设计M6020A工具磨床磨架外壳零件的机械加工工艺规程及加工 主轴孔工序的专用夹具.docx
《设计M6020A工具磨床磨架外壳零件的机械加工工艺规程及加工 主轴孔工序的专用夹具.docx》由会员分享,可在线阅读,更多相关《设计M6020A工具磨床磨架外壳零件的机械加工工艺规程及加工 主轴孔工序的专用夹具.docx(20页珍藏版)》请在冰豆网上搜索。
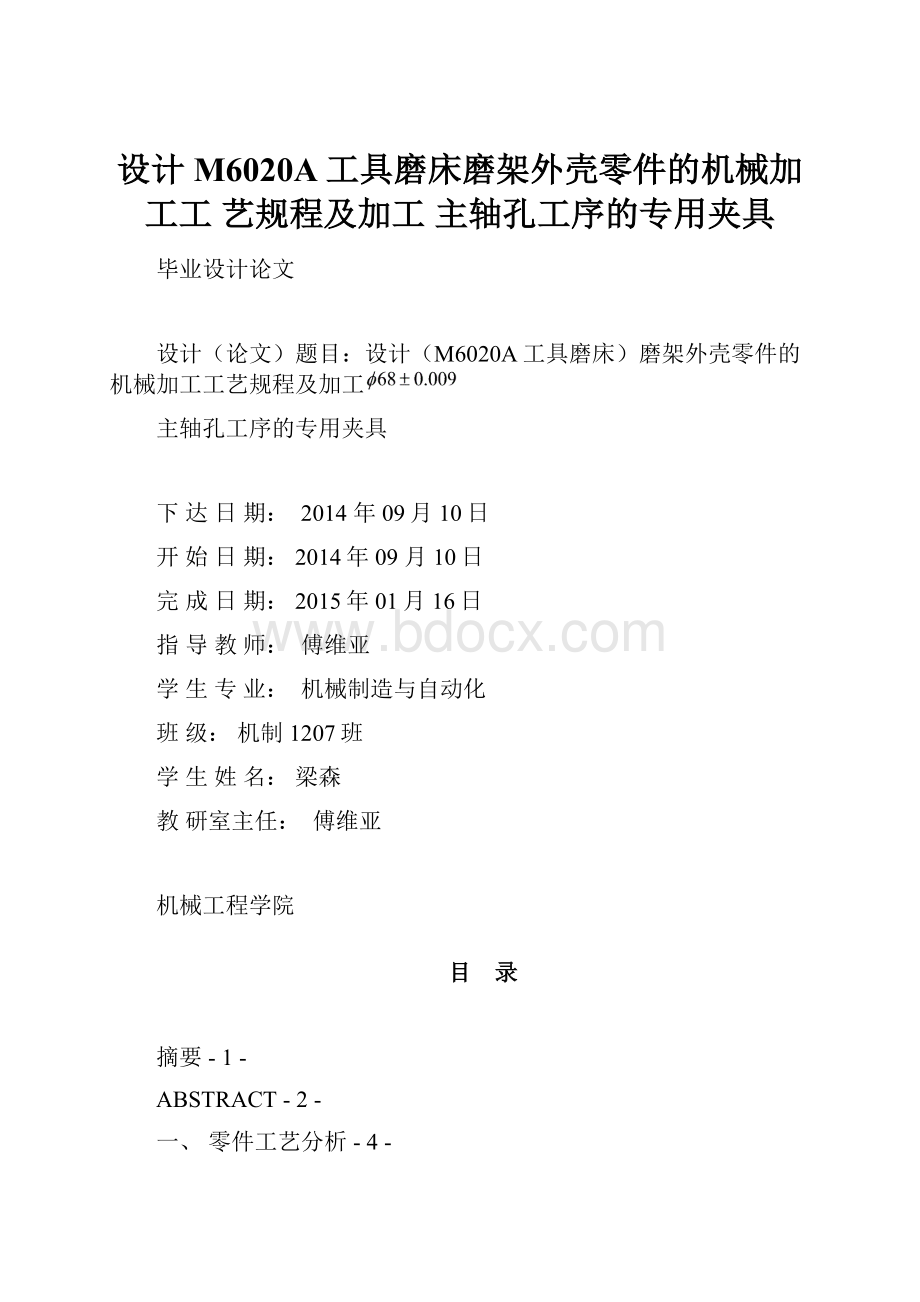
设计M6020A工具磨床磨架外壳零件的机械加工工艺规程及加工主轴孔工序的专用夹具
毕业设计论文
设计(论文)题目:
设计(M6020A工具磨床)磨架外壳零件的机械加工工艺规程及加工
主轴孔工序的专用夹具
下达日期:
2014年09月10日
开始日期:
2014年09月10日
完成日期:
2015年01月16日
指导教师:
傅维亚
学生专业:
机械制造与自动化
班级:
机制1207班
学生姓名:
梁森
教研室主任:
傅维亚
机械工程学院
目 录
摘要-1-
ABSTRACT-2-
一、零件工艺分析-4-
1、零件功用-4-
该零件为M6020A万能工具磨床的砂轮磨架外壳,其主要作用是支承内孔主轴,安装砂轮。
-4-
2、主要技术要求分析-4-
3、工艺分析-4-
二、制订工艺路线-6-
1、毛坯的选择-6-
2、确定毛坯余量-6-
3、精基准的选择-6-
4、制定工艺路线-7-
(1)工艺路线方案一:
-7-
(2)工艺路线方案二-8-
(3)工艺方案的比较与分析-8-
5、机械化加工余量、工序尺寸及毛坯尺寸确定:
-8-
6、确定切削用量-9-
(1)加工条件:
-9-
(2)计算切削用量-10-
(3)工时定额-13-
三、机床夹具设计-13-
1、自由度分析-13-
2、定位基准的选择-13-
3、夹紧设计-14-
4、(附图2)装配图-15-
5、定位误差的分析计算:
-16-
(1)夹具精度分析及计算:
-16-
(2)安装误差分析计算:
-16-
(3)△G加工误差计算:
-16-
四、致谢-17-
五、参考文献-18-
摘要
本文是一篇关于M6020A万能及工具磨床箱体工艺方案设计的说明书。
全文贯穿了设计的全过程,包括分析零件结构和加工技术要求,确定生产类型,选择毛坯及毛坯尺寸,确定零件定位基准,选择各表面的加工方法,划分加工阶段,确定各工序的加工方法,具体划分各工序的安装和工步,确定工序余量和工序尺寸及公差,确定切削用量,计算工时定额,编写加工工艺过程卡、加工工艺卡,工序卡三种工艺文件卡,车床专用夹具设计,工件的定位分析,拟定定位方案及定位元件的选择,定位误差的分析,拟定夹紧方案,计算夹紧力等,选择加工设备、夹具刀具及量具,最后设计加工
主轴孔工序的专用夹具,绘制装配图和零件图。
由于本人是初次设计,能力有限,加之时间仓促,尚有许多不足之处,设计中的错误和不当之处,恳请老师予以指出和改正。
关键词:
磨床箱体,毛坯,工时定额,专用夹具
ABSTRACT
Thisisanarticleaboutthe M6020Auniversal toolgrinder andthe designof boxprocessprogram instructions. Thefulltext runsthrough thewholeprocessofdesign, includingthe analysisoftherequirementsof partstructureandprocessingtechnology, determinethe productiontype, thechoiceofblank andfur size, determinethe datumlocation, select thesurfaceprocessingmethod,processingofthedivided stage, determinetheprocessing methodofeachprocedure, thedetaileddivisionof eachprocessof installation andprocesssteps, determine theprocessallowanceand processdimensionandtolerance, todeterminethecuttingparameters, calculationof manhourquota, compilemachiningprocess card, process cards, process cardsofthree processfile card,specialfixturefor lathedesign, analysisoftheworkpiece positioning, formulateprogramsandpositioning positioningelement selection, positioningerroranalysisof the proposed scheme, clamping, clampingforcecalculation. Selectionofmachiningequipment andfixture, toolandmeasuring, aspecialfixture designprocess last spindlehole process, assemblyandpartsdrawing.BecauseIwasthefirsttimedesign,limitedcapacity,coupledwithtimeconstraints,therearestillmanyshortcomings,designerrorsandinappropriate,asktheteachertobepointedoutandcorrected.
