专用铣床的液压及电控系统的设计与维护毕业设计论文.docx
《专用铣床的液压及电控系统的设计与维护毕业设计论文.docx》由会员分享,可在线阅读,更多相关《专用铣床的液压及电控系统的设计与维护毕业设计论文.docx(31页珍藏版)》请在冰豆网上搜索。
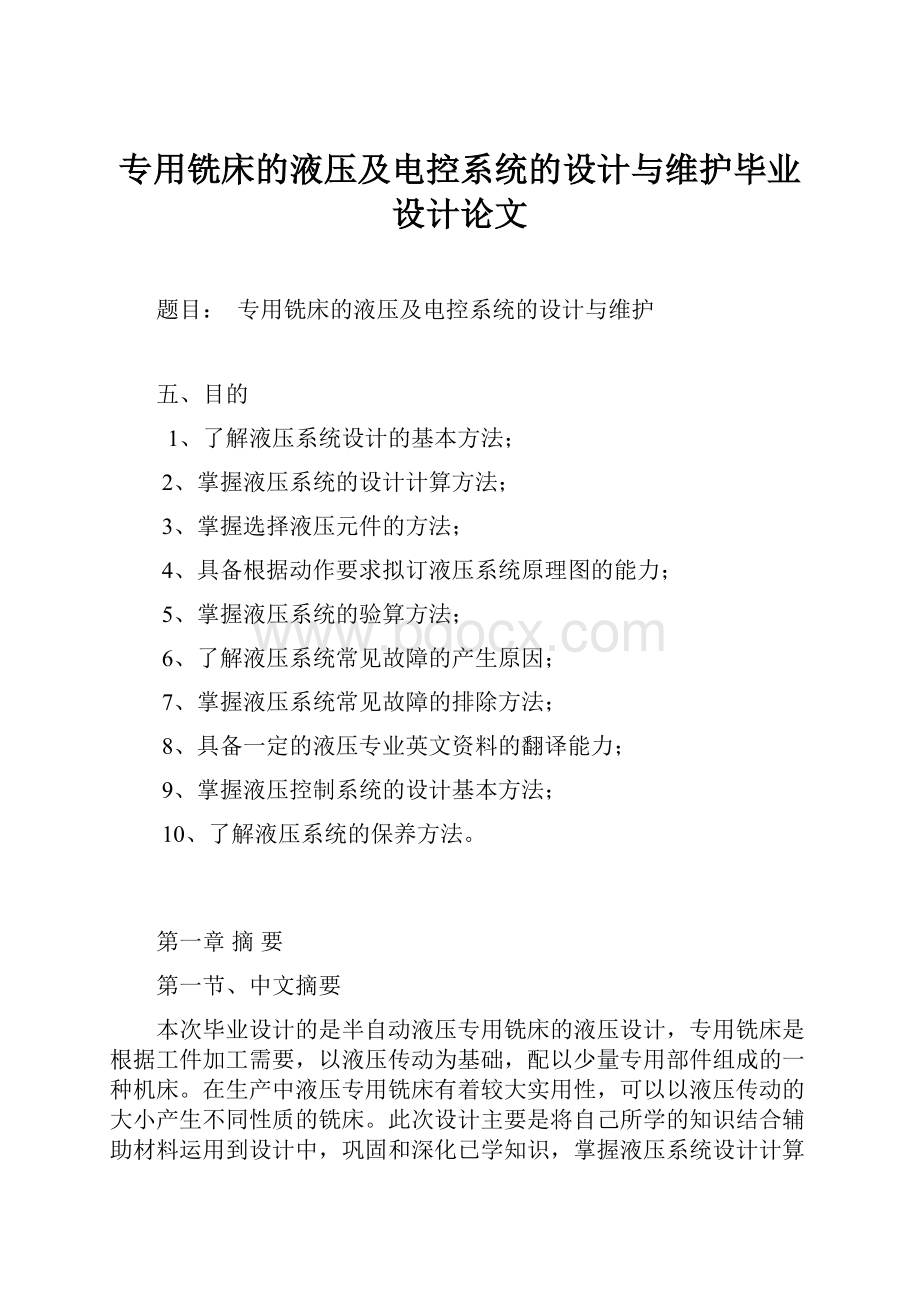
专用铣床的液压及电控系统的设计与维护毕业设计论文
题目:
专用铣床的液压及电控系统的设计与维护
五、目的
1、了解液压系统设计的基本方法;
2、掌握液压系统的设计计算方法;
3、掌握选择液压元件的方法;
4、具备根据动作要求拟订液压系统原理图的能力;
5、掌握液压系统的验算方法;
6、了解液压系统常见故障的产生原因;
7、掌握液压系统常见故障的排除方法;
8、具备一定的液压专业英文资料的翻译能力;
9、掌握液压控制系统的设计基本方法;
10、了解液压系统的保养方法。
第一章摘要
第一节、中文摘要
本次毕业设计的是半自动液压专用铣床的液压设计,专用铣床是根据工件加工需要,以液压传动为基础,配以少量专用部件组成的一种机床。
在生产中液压专用铣床有着较大实用性,可以以液压传动的大小产生不同性质的铣床。
此次设计主要是将自己所学的知识结合辅助材料运用到设计中,巩固和深化已学知识,掌握液压系统设计计算的一般步骤和方法,正确合理的确定执行机构,选用标准液压元件,能熟练的运用液压基本回路,组成满足基本性能要求的液压系统。
在设计过程中最主要的是图纸的绘制,这不仅可以清楚的将所设计的内容完整的显示出来,还能看出所学知识是否已完全掌握了。
整个设计过程主要分成六个部分:
参数的选择、方案的制定、图卡的编制、专用铣床的设计、液压系统的设计以及最后有关的验算。
主体部分基本在图的编制和液压系统的设计两部分中完成的。
关键词:
专用液压铣床,液压传动,回路,夹具
第二节、Abstract
Thegraduationdesignissemi-automatichydraulicspecialmillingmachine,hydraulicdesignspecialmillingmachineisbasedonneedsofwork,basedonhydraulictransmission,matchwithafewspecialpartsofamachinetool.Duringproductionhasgreatpracticalhydraulicspecialmillingmachine,canwithhydraulicdrivesizeproducesdifferentnatureofthemillingmachine.Thisdesignismainlywithmyownknowledgewillbeappliedtodesignofauxiliarymaterials,strengtheninganddeepeningpriorknowledgeofhydraulicsystemdesigncalculation,thegeneralprocedureandmethodtodeterminethecorrectmethodofactuator,choosestandardhydrauliccomponents,canskilledusinghydraulicbasiccircuit,compositionsatisfybasicperformancerequirementsofthehydraulicsystem.Inthedesignprocessofthemainisdrawing,whichnotonlycanclearlydrawndesignedbythecompletenessofthecontentswillshowout,stillcanseewhethertheknowledgealreadycompletemastery.
