基于S7200PLC的自动配料控制系统设计.docx
《基于S7200PLC的自动配料控制系统设计.docx》由会员分享,可在线阅读,更多相关《基于S7200PLC的自动配料控制系统设计.docx(28页珍藏版)》请在冰豆网上搜索。
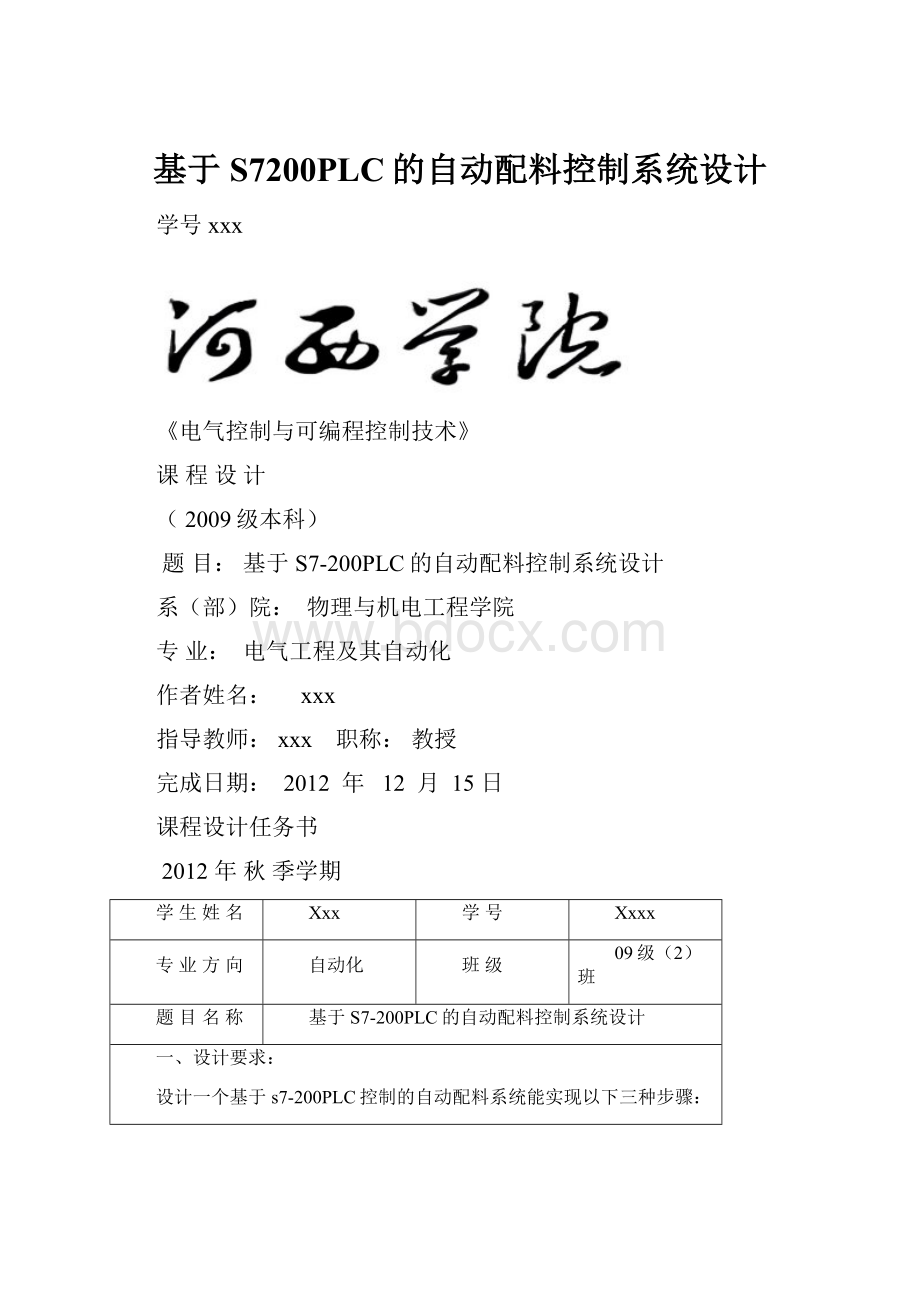
基于S7200PLC的自动配料控制系统设计
学号xxx
《电气控制与可编程控制技术》
课程设计
(2009级本科)
题目:
基于S7-200PLC的自动配料控制系统设计
系(部)院:
物理与机电工程学院
专业:
电气工程及其自动化
作者姓名:
xxx
指导教师:
xxx职称:
教授
完成日期:
2012年12月15日
课程设计任务书
2012年秋季学期
学生姓名
Xxx
学号
Xxxx
专业方向
自动化
班级
09级
(2)班
题目名称
基于S7-200PLC的自动配料控制系统设计
一、设计要求:
设计一个基于s7-200PLC控制的自动配料系统能实现以下三种步骤:
第一步:
根据两种料的比例,从A、B两处分别取料;
第二步:
将两种料进行混合;
第三步:
将配好的料进行自动装车。
二、设计的主要内容
根据控制要求,明确设计任务,应用所学的理论知识,拟定设计方案,如下设计:
1.完成控制系统的硬件设计,主要包括:
电气元件的选择、电气原理图设计、可编程控制器输入输出接线图设计及控制面板设计等。
2.完成控制梯形图的软件设计,主要包括:
控制程序流程图设计、梯形图程序设计及仿真调试。
3.完成课程设计说明书的撰写,主要包括:
封面、目录、设计任务书、设计总体思路、硬件设计、软件设计、总结体会、参考文献等。
三、设计进度安排
第一周星期一下达设计任务书,了解控制系统设计相关知识
星期二~星期四查阅文献资料,确定控制系统的总体设计方案,完成控制系统的硬件设计
星期五至第二周星期一~星期二完成控制系统的软件设计及调试
星期三~星期四撰写课程设计说明书
星期五答辩
指导教师签字:
一、引言
PLC的定义有许多种。
国际电工委员会(IEC)对PLC的定义是:
可编程控制器是一种数字运算操作的电子系统,专为在工业环境下应用而设计。
它采用可编程序的存贮器,用来在其内部存贮执行逻辑运算、顺序控制、定时、计数和算术运算等操作的指令,并通过数字的、模拟的输入和输出,控制各种类型的机械或生产过程。
可编程序控制器及其有关设备,都应按易于与工业控制系统形成一个整体,易于扩充其功能的原则设计。
PLC具有通信联网的功能,它使PLC与PLC之间、PLC与上位计算机以及其他智能设备之间能够交换信息,形成一个统一的整体,实现分散集中控制。