KEYWORDS:
grindingmachine box, blank, manhourquota, specialfixture
一、零件工艺分析
1、零件功用
该零件为M6020A万能工具磨床的砂轮磨架外壳,其主要作用是支承内孔主轴,安装砂轮。
2、主要技术要求分析
M6020A万能工具磨床的磨架外壳零件共有两组加工表面,而这两组加工表面之间有一定的位置要求,现将这两组加工表面分述如下:
1.以Ø90为中心的加工表面
这一组加工表面包括Ø28h6的端面及外圆,与之平行的外圆及端面,Ø68的也及M12-7H孔端面,2×0.5、3×1的切断槽及Ø70的环形槽及倒角;
2.以Ø68为中心的加工表面
这一组成加工表面包括铣Ø90两侧30宽,钻攻2×3-M5-7H和M10-7H也和2×M12-7H
3.这两组加工表面之间有着一定的位置要求
Ø90mm的圆柱面与Ø68也中心线的平行度公差为0.02。
4.Ø90的端面需要一定的平面度为0.006和圆跳动为0.02
3、工艺分析
由以上分析可知,对于这两组加工表面,我们可以先加工一组表面,然后借助于专用夹具进行另一表面的夹正,并保证它们之间有位置精度要求。
(附图1)零件图
二、制订工艺路线
1、毛坯的选择
由零件图和设计任务可知,磨架外壳零件材料为HT200,同时考虑到该零件在磨床工作中需要经常转动,且零件在工作过程中需要承受高变及冲击性载荷,为了降低其振动频率,因此应该选用铸件,以保证零件工作可靠。
已知零件的生产纲领为800件/年,通过计算,该零件质量为7.2Kg,由《金属机械加工工艺人员手册》可知,其生产类型为成批生产,故选择二级铸件毛坯,采用手工砂型木模铸造工艺,其上Ø90磨架外壳凸台面和Ø68孔需要铸出。
2、确定毛坯余量
查阅《金属机械加工工艺人员手册》中铸件机械加工余量可知,体壳零件上Ø68孔的总余量取值7mm(双边余量);Ø90磨架外壳凸台面毛坯余量取值5mm,该零件的其余各表面的毛坯余量的具体分布情况见“零件-毛坯合图”所示。
3、精基准的选择
加工磨架外壳Ø68砂轮主轴孔时,为保证基准重合,采用了典型的“3、2、1”工件定位方案(见下图所示),即:
选择外壳底座Ø90端面(限制工件3个自由度)和Ø28H6外圆(限制工件2个自由度)作为主定位面,选择磨架外壳宽度尺寸为30的侧面(或Ø90毛坯面,即:
Ø68砂轮主轴孔同轴的毛坯外圆)作为防转面(限制工件转动自由度)。
粗基准的选择:
磨架外壳零件粗基准至关重要。
对于一般轴类零件而言,以外圆为粗基准是完全合理的,但对本零件来说,若以Ø90的外圆为基准,则会造成加工Ø68主轴孔的加工余量不均匀。
现选取Ø68主轴孔的未加工前的毛坯孔为粗基准,起到定心作用,并利用毛坯孔的端面作为主要定位面限制三个自由度。
另外,以磨架外壳零件的腰部Ø80不加工毛坯面作为防转面,限制工件转动自由度,达到完全定位。
4、制定工艺路线
制定工艺路线的出发点,应当是使零件的几何形状及位置精度等技术要求能得到合理保证,在生产纲领已确定为成批生产条件下,可以考虑采用万能性机床配以专用夹具,并尽量采用工序集中来提高生产率,除此以外,还应当考虑经济效益,以便使生产成本尽量下降。
(1)工艺路线方案一:
工序Ⅰ铸造;
工序Ⅱ人工时效
工序Ⅲ车Φ28、Φ90的端面及外圆,钻攻M12—7H孔,切3×1、2×0.5Φ90的槽
工序Ⅳ铣Φ90端面尺寸55
工序Ⅴ调头、校正,铣Φ90端面尺寸120
工序Ⅵ铣Φ90的两侧30宽
工序Ⅶ粗精镗Φ68端面及孔
工序Ⅷ钻攻2×3-M5-7H和M10-7H孔
(2)工艺路线方案二
工序Ⅰ铸造;
工序Ⅱ人工时效
工序Ⅲ车Φ28、Φ90的端面及外圆
