公用工程用能分析.docx
《公用工程用能分析.docx》由会员分享,可在线阅读,更多相关《公用工程用能分析.docx(12页珍藏版)》请在冰豆网上搜索。
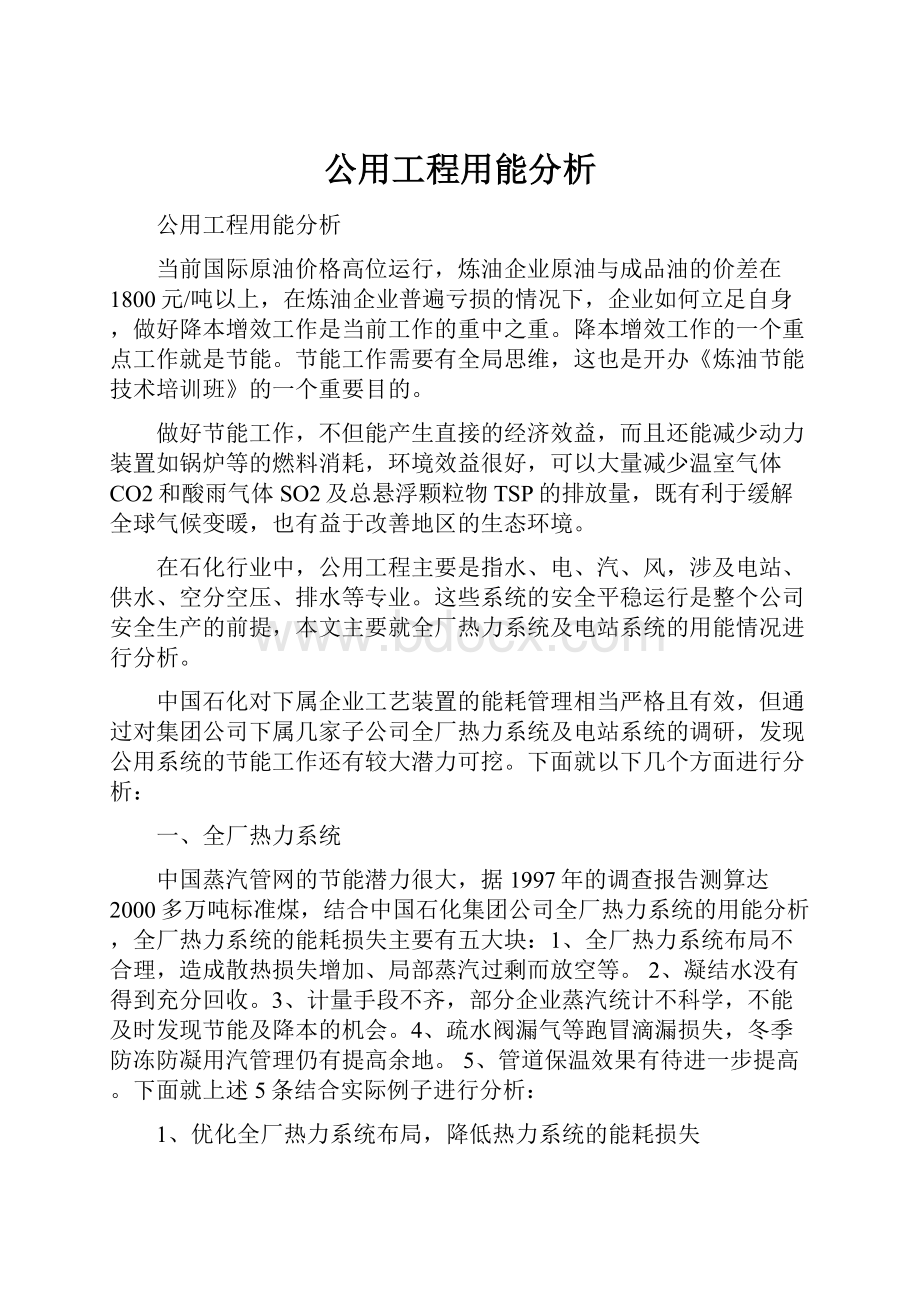
公用工程用能分析
公用工程用能分析
当前国际原油价格高位运行,炼油企业原油与成品油的价差在1800元/吨以上,在炼油企业普遍亏损的情况下,企业如何立足自身,做好降本增效工作是当前工作的重中之重。
降本增效工作的一个重点工作就是节能。
节能工作需要有全局思维,这也是开办《炼油节能技术培训班》的一个重要目的。
做好节能工作,不但能产生直接的经济效益,而且还能减少动力装置如锅炉等的燃料消耗,环境效益很好,可以大量减少温室气体CO2和酸雨气体SO2及总悬浮颗粒物TSP的排放量,既有利于缓解全球气候变暖,也有益于改善地区的生态环境。
在石化行业中,公用工程主要是指水、电、汽、风,涉及电站、供水、空分空压、排水等专业。
这些系统的安全平稳运行是整个公司安全生产的前提,本文主要就全厂热力系统及电站系统的用能情况进行分析。
中国石化对下属企业工艺装置的能耗管理相当严格且有效,但通过对集团公司下属几家子公司全厂热力系统及电站系统的调研,发现公用系统的节能工作还有较大潜力可挖。
下面就以下几个方面进行分析:
一、全厂热力系统
中国蒸汽管网的节能潜力很大,据1997年的调查报告测算达2000多万吨标准煤,结合中国石化集团公司全厂热力系统的用能分析,全厂热力系统的能耗损失主要有五大块:
1、全厂热力系统布局不合理,造成散热损失增加、局部蒸汽过剩而放空等。
2、凝结水没有得到充分回收。
3、计量手段不齐,部分企业蒸汽统计不科学,不能及时发现节能及降本的机会。
4、疏水阀漏气等跑冒滴漏损失,冬季防冻防凝用汽管理仍有提高余地。
5、管道保温效果有待进一步提高。
下面就上述5条结合实际例子进行分析:
1、优化全厂热力系统布局,降低热力系统的能耗损失
中石化旗下的不少企业是经历几十年逐步发展起来的,虽然当年对全厂热力系统的布局也做了全面的技术经济分析,采取了相对最优化的方案,但在涉及投资控制时,公用工程总是压缩投资的优先对象,所以从能耗分析的角度看,热力系统的布局还是存在相当多的问题,这也是企业能耗损失大的一个重要原因。
全厂热力系统布局不合理,主要问题有:
(1)局部蒸汽放空,造成极大的能耗损失。
如我所在企业在2000-2002年,新区扩建后1.0Mpa蒸汽有多余,虽然已有联络线,但输送量有限,二催化装置的气压机背压偏高,新区的1.0Mpa蒸汽在夏季仍有部分放空。
解决方案:
①新增一条管线,引新区的1.0Mpa蒸汽至老区。
②优化操作,提高3.5Mpa蒸汽进二催化装置气压机的参数,满足气压机的做功需要。
(2)部分企业减温减压器布置较多且带量运行,有用功损耗极大。
主要原因:
①不少减温减压器因减温水调节阀内漏严重,必须带量运行;②有些因管线流通或瓶颈问题,不得不带一定的负荷。
③抽汽机组运行不稳定,抽汽量受制约。
减温减压器带量运行,带来巨大的有用功损失,如果1t/h蒸汽从3.5Mpa蒸汽减温减压至1.0Mpa与通过汽轮机组抽汽或背压机组供汽,全年将产生30多万元/年的收益。
