烧结钕铁硼的生产工艺流程概要.docx
《烧结钕铁硼的生产工艺流程概要.docx》由会员分享,可在线阅读,更多相关《烧结钕铁硼的生产工艺流程概要.docx(14页珍藏版)》请在冰豆网上搜索。
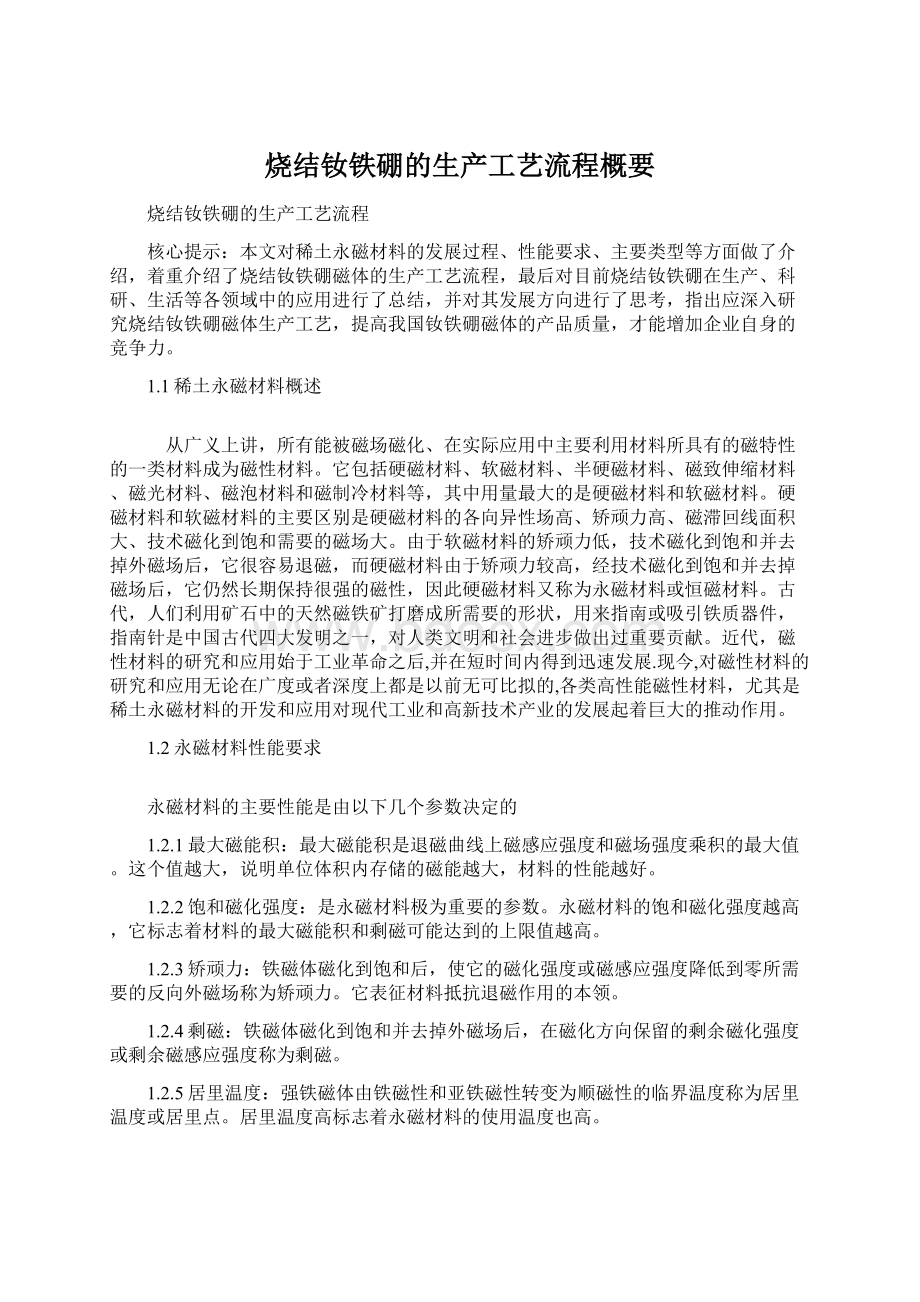
烧结钕铁硼的生产工艺流程概要
烧结钕铁硼的生产工艺流程
核心提示:
本文对稀土永磁材料的发展过程、性能要求、主要类型等方面做了介绍,着重介绍了烧结钕铁硼磁体的生产工艺流程,最后对目前烧结钕铁硼在生产、科研、生活等各领域中的应用进行了总结,并对其发展方向进行了思考,指出应深入研究烧结钕铁硼磁体生产工艺,提高我国钕铁硼磁体的产品质量,才能增加企业自身的竞争力。
1.1稀土永磁材料概述
从广义上讲,所有能被磁场磁化、在实际应用中主要利用材料所具有的磁特性的一类材料成为磁性材料。
它包括硬磁材料、软磁材料、半硬磁材料、磁致伸缩材料、磁光材料、磁泡材料和磁制冷材料等,其中用量最大的是硬磁材料和软磁材料。
硬磁材料和软磁材料的主要区别是硬磁材料的各向异性场高、矫顽力高、磁滞回线面积大、技术磁化到饱和需要的磁场大。
由于软磁材料的矫顽力低,技术磁化到饱和并去掉外磁场后,它很容易退磁,而硬磁材料由于矫顽力较高,经技术磁化到饱和并去掉磁场后,它仍然长期保持很强的磁性,因此硬磁材料又称为永磁材料或恒磁材料。
古代,人们利用矿石中的天然磁铁矿打磨成所需要的形状,用来指南或吸引铁质器件,指南针是中国古代四大发明之一,对人类文明和社会进步做出过重要贡献。
近代,磁性材料的研究和应用始于工业革命之后,并在短时间内得到迅速发展.现今,对磁性材料的研究和应用无论在广度或者深度上都是以前无可比拟的,各类高性能磁性材料,尤其是稀土永磁材料的开发和应用对现代工业和高新技术产业的发展起着巨大的推动作用。
1.2永磁材料性能要求
永磁材料的主要性能是由以下几个参数决定的
1.2.1最大磁能积:
最大磁能积是退磁曲线上磁感应强度和磁场强度乘积的最大值。
这个值越大,说明单位体积内存储的磁能越大,材料的性能越好。
1.2.2饱和磁化强度:
是永磁材料极为重要的参数。
永磁材料的饱和磁化强度越高,它标志着材料的最大磁能积和剩磁可能达到的上限值越高。
1.2.3矫顽力:
铁磁体磁化到饱和后,使它的磁化强度或磁感应强度降低到零所需要的反向外磁场称为矫顽力。
它表征材料抵抗退磁作用的本领。
1.2.4剩磁:
铁磁体磁化到饱和并去掉外磁场后,在磁化方向保留的剩余磁化强度或剩余磁感应强度称为剩磁。
1.2.5居里温度:
强铁磁体由铁磁性和亚铁磁性转变为顺磁性的临界温度称为居里温度或居里点。
居里温度高标志着永磁材料的使用温度也高。
1.3稀土永磁材料的主要类型
至今,稀土永磁材料已有两大类、三代产品
第一大类是稀土-钴合金系(即RE-Co永磁),它又包括两代产品。
1996年K.Strant发现SmCo5型合金具有极高的磁各向异常数,产生了第一代稀土永磁体1:
5型SmCo合金。
从此开始了稀土永磁材料的研究开发,并于1970年投入生产;第二代稀土永磁材料是2:
17型的SmCo合金大约是1978年投入生产。
它们均是以金属钴为基体的永磁材料合金。
第二大类是钕铁硼合金(即Nd-Fe-B系永磁)。
1983年日本和美国同时发现了钕铁硼合金,称为第三代永磁材料,当Nd原子和Fe原子分别被不同的RE原子和其他金属原子取代可发展成多种成分不同、性能不同的Nd-Fe-B系永磁材料。
其制备方法主要有烧结法、还原扩散法、熔体快淬法、粘结法、铸造法等,其中烧结法和粘结法在生产中应用最广泛[3]。
下表列出了不同稀土永磁材料的磁性能。
材料种类
最大磁能积
/Kj.m-3
剩余磁通
/T
磁感矫顽力
/kA.m-1
内禀矫顽力
/kA.m-1
居里温度
/0C
SmCo5系
100
0.76
550
680
740
SmCo5系(高Hc)
160
0.90
700
1120
740
Sm2Co17系
240
1.10
510
530
920
Sm2Co17系(高Hc)
280
0.95
640
800
920
烧结Nd-Fe-B系
240-400
1.1-1.4
800-2400
-
310-510
粘结Nd-Fe-B系
56-160
0.6-1.1
800-2100
-
310
Sm-Fe-N系
56-160
0.6-1.1
600-2000
-
310-600
从上表可以看出钕铁硼永磁材料的综合磁性能最好,并且烧结法优于粘结法。
所以下面主要介绍烧结钕铁硼永磁材料的生产流程。
2烧结钕铁硼的生产流程
总流程如下:
2.1熔炼工段
熔炼工段主要负责将按比例称量好的原材料进行熔炼,分为配料和熔炼两个部分
2.1.1配料
1、常用的金属有如下几种:
金属钕,镨钕,特硼,精硼,铜,铝,镓,铽,钴,铁(太原铁、武钢铁、上海铁),镝铁,铌铁。
2、所用仪器、工具、辅助材料等:
不同规格的电子秤、钢筋切断机、除锈抛光机、橡胶手套、口罩
3、工作流程:
根据当天的生产要求,统计各种原材料的用量,经核对后去原材料库领料;回来后据单配料,大体上分为两种,与熔炼工段的熔炉相对应,大炉用来铸片,小炉铸锭。
配料时以及配料完成后要完成相关的记录。
接下来有专门人员会来复称,大炉的料样样都要检,检后配放锁车推至熔炼处,为第二天的备料。
小炉的料一般要抽查,基本每一车8桶左右,每车抽一桶检验,复称小料及其他,查看是否合格。
基本上每天的小炉备料为55桶。
大炉的备料一般在10桶以下。
4、注意事项:
(1)因称量金属时在空气中有金属粉末,所以在操作过程中需要戴口罩。
而且为防止金属碰伤手需要佩戴专用手套
(2)由于原材料库中的铁棒较长并且容易生锈,所以在配料时需要切断并抛光,以便于称量并减少杂质。
(3)在操作钢筋切断机时需要特别注意安全,小心伤到手指。
(4)正确熟练掌握电子称的用法,将公差严格控制在要求范围内。
