185曲轴铣端面打中心孔组合机床和专用夹具设计.docx
《185曲轴铣端面打中心孔组合机床和专用夹具设计.docx》由会员分享,可在线阅读,更多相关《185曲轴铣端面打中心孔组合机床和专用夹具设计.docx(38页珍藏版)》请在冰豆网上搜索。
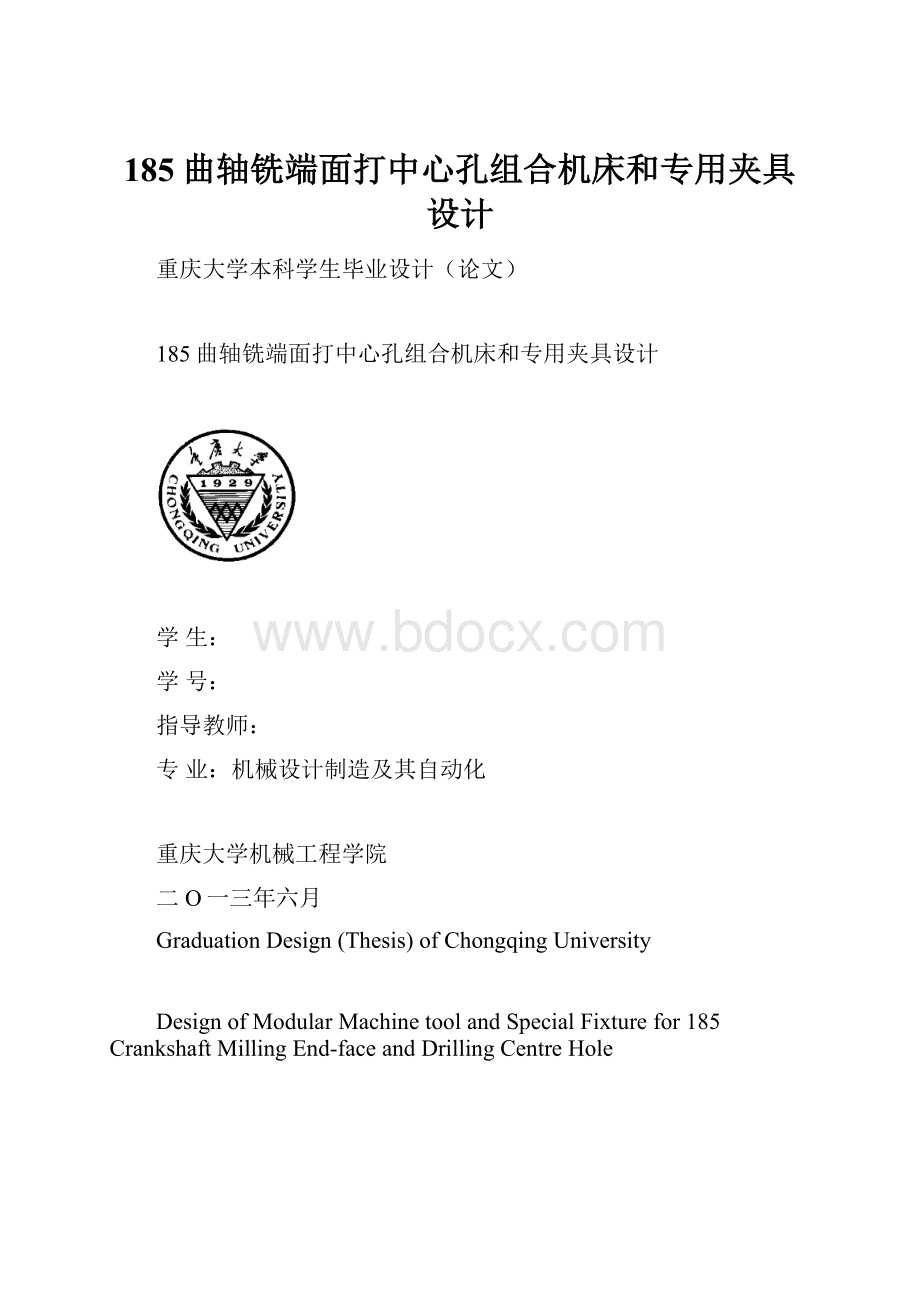
185曲轴铣端面打中心孔组合机床和专用夹具设计
重庆大学本科学生毕业设计(论文)
185曲轴铣端面打中心孔组合机床和专用夹具设计
学生:
学号:
指导教师:
专业:
机械设计制造及其自动化
重庆大学机械工程学院
二O一三年六月
GraduationDesign(Thesis)ofChongqingUniversity
DesignofModularMachinetoolandSpecialFixturefor185CrankshaftMillingEnd-faceandDrillingCentreHole
Undergraduate:
Supervisor:
Major:
MechanicalDesignandManufactureofAutomation
CollegeofMechanicalEngineering
ChongqingUniversity
June2013
摘要
本次毕业设计主要任务是为曲轴零件铣端面打中心孔设计专用夹具和组合机床。
具体包括编制曲轴零件的加工工艺规程、专用组合机床的总体设计和专用夹具设计。
曲轴的加工工艺规程主要研究内容有确定零件的生产类型,对曲轴零件进行工艺分析,毛坯的确定,工艺路线的拟定,及工序的加工余量,计算工序尺寸及公差和确定切削用量及时间定额。
本次设计的组合机床选用的是配置形式是卧式双面组合机床,最终结果是绘制机床联系尺寸图。
主要是对动力部件、支撑部件、输送部件和辅助部件的选择。
具体涉及到的内容如下:
绘制零件的加工示意图和加工工序图,机床的配料高度的确定,夹具外形轮廓的确定,侧底座、中间底座尺寸的确定,主轴箱外形尺寸的确定。
本工序的专用夹具用两个V形块和一个定位销来定位,限制5个自由度。
夹紧机构选用移动压板式夹紧机构。
要求夹具稳定可靠、拆卸方便。
采用硬质合金端铣刀铣曲端面,并且铣刀通过两个直角对刀块进行对刀。
钻中心孔采用中心钻。
关键词:
组合机床设计、夹具设计、工艺规程、联系尺寸图
ABSTRACT
ThemaintaskofthegraduatedesignisDesignofModularMachinetoolandSpecialFixturefor185CrankshaftMillingEnd-faceandDrillingCentreHole.Itmainlycontainscompilingtheprocessingtechnicspecificationofthecrankshaft,modularmachinetooldesignandspecialfixturedesign.Themainresearchcontentsoftheprocessingtechnicspecificationofthecrankshaftisdeterminingtheproductiontypeofthepart,analyzingtheprocessingtechnicofthecrankshaft,determiningtheroughpart,studyingouttheprocessroute,calculatingthemachiningallowanceandprocessdimensionandtolerance,atlast,determiningthecuttingdosagesandtimefixed.
Theconfigurationformofthemodularmachinetoolishorizontaldouble-sizedmachinetool.Atlast,drawingamachinetoolcontactdimensiondrawing.Mainlychoosingthedynamiccomponents,supportingparts,transmissionpartsandauxiliaryparts.Theconcretecontentincludes:
drawingtheprocessingschematicdiagramandprocessingprocedurechart.Determiningtheheightofthemachineingredients.Determiningthecontouroffixture.Determiningthesizeofthewingbaseandmiddlebase.Finally,determiningthecontourdimensionofthespindlebox.
ThelocatingsystemofthespecialfixtureistwoV-blocksandapin,limiting5degreesoffreedom.Thepartisclampedbymovingplaten.Besides,thefixtureshouldstableandreliable,demolitionconvenient.Thetoolofmillingend-faceanddrillingcentreholeishardalloyendmillingcutterandcentrebit.Toolsettingofthemillingcutteristhroughtherightangleknifeblock.
