三菱FX2N微型可编程控制器对CK9930机床的电气控制部分的改造设计.docx
《三菱FX2N微型可编程控制器对CK9930机床的电气控制部分的改造设计.docx》由会员分享,可在线阅读,更多相关《三菱FX2N微型可编程控制器对CK9930机床的电气控制部分的改造设计.docx(40页珍藏版)》请在冰豆网上搜索。
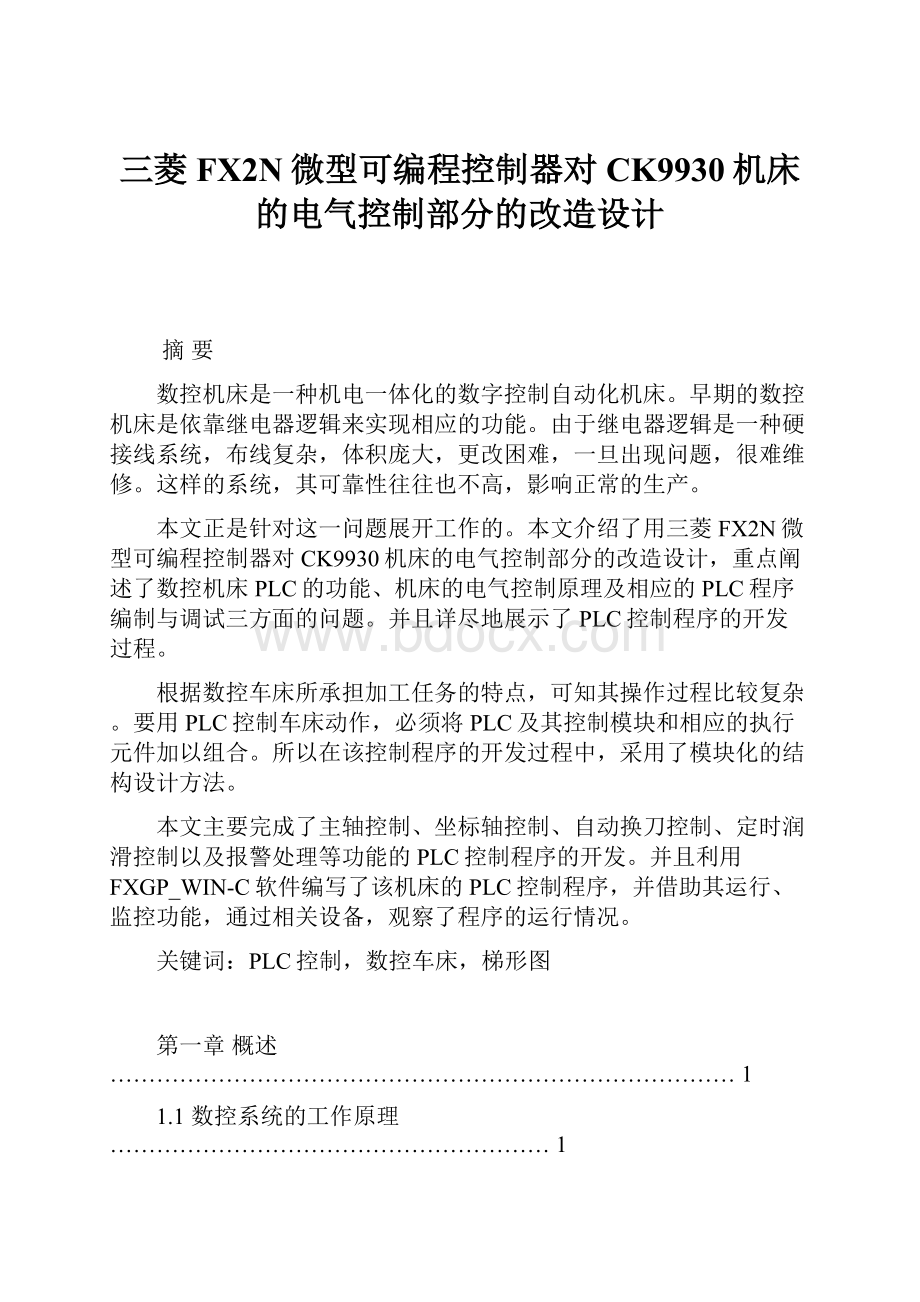
三菱FX2N微型可编程控制器对CK9930机床的电气控制部分的改造设计
摘要
数控机床是一种机电一体化的数字控制自动化机床。
早期的数控机床是依靠继电器逻辑来实现相应的功能。
由于继电器逻辑是一种硬接线系统,布线复杂,体积庞大,更改困难,一旦出现问题,很难维修。
这样的系统,其可靠性往往也不高,影响正常的生产。
本文正是针对这一问题展开工作的。
本文介绍了用三菱FX2N微型可编程控制器对CK9930机床的电气控制部分的改造设计,重点阐述了数控机床PLC的功能、机床的电气控制原理及相应的PLC程序编制与调试三方面的问题。
并且详尽地展示了PLC控制程序的开发过程。
根据数控车床所承担加工任务的特点,可知其操作过程比较复杂。
要用PLC控制车床动作,必须将PLC及其控制模块和相应的执行元件加以组合。
所以在该控制程序的开发过程中,采用了模块化的结构设计方法。
本文主要完成了主轴控制、坐标轴控制、自动换刀控制、定时润滑控制以及报警处理等功能的PLC控制程序的开发。
并且利用FXGP_WIN-C软件编写了该机床的PLC控制程序,并借助其运行、监控功能,通过相关设备,观察了程序的运行情况。
关键词:
PLC控制,数控车床,梯形图
第一章概述………………………………………………………………………1
1.1数控系统的工作原理…………………………………………………1
1.1.1数控系统的组成…………………………………………………1
1.1.2数控系统的工作原理……………………………………………2
1.2PLC的硬件与工作原理………………………………………………3
1.2.1PLC的简介………………………………………………………3
1.2.2PLC的基本结构…………………………………………………3
1.2.3PLC的工作原理…………………………………………………4
第二章数控车床的PLC…………………………………………………………5
2.1数控车床PLC的信息传递………………………………………………5
2.2数控车床中PLC的功能…………………………………………………6
2.2.1PLC对辅助功能的处理…………………………………………6
2.2.2PLC的控制对象…………………………………………………6
2.3用PLC实现车床电气控制系统的功能…………………………………7
2.4利用PLC代替继电器—接触器控制方式的优越性…………………8
第三章CK9930数控车床电气控制分析………………………………………9
3.1车床主要结构和运动方式……………………………………………9
3.2车床对电气控制的要求………………………………………………9
3.3车床的电气控制电路分析……………………………………………10