工序Ⅳ切3×1、2×0.5、Φ90的槽
工序Ⅴ铣Φ90的两侧30宽
工序Ⅵ钻攻2×3-M5-7H和M10-7H及M12-7H孔
(3)工艺方案的比较与分析
上述两个工艺方案特点在于:
方案一先加工Φ28、Φ90端面及外圆,再镗Φ68的端面及孔,方案二则与此相反,先镗Φ68的端面及孔,再加工Φ28、Φ90的端面及外圆。
两相比较,可以看出第一方案加工余量均匀,因此决定将采用方案一。
5、机械化加工余量、工序尺寸及毛坯尺寸确定:
“磨架外壳”零件材料:
灰口铸铁HB150~200;毛坯重量:
7.2000kg;生产类型:
成批生产;采用成件毛坯,6级精度组(成批生产)
根据上述原始资料及加工工艺,分别确定各加工表面的机械加工余量,工序尺寸及毛坯尺寸如下:
1.车Φ28、Φ90的端面z=2mm
2.粗车Φ28、Φ90的外圆2z=4mm
3.精车Φ90的外圆2z=0.8mm
4.钻攻M12-7H孔2z=12mm
5.铣Φ68端面2z=4mm
6.切3×1、2×0.5、Φ90的槽2z=1mm
7.铣Φ90的两侧30宽2z=3mm
8.粗镗Φ68孔2z=5mm
9.精镗Φ68孔2z=0.8mm
10.钻攻2×3-M5-7H孔2z=5mm
11.钻攻M10-7H孔2z=10mm
余量分布图:
(2)余量分布图(见上图)
选择Ø68孔,其余量分布图如下:
毛坯孔直径为 Ø68-(0.8+1.2+5)=Ø61±1.0mm
粗镗孔直径为 Ø61+5=Ø66H13(
)
半精镗孔直径 Ø66+1.2=Ø67.2H10(
)
精镗孔直径为 Ø67.2+0.8=Ø68H7(
)
超精加工孔至设计尺寸 (
)
6、确定切削用量
工序Ⅰ车Φ28、Φ90的端面及外圆
本工序采用计算法:
(1)加工条件:
(1)加工材料:
灰口铸铁:
σD≥130,成批毛坯
(2)加工要求:
车工Φ28端面有外圆,粗车Φ90外圆
(3)机床:
CA6150普通车床
(4)端面车刀
刀片材料:
YG15;
刀杆尺寸:
16×25mm,kr=90,r0=15,a0=12,re=0.5mm
(2)计算切削用量
(1)车端面
1)ap=1,f=0.2mm/r
2)计算切削速度、耐用度t=45min
V=kv.Cv/(tmapxvfyv)
=292×0.81×0.8×1.54/(450.18×10.15×0.20.3)
=243(m/min)(4.04m/s)
3)确定主轴转速
Ns=1000v/3.14dw=1000×4.04/(3.14×28)
=46(r/s)(2757r/min)
按机床选取nw=10r/s(600r/min)(48m/min)
所以实际的切削速度为v=0.8m/s
4)切削工时tm=L/10.f=2/10×0.2=1(s)
(2)粗车外圆:
要求校验机床功率及进给机构强度
1)切削深度:
2z=4mm可一次性切除
2)进给量:
f=0.8mm/rap=3mm
3)计算切削速度:
v=0.99×292/(450.18×30.15×0.80.3)
=129(m/min)(2.15m/s)
(3)确定主轴转速:
ns=1000×2.15/(3.14×90)=7.6(r/s)(456r/min)
按机床选取nw=10m/s(600r/min)
所以实际切削速度为v=2.83(m/s)
4)切削工时:
tm=6/(10×0.8)=0.75m/s
(4)粗镗Φ68通孔
1)ap=2mm,f=0.3mm/r
2)镗刀25×200
3)计算切削速度、耐用度t=40min
V=292×0.81×0.8×1.54/(400.18×20.15×0.30.3)