Keywords:
modularmachinetooldesign,fixturedesign,processplanning,
contactdimensiondrawing
1绪论
曲轴是发动机上的一个重要零件。
曲轴承受由活塞通过连杆传来的力,活塞的往复直线运动通过连杆传递给曲轴而转变为旋转运动。
曲轴结构形状复杂,刚性极差,但技术要求较高,使得曲轴加工难度较大。
本次课题是185曲轴铣端面打中心孔组合机床及专用夹具设计,为了使曲轴加工方便,设计组合机床对曲轴铣端面打中心孔在同一组机床上进行。
是曲轴加工工序集中,减少工时。
并设计专用夹具,保证曲轴的加工精度,满足工艺要求。
组合机床是由一些通用部件和专用部件组成。
在国内外研究都相当有结果,在我国,组合机床发展已有28年的历史,其科研和生产都具有相当的基础,应用也已深入到很多行业。
组合机床及其自动线是集机电于一体的综合自动化程度较高的制造技术和成套工艺装备。
它的特征是高效、高质、经济实用,因而被广泛应用于工程机械、交通、能源、军工、轻工、家电等行业。
我国传统的组合机床及组合机床自动线主要采用机、电、气、液压控制,它的加工对象主要是生产批量比较大的大中型箱体类和轴类零件(近年研制的组合机床加工连杆、板件等也占一定份额),完成钻孔、扩孔、铰孔,加工各种螺纹、镗孔、车端面和凸台,在孔内镗各种形状槽,以及铣削平面和成形面等。
随着技术的不断进步,一种新型的组合机床——柔性组合机床越来越受到人们的青睐,它应用多位主轴箱、可换主轴箱、编码随行夹具和刀具的自动更换,配以可编程序控制器(PLC)、数字控制(NC)等,能任意改变工作循环控制和驱动系统,并能灵活适应多品种加工的可调可变的组合机床。
另外,近年来组合机床加工中心、数控组合机床、机床辅机(清洗机、装配机、综合测量机、试验机、输送线)等在组合机床行业中所占份额也越来越大。
而在国外,超高速和超高精度加工技术装备与复合、多功能、多轴化控制设备等深受欢迎。
据专家分析,机床装备的高速和超高速加工技术的关键是提高机床的主轴转速和进给速度,目前国际水平主轴转速达到10000~20000r/min,最高进给速度可达20~60m/min;复合、多功能、多轴化控制装备的前景亦被看好。
在零部件一体化程度不断提高、数量减少的同时,加工的形状却日益复杂。
多轴化控制的机床装备适合加工形状复杂的工件。
本次设计课题必须完成的内容有:
曲轴的工艺规程设计;组合机床的总体设计;专用夹具的设计。
实现途径是在老师的帮助下,通过已学过的专业知识,和查阅相关资料图表,分析曲轴的结构特征,制定加工工艺规程;在了解组合机床的特征和设计要求的要求上,选择通用部件、绘制工序图和加工工序图,确定各部分的尺寸,绘制组合机床尺寸联系图;根据组合机床和曲轴的结构和尺寸要求,选择合理的定位元件和夹紧机构,实现六点定位和夹紧工件。
合理的布置个部件的位置,绘制夹具总装图。
由于个人能力有限,不足的地方望老师批正。
2曲轴加工工艺规程
2.1曲轴零件的分析
2.1.1曲轴的结构特点
轴类零件的功用为支承传动零件、传递扭矩和承受载荷以及保证装在轴上的工件(刀具)具有一定的回转精度。
曲轴一般由主轴颈,连杆轴颈、曲柄、平衡块、前端和后端等组成。
曲轴在轴类零件分类中属于异形轴,是发动机上的一个重要零件,承受由活塞通过连杆传来的力,并将活塞的往复运动通过曲柄连杆机构变为旋转运动,将发动机所做的功传递出去。
轴在工作时所承受的是很大的扭转力矩以及大小和方向都变化的弯曲力。
因此,要求曲轴具有足够的刚度和强度,具有良好的承受冲击载荷的能力,耐磨损且润滑良好。
本次设计的185曲轴零件,如图2-1所示。
185曲轴采用球墨铸铁,毛坯为铸件。
其外形结构是曲轴零件中比较简单的一种。
它的工作过程是:
在外力作用下使曲轴旋转,通过连杆轴颈上的连杆将运动传递到缸筒内的活塞,从而压缩缸内的高压油并将油点燃,燃烧的高压油将自身的内能转换为动能推动活塞运动,运动又传到连杆再通过连杆带动连杆轴颈,这样曲轴继续旋转。
图2-1
2.1.2零件的技术要求