3.3.1主电路分析……………………………………………………11
3.3.2控制电路分析…………………………………………………11
第四章PLC控制程序的设计……………………………………………………12
4.1PLC程序设计方法……………………………………………………12
4.1.1PLC的程序设计步骤……………………………………………12
4.2PLC程序的模块化设计…………………………………………12
4.3输入输出分配………………………………………………………12
4.4梯形图程序设计………………………………………………………15
4.4.1梯形图总体框图………………………………………………15
4.4.2公用程序………………………………………………………16
4.4.3回原点程序……………………………………………………16
4.4.4主轴控制程序…………………………………………………17
4.4.5坐标轴控制程序………………………………………………17
4.4.6报警处理程序…………………………………………………18
4.4.7定时润滑控制程序……………………………………………18
4.4.8冷却程序………………………………………………………19
4.4.9自动换刀控制程序……………………………………………19
4.4.10需要说明的问题……………………………………………21
4.5梯形图程序的调试……………………………………………21
4.6本章小结……………………………………………………21
结论……………………………………………………………………………22
参考文献……………………………………………………………………………23
第1章概述
CK9930型数控车床配备的是华中I型数控系统,是一种比较老式的小型简易经济型数控系统。
随着数控技术的不断进步与发展,这一数控系统已不能满足加工要求,本课题就是对现有的CK9930数控车床所进行的改造项目的一个组成部分。
主要是车床电气控制部分进行改造。
车床电气控制系统是控制车床各部分的工作、协调完成车床加工任务的核心部分,它由大量继电器构成一个复杂的逻辑控制电路。
该车床复杂的继电器逻辑控制线路构成的电气控制系统故障率高,难于维护,很有必要对其进行改造,即用PLC代替继电器--接触器控制方式。
1.1数控系统的工作原理
国际信息处理联盟对数控机床做了如下定义定义:
数控机床是一种装有程序控制系统的机床,该系统能够逻辑地处理具有使用号码或其他符号编码指令规定的程序。
这里所说的程序控制系统就是数控系统(NumericalControl,简称NC)而现在的数控系统都是以计算机作为控制中心,所以称为计算机数控(ComputerizedNumericalControl,简称CNC)。
1.1.1数控系统的组成
CNC系统的一般结构如图1.1所示,CNC系统主要是指图中的CNC控制器,它是由计算机硬件、数控系统软件及相应的输入/输出接口构成的专用计算机和
可编程控制器所组成。
前者处理机床轨迹运动的数字控制,后者则处理开关量的逻辑控制。
图1-1CNC系统的一般结构框图
1.1.2数控系统的工作原理
虽然数控系统种类繁多,但其的基本原理都是相通的。
即都是通过运算器进行插补运算,然后对进给轴进行闭环控制,实现机床的数控功能。