解决方案:
①优化减温减压器的运行,停用部分减温减压器。
如我所在企业就停用了新区CFB锅炉区域的高/低减温减压器,当然这需要承担一旦汽轮机组故障,不能及时投用低压蒸汽的风险。
②消除瓶颈,取消部分减温减压器。
③解决汽轮机组投用抽汽后的调节系统稳定性问题。
④将部分质量不好国产减温减压器更换为进口的多级降压的减温减压器,减少热备流量。
(3)蒸汽输送距离长,散热损失大。
如我所在企业,动力中心有三块,为应对事故的冲击,三个区域的蒸汽保持联通。
由于蒸汽与水不一样,蒸汽管线必须维持一定的流通量,否则蒸汽管线温度将大幅降低,不能起到事故状况下的备用作用,所以蒸汽母管(Dn300mm以上)的流通量庆保持在15t/h以上。
这造成蒸汽管线输送距离长,散热损失增加,管网线损增加。
如我所以企业新老区之间的3.5Mpa蒸汽返送汽管线距离近2公里,中间用户使用30t/h后,因受新区锅炉容量限制及新区二催化余热锅炉的汽包压力限制,正常情况下送至老区的蒸汽量只有15至25t/h,蒸汽温度从435℃降至390至405℃。
解决方案:
①新区2×220t/h的CFB锅炉扩能,提高蒸汽产量,目前已通过CFB锅炉的扩能试验,锅炉供应商FW公司已提供了书面的证明,待技监局批准后,可解决蒸汽产量不足的问题。
②二催化装置余热锅炉的汽包安全阀重新定压,尽可能提至设计的上限。
③新区处于扩建期间,新区的3.5Mpa蒸汽用户增加,3.5Mpa蒸汽压力自然可逐步下降。
④在适当的时机,在新区的CFB锅炉区域新增锅炉,将新区的CFB锅炉装置建成炼油区域的动力中心,改变全厂热力系统的格局。
(4)装置自产蒸汽与自用蒸汽基本平衡,蒸汽流通成问题。
如某企业因装置自产3.5Mpa蒸汽量只有1t/h,蒸汽无法外送,最终只能通过新增减温减压器解决流通量问题。
(5)蒸汽管网存在瓶颈问题。
随着装置的扩建或成本优化等原因,原有的蒸汽输送管线不能满足现有的需要。
如我所在企业化肥区域的煤代油项目上马后,设计时考虑送炼油区域的蒸汽不到130t/h,但现在化肥区域三电站2×410t/h的CFB锅炉扩能至2×450t/h后,同时现在因浙江不再缺电,发电不能上网,蒸汽输送量提高至140t/h后就无法进一步提高,制约了CFB锅炉蒸汽负荷率。
解决方案:
在适当时机新增一条管线,提高蒸汽输送量,但蒸汽管线的接入位置综合考虑全厂热力系统后建议接至新区的CFB锅炉动力中心。
全厂热力系统的布局合理与否,以全厂综合规划准确为前提条件,然后充分考虑各用户蒸汽的能级需要,对热力系统的布局进行优化。
全厂热力系统布置时应考虑这几点:
(1)动力中心应布置在中心,用汽大户应尽可能就近布置。
(2)管网压力等级设置应尽可能少,以方便布置及操作。
(3)一般应尽可能少建立低压的热力管网。
因为低压管网的输送能力低,管损大,但如就近有低能级的产耗用户,也可在小范围内建立低压如0.45Mpa甚至更低压力的蒸汽管网,提高蒸汽的综合利用能力。
(4)减少并集中布置减温减压器,以利于优化运行,尽可能使减温压器热备运行。
(5)蒸汽母管的管径设置应兼顾此沿路工艺装置的发展前景及现实运行这二种工况,运用技术经济比较方法确定管径的大小。
