无凸缘圆筒形件冲压成形工艺及模具设计.doc
《无凸缘圆筒形件冲压成形工艺及模具设计.doc》由会员分享,可在线阅读,更多相关《无凸缘圆筒形件冲压成形工艺及模具设计.doc(24页珍藏版)》请在冰豆网上搜索。
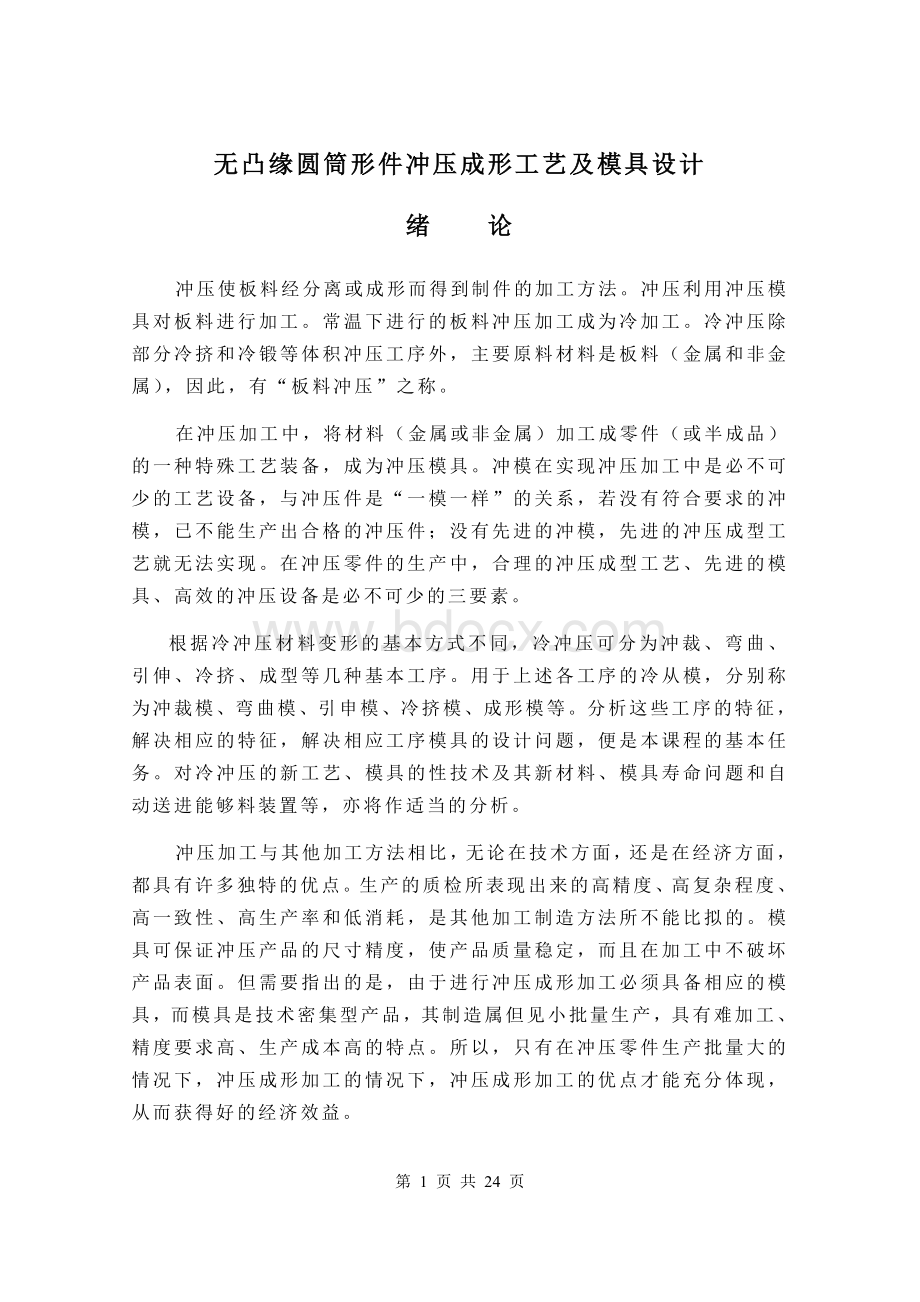
无凸缘圆筒形件冲压成形工艺及模具设计
绪论
冲压使板料经分离或成形而得到制件的加工方法。
冲压利用冲压模具对板料进行加工。
常温下进行的板料冲压加工成为冷加工。
冷冲压除部分冷挤和冷锻等体积冲压工序外,主要原料材料是板料(金属和非金属),因此,有“板料冲压”之称。
在冲压加工中,将材料(金属或非金属)加工成零件(或半成品)的一种特殊工艺装备,成为冲压模具。
冲模在实现冲压加工中是必不可少的工艺设备,与冲压件是“一模一样”的关系,若没有符合要求的冲模,已不能生产出合格的冲压件;没有先进的冲模,先进的冲压成型工艺就无法实现。
在冲压零件的生产中,合理的冲压成型工艺、先进的模具、高效的冲压设备是必不可少的三要素。
根据冷冲压材料变形的基本方式不同,冷冲压可分为冲裁、弯曲、引伸、冷挤、成型等几种基本工序。
用于上述各工序的冷从模,分别称为冲裁模、弯曲模、引申模、冷挤模、成形模等。
分析这些工序的特征,解决相应的特征,解决相应工序模具的设计问题,便是本课程的基本任务。
对冷冲压的新工艺、模具的性技术及其新材料、模具寿命问题和自动送进能够料装置等,亦将作适当的分析。
冲压加工与其他加工方法相比,无论在技术方面,还是在经济方面,都具有许多独特的优点。
生产的质检所表现出来的高精度、高复杂程度、高一致性、高生产率和低消耗,是其他加工制造方法所不能比拟的。
模具可保证冲压产品的尺寸精度,使产品质量稳定,而且在加工中不破坏产品表面。
但需要指出的是,由于进行冲压成形加工必须具备相应的模具,而模具是技术密集型产品,其制造属但见小批量生产,具有难加工、精度要求高、生产成本高的特点。
所以,只有在冲压零件生产批量大的情况下,冲压成形加工的情况下,冲压成形加工的优点才能充分体现,从而获得好的经济效益。
由于冲压加工具有上述突出的优点,因此在批量生产中得到了广泛的应用,在现代工业生产中占有十分重要的地位。
板料冲压加工在国民经济制造行业中占有十分重要的地位,在机械、电子、汽车、航空、轻工业(如自行车、照相机、五金、日用器皿等生产)等领域有广泛的应用。
由于冲压加工具有生产率高、生产成本低、操作简单、适合大批量生产等优点,在我国现代化建设中有着广阔的发展前景,因而需要大量的工程技术人员,国外发达国家对冲压加工技术的应用、研究和开发都比较重视。
我国也非常重视冲压技术人才的培养,全国除了有几十所设有金属塑性加工专业外,还有为数众多的专科学校、职业技术学校培养冲压工艺与模具的各级各类技术人才。
