程考核)(50分)
考核内容如下
工作过程考核
考核项目
自我评价
小组互评
教师评价
安全文明生产(15分)
规范操作(15分)
情感态度(15分)
学习能力(5分)
2.理论考试考核(30分)
3.技能证书考核(20分)
课程教学资源:
1.教材《车工项U式应用教程》清华大学出版社新课改中职教材
2.参考书《车工技能训练项LJ教程》、《普通车工项目式教程》等
3.其他课程网站、课程教学录像、电子课件、习题库等学生知识、能力要求:
1.具有一定机械材料基础知识;
2.识图知识;
3.具有工差配合及技术测量基础知识和基本技能;
4.具有一定机械原理、机械零件的基础知识;
5.具有查阅技术资料的基础知识及基本技能;
6.具有基本的身体协调能力;
7.具有一定的语言表达能力及继续学习能力。
教师能力要求:
1.获得职业学校教师资格证(专任教师);
2.熟悉机械图纸,具备车工中级以上技能证书;
3.掌握工程材料、切削刀具的相关知识;
4.具备熟练、规范操作各种测量工具、仪器的技能;
5.熟悉相应国家标准和工艺规范;
6.熟悉普通车工国家技能等级要求。
任务编号1
任务名称安全与文明生产
学时数
教学
内容
1.车工工作环境认识;
2.车工安全文明生产;
3.车工规范操作要求;
4.“6S”管理体系。
教学
目标
专业
能力
1.初步具有安全文明生产知识;
2.初步认识“6S”管理体系。
职业
素质
1.掌握规范执行工艺文件要求方面的知识;
2.培养学生查阅资料及团队协作、语言表达等方面的能力。
教学
设计
序号
过程
内容
教学方法
1
明确任
务
1.车工工作环境如何?
2.车工安全文明生产有何要求?
3.规范化操作对车工有何意义?
4.“6S”管理体系的构成及意义。
1.讨论法
2.头脑风暴法
3.现场教学
法
4.问答法
5.市场调查
法
2
制定计
划
1.学生分组讨论;
2.头脑风暴提出完成任务的方案;
3.确定具体实施方案。
3
实施计
划
1.走进车间,认识车工工作环境;
2.查阅资料、走访企业相关人员调研;
3.各组学生分别给出各自结论。
4
检査评
价
1.任务是否完成?
2.任务完成过程中存在哪些问题?
是
否解决?
方法是否得当?
3.各组分别展示自己学习成果。
4・老师给出结果评价,评选最优方案
5
总结
1.老师引导学生总结相关知识点;
2.老师整理学生评价资料;
3.布置课后作业:
查阅有关车床用途及结构组成、日常保养方面的资料。
考核项目
自我评价
小组互评
教师评价
工作
安全文明生产
过程
规范操作
评价
情感态度
学习能力
教学
1.车工实训教室
资源
2.多媒体网络
3.相关技术、
管理资料
任务编号
2
任务名称车床用途、结构及日常保养学时数
教学
内容
1.车床用途;
2.车床结构组成;
3.车床的日常保养。
教学
目标
专业
能力
1.初步认识车床作用;
2.初步了解车床组成及各部分作用;
3.简单了解车床日常保养项目及部位
职业
素质
1.培养学生认真负责、一丝不苟的劳动态度;
2.培养学生查阅资、团队协作、语言表达及继续学习方面的能力;
3.培养学生严格执行操作规范要求的职业素养。
教学
设计
序号
过程
内容
教学方法
1
明确
任务
1.车床有何作用(车床能加工零件哪些表面)?
2.车床组成及各部分作用?
3.车床日常保养项目及部位。
1.讨论法
2.头脑风暴法
3.现场教
学法
4.问答法
5.市场调查法
6.示范教
2
制定
计划
1.学生分组讨论;
2.头脑风暴提出完成任务的方案;
3.老师确定具体实施方案。
3
实施
计划
1.查阅资料、走访企业相关人员调研;
2.走进车间,认识车床组成及各部分作用;
3.讲解车床日常保养项目及保养部位。
4
检査
评价
1.任务是否完成?