=99.8(m/min)(1.7m/s)
4)确定主轴转速ns=1000×1.7/(3.14×68)=7.96(r/s)
按机床选取nw=1.7(r/s)
所以实际切削速度v=0.4(m/s)
5)切削工时tm=120/(1.7×0.3)=235(s)
(5)钻攻M12-7H
1)ap=10mm,f=0.4mm/r
2)Φ10.2钻头
3)计算切削速度、耐用度t=120min
V=292×0.81×0.8×1.54/(1200.18×100.15×0.40.3)
=112(m/min)(1.9m/s))
4)确定主轴转速
ns=1000×1.9/(3.14×12)
=50.4(r/s)
按机床选取nw=5(r/s)
所以实际切削速度v=0.19(m/s)
5)M12-6H丝锥耐用度t=60min
ap=0.5mm,f=1mm/r
V=292×0.81×0.8×1.54/(600.18×0.50.15×10.3)
=161(m/min)(2.7m/s)
ns=1000×2.7/(3.14×12)
=71.6r/s
按机床选取nw=1.7r/s
所以实际切削速度v=0.06(m/r)
6)切削工时tm=14s
切削工时tm=0.2s
∴总的切削工时为:
t=14+0.2=14.2s
tm=12/(0.5×1.7)=1.4(s)
查阅《机械制造工艺与机床夹具课程设计指导》以及《机械加工工艺人员手册》根据零件尺寸、材料确定各工序的切削用量:
工序
工步
切削深度
(mm)
切削速度
(m/min)
转速r/min
或往复次数
进给量min/r
或mm/双行程
40
1
1
37.68
150
2.5
2
0.5
47.73
190
1.24
3
0.2
59.03
235
1
50
1
1
29.44
375
1.25
2
0.3
37.29
475
0.4
60
1
1
29.44
375
1
2
0.3
37.29
475
0.4
100
1
1.8
37.68
150
2.63
2
0.2
39.03
235
0.85
110
1
3
12.56
80
0.37
2
0.5
19.6
125
0.13
3
0.42
75.26
400
1.43
4
0.08
59.35
315
1.03
120
1
2.3
20
500
0.3
2
0.2
6
180
0.3
3
2.3
20
1000
0.2
4
0.2
15
710
0.3
5
11
20
710
0.3
(3)工时定额
外形尺寸主要在铣床加工,故准备—终结时间为65min;
切削用量的确定举例:
例如:
工序号40,铣大底面,查《金属机械加工工艺人员手册》表14-7,取粗铣时的每齿进给量
,
fz=0.15,z=18.则f=2.7mm/F,切削速度v=42.8m/min,则n=[1000*v/(д*d)]=1000*42.8/3.14*80=170,由机床手册可知,主轴转速取150m/min,则切削速度v=д*d*n/1000=3.14*80*150/1000=37.68m/min。
f=2.7*150=405mm/min,由机床纵向进给量可知(查表)f=375mm/min,则f=375/150=2.5mm/r。
工序号110.精镗Φ60H7孔时,查《金属机械制造加工工艺人员手册》表14—5及机床进给量(即T68镗床的实际进给量中选取)0.25—0.5取f=0.37mm/r切削速度v=12m/min,则n=1000*v/(д*d)=1000x12/(3.14x45)=84.92m/min,取主轴转速n=80r/min,则实际切削速度Vo=80x3.14x45/1000=11.3mm/min.