并且冲压是国防工业及民用工业生产中必不可少的加工方法。
模具使大批量生产同行产品的工具,是工业生产的主要工艺装备。
模具工业是国民经济的基础工业。
冷冲压的推广和发展少、无且屑加工是提高机械加工、提高生产率的技术发展方向。
介于模具是实现少、无切屑加工的重要工艺装备之一,因此,随着生产的高速度发展个冷冲压、精冲压、冷挤压、温(热)挤压、半液态挤压、旋压、爆炸成型等少、无且屑加工新工艺的推广使用,对模具的产量和质量提高到了很高的要求,许多企业因为模具影响来新工艺的应用,设置影响到产品试制或生产,以模具技术水平的先进与落后(主要表现在模具制造周期、使用寿命、模具制造精度及成本等四个方面)是能否多快、好、省的发展机电工业产品的关键,也是衡量工业发展程度的重要标志之一。
“产品要发展,模具是关键”这一点,应该引起我们的足够重视。
近年来,我国模具行业的广大工人、干部和技术人员,以实现四个现代化为奋斗目标,在模具结构、加工工艺新材料应用和模具使用等方面取得来可喜的成绩,为机电产品的生产和发展做出了贡献。
当前各种模具设计和制造技术的发展主要趋势是:
(1)模具的设计与结构纲要与成型工艺的高速自动精密化相适应,即发展高效率、高寿命、高精度的模具;
(2)积极开展标准化工作,扩大标准件范围,推行模具典型组合结构,最大限度地缩减模具临时的设计和制造工作量。
(3)采用计算机辅助设计,提高设计质量,缩短设计周期。
(4)减少模具制造中的手工操作比例,采用计算机辅助制造模具,提高加工自动化程度,发展电工技术,发展反馈控制自动仿行机床,扩大数控铣床的应用。
(5)发展各类建议模具及建议模具的各类材料,以适应小批和试制的生产需要;
(6)发展高强度、高寿命及特殊性能的模具钢材;
(7)发展模具表面处理工艺,提高寿命。
总的来说我国模具工业起步晚、基础差,就总量来看,大型、精密、复杂、长寿命模具产需矛盾仍然十分突出。
为了进一步振兴模具工业,国家有关部门进一步部署,相信在政府的大力支持下,通过本行业和相关行业以及广大模具工作者的共同努力,我国模具工业水平必将大大提高,为国家经济建设做出更大的贡献。
冲压模具设计与制造课程设计
1零件及其冲压工艺分析
图1-1
该零件为空心圆筒形件的拉深,形状简单对称,所有尺寸均为自由公差,对零件的厚度变化也没有要求。
在满足工艺性要求时,进行大批量生产,一般采用拉深成形。
圆筒形件的毛坯为圆形板料,可以通过落料获得。
因此,该零件在满足冲压工艺性要求的前提下,采用的冲压工
序是落料、拉深,可在最后再安排一道修边工序达到要求。
该零件的外径为φ20,精度等级为IT14级,拉深工艺容易保证。
该零件的圆角半径R2能满足拉深工艺对该处圆角的要求。
[R≧(2—3)t]
上所述,该零件的精度及结构尺寸都能满足冲压工艺要求。
