硫铵.docx
《硫铵.docx》由会员分享,可在线阅读,更多相关《硫铵.docx(17页珍藏版)》请在冰豆网上搜索。
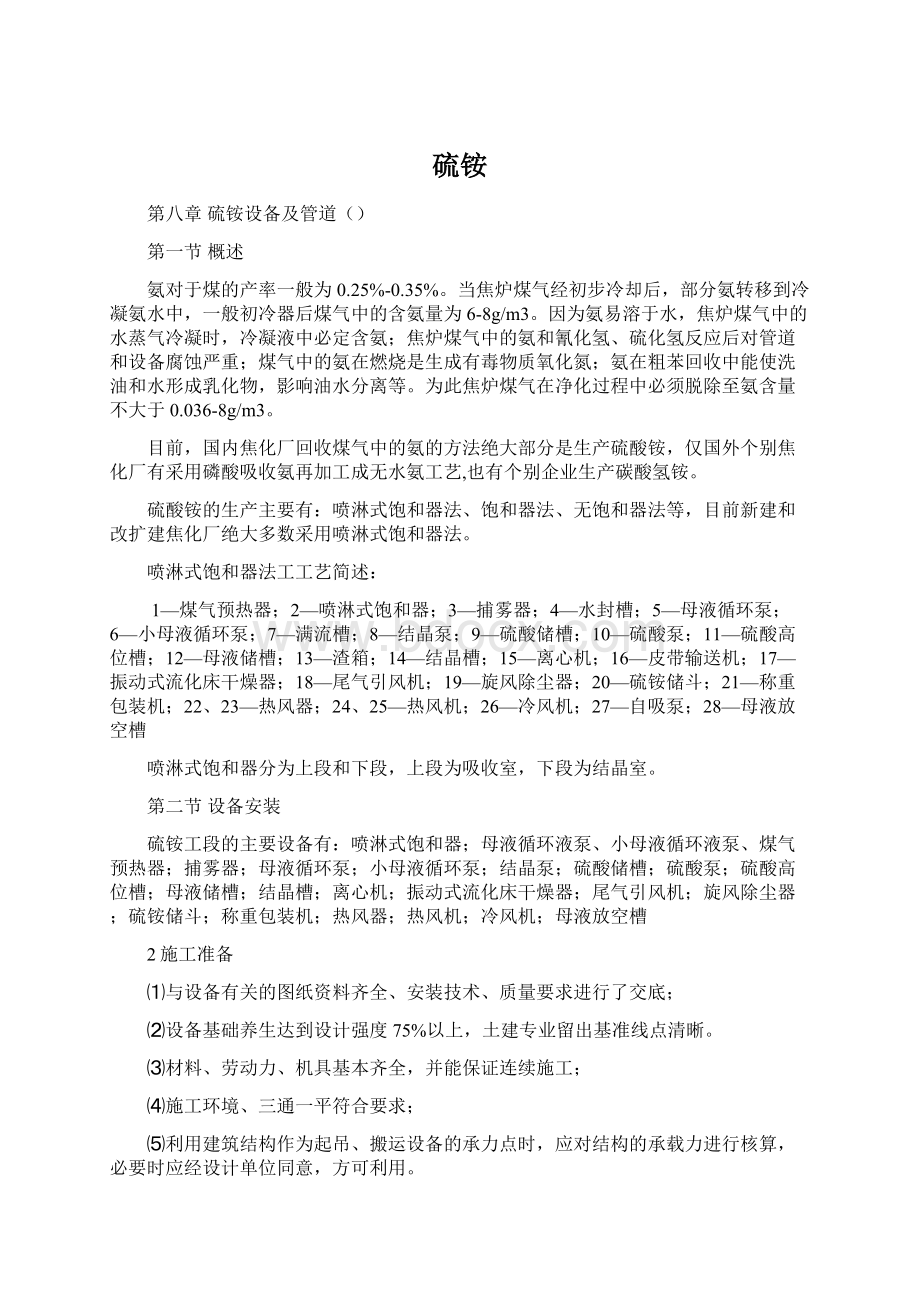
硫铵
第八章硫铵设备及管道()
第一节概述
氨对于煤的产率一般为0.25%-0.35%。
当焦炉煤气经初步冷却后,部分氨转移到冷凝氨水中,一般初冷器后煤气中的含氨量为6-8g/m3。
因为氨易溶于水,焦炉煤气中的水蒸气冷凝时,冷凝液中必定含氨;焦炉煤气中的氨和氰化氢、硫化氢反应后对管道和设备腐蚀严重;煤气中的氨在燃烧是生成有毒物质氧化氮;氨在粗苯回收中能使洗油和水形成乳化物,影响油水分离等。
为此焦炉煤气在净化过程中必须脱除至氨含量不大于0.036-8g/m3。
目前,国内焦化厂回收煤气中的氨的方法绝大部分是生产硫酸铵,仅国外个别焦化厂有采用磷酸吸收氨再加工成无水氨工艺,也有个别企业生产碳酸氢铵。
硫酸铵的生产主要有:
喷淋式饱和器法、饱和器法、无饱和器法等,目前新建和改扩建焦化厂绝大多数采用喷淋式饱和器法。
喷淋式饱和器法工工艺简述:
1—煤气预热器;2—喷淋式饱和器;3—捕雾器;4—水封槽;5—母液循环泵;6—小母液循环泵;7—满流槽;8—结晶泵;9—硫酸储槽;10—硫酸泵;11—硫酸高位槽;12—母液储槽;13—渣箱;14—结晶槽;15—离心机;16—皮带输送机;17—振动式流化床干燥器;18—尾气引风机;19—旋风除尘器;20—硫铵储斗;21—称重包装机;22、23—热风器;24、25—热风机;26—冷风机;27—自吸泵;28—母液放空槽
喷淋式饱和器分为上段和下段,上段为吸收室,下段为结晶室。
第二节设备安装
硫铵工段的主要设备有:
喷淋式饱和器;母液循环液泵、小母液循环液泵、煤气预热器;捕雾器;母液循环泵;小母液循环泵;结晶泵;硫酸储槽;硫酸泵;硫酸高位槽;母液储槽;结晶槽;离心机;振动式流化床干燥器;尾气引风机;旋风除尘器;硫铵储斗;称重包装机;热风器;热风机;冷风机;母液放空槽
2施工准备
⑴与设备有关的图纸资料齐全、安装技术、质量要求进行了交底;
⑵设备基础养生达到设计强度75%以上,土建专业留出基准线点清晰。
⑶材料、劳动力、机具基本齐全,并能保证连续施工;
⑷施工环境、三通一平符合要求;
⑸利用建筑结构作为起吊、搬运设备的承力点时,应对结构的承载力进行核算,必要时应经设计单位同意,方可利用。
5设备安装
5.1施工工艺流程
开箱检查→基础验收及划线→设备就位→初找水平→地脚螺栓灌浆→精平→抹面→单机试运
5.2开箱检查
按图纸或设备装箱单对设备及所带附件进行清点,检查数量是否齐全,规格是否符合设计要求,随机文件合格证明书是否齐全。
并及时填写《设备开箱验收记录》。
5.3基础验收及处理
设备基础应符合施工及验收规范中基础验收规定;对检查不合格的,应及时进行处理或修复工作,及时填写《基础复检记录》。
