输料自动化.ppt
《输料自动化.ppt》由会员分享,可在线阅读,更多相关《输料自动化.ppt(41页珍藏版)》请在冰豆网上搜索。
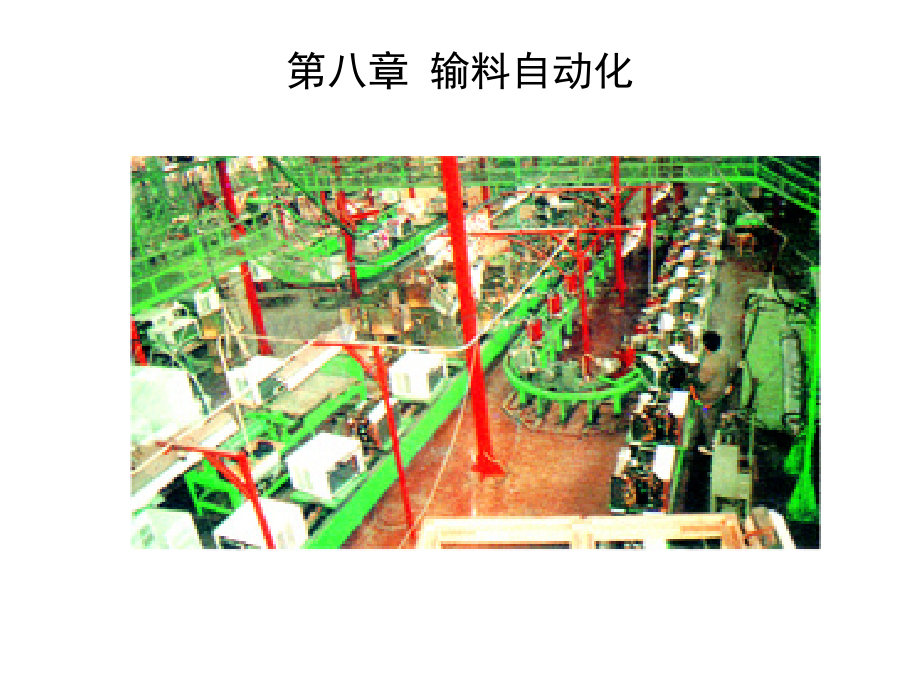
第八章输料自动化第一节第一节基本概念基本概念一、输料自动化的意义在机械制造工业中,工件的传输时间约占整个生产过程时间的80%90%,生产中的事故、故障,约85%是出现在工件的传输过程中。
因而,工件的自动输送系统是机械制造自动化系统中最重要的组成部分,它包括工件自动上下料装置、自动输料装置、自动转位装置、自动贮料装置、随行夹具的升降及返回装置、自动排屑装置等。
自动输料装置是将被加工工件从一个工位自动传送到下一个工位,从一台设备输送给下一台设备,从而为自动线按生产节拍连续地工作提供了条件;并从结构上把自动线的各台设备联结成为一个整体。
因而输料装置的自动化程度直接影响着自动线的生产稳定性、生产效率、总体布局和结构型式,所以它是自动线中最重要的辅助设备。
尤其对于柔性制造系统来说,传输系统和加工系统的功能是不可分开的。
二、自动输料装置的类型自动输料装置的型式与工件的结构和尺寸特性、自动线中设备的类型和布局以及自动线工艺过程的特性等因素有关。
按其输送的方法和结构,可分为重力输料、强制输料和步伐式输料。
重力输料装置分为滚动输料槽和滑动输料槽,适用于外形简单的中小型回转体工件。
结构简单,但并不十分可靠。
强制输料装置又分为链条式输送带、链板式输送带、机械手直接传送及其他动力推料装置等,它适用于大中型回转体或畸形工件等外形较复杂工件的输送。
当无法利用工件重力输送或为了保证输送可靠性时,常采用强制输料装置。
步伐式输料装置有弹簧棘爪式、摆杆式、抬起带走式和托盘式等,适用于加工箱体和杂件的组合机床自动线。
三、设计输料装置的基本要求设计和选择输料装置时,除要考虑结构简单,工作可靠和便于布置外,还应注意以下几点:
1.输料速度要高,以缩短自动线的附助时间,满足生产节拍的要求。
2.输送的位置精度要满足固定夹具或上料装置的定位要求。
3.输送过程中要严格保持工件预定的方向。
为此要设导向板、导向杆、托盘、托架和限位块等机构。
4.输料装置中的工件限位和导向机构,在工件定位时,不应与固定夹具系统干涉,运动部分不应相碰。
5.理想的输料装置应具有供料的“缓冲性”(兼有贮料作用),以使输料装置动作不必与机床工作保持严紧的节奏性,可提高自动线的工作效。
第二节第二节重力输料装置重力输料装置一、重力输料装置的结构型式及特点重力输料装置按其输料槽的结构形式,又分为滚动式输料槽和滑动式输料槽。
在大多数情况下,输料槽是靠工件的重力实现工件传送的,不需要其它动力源或特殊装置。
只有在无法用重力输送或为了保证运送的可靠性时,才采用强制输送的输料槽。
同时,输料槽往往兼有贮料功能,在一些加工中小型回转体工件(如:
盘、环、销及短轴等)的自动线中,常常被作为基本输送装置。
由于受工件形状和尺寸限制,输料槽传送的可靠性不高,容易出现工件阻塞,甚至跳出槽外等故障。