2.任务完成过程中存在哪些问题?
是否解
决?
方法是否得当?
3.各组分别展示自己学习成果。
4.老师给出结果评价,评选最优方案
学法
5
总结
1.老师引导学生总结相关知识点;
2.老师整理学生评价资料;
3.布置课后作业:
查阅有关车刀材料、结
构及形状方面的资料。
工作
过程
评价
考核项目
自我评价
小组互评
教师评价
安全文明生产
规范操作
情感态度
学习能力
教学
资源
1.车工实训教室;
2.多媒体网络;
3.相关技术、管理资料。
任务编号
3
任务名称车刀认识及刃磨
学时数
教学
内容
1.车刀材料及性能要求;
2.车刀分类(按用途及结构形式);
3.外圆车刀表面组成及角度;
4.车刀刃磨。
教学
目标
专业
能力
1.掌握对车刀材料性能的要求;
2.常用刀具材料及适用场合;
3.掌握车刀分类及各种车刀用途;
4.掌握车刀组成表面、角度及对加工的影响;
5.掌握车刀刃磨方法及要求。
职业
素质
1.培养学生查阅资、团队协作、语言表达及继续学习方面的能力;
2.培养学生认真负责、一丝不苟的劳动态度;
3.培养学生严格执行操作规范要求的职业素养。
教学
设计
序号
过程
内容
教学方法
1
明确
任务
1.车刀材料及性能要求?
2.车刀分类及适用场合?
3.车刀组成表面及对切削的影响?
4.车刀刃磨规范。
1.讨论法
2.头脑风暴法3.现场教学法
4.问答法
5.市场调查
2
制定
计划
1.学生分组讨论;
2.头脑风暴提出完成任务的方案;
3.确定具体实施方案。
3
实施
计划
1.查阅资料、走访企业相关人员调研;
2.走进车间,认识车刀;
3.在老师带领下掌握车刀刃磨操作要
领。
法
6.示范教学
法
4
检查
评价
1.任务是否完成?
2.任务完成过程中存在哪些问题?
是
否解决?
方法是否得当?
3.各组分别展示自己学习成果。
4.老师给出结果评价,评选最优方案
5
总结
1.老师引导学生总结相关知识点;
2.老师整理学生评价资料;
3.布置课后作业:
工件的装夹方案
工作
过程
评价
考核项目
自我评价
小组互评
教师评价
安全文明生产
规范操作
情感态度
学习能力
教学
资源
1.车工实训教室;
2.多媒体网络;
3.相关技术、管理资料。
任务编号
4
任务名称工件的安装
学时数
教学
内容
1.工件定位原理及定位方式;
2.三爪卡盘结构、原理及适用场合;
3.四爪卡盘结构、原理及适用场合。
教学
目标
专业
能力
1.掌握工件定位原理及定位方式基本知识;
2.掌握二爪卡盘使用方法;
3.掌握四爪卡盘使用方法。
职业
素质
1.培养学生查阅资、团队协作、语言表达及继续学习方面的能力;
2.培养学生认真负责、一丝不苟的劳动态度;
3.培养学生严格执行操作规范要求的职业素养。
教学
设计
序号
过程
内容
教学方法
1
明确
任务
1.工件的定位原理?
2.工件的定位方式?
3.三爪卡盘结构及原理?
4.三爪卡盘的规范使用?
5.四爪卡盘的结构、原理及规范使用。
1.讨论法
2.头脑风暴法3.现场教学法
4.问答法
5.市场调查法
6.示范教学
法
2
制定
计划
1.学生分组讨论;
2.头脑风暴提出完成任务的方案;
3.确定具体实施方案。
3
实施
计划
1.查阅资料、走访企业相关人员调研;
2.走进车间,认识车床常用夹具;
3.在老师带领下掌握工件在三爪及四爪卡盘正确安装操作要领。
4
检查
1.任务是否完成?
评价
2.任务完成过程中存在哪些问题?
是
否解决?
方法是否得当?
3.各组分别展示自己学习成果。
4.老师给出结果评价,评选最优方案
5
总结
1.老师引导学生总结相关知识点;
2.老师整理学生评价资料;
3.布置课后作业:
轴类零件都有哪些?