Thewholedesignprocessmainlydividedintosixparts:
parameterselection,planformulation,thefigurecardplanning,specialmillingmachinedesign,hydraulicsystemdesignandfinalrelevantcalculating.Themepartincludesgraphpreparationandhydraulicsystemdesign
KeyWords:
Specialmillingmachine,hydraulictransmission,loop,fixture
目录
第一章摘要……………………………………………………………………………3
第一节中文摘要…………………………………………………………………3
第二节Abstract…………………………………………………………………4
第二章设计的目的……………………………………………………………………6
第三章液压系统的优点与不足…………………………………………………………6
第四章设计内容………………………………………………………………………7
第五章负载分析与计算…………………………………………………………………7
第六章液压原理图设计与分析…………………………………………………………10
第一节液压缸参数的设计………………………………………………………11
第二节确定液压泵的流量、压力和选择泵的规格……………………………14
第三节液压阀,液压阀,油管和邮箱的选择…………………………………15
第四节液压系统的验算…………………………………………………………17
第七章液压系统的维护与保养…………………………………………………………20
第一节日常维护…………………………………………………………………20
第二节定期维护…………………………………………………………………20
第三节综合维护…………………………………………………………………20
第四节液压系统常见故障及排除方法…………………………………………20
第八章电控系统控制设计………………………………………………………………23
第一节各电磁铁动作顺序表……………………………………………………23
第二节PLC控制连接图…………………………………………………………24
第三节继电器-接触器控制连接图………………………………………………25
第四节PLC控制梯形图…………………………………………………………26
第五节指令语句表………………………………………………………………27
第九章感受与收获………………………………………………………………………28
第十章致谢………………………………………………………………………………28
第十一章参考资料………………………………………………………………………29
第二章、设计的目的
1、了解液压系统设计的基本方法;
2、掌握液压系统的设计计算方法;
3、掌握选择液压元件的方法;
4、具备根据动作要求拟订液压系统原理图的能力;
5、掌握液压系统的验算方法;
6、了解液压系统常见故障的产生原因;
7、掌握液压系统常见故障的排除方法;
8、具备一定的液压专业英文资料的翻译能力;