在大批量生产时,可用冲压加工。
冲压的基本工序是落料拉深。
1.1工艺计算
由图可知,因为材料的厚度是0.5㎜,所以:
零件的直径为d﹦20-﹦㎜
零件的高度为h﹦10-=㎜
圆角的半径为r﹦2㎜
料的厚度为 t﹦0.5㎜
图1-2
1.2毛坯尺寸的计算
由于板料的厚度是0.5㎜,故可直接但工件的尺寸计算,不必按中心线尺寸计算。
因此:
﹦
查《实用冲压技术手册》表4-4[10]。
可查得:
修边余量δ﹦1㎜则
H﹦h+δ﹦+1﹦㎜
依据圆筒形件拉深时的毛坯尺寸计算公式(式4—1)[10]为:
将㎜,㎜,㎜代入上式中,即得毛坯的直径为:
㎜
1.3拉深次数的确定
1.3.1确定是否用压边圈
因
由《冲压模具设计与制造》表4.4.4[3]可查得:
可以不用压边圈,但是为了保险起见,首次拉深仍采用压料圈。
采用压料圈后,首次拉深可以选择较小的拉深系数,有利于减少拉深次数。
查表4.4.3[5]可得极限拉深系数:
﹦0.50~0.53取﹦0.53
﹦0.75~0.76取﹦0.76
零件所需的拉深系数:
﹦
所以该零件能一次拉深成形。
2工艺方案的确定
根据以上分析,冲压该零件可能有以下三种方案:
方案一:
先落料,后拉深。
采用单工序模生产。
单工序模易于制造和维修,模具在冲床上安装时,调整间隙的均匀度困难,凸模与凹模的相对正确位置只能靠冲床导轨与滑块的配合精度来保证,因此模具的导向精度低,使用安全性差,不是与薄板料的冲裁。
虽然模具结构简单,但需两道工序两副模具,生产效率低,难以满足该工件大批量生产的要求
方案二:
落料—拉深复合模。
采用复合模生产。
调料在复合模中进行冲裁时,一次定位就可以完成冲裁件的内外形尺寸,故制件的内外形的位置尺寸精度高,生产效率高、生产效率高,适合位置精度高、生产批量大的制件选用。
但这种模具结构复杂,制造困难、周期长,当制件内外形尺寸像差较小时也不宜选用复合模。
复合模结构上的特点是具有既是落料凸模又是冲孔凹模的所谓凸凹模。
利用复合模能够在模具的同一部位上同时完成制件的落料和冲孔工序,从未而保证冲裁件的内孔与外援的相对位置精度和平整性、生产效率高;而且条料的定位精度比连续模低,模具轮廓尺寸也比连续模小。
但是,模具结构复杂,不易制造,成本高,适合于大批量的生产。
而且只需一副模具,生产效率高,尽管模具结构较方案一复杂,但由于零件的几何形状简单对称,模具制造并不困难
方案三:
拉深级进冲压。
采用级进模生产。
压力机一次冲程中,在模具不同部位上同时完成数道冲裁工序的模具,称为连续模。
使用连续模可以减少模具和设备数量,提高生产效率,而且容易实现生产自动化。
但连续模比简单模制造复杂,成本也高。
虽然只需一副模具,生产效率高,但模具结构比较复杂,送进操作不方便。