=
=21min
三、机床夹具设计
1、自由度分析
由于要镗Φ68端面及孔,所以至少要限制除Y转动外其余5个自由度。
大底面限制X转动,Y转动,Z移动,Φ28外圆孔限制X移动,Y移动,侧面支撑钉限制Z转动,X移动,共限制7个自由度。
2、定位基准的选择
有零件图可知,Φ68的孔与其端面有一定的垂直度要求,与Φ90的端面有一定的平行度要求,其设计基准为孔的中心线。
为了使定位误差为零,应该选择以Φ68孔的中心线为定位基准,但为了夹具结构简单,因此这里选Φ90的端面为主要定位基准,以Φ28的外圆面和一个120×30侧面为次要定位面。
共限制7个自由度,虽为过定位对加工有微小的影响,但可增加工件系统的刚性。
3、夹紧设计
加紧是在Φ68外圆上用V形块压紧。
联接处设计为浮动链接,目的是为了补偿同批工件尺寸公差的变化,确保了夹紧装置的可靠性。
4、(附图2)装配图
5、定位误差的分析计算:
(1)夹具精度分析及计算:
△D定位误差分析:
由于定位基准与工序基准不重合,则△B=0.015mm,定位误差与限位基准重合,则△Y=0,因此△D=△B+△Y=0.015mm
=(0.018+0.013+0.021)
=0.052mm
(2)安装误差分析计算:
镗套与支架的采用H7/h6最大间隙为0.01mm,所以△A=0.01mm
(3)△G加工误差计算:
△G主要取决于机床的制造精度以及工艺的安排等多方面的因素,一般取零件加工精度的1/3到1/5,故取△G=&K/3=0.03/3=0.01mm.夹具的总加工精度∑D=(△D2+△A2+△G2+△A2)1/2=0.021<&K=0.03mm.因此,此镗床的夹具定位方案合理.
四、致谢
历时几个月的毕业设计终于完成了,在这儿段时间里,我所运用的大学所学的专业知识比较成功的完成了本次毕业设计。
在设计中通过方案论证,理论设计计算,机械结构的设计,图纸的绘制,设计说明书的撰写等环节的训练,已经使个人理论水平和实际动手能力有了一定的飞跃。
本次设计锻炼了个人在设计、分析、动手方面的能力,同时使所学的专业知识得到了一次全面的巩固和加强。
此次毕业设计能够顺利完成,我得到了很多老师,同学的关心帮助和支持,在此我首先向他们表示感谢。
在毕业设计的过程中,我的指导老师给了我很多专业知识方面的帮助。
在设计前期的准备时,就非常关注我的选题,指明选题方向,帮助分析题目的可行性和实际中可能出现的问题以及需要注意的事项;在进行方案选择时,为我指出所需要重点掌握的知识范围,并帮助我分析相应知识难点的原理,使我的毕业设计能够顺利进行。
同时我要我要感谢大学所有教过和没有教过但给我很多帮助的老师,是他们的教导让我们能在这里学到很多的专业知识,给我以后的工作和学习打下了坚实的基础,是他们的谆谆教诲使我明白了很多为人处世的道理,给我以后的人生足迹烙下更深的印迹,在此我衷心的感谢所有帮助过我的老师。
此外,非常感谢许多其他同学,他们的许多想法和建议对我启发很大。
在此一并致谢!
还有在其他场合提供给我帮助的朋友们,在此也一并致谢,谢谢你们!
由于时间和个人知识及能力水平有限,论文中难免有一些纰漏和错误之处,恳请各位老师批评指正。
不胜感谢!
学生:
梁森
2014年12月
五、参考文献
1、薛源顺主编《机床夹具设计》北京:
机械工业出版社
2、郑修本主编《机械制造工艺学》北京:
机械工业出版社
3、冯丽萍主编《公差配合与测量技术》北京:
机械工业出版社
4、刘思俊主编《工程力学》北京:
机械工业出版社
5、陆剑中,孙家宁主编《金属切削原理与刀具》北京:
机械工业出版社
6、朱耀祥,浦林祥主编《机械夹具设计手册》北京:
机械工业出版社
7、赵如福主编《机械加工工艺人员手册》上海:
上海科学技术出版公司
8、赵家齐主编《机械制造工艺学课程设计指导书》北京:
机械工业出版社