1)铸件应该经正火处理,硬度为240~190HB,显微组织按部标JB1802,石墨数不低于5级球化体大于75%,允许有少于5%的碳化铁+磷共晶,但磷共晶为0%~5%。
2)未标圆角半径为3mm。
3)加工面不应该有毛刺、裂缝、结疤、夹渣等缺陷,并应清理清洁。
4)所有加工表面应光洁,不可有裂缝、压痕、毛刺、气孔、凹陷以及非金属夹杂物,在磨光表面上不该有深痕和黑点。
5)锥形规涂色检查锥面密合面应不少于70%。
6)清出油道及其其他部分的金属屑、污染物及其他杂物,并清洗吸干。
7)中心孔必须保持完好。
8)精加工后,应经磁力探伤并退磁。
2.2工艺规程的制定
零件加工的工艺规程就是一些列不同工序的综合。
由于生产规模和具体情况的不同,对同一零件的加工工序可能有很多方案。
但应根据具体条件采用其中最完善和最经济的一种方案。
但工艺规程选择要考虑的基本因素如下:
生产规模是决定生产类型的主要因素,及设备、用具、机械化、自动化程度等。
1)制造零件所用的坯料或型材的形状、尺寸和精度。
2)零件材料的性质。
3)零件制造的精度,包括尺寸公差、形位公差以及零件图上所指定的要求。
4)零件表面的粗糙度。
5)特殊限制条件,如:
工厂设备和用具条件。
6)编制的加工规程要在生产规模与生产条件下达到最经济与安全的效果。
2.2.1185曲轴材料及毛坯
185曲轴的材料为球墨铸铁(QT60-2),该材料的强度高、耐磨,并且有一定的韧性。
毛坯种类的确定始于零件的结构形状、尺寸大小、材料的力学性能和零件的生产类型直接相关的,另外还和毛坯车间的具体生产条件相关。
185曲轴的选择毛坯为铸件。
在大批量生产中,常采用精度和生产率高的毛坯制造方法,如金属型铸造,可以使毛坯的形状接近于零件的形状,因此可以减少切削加工用量,从而提高材料的利用率,降低了机械加工成本。
本零件选用的造型方法为砂型机器造型。
2.2.2生产类型及工艺特征
零件的生产纲领:
N=Qn(1+a)(1+b)(2-1)
式中N——零件的生产纲领,件/年;
Q——产品的年产量,台/年;
n——每台产品中包含该零件的数目;
a——该零件设备的百分率,%;
b——该零件废品的百分率,%。
划分生产类型时,既要根据生产纲领,同时还要考虑零件的体积、质量等因素。
值得一提的是生产类型将直接影响工艺过程的内容和生产的组织形式,并在一定程度上对产品的结构设计也起着重要的作用。
由于本零件是大批量生产,它的主要工艺特征是广泛的用专用机床、专用夹具和专用刀具、量具,机床按工艺路线排列组织流水线生产。
为减轻工人的劳动强度,留有进一步提高生产率的可能,曲轴在工艺设计上采用组合机床流水线加工的方式。
2.2.3定位基准的选择
工件在机床上用夹具进行夹紧加工时,用来决定工件相对于刀具的位置的工件上的这些表面称为定位基准。
定位基准分粗基准和精基准。
曲轴和一般轴类零件的区别是:
一般轴件的全部轴颈都位于同一轴线上,而曲轴的主轴颈虽然也位于同一轴线上,但是其连杆轴颈不与主轴颈同轴,而是离开一定距离而彼此平衡。
为保证各轴颈的同轴度要求,在基准选择时采用基准统一的原则,即粗、精加工各主轴颈时都采用顶尖孔作为定位基准。
对于连杆轴颈的加工,为保证连杆轴颈轴线与主轴颈的轴线之间的平行,在基准选择时应采用定位基准和装配基准重合的原则,即粗、精加工连杆轴颈时都采用两个主轴颈作为定位基准。
因此,在加工连杆轴颈时选择主轴颈定位,加工主轴颈时则选择顶尖孔定位。
2.2.4工艺路线的拟定
拟定工艺路线的出发点是使零件的几何形状、尺寸精度以及位置精度等技术要求能得到保证。
工艺路线的拟定一般需要做两个方面的工作:
一是根据生产纲领确定加工工序和工艺内容,根据工序的集中和分散程度划分工艺;二是选择工艺基准,即主要选择定位基准和检验基准。
在生产纲领已确定为批量生产的条件下,可以考虑采用万能机床、组合机床和专用夹具,并尽量采用工序集中的原则,减少安装的次数来提高生产效率。
除此之外,还应尽量考虑经济精度以使生产成本尽量下降,根据以上原则,拟定的工艺路线如下:
0铣端面,钻中心孔
5粗车长头各外圆
10粗车短头各外圆
15钻短头孔,锪60°锥面
20精车短头各外圆
25精车长头各外圆
