线切割详细的加工过程穿丝缠丝等.docx
《线切割详细的加工过程穿丝缠丝等.docx》由会员分享,可在线阅读,更多相关《线切割详细的加工过程穿丝缠丝等.docx(23页珍藏版)》请在冰豆网上搜索。
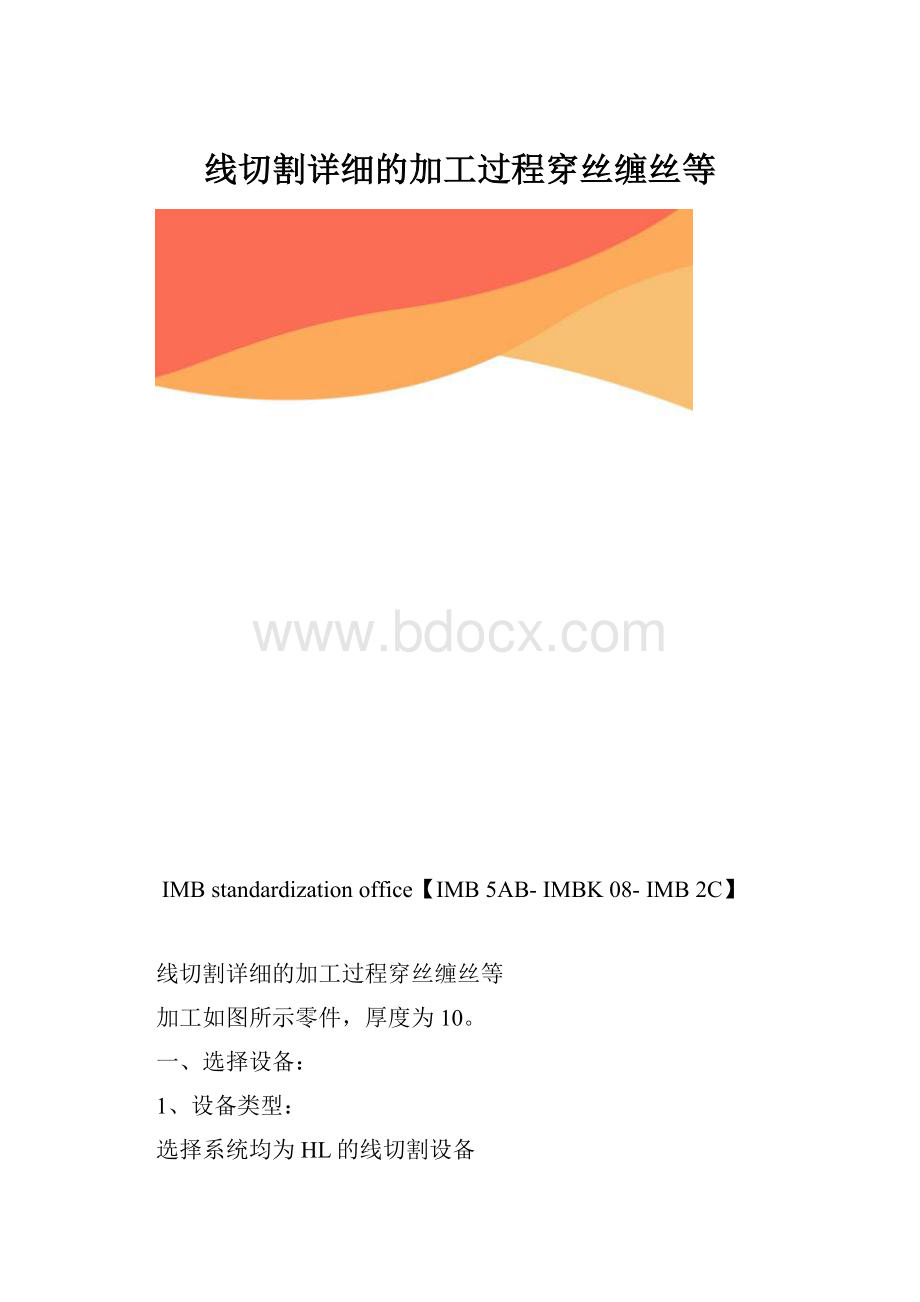
线切割详细的加工过程穿丝缠丝等
IMBstandardizationoffice【IMB5AB-IMBK08-IMB2C】
线切割详细的加工过程穿丝缠丝等
加工如图所示零件,厚度为10。
一、选择设备:
1、设备类型:
选择系统均为HL的线切割设备
2、设备加工范围
工件尺寸为长180宽170
所以选择设备的加工范围需大于180×170mm,设备需要标识最大加工范围等,如下图所示
本例的设备型号为DK7750,最大加工范围为630×500mm。
最大厚度为400
二、划线
1、按如图所示放置工件
2、将高度尺尺寸调整至45与120,在工件上画出如图所示的蓝色线条。
3、将工件旋转90度。
4、将高度尺尺寸分别调整为50及128,在工件上画出如图所示的红色线条。
5、校核穿丝孔划线位置是否正确
5、打样冲眼
冲眼目的:
钻孔下钻定位
要求:
冲点清楚,大小适当
扬冲
三、加工穿丝孔
采用直径为6的钻头钻孔
钻头
四、开机
1、开启控制柜开关
先按控制柜上面的绿色按钮,然后按机箱上的按钮。
控制柜开机开关机箱开关
2、开启机床总控开关
右旋拉开机床总控开关。
机床总控开关
四缠丝
缠丝的过程是将电极丝从丝盘绕到快走丝线切割机床储丝筒上的过程。
1、缠丝以前,要先移开左、右行程开关。
2、用摇把将丝筒逆时针旋转至左侧极限位置。
(将其移到行程左端或右端极限位置目的是将电极丝上满,如果不需要上满,则需与极限位置有一段距离)。
3、将丝盘1放置于缠丝架上,将丝头从丝筒下方穿过,从丝筒上方传出,依次通过2、3、4等导轮及档丝棒(需要从档丝棒里穿过),并注意需要与导电块接触,丝头固定在储丝筒左侧紧固螺钉处。
4、用左手扶住丝盘,右手用摇把顺时针旋转储丝筒,当缠丝宽度达到8mm左右时暂时停止缠丝。
5、调整左侧行程开关。
松开左侧限位块上的紧固螺钉,移动限位块至接近左侧行程开关的中心位置后固定限位块。
6、继续缠丝,缠丝至右侧紧固螺钉30mm左右处停止缠丝,将电极丝剪断,丝头固定在储丝筒右侧紧固螺钉处。
7、调整右侧行程开关。
将丝筒逆时针旋转8mm左右处,松开右侧限位块上的紧固螺钉,移动限位块至接近右侧行程开关的中心位置后固定限位块。
四紧丝
新装上去的电极丝,要经过紧丝操作,才能投入工作。
1、打开机床运丝开关,丝筒向右运行,运行至左侧换向位置,运丝停。
2、手持紧丝轮靠在电极丝上,加适当张力。
继续运丝,运行至右侧换向位置时,运丝停。
3、用摇把顺时针向右手动运丝8mm左右至右侧紧定螺钉处,紧丝轮移开,松开紧定螺钉,将丝头收紧后重新装回储丝筒右侧紧定螺钉处。