多数PLC具有RS-232接口,还有一些内置有支持各自通信协议的接口。
配料工人收到每天的生产作业表后,将依次对每种原料进行称重。根据配料的多少,先计算每种成分的重量,然后在各种成分的料桶中取料,送到电子称上进行称重,最后进行包装。在这个过程中工人工作繁重,出错率高,称重重量无监测,生产数据无纪录等不能保证企业的生产工艺。文中以PC机编程,可编程逻辑控制器(PLC),现场总线技术等现代工控技术为基础,开发了以PC机为上位机,以PLC作为下位机的自动配料系统。在整个生产过程中,一旦生产计划制定完成,计算机将按照计划对每种原料进行称重,不再需要人工来干预。在这个过程中工人只是进行取料,由计算机通过电子称发来的数据校核重量,减轻了工人的工作负担,提高了工作效率。
随着社会的不断发展,科学技术的不断进步,人们已经对越来越多的事物不是进行手工操作,而是进行人工智能控制。
例如智能机器人以及立体式储存仓库的生产等等,一改往日以前人们取料时间长,难度大,效率低等缺点。
本次课程设计题目自动配料系统也正是在这样的背景下应运而生的,本次课程设计的目的是掌握机电传动控制系统的基本原理PLC控制电路的设计方法以及继电器-接触器控制电路的PLC改造方法。
掌握机电传动控制系统中继电器-接触器控制和PLC控制的基本原理,设计方法及两者的关系。
掌握常用电器元件的选择方法。
具备一定的控制电路的分析能力与设计能力。
运用所学的可编程控制器的相关知识在实验电路板上实现小车的取料控制。
改变以往人工取料时间长,难度大,效率低的缺点。
提高工作效率,节省人力资源。
人们已经对越来越多的事物不是进行手工操作,而是进行人工智能控制。
正是在这样的科技大潮牵引下,我们所学的只是也越来越多和先进科技接轨了。
本次课程设计正是基于此种情况,其目的是为了实现小车自动取料。
二、设计目的
通过对自动配料系统PC-PLC控制系统的工作原理的分析、系统设计、编程、及上机调试工作的实践,了解电器控制系统的一般设计思路,熟悉和掌握外围电路系统和软件设计的方法,并掌握利用PC对PLC工作状况进行监控的方法。
三、设计任务及要求
3.1设计要求
图1设计实物图
如图1所示,配料车从配料罐O处出发,到A处取m车料,送回配料罐,再到B处取n车料,送回配料罐进行配料混合。
A处料和B处料的数量可以进行设定。
可以根据A处料和B处料配料的比例首先进行设定。
设定A料、B料相应的减计数器C0和C1。
当按下启动按钮时,配料车能根据A料和B料的设置比例,自动地从配料罐处开始,往返于A料和B料两地之间,取的所要的料后,停止在配料罐处。
然后,开始混合这两种料(通过搅拌电机来实现)。
