材料成型及控制工程毕业设计摩托车油箱注油口冲压.docx
《材料成型及控制工程毕业设计摩托车油箱注油口冲压.docx》由会员分享,可在线阅读,更多相关《材料成型及控制工程毕业设计摩托车油箱注油口冲压.docx(29页珍藏版)》请在冰豆网上搜索。
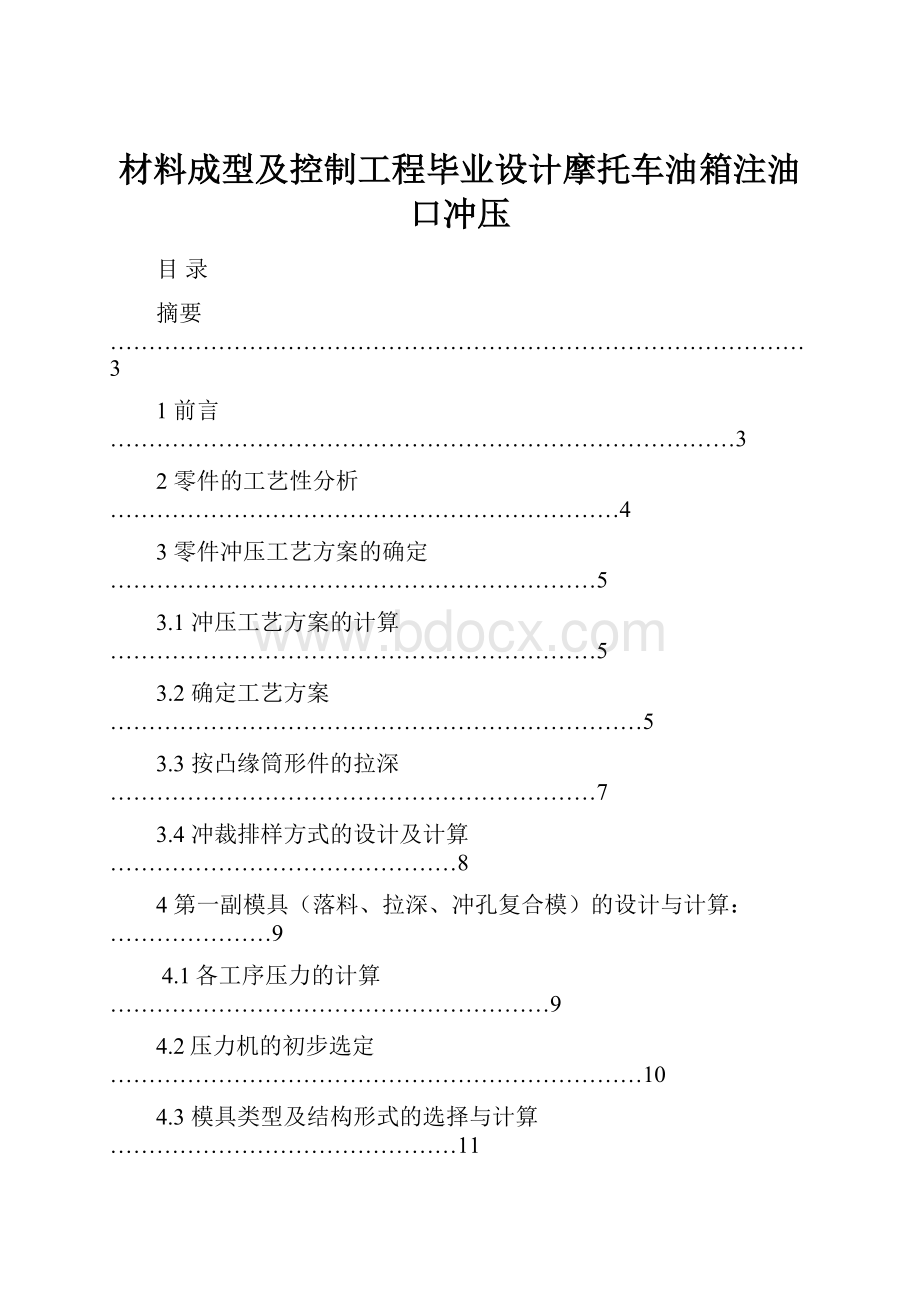
材料成型及控制工程毕业设计摩托车油箱注油口冲压
目录
摘要………………………………………………………………………………3
1前言………………………………………………………………………3
2零件的工艺性分析…………………………………………………………4
3零件冲压工艺方案的确定………………………………………………………5
3.1冲压工艺方案的计算………………………………………………………5
3.2确定工艺方案……………………………………………………………5
3.3按凸缘筒形件的拉深………………………………………………………7
3.4冲裁排样方式的设计及计算………………………………………8
4第一副模具(落料、拉深、冲孔复合模)的设计与计算:
…………………9
4.1各工序压力的计算…………………………………………………9
4.2压力机的初步选定……………………………………………………………10
4.3模具类型及结构形式的选择与计算………………………………………11
4.4模具工作部分刃口尺寸和公差的计算………………………………12
4.4.1落料凸、凹模的刃口尺寸…………………………………………12
4.4.2拉深凸、凹模的刃口尺寸…………………………………………13
4.4.3冲孔凸、凹模刃口尺寸的计算……………………………………14
4.5落料、拉深凸、凹模高度的确定……………………………………………14
4.6落料凹模外形尺寸的设计与粗略计算……………………………………15
4.7模具其他零件的设计与计算………………………………………………15
4.7.1模架的选用………………………………………………………15
4.7.2定位零件…………………………………………………………16
4.7.3卸料与推(顶)件装置……………………………………………16
4.7.4固定与连接零件…………………………………………………16
4.8模具压力中心的设计与计算…………………………………………………16
5第二副模具(翻边模)的设计与计算…………………………………16
5.1各工序压力的计算与压力机的初步选用……………………………………16
5.2压力机的初步选用……………………………………………………………17