9、掌握液压控制系统的设计基本方法;
10、了解液压系统的保养方法。
第三章、液压系统的优点与缺点
1、优点:
(1)单位功率的重量轻,统计资料表明,液压泵和液压马达单位功率只有发电机和电动机的十分之一,液压泵和液压马达可小至0.0025N/m,而同等功率的发电机和电动机则约为0.03N/W。
至于尺寸,前者约为后者的12%-13%,就输出而言,用泵很容易得到极高压力的液压油液,将此油液传送至液压缸后即可产生很大的作用力,所以液压技术具有重量轻,体积小和出力大的突出特点,有利于机械设备及其控制系统的微型化、小型化、并进行大功率作业。
(2)布局灵活方便。
液压元件的布置不受严格的空间来限制,容易照机器的需要通过管道来实现,系统中各部分的连接,布局安装具有很大的柔性能构成用其他方法难以组成的复杂系统。
(3)调速范围大。
通过控制阀,液压传动可以在运行过程中实现液压执行器大范围的无极调速,调速的范围可达2000.
(4)工作平稳,快速性好,油液具有弹性,可吸收冲击,故液压传动传递运动均匀平稳,易于实现快速启动、制动和频繁换向,往复回转运动的换向频率,可达500次/分,往复直线运动的换向频率高达1000次/分。
(5)易于操纵控制并实现过载保护。
液压系统操纵控制方便,易于实现自动控制,远距离遥控和过载保护,运转时可以自行润滑,有利于散热和延长使用寿命。
(6)易于自动化和机电液体一体化,液压技术容易与电气、电子控制技术相整合,组成机电液一体化的复杂系统,实现自动化工作循环。
(7)易于实现直线运动,用液压实现直线运动比机械实现直线运动方便。
(8)液压系统设计,制造和使用维护方便,液压元件属于机械工业基础件,已实现了标准化、系列化和通用化、因此,便于液压系统的设计、制造和使用维护,有利于缩短机器设备的设计制造周期并降低制造成本。
2、缺点:
(1)不能保证定比运动,由于液体的压缩性和泄露等因素的影响,液压技术不能严格保证定比运动。
(2)传动效率偏低。
传动过程中需经两次转换,常有较多的能量损失,因此传动效率偏低。
(3)工作稳定性易受温度影响,液压系统对温度较为敏感,不宜在过高或过低温度下工作,采用石油基介质作为传动介质时还需注意防火问题。
(4)造价较高,液压元件制造精度要求较高以防止和减少泄露,所以造价较高。
(5)故障诊断困难。
液压元件与系统容易因液压油液污染等原因造成系统故障,且发生的故障不易诊断。
第四章、设计内容
1、液压系统设计要求:
设计一套专用双行程铣床的液压系统。
要求:
工作安装在工作台上,工作台往复运动有液压系统实现。
双向铣削。
工件的定位和加紧由液压实现、铣刀的进给由机械步进装置完成,每一行程进刀一次。
要求采用容积节流调速回路,即采用限压式变量泵加调速阀调速,回油要求有背压,工作台双向速度相等,但要求前四次速度为V01(粗加工),然后手动切换为V02。
再往复运动四次(精加工)。
机床的工作循环为:
手工上料------按电钮------工件自动定位夹紧------工作台往复运动铣削工件若干次------停止铣削------夹具松开------手工卸料(泵卸载)。
定位缸的负载F1200N、行程S110mm,动作时间t11S;
夹紧缸的负载F22000N、行程S215mm,动作时间t21S;
工进缸的铣削负载为:
F0118000N(粗加工)和F029000N(精加工);
工作台要求速度:
V01为0.6-6m/min(粗加工)和V02为0.5-5m/min(精加工);
工作台往复运动的行程为:
S3100-270mm。
根据设计的需要,假设铣床的快进和快退的最快的速度为:
16m/min