搅拌时间为根据A料和B料总的数量的多少来设定。
搅拌时间(分钟)=(A料车数+B料车数)/2。
装车过程中,当汽车开进装车位置时,限位开关SQ1置为ON,启动电机M3,经过6s后,再启动启动M2,再经过6s最后启动M1,同时打开出料阀(D2亮),物料经料斗出料。
车装满时,限位开关SQ2为ON,料斗关闭,6s后M1停止,M2在M1停止6s后停止,M3在M2停止6s后最后停止。
汽车可以开走。
3.2设计任务
根据控制要求,明确设计任务,应用所学的理论知识,拟定设计方案,如下设计:
1.完成控制系统的硬件设计,主要包括:
电气元件的选择、电气原理图设计、可编程控制器输入输出接线图设计及控制面板设计等。
2.完成控制梯形图的软件设计,主要包括:
控制程序流程图设计、梯形图程序设计及仿真调试。
3.完成课程设计说明书的撰写,主要包括:
封面、目录、设计任务书、设计总体思路、硬件设计、软件设计、总结体会、参考文献等。
四、系统的电气原理图
图2小车电机正反转主电路设计
五、硬件外部接线图
5.1PLC的选型原则
1.最大限度地满足被控对象的控制要求
2.保证PLC控制系统安全可靠
3.力求简单、经济、使用及维修方便
4.适应发展的需要
5.2PLC选型
S7-200PLC它有四种不同的型号,由于本设计要求有15个输入点和10个输出点,因而选择S7-CPU226最为合适。
5.3PLC连线图
根据设计任务要求PLC主机的硬件接线图如图-3所示
图3PLC连线图
5.4I/O分配表
表1I/O分配表
输入信号(地址)
信号原件及作用
输出信号(地址)
控制对象及作用
I0.0
启动信号按钮SB1
Q0.0
电机1正转电磁线圈KM1
I0.1
停止信号按钮SB2
Q0.1
电机1反转电磁线圈KM2
I0.2
O点限位开关SQ1
Q0.2
装A料控制阀YV1
I0.3
A点限位开关SQ2
Q0.3
装B料控制阀YV2
I0.4
B点限位开关SQ3
Q0.4
卸料控制阀YV3
I0.5
小车的料位开关SQ4
Q0.5
配料罐搅拌机电磁线圈KM3
I0.6
A料手动按钮SB3
Q1.0
传送带M1电机电磁线圈KM4
I0.7
B料手动按钮SB4
Q1.1
传送带M2电机电磁线圈KM5
I1.0
传送带启动按钮SB5
Q1.2
传送带M3电机电磁线圈KM6
I1.1
传送带停止按钮SB6
Q1.3
配料罐下料口控制阀YV4
I1.2
传送带M1的故障端
CG1
M1的故障端
I1.3
传送带M2的故障端
CG2
M2的故障端
I1.4
传送带M3的故障端
CG3
M3的故障端
I1.5
汽车的限位开关SQ5
I1.6
汽车的料位开关SQ6
六、系统的程序设计