基础验收合格后,根据选定的安装中心线进行划线。
5.4设备的就位与找正、找平
整体泵安装时,吊装点应选在机座上或泵体下部,绝对不允许吊索挂在设备轴或轴承上,避免造成轴弯曲。
设备的找正:
纵向中心线是以设备轴中心线作为基准(可采用在设备体两端吊垂线找正),横向中心线以进出口法兰中心线等作为定位基准找正。
设备的找平:
采用三点调平法,在机座一端中心部位和另一端地脚螺栓两侧放置相同厚度的临时垫铁,然后在设备体加工面上用水平仪测量,通过调整三组临时垫铁高度,使设备体达到水平(初平),复查中心位置之后,即可进行地脚螺栓的灌浆,冬季施工要有相应的防冻,速凝等措施,灌浆用水泥砂浆标号应比基础或地墙砼标号高一级。
放置正式垫铁,拆除临时垫铁,通过正式垫铁中的斜垫铁,调整泵体的精平(测量方法同初平)。
设备找正完毕后,将垫铁组点焊牢固,二次灌浆。
联轴器连接时,两半联轴器的径向位移,端面间隙,轴线倾斜,均应符合规定。
每一组正式垫铁一般不超过五块。
整体安装的泵,纵向水平偏差不应大于千分之0.10,横向水平偏差不应大于千分之0.20。
解体安装的泵纵向和横向安装水平偏差均不应大于千分之0.5。
其他设备安装时按照技术文件要求对设备进行找平找正。
喷淋式饱和器一般为工厂制作现场安装,根据现场情况,制定运输吊装方案,选择吊车、索具、确定吊车站位。
一般饱和器制造时已经焊好吊耳或吊点。
运输和吊装时,要对运输道路、吊装场地进行勘察,对施工人员进行技术交底,使施工人员熟悉吊装方法、步骤和安全注意事项。
振动式流化床干燥器等室内设备安装要在厂房封闭时选择合适的部位预留吊装孔洞。
5.5设备的试运转
试运前的检查:
电动机转向应与设备转向相符,且电动机安装、试运合格。
固定连接部位应无松动。
各润滑部件加油润滑剂的规格和数量应符合设备技术文件规定;有润滑要求的部位应按规定进行预润滑。
各指示仪表、安全保护装置及电控装置均应灵敏、准确、可靠。
盘车灵活,无异常现象。
检查管路系统及各进出口阀门位置应正确。
试运:
启动设备达到正常状态时,使其在工作状态下运行。
运行时间不小于4小时或根据规范及技术文件要求进行,填写《设备试运转记录》,记录试运转结果。
第三节管道安装
本工段的管道按介质分有:
煤气管道、浓硫酸管、母液管、蒸汽管、水管道、氮气管、尾气除尘管等;按材质分有316L不锈钢管、304不锈钢管、碳钢管。
本工段的硫铵母液管道目前大部分采用316L不锈钢管道,该材质管道耐酸性较好,使用寿命较长。
但是母液中游离酸浓度在操作过程中超标较大时,焊缝和热影响区易出现腐蚀,由于操作过程中经常出现腐蚀造成泄漏。
目前也有采用钢丝网骨架聚乙烯复合管的,在耐腐蚀方面效果较好。
1施工准备
1.1到货的配管材料满足施工要求,施工所需机具、工具、仪器及消耗材料等配备齐全。
1.2与管道有关的土建工程已经检验合格,满足安装要求,并已办理交接手续。
1.3与管道连接的设备找正合格,固定完毕。
1.4焊接工艺规程已经审定,焊接人员已经过培训并经考试合格。
1.5技术人员、检验人员及施工人员应认真熟悉图纸和有关规范、标准、设计要求。
1.6对管道组成件及管道支承件进行检验,应具有备质量证明书。
1.7管道加工、预制场地满足要求。
已制定相应的安全应急预案。
2.管道组成件及管道支承件的检验
2.1一般规定
2.1.1管道元件必须具有制造厂的质量证明文件,并应符合有关国家现行标准和设计文件的规定。
2.1.2管道元件在使用前应按国家现行标准和设计文件的规定核对其材质、规格、型号、数量和标识,并进行外观质量和几何尺寸检查验收,其结果应符合相应产品标准的规定。
表面应无裂纹、缩孔、夹渣、折迭、重皮等缺陷,表面不得有超过壁厚负偏差的锈蚀和凹陷。
螺纹密封面应良好,精度及光洁度达到设计要求。
材料标识应清晰完整,压力管道元件上应标有TS标志。
检查不合格的管道元件不得使用,并应作好标识和隔离。
2.1.3管道元件在施工过程中应妥善保管,不得混淆或损坏,其标记应明显清晰。
材质为不锈钢的管道元件,在运输和储存期间不得与碳素钢接触。
不锈钢管道在存放和施工为防止混淆和用错,必须对管材进货后及时对管材进行标示,一般采用油漆或记号笔做通长标示。
2.1.4对管道元件的检查验收结果,应按规定填写“管道元件检查记录”
2.2阀门的检验
2.2.1阀门安装前应进行外观质量检查,阀体应完好,开启机构应灵活、阀杆应无歪斜、变形、卡涩现象及标牌齐全。
应检查填料,其压盖螺栓应留有调节裕量。
2.2.2用于管道的阀门应按设计文件和相关标准规定进行壳体压力试验和密封试验,不合格者不得使用。
2.2.3阀门的壳体试验压力应为其公称压力的1.5倍,密封试验宜以公称压力进行,密封试验不合格的阀门可解体检验,并重新试验。
2.2.4具有上密封结构的阀门,应对上密封进行试验,试验压力为公称压力的1.1倍。
试验时应关闭上密封面,并应松开填料压盖。
2.2.5阀门液体压力试验和上密封试验应以洁净水为介质。
不锈钢阀门液体压力试验时,水中的氯离子含量不得超过50×10-6mg/l(50ppm)。
当有特殊要求时,试验介质应符合设计文件的规定。
试验合格后应立即将水渍清除干净。
2.2.6阀门进行各项压力试验时,试验时间不得少于5min。
试验时的环境温度不得低于5℃,当低于5℃时,应采取防冻措施。
2.2.7公称压力小于1.0MPa,公称尺寸大于或等于600mm的闸阀,密封性试验可用色印等方法对闸板密封面进行检查,接合面应连续,可不单独进行壳体压力试验和闸板密封试验。
壳体压力试验宜在系统试压时按管道系统的试验压力进行试压。
2.2.8试验合格的阀门,应及时排尽内部积水,并应吹干。
除需要脱脂的阀门外,密封面与阀杆上应涂防锈油,应关闭阀门,封闭出入口,并应做出明显的标记。
2.2.9应填写“阀门试验记录”。
2.2.10安全阀应按《安全阀安全技术监察规程》TSGZF001和设计文件的规定进行整定压力调整和密封试验。