滑动式输料槽多用于传送回转体工件,也可以传送非回转体工件。
但滑动式输料槽摩擦阻力比滚动式输料槽大,因此要求倾斜角较大,通常25。
对于倾斜角较大的长型滑道,为了避免工件末速度过大产生冲击,可把滑道末段做得平些或采用缓冲减速器。
在某些情况下,为了减少输送时的摩擦阻力,也可采用辊道式输料槽代替滑动式输料槽,但辊道式输料槽的结构较为复杂。
二、滚动式输料槽的设计1.工件形状特性与槽宽的关系工件形状特性(长度与直径之比,简称长径比)与槽宽的关系是影响滚动式输料槽工作性能好坏的一个重要因素。
设计滚动料槽时,要依据工件的长径比来确定料槽内壁宽度B;对已有料槽要依据工件长径比和宽度来进行可通过性验算。
工件在料槽中滚动时,由于存在间隙S,可能因摩擦阻力的变化或工件存在一定锥度误差而滚偏一个角度。
当工件对角线长度C接近或小于槽宽B时,就可能出现卡住或完全失去定向作用。
当工件偏转到两个对角与料槽侧壁相接触时,其对角线C与垂直于侧壁的OM线之间夹角为。
工件能在料槽内运动的条件是:
即tgtg式中:
工件与侧壁的摩擦角;工件于侧壁的滑动摩擦系数。
料槽宽度:
BLS式中:
S间隙,mm;L工作长度,mm。
且(8-1)根据三角函数的基本关系可知:
将不自锁条件tg代入,得出不自锁的允许间隙:
(8-2)上式表明:
允许的间隙SK与工件的长径比(L/D)和摩擦系数有关。
要求实际的最大间隙SmaxSK,工件才能在料槽中可靠地通过。
否则,不能采用自重滚动式输送,而应改用其他方式输送。
工件偏转的程度还与其导向端面的形状有关,当工件的导向端面有倒角时,会偏转得厉害些。
所以在应用上式时,应以计算直径Dj代替式中D。
)两端有倒角时,其计算直径DjD2a;b)两端为不同直径的阶梯轴时,其计算直径DjDa。
2.输料槽内壁宽度根据工件的形状特性与宽度关系的分析可知,料槽宽度不应太大。
否则,当实际间隙超过允许间隙SK时会卡料(自锁)或完全失去定向。
但也不能太小,否则,由于料槽结构不良和制造误差会使局部尺寸小于工件长度,也会产生卡料现象。
在实际确定料槽宽度B时,应考虑料槽及工件的制造误差,其计算公式如下:
LSmaxBLSminBL(mm)(8-3)式中:
Smax料槽与工件间的最大间隙;Smin为保证工件在料槽中滚送所必需的最小间隙,可以L为公称尺寸,按H8/h8H11/h11级配合间隙选取;B料槽宽度的制造公差,mm;L工件长度公差,mm。
宽度B确定后,还应该用下式进行可通过性验算。
即应满足:
SmaxSK(8-4)3.侧板高度输料槽侧板的高度与产生的阻力有关,侧板愈高,在一定范围内则阻力愈大。
但也不能做得过低,否则,如果工件在较长的输料槽中,以较大的加速度滚到终点碰撞前面的工件时,可能跳出槽外或产生歪斜而卡住后面的工件。
一般推荐:
(0.51)D。
24.输料槽的倾斜角输料槽的倾斜角输料槽的倾斜角愈是影响输料的稳定性和可靠性的主要因素之一。
倾斜角过大时,工件滚动的速度愈大,易产生冲击、歪斜及跳出槽外等不良后果。
同时也会引起机床间输料高度差增大,浪费能源,布局不合理。
而倾斜角过小时,易出现停滞现象。