30铣角向定位面
35粗车连杆轴颈
40钻注油孔
45钻出油孔
50锪出油孔口
55车短头
60车长头
65精磨长头轴承位外圆
70精磨短头轴承位外圆
75精磨连杆轴颈外圆
80铣齿顶平面
85粗铣短头键槽
90精铣短头键槽
95粗铣长头键槽
100精铣长头键槽
105钻长头平衡块螺孔M12×1.25
110钻短头平衡块螺纹底孔
115钻M6孔螺纹底孔
120M6孔倒角
125M6孔攻丝
130铣齿槽
135螺纹孔及底孔吹拈渣
140精磨连杆轴颈外圆
145连杆轴颈油孔抛光
150精磨封油位
155精磨1:
8锥度
160车长头外螺纹
165研磨连杆颈孔
175磨正时齿轮位外圆
180电击
185去毛刺
190清洗
195探伤
200再清洗
205清理丝孔
2.2.5毛坯机械加工余量、工序尺寸确定和切削用量的计算
1、毛坯机械加工余量的确定
目前,我国曲轴毛坯的加工余量都比较大。
通常曲轴轴颈单边为5~7mm,
因曲轴形状较为复杂且生产批量大,故毛坯选用铸件,造型方法为砂型机器造型。
查《机械加工工艺手册》得铸件机械加工余量见表2-1,2-2。
表2-1毛坯零件圆柱面机械加工余量
基本尺寸(mm)
加工余量(mm)
附注
φ40
3.0
双侧
φ50
3.0
双侧
φ52
3.0
双侧
φ55
3.0
双侧
φ45
3.0
双侧
表2-2零件各端面的加工余量
基本尺寸(mm)
加工余量(mm)
附注
290(两外端面)
5
单侧
31.95(齿顶平面到连杆轴颈中心线长)
2
单侧
下面分别对铣、车、磨三种加工方法列出加工工序尺寸及方差的计算(每种加工方法只列出一道工序)。
表2-3铣两端面加工余量(单位:
mm)
工序名称
工序基本余量
经济精度IT
工序基本尺寸
工序尺寸及偏差
精铣
1.0
IT9(0.13)
290
290
+0.065
-0.065
粗铣
4.0
IT11(0.32)
290+1=291
291
+0.32
0
毛坯
5.0
IT14(1.3)
291+4=295
295±0.65
表2-4车长头主轴颈外圆(单位:
mm)
工序名称
工序基本余量
经济精度IT
工序基本尺寸
工序尺寸及偏差
(粗、精)磨削
0.6
IT6(0.019)
55
φ55
+0.021
+0.002
精车
0.6
IT9(0.074)
55+0.6=55.6
φ55.6
0
-0.074
粗车
1.8
IT11(0.19)
55.6+0.6=56.2
φ56.2
0
-0.19
毛坯
3.0
IT14(0.74)
56.2+1.8=58
φ58±0.37
表2-5磨连杆轴颈外圆(单位:
mm)
工序名称
工序基本余量
经济精度IT
工序基本尺寸
工序尺寸及偏差
精磨
0.2
IT6(0.016)
45
φ45
-0.040
-0.056
半精磨
0.4
IT8(0.039)
45+0.2=45.2
φ45.2
0
-0.039
粗磨
0.5
IT10(0.1)
45.2+0.4=45.6
φ45.6
0
-0.1
(粗、精)车
1.9
IT11(0.16)
45.6+0.5=46.1
φ46.1
0
-0.16
毛坯
3.0
IT14(0.62)
46.1+1.9=48
φ48±0.31
综合考虑与零件的结构形状与外形尺寸、生产类型、生产条件及各工序的加工余量,初步的确定其毛坯图如图2-2所示。
图2-2
2、主要切削用量的确定
在选择切削用量时,要综合考虑切削过程的质量、生产率和成本等问题。
合理的切削用量指在充分利用刀具和切削性能和机床性能(功率、转矩),以保证工件的加工质量的前提下,能获得高的生产率和低的加工成本的切削用量。
选择切削用量的原则是在机床、刀具、工件的强度以及工艺系统刚性允许的条件下,首先选择尽可能大的背吃刀量asp,其次选择在加工条件和加工要求限制下允许的进给量f,最后再按刀具寿命的要求确定一个合适的切削速度vc。
查《组合机床设计》2-16得硬质合金端铣刀的铣削用量:
加工材料
工序
铣削深度(mm)
铣削速度(m/min)
每齿走刀量
S齿(mm/z)
铸铁
粗铣
2~5
50~80
0.2~0.4
精铣
0.5~1
80~130
0.05~0.2
由表2-3可知,粗铣深度为4mm,精铣为1mm。
所以初选粗铣时,铣削速度65m/min,每齿走刀量0.2mm/z。
精铣时,铣削速度110m/min,每齿走刀量0.1mm/z。
查《机械加工工艺手册》选择铣刀类型为YG6。
(1)粗铣时:
ap=4,每齿进给量fz=0.2
查《切削用量简明手册》表3.7,铣刀刀齿后刀面最大磨损量为1.3。
查表3.1得铣刀直径d0=125mm,表3.8得刀具寿命T=180min。
查表3.16得YG6硬质合金端铣刀的切削用量vt=68m/min,nt=175r/min,vft=461mm/min。
修正系数Kmv=1.0
Knv=0.8
所以,Vc=vt×Kmv×Knv=68×1.0×0.8=54.4m/min
n=nt×Kmv×Knv=175×1.0×0.8=140r/min
vf=vft×Kmv×Knv=461×1.0×0.8=368.8mm/min
基本工时
式中:
L=l+y+Δ,l=53mm,y+Δ由《切削用量简明手册》表3.26不对称铣得入切量及超切量y+Δ=40mm。
计算tm=0.25min
(2)精铣时:
ap=1,每齿进给量fz=0.1
查《切削用量简明手册》表3.7,铣刀刀齿后刀面最大磨损量为0.5。
查表3.1得铣刀直径d0=125mm,表3.8得刀具寿命T=180min。
查表3.16得YG6硬质合金端铣刀的切削用量vt=124m/min,nt=315r/min,vft=304mm/min。
修正系数Kmv=1.0
Knv=0.8
所以,Vc=vt×Kmv×Knv=124×1.0×0.8=99.2m/min
n=nt×Kmv×Knv=315×1.0×0.8=252r/min
vf=vft×Kmv×Knv=304×1.0×0.8=243.2mm/min
基本工时
式中:
L=l+y+Δ,l=53mm,y+Δ由《切削用量简明手册》表3.26不对称铣得入切量及超切量y+Δ=40mm。
计算tm=0.38min
查《组合机床设计》表2-7得,高速钢钻头加工铸铁的切削用量:
加工直径(mm)
HB=160~200
HB=200~241
v(m/min)
S转(mm/s)
v(m/min)
S转(mm/s)
6~12
16~24
0.12~0.2
10~18
0.1~0.18
刀具选择中心钻。
钻孔直径d=6.3mm,钻孔深度为13mm。
(1)确定进给量
1按加工要求决定进给量:
根据《切削用量简明手册》表2.7,铸件硬度为240~190HB(初定220HB),加工精度为H12~H13,d=6.3mm时,f=0.22~0.26mm/r。
孔深l/d<8,不需修正。
2按钻头要求决定进给量:
根据《切削用量简明手册》表2.8,当铸铁硬度大于213HB,d=6.3mm,钻头所允许的进给量f=0.57mm/r(差除法算得)。
综合考虑两种条件下的进给量,选择进给量为0.24mm/r。
(2)确定钻头磨钝标准及寿命
由《切削用量简明手册》表2.12可知,当d=6.3mm时,钻头后刀面最大磨损量为0.5~0.8,寿命T=35min。
(3)切削速度的确定
由《切削用量简明手册》表2.15可知,当f=0.24mm/r时,vt=13.6m/min(差除法)。
根据表2.31查的修正系数
KTv=1.0
Kcv=1.0
Klv=0.85
Ktv=1.0
故,v=vt×Kv=13.6×1.0×1.0×0.85×1.0=11.56m/min
=
=584.4r/min
(4)基本工时的计算
式中:
L=l+y+Δ,l=13mm,y+Δ由《切削用量简明手册》表2.29查得入切量及超切量y+Δ=3.15mm(差除法)。
nf=n×f=140.2,故tm=0.12min。
3、切削力、力矩和功率的计算
(1)铣削时,铣削力、力矩及功率的计算。
根据《机械加工工艺手册》铣削、锯削加工单行本可查:
圆周铣削力
扭矩
功率
查手册表2.1-78可知:
CF=534
xF=0.9
yF=0.74
uF=1.0
wF=0
qF=1.0
查表2.1-79
(2)得kFc=1.