(1)进给系统控制
进给系统的控制大多是通过控制步进电机来实现的。
步进电机是一种在外加电脉冲信号的作用下一步一步地运转,将电脉冲信号转换成相应角位移的机电元件。
其角位移量和输入脉冲的个数严格成正比,在时间上与输入同步,控制输入脉冲的数量、频率及电机绕组通电顺序,便可获得所需的转角、速度及转动方向;无脉冲输入时,在绕组电源的激励下,气隙磁场使转子保持原来的位置状态。
利用这一原理,便可实现加工时纵、横向的进给,并可获得较高精度。
(2)开关量控制
数控机床的开关量信号控制是通过PLC来完成的。
机床的各开关量可通过I/O口进行信息交换。
由于I/O口可输入信号和输出信号,其输出信号经过逻辑译码电路转换成多路的输出信号,可实现主轴电机、冷却泵及主轴变速等的控制;输入口可接受行程限位开关暂停、主轴同步脉冲、选刀回答等信号。
从而实现各种状态的检测,最终实现机床的各开关量控制。
(3)主轴控制
数控系统只对主轴系统进行开关控制。
数控装置通过PLC对主轴系统进行起停控制。
1.2PLC的硬件与工作原理
1.2.1PLC简介
可编程序控制器(ProgrammableController)简称PC,为了不与个人计算机(也简称PC)混淆,通常将可编程序控制器称为PLC。
它是在电器控制技术和计算机技术的基础上开发出来的,并逐渐发展成为以微处理器为核心,把自动化技术、计算机技术、通信技术融为一体的新型工业控制装置。
目前,PLC已被广泛应用于各种生产机械和生产过程的自动控制中,成为一种最重要、最普及、应用场合最多的工业控制装置,并被公认为现代工业自动化的三大支柱(PLC、机器人、CAD/CAM)之一。
与一般微机控制系统最大的区别是,PLC必须具有很强的抗干扰能力、广泛的适应能力和广阔的应用范围。
1.2.2PLC的基本结构
PLC也是由硬件系统和软件系统两大部分组成。
PLC硬件系统的基本结构如图1.2所示。
图1-2PLC的基本结构示意图
PLC的软件系统则包括系统软件和用户应用软件。
从广义上讲,可编程序控制器PLC实质上是一种专用工业控制计算机,只不过比一般的计算机具有更强的与工业过程相联接的接口,以及具有更直接的适用于工业控制要求的编程语言。
1.2.3PLC的工作原理
(1)PLC的工作过程
PLC上电后,就在系统程序的监控下,周而复始地按一定的顺序对系统内部的各种任务进行查询、判断和执行,这个过程实质上是按顺序循环扫描的过程。
执行一个循环扫描过程所需的时间称为扫描周期,其典型值为1~100ms。
PLC的工作过程如图1.3所示。
图1-3PLC的工作过程
(2)用户程序的循环扫描过程
PLC的工作过程与CPU的操作模式有关。
CPU有两个操作模式:
STOP模式和RUN模式。
在扫描周期内,STOP模式和RUN模式的主要差别是:
RUN模式下执行用户程序,而在STOP模式下不执行用户程序。
PLC对用户程序进行循环扫描可分为三个阶段进行,即输入采样阶段、程序执行阶段和输出刷新阶段。
第2章数控车床PLC
在数控车床中,位置控制是由位置控制器来实现的。
而其它的大部分动作即辅助机械动作的控制如主轴启停、换向,换刀控制、冷却和润滑系统的运行以及报警监测等功能则可由可编程控制器(PLC)来实现。