动摩擦力为2500N,静摩擦力为5000N
参数:
F1
F2
S1
S2
T1
T2
F01
F02
V01
V02
S3
280
2200
8
12
1
1
16000
7000
0.6-6
0.5-5
100-270
第五章、负载分析与计算
取液压缸的机械效率为0.9。
计算液压缸驱动力
(N)2-1
根据公式2-1,计算液压缸驱动力
得定位液压缸的驱动力为
得夹紧液压缸的驱动力为
切削负载(F01/F02):
16000/7000N;
工作台液压缸总负载
2-2
为工作负载,为惯性负载,为摩擦阻力负载
=F01/F02=13000/6500N,不作考虑,设动摩擦为2500N,
静摩擦为5000N,F01粗加工的铣销负载,F02粗加工的铣销负载
由公式2-1,工作台液压缸的工作推力
快进、快退时外负载F=2500N,启动加速是外负载F=5000N,工作缸的外负载为
表1铣床要求的工作参数
动力部件快进,快退摩擦阻力(N)
动力部件切削负载(N)(Ⅰ/Ⅱ)
快进速度(m/min)
(Ⅰ/Ⅱ)工进速度
(m/min)
快退速度
(m/min)
2500
17778/7778
16
(0.6~6)/(0.5~5)
16
根据工作的设计的需要假设快进和快退的速度相等,同事都为16m/min
表2液压缸在各工作阶段的负载值
工况
液压缸负载F(N)
液压缸驱动力(N)
快进
2500
2778
Ⅰ工进
18500
20556
Ⅱ工进
9500
10556
快退
2500
2778
定位
280
311
夹紧
2200
2444
按照要求,作出系统的工作循环图如下:
图1工作循环图
图2速度循环图
根据上述计算结果各工作阶段所受的外负载,并画出负载循环图。
图3负载循环图
第六章、液压系统原理图设计分析
(1)确定供油方式:
根据设计背景要求,供油方式采用限压式变量泵,变量泵选择用带压力反馈的限压式变量叶片泵。
(2)调速方式的选择:
调速阀调速。
(3)速度换接方式的选择
采用电磁阀的快慢速换接回路,特点是结构简单、调节行程比较方便,但速度换接的平稳性较差。
若要提高系统的换接平稳性,则可改用行程阀切速的速度换接回路。
(4)夹紧回路的选择
用二位四通阀来控制夹紧、松开换向动作时,为了避免工作时突然失电而松开,应该用失电夹紧方式。
考虑到夹紧时间可调节和当进油路压力瞬间下降时仍能保持夹紧力,所以接入节流阀调速和单向阀保压。
在该回路中还装有减压阀,用来调节夹紧力的大小和保持夹紧力的稳定。
图4液压系统原理图
液压系统的工作原理图分析
1、夹紧缸工作:
启动液压泵,4YA得电,三位四通换向阀工作在左位,夹紧缸的无杆腔进油,夹紧缸工作,夹紧缸的力的大小由单向节流阀15来控制。
2、定位缸工作:
4YA得电,三位四通换向阀工作在左位,定位缸的无杆腔进油,定位缸工作,定位缸的工作压力的大小由单向阀14来控制。
3、快速运动:
4YA和2YA得电,液压缸22快速运动
4、工进1(往):
4YA和7YA得电,油液由调速阀18和19经三位四通阀进入液压缸
5、工进1(复):
4YA和6YA得电,油液由调速阀18和19进入三位四通阀的右侧,进入液压缸。
6、工进2(往):
4YA和7YA得电,油液由调速阀18和19经三位四通阀左侧进入液压缸。
7、工进2(复):
4YA和6YA得电,油液由调速阀18和19进入三位四通阀的右侧进入液压缸。
8、快退:
1YA和4YA得电,液压缸工作在左侧。
9、停止:
3YA得电,夹紧缸和定位缸的有杆腔进油,工件松开。
第一节、液压缸参数计算
(1)参考:
《液压传动系统及设计》表5-6。
铣床液压系统的工作压力选为5MPa。
