汽车专业英语2版参考译文第13章 汽车制造.docx
《汽车专业英语2版参考译文第13章 汽车制造.docx》由会员分享,可在线阅读,更多相关《汽车专业英语2版参考译文第13章 汽车制造.docx(13页珍藏版)》请在冰豆网上搜索。
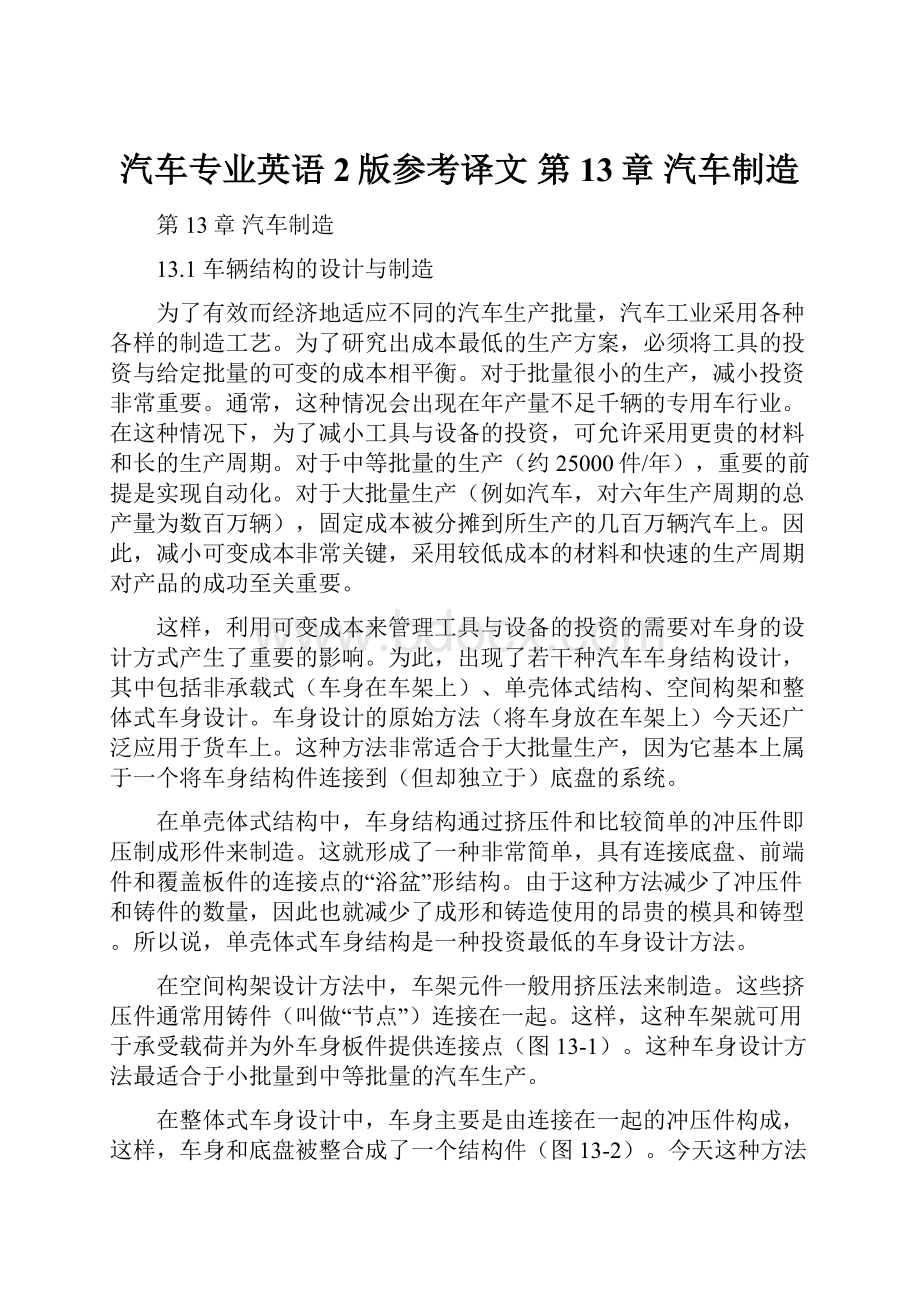
汽车专业英语2版参考译文第13章汽车制造
第13章汽车制造
13.1车辆结构的设计与制造
为了有效而经济地适应不同的汽车生产批量,汽车工业采用各种各样的制造工艺。
为了研究出成本最低的生产方案,必须将工具的投资与给定批量的可变的成本相平衡。
对于批量很小的生产,减小投资非常重要。
通常,这种情况会出现在年产量不足千辆的专用车行业。
在这种情况下,为了减小工具与设备的投资,可允许采用更贵的材料和长的生产周期。
对于中等批量的生产(约25000件/年),重要的前提是实现自动化。
对于大批量生产(例如汽车,对六年生产周期的总产量为数百万辆),固定成本被分摊到所生产的几百万辆汽车上。
因此,减小可变成本非常关键,采用较低成本的材料和快速的生产周期对产品的成功至关重要。
这样,利用可变成本来管理工具与设备的投资的需要对车身的设计方式产生了重要的影响。
为此,出现了若干种汽车车身结构设计,其中包括非承载式(车身在车架上)、单壳体式结构、空间构架和整体式车身设计。
车身设计的原始方法(将车身放在车架上)今天还广泛应用于货车上。
这种方法非常适合于大批量生产,因为它基本上属于一个将车身结构件连接到(但却独立于)底盘的系统。
在单壳体式结构中,车身结构通过挤压件和比较简单的冲压件即压制成形件来制造。
这就形成了一种非常简单,具有连接底盘、前端件和覆盖板件的连接点的“浴盆”形结构。
由于这种方法减少了冲压件和铸件的数量,因此也就减少了成形和铸造使用的昂贵的模具和铸型。
所以说,单壳体式车身结构是一种投资最低的车身设计方法。
在空间构架设计方法中,车架元件一般用挤压法来制造。
这些挤压件通常用铸件(叫做“节点”)连接在一起。
这样,这种车架就可用于承受载荷并为外车身板件提供连接点(图13-1)。
这种车身设计方法最适合于小批量到中等批量的汽车生产。
在整体式车身设计中,车身主要是由连接在一起的冲压件构成,这样,车身和底盘被整合成了一个结构件(图13-2)。
今天这种方法已经成为制造大批量生产的汽车的一种普通方法。
在整体式车身设计方法中,通常,通过将两个独立的冲压件拼合成箱式断面结构,来获取要求的刚度和强度。
最近几年,越来越多地采用液压成形管材来替代某些冲压和焊接薄壁断面结构。
图13-1奥迪A2铝空间构架白车身
图13-2车顶和底板板件与车身整合成一个结构件的整体式结构白车身
为了制造复杂的金属板冲压件,整体式车身设计需要在工具和模具方面进行巨大的投资。
