轴承支座铸造工艺设计 全套图纸.docx
《轴承支座铸造工艺设计 全套图纸.docx》由会员分享,可在线阅读,更多相关《轴承支座铸造工艺设计 全套图纸.docx(60页珍藏版)》请在冰豆网上搜索。
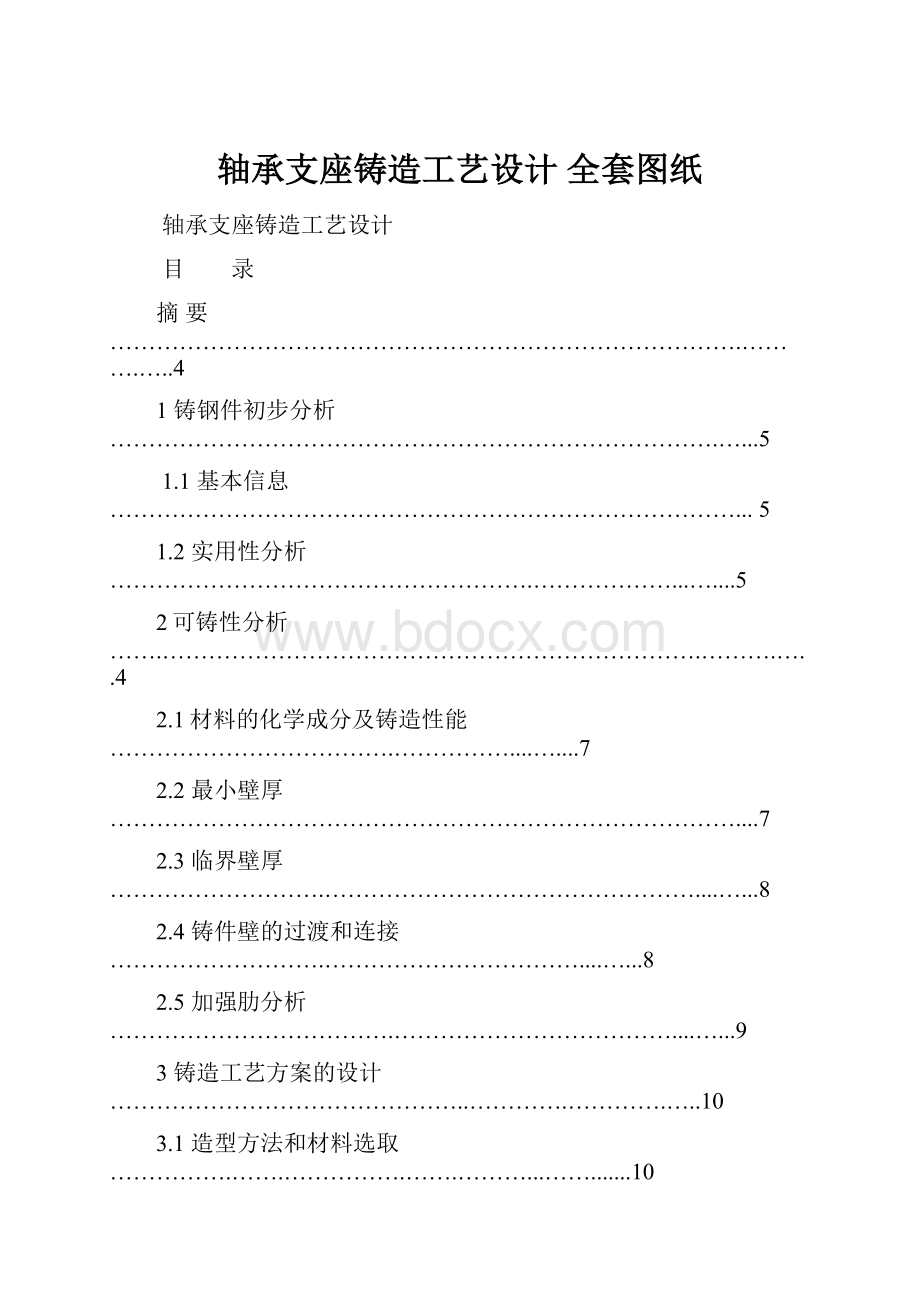
轴承支座铸造工艺设计全套图纸
轴承支座铸造工艺设计
目 录
摘要……………………………………………………………………….……….…..4
1铸钢件初步分析…………………………………………………………………….…...5
1.1基本信息………………………………………………………………………...5
1.2实用性分析……………………………………………….………………...…....5
2可铸性分析…….…………………………………………………………….……….…..4
2.1材料的化学成分及铸造性能……………………………….……………....…....7
2.2最小壁厚………………………………………………………………………....7
2.3临界壁厚……………………….…………………………………………....…...8
2.4铸件壁的过渡和连接……………………….……………………………....…...8
2.5加强肋分析……………………………….………………………………....…...9
3铸造工艺方案的设计………………………………………..………….………….…..10
3.1造型方法和材料选取…………….…….…………….…….………...…….......10
3.1.1呋喃树脂砂成分的选择…….….….…….………….…………......…...10
3.1.2铸造涂料的选择…….…….…….…………………………….…..…....10
3.2铸造工艺参数的确定……………………….…………………………......…...11
3.2.1铸件尺寸公差……………….……………………………………..…...11
3.2.2机械加工余量………………………..………………………..…..…....11
3.2.3铸件收缩率……………………….………………………………....….12
3.2.4起模斜度……………………….………………………………...……..13
3.2.5最小铸出孔和槽………………….………………………………...…..13
3.2.6补充说明……………………………….…………………………...…..13
3.3摆放位置与分型面…………………….…………………………..............…...13
3.3.1摆放位置的确定…………….……………………………………..…...13
3.3.2分型面的确定………………………..………………………..…..…....14
3.4浇注系统设计………………….………………………………...……………..15
3.4.1设计原则………………………….…………………………............….15
3.4.2确定浇注位置……………………………………………….............….16
3.4.3各浇道截面计算……………….…………………………………....….17
3.4.4浇口杯的选择………………….………………………………….........19
3.5冒口和冷铁设计………….……………………………………………….........20
3.5.1冒口的设计………………….…………………………………………..20
3.5.2冷铁的设计………………….……………………………….………….22
4工艺方案优化………………………………………………….…………………….....23
4.1铸件缺陷分析………………….…………………………………………..…...23
4.2缺陷改进………………….…………………………………………...........…...25
5砂芯及芯盒的设计…………………………………………………….…………….…27
5.1制芯方法的确定……………………….…………………………...…………..27
5.2芯头的定位和间隙………………….……………………………...…………..27
5.3芯骨的设计………………….………………………………........................….28
5.4砂芯的排气………………….………………………………...…............……..28
5.5芯盒的设计……………………….…………………………...…….…………..29
6铸造工艺工艺装备设计…………………………………………….………………….30
6.1砂箱的选择与设计……………………….…………………………...…..........30
6.1.1砂箱及其附件的材料………………….……………………...…..........30
6.1.2砂箱各部分的机构和尺寸………………….…………………...…......30
6.2模样的设计……………………….…………………………...…......................36
6.3铸型造型……………………….…………………………...…..........................36
7熔炼和后处理…………………………………………….………………………….….37
7.1铸钢的熔炼……………………….…………………………...…......................37
7.1.1配料………………….……………………...…......................................37
7.1.2熔炼过程的技术要求………………….…………………...…..............37
7.2铸件的清理……………………….…………………………...…......................40
7.2.1铸件的落砂除芯………………….……………………...…..................40
7.2.2浇冒口和毛刺的去除………………….…………………...…..............40
7.2.3铸件的表面清理………………….……………………...…..................40
7.2.4铸件的热处理………………….…………………...…..........................40
7.3气孔缺陷的防治……………………….…………………………...…..............41
8参考文献…………………………………………….………………………………….42
零件图
铸件图
摘要
本工艺方案的设计准则是:
在保证铸件质量的前提下,尽量提高方案的经济性和可实施性。
在设计工艺方案过程中,我们结合铸件的实际情况,并从权威文献查找标准,将理论与实际相结合。
同时,用UG软件进行三维造型,用CAE软件进行模拟分析,在不断的尝试、改进中完善本方案。
设计方案之前我们需要了解零件的功能来判断其重要部位,但是图纸中并没有直接告知我们用途,我们只能通过零件结构特点并在网上查询资料,最终确定该零件为轴承支座。
其重要部位为上部两端半圆筒和下部大平板。
上部两端圆筒用于与其他零件相配合,来放置轴承,是零件的直接受力处,此处应该具有足够的强度;下部大平板上有许多沉头孔,是零件定位和固定的根本。
所以在工艺方案设计中我们要首先保证这两个部位的质量。