(2)由于要求工作台双向移动速度相等,快进,快退速度相等,故工作液压缸选用单缸双杆式。
夹紧和定位缸均选单缸单杆式。
(3)计算工作液压缸内径D和活塞杆直径d,最大负载为20556N,取背压为0.5Mpa,(查:
《液压传动系统及设计》表5-8)。
试取d/D=0.7。
将数据代入式
3-1
得,根据液压缸内尺寸系列GB2348-1993,液压缸内径圆整为标准系列直径D=110mm,按d/D=0.7,取d=77mm。
(4)计算夹紧缸和定位缸内径D和活塞杆直径d。
按工作要求的夹紧力由一个夹紧缸提供,考虑到夹紧力的稳定,夹紧缸的工作压力应低于进给液压缸的的工作压力,现取夹紧缸的工作压力为2Mpa,回油背压力为0.5Mpa,取液压缸的机械效率为0.9。
取d/D=0.7代入下式
3-2
所以得:
得,按液压缸内尺寸系列GB2348-1993,和活塞杆直径系列GB2348-1993,取夹紧液压缸的D和d分别为50mm及35mm。
取定位缸工作压力为2Mpa,回油背压力为0.5Mpa,取液压缸的机械效率为0.9。
取d/D=0.7代入式3-2,
得:
得,取定位液压缸的D和d分别为16mm及12mm。
(5)按最低工进速度验算液压缸的最小稳定速度,
3-3
A>,是由产品样本查得的最小稳定流量0.05L/min(由本产品查得GE系列调速阀AQF3—E10B的最小稳定流量)。
得A>,调速阀安装在回油路上,液压缸的有效工作面积应选取液压缸有杆腔的实际面积
所以:
A>Amin=1cm2
可见满足要求。
3)计算在各工作阶段液压缸所需要的流量
,
,
。
表3液压缸在各工作阶段的压力,流量和功率
工况
计算公式
负载
回油腔压力(MPa)
进油腔压力(MPa)
输入流量Q()
功率
P(KW)
快进
2500
0.5
1.125
64.056
1.2
Ⅰ工进
18500
0.5
5.12
24.021
2.05
Ⅱ工进
9500
0.5
2.88
20
0.96
快退
2500
0.5
1.125
64.056
1.2
液压缸的进油腔压力,输入流量和功率用图示分别表示如下:
(其中各工作阶段的运动时间为:
快进,工进一,工进二,快退。
)
图5进油腔的压力图
图6输入流量图
图7功率图
第二节、确定液压泵的流量、压力和选择泵的规格
1)泵的工作压力的确定。
由于油管有一定的压降,所以泵的工作压力为
3-4
(公式《液压传动系统及设计》)
式中:
P1——P-t图中的最高工作压力Pa
——系统进油路上的总压力损失
取为0.5Mpa,(初算是,简单系统可取0.2-0.5MPa,复杂的系统可取0.5-1.5MPa,这里取0.5MPa)故=5.12+0.5=5.62Mpa。
是系统的静态压力,考虑到系统在各种工况的过渡阶段出现的动态压力往往超过静态压力。
另外考虑到一定的压力储备量,并确保泵的寿命,因此选泵的额定压力。
选取1.25=1.25x5.62=7.025Mpa。
2)泵的流量确定。
液压泵的最大流量应为,为泄漏系数,一般取为1.1~1.3,现取为=1.1。
(《液压传动系统及设计》参见图5-10)
=64.056x1.1=70.5L/min。
3)选择液压泵的规格。
根据以上计算的=7.025MPa和=70.5MPa3)查阅《机械设计手册》,按照需求选用YBX-D50(V3)限压式变量叶片泵,该泵的基本参数为:
每转排量50ml/min,泵的额定压力为10Mpa,最高的压力10MPa,,最流量为72.5L/min,驱动功率10kW,容积效率:
88%,总效率。
(查阅:
4)与液压泵匹配的电动机的选定。