然而,由于冲压件的可变成本相对较低,所以这种设计非常适合于大批量生产。
整体式车身设计适合于大批量生产还因为冲压和车身装配作业速度快,周期短。
13.2注射成型技术
注射成型是大多数热塑料汽车零件采用的主要加工方法。
这种方法能够生产形状与几何结构复杂的零件,且生产速度快,尺寸精度高,零件表面非常光洁。
在注射成型中可以完成模内表面修饰和形成表面网纹组织。
注射机的基本结构(见图13-3)包括注射装置和夹紧装置两个部分。
注射装置包括加热的料筒和在料筒内旋转的经过适当设计的螺杆。
将固态聚合物颗粒加入位于注射装置后端的料斗内。
在旋转螺杆的推动下,颗粒状物料向前移动,然后颗粒状物料开始熔化并最终变成均匀的液态聚合物,这些液态聚合物进入注射装置前部的一个小室内。
当小室内的聚合物量达到要求时,螺杆转动停止,并且现在像柱塞一样向前移动,从而使聚集的液态聚合物被挤入夹紧装置内的封闭的模膛内。
即使在模膛充满聚合物后,还要将一部分额外的液态聚合物注入模膛,以便对开始冷却时模内聚合物的收缩进行补偿。
模膛保持封闭,一直到聚合物零件的平均温度下降到该聚合物的固化温度以下为止。
然后打开模板,进行零件脱模,并使零件在模外进一步冷却到室温。
图13-3简单的注塑成型机
模内冷却时间(会对注射成型生产周期产生重要影响)取决于零件厚度、熔化温度(注射时液态聚合物的温度)、模壁温度和脱模温度(零件从模中顶出时的平均温度)。
为了缩短冷却时间,在不会导致零件瑕疵和不影响注射成型件质量的前提下,熔化温度和模壁温度应选的尽可能低些,而脱模温度应选的尽可能高些。
根据部件结构、成型模结构和加工参数的不同,注射成型零件会出现各种不同的模制瑕疵,如未充满模膛、表面损伤、内部空隙、高度收缩、翘曲、陷落痕迹、焊接线和残余应力。
通过选择合适的工艺参数,如熔化温度、模壁温度、注射压力和注射速度,可以减少或消除瑕疵。
工艺参数还会影响到分子的排列、残余应力和结晶度(对于结晶型聚合物),这又会影响到注射成型零件的性能。
注射成型有多种方法,它们的应用扩大了热塑性塑料在汽车工业的应用。
它们还创造了增加多种设计特征和优化材料利用率的机会。
这些方法当中的某一些(如嵌入成型和包容成型)是传统注射成型法的变型。
在嵌入成型中,在注射熔化的聚合物之前,先将少量的其他材料(如内螺纹金属插件、金属销和导电金属条)置于模膛中。
接着,将融化的聚合物注射到膜腔内,因此,聚合物会将预置的零件包裹起来,使它们与模制的零件成为一个整体。
在包容成型中,将熔化的聚合物注射到置于模膛内的一个金属框架上。
该金属框架上含有许多冲制的孔眼或突出的销钉,以便聚合物的固着。
这两种方法都会显著减少装配步骤、装配时间以及因此导致的装配成本。
对另外的一些注射成型法列举如下。
1)失芯注射成型法。
此成型法可使用一步成型操作生产具有复杂内部几何结构和切槽的空心注射成型零件(使用举例:
进气歧管)。
2)气压辅助注射成型法。
在这种方法中,液态聚合物部分注满模膛后,将压缩氮气注入液态聚合物内,从而在液态聚合物的心部形成一个空心通道。
随着氮气的前移,推动液态聚合物使之充满模膛的剩余空间。
零件重量、材料的使用量和夹紧力的减小,生产周期的缩短以及表面瑕疵的减少是气压辅助注射成型法的优点(使用举例:
车门摇把)。
3)结构泡沫注射成型法。
此方法用于生产表皮为聚合物薄壁实体结构、内芯为同种聚合物的泡沫结构的分层结构零件。
结构泡沫成型法的优点是可生产较高刚度/重量比的零件(应用举例:
仪表板)。
4)共同注射成型即分层成型法。
这种方法将两种不同但却相容的聚合物进行顺序注射或同时注射,从而生产由一种聚合物形成表层,而另一种聚合物形成芯部的层状结构零件。
这种层状结构具有单一聚合物不能实现的性能或成本的优越性(应用举例:
仪表板)。
5)多层注射成型法。
此法利用具有不同颜色的同种聚合物进行顺序注射来生产多色零件。
还可以对不同特性的聚合物进行过度注射成型,从而来生产多功能产品(应用举例:
多色尾灯配光镜)。
6)多孔注射成型法。
在这种方法中,将一种超临界气体(通常为氮气或二氧化碳)与液态聚合物混合,从而形成一种单相溶体。
在充模期间,该气体会在零件的内部形成极为均匀的微孔(直径为0.1~10μm)。
此泡沫化过程所产生的压力减轻了收缩和表面瑕疵(如陷落痕迹)。
将超临界气体与液态聚合物混合会大大减小聚合物的粘性,因而可以在较低的温度下和以较低的压力对零件进行成型。
另外,由于结构的泡沫化,减轻了零件的重量,并缩短了生产周期(应用举例:
内饰件)。
7)注射-压缩成型法。
此法将注射成型与压缩成型相结合,来生产零件。
首先使用注射成型,使模膛内部分充满液态聚合物。
当将模具的一侧前移,压缩液态聚合物之后,再完成后续的充模过程。
这样可使液态聚合物进入模膛的剩余部分,从而形成最终的厚度。
压注成型法能以比普通注射成型法低得多的压力和更短的生产周期,生产尺寸稳定、无残余应力的零件。
压注成型法用于制造表面精度高的薄壁零件,或者制造不容易进行注射成型的聚合物零件(应用举例:
车门模块托架)。
13.3轻量化汽车的连接技术
随着汽车轻量化的趋势愈来愈明显,汽车的车身材料正在从几乎全部是低碳钢向着多种材料(既有低碳钢,又有高强度钢、像铝合金和镁合金这样的轻质有色金属合金以及碳纤维增强聚合物)混杂使用转变。
对这些材料的认可程度将不仅取决于它们的结构性能和加工性能,还取决于将它们快速、牢固、可靠地装配到一起所使用的连接方法。
连接的结构性能取决于连接方法、连接几何参数和连接质量。