特别是在料槽中贮满工件的情况下,工件互相挤压在一起,接触点处运动方向相反,产生较大的滑动摩擦阻力,因而易停滞不向下滚动。
倾斜角度的大小取决于料槽支承板和工件表面的质量。
若支承板精度较高,工件经过精加工,一般57;若支承板精度一般,工件经过粗加工,取710;若支承板精度很低,工件为毛坯或表面有缺陷,则取1015。
三、滑动式输料槽的设计滑动式输料槽的截面形状有各式各样,其滑动摩擦阻力各不相同。
为了能应用与平面摩擦力相似的计算公式F等W来计算滑动摩擦阻力,这里引入了“等效摩擦系数”的概念。
1.V型滑动输料槽工件在V型滑槽中滑动,要比平底滑槽受到更大的摩擦阻力。
设工件的重量为W,工件对V型槽边的正压力分别为N1和N2。
工件与料槽之间的滑动摩擦系数为,则每边的摩擦阻力为:
总的摩擦阻力为:
(85)为写成与平面摩擦力相似的公式,则有:
F等W(86)由(85)式和(86)式求得:
(87)由力平衡关系式,可得:
求解出N1和N2代入(87)式,得V型滑槽的等效摩擦系数为:
(88)若90(即V型槽对称线与地面垂直),则:
(89)由(88)式及(89)式可知,其半角愈小,等愈大,即滑动摩擦阻力愈大,工件输送稳定性愈好,定向精度愈高。
通常取4560,重而大的工件取60;对轻小件可取45,即采用标准角铁制作。
V型输料槽的倾斜角料槽,一般应为等效摩擦系数所确定的摩擦角等的1.41.5倍,即:
料槽(1.41.5)等(810)式中:
等等效摩擦角,。
2.双轨滑动式输料槽双轨滑动式输料槽双轨滑动式输料槽可以看成是形输料槽的一种特殊形式,如图所示。
只要通过几何关系找出sin和sin,代入(88)式,即可求出等。
由几何关系得:
则得:
(811)式中:
B两导轨间距离,mm;h两导轨的高度差,mm;D工件直径,mm;d导轨的直径,mm。
若两导轨在同一水平面内,h0,则:
(8-12)用双轨滑道输送带肩部的工件时,为使工件在输料过程中,肩部不致互相叠压而卡住,应使:
K1.1(813)式中:
工件肩部的高度。
若使(813)式成立,必须尽量减小杆部倾斜角。
为减小角,应尽可能增大S。
由图b可知,两支承点间距离S为:
SBh(mm)式中:
B两导轨内壁之间距离,mm;h导轨板厚度(或圆导轨直径),mm。
设d为杆部直径,一般取B1.1d,则:
S1.1dh(mm)要减小L应增大S,所采取的方法不应该是增大B,因增大B易使工件失去导向而挤在内壁上,使滑动发生困难。
而应使导轨板加厚,并使导轨板削成斜面,如图c所示。
此外在料槽出口处还应设置剔除器(图中d)。
当工件肩部较厚时,不应采用肩部重叠法传送,而应按并列法传送,此时不存在肩部叠压问题。
为使柄部下滑中不发生较大的摇摆,可在肩部上方设置可调压板。
第三节第三节强制输料装置强制输料装置当无法采用自重滚动输送或为了提高输料的可靠性时,往往采用具有动力驱动装置的强制输料装置。
链条式输送带就是其中一种典型的强制输料装置。
本节以链条式输送带和链板履带式输送带为例,介绍强制输料装置的工作原理及结构特点。
一、链条式输送带1.链条式输送带的结构及工作原理输送中小工件时,V形块应做成整块的,装在同一链节上;输送粗大工件时,将V型块分成两个半块,分装在跨链节上。
也可采用一条长板开有等距的V型槽口,它固定不动,而链条及拨爪运动,靠拨爪推动工件沿V型槽口逐步前进。
对于沿工件径向传送工件的链带,其V型块间距离应尽量小,以便能贮存较多的工件。
但必须考虑上下料机械手抓放的张开位置。
对于沿工件轴向传送的链带,其V型块的间距t可由下式计算:
t=(L+S)/2(mm)式中:
L工件的长度,mm;S工件之间的间隙,mm。
2.链条式传送带的运动型式链条式传送带的运动型式1)往复运动型兼有输料和贮料功能。
它由电动机或液压马达驱动,链条可做往复运动。
料道上设有料空、料满、前进、后退等多个行程开关,实现“步进贮料”、“快进贮料”、“快退接料”和“步进供料”等多种运动。
这种类型输送带,控制系统较复杂,但输料效率高。
2)单向循环运动型链条输送带作连续循环运动,不论输送带上有无工件,始终运动。
仅用于传送工件,效率不高。
3)步进运动型通过油缸、齿轮齿条及棘轮棘爪机构,驱动输送带作步进运动。
这种类型输送带,多设在自动线的线首及线尾,或设在非通过式的中间料仓处,用于步进供料,或步进贮料。
二、链板履带式输送带二、链板履带式输送带链板履带式输送带是由一节节带齿的链板组成。
链板上表面磨光,靠其摩擦力传送工件。
链板下面有齿,与驱动链轮相啮合,带动封闭式链板作单向循环运动。
为防止链带下垂,用两条光滑托板支承起来。
在链板带上面设置分路挡板机构,实现分料、合料、拨料、限位等运动。
链板履带式输送带结构简单,动作可靠,贮料较多,容易实现“分料”及“合料”。
其缺点是磨损较快,需定期调整或更换。
这种输送带属于自动流动式传送装置,通用性好。
国外已把它定为标准传送装置之一。
第四节第四节步伐式输料装置步伐式输料装置步伐式输料装置是组合机床自动线的典型工件输送装置。
在加工箱体类零件的自动线以及带随行夹具的自动线中,使用非常普遍。
一、步伐式输料装置类型及特点常用的步伐式输送装置有弹簧棘爪式、摆杆式、抬起带走式及托盘式等四种。
1.弹簧棘爪式输送带2.摆杆式输送带3.抬起带走式输送装置4.托盘式输送装置1.弹簧棘爪式输送带弹簧棘爪式输送带设计时应注意以下几点:
(1)在一节输送带上,最好只安装一台机床加工工位的棘爪。
如果在一节输送带上装有两台机床的棘爪,则不但要求棘爪间具有精确的距离,而且机床安装时的中心距离要求也很严,这是不合理的。
(2)由于整个输送带比较长,考虑到制造及安装工艺性,一般都把它做成若干节,用联结板联成整体。
联结板一般固定在前一节输送带上,安装调好后打销固定。
输送带中间的棘爪,一般都做成等距的,爪间距为3501600mm。
自动线的首端及末端棘爪,与其相邻棘爪之间的距离,根据要求可做得比输送步距短一些,但至少可容纳一个工件,一般首端棘爪间距不小于310mm;末端棘爪间距不小于155mm。
(3)调整输送带时,输送带向前到达终点,工件应比规定的定位安装位置滞后0.30.5mm。
定位时以定位销