2、提高凝结水回收率
据中国节能服务网报道,中国蒸汽管网产生的高温凝结水约有70%被丢弃,另外的30%是降温回收的,主要原因是水泵汽蚀问题未能解决。
目前集团公司下属企业的凝结水回收率也很低,不少企业凝结水回收率不到50%,如某企业的凝结水回收率报表上数据为50%,但通过对蒸汽报表及凝结水报表的对比分析,发现实际回收率只有40%。
中石化下属企业中,凝结水回收率在60%以上就已经是先进水平了,这说明我们在这方面仍有很大的潜力。
凝结水回收率低的原因主要是:
(1)部分企业建厂年代早,设计时对凝结水回收没有通盘考虑;
(2)伴热管线等疏水分散,回收成本高。
(3)装置工艺凝结水含油等杂质冲击,造成凝结水回收装置大量溢流。
(4)凝结水回收装置的精密过滤器反冼频率高。
(5)凝结水回收站的余热再利用困难,原因是余热量不稳定且凝结水可能携带杂质,致使寻找余热用户困难。
(6)高温凝结水先降温再回收,能量损失。
(7)凝结水价格扭曲,凝结水价格不少企业的内部价格只有8元/吨,甚至更少,导致部分凝结水因技术经济比较没有收益而未回收。
根据上面分析的原因,可采取以下应对措施:
(1)通过分析,在全厂范围内按凝结水不同品质建立几个凝结水回收中心,使凝结水按区域及品质实施回收,降低回收成本。
如我所在企业就建立了三个凝结水回收中心,其中一个为透平凝结水,二个为工艺凝结水。
(2)建立凝结水回收母管(一次投资较高)方便凝结水的回收。
如扬子石化的凝结水回收工作就做得相当好,通过敷设凝结水回收母管,凝结水集中排放至收集区,极大提高了凝结水的回收率。
(3)各种伴热疏水等设计时就应充分考虑凝结水回收的距离,以利用凝结水回收。
如也可将伴热管线分成二段设置,使疏水点靠近凝结水回收站。
(4)按市场价格核算凝结水的价格,为回收凝结水技术经济比较提供准确依据。
目前凝结水的价格均为内部价格,大多数凝结水价格在8元/吨左右,不能准确反映凝结水的实际价格。
凝结水的价格应考虑水价、水处理费、热量价值、人工费、折旧的因素,据1996年国家统计数据,北京凝结水的价格为25元/吨。
如某企业生活区有3t/h的凝结水未回收,是因为距离远,投资高达50万元,回收运行成本高。
但如果凝结水价格提高至25元/吨,那么回收的经济效益就相当可观了。
(5)加强对工艺凝结水的质量分析,及时发现凝结水水质不合格,快速查清源头并切出检修,减少对凝结水回收装置的冲击,减少溢流量。
(6)建议工艺凝结水尽量回收至中、低蒸汽锅炉除氧器。
因为有机物如油等在锅炉汽包内积聚到一定程度会发生降解,导致PH大幅下降,高压锅炉降解的程度明显强于中压锅炉。
如我所在企业有一次受到凝结水含油冲击,中压锅炉炉水品质没有明显恶化,但高压锅炉炉水PH值大幅下降,最终通过直接加NaOH溶液才控制住炉水的PH值。
(7)控制源头---凝结水的杂质含量,选用合适的滤芯材质及过滤网孔隙,减少凝结水回收站精密过滤器反洗频率。
此问题的关健还是控制源头凝结水的杂质,包括保证前期回收管道的冲洗质量、通过预防性检修控制换热器的泄漏等。
(8)通过对全厂用能的分析,查找需要低温热的地方。
如利用余热加热除盐水等。
(9)应用新技术,提高凝结水中的热量回收。
现在国内已开发成功消除水泵汽蚀的技术和设备,能够将200℃以下的凝结水连同二次汽一起封闭式回收,送到锅炉或除氧器使用;国外也有不用水泵的凝结水回收技术和设备进入中国使用。
两种技术和设备均有一批成功的案例。
100-200℃凝结水(饱和水)的热焓是同温度饱和蒸汽热焓的15%-30%,考虑到燃煤为主的中国国情,计入锅炉的热效率,回收这段温度的凝结水,至少可以节约等量的锅炉燃煤,同时节约回收凝结水等量的水资源及其净化处理费用,技术改造资金不足1年即可回收。
蒸汽凝结水直接密闭回收系统示意图
1-蒸汽锅炉 2-用热设备 3-集中疏水器
4-凝结水回收器(带高温水泵) 5-除氧器(低位、带高温水泵或高位)
3、完善计量手段,建立完整蒸汽产耗分析报表,为寻找节能机会提供科学依据。
集团公司下属企业不少因为投入少,蒸汽系统的计量不齐全,很多装置的蒸汽用量只能估算,不能准确反映装置的能耗水平,也不利用分析节能管理工作存在的问题。
有部分企业对蒸汽统计报表重视程度不足,在已经考虑线损的情况下,甚至产耗也未做平衡。
分析技术原因主要是把产与供等同考虑,在蒸汽统计报表中,只需考虑产的情况,而不能将供的产量计入,导致分析不准。
建议:
(1)先完善部分重要的蒸汽计量。
(2)完善蒸汽产耗统计报表,为技术经济分析提供依据。
如某企业的减温减压器流量没有计量,原认为夏季减温减压器的流量在5t/h左右。
最终减温减压器蒸汽流量只能通过蒸汽平衡来反推,通过发电用汽量及各装置用汽量反推,发现其3.5Mpa蒸汽通过减温减压器至1.0Mpa的蒸汽量相当大,2005年夏季高温季节仍至少有25.0t/h的蒸汽通过减减温减压器外供,如果减少减温减压器外供蒸汽负荷20t/h,效益高达720万元/年。
2005年8月
2005年9月
2005年7月
2006年1月
3.5MPa蒸汽
产
1#炉
22.3
6.9
11.6
11.3
2#炉
0.0
0.0
0.0
1.4
3#炉
31.9
31.3
17.5
35.9
2#催化
43.9
42.3
41.1
43.7
汇总
98.1
80.5
70.2
92.2
耗
制氢减温减压器
0.7
0.7
0.7
0.7
动力减温减压器
29.0
25.0
29.5
42.4
1#机
0.0
0.0
0.0
41.1
2#机
22.7
11.8
21.7
0.5
3#机
40.3
38.9
12.9
2.1
线损
5.4
4.2
5.4
5.4
汇总
98.1
80.5
70.2
92.2
某企业蒸汽平衡反推后的3.5Mpa蒸汽报表
4、消除疏水阀漏汽等跑冒滴漏损失,统筹把握好节能与防冻防凝工作的关系,降低蒸汽损失。
据调查,中国蒸汽供热系统使用的疏水阀,绝大部分存在着不同程度的漏汽,不仅影响生产工艺和生产环境,还浪费大量锅炉燃料和水资源。
类似问题在中石化也存在,而且有些部位还存在跑冒滴漏损失,如在某企业检查发现动力作业部连排扩容器的安全阀泄漏,询问为连排至除氧器的汽平衡阀关不严而未检修。
冬季防冻防凝时,蒸汽消耗大幅增加,但把握好节能与防冻防凝工作的度,仍有较大的节能潜力。
疏水阀漏汽从技术角度看,除国产疏水阀质量不好之外,还有设计不合理造成的使用不当问题;但大多数跑冒滴漏问题与冬季防冻防凝工作过头问题属于管理问题。
近几年国内已开发成功集中疏水技术和相应的设备,已在一批企业中成功使用。
按原疏水阀运行状况不同,技术改造后,可以减少10%-30%的蒸汽消费量,节能效果很好,还可以减少系统建设初投资和长年的疏水阀维修费,技术改造投资半年左右即可收回。
跑冒滴漏及防冻防凝的损失应通过制定明确可行的管理制度或规范进行约束,加强检查与考核,还是很容易消除的。
如我所在企业2005年冬季,公司通过加强检查与考核,冬季的防冻防凝用汽量从70t/h减少至65t/h,效益明显。
5、改善管道保温,减少散热损失
通过检查,发现集团公司下属企业对公用系统投入不足,现用的蒸汽管网(含热水管网)有许多保温层陈旧、脱落,部分阀门无保温,部分保温材料性能也差。
如有些企业,管道保温效果优秀的,3.5Mpa蒸汽外壁温度与气温差只有2℃,而一般这个温度差在10-16℃,部分保温不好的就超过20℃,甚至达到60℃,所以节能潜力巨大。
如前所述我所在企业从新区返送老区的3.5Mpa蒸汽温度降达到30至45℃,相当于损失2.1-3.1%的3.5Mpa蒸汽。
建议:
(1)定期检测蒸汽管线的外壁温度,对局部保温效果较差的部位及时检修或更换保温,减少蒸汽管线的散热损失。
(2)在管道施工时加强对保温施工质量的管理,尤其是对保温缝隙的控制。
(3)建议蒸汽管道保温施工费根据投用后保温外壁温度与气温差考虑系数,调动施工人员积极性。
(4)选用优质保温材料,完善管网保温。
二、电站系统
电站系统主要由机、炉、电、化、燃料五大部分组成。
电站的设计由于有专业设计院,配置也相对固定,技术的成熟度相当高,整体优化的水平也相对较高,但在石化集团下属企业的一些小电站建设时,因为容量小且受投资控制,所以系统配置也未做到最优化,导致运行过程中仍有不少工作可做。
1、电力系统主要问题及解决措施如下:
(1)低压长距离送电改为高压长距离、低压短距离送电,减少送电线路的损耗。
企业的用电设备远离配电中心,使得低压(0.4千伏)送电距离过长,造成很大的线路损耗和电压降落。
这种情况在旧的大、中型企业中普遍存在,原因是当时设计规定配电中心要建在企业的引进电源的一端。
改善的措施是在保证安全的前提下,尽量移近配电中心与用电设备的距离,将原来低压长距离送电改为高压长距离、低压短距离送电,可以大大减少送电线路的损耗。
(2)增加补偿电容,改变无功功率短缺现状,减少线路损耗。
随着经济的发展,供配电系统中感性负荷迅速增加,众多的配电变压器和电动机处于低负荷率的非经济运行状态,造成供配电系统无功功率的大量需求,如不及时补充,将引起供电电压质量下降,系统损耗增加,既要浪费电能,又将影响供配电设备的使用率,甚至造成事故。
解决以上问题的技术措施是在供电方和用电方加装补偿电容,前者称集中补偿,直接受益者是供电部门,用户的效益来自少受功率因数不达标的罚款;后者称为就地补偿,直接受益者是用户,主要是减少线路损耗。
无功补偿的效益除上述之外,还可以增大发电机、变压器等设备的利用率,降低供电成本,提高系统运行的安全性。
(3)选用新型配电设备,降低损耗。
我国在用的配电设备如配电变压器及各类开关,许多是陈旧落后的,由于资金不足和相关部门节能意识不够等原因,不能及时更新,结果浪费了大量电能。
如配电变压器的空载损耗60年代初的ST型变压器是70年代初期产品S1型变压器的1.32倍,S1系列又比S6系列的大约14%,而90年代后期以前应用的S7系列变压器又比S6系列的小45%,90年代末国家推广使用的S9系列变压器的空载损耗和负载损耗更小。
其它如电磁开关、电缆接头及连接金具等情形类似。
如能及时更新这些陈旧落后的配电设备,可使配电系统减少大量无谓的电能浪费。
2、提高抽汽比(包括背压汽),降低减温压器蒸汽负荷,减少排汽损失。
如:
某企业通过蒸汽平衡反推,发现动力车间3.5Mpa蒸汽通过减温减压器至1.0Mpa的蒸汽量相当大,2005年在25.7t/h至43.1t/h之间,为保证蒸汽系统的安全运行,动力车间的减温减压器必须保持3至5t/h的热备量,推算至少可将平均20t/h的蒸汽通过2、3#机的抽汽或1#背压机来提供1.0Mpa蒸汽。
但目前受锅炉低蒸汽负荷限制,不能同时维持1#背压机及2或3#机运行,所以不能长期运行1#背压机。
2#机抽汽工况不甚稳定,而且设计负荷只有6000KW,不能满足瓦斯量大时锅炉蒸汽负荷被迫增加的需要。
而3#机为12MW的机组,能满足平衡瓦斯的需要,但抽汽管线因系统不能停用而未碰头,不能投用抽汽。
建议:
(1)根据蒸汽平衡,安排1#背压机的运行,但不能频启停1#背压机。
(2)将3#机的抽汽管线先接至2#机抽汽管线出口的二个隔离阀之间,为保证安全,2#机抽汽管线还需增加一个隔离阀,约10万元。
(3)投入3#机抽汽系统,调试3#机的抽汽运行工况,达到平稳运行。
效益:
3#机因无设计资料,3#机的效率按78%估算,每1kw的发电量必须要有4615KJ的焓降,沧州分公司提供的3.5MPa蒸汽焓为3350KJ/kg,1.0MPa蒸汽焓为3080KJ/kg,120℃减温水(除氧水)焓为507.9KJ/kg,1.0MPa蒸汽按111元/吨,排汽焓按2370KJ/kg计算。
(1)通过减温减压生产20t/h的1.0MPa蒸汽需要3.5MPa蒸汽量为(3080-507.9)/(3350-507.9)*20=18.1t/h
(2)18.1t/h的3.5MPa蒸汽通过汽轮机发电后从1.0MPa抽汽口抽出供工艺装置,可多发电18.1*(3350-3080)/4615=1.06MW。
全年按365天运行时间计算,电价为0.42元/度,可产生效益365*24*1.06*1000*0.42/10000=389.6万元/年
(3)用来发电的蒸汽消耗:
发电所消耗的热值折算成1.0MPa蒸汽量为18.1*(3350-3080)/3080=1.6t/h。
(4)发电1.06MW减少排汽损失热值折算成1.0Mpa蒸汽量:
1.06*4615/(3350-2370)=5.0t/h。
综合二者,可减少1.0MPa蒸汽量为3.4t/h,这些蒸汽的产生的收益为365*24*3.4*111/10000=330.6万元/年。