复称时更需严格把关,保证后续的有效正常生产。
作业过程的正确与否直接影响到产品的优劣高低。
2.1.2熔炼
熔炼主要负责将配好的料进行铸片或铸锭,分别由大炉和小炉完成。
1、铸片熔炼
(1)所用仪器、工具、辅助材料等:
FMI-I-500R真空熔炼铸片炉、行车、原料车、吊具、铁锤、铁夹、吸尘器、辅助照明工具、炉渣桶、秒表、热电偶、氮气、氩气、手套、防尘口罩、海绵
(2)流程图如下:
(3)注意事项
①装料时,一般坩埚口周围温度较高,操作时应穿大头鞋、防护手套、垫好隔热垫,以免烫伤
②吊装过程中必须在吊装区内作业;吊装前应仔细检查钢丝绳、吊钩、吊架,确保正常;吊装时,应确保安全隔离区内无人,设备平台吊装车行进路线上无人、以防人员伤害
③浇注时,上操作员应留在浇注控制位,观察浇注口液体流动情况,并时刻留意下操作员的信息反馈;下观察员应持续观察中间包侧部溢流口及铜辊轮与中间包结合部位情况,当发现溢流口合金液溢出或中间包底板漏液等异常现象时应及时通知上操作员,此时应暂停浇注,待异常消除后继续浇注[4]。
④更换中间包作业需佩戴口罩,减小粉尘对人体的危害。
⑤卸料及装料时操作人员应佩戴手套、口罩、不得裸手作业。
防止人体对铸片的污染;防止铸片划伤人体。
2、铸锭熔炼
(1)所用所用仪器、工具、辅助材料等:
真空感应熔炼炉、原料车、出料车、铁夹、炉渣桶、辅助照明灯、套装工具、出料桶、氮气、氩气、耐火材料、绝热手套、防尘口罩
(2)流程:
准备→装料→抽真空→熔炼→浇铸→冷却→出料
(3)操作规程:
预抽阀开,真空计开→抽到0.08以下→开罗茨泵→真空计为0时→关闭预抽阀和罗茨泵,关真空计→开充气阀充氩→至压力表压力为0.05MPa时(0.04-0.06MPa)→关闭充气阀停止充氩→开主电源和控制电源→功率调大→铁棒全溶入合金液时,精炼,静置2分钟→开始浇铸→冷却25分钟(出炉温度要求在80℃以下)→放气(开放气阀,手动)→关电源→出炉[5]。
(4)注意事项
①装料和出料时戴好口罩,防止吸入金属粉尘;
②设备电气操作与检查时应注意力集中,防止触电;
③在熔炼过程中,应密切注意各路冷却水的流量和温度。
由于停电或其它原因导致冷却水不能正常供应时,需将自来水送入冷却系统;如正在熔炼过程出现停水现象,应迅速停止输送功率,并将自来水接入冷却系统,重点冷却感应线圈。
待循环冷却水恢复正常时,再关闭自来水,切换成循环冷却水,继续升温熔炼。
如钢液有飞溅现象,应立即停止送功率,检查并排除故障;
④在浇注过程中,如遇到浇穿冷锭模,并出现大量漏水,应迅速关闭冷锭模冷却水开关,注意氩气压力表的变动,打开炉门取出材料;若在熔炼时发生线圈漏水则应停止送功率,减少感应线圈冷却水的流量,在氩气保护下,待坩埚内料冷却后,方可打开炉盖进行处理[6]。
⑤在出料后,若发现浇口杯有明显裂纹、断裂现象,应及时更换,以防下次浇注时合金液外流。
2.2制粉工段
制粉工段负责将熔炼后的产品制成细粉,主要过程有氢碎(中碎)、粗粉搅拌、气流磨、细粉搅拌。