2.1数控车床PLC的信息传递
通过PLC来实现车床电气控制系统的各项功能,需要将各种控制和检测信号通过按钮和检测元件输入PLC,再通过PLC内部程序的运算将结果输出到各种执行设备,完成电气控制系统对于车床的控制。
所以就涉及PLC与数控装置、机床之间的信息交换。
可编程控制器与CNC机床的强电、CNC数控装置I/0口的联接可归纳为下列三部分:
(1)PLC输入输出端与机床面板信号联接
CNC数控机床操作面板上有按钮、旋钮开关和指示灯等,按钮、旋钮开关直接与可编程控制器的输入端接线柱相连,指示灯直接与PLC输出端接线柱相连。
(2)PLC输出端与机床强电信号联接
PLC在CNC机床中的主要作用是控制强电部分,如:
主控电源、伺服电源、刀架电机正转、润滑电机等。
每个电机的运行程序控制逻辑都固化在PLC中,受机床操作面板开关和数控系统软件的控制。
(3)PLC输入端与CNC机床数控装置I/O口的联接
可编程控制器输出端的通断是由其输入端通断状态及梯形图程序决定的,CNC机床数控装置与可编程控制器的联接是通过软开关直接控制PLC输入端的通断,以决定PLC输出端的状态。
从数控装置I/O口的信息流向分析,可以分为两种情况:
一是数控装置从I/O口输出指令,控制PLC完成相应的动作;另一种是检测PLC输入口的开关状态,数控装置的I/O口是输入信号,数控装置根据输入信号的性质做出相应的控制。
2.2数控车床中PLC的功能
2.2.1PLC对辅助功能的处理
目前,数控机床程序中,有关机床坐标系约定、准备功能、辅助功能、刀具功能及程序格式等方面己趋于统一,形成了统一的标准,即所谓的CNC机床ISO代码。
归纳起来有4种功能:
一种是准备功能,即所谓的G代码;第二种是辅助功能,即所谓的M代码;第三种是刀具功能,即所谓的T代码;第四种是转速功能即所谓的S代码。
其中,G功能主要与联动坐标轴驱动有关,是通过CPU控制数控装置的I/0接口实现;M功能主要控制机床强电部分,包括主轴换向、冷却液开关等功能;T功能与刀具的选择和补偿有关。
⑴M功能的处理
M指令主要有M02(程序停止)、M03(主轴顺时针旋转)、M04(主轴逆时针旋转)、M05(主轴停止)、M06(准备换刀)等。
其中一部分是由数控系统本身的硬件和软件来实现,还有一部分需要数控装置与PLC相结合来实现。
⑵T功能的处理
在PLC上实现的主要是刀具选择。
当遇到包含某个刀具编码的换刀指令时,对应的数控装置I/O口变成高电平,数控系统将T代码指令送给PLC,PLC经过译码指令进行译码后,检索刀号,然后控制换刀装置进行换刀。
⑶S功能的处理
S功能主要完成对主轴转速的控制,常用的有代码法和直接指定法。
代码法是S后面跟二位数字,这些数字不直接表示主轴转速的大小,而是机床主轴转速数列的序号;直接指定法是S后面直接就是主轴转速的大小,例如S1500表示主轴转速是1500r/min。
2.2.2PLC的控制对象
数控系统可以分为两部分:
控制伺服电动机和主轴电机动作的系统部分NC和控制辅助电气部分的PLC。
数控机床PLC主要完成数控机床的顺序控制,包括对NC、机床及操作面板传来的信号进行处理,实施急停及超程信号的监控,并且完成对主轴、刀架、冷却、润滑等功能的控制。