当有特殊要求时,还应进行其他性能试验。
安全阀校验应做好记录、铅封,并应出具校验报告。
2.2.11对阀门的传动装置和操作机构应进行清洗检验,更换油脂,并检查其动作是否灵活可靠。
2.2.12合金钢阀门应逐个对壳体进行光谱分析,复查材质。
对合金钢阀门内件的材质进行抽查,每批抽查数量不应少于1个。
2.3其它管道元件的检验
2.3.1弯头、异径管、三通、管帽、凸台、活接头、法兰、盲板、膨胀节、补偿器及紧固件等应对其材质及尺寸进行检查,尺寸偏差应符合技术条件规定。
2.3.2螺栓及螺母的螺纹应完整,无伤痕、毛刺等缺陷。
螺栓与螺母配合应良好,无松动或卡涩现象。
2.3.4法兰密封面应平整光洁,不得有毛刺及径向沟槽。
螺纹法兰部分应完整、无损伤。
凹凸面应能自然嵌合,凸面的高度不得低于凹槽的深度。
2.3.5垫片的检验
(1)包金属及缠绕式垫片不得有径向划痕、松散、翘曲等缺陷。
(2)石棉橡胶、橡胶、塑料等非金属垫片应质地柔韧,无老化变质或分层现象。
表面不得有折损、皱纹等缺陷。
(3)补偿装置,其材质、规格、型号等应符合设计文件规定,其它技术要求应符合下列规定:
1)波纹膨胀节管口的周长允许偏差:
当公称直径大于1000mm时,应为±6mm,当公称直径小于或等于1000mm时,应为±5mm。
2)填料式补偿器的插管与套管的轴向装配间隙应符合实际文件规定,且不应小于20mm,插管上应有伸缩距离的标志,并能自由伸缩。
3.管道预制
3.1一般规定
3.1.1管道预制要在已设置的管道加工厂内或现场加工预制平台上进行。
3.1.2管道预制应按管道轴测图规定的规格、材质选配管道组成件,并应按轴测图标明管线号、焊缝号。
若设计未提供管道轴测图,则应在现场补充绘制。
3.1.3一般情况下,除敷设在管廊架上的管线或DN50以下的普通碳钢管道外,均匀预制。
3.1.4预制前需到现场实测,确保预制好后能适合运输和安装。
3.1.5预制管线上的所有仪表一次部件应在预制时按图施工完毕。
3.1.6预制管线的长度应留有适当的余量,具体余量由工程技术人员和现场施工人员确定。
预制管线应留有适当的活口,以利于安装时调节。
3.1.7预制管线应具有足够的刚性,必要时可进行加固。
3.1.8预制完毕的管段,应将内部清理干净,及时封闭管口,及时编号。
3.1.9预制管段加工尺寸偏差应符合表3.1.9规定。
表3.1.9预制管段加工尺寸允许偏差(mm)
项目
允许偏差
自由管段
封闭管段
长度
±10
±1.5
法兰面与管子中心垂直度
DN<100
0.5
0.5
100≤DN≤300
1.0
1.0
DN>300
2.0
2.0
法兰螺栓孔对称水平度
±1.6
±1.6
3.2管子切割与加工
3.2.1切割管子时,原则上采用切管机或砂轮机,切割不锈钢管时,应采用不锈钢专用砂轮片。
3.2.2对于大口径管,应按以下办法切割:
(1)碳钢采用手工、自动或半自动火焰切