低牌号产品生产流程:
配料→铸锭→破碎→中碎→粗粉搅拌→气流磨→细粉搅拌。
高牌号产品生产流程:
配料→铸片→氢碎→粗粉搅拌→气流磨→细粉搅拌。
流程图如下:
2.2.1氢碎
1、氢碎原理:
利用稀土金属间化合物的吸氢特性,将钕铁硼合金置于氢气环境下,氢气沿富钕相薄层进入合金,使之膨胀爆裂而破碎,沿富钕相层处开裂,从而使薄片变为粗粉[7]。
2、所用仪器、工具、辅助材料等:
国产YS200型氢碎炉、日产PHGgr50/50/200S氢碎炉、装料装置、装卸料车、氩气、氢气、氮气、风扇
3、操作规程
(1)准备:
观察氮气压力、水源压力符合氢碎工艺卡要求。
在氢碎炉控制仪上设定工艺参数,并复核。
根据《设备检点表》对设备进行检点。
(2)装炉:
打开炉门,用吸尘器清理炉膛,取下料筒固定销,用装料车将氢碎料筒放入炉膛内,将装料车高度放低拉出。
用棉布擦拭炉门、胶圈,关闭炉门。
将已填写的《产品标识卡》放置在炉门上。
(3)氢碎:
①检漏:
按下“自动运行”,氮气导入炉体,设备开始进行正压检漏,检漏后炉体排气至大气压,进行抽真空负压检漏。
当符合工艺卡要求后,设备报警提示,此时按下H2阀开,氢碎进入自动运行阶段,导入氢气。
②导氢:
当炉内压力达到工艺卡中吸氢最大值时关闭,料吸氢后炉内压力下降,系统自动导入氢气至最大值,反复这一过程,经过系统确认,料筒旋转启动,压力保持在最大值不变,标明料不再吸氢,确认8分钟,导氢完成。
③置换:
系统自动打开排气阀,排气至大气压时关闭,三个氩气导入阀先后打开。
压力达到置换压力时,其中一个氩气导入阀关闭,其他两个为常开,排气阀自动打开排气,如此反复到设定时间。
排气阀打开,排气至大气压,置换完成。
④脱氢:
抽气系统自动启动,先抽气至40mba以下时,系统自动通电升温,边升温边抽真空,一般升温40分钟。
温度达到工艺卡设定温度时,保温1-3小时。
真空度达到工艺卡要求时,脱氢完成。
若达不到要求会继续抽气,直至达到要求,脱氢完成,抽气系统自动关闭。
⑤冷却:
抽气系统关闭后,此时三个氩气阀自动打开充入氩气于置换压力值,风机自动风冷,炉内压力不足时,自动补充,风冷3-5小时左右,达到35-40度时系统开始记录冷却停止时间,一般为20分钟左右。
到达冷却设定时间后,氩气导入阀自动关闭,风机自动关闭,排气阀打开排气,排气至大气压时可出炉。
⑥出炉:
氢碎完成后,“EDN”指示灯亮,设备发出报警提示声音,此时可出炉。
打开炉门,用装料车将料筒取出放置在冷却区料筒架上,及时给料筒通入氮气,打开冷却风扇。
⑦料筒在冷却区达到冷却温度后,将料筒转运到出料区,将料筒的盖子换为漏斗状盖子,将产品倒入已清洗的钢瓶中。
4、粗粉搅拌
粗粉搅拌是通过搅拌罐的旋转使氢碎(中碎)后的粗粉混合均匀。
工艺流程:
(1)搅拌罐定压:
打开搅拌罐截止阀,打开搅拌罐排气罐,观察压力表,直至符合工艺卡要求。
间断打开关闭排气罐,观察压力