5.3翻边凸、凹模刃口尺寸和公差的计算………………………………………18
5.4模具结构类型及形式的选择与设计…………………………………………19
5.5压力中心的计算……………………………………………………………19
5.6冲模闭合高度的计算…………………………………………………19
5.7模座的选用………………………………………………………………19
6第三副模具(垂直切边模)的设计与计算………………………………20
6.1各工序压力的计算与压力机的初步选用……………………………………20
6.2切边凸凹模刃口尺寸和公差……………………………………………21
6.3模具结构类型及形式的选择与设计……………………………………22
6.3压力中心的计算……………………………………………………………22
6.4冲模闭合高度的计算………………………………………………………22
6.5模座的选用……………………………………………………………22
心得与体会………………………………………………………………………23
致谢词……………………………………………………………………………24
参考文献…………………………………………………………………………24
摘要
本次毕业设计是完成摩托车油箱注油口冲压工艺及模具设计。
采用落料、拉深、冲孔、翻边、切边工艺。
设计中分析了工件的冲压工艺性,计算了毛坯排样、冲压力、刃口尺寸计算等。
进行了模具总体结构、主要零部件的设计,绘制了落料、拉深、冲孔复合模和翻边、切边的单工序模具装配图和零部件图。
关键词:
冲压工艺冲压模具设计装配图
Abstract:
Themainprogramforthisgraduationdesignistofinishpressprocessandthedesignofmotorcycletankpouringorifice.Thepressprocessofblanking,drawing,perforating,flaring,trimmingareadopted.Inthispaper,theprocesssuitabilityofpartisanalysed.Theprocessparameters,suchasblanklayoutandpressforcearecalculated.Thegeneralconstructionofmoldandmainpartsaredesigned.Thecompounddieofblanking,drawing,perforatingandthesimplepresstoolofflaring,trimminganddetaildrawingsofmainpartsaredrawn.
