机械零件的失效及分析.docx
《机械零件的失效及分析.docx》由会员分享,可在线阅读,更多相关《机械零件的失效及分析.docx(28页珍藏版)》请在冰豆网上搜索。
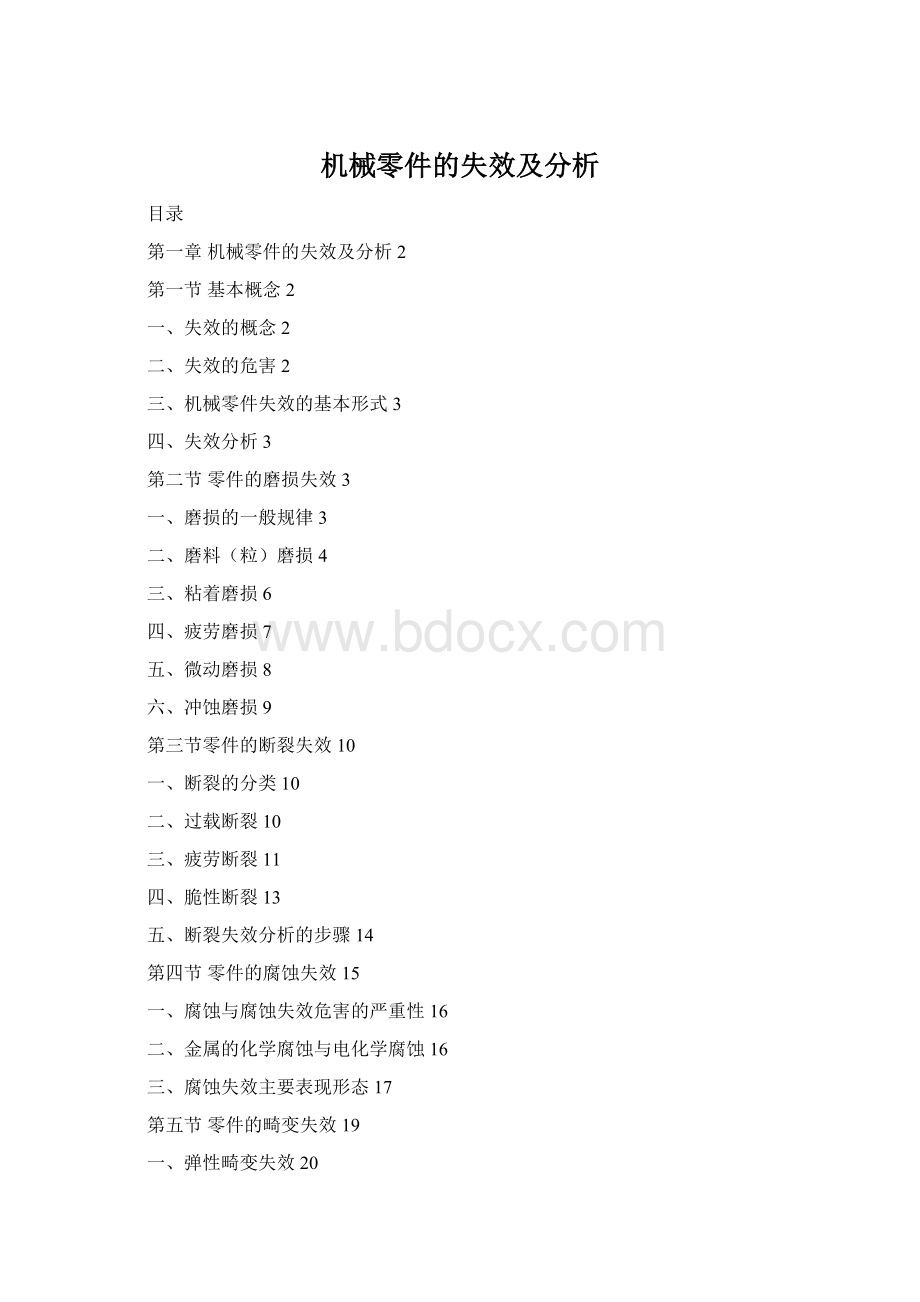
机械零件的失效及分析
目录
第一章机械零件的失效及分析2
第一节基本概念2
一、失效的概念2
二、失效的危害2
三、机械零件失效的基本形式3
四、失效分析3
第二节零件的磨损失效3
一、磨损的一般规律3
二、磨料(粒)磨损4
三、粘着磨损6
四、疲劳磨损7
五、微动磨损8
六、冲蚀磨损9
第三节零件的断裂失效10
一、断裂的分类10
二、过载断裂10
三、疲劳断裂11
四、脆性断裂13
五、断裂失效分析的步骤14
第四节零件的腐蚀失效15
一、腐蚀与腐蚀失效危害的严重性16
二、金属的化学腐蚀与电化学腐蚀16
三、腐蚀失效主要表现形态17
第五节零件的畸变失效19
一、弹性畸变失效20
二、塑性畸变失效20
三、翘曲畸变失效21
四、畸变失效分析21
第二章设备的使用与维护22
第一节设备的使用22
一、合理安排生产任务23
二、配备合格的设备操作人员23
三、设备操作的基本功培训23
四、建立健全的设备使用管理规章制度24
第二节延长机械的使用寿命的方法24
一、优秀的设计是延长机械使用寿命的首要环节25
二、提高机械产品的质量使之经久耐用26
三、正确合理使用是延长施工机械的寿命的关键26
四、实行定期保养27
五、掌握正确的机械维修的方法有效地延长使用寿命27
六、其它28
第三节润滑保养28
一、润滑油检测的传统方法28
二、油品的报废判断29
三、传统润滑油检测方法的不足之处30
四、专业、科学的润滑油检测方法30
六、设备润滑的作用32
七、润滑管理的基本要求32
参考文献33
第一章机械零件的失效及分析
第一节基本概念
一、失效的概念
机械设备中各种零件或构件都具有一定的功能,如传递运动、力或能量,实现规定的动作,保持一定的几何形状等等。
当机件在载荷(包括机械载荷、热载荷、腐蚀及综合载荷等)作用下丧失最初规定的功能时,即称为失效。
一个机件处于下列三种状态之一就认为是失效:
①完全不能工作;②不能按确定的规范完成规定功能;③不能可靠和安全地继续使用。
这三个条件可以作为机件失效与否的判断原则。
二、失效的危害
机械零件与构件的失效最终必将导致机械设备的故障。
关键机件的失效会造成设备事故,人身伤亡事故,甚至大范围内灾难性后果。
在生产线上一个小小的零件失效,可以是整个生产线瘫痪。
因此有效的预防、控制、监测零件的失效是一项意义重大的工作。
三、机械零件失效的基本形式
一般机械零件的失效形式是按失效件的外部形态特征来分类的,大体包括:
磨损失效、断裂失效、变形失效和腐蚀与气蚀失效。
在生产实践中,最主要的失效形式是零件工作表面的磨损失效;而最危险的失效形式是瞬间出现裂纹和破断,统称为断裂失效。
四、失效分析
失效分析是指分析研究机件磨损、断裂、变形、腐蚀等现象的机理或过程的特征及规律,从中找出产生失效的主要原因,以便采用适当的控制方法。
失效分析的直接的、技术上的目的是为制订维修技术方案提供可靠依据,并对引起失效的某些因素进行控制,以降低设备故障率,延长设备使用寿命。
此外,失效形式分析也能为设备的设计、制造反馈信息;为设备事故的仲裁提供客观依据。
第二节零件的磨损失效
摩擦与磨损是自然界的一种普遍现象。
当零件之间或零件与其他物质之间相互接触,并产生相对运动时,就称为摩擦。
零件的摩擦表面上出现材料耗损的现象称为零件的磨损。
材料磨损包括两个方面:
一是材料组织结构的损坏;二是尺寸、形状及表面质量(粗糙度)的变化。
如果零件的磨损超过了某一限度,就会丧失其规定的功能,引起设备性能下降或不能工作,这种情形即称为磨损失效。
根据摩擦学理论,零件磨损按其性质可以分为磨料磨损、粘着磨损、微动磨损、冲蚀磨损和腐蚀磨损。
一、磨损的一般规律
零件磨损的外在表现形态是表层材料的磨耗。
在一般情况下,总是用磨损量来度量磨损程度。
一般可以分为三个阶段:
(1)初期磨损阶段
对机械设备中的传动副而言是磨合过程。
这一阶段的特点是在短时间内磨损量增长较快。
如果表面粗糙、润滑不良或载荷较大,都会加速磨损。
经过这一阶段后,零件的磨损速度逐步过渡到稳定状态。
机械设备的磨合阶段结束后,应清除摩擦副中的磨屑,更换润滑油,才能进入满负荷正常使用阶段。
(2)正常磨损阶段
摩擦表面的磨损量随着时间的延长而均匀,、缓慢增长,属于自然磨损。
在磨损量达到极限之前的这一段时间是零件的磨损寿命,它与摩擦表面工作条件、技术维护好坏关系极大。
使用保养得好,可以延长磨损寿命,从而提高设备的可靠性与有效利用率。
(3)急剧磨损阶段
当零件表面磨损量超过极限值以后如继续摩擦,其磨损强度急剧增加,其原因是:
①零件耐磨性较好的表层被破坏,次表层耐磨性显著降低;②配合间隙增大,出现冲击载荷;③摩擦力与摩擦功耗增大,使温度升高,润滑状态恶化、材料腐蚀与性能劣化等。
最终设备会出现故障或事故。
因此,这一阶段也称为事故磨损阶段。
当零件磨损表面的磨损量达到极限值时,就已经失效,不能继续使用,应采取调整、维修、更换等措施,防止设备故障与事故的发生。
二、磨料(粒)磨损
零件表面与磨料相互摩擦,而引起表层材料损失的现象称为磨料磨损或磨粒磨损。
磨料也包括对零件表面上硬的微凸体。
在磨损失效中,磨料磨损失效是最常见、危害最为严重的一种。
(一)磨料磨损工况的分类
磨料磨损分为三种情况:
第一种是直接与磨料接触的机件所发生的磨损,称为两体磨损;第二种是硬颗料进入摩擦副两对摩表面之间所造成的磨损,称为三体磨损;第三种是坚硬、粗糙的表面微凸体在较软的零件表面上滑动所造成的损伤,称为微凸体磨损。
(二)磨料磨损的原理与特征
磨料磨损的过程实质上是零件表面再磨料作用下发生塑性变形、切削与断裂的过程。
磨料对零件表面的作用力分为垂直于表面与平行于表面的两个分力,垂直分力使磨料压入材料表面,而平行分力使磨料向前滑动,对表面产生耕犁与微切削作用。
微切削作用会产生微切屑。
而耕犁作用会使材料向磨料两侧挤压变形,使犁沟两侧材料隆起。
随着零件表层材料的脱离与表面性能的劣化,最终导致表面破坏和零件失效。
磨料磨损的显著特点是:
磨损表面具有与相对运动方向平行的细小沟槽;磨损产物中螺旋状、环状或弯曲状细小切屑及部分粉末。
(三)磨料磨损的影响因素分析
(1)金属材料的硬度
一般情况下,金属材料的硬度越高,耐磨性越好。
实验证明,未经热处理的金属材料,其相对耐磨性与硬度成正比,而与合金含量无关。
经淬火后的钢,其相对耐磨性仍然与淬火硬度成正比,但合金含量较高的钢材,其相对耐磨性增长得较快。
(2)材料的显微组织
一般来说,具有马氏体组织的材料有较高的耐磨性。
而在相同硬度条件下,贝氏体又比马氏体高得多。
同样硬度的奥氏体与珠光体相比,奥氏体的耐磨性要高得多。
(3)磨料性质
许多研究工作者发现,磨料粒度对材料的磨损率存在一个临界尺寸。
当磨料粒度小于临界尺寸时,材料的磨损率(单位时间磨损量)随磨料粒度的增加而增加,且材料越软越敏感。
当磨料粒度超过临界尺寸后,磨损率与粒度几乎无关,即磨损率基本上不随粒度的增加而增加。
(4)其他因素
影响磨料磨损还有其他因素,例如磨料硬度、摩擦表面相对运动的方式,磨损过程的工况条件等。
(四)减少磨料磨损的措施
对工程机械、农业机械、矿山机械中的许多遭受二体磨损机件,主要是选择合适的耐磨材料,优化结构与参数设计。
对所有机械设备中可能遭受三体磨损的摩擦副,如轴颈与轴瓦,滚动轴承,缸套与活塞,机械传动装置等,应设法阻止外界磨料进入摩擦副,并及时清除摩擦副磨合过程中产生的磨屑及硬微凸体磨损产生的磨屑。
具体措施是对空气、油料过滤;注意关键部分的密封;经常维护、清洗换油;提高摩擦副表面的制造精度;进行适当的表面处理等。
三、粘着磨损
粘着磨损是指两个作相对滑动的表面,在局部发生相互焊合,使一个表面的材料转移到另一个表面所引起的磨损。
(一)粘着磨损的机理
由于摩擦表面粗糙不平,两摩擦表面实际上只是在一些微观点上接触。
在法向载荷作用下,接触点的压力很大,使金属表面膜破裂,两表面的裸露金属直接接触,在接触点上发生焊合,即粘着。
当两表面进一步相对滑动时,粘着点便发生剪切及材料转移现象。
在邻近区域,凸出的材料又可能发生新的粘着,直至最后在表面上脱落下来,形成磨屑。
(二)影响粘着磨损的因素
(1)金属互溶性的影响
一般规律是互溶性越好,粘着倾向越大。
同种材料互溶性好,异种材料互溶性差,故同种材料对磨损比异种材料磨损大得多。
(2)金属点阵结构与硬度的影响
一般面心立方点阵的金属明显比其他点阵形式金属的粘着倾向大,而六方点阵表现了最小的粘着倾向。
材料的硬度增加时,粘着的倾向减少。
(3)载荷与速度的影响
当载荷较轻时,金属表面有氧化膜保护,就不发生粘着。