①操作信号处理
接收操作面板上的信号和NC部分传来的数控信号以控制数控系统的运行。
②主轴控制
控制主轴的启动、停止及正反转。
③坐标轴控制
控制坐标轴的伺服驱动及限位开关等。
④换刀控制
实现对程序换刀的控制。
⑤冷却控制
实现程序控制冷却的启动、停止。
⑥润滑控制
实现定时润滑的控制。
2.3用PLC实现车床电气控制系统的功能
从本质来讲,基于PLC的机床电气控制系统对机床的控制思路仍然与继电器-接触器控制系统是一致的。
只是在控制手段上采用了先进的控制设备。
PLC控制系统其优点在于根据加工工艺要求的不同相应的修改程序就可以实现。
车床电气控制系统属于广泛的应用系统,不针对特殊的加工工艺,因此PLC内部的程序只需要相对每个控制按钮发出的信号,做出相应的动作即可。
通过PLC来实现车床电气控制系统的各项功能,需要将各种控制和检测信号通过按钮和检测元件输入PLC,再通过PLC内部程序的运算将结果输出到各种执行设备,完成电气控制系统对于车床的控制。
每个功能的输入信号,都可以通过控制面板上的按钮进行操作,输出则可以通过接触器、电磁阀等执行机构完成。
基于PLC的车床电气控制系统功能分解如图2-1。
图2-1PLC车床控制系统分解图
2.4利用PLC代替继电器--接触器控制方式的优越性
⑴可维护性好采用PLC进行控制后,由于采用了专用芯片及集成电路,提高了集成度,减少了元器件数量,机床控制电路的接线量大为减少,故障率大大降低。
可维护性好,基本上无需维护。
⑵可靠性高PLC的平均无故障工作时间高达300000h(约34.2年),所以其可靠性高。
而采用继电器--接触器控制机床的控制则因为存在大量机械触点,工作电压和工作电流较大,可靠性较差。
⑶提高机床柔性当机床加工程序发生变化时,只需要修改PLC的程序就可以进行新的加工,更改较方便,机床的柔性很好。
⑷效价比高交流接触器的额定寿命约为800~1600h,远低于PLC,
再考虑到因更换坏掉的接触器所耽误的工时,从经济性的角度来看,用PLC也是很合算的(PLC价格与I/O点数成正比,而机床所要用的I/O点数并不多)。
⑸可联网通信由于PLC具有通信功能,采用可编程控制器进行机床改造后,可以与其它智能设备联网通信,在今后的进一步技术改造升级中,可根据需要联入工厂自动化网络中,提高工厂自动化水平。
第3章CK9930数控车床电气控制分析
数控车床主要用于轴类、盘类零件的加工,能自动完成外围柱面、内孔、锥面、圆弧面、螺纹等工序的粗细加工,并能在圆柱面或端面上进行铣槽、钻孔、铰孔等工作,可以实现回转体零件在预先加工好定位基面后,一次装夹下完成从毛坯到成品的全部工序.因此,能够极大地提高生产率。
3.1车床主要结构和运动形式
CK9930数控车床是为两轴车床。
床身最大工件回转直径300mm,最大工件长度500mm,刀架上最大工件回转直径140mm,外型尺寸1100mm×580mm×580mm。
其结构主要有床身、主轴变速箱、床鞍、卡盘、刀架、丝杠和尾架等组成。
其中,床身是一个整体的铸件。
刀架通过床鞍安置在床身的导轨上。
CK9930数控车床的运动形式有:
⑴主运动:
工件的旋转运动,是主轴通过卡盘带动工件旋转的运动形式。
⑵进给运动:
刀架的横向或纵向的直线运动。