泵的机械效率为,电机的工况条件下,取机械效率为。
电机所需功率为3-5
快退和快进时,进油腔压力为1.125Mpa,其中=0.5MPa是进油路压力损失,=0.5MPa是压力继电器可靠动作需要的压力差,,推出,;
Ⅰ工进时,电机所需功率,根据公式3-5,其中=0.5MPa是调速阀所需最小压力,=0.5MPa是压力继电器可靠动作需要的压力差,,得,;
由以上计算可知,最大功率出现在Ⅰ工进阶段,Pmax=4663W,则电动机的功率应为Np>4663W。
据此查样本选用Y2-132M-4三相异步电动机,电动机额定功率为5.5KW,额定转速为。
效率为85.5%,额定转矩为2.2N.m
第三节、液压阀,过滤器,油管及油箱的选择
1)液压阀及过滤器的选择
根据液压系统的最高工作压力和通过各个阀类元件和辅助元件的最大流量,可选出这些元件的型号及规格,列表如下:
编号
元件名称
估计通过流量(L/min)
元件型号
规格
1
XU线隙式滤油器
70
2.5MPa
2
油箱
—
—
420L
3
冷却器
—
—
—
4
三相异步电动机
—
Y132S-4
5.5Kw
5
变量叶片油泵
70
YBX-D50(V3)
10MPa
6
溢流阀
7.04
YF-L20B
5-70MPa
7
指针式压力计
—
Y-100
10MPa
8
减压阀
—
JF-L10G
7MPa
9
单向阀
7.04
S-10A0
10L/min
10
背压阀
B-63B
0.5MPa
11
三位四通换向阀
34D-63B
7MPa
12
三位四通换向阀
34D-63B
7MPa
13
蓄能器
—
HXQ-C16D
HXQ-C16D
14
单向顺序阀
4.48
X2F-L10E
3MPa
15
单向顺序阀
2.56
X2F-L10E
3MPa
16
液压缸
4.48
20x18
20x14
17
液压缸
2.56
50x28
50x36
18
调速阀
64.056
Q-H20
32MPa
19
调速阀
64.056
Q-H20
32MPa
20
两位二通换向阀
22D-63B
7MPa
21
三位四通换向阀
34D-63B
7MPa
22
液压缸
64.056
100x70
100x70
23
指针式压力计
—
Y-100
10MPa
24
指针式压力计
—
Y-100
10MPa
25
指针式压力计
—
Y-100
10MPa
26
指针式压力计
—
Y-100
10MPa
27
指针式压力计
—
Y-100
10MPa
28
指针式压力计
—
Y-100
10MPa
2)油管的选择
根据选定的液压阀的连接油口尺寸确定管道尺寸。
由于系统在液压缸工进速度最快时,流量最大,实际最大流量约为:
,则泵的流量为额定流量70,连接液压缸的进出油路油管的直径选择公称通径为20mm。
所以,按产品样本标准JB827-66,JB/Z95-67,选用公称通径为20mm的管件。
3)油箱容积的选择
中压系统的油箱容积一般取液压泵额定流量的5~7倍,《液压系统设计简明手册》表4-1.这里取6倍,即,其中为液压泵每分钟排出压力油的体积。
得,V=420L。
第四节、液压系统的验算
(1)系统压力损失验算
由于系统的具体管路布置尚未清楚,整个回路的压力损失无法估算,仅只有阀类元件对压力损失所造成的影响可以看得出来,供调定压力值时参考。
由于快进时的油液流量比快退时的流量大,所以其压力损失也就比快退时的大。
因此必须计算快进时进油路与回油路的压力损失。
假定液压系统选用L-HL32号液压油,考虑最低工作温度为15℃,由手册查出此时油的运动粘度《液压系统设计简明手册》,油的密度,《液压传动系统