6.1程序设计的流程图
图3程序流程图
6.1程序设计梯形图
指令语句表见附录1。
七、系统仿真与调试
采用S7_200仿真对设计系统进行仿真及调试,采集的图如下图所示:
启动I0.1,小车卸料开关Q0.4打开,小车电机正转,离开O处,小车卸料开关Q0.4关闭,小车行驶A处。
小车行驶到A处,打开A处限位开关(I0.3),小车电机停止,A料控制开关(Q0.2)打开,小车接料。
当小车处装满时,小车料位开关(I0.5)闭合,关闭A料控制开关(Q0.2),小车电机反转。
到O处,小车停止,小车卸料开关Q0.4打开,开始卸料10s,小车料位开关(I0.5)打开,之后小车小车电机正转,离开O处,小车卸料开关Q0.4关闭,小车行驶A处。
以此循环装A料2次。
当A料运完后,小车小车电机正转,离开O处,经过A处限位开关(I0.3)小车无响应。
小车行驶到B处,打开B处限位开关(I0.4),小车电机停止,B料控制开关(Q0.3)打开,小车接料。
当小车处装满时,小车料位开关(I0.5)闭合,关闭B料控制开关(Q0.3),小车电机反转到O处卸料,以此循环装A料3次。
当B料运第3次到O处,闭合O处限位开关(I0.2),小车卸料十秒后,启动配料罐搅拌电机(Q0.5)搅拌。
启动传送带(I1.0)等待汽车装料。
当汽车到接料口处,汽车限位开关(I1.5),传送带逆序启动后,再打开配料罐控制开关(Q1.3),其中自动配料过程锁死,防止配料不均匀。
当汽车料满,汽车料位开关(I1.6)闭合,先关闭配料罐控制开关(Q1.3),在传送带顺序停止。
经电脑软件多次调试发现了一些问题,后面又进行了几次修改,最后的程序没有什么结构、语法等错误,最后能得出的结果是当输入是按下启动按钮1,输出则是小车自动向右运动;输入是O处限位开关电平时,输出卸料;输入A处限位开关时,输出装A料再向左运动;输入B处限位开关信号时,输出装B料再向左运动。
调试之后仿真的结果大致如上,满足课题的要求,所以该方案可行。
八、设计总结
通过本次论文设计,使我对PLC控制的知识有了更深层次的认识,同时通过多次上机操作,我对计算机的应用能力也有很大的提高,而在论文设计中通过查
阅文献,搜集资料,综合分析等方面的训练,使我综合应用各方面知识,分析解决实际问题的能力也得到了很大的提高。
在具体的设计过程中,通过老师和同学的帮助和自己的不断摸索,掌握了不少的工程技术方法,同时也培养了自己的工程设计思想,为以后的实际工作打下了一定的基础。
九、参考文献
[1]张晓锋,张静.电气控制与可编程控制技术及应用.北京:
国防工业出版社,2010.
[2]宋伯生.PLC编程控制指南.北京:
机械工业出版社,2007.