连接方法常常取决于被连接的材料,但是,在批量生产条件下,连接方法必须生产速度快,很少受到被连接零件的配合和尺寸变动的影响,并尽可能无缺陷。
在汽车设计中,连接是一个重要的考虑因素,因为连接处通常是结构的最薄弱处,因而在使用中,连接处常常成为失效的起始位置。
随着车身材料从单一材料向着混合材料转变,连接将成为一个更加重要的问题,因为在相互可连接性、表面特性、腐蚀、装配应力等方面,不同的材料之间的相容性可能会提出许多技术难题,因而在设计过程和材料选择中必须予以考虑。
由于在将来高强度钢和铝合金将成为车身结构的主要材料选择,本章将研究最适合于这两种材料的连接方法。
所研究的这些连接方法可分为四类:
液相焊接(即熔焊)、固相焊接、机械连接和粘接。
在这些连接方法中,有若干不同的可用技术(见表13-1)。
例如,液相焊接即熔焊包括电阻点焊(图13-4)、弧焊和激光焊。
气体保护金属极电弧焊(GMAW)(图13-5)和钨电极气体保护弧焊(GTAW)(图13-6)是两种最常用的电弧焊方法,但是还有许多其他的电弧焊方法,它们或用于特别的场合,或者用于受限制的应用场合。
在没有将材料熔化的情况下完成的固相焊接包括搅拌摩擦焊以及其他的几种刚刚出现的技术,如磁脉冲焊接和超声焊接。
机械连接包括采用螺栓和螺母的传统的机械连接方法,还包括像自穿孔铆接和冲铆这样的铆接新技术。
粘接也是一种成熟的连接方法,但将粘接与焊接或者铆接相结合的连接方法是一种较新的连接方法,并且特别是在空间构架车身结构设计中,将得到更为广泛的应用。
表13-1汽车工业中使用的各种金属板材连接方法
液相焊接
固相焊接
机械连接
粘接
·电阻点焊
·电弧焊
气体保护金属极电弧焊;
气体保护钨电极电弧焊;
焊剂芯电弧焊;
等离子电弧焊
·激光焊接
·搅拌摩擦焊
·搅拌摩擦点焊
·磁脉冲焊接
·超声焊接
·螺栓连接
·螺钉连接
·自穿孔铆接
·冲铆
·粘接
·粘接点焊
·粘接铆接
液相焊接的操作过程是,将待连接的两种材料局部加热到熔化,并对它们加压力,形成熔接,然后再在继续加压力的情况下,将熔接的液相材料冷却,从而形成连接点。
汽车工业使用的主要液相焊接方法是电阻点焊和电弧焊。
电阻点焊是用于低碳钢车身制造的主要连接方法。
图13-4电阻点焊(RSW0工艺
图13-5金属电极气体保护电弧焊(GMAW)工艺
图13-6惰性气体保护钨电极电弧焊(GTAW)
在固相焊接中,两张材质相同或不同的板材在材料没有熔化的情况下,通过形成冶金接合而连接起来。
由于在固相焊接中不会发生缩孔、晶粒边界开裂和其他的常常与液相焊接有关的问题,所以通常情况下,焊接质量非常好。
总体上讲,机械性能等同于甚至优于液相焊接。
另一个优点是,由于没有形成固化后会显著收缩的材料熔池,焊接后的零件变形和残余应力相对较小。