如何加工?
工作
过程
评价
考核项目
自我评价
小组互评
教师评价
安全文明生产
规范操作
情感态度
学习能力
教学
资源
1.车工实训教室;
2.多媒体网络;
3.相关技术、管理资料。
任务编号
5
任务名称车削外圆、端面、钻中心孔
学时数
教学
内容
1.机床运动分析;
2.切削表面与切削用量;
3.车床车削外圆、端面、钻中心孔
教学
目标
专业
能力
1.掌握机床传动的基本知识;
2.掌握车削加工过程中切削表面及切削用量的知识;
3.掌握车削外圆、端面及钻中心孔操作要领。
职业
素质
1.培养学生分析方法能力;
2.培养学生基本计算能力;
3.培养学生认真负责、一丝不苟的劳动态度;
4.培养学生严格执行操作规范要求的职业素养。
教学
设计
序号
过程
内容
教学方法
1
明确
任务
丄.机床运动包括哪些?
2.机床传动的组成?
3.车削不同表面时切削表面有哪些?
4.车削时的切削用量的概念、意义及对
加丄的影响?
5.如何车削外圆?
6.如何车削端面?
7.钻中心孔的操作要领?
8.如何车削阶梯轴?
1.分析讨论
法2.展示法
3.问答法
4.讲解法
5.现场教学法
6.示范教学法
2
制定
汁划
1.分析任务,将所提出任务进行归类;
2.提出完成不冋任务的方案;
3.确定完成各具体任务的实施方案。
3
实施
计划
1.査阅资料、走访企业相关人员调研;
2.走进车间,认识车床各种运动及加工方式;
3.在老师引导下掌握机床传动、切削用量概念及与车床加工之间的关系;
4.在老师示范引导下完成车外圆、端面、台阶轴及钻中心孔规范操作要领的掌握。
7•练习法
4
检查
评价
1.任务是否完成?
2.任务完成过程中存在哪些问题?
是
否解决?
方法是否得当?
3.老师给出结果评价,评选最优方案
5
总结
1.老师引导学生总结相关知识点;
2.老师整理学生评价资料;
3.布置课后作业:
外锥面如何车削
考核项目
自我评价
小组互评
教师评价
工作
安全文明生产
过程
规范操作
评价
情感态度
学习能力
教学
资源
1.车工实训教室;
2.多媒体网络;
3.相关技术、管理资料;
4.其它阅读教材。
任务编号
6
任务名称车槽、切断及倒角
学时数
教学
内容
1.轴类零件外表面环槽及倒角的作用;
2.车槽;
3.轴类零件的切断;
4.轴端倒角加工。
教学
目标
专业
能力
1.了解轴类零件表面环槽及倒角知识;
2.掌握车槽的操作要领;
3.掌握切断的操作要领;
4.掌握倒角加工的操作要领。
职业
素质
1.培养学生认真负责、一丝不苟的劳动态度;
2.培养学生严格执行操作规范要求的职业素养。
教学
设计
序号
过程
内容
教学方法
1
明确
任务
1.轴类零件外表面环槽及倒角有何作用?
2.如何车削轴类零件外表面环槽?
3.轴类零件如何在车床上切段?
4.如何车削轴端倒角?
1.分析讨论法2.问答法
3.讲解法
4.现场教学法
5.示范教学法
6.练习法
2
制定
计划
1.分析任务,査阅资料;
2.老师引导提出方案;
3.确定完成各具体任务的实施方案。
3
实施
计划
1.查阅资料、走访企业相关人员调研轴类零件表面环槽及倒角的作用;
2.在老师示范引导下掌握车轴类零件外表面环槽规范操作要领;
3.学习练习切断轴类零件;
4.学习练习车削轴端倒角。
4
检查
评价
1.任务是否完成?
2.任务完成过程中存在哪些问题?
是
否解决?
方法是否得当?