3.2车床对电气控制的要求
车床工艺范围广,因而它的调速范围大、运动多。
其对电气控制的要求有:
①为适应各种工件加工工艺的要求,主轴应能在一定范围内调速,采用交流电动机驱动的齿轮变速系统。
②由于采用齿轮变速,为防止出现顶齿现象,要求主轴系统变速时作低速断续冲动。
③要求主轴能够实现正反转。
④电路应有必要的保护和联锁的措施。
3.3车床的电气控制电路分析
CK9930数控车床的电气原理图如图3-1所示。
图3-1CK9930数控车床电气原理图
3.3.1主电路分析
将三相电源经空气断路器Q1和Q2引入,单相电容运转主轴电动机M1用接触器KM3和KM4形成的互锁电路控制正反转。
变压器T1为X轴、Z轴步进电机驱动器提供AC55V供电电源;变压器T2为强电控制电路提供AC220V电源;变压器T3和整流电路为弱电控制电路和主控电路板提供DC24V供电电源。
3.3.2控制电路分析
(1)启动过程
启动时,合上Q1,引入三相电源。
按下启动按钮SB2,接触器KM1线圈通电吸合,则KM1的主触头闭合,电动机接通电源直接启动运行。
与此同时,在超程解除(X33)有效状况下闭合继电器RA2,且使X31有效(控制器收到主电路接通信号),则继电器RA1通电,RA1的触点闭合,接触器KM2线圈通电吸合,KM2的主触头闭合,为步进电机驱动器供电,且主轴电机也通电。
在控制面板上采用的是旋钮开关,拨到“开”的位置后能一直保持接通状态,从而使得KM1能够持续闭合,为控制电路供电。
(2)主轴正反转
该车床采用两个接触器KM3和KM4来实现对电动机的正、反转控制。
在电路中,为了防止两个接触器同时动作而造成短路,将实现正、反转的KM3和KM4进行互锁。
所以,电动机的正反转控制电路实际上是由互锁的两个方向相反的单向运行线路组成的。
其具体的控制过程如下:
继电器RA3闭合,RA3常闭触点断开。
1、接触器KM3闭合,KM4由互锁电路断开(即使RA4误动作也不会闭合),主轴电机正转。
2、继电器RA4闭合,RA4常闭触点断开。
3、接触器KM4闭合,KM3由互锁电路断开(即使RA4误动作也不会闭合),主轴电机反转。
正如上面所指出的那样,在该正反转控制电路中,两个接触器的常闭触头KM3和KM4互锁。
所以在进行电动机的换向操作时,必须先按下停止按钮才能反向启动。
(3)停止过程
按下急停按钮SB1,则继电器RA2断电,RA2的辅助触点断开,从而使得与之串联在一起的继电器RA1断电,RA1的辅助触点断开。
与RA1的触点串联的接触器KM2线圈断电,同时接触器KM1的触头也断开。
KM2线圈断电使步进电机断电。
KM2的触头也会随KM2线圈的断电而断开,则主轴控制电路断电。
KM1触头的断开也会使控制电路断电。
另外,若是行程开关接通,也会使继电器RA2断电,同理,整个控制电路也将会断电。
补充:
若为按下急停,X30有效,单片机控制电路无法正常启动;若为行程开关接通(206为高电平),X30无效,单片机控制电路可以正常启动,认知超程错误。
第4章PLC控制程序的设计
4.1PLC程序设计方法
4.1.1PLC的编程语言
国际电工委员会(IEC)于1994年5月公布了可编程序控制器语言标准(IEC61131-3),详细地说明了句法、语义和下述5种编程语言:
⑴顺序功能图(Seouentialfunctionchart);
⑵梯形图(Ladderdiagram);
⑶功能块图(Functionblockdiagram);
⑷指令表(Instructionlist);
⑸结构文本(Structuredtext)。
该标准中有两种图形语言——梯形图(LD)和功能块图(FBD),还有两种文字语言——指令表(IL)和结构文本(ST),顺序功能图(SFC)是一种结构块控制程序流程图。
[8]
其中,梯形图是使用的最多的图形编程语言,有PLC第一编程语言之称。
梯形图采用类似于继电器触点、线圈的图形符号,容易理解和掌握。
梯形图常被称为程序,梯形图的设计称为编程。
梯形图也很适合于开关量逻辑控制。
本文也采用梯形图进行程序的编制。
4.1.2PLC程序设计步骤
图4-1所示为PLC控制系统设计与调试的一般步骤。
-0
图4-1PLC控制系统设计与调试的一般步骤
4.2PLC程序的模块化设计
由于车床的操作过程复杂,机加工控制对象每一工作循环周期的控制关系比较复杂,因此,如果将各种控制程序“混合”在一起设计,则各程序间必然会相互“牵连”,从而使设计的难度成倍增大。
为此作者决定在PLC用户程序程序设计中,采用模块化设计思想,即对系统按照控制功能进行模块划分,将不同功能的程序放在不同的模块中设计,依次对各控制功能的模块设计梯形图。
这样,使得每一部分的程序都可以单独设计和修改,也就是说设计和修改某一部分程序时,不必担心会对另一部分程序造成影响。
程序结构清晰,便于调试,还可以根据需要灵活增加其他控制功能。
本次设计中,综合车床的特点,在开发该机床的PLC控制程序的过程中将PLC程序划分为7个模块,即公用程序模块、主轴模块、坐标轴控制模块、润滑控制模块、自动换刀模块、报警模块和冷却控制模块。
4.3输入输出分配
接下来就是编制I/O分配表。
I/O分配表是设计梯形图程序的基础资料之一,也是设计PLC控制系统时必须首先完成的工作,会给PLC系统软件设计和系统调试带来很多方便。
在编制I/O分配表时,同类型的输入点或输出点尽量集中在一起,连续分配。
本次程序开发所用I/O分配见表4-1所示。
表4-1输入输出设备与PLC输入输出端子分配一览表
输入端输出端
输入设备输入端子号输出输出端子号
旋钮开关X0—X13循环启动Y0
循环启动按钮X14进给保持Y1
进给保持按钮X15单段Y2
单段按钮X16机床锁住Y3
机床锁住按钮X17快进Y4
主轴正转按钮X20主轴正转Y5
主轴反转按钮X21主轴反转Y6
主轴停按钮X22主轴停Y7
X向退按钮X23X向退Y10
X向进按钮X24X向进Y11
Z向退按钮X25Z向退Y12
Z向进按钮X26Z向进Y13
快进按钮X27NC报警Y14
急停按钮X30超程报警Y15
超程解除按钮X33X回参考点Y16
Z正向行程开关X34Z回参考点Y17
Z反向行程开关X35进行润滑Y20
X正向行程开关X36润滑故障报警Y21
X反向行程开关X37换刀完成Y22
冷却开按钮X40刀架正转Y23
冷却关按钮X41驱动指示Y24
润滑电机起动按钮X42冷却开Y25
润滑油路压力继电器X43X轴驱动使能Y26
1~4号刀到位X44—X47Z轴驱动使