(5)总收益为389.6+330.6=720.2万元/年
3、提高给水高压加热器的投用率,逐级利用疏水,提高汽轮机组的回热效率。
如:
某企业动力车间新增的高压加热器因1、2、3#锅炉不能全停,至今未完成给水侧的碰头工作,降低了汽轮机组的回热效率。
建议:
(1)创造条件,择机全停1、2、3#锅炉,完成高压加热器给水管线的碰头工作,为投用高压加热器创造条件。
(2)用于高压加热器加热的蒸汽必须来源于抽汽,这是投用高压加热器的前提,否则没有效益。
效益:
全年锅炉给水量平均按30t/h计算,给水温度从目前的120℃提高至160℃,高压加热器使用1.0Mpa蒸汽加热,焓值为3080kJ/kg,疏水温度按170℃,焓值为724kJ/kg。
1.0Mpa蒸汽价值为111¥/t。
(1)则用于高压加热器的1.0Mpa蒸汽流量为30*(160-120)*4.186/(3080-724)=2.13t/h。
汽轮机组的排汽焓按2370kJ/kg估算,抽出2.13t/h蒸汽可减少排汽损失的热量折算成1.0Mpa蒸汽为2.13*2370/3080=1.64t/h。
(2)由于给水温度提高,将提高锅炉的排烟温度,排烟温度估算将提高10℃,少产蒸汽折算成1.0Mpa蒸汽为30*6.708%*10/152.8*3350/3080=0.14t/h。
(3)增加1.0Mpa蒸汽量为1.64-0.14=1.5t/h。
增加效益为1.5*365*24*111/10000=145.3万元/年。
4、降低锅炉氧量,减少锅炉排烟损失,提高锅炉效率。
如:
某企业检查现场氧量仪,130t/h锅炉的数据为4.5至7.3%(v),氧量控制过高。
氧量控制过高原因,作业部反映是锅炉负荷低及避免烟囱冒黑烟。
现在检查发现没有氧量自动控制器。
锅炉设计氧量为3%,因锅炉运行负荷较低,建议控制在3.5%。
65t/h锅炉3#炉氧量仪坏,查报表,氧量控制平均在7%左右,4#锅炉进PSA尾气后,燃烧效果差,100%额定负荷时氧量仍有7%,正常运行时达10%,需要改造单位攻关解决。
锅炉设计氧量为2.6%,因锅炉运行负荷较低,建议控制在3.5%。
建议:
(1)首先加强操作管理,及时调整送风机档板开度,控制氧量。
建议公司规定一个氧量控制指标,达到后给予奖励,达不到考核。
(2)增加一个氧量控制器(可以公司内部利旧),用氧量自动调节送风机档板。
(3)4#锅炉要请改造厂家核实,解决冒黑烟问题。
(4)3#锅炉的氧量分析仪必须尽快修复。
效益:
(1)130t/h锅炉氧量平均按5.9%计算,从理论上至少可控制到3%,平均控制在3.5%,可减少烟气量11.43%,锅炉设计排烟损失为6.65%,可减少排烟损失为6.65%*11.43%=0.760%。
二台锅炉总计负荷按70t/h计算,可节省渣油0.0364t/h,渣油按每吨2000元计算,两台130t/h锅炉可增效益为0.0364*24*365*2000=63.8万元/年。
(2)65t/h锅炉氧量平均按7%计算,从理论上至少可控制到2.6%,平均控制在3.5%,可减少烟气量16.67%,锅炉设计排烟损失为5.38%,可减少排烟损失=5.38%*16.67%=0.897%。