4、电极丝运行平稳,松紧适度时结束紧丝。
五穿丝操作
1、自动运丝至右侧极限位置后停止运丝,手动顺时针旋转丝筒至右侧紧定螺钉处,松开丝筒右侧丝头紧定螺钉,拉动电极丝头,从丝筒下方依次通过4、3、2导轮及档丝棒(需要从档丝棒里穿过),并注意需要与导电块接触,丝头从丝筒上绕过固定在储丝筒右侧紧固螺钉处。
2、开机工作前,手动摇把逆时针旋转丝筒8mm左右处后开机工作。
穿丝中要注意控制左右行程开关,使储丝筒左右往返换向时,储丝筒左右二端留有3~5mm的余量。
穿丝完成后要注意电极丝是否穿过档丝棒、位于导轮中心及是否与导电块接触。
a.要将电极丝装入导轮的槽内,并与导电块接触良好。
并防止电极丝滑入导轮或导电块旁边的缝隙里。
b.操作过程中,要沿绕丝方向拉紧电极丝,避免电极丝松脱造成乱丝。
导轮槽电极上
电极下
六、电极丝垂直找正
在具有UV轴的线切割机床上,电极丝运行运行一段时间、重新穿丝后或加工新工件之前,需要重新校正电极丝对工作台平面的垂直度。
电极丝垂直度找正的常见方法有两种,一种是利用找正块,一种是利用校正器。
本例采用火花法找正。
找正块是一个六方体或类似六方体(a图)。
在校正电极丝垂直度时,首先目测电极丝的垂直度,若明显不垂直,则调节U、V轴,使电极丝大致垂直工作台;然后将找正块放在工作台上,在弱加工条件下,将电极丝沿X方向缓缓移向找正块。
当电极丝快碰到找正块时,电极丝与找正块之间产生火花放电,然后肉眼观察产生的火花:
若火花上下均匀(如图(b)所示),则表明在该方向上电极丝垂直度良好;若下面火花多(如图(c)所示),则说明电极丝右倾,故将U轴的值调小,直至火花上下均匀;若上面火花多(如图(d)所示),则说明电极丝左倾,故将U轴的值调大,直至火花上下均匀。
同理,调节V轴的值,使电极丝在V轴垂直度良好。
电火花均匀
七、工件找正
1、调整垫铁宽度,装夹工件,先压注工件一角,压板不要压的过紧,工作台支撑面移动至倾斜状态,在电极丝一侧露出工件基准角。
2、使用百分表找正工件的一面,百分表的跳动不要超过。
百分表一圈刻度是100,为1mm,即为2个小格。
铜棒调整工件位置,找正工件
3、压板压住工件
找正工件后用压板压住工件另一侧
八、工件基准角找正
工件基准角如上图所示。
电极丝第一个穿丝孔的中心需要根据基准角确定尺寸。
需要将X、Y向的坐标轴原点设置在基准角。
1、移动工作台,电极丝贴近工件露出外面一角的工件
2、电极丝先以Y轴(X或轴)贴火(设备有XY轴标识,短轴为X轴,长轴为Y轴,编程的XY与机床的XY一致),旋转Y方向手轮,待到火花均匀时按F12将机床锁住,然后Y方向手轮调到零并固定。
Y方向基准找正
Y轴贴火(工件未贴火前)
电极丝
Y方向手轮调到零
X方向基准找正
按F12键松开机床,接着旋转X方向手轮,将工件检验角移动至电极丝处,贴火前先将Y方向手轮负向旋转1圈(具体旋转圈数数据视情况而定,使电极丝能够沿着X轴方向移动),Y轴方向贴火,Y轴方向贴火时待火花均匀时按F12将机床锁住,将手轮调到零。