[3]史国生.电气控制与可编程控制技术.北京:
化学工业出版社,2004.
[4]张万忠.可编程控制器入门与应用实例(西门子S7-200系列).北京:
清华大学出版社,2007.
[5]王鑫.PLC机电控制系统应用设计技术.北京:
电子工业出版社,2010.
[6]王永华.现代电气控制及PLC应用技术[M]北京:
北京航空航天大学出版社第二版2010,10
[7]赵相宾.可编程控制器技术与应用系统设计机械工业出版社2002,7
[8]廖常初.PLC编程及应用机械工业出版社2005,3
[9]陈白宁.机电传动控制基础机械工业出版社2008,6
[10]胡学林.可编程控制原理及应用电子工业出版社2007,1
[11]方承远.工厂电器控制技术机械工业出版社2005,6
附录
附录1:
指令语句表
Network1////自动配料
LDI0.0
OM0.0
OI0.6
OI0.7
LPS
EU
SM0.3,1
RM0.6,1
LPP
ANT38
ANI0.1
ANM0.2
ANM0.7
ANQ1.3
=M0.0
Network2
LDI0.6
OM1.1
LPS
AT37
=M0.2
LPP
=M1.1
Network3
LDI0.7
LDNM0.7
AM1.0
OLD
LPS
AT38
=M0.7
LPP
=M1.0
Network4
LDNC0
ANM1.0
AI0.3
OI0.4
=M0.4
Network5
LDM0.3
OT37
OM0.1
AM0.0
ANQ0.5
ANM0.4
=Q0.0
=M0.1
Network6
LDM0.0
LPS
ANC0
ANM1.0
AI0.3
LPS
ANI0.5
=Q0.2
LPP
RM0.3,1
LRD
AI0.4
ANI0.5
=Q0.3
RM0.3,1
LRD
ANI0.2
AI0.5
=Q0.1
LPP
AI0.2
=Q0.4
TONT37,100
Network7
LDI0.2
LDT38
OM0.3
CTDC0,2
Network8
LDC0
AI0.4
SM0.6,1
Network9
LDI0.2
AM0.6
LDT38
OM0.3
CTDC1,3
Network10
LDC1
AT37
AI0.2
=Q0.5
Network11
LDQ0.5
TONT38,300
Network12////自动装车
LDI1.0
OM1.6
LPS
AI1.5
ANI1.6
SQ1.2,1
LPP
=M1.6
Network13
LDQ1.2
TONT39,60
Network14
LDT39
SQ1.1,1
Network15
LDQ1.1
TONT40,60
Network16
LDT40
SQ1.0,1
SQ1.3,1
Network17
LDI1.1
OM1.5
OM1.2
OI1.4
OI1.6
ONI1.5
LPS
RQ1.3,1
ANM1.4
=M1.5
LPP
TONT43,60
Network18
LDT43
OI1.2
OI1.3
OI1.4
ONI1.5
RQ1.0,1
SM1.2,1
Network19
LDM1.2
TONT41,60
Network20
LDT41
OI1.3
OI1.4
ONI1.5
RQ1.1,1
SM1.3,1
Network21
LDM1.3
TONT42,60
Network22
LDT42
OI1.4
ONI1.5
RQ1.2,1
RM1.3,1
=M1.4
RM1.2,1
电气控制与PLC课程设计成绩评定表
姓名
Xxx
学号
Xxx
专业班级
电气工程09级2班
课程设计题目:
基于S7-200PLC的自动配料控制系统设计
课程设计答辩或质疑记录:
成绩评定依据:
评定项目
评分成绩
1.设计方案可行性及其选优(20分)
2.设计过程及结果(40分)
3.平时成绩(态度认真、遵守纪律)(10分)
5.设计报告的规范性、参考文献充分(不少于5篇)(10分)
6.答辩(20分)
总分
最终评定成绩(以优、良、中、及格、不及格评定)
指导教师签字:
年月日