当载荷或速度增大,微观接触点上的温度升高,氧化膜遭到破坏,就会发生严重粘着磨损现象。
然而,当载荷较大或速度极快、摩擦表面温度很高时,磨损率反而显著下降,因为表露出的金属会在高温下迅速生成新的保护膜。
(三)减少粘着磨损的措施
(1)合理润滑
建立可靠的润滑保护膜,隔离相互摩擦的金属表面,是最有效、最经济的措施。
(2)选择互溶性小的材料配对
铅、锡、银等在铁的溶解度小,用这些金属的合金做轴瓦材料,抗粘着性能极好(如巴氏合金、铝青铜、高锡铝合金等),钢与铸铁配对抗粘着性能也不错。
(3)金属与非金属配对
钢与石墨、塑料等非金属摩擦时,粘着倾向小,用优质塑料作耐磨层是很有效的。
(4)适当的表面处理
表面淬失、表面化学处理、磷化处理、硫化处理、渗氮处理、四氧化三铁处理以及适当的喷涂处理,都能提高金属抗粘着磨损的能力。
四、疲劳磨损
当摩擦副两接触表面做相对滚动或滑动时,周期性的载荷使接触区受到很大的交变接触应力,使金属表层产生疲劳裂纹并不断扩展、引起表层材料脱落,造成点蚀和剥落,这一现象称为表面疲劳磨损。
(一)疲劳磨损的机理与特征
近年来,人们对疲劳机理的研究形成了一种新的、比较深入的理论,认为疲劳磨损主要是由于接触区切应力周期的出现和消长造成的。
当一个表面在另一个表面作纯滚动或滚动加滑动时,最大切应力发生在亚表层。
在它的作用下,亚表层内的材料将产生错位运动,错位在非金属夹杂物及晶界等障碍物处形成堆积。
由于错位的相互切割产生空穴,空穴集中形成空洞,进而变成原始裂纹。
裂纹在载荷作用次下逐步扩展,最后折向表面。
由于裂纹在扩展过程中相互交错,加上润滑油在接触点处被压入裂纹产生楔裂作用,使表层产生点蚀或剥落。
当原始裂纹较浅时,表现为点蚀(麻点状),若原始裂纹在表层以下大于200μm时,表层材料呈片状剥落(麻坑状)。
(二)提高抗疲劳磨损的途径
凡是能阻止疲劳裂纹形成与扩展的措施都能减少疲劳磨损。
具体可以考虑以下几条主要途径:
(1)减少材料中的脆性夹杂物
脆性夹杂物边缘极易产生微裂纹,降低材料的疲劳寿命。
硅酸盐类夹杂物对疲劳寿命危害最大。
(2)适当的硬度
在一定的硬度范围内,材料抗疲劳磨损的性能随硬度的升高而增大,对于轴承钢,抗疲劳的最佳峰值硬度为62HRC左右,钢制齿轮的最佳表面硬度为58-62HRC。
此外,摩擦副设当的硬度匹配也是减少疲劳磨损的正确途径。
(3)提高表面加工质量
降低摩擦表面粗糙度和形状误差,可以减少微凸体,均衡接触应力,提高抗疲劳磨损的能力。
接触应力越大,对加工质量的要求也越高。
(4)表面处理
一般来说,当表层在一定深度范围内存在残余压应力时,不仅可以提高弯曲、扭转疲劳抗力,还能提高接触疲劳抗力,减少疲劳磨损。
当进行表面渗碳、淬火、表面喷丸、滚压处理时,都可使表层产生残余压应力。
(5)润滑
润滑油的衬垫作用,可使接触区的集中载荷分散。
润滑油粘度越高,接触区压应力越接近平均分布。
但应注意,如果润滑油粘