接着再按F12松开机床,正向旋转Y向手轮一圈,使Y方向归零。
按F12锁住机床。
(F12按一下松开,F12再按一次锁住)。
X、Y原点确定后操作面板清零。
九、确定第一个穿丝孔中心
工件第一个穿丝孔应为较小孔,最后一个穿丝孔应为较大孔。
本例第一个穿丝孔为直径25的孔中心。
X向尺寸为120,Y向尺寸为50。
通过手轮调整。
手轮一圈400刻度,旋转一圈4mm。
1、拆除电极丝
2、将Y方向手轮正向摇12圈零200(从小数往大数摇到200,12×4+2=50),X轴手轮正向摇30圈
3、按住F12把床子锁上。
4、穿丝
十、程序编制
1、绘制二维图纸并另存为dxf文件
在AutoCAD中将文件另存为DXF文件
2、启动CAXA线切割,导入dxf文件。
打开CAXA线切割软件
,单击【文件】/【数据接口】选项,文件类型选择DWG/DXF,单击打开文件,在下一个对话框中单击取消,打开待加工图纸。
3、测量电极丝直径,确定切割补偿距离
切割补偿距离=d/2+Z,式中d表示电极丝的直径,Z表示放电间隙。
如测量电极丝直径为,放电间隙为,则补偿距离为+=
4、线切割参数设置
选择下拉菜单“线切割”→“轨迹生成”命令,弹出“线切割轨迹生成参数表”对话框。
单击“切割参数”选项卡,设置“切入方式”为“指定切入点”,“切割次数”为“1”,“补偿实现方式”为“轨迹生成时自动实现补偿”,“拐角过渡方式”为“尖角”,“样条拟合方式”为“圆弧”,其他具体参数数值如图所示。
注意:
加工工件的“切割次数”最多为10次,切割次数为1,表示仅进行粗加工。
切割次数为几次,“后面偏移量/补偿值中就有几项与之对应”。
5、偏移量/补偿值设置
单击“偏移量/补偿值”选项卡。
由于加工轨迹与图形轮廓要有偏移量,设置参数数值如图所示。
然后单击“确定”按钮。
“偏移量/补偿值”选项卡
6、生成刀具轨迹
完成加工参数设置后,系统在界面的左下方提示“拾取轮廓”,直接拾取零件的外轮廓,轮廓变为红色虚线,同时在鼠标单击的位置上沿着轮廓线出现一对双向粉色箭头,根据系统提示“选择链拾取方向”(系统默认时为链拾取方向),选取逆时针方向后,在垂直轮廓线的方向上又出现一对粉色箭头,系统继续提示“选择加工的侧边或补偿方向”,拾取指向轮廓内侧的箭头(因为内部是废料)。
选择鼠标所在的逆时针加工方向箭头拾取加工轮廓后出现一对粉丝箭头
二次出现的粉色箭头确定补偿方向穿丝点位置和退出点
拾取指向轮廓内侧的箭头后,系统继续提示“输入穿丝点位置”,直接拾取圆心创建穿丝点,即确定了穿丝点位置,系统又提示“输入退出点(回车则与穿丝点重合)”,接着输入切入点,按Enter键后垂直切入,系统开始计算,稍后得出轨迹如图所示。
其余加工轨迹的生成同上。
加工轨迹加工轨迹在内侧(绿线处)
全部轨迹生成
可做线切割仿真演示。
将步长值适当减小,接着拾取加工轮廓,效果如视频所示。
(线切割加工仿真)
6轨迹跳步
为提高加工效率,针对多个复杂线切割加工路线,优先采用跳步加工。
选择下拉菜单“线切割”→“轨迹跳步”命令,系统在界面左下方的状态栏中提示“拾取加工轨迹”,按加工顺序依次拾取刚生成的刀具轨迹,然后单击右键结束操作即可。
便生成了图所示轨迹。
注意:
轨迹跳步的目的是使轨迹与轨迹之间将按拾取的先后顺序,生成跳步线,则被拾取的轨迹将变成一个轨迹。
生成加工代码时拾取该加工轨迹,则可自动生成跳步模加工代码。
生成轨迹跳步
生成轨迹仿真
7轨迹仿真
选择下拉菜单“线切割”→“轨迹仿真”命令,弹出立即菜单,单击后在其弹出胡快捷菜单中选择“连续”,并且设置步长为“”如图16所示。
设置轨迹仿真参数
同时,系统在界面左下方的状态栏中提示“拾取轨迹加工”,直接拾取刚生成的刀具轨迹,然后系统便完成整地模拟从起步到加工结束之间的全过程。
8生成3B代码
生成代码就是按照当前机床类型的配置要求,把已经生成的加工轨迹转化生成3B加工代码数据文件,即线切割加工程序,有了数控程序就可以直接输入机床进行数控加工。
操作步骤如下:
(1)选择下拉菜单“线切割”→“生成3B代码”命令,系统自动弹出“生成3B加工代码”对话框。
选择合适的保存位置,按要求填写后置文件名,如图所示。
“生成3B加工对话框”
拾取加工轨迹并设置如图所示
(2)单击“保存”按钮,系统弹出一个立即菜单,如图所示设置加工参数。
生成3B代码设置
此时系统提示“拾取加工轨迹”,拾取加工轨迹。
当拾取到加工轨迹后,该加工轨迹变为被拾取颜色。
单击鼠标右键结束拾取,系统即生成数控程序。
该程序是“记事本”文件,如图所示。
(3)选择下拉菜单“文件”→“保存”命令,保存所创建的加工文件。
B12400B0B12400GXL1
B12400B0B49600GYNR1
B12400B0B12400GXL3
D
B75000B0B75000GXL3
D
B9900B0B9900GXL1
B0B22400B22400GYL2
B19800B0B19800GXL3
B0B44800B44800GYL4
B19800B0B19800GXL1
B0B22400B22400GYL2
B9900B0B9900GXL3
D
B75000B78000B78000GYL1
D
B9950B17234B17234GYL2
B9950B17234B52466GYSR2
B22737B0B22737GXL3
B0B9900B19800GXSR3
B22737B0B22737GXL1
B17263B9900B7313GXSR2
B9950B17234B17234GYL4
DD
(4)修改3B代码
在第一段的最后一句之前添加一个D停止命令,防止电极丝拖动废料损坏设备及电极丝断裂。
矩形程序做同样处理。
最后一段加工不规则形状的程序D添加的位置在倒数第二句。
没加工完成时使用吸铁石固定住废料与零件之间,防止废料落下损坏设备。
修改后的程序如图所示。
B12400B0B12400GXL1
B12400B0B49600GYNR1
D
B12400B0B12400GXL3
D
B75000B0B75000GXL3
D
B9900B0B9900GXL1
B0B22400B22400GYL2
B19800B0B19800GXL3
B0B44800B44800GYL4
B19800B0B19800GXL1
D
B0B22400B22400GYL2
B9900B0B9900GXL3
D
B75000B78000B78000GYL1
D
B9950B17234B17234GYL2
B9950B17234B52466GYSR2
B22737B0B22737GXL3
B0B9900B19800GXSR3(N)
B22737B0B22737GXL1
D
B17263B9900B7313GXSR2
B9950B17234B17234GYL4
DD
十一加工
1、U盘插入数据接口
2、光标移动至【文件调入】,按回车键,单击F4键调盘,将光标移动至USB盘,按回车键,打开U盘,选择待加工文件,单击F3键,选择虚拟盘后按回车键。
按ESC键退回编程系统界面。
3、输入W,单击回车(或将光标移动至Work加工#后回车),选择【切割】,回车,调出图形。
4、先按控制面板上的绿色供水按钮,再按控制面板上绿色的运丝按钮。
5、电压选择75V,加工电流选择。
6、选中F10、F11、F12,单击F1键,再按回车键进行切割。
X、Y轴走的是绿色字说明切割正确,反之则切割错误。
注意:
按F3可以调切割进给频率(速度)。
根据材料厚度调整。
绿色为供水开按钮运丝开按钮
F3键调节频率
7.跳步
第一个孔加工后拆掉电极丝,只保留F12,屏幕出现【继续】时单击回车,进行跳步,跳到下一个穿丝孔的中心,然后进行上丝,进行切割。
最后一个孔按上述加工。
注意:
机床在锁的情况下才能自动跳步,否则不可以。
8.卸件
切割完成后,先关运丝开关,再关水开关,然后拆除运行丝,最后卸下加工好的工件,把机床上杂物清理干净。
红色按钮为关水按钮红色按钮为关丝按钮
9.关机
先关控制柜上的红色按钮,再按控制面板上的红色旋合按钮。
控制柜关机按钮机床关机旋合按钮
10、清理并检查检查
1)清洗工件
2)擦拭工件
3)检查工件关键尺寸
按照图纸检查加工工件尺寸是否正确。
十二调整加工参数及切割速度
1、电加工参数
切割加工前,要根据加工材料和精度要求调整好电加工参数。
电加工参数主要有:
脉冲宽度tw、脉冲间隔t、开路电压u0、放电峰值电流ip等。
脉冲宽度增大,单个脉冲能量增多,切割速度提高,表面粗糙度数值变大,放电间隙增大,加工精度下降。
粗加工时一般采用较大的脉宽。
脉冲间隔增大,单个脉冲能量减少,切割速度下降,表面粗糙度数值下降。