3.老师给出结果评价,评选最优方案。
5
总结
1.老师引导学生总结相关知识点;
2.老师整理学生评价资料;
3.布置课后作业:
轴类零件表面滚花的作用。
工作
过程
评价
考核项目
自我评价
小组互评
教师评价
安全文明生产
规范操作
情感态度
学习能力
教学
资源
1.车工实训教室;
2.多媒体网络;
3.相关技术、管理资料;
4.其它阅读教材。
任务编号
7
任务名称车削外锥面
学时数
教学
内容
1.轴类零件外锥面的作用;
2.摆移小刀架法车外圆锥面;
3.偏移尾座法车外锥面;
4.宽刀法车外锥面。
教学
目标
专业
能力
1.掌握轴类零件外锥面在零件中所起作用的基本知识;
2.掌握摆移小刀架法车外圆锥面的操作要领;
3.掌握偏移尾座法车外锥面;
4.了解宽刀法车外锥面。
职业
素质
1.培养学生基本计算能力;
2.培养学生认真负责、一丝不苟的劳动态度;
3.培养学生严格执行操作规范要求的职业素养。
教学
设计
序号
过程
内容
教学方法
1
明确
任务
1.轴类零件外锥面有何作用?
2.如何车削外圆锥面?
1.分析讨论法2.问答法
3.讲解法
4.现场教学法
5.示范教学法
2
制定
计划
1.分析任务,查阅资料;
2.提出完成不同任务的方案;
3.确定完成各具体任务的实施方案。
3
实施
计划
1.查阅资料、走访企业相关人员调研外锥面的作用;
2.在老师示范引导下掌握车外锥面规范操作要领。
4
检查
评价
1.任务是否完成?
2.任务完成过程中存在哪些问题?
是
否解决?
方法是否得当?
3.老师给出结果评价,评选最优方案
6•练习法
5
总结
1.老师引导学生总结相关知识点;
2.老师整理学生评价资料;
3.布置课后作业:
外锥面如何车削
工作
过程
评价
考核项目
自我评价
小组互评
教师评价
安全文明生产
规范操作
情感态度
学习能力
教学
资源
1.车工实训教室;
2.多媒体网络;
3.相关技术、管理资料;
4.其它阅读教材。
任务编号8任务名称
车普通外螺纹
学时数
教学
内容
1•加工普通外螺纹;
2.测量普通外螺纹
教学
目标
专业
能力
1.了解三角螺纹的标记方法,掌握三角螺纹的尺寸计算方法;
2.掌握普通外螺纹车刀儿何形状和刃磨方法;
3.掌握普通外螺纹车刀的加工方法;
4.掌握普通外螺纹的检测方法。
职业
素质
1.培养学生团队协作、语言表达及继续学习方面的能力;
2.培养学生认真负责、一丝不苟的劳动态度;
3.培养学生严格执行操作规范要求的职业素养。
教学
设计
序号
过程
内容
教学方法
1
明确任务
1.普通外螺纹如何标记?
2.普通外螺纹各部分名称及其尺寸如何计算?
3.普通外螺纹车刀有何特点?
如何装夹?
4.车螺纹询机床如何调整?
5.如何车外螺纹?
1.分析讨论法
2.问答法
3.讲解法
4.现场教学法
5.示范教学法
6.练习法
2
制定计划
「学生分组讨论;
2.头脑风暴提出完成任务的方案;
3.老师确定具体实施方案。
3
实施计划
外螺纹标记、尺寸计算、螺纹车刀儿何参数等内容自学、讨论、合作学习后进行组内、组间讲解,教师进
行补充。
2.车刀刃磨、机床调整、车外螺纹等内容进行现场教学演示后学生进行练习操作。
4
检查评价
1.任务是否完成?
2.任务完成过程中存在哪些问题?
是否解决?
方法是否得当?
3.各组分别展示自己学习成果。
4.老师给出结果评价。
5
总结
1.老师引导学生总结相关知识点;
2.老师整理学生评价资料;
3.布置课后作业:
工作
过程
评价
考核项目
自我评价
小组互评
教师评价
出勤、课堂纪律
工夹量具的正确
选择
规范操作
任务完成情况
其他方面
教学
资源
1.车工实训教室;
2.多媒体网络;
3.相关技术、管理资料;
4.其它阅读教材。