以上述分析为基础,我们对铸件生产过程中的“摆放方式”、“分型面”进行分析,在这个过程中发现我无法明显判断出“大平板朝下”、“大平板侧立,L形朝上”两种摆放方式的优劣,所以我们对两种摆放方式做出两组工艺方案,并通过两种方案的最终模拟结果来决定终方案。
在设计浇注系统和补缩系统中,考虑到铸件属于中大型铸钢件,容易产生缺陷。
所以为保证充型过程的平稳和铸件成品的质量,我们采用了开放式浇注系统,确保金属液稳定流动和充型。
同时,使用冒口和冷铁控制铸件自远离冒口的末端区向着冒口方向实现明显的“顺序凝固”。
然后我们使用CAE软件进行网格的剖分,充型、凝固的模拟。
在经历多次的方案优化后,我们最终成功消除铸件中的所有缩孔,并使缩松极少量的残存,使铸件达到合格的标准,最终我们的工艺出品率为80.5%。
关键词:
轴承支座顺序凝固设计和优化
全套图纸加153893706
1铸钢件初步分析
1.1基本信息
零件名称:
轴承支座材质:
ZG310-570
外形尺寸:
1430mm×1160mm×810mm
零件重量:
2600Kg生产规模:
批量生产
技术要求:
(1)锐角倒钝。
(2)铸件应符合JB/T5000.6-1998规定要求。
(3)铸件不允许有裂纹、夹渣、疏松、气孔、砂眼等影响机械性能的外观缺陷。
(4)工艺方法采用砂箱造型。
根据所给图纸,使用UG软件对零件进行造型得其三维零件图,如图1.1所示:
图1.1零件的三维造型
1.2实用性分析
零件整体上可分为三个部分:
第一部分为固定轴承和轴的圆筒,第二部分为下平板,第三部分为连接和辅助部分,包括四个肋板以及连接圆筒和下平板的部分。
其中第一部分为固定轴承和轴的圆筒,其内部壁厚为120mm,两端(只有一半圆筒部分)壁厚为95mm,最小内直径为360mm。
圆筒中间部分内表面的粗糙度为Ra6.3,且内部空心半径圆柱比两端大,可在内部放润滑物质。
两端的半圆筒内表面粗糙度为Ra1.6,而且平行度要求为为0.02,半圆筒侧视图比标准半圆少2mm便于同其他零件进行组合形成剖分式的轴承支座,同时可形成一个26mm的凹槽,可用于放置密封装置,为防止与轴承等零件接触配合时出现误差,不能有缩松缩孔及其它缺陷。
第二部分为下平板,由两个平面组成,一个为水平平面,其上分布着16个沉头螺钉孔和2个定位销孔,用于竖直方向的固定和定位;另一个为竖直平面,其上分布5个螺栓孔,用于水平方向上的固定和定位,主要受零件工作时来自震动的横向力和分布径向力。
结合零件功能,下平板承受来自圆筒的力以及起到整体固定作用,所以要做成大平面,用于保证安装时的平整性,工作时的稳定性和承受更大的力。
下平板在工作时用螺栓与其它部件连接,所以这部分是比较重要的部分。
除此,平板底部有正方形的凹陷,这是为了在加工平板底部时,减少加工余量而设置的。
第三部分为连接和辅助部分,包括四个肋板以及连接圆筒和下平板的部分。
四个肋板即加强部分,以相同的间距均匀分布在圆筒下方,连接圆筒和下平板,其主要作用是支撑和加强圆筒的强度。
肋板的形状为横截面上小下大的平薄板件,按等强度梁的思想设计,一方面符合受力情况下的强度,另一方面节省材料,节省材料又保证强度要求,达到事半功倍的效果。
连接圆筒和下平板的部分本身厚度最小为30mm,加上筒壁厚以及下平板厚,达到225mm,是该零件中壁厚最大的部分。
2可铸性分析
铸件的生产,不仅需要采用合理的、先进的铸造工艺和设备,而且还要求零件的设计结构适合铸造生产的要求,因为合理的零件结构可以消除很多铸造缺陷。
为保证获得优质铸件,对零件的要求应考虑以下几个方面:
2.1零件材质的化学成分及铸造性能
本铸件材质为ZG310-570,属于铸造中碳钢,查标准JB/T5000.6-1998可得其化学成分和力学性能如表1.1和表1.2所示。
表1.1ZG310-570化学成分元素的最高含量(%)
C
Si
Mn
S
P
残余元素
Ni
Cr
Cu
Mo
V
0.50
0.50
0.90
0.04
0.04
0.30
0.35
0.30
0.20
0.05
表1.2ZG310-570力学性能指标
密度
(g/cm3)
弹性模量
(GPa)
屈服强度
(MPa)
抗拉强度
(MPa)
7.85
210
≥310
≥570
铸钢的铸造能较差,流动性较低,容易形成冷隔;氧化和吸气性也较大,容易形成夹渣和气孔;体收缩和线收缩都偏大,容易形成缩孔、缩松、热裂和冷裂;熔点较高,易形成粘砂。
ZG310-570其中主要合金素如Mn、Si、Ni等可适量提高钢水的流动性和提供良好的脱氧效果,但同时也会增加铸钢件的热裂及缩孔、缩松的倾向。
对于本零件,没有很薄的壁厚,不易出现冷隔和浇不足的现象。
但是,考虑到加工面上不易加冒口,来控制缩松和缩孔,以及在圆筒和平板的连接处存在很大热节圆,因此在后续的工艺设计方案中解决缩松和缩孔的问题将是主要的任务。
为此,方案将会将冒口与浇注系统、冷铁等相配合使用,是铸件在较大的温度梯度下,自远离冒口的末端区向着冒口方向实现明显的顺序凝固,同时采用退让性,透气性好的型砂来造型和造芯。
2.2铸件的最小壁厚
从保证合金液充型能力来看,在设计壁厚是,要考虑合金液的流动性和铸件的轮廓尺寸,在一定的铸造条件下,铸造合金能充满铸型的最小厚度称为该铸造合金的最小壁厚。
为了避免铸件的浇不到和冷隔等缺陷,应使铸件的设计壁厚不小于最小壁厚。
在将零件图转化成铸件图后可的其最大轮廓尺寸为1470mm,其壁厚最小处为50mm。
根据表2.1可知符合的最小壁厚为16~18mm,可知该零件满足铸件最小壁厚的要求。
表2.1砂型铸造铸钢件的最小壁厚(单位:
mm)
铸钢种类
当铸件最大轮廓尺寸为下列值时
〈200
200~400
400~800
800~1250
1250~2000
碳钢
8
9
11
14
16~18
2.3铸件的临界壁厚
在铸件结构设计时,为了充分发挥金属的潜力,节约金属,必须考虑铸造合金的力学性能对铸件壁厚敏感性。
壁厚铸件易产生缩松缩孔晶粒粗大偏析和硬度低等缺点,从而使铸件的力学性能下降。
从这方面考虑,各种铸造合金都存在一个临界壁厚,铸件的壁厚超过临界壁厚以后。
铸件的力学性能并不能按比例地随着铸件厚度的增加而增加,而是显著地下降。
因此,铸件的结构设计应科学地选择壁厚以节约金属和减轻铸件的质量。
根据文献1可知砂型铸造的各种铸造合金铸件的临界壁厚可按其最小壁厚的三倍来考虑。
则零件的临界壁厚为150mm,但在连接圆筒和下平板的部分本身厚度最小为30mm,加上筒壁厚以及下平板厚,达到225mm,是该零件中壁厚最大的部分。
为防止热结过大,出现缩松缩孔等缺陷,导致该处的力学性能下降,该部位要尽量加冷铁,以达到减小冷却时间的目的,改善组织。
2.4铸件壁的过渡和连接
一般情况下,铸件壁的断面尺寸不可能完全相同,同时,铸壁间有类型各异的接头。
在接头处,凝固速度慢,容易产生应力集中、裂纹、变形、缩孔、缩松等缺陷。
因此,为保证结构合理性急铸造工艺要求,各个壁或面的过渡处要尽量做到平缓过渡。
对于本铸件存在K形连接接头且分布不是太合理,但考虑铸件的功能和要求,这样也是无法避免。
只能通过后期的铸造工艺方案设计来减少缺陷。
缩孔
a)不合理b)合理图2.1铸件剖切图
2.5加强肋分析
为了增强铸件的力学性能,减轻铸件重量,消除铸件的缩孔和防止铸件产生裂纹、变形、夹砂等缺陷,在铸件结构设计中大量采用肋。
在本铸件中因为铸件下方存在大平面的结构,在浇注时因金属液的烘烤,大平面处的造型易“起皮”而产生夹砂缺陷。
增强肋后提高了铸件质量和载荷性能,使平板处不易“起皮”,也就不易产生夹砂缺陷,且有利于合金液充满该平面。
同时,这些肋的设置在一定程度上减小了该处的热节。
3铸造工艺方案的设计
3.1造型方法和材料的选取。
零件的外形尺寸为1430mm×1160mm×810mm,重量达2600Kg,属于大型零件,大型零件的铸造方式不易采用机械一体化流水生产,可采用连续氏混砂机填砂并配合人工起模进行造型。
从使用黏结剂造型方法分类上讲,本方案采用自硬树脂砂造型,采用自硬树脂做黏结剂。
将树脂、固化剂和原砂混合,砂型自行硬化,起模后获得砂型。
其主要优点在于:
树脂砂具有较好的流动性、易紧实,且树脂砂的刚度高,能获得高精度、表面光洁的铸件。
同时,树脂砂造型中不用对砂型进行烘干处理,缩短了生产周期,节约了能源。
3.1.1自硬呋喃树脂砂原材料成分的选择
铸件材质为铸钢,易选用酚醛树脂做黏合剂,但是其价格较高,经济性不强,特别是本方案铸型和砂芯较大,树脂使用量较大,因此我们选用性价比更高的呋喃树脂。
呋喃树脂适用于小批量生产的铸钢件,其主要优点如下:
常温下强度高,树脂加入量少,耗砂量少,粘度小便于混砂且硬透性好。
根据文献2得树脂自硬砂的配比方案如表3.1所示:
表3.1树脂自硬砂配方
配方(%)
新砂
旧砂
树脂(占砂量)
固化剂(占树脂量)
10
90
0.8-1.5
25-50
结合本铸件的特征,查询文献2的树脂自硬砂对原砂和固化剂的要求如下表:
表3.2树脂自硬砂对原砂的要求指标(质量分数%)
SiO2
粒度组别
含泥量
含水量
酸耗值(ml)
灼减量
≥96
40/70
≤0.2
≤0.1-0.2
≤5
≤0.5
固化剂:
固化剂影响树脂砂的硬化速度和终强度,对于呋喃树脂砂多用磺酸类固化剂。
3.1.2铸造涂料的选择
液态钢温度较高,当铸型和液态金属接触时,会发生铸型膨胀、收缩及树脂的燃烧而产生气体,树脂分解会降低铸型强度和耐热性,有因型腔内饰非氧化性气氛,树脂燃烧比较缓慢,其结果是铸型膨胀两增大,而且膨胀时间长,扩大了砂粒之间的孔隙,特别是浇注大型厚壁铸件时,由于铸型表面长期高温作用下并受到较高金属液压力,所以从裂纹处侵入的金属也想铸型深处渗透,最后导致严重机械渗透粘砂缺陷。
树脂砂型还容易产生气孔缺陷,这是因为树脂中的碳氢化合物和水在高温热作用下产生大量气体,如果处理不当,易使铸件产生产生大量气体。
为防止上述缺陷,提高铸型表面强度和耐火度,减少砂粒之间的间隙,刷涂料是极其有效的措施。
涂料一般由耐火材料、载体、悬浮剂、粘结剂四个部分组成。
本方案采用醇基快干涂料。
将涂料在碾压机碾压4h左右,将碾压好的涂料倒入搅拌机中配制成密度1.6g/cm3~1.8g/cm3搅拌均匀后即可使用。
涂料的具体配比如表3.3所示:
表3.3醇基快干涂料配制工艺(%)
刚玉粉
细粉
粘土
有机土
漆液
硅胶
酒精
68.0
7.4
0.75
2.8
7.6
4.0
适量
3.2铸造工艺参数的确定
3.2.1铸件尺寸公差
铸件尺寸公差是指铸件公称尺寸的两个允许极限尺寸尺差。
在这两个允许极限尺寸之内,铸件可满足加工、装配和使用的要求。
根据JB/T5000.6-1998的规定铸钢件公差等级按CT13~CT15,公差等级按毛胚铸件最大尺寸选取,属于此铸件的所有较小尺寸的公差等级与该铸件最大尺寸的公差等级相同。
本方案取公差等级为CT14,查标准表6得公差值为23mm。
3.2.2机械加工余量
机械加工余量是为保证铸件加工面尺寸和零件精度,在铸件工艺设计时预先增加的而在机械加工时去除的金属层厚度。
铸件的某一部分在铸态下的最大尺寸应不超过成品尺寸与要求的加工余量及铸造总公差之和。
因此可知铸件机械加工余量同
所要求的加工余量等级和尺寸公差有关。
根据JB/T5000.6-1998规定可得加工余量与铸件尺寸的关系,且加工余量按最终加工后成品铸件的最大外形尺寸选取,属于此铸件的所有较小尺寸的加工余量与最大外形尺寸加工余量相同。
可知铸件最大外形尺寸1430mm,查标准JB/T5000.6-1998表7可知,对于非顶面加工余量为14mm对于顶面加工余量为18mm。
再根据表3.4和结合铸件结构得各处机械加工余量。
表3.4铸件尺寸与配套的尺寸公差(单位:
mm)
尺寸
尺寸公差(CT14)
〉63~100
11
〉400~630
18
〉1000~1600
23
2
3
4
1
图3.1加工面示意图
不同情况下机械加工余量计算方式不同,根据加工面所在位置采用不同公式的如表3.4结果。
表3.4各面加工余量计算结果(单位:
mm)
加工面
所属类型
计算公式
加工余量
1
铸件侧面
δ=RAM+CT/2
25.5
2
圆弧面
δ=-2RAM-CT/2
37
3
铸件底部
δ=RAM+CT/2
23.5
4
底部侧面
δ=RAM+CT/2
23.5
3.2.3铸件收缩率
铸件收缩率有又称铸件线性收缩率或铸造收缩率,以模样与铸件的长度差除以模样长度的百分比表示:
ε=[(L1-L2)/L1]×100%
式中:
ε为铸件收缩率,L1是模样长度,L2是铸件长度。
铸件收缩率是是受各种因素影响后铸件的实际收缩率,不仅与铸造金属的收缩率和线收缩起始温度有关,还与铸件结构、铸型种类、浇冒口系统结构、铸型和型芯的退让性等有关。
对于本方案,因为铸型材料选用自硬砂,其退让性较差,对铸件的收缩阻力比较大,且阻碍收缩的砂芯面积较大。
再根据文献1图3-114,确定铸件收缩率为2.0%。
3.2.4起模斜度
当铸件本身没有足够的结构斜度,应在铸件设计或铸造工艺设计时给出铸件的起模斜度,以保证铸型的起模。
起模斜度可采取增加铸件壁厚、增减铸件壁厚或减少铸件壁厚的方式来形成。
在铸件上加起模斜度,原则上不超过铸件的壁厚公差要求。
在制造模样和砂芯是要将起模斜度考虑在内,起模斜度斜度与尺寸以及造模方法有关。
本方案采用木模样,其高度在1000~1600mm的范围内,查文献1可以得铸件的起模斜度为0°25′,a=11.6mm。
但是由于本方案的砂芯雨铸型相接触,因此砂芯外部域铸型相接触表面的斜度一致,考虑到铸件的起模斜度太小,不利于合箱和下芯。
因此参考下文芯头与间隙章节,且方案型芯高且大,设定铸件的起模斜度为3°。
3.2.5最小铸出孔和槽
机械零件上往往有很多孔、槽和台阶,一般应尽可能在铸造时铸出。
这样既可节约金属,减少机械加工的工作量、降低成本,有可是铸件壁厚比较均匀,减少形成缩孔、缩松等铸造缺陷的倾向。
但是,当铸件上的孔、槽尺寸太小,而铸件的壁厚又较厚和金属压力较高时,反而会使铸件产生粘砂,造成清理和机械加工困难。
所以对铸件要考虑最小铸出孔。
根据文献1得铸钢件最小铸出孔标准如表3.5所示。
对于本铸件,孔深不过100mm,直径最大为58mm,小于表中的80mm,所以零件上的孔均为不可铸出孔。
表3.5普通碳钢铸件最小铸出孔(单位:
mm)
孔深
H
孔壁厚度δ
≤25
26~50
51~75
76~100
60
60
70
80
3.2.6补充说明
(1)本方案采用树脂砂造型,铸型强度高,表面稳定性好,无需烘干,减小铸型变形的可能,所以不考虑分型负数和非加工壁厚负余量。
(2)圆筒外端半圆处的凹槽为加工面,其宽度相对于整体铸件较小,如果铸出不利于型芯的制作和配合,所以不铸出,后期机械加工做出。
(3)铸件下部的正方形凹陷与四周只有5mm高度差,无法铸出,但其四周为加工面,加上加工余量后高度差达28.5mm。
且考虑到凹陷本身是为了减少加工面,所以本方案铸出。
(4)底部平板与肋板接触面处,为便于起模和制芯,肋板倾斜面延伸,直接与平板接触。
最终的铸件图如下:
图3.2铸件三维造型
3.3摆放位置与分型面
3.3.1摆放位置的确定
根据图纸要求,如图3.1图所示,铸件的重要工作面和加工面为大平板内表面、圆筒端