精加工及厚工件切割时,一般采用较大的脉冲间隔,有利于排屑和提高加工的稳定性,防止断丝。
开路电压增大时,放电间隙增大,排屑容易,可以提高切割速度和加工稳定性,但会使工件的表面粗糙度变差。
开路电压一般在60-150V之间。
放电峰值电流,是决定单脉冲能量的主要因素之一。
ip增大,切割速度迅速提高,表面粗糙度数值增大,电极丝损耗加大,容易断丝。
一般精加工时,采用较小的ip。
切割规范
序
号
工件厚
度/mm
加工
电压/V
加工电流/A
脉冲宽度/us
脉冲间
隔/μs
功率输
出/只
粗糙度/μm
切割速度/(mm2/min)
波形选择
1
20-30
70
15
12
60
3
≤
≥30
矩形脉冲
2
30-50
75
5-15
28
112
3
≤
≥50
3
30
80
1
25×4
75
3
≤
≥15
分组脉冲
4
50
80
2
40×4
80
5
≤
≥40
5
60
75
35
48
144
5
≤5
≥80
矩形脉冲
6
80-100
85
25
52
260
4
≤
≥60
7
150-180
85
10
36
196
4
≤
≥40
8
250-280
85
25
40
280
5
≤
≥40
2、加工工艺指标
电火花线切割加工工艺指标主要包括切割速度、表面粗糙度、加工精度等。
此外,放电间隙、电极丝和加工表面层变化也是反映加工效果的重要内容。
电火花线切割的切割速度通常用单位时间内工件切割的面积来衡量,快走丝的切割速度一般在40一80mm2/min,它与加工电流大小关系密切。
一般情况下,放电间隙为,电极丝的损耗为每切割10000mm2电极丝直径减小小于。
影响工艺指标的因素很多,如机床精度、脉冲电源的性能、工作液脏污程序、电极丝与工件材料及切割工艺路线等。
提高生产率的主要途径:
(1)增大脉冲电压幅值;
(2)增加脉冲宽度;
(3)减少脉冲间隔时间;
(4)适当增大脉冲电源的功率。
影响加工表面粗糙度的几个因素:
(1)导丝轮及其轴承因磨损而使精度变差;
(2)电极丝移动不平稳,有振动;
(3)电极丝绕得太松,张力不够;
(4)脉冲电源电参数选择不当,拉弧现象太多;
(5)钼丝损耗过大、变细了的钼丝在导轮内窜动;
(6)进给速度调节不当,加工不稳定。
影响加工精度的因素:
(1)脉冲电源电压不稳定,不能保证恒定的放电间隙;
(2)电极丝和工作台的垂直度不好;
(3)机床制造精度不高;
(4)电极丝颤动。
对工作液的要求:
(1)有一定的介电能力;
(2)有较好的冷却性能;
(3)有良好的洗涤性能;
(4)有较好的去游离能力和灭弧能力;
(5)防锈;
(6)无公害。
电极丝的选择要求:
(1)有良好的耐蚀性,利于提高加工精度;
(2)良好的导电性,有利于提高电路效率;
(3)有较高的熔点,有利于大电流加工;
(4)有较高的抗拉强度和良好的直线性以利于提高使用故作寿命。