Keywords:
PressprocessPresstooldesignassemblydiagram
1前言
随着经济的发展,冲压技术应用应用范围越来越广泛,在国民经济各部门中,几乎都有冲压加工生产,它不仅与整个机械行业密切相关,而且与人们的生活紧密相连。
冲压工艺与冲压设备正在不断地发展,特别是精密冲压。
高速冲压、多工位自动冲压以及液压成形、超塑性冲压等各种冲压工艺的迅速发展,把冲压的技术水平提高到了一个新高度。
新型模具材料的采用和钢结合金、硬质合金模具的推广,模具各种表面处理技术的发展,冲压设备和模具结构的改善及精度的提高,显著地延长了模具的寿命和扩大了冲压加工的工艺范围。
由于冲压工艺具有生产效率高、质量稳定、成本低以及可加工复杂形状工件等一系列优点,在机械、汽车、轻工、国防、电机电器、家用电器,以及日常生活用品等行业应用非常广泛,占有十分重要的地位。
随着工业产品的不断发展和生产技术水平的不断提高,冲压模具作为个部门的重要基础工艺装备将起到越来越大的作用。
2工件的冲压工艺分析
本次毕业设计的冲压件是摩托车油箱注油口冲压件的生产过程的设计。
该工件是一个带凸缘的筒形件,在
53mm的内孔中,用来注油要求有较高的光洁度和相对的位置精度。
除了要保证它的公差外还要保证它的高度及其孔内的圆角半径R5mm。
从以上对摩托车油箱注油口的形状分析当中不难看出,它需要经过落料,拉深,冲预制孔,翻边,修边等冲压工序,但它需要几次拉深,冲预制孔、翻边尺寸如何计算以及冲侧孔应该采用哪种方式和如何布置等成为本次设计的重点和难点。
本次设计的模具精度并不需要很高,达到IT10-IT9均可满足要求。
工件图见图2-1。
图2-1摩托车油箱注油口工件图
3零件冲压工艺方案的确定
3.1工件孔冲制的方案
此件虽然是一般带凸缘拉深件,但加工底部
53mm孔可以有多种方案:
方案一:
拉深后再车去底部
方案二:
拉深后再冲去底部
方案三:
拉深后冲预制孔再翻边
a落料、拉深复合,再冲孔、翻边复合
b落料、拉深、冲孔复合,再翻边
在上述三种加工方案中,采用第一种方案,工件的质量较高,但生产率低,而且费料。
在工件底部要求不高的情况下,不适宜采用。
第二种方案需要增加整形工序,而且质量不易保证。
采用第三种方案中,a方案冲孔、翻边复合将使翻边凸模的厚度太薄,加工较麻烦,而且可能造成强度不够等缺点。
b可以避免a中的缺点且生产率高,而且省料。
另外,按工件使用情况翻边工序完全可以保证工件技术要求。
所以采用第三种方案中的b较合理。
3.2计算毛坯尺寸
在计算毛坯尺寸前,需要先确定翻边前的半成品的形状和尺寸。
孔
53的高度太大,不能用翻边的办法全部都制造出来,而是一部分要靠拉深形成的。
翻边高度具体计算如下:
将直径D=54mm,翻边圆角半径r=5mm,板料厚度t=1.0mm带入翻
边系数公式得:
K
=1-
(H-0.43r-0.72t)
=1-
(26-0.43×6-0.72×1)
=0.16
则预制孔径d=0.16×54=8.6
从表6-5查得翻边系数K
=0.51(采用平底凸模冲制底孔),即计算翻边系数大于表中查得的翻遍系数,说明不能一次翻边而成。
取极限翻边系数K0max=0.52
翻边极限高度
hmax=
(1-K
)+0.57(r+
)
=
(1-0.52)+0.57(5+0.5)
=16.95mm
取翻边高度为h=15mm
冲预制孔径:
d=
m×D=0.52×54=28.08
冲预制孔为d=28mm
冲孔、翻边前半成品如图3-1所示。
图3-1计算毛坯尺寸用图
3.3按凸缘筒形件的拉深
确定修边余量
值:
=
=2>1.40查表5-12得
=3.0mm
所以拉深件实际凸缘直径:
dF=dt+2
=108+2×3.0=114mm
计算毛坯直径:
当r=R时毛坯直径d0=
=
=119mm
确定能否一次拉深成形:
由相对凸缘直径和相对毛坯厚度查表
=
=2.11
=
×100=0.84
查表5-14得【h1/d1】max=0.27~0.33
而实际零件h/d=11/54=0.2<【h1/d1】max=0.27~0.33
查表5-13得m1=0.42
而且m=d1/d0=54/119=0.45>0.42故此件能一次拉深
摩托车油箱注油口拉深件毛坯尺寸计算如图3-2所示。
图3-2拉深件尺寸计算
3.4冲裁排样方式的设计及计算
工件毛坯直径
119mm尺寸较大,考虑到操作方便,采用单排。
查有关表得搭边值:
a=1.5,a1=1.5
进距:
s=D+a1=119+1.5=120.5
条料宽度:
b=D+2a=119+2×1.5=122mm
板料规格拟选用:
1×1100×2900
采用纵裁:
裁板条数n1=B/b=1100/122=9余2mm
每条个数n2=(L-a1)/s=(2900-1.5)/120.5=24余13mm
每板总个数n3=n1·n2=9×24=216(个)
板的利用率:
η=
×100%=71.1%
采用横裁:
裁板条数n1=L/b=2900/122=23余94mm
每条个数n2=(B-a1)/s=(1100-1.5)/120.5=9余28mm
每板总个数n3=n1·n2=23×9=207(个)
板的利用率:
η=
×100%=68.1%
综上比较第一种排样方式的利用率高,故采用进行纵裁排样(排样图见图3-3)
图3-3排样图
4第一副模具(落料、拉深、冲孔复合模)的设计与计算
4.1各工序压力的计算
落料力P1=1.3×3.14×D×t×τb
=1.3×3.14×119×1×350
=170015.5N
式中τb(抗剪强度)=350MPa,由《冲压手册》表8-7查得。
P1(=∏Dtτb)——计算冲裁力
D——毛坯直径
t——冲件材料厚度
卸料力P2=K1P1
=0.07×170015.5
=11901N
式中:
K1=0.07,由《冲压手册》表2-37查得。
拉深力P3=3.14×d×t×σbK1
=3.14×54×1×450×1.05
=80117N
式中:
σcp=450MPa,由《冲压手册》表8-7查得。
K1=10.5,由《冲压手册》表4-86查得。
压边力P4=∏/4[d02-(d1+2r)2×2.5
=∏/4[1192-(54+2×5)2]×2.5
=19752.6N
冲预制孔的力
F冲=1.3∏dtτb
=1.3×3.14×28×1×350
=40003.6N
式中:
τb(抗剪强度)=350MPa,由《冲压手册》表8-7查得,
d——预制孔直径
推件力
F推=n.K2F冲
=5×0.055×40003.6
=11000.99N
式中:
K2=0.063,由《冲压手册》表2-37查得。
N=5,同时卡在凹模里的废料片数。
(设凹模直筒口径高度h=4㎜,n=h/t=4/0.5=8)
4.2压力机的初步选用
综上计算所知,因为选用的是弹性卸料结构,所以总压力F总为各力的总和,其中包括卸料力.故
F总=P1+P2+P4+F冲+F推件
=170015.5+11901+19752.6+40003.6+11000.99
=242673.69N
≈243KN
在考虑各因素后,取一安全系数0.7左右,所以必须选用250KN的公称压力机.则根据所需总压力初选公称压力为250KN的开式压力机。
(参看《冲压手册》相关章节543页。
压力机的主要技术参数如下表4-1所示
表4-1压力机的主要技术参数
公称压力
滑块行程/㎜
行程次数/min-1
最大闭合高度/㎜
250
80
100
250
封高度调节量
㎜
工作台
模柄孔尺寸
前后㎜
左右㎜
直径㎜
深度
㎜
70
360
560
50
70
4.3模具类型及结构形式的选择与计算
本次设计第一副模具采用落料、拉深、冲孔的复合模结构。
本次设计的冲压件可一次拉深到所要求的高度,原则上属于浅拉深凸缘形件,落料、拉深、冲孔复合模采用典型结构,即落料、冲孔采用正装式,拉深采用倒装式。
下模座的压边圈兼作压边和顶件装置,另设刚性推件装置。
该结构的优点是操作方便,出件畅通无阻,生产率高。
适合于拉深深度不太大,材料较薄的情况。
在上模部分,为了不让工件底部变形,使其不让刚性接触,采用了连接推杆装置来推动推件块来推出工件。
对于此工序,由于拉深深度为11㎜,不算太大,材料厚度为1㎜较薄,因此采用弹性卸料较合适。
另外在下模座下部设有气垫装置,它驱动托杆向上运动,使压边圈兼做顶件和压边的作用,且在上模上设有刚性推件装置,并在下模上设有刚性卸料板装置,采用这些结构的特点主要是结构紧凑,布局合理且制造使用都简单方便,唯一的不足是,拉深件有可能留在刚性卸料板内不易出件,有时还需要工人用手工去把它拿出,带来了操作的不便,但是只要托杆长度设计合理,气垫压力足够,就能克服这点不足。
另外考虑到装模和操作方便,模具采用后侧布置导柱的模架。
第一副模具(落料、拉深、冲孔复合模)装配简图如图4-1所示
图4-1落料、拉深、冲孔复合模装配简图
4.4模具工作部分刃口尺寸和公差的计算
4.4.1落料凸、凹模的刃口尺寸
圆形凸模和凹模可采用分开加工。
落料前的毛坯未注公差尺寸的极限偏差,故取落料件的尺寸公差为
Ф119
㎜
由《冲压手册》表2-31的公式进行计算
D凹=(D-x△)+δ凹
=(119-0.5×(-0.87))
=119.44
式中:
x=0.5,由《冲压手册》表2-30查得,
δ凹=+0.035,由《冲压手册》表2-28查得。
D凸=(D-x△-2Cmin)-
=(119-0.5×(-0.87)-2×0.07)
=119.37
式中:
Cmin=0.07,由《冲压手册》表2-25查得,表查得Cmax=0.1)
δ凸=-0.025,由《冲压手册》表2-25查得。
+
=0.035+0.025=0.06<=2(Cmax-Cmin)t
=2×(0.1-0.07)
=0.06㎜
故上述计算是合理的。
落料凹模最小模壁c,由《冲压手册》表2-39查得为36㎜,实际取为36㎜
4.4.2拉深凸、凹模的刃口尺寸
拉深件按未注公差尺寸的极限偏差考虑,并标注内形尺寸,故拉深件的尺寸为
Ф53
㎜
由《冲压手册》表4-75的公式计算
d凸=(D+x△)-
=(53+0.4×0.74)
=53.3
式中:
x=0.4,由《冲压手册》表2-30查得
δ凹=+0.05由《冲压手册》表4-76查得
D凹=(D+x△+2C)+δ凹
=(53+0.4×0.74+2×1.05)
=55.4
式中:
x=0.4,由《冲压手册》表2-30查得,
c由《冲压手册》表4-74取为c=(1~1.1)t=1.05㎜
拉深凹模最小模壁c,由《冲压手册》表2-39查得为30㎜
4.4.3冲孔凸、凹模刃口尺寸的计算
冲孔件按未注公差尺寸的极限偏差考虑,并标注内形尺寸,故冲孔件的尺寸为Ф28
㎜
d凸=(d+x△)-
=(28+0.5×0.52)
=28.26
d凹=(d+x△+2Cmin)+δ凹
=(28+0.5×0.52+2×0.07)
=28.27
式中:
x=0.5,由《冲压手册》表2-30查得,
Cmin=0.07,由《冲压手册》表2-25查得,表查得Cmax=0.1)
δ凹=1/4△=0.021
4.5落料、拉深凸凹模高度的确定
L=h1+h2+h3+h
其中:
h1为凸模固定板厚度,一般为凸模高度的40%左右,计算取为28㎜。
h2为卸料板的厚度,查课本P23页一般为6~12㎜,取为10㎜。
h3为导料板厚度2㎜。
h为附加长度,包括修模余量和安全长度,取30㎜。
综上,则:
L=28+10+2+30
故:
L=70㎜
即凸凹模的长度为70㎜,具体长度根据实际情况调整后再确定。
4.6落料凹模外形尺寸的设计与粗略计算(具体情况根据装配图确定)
参见课本P63页图3-12:
凹模厚度h=Kb(大于15㎜),
凹模壁厚c=(1.5——2h)(大于30——40㎜)
其中:
b——冲裁件最大外形尺寸
K——系数,形状简单取较小值,形状复杂取较大值。
故根据课本P64页表3—3取K=0.20,
则:
查《冲压设计简明手册》P34页:
h=Kb=0.20x87=17.4(㎜)(但是本次模具不是落料单工序模,因此,落料凹模的对应尺寸应该比拉深凸模原则上高1个料厚t才可满足强度要求.但是在此模具设计,凹模里面还有卸料结构,根据作图得初h取25㎜)
凹模壁厚:
c=(1.5—2.5)h,取36㎜。
4.7模具其他零件的设计与计算
4.7.1模架的选用
根据落料凹模的周界尺寸,查《冲压手册》P591页相关资料,同时为了安装方便,故采用后侧导柱式模架.由于本次落料凹模的周界尺寸长度在200㎜左右,按资料中的LXB选用则上模座为200×200×50㎜,下模座为200×200×50㎜的规格,其他结构的尺寸值不变。
此时,再反过来校核所初步选用的压力为250KN的公称压力。
工作台尺寸:
左右为560㎜,前后360㎜。
工作台的闭合高度为250㎜,显然可以放下该模座,且最大闭合高度也满足要求,因此所选压力机符合要求。
则模柄的规格为直径50,高70㎜,其它结构的尺寸参见《冲压简明手册》P436页,与此同时,在模座确定以后,导柱,导套的规格和结构尺寸也随之确定下来由《冲压简明手册》相关章节查得。
4.7.2定位零件
本副模具采用两个导料销导向送料,为使条料顺利通过导料销的间隙,在计算排样尺寸图时一并算出,此处不在叙述。
结构和规格与挡料销相同。
同时在本副模具中采用固定挡料销来限制条料的送近步距,使用圆形挡料销,规格为Φ4×6。
该结构的挡料结构简单,制造容易,使用方便,适用于固定卸料板及手工送料的冷冲模结构。
4.7.3卸料与推(顶)件装置
由于板料厚度为1㎜〉0.8mm,故要采用固定卸料板结构,其结构简单,卸料力大,用于板料厚度较薄的情况。
卸料力前面已算出F卸=11901N
采用带导尺的固定卸料板,卸料板只起卸料的作用,卸料板的型孔与凸模的单面间隙为0.5㎜,厚度为10㎜。
打杆长度:
H>(模柄总长+凸凹模高度-推件高度)
但是由于使用了三爪推板推出机构,因此打杆长度应在(模柄总长-推板厚度)具体情况根据装配图确定。
托杆长度:
L>(l+h3)
其中:
l——气垫长度
h3——气垫上平面与下平面之间隙
综上,取L=48㎜。
4.7.4固定与连接零件
采用固定板将凸凹模固定在上模座上,固定板与凸凹模之间采用阶梯固定的形式。
固定板与上模座之间采用内六角螺钉与圆柱销来连接和定位,螺钉尺寸与圆柱销尺寸根据被连接的两部分零件厚度来确定。
此外,由于本副模具的尺寸所需冲裁力较大,因此采用垫板的结构。
4.8模具压力中心的设计与计算
由于落料,拉深和冲预制孔的凸,凹模形状均为对称性形状,因此其压力中心均为其各自的几何形心,故以模座中心为原点,建立直角坐标系,则落料和拉深的压力中心均在原点上。
5第二副模具(翻边模)的设计与计算
5.1计算冲裁力
翻边力
F翻边=1.1∏t(D-d0)σs
=1.1×3.14×1×(54-28)×196
=17602N
式中:
σs=196MPa,由《冲压手册》表8-7查得。
顶件力
顶件力取翻边力的10%,则
F顶件=10%×F翻边
=10%×17602
=1760N
5.2压力机的初步选用
综上计算所知,因为选用的是弹性卸料结构,所以总压力F总为各力的总和,其中包括卸料力.故
F总=F翻边+F顶件
=17602+1760
=19362N
≈20KN
在考虑各因素后,取一安全系数0.7左右,所以必须选用大于20KN的公称压力机.则根据所需总压力初选公称压力为160KN的开式压力机。
(参看《冲压手册》相关章节543页。
第二副模具(翻边模)装配简图见图5-1所示。
图5-1翻边模装配简图
5.3翻边凸、凹模刃口尺寸的计算
从模具装配图的设计中知道,翻边凸模基本尺寸为Ф53㎜。
翻边件按未注公差尺寸的极限偏差考虑,并标注内形尺寸,故翻边件的尺寸为Ф53
㎜
由《冲压手册》表4-75的公式计算
d凸=(D+x△)-
=(53+0.4×0.74)
=53.3
式中:
x=0.4,由《冲压手册》表2-30查得,
δ凹=+0.05由《冲压手册》表4-76查得
D凹=(D+x△+2C)+δ凹
=(53+0.4×0.74+2×1.05)
=55.4
式中:
x=0.4,由《冲压手册》表2-30查得,
c由《冲压手册》表4-74取为c=(1~1.1)t=1.05㎜
翻边凹模最小模壁c,由《冲压手册》表2-39查得为36㎜
5.4模具结构形式的选择计算
本副模具主要目的是为了翻边工序,翻边高度为11mm.翻边所需求的精度比较高,故在本次翻边模具的设计中,翻边模的精度为中等精度要求。
在本副翻边模的设计中,翻边凹模设计在上模座上。
预先拉深后的带凸缘筒形件也放在上模座上,然后利用固定板固定,而固定板利用内六角螺钉和圆柱销钉将其连接与紧固在上模座上。
卸料时,上模采推件块推件的方式将坯料从