固相焊接不产生烟雾,并且没有电弧炫目或反射激光束,所以不会环境造成影响。
搅拌摩擦焊(FSW)和搅拌摩擦点焊(FSSW)是用于焊接钢、铝和各种其他金属材料的两种常见的固相焊接法。
这两种焊接法最初由英国焊接学会(TWI)开发。
FSW于1991年研究成功,此后,在汽车工业和飞机工业的铝合金焊接中得到了越来越广泛的应用。
FSSW后来开发成功,并在汽车工业中得到了越来越多的应用。
在这两种工艺中,通过旋转的焊接工具与待焊接的金属板之间产生的摩擦热,使焊接接头处的材料达到软化状态。
这两种工艺能够连接难以熔焊在一起的材料,例如,2000系列和6000系列铝合金。
FSW和FSSW的另一个主要优点是能耗低。
用摩擦搅拌焊焊接铝合金的电能消耗仅为RSW焊接的5%。
由于FSW不需要使用RSW所需要的大电流、冷却液和压缩空气,所以FSW总能量消耗大大减小。
自穿孔铆接的原理如图13-9所示。
自穿孔铆接工艺(图13-10)和无铆钉冲铆工艺(图13-11)也是汽车工业中金属连接所用的连接方法。
图13-7搅拌摩擦焊(FSW)工艺
图13-8搅拌摩擦点焊(FSSW)工艺
图13-9自穿孔铆接接头
图13-10自穿孔铆接(SPR)工艺过程
图13-11冲铆工艺过程
13.4All-newAudiA8Car’sAdvancedJoiningProcesses
全新奥迪A8轿车的先进连接工艺
全新2018年款奥迪A8轿车将广泛采用了铝合金,但是也使用钢、镁以及碳纤维增强聚合物(CFRP),见图13-12。
使用CFRP主要是为了减轻重量和提高扭转刚度。
同时,这款新车还将使用许多先进的连接工艺,见图13-13。
图13-12新款奥迪A8轿车多材料车身空间构架
图13-13新款奥迪A8轿车先进的连接工艺
奥迪A8轿车采用的技术中一个重要的方面是在车身装配中使用了14种不同的连接工艺。
这些环抱式滚压卷边、有铆钉冲铆和铝材的远距离激光焊接,铝材的远距离激光焊接是是世界上首次在内卡苏尔姆使用。
奥迪说,滚压卷边越来越多地用于前、后车门开口的周边处,,一方面提高乘客出入的方便性,另一方面改善了A立柱周围的驾驶员视野。
与2017年款相比,开口处的空间增加36mm。
将侧壁梁固定到位的夹持有铆钉冲铆与滚压卷边同时应用,滚压卷边可得到结构粘接的辅助加固。
开发和应用这些连接技术,在B立柱处将铝侧壁梁与热成型HSS板相结合,车顶两侧纵向条、门槛带有很小的翻边,奥迪为此而感到特别自豪。
铝材远距离激光焊接也是重要的连接技术应用。
据说,激光束相对于焊接边缘的精确定位“大幅”降低了热开裂的危险性。
在批量生产中,这项新工艺的应用不再需要采用昂贵的工艺控制,从而节省95%的返工成本。
该车的空间构架将由内卡苏尔姆工厂的新设备进行制造,生产线的机器人约有500套。