通过对上述方案的分析比较,该件若能一次拉深,则其冲压采用方案二为佳[9]。
3主要工艺参数的计算
3.1毛坯尺寸的计算
根据表面积相等原则,有解析法求该零件的毛坯直径D。
已求得
D﹦㎜
3.2排样及相关尺寸的计算
根据零件的工艺性的要求,采用有废料直排的排样方式,排样图3-3所示如下:
3.2.1冲裁件面积的计算
㎜
3.2.2板料厚度是t﹦0.5㎜,则表2.5.2可查得
工件间的搭边值:
﹦1.2㎜
侧面间的搭边值:
﹦1.5㎜
条料与导料板的间隙:
﹦0.5㎜
因此条料宽度的值如下:
㎜
3.2.3步距[3]
㎜
3.2.4一个步距内材料的利用率[3]
η﹦
3.2.5成形次数的确定
由前所述,零件可一次拉深成形,所以采用落料—拉深复合模。
3.3冲压工序压力的计算
3.3.1计算压边力
由表4.24[3]确定压边力的计算:
式中,㎜,㎜,由表4.25查得:
。
把各已知数据代入上式,得压力为:
3.3.2计算压边力
查表4.17[3]计算拉深力
已知,由表4.18查得,。
代入上式得 N
3.3.3计算冲裁力
[3]
已知㎜,,㎜,代入上式为
3.3.4综合以上计算可得总的冲压力
N
故 =++=N
因该副模具采用的是正装的复合模,固定卸料与推件。
3.3.5选用冲压设备
设备类型选择的主要依据是所完成的从压工序性质、生产批量、冲压件的尺寸及精度要求、现有设备条件等。
中小型冲压件主要选用开式单柱(或双柱)的机械压力机;大、中型冲压件多选用双柱闭式的机械压力机。
根据冲压工序可分别选用通用压力机、专用压力机(挤压压力机、精压力、双动拉伸压力机等);大批量生产时,可选用高速压力机或多工位自动压力机;小批量生产,尤其大型后半零件的成行时,可采用液压机。
压力机技术参数选择主要依据是冲压件尺寸、变形力大小及模具尺寸,并进行必要效核。
压力机的行程,必须保证成型备料能够放入、成型零件能够取出。
压力机的装模空间必须与冲模总体结构尺寸相适应。
压力机工作台面的尺寸应大于模具的总体平面尺寸,并留有安装固定的余地。
压力机的装模高度货币和高度应与模具的闭合(封闭)高度相适应。
模具与压力机相关的尺寸以在以上算出来。
冲模的闭合高度是指指模具工作形成终了时,上模座的上平面只小木做得下平面之间的距离。
而压力机装模高度是指压力机滑块在下止点时,滑块下平面之垫板上平面之间的距离。
封闭高度和装模高度相差一个垫板厚度。
没有垫板的压力机,其封闭高度与装模高度相等。
冲模的封闭高度必须在压力机的最大装模高度和最小装模高度之间。
一般取:
式中:
——压力机最大封闭高度(㎜);
——压力机最小封闭高度(㎜);
——冲模的封闭高度(㎜);
——垫板高度(㎜)。
根据冲压工艺力计算结果并结合工件高度,初选开式双柱可倾压力机。
其参数如下:
公称压力:
25吨
滑块行程: