精馏塔很实用设计论文.docx
《精馏塔很实用设计论文.docx》由会员分享,可在线阅读,更多相关《精馏塔很实用设计论文.docx(50页珍藏版)》请在冰豆网上搜索。
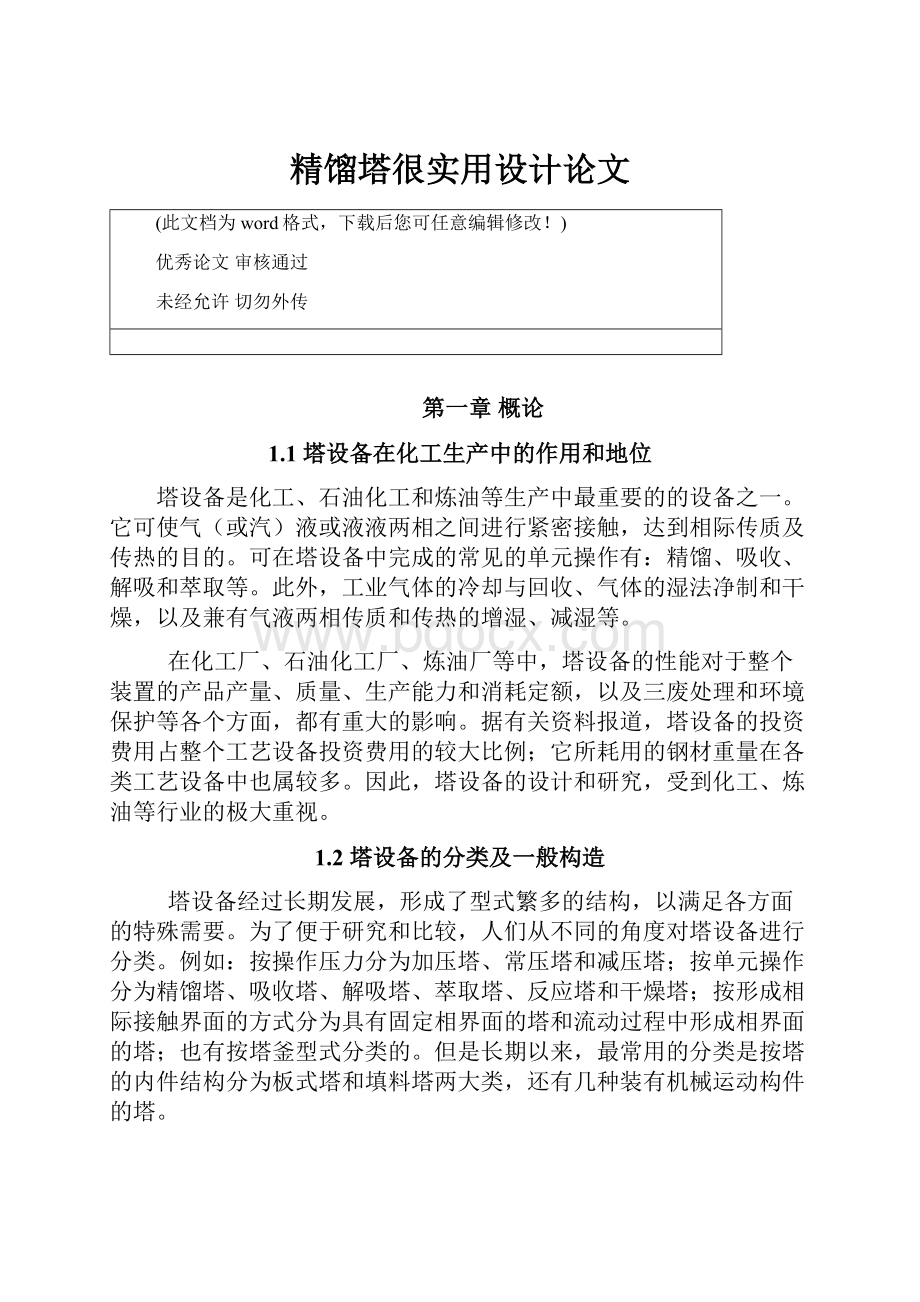
精馏塔很实用设计论文
(此文档为word格式,下载后您可任意编辑修改!
)
优秀论文审核通过
未经允许切勿外传
第一章概论
1.1塔设备在化工生产中的作用和地位
塔设备是化工、石油化工和炼油等生产中最重要的的设备之一。
它可使气(或汽)液或液液两相之间进行紧密接触,达到相际传质及传热的目的。
可在塔设备中完成的常见的单元操作有:
精馏、吸收、解吸和萃取等。
此外,工业气体的冷却与回收、气体的湿法净制和干燥,以及兼有气液两相传质和传热的增湿、减湿等。
在化工厂、石油化工厂、炼油厂等中,塔设备的性能对于整个装置的产品产量、质量、生产能力和消耗定额,以及三废处理和环境保护等各个方面,都有重大的影响。
据有关资料报道,塔设备的投资费用占整个工艺设备投资费用的较大比例;它所耗用的钢材重量在各类工艺设备中也属较多。
因此,塔设备的设计和研究,受到化工、炼油等行业的极大重视。
1.2塔设备的分类及一般构造
塔设备经过长期发展,形成了型式繁多的结构,以满足各方面的特殊需要。
为了便于研究和比较,人们从不同的角度对塔设备进行分类。
例如:
按操作压力分为加压塔、常压塔和减压塔;按单元操作分为精馏塔、吸收塔、解吸塔、萃取塔、反应塔和干燥塔;按形成相际接触界面的方式分为具有固定相界面的塔和流动过程中形成相界面的塔;也有按塔釜型式分类的。
但是长期以来,最常用的分类是按塔的内件结构分为板式塔和填料塔两大类,还有几种装有机械运动构件的塔。
在板式塔中,塔内装有一定数量的塔盘,气体以鼓泡或喷射的形式穿过塔盘上的液层使两相密切接触,进行传质。
两相的组分浓度沿塔高呈阶梯式变化。
在填料塔中,塔内装填一定段数和一定高度的填料层,液体沿填料表面呈膜状向下流动,作为连续相的气体自下而上流动,与液体逆流传质。
两相的组分浓度沿塔高呈连续变化。
人们又按板式塔的塔盘结构和填料塔所用的填料,细分为多种塔型。
装有机械运动构件的塔,也就是有补充能量的塔,常被用来进行萃取操作,液有用于吸收、除尘等操作的,其中以脉动塔和转盘塔用得较多。
塔设备的构件,除了种类繁多的各种内件外,其余构件则是大致相同的。
1.塔体塔体是塔设备的外壳。
常见的塔体是由等直径、等壁厚的圆筒和作为头盖和低盖的椭圆形封头所组成。
随着化工装置的大型化,渐有采用不等直径、不等壁厚的塔体。
塔体除满足工艺条件(如温度、压力、塔径和塔高等)下的强度、刚度外,还应考虑风力、地震、偏心载荷所引起的强度、刚度问题,以及吊装、运输、检验、开停工等的影响。
对于板式塔来说,塔体的不垂直度和弯曲度,将直接影响塔盘的水平度(这指标对板式塔效率的影响是非常明显的),为此,在塔体的设计、制造、检验、运输和吊装等各个环节中,都应严格保证达到有关要求,不使其超差。
2.塔体支座塔体支座是塔体安放到基础上的连接部分。
它必须保证塔体坐落在确定的位置上进行正常的操作。
为此,它应当具有足够的强度和刚度,能承受各种操作情况下的全塔重量,以及风力、地震等引起的载荷。
最常用的塔体支座是裙式支座(简称为“裙座”)。
3.除沫器除沫器用于捕集夹带在气流中的液滴。
使用高效的除沫器,对于回收贵重物料、提高分离效率、改善塔后设备的操作状况,以及减少对环境的污染等,都是非常必要的。
4.接管塔设备的接管是用以连接工艺管路,把塔设备与相关设备连成系统。
按接管的用途,分为进液管、出液管、进气管、出气管、回流管、侧线抽出管和仪表接管等。
5.人孔和手孔人孔和手孔一般都是为了安装、检修检查和装填填料的需要而设置的。
在板式塔和填料塔中,各有不同的设置要求。
6.吊耳塔设备的运输和安装,特别是在设备大型化后,往往是工厂基建工地上一项举足轻重的任务。
为起吊方便,可在塔设备上焊以吊耳。
7.吊柱在塔顶设置吊柱是为了在安装和检修时,方便塔内件的运送。
1.3对塔设备的要求
作为主要用于传质过程的塔设备,首先必须使气(汽)液两相能充分接触,以获得较高的传质效率。
此外,为了满足工业生产的需要,塔设备还得考虑下列各项要求。
(1)生产能力大。
在较大的气(汽)液流速下,仍不致发生大量的雾沫夹带、拦液或液泛等破坏正常操作的现象。
(2)操作稳定、弹性大。
当塔设备的气(汽)液复合量有较大的波动时,仍能在较高的传质效率下进行稳定的操作。
并且塔设备应保证能长期连续操作。
(3)流体流动的阻力小,即流体通过塔设备的压力降小。
这将大大节省生产中的动力消耗,以降低经常操作费用。
对于减压蒸馏操作,较大的压力降还将使系统无法维持必要的真空度。
(4)结构简单、材料耗用量小、制造和安装容易。
这可以减少基建过程中的投资费用。
(5)耐腐蚀和不易堵塞,方便操作、调节和检修。
事实上,对于现有的任何一种塔型,都不可能完全满足上述的所有要求,仅是在某些方面具有独到之处。
人们对于高效率、生产能力大、稳定操作和低压力降的追求,推动着塔设备新结构型式的不断出现和发展。
1.4塔设备的发展及现状
泡罩塔是1813年Cellier提出的,它在化工生产中一直占有重要的地位。
从1832年开始用于酿造工业,是出现较早并获得广泛应用的一种塔型。
工业规模的填料塔始于1881年的蒸馏操作中,1904年才用于炼油工业,当时的填料是碎砖瓦、小石块和管子缩节等。
20世纪初,随着炼油工业的发展和石油化学工业的兴起,塔设备开始被广泛采用,并逐渐积累了有关设计、制造、安装、操作等方面的数据和经验。
当时,炼油工业中多用泡罩塔,无机酸碱工业则以填料塔为主,则筛板塔因当时尚无精确的设计方法和操作经验,故未能广泛使用。
20世纪中期,为了适应各种化工产品的生产和发展,不仅需要新建大量的塔,还得对原有得塔设备进行技术改造,故而陆续出现了一批能适应各方面要求的新塔型。
这一时期发展的塔盘如下。
1.泡罩型
(1)条形泡罩塔盘。
(2)单流式泡罩塔盘(unifluxtray),亦称S形塔盘。
2.筛板型
(1)有溢流的栅板塔盘。
(2)波纹筛板塔盘(rippletray)。
3.浮阀型
(1)条形浮阀塔盘(nutterfloatvalvetray)。
(2)重盘式浮阀塔盘(ballastvalvetray)。
(3)A型和T型的圆盘形浮阀塔盘(flexitray)。
4.喷射型
(1)文丘里阶梯式塔盘(benturikaskadetray)。
(3)舌形塔盘(jettray)。
(4)导向浮阀塔盘。
这批新型塔盘的出现,不仅为创建综合性能更好的塔型打开了思路,而且为接着发生的设备大型化后选择塔型指出了方向。
在此期间,许多学者总结了塔设备长期操作的经验,并对筛板塔作了系统研究,认为设计合理筛板塔,不仅保留了制造方便、用材省、处理能力大等优点,而且操作负荷在较大范围内变动时,仍能保持理想的效率。
近年来,随着对筛板塔研究工作的不断深入和设计方法的日趋完善,筛板塔已成为生产上最为广泛采用的塔型之一。
这一时期填料塔也进入了一个新的发展阶段。
在瓷环填料,亦称拉西环填料(Raschigring)被广泛采用后,弧鞍形填料(Berlsaddle)相继问世,特别是出现了斯特曼(Stedman)填料后,更大大地促进了规整填料的发展,其中有:
帕纳帕克(Panapak)填料、古德洛(Goodloe)填料、斯普雷帕克(Spraypak)填料等。
同时,麦克马洪(Mcmahon)填料、鲍尔环填料(Pallring)、狄克松环填料(Dixonring)、坎农(Cannon)填料和矩鞍形填料(Intaloxsaddle)等颗粒型填料也纷纷出现。
除了各种填料大量涌现外,还发展了多管塔、乳化塔等被称为高效填料塔德新塔型。
从20世纪60年代起,由于化工机械制造业成功地解决了高压离心式压缩机的转动密封和高温高压废热锅炉的结构强度设计等技术关键,使化肥和石油化工的生产,在能量综合利用方面提高到一个新水平,继而带动了整个化学、炼油工业向大型化方向迅速发展。
据有关资料报道,炼油装置的年处理能力也达1000万吨,年产60~90万吨的乙烯工厂、60万吨的甲醇工厂、45万吨的氯乙烯工厂、34万吨的低密度聚乙烯工厂、31.5万吨的苯乙烯工厂以及22.5万吨的异丙苯工厂,也将相继兴建。
在大型装置中,塔设备的单台规模也随之增大。
直径在10m以上的板式塔时有出现(如某炼油厂的减压蒸馏塔塔径为12.2m,并在酝酿设计18m直径的塔),塔板数多达上百块,塔的高度达80余米,设备重量有几百吨(操作时的最大塔重可达1500吨);填料塔的最大直径也有15m,塔高达100m。
近年来,由于出现了世界性的能源危机,暴露出设备大型化带来的不容忽视的问题:
大型设备必须保证在全负荷下长期连续运转,否则经济损失将是非常巨大的。
在此期间,为了满足设备大型化以及化工工艺方面提出的高压、减压、高操作弹性等特殊要求,又出现了很多新型塔盘,但按其结构特点,仍属泡罩、筛板、浮阀、舌型等几种典型塔型的改进或相互结合。
举例如下。
1.属泡罩型的
(1)旋转泡罩塔盘。
(2)带有导流叶片的泡罩塔盘。
(3)扁平泡罩塔盘。
(4)蜂窝形泡罩塔盘。
2.属筛板型的
(1)导向筛板塔盘(lindesievetray),即林德筛板塔盘。
(2)多降液管筛板塔盘(multipledowncomersievetray),即MD筛板塔盘。
(3)筛网塔盘(cm
根据式(2.20)、(2.21)、(2.23)计算,同理可得:
提馏段平均表面张力:
13.65dyncm
2.7汽化热和热容的计算
内插关系式:
(2.24)
内插关系式:
(2.25)
混合物的汽化热:
(2.26)
混合物的热容:
(2.27)
表2.5各组分的汽化热与温度的关系
表2.6各组分的热容与温度的关系
查表2.5并根据式(2.24)、(2.26)计算加料板平均汽化热:
查表2.6并根据式(2.25)、(2.27)计算,同理可得:
料液平均热容:
190.171Jmol﹒K
2.8物性数据总汇
T
Jmol
K
塔顶
37.209
0.2
14.15
加料板
48.527
0.21
13.95
塔釜
66.617
0.21
13.35
27635.002
精馏段
42.868
3.04
611.97
2.85
0.21
14.05
27805.24
提馏段
57.57
613.6
2.98
160603.4
54521.04
全塔
50.22
2.95
2.91
0.2
13.65
料液
41.76
190.171
第三章塔板计算
3.1物料衡算
F=D+W(3.1)
(3.2)
其中,F、D、W分别为进料、塔顶、塔釜的摩尔流量,(kmolcm的物系负荷系数计算而得,由史密斯关联图查得。
查史密斯关联图得方法:
分别由精馏段和提馏段的参数得史密斯关联图的横坐标值A(精)、A(提),以及曲线值B,在图中查得值。
(4.1)
(4.2)
(4.3)
其中=板间距(m)由塔径选用,=塔板上液层高度且取值范围0.05-0.08m
表4.1塔径与板间距的关系
板间距选择为:
300、350、450、500、600、800mm
图4.1史密斯关联图
取塔板上液层高度为0.06m,塔径为1.6m,板间距为0.45m并根据式(4.3)计算史密斯图曲线值B:
m
根据式(4.1)计算史密斯图横坐标值A(精):
根据式(4.2)计算史密斯图横坐标值A(提):
4.2空塔气速及塔径
极限空塔气速
(4.4)
(4.5)
空塔气速(4.6)
塔径(4.7)
其中,为极限空塔气速(ms),u为空塔气速(ms),为体积流量(),应将精馏段和提馏段的体积流量分别代入塔径计算公式,可得两段的塔径,D为塔径,两段塔径求出后应分别圆整成标准塔径,塔径可为0.6、0.7、0.8、1.0、1.2、1.4、1.6、1.8、2.0、2.2、2.4、……、4.2m
根据式(4.5)计算精馏段负荷系数C(精):
根据式(4.4)计算精馏段极限空塔气速:
ms
根据式(4.6)计算精馏段空塔气速(ms):
ms
根据式(4.7)计算精馏段塔径:
m圆整为1.6m
同理,可根据式(4.4)、(4.5)、(4.6)、(4.7)分别计算出:
提馏段负荷系数C(提):
0.065
提馏段极限空塔气速:
0.929ms
提馏段空塔气速:
0.696ms
提馏段塔径:
1.561m圆整为1.6m
4.3溢流装置计算
1.在溢流装置计算时,所用的塔径是圆整后的塔径,在实际生产中,使用的精馏塔一般精馏段和提馏段的塔径相同,因此在两段塔径圆整后,取较大一段的塔径设计溢流装置。
2.由于精馏段与提馏段流体的体积流量相差很多,因此在设计溢流装置时,选用的参数应考虑流量的影响(最好精馏段和提馏段的的结构不一样),以满足流体力学要求。
3.为求降液管的宽(Wd)和降液管的面积(Af),需查图获得,此图的横坐标值为LWD,用K表示。
在图中横坐标为K处向上做垂线,与图中的两条曲线各得一交点,由这两点分别作水平线与纵轴分别交于两点I和J,I=WdD,J=AfAT,AT为塔截面积。
AT=πD24(4.8)
堰上液层高:
(4.10)
堰高:
(4.11)
降液管底隙高:
(4.12)
(4.13)
其中,E为堰长系数且常取0.6~0.8,K为求弓形降液管的宽和面积图的横坐标值,由K值可在图中查得和值。
纵坐标值:
(4.14)
(4.15)
塔截面积:
(4.16)
其中,I、J为由横坐标K值在图中查得的纵坐标值,为塔截面积(),为降液管面积(),为降液管宽()。
图4.2和值与LWD的关系
精馏段:
根据式(4.9)计算堰长(m):
m
根据式(4.10)计算堰上液层高度(m):
m
根据式(4.11)计算堰高:
m
根据式(4.12)计算降液底隙高:
m
根据式(4.13)计算精馏段横坐标值K:
根据式(4.16)计算塔截面积():
由图4.2查得I为0.15,J为0.09并根据式(4.15)计算降液管面积()和降液管宽:
m
同理根据式(4.9)、(4.11)、(4.12)、(4.13)、(4.14)、(4.15)、(4.16)计算提馏段:
堰长(m):
1.12m
堰上液层高度(m):
0.028m
堰高(m):
0.032m
降液底隙高(m):
0.0264m
提馏段横坐标值K:
0.7
塔截面积():
2.011
降液管面积():
0.181
降液管宽(m):
0.24m
4.4阀孔数计算
液体在降液管内的停留时间
(应大于5秒):
(4.17)
阀孔气速(ms):
(4.18)
计算阀孔数:
(4.19)
其中,为阀孔气体的动能因子,对重阀,适宜选择范围为9-12,为降液管截面积,为板间距,为阀孔直径且取0.039m。
s
根据式(4.18)、(4.19)计算精馏段理论阀孔数:
ms
同理根据式(4.17)、(4.18)、(4.19)计算:
提馏段理论阀孔数:
192.563
4.5塔板布孔
塔板阀孔的排布是根据下面原则进行的:
矩形板宽为377mm,长为M,通道板为400mm,长为M,弓形板宽为E,长为M
(4.20)
(4.21)
其中,为矩形板数,为塔盘分块总数。
图4.3矩形板的尺寸图
第一列孔的位置26+x'>Ws
4.5.1塔板布孔——精馏段
1.采用三角形叉排,孔心距取75毫米;
2.相邻排间距可取65、80、100毫米中的一种进行作图;
3.直径大于800毫米的塔,应将塔盘分块,保持有一块通道板,两块弓形板,其余为矩形板,分块情况如下:
表4.2塔盘分块数与塔径的关系
4.根据要求作图得实际阀孔数,其值应接近算的阀孔数;
5.排孔时塔盘的边缘区宽的适宜范围为50~75mm;
6.排孔时塔盘的破沫区宽取值为:
D小于1.5m取60~75mm
D大于1.5m取80~110mm
D小于1.0m可适当减小
7.开孔率=阀孔总面积塔截面积
精馏段阀孔数:
如下图所示
图4.4精馏段阀孔数
4.5.2塔板布孔——提馏段
图4.5提馏段阀孔数
第五章流体力学
5.1塔板流体力学验算
(一)
5.1.1气体通过塔板的压力降
(1)——精馏段
压力降(5.1)
塔板压力降应为10——526Pa
压力降用液柱高表示为(5.2)
其中,为干板压力降(m),为气体通过液层的压力降(m),为由表面张力产生的阻力损失。
(可忽略)
当阀全开前
(5.3)
当阀全开后
(5.4)
当阀刚刚全开时式(5.3)、(5.4)两式相等,求得的孔速为临界阀孔气速()
(5.5)
其中,为阀孔气速(ms),为精馏段液体密度(Kg),为精馏段气体密度(Kg)。
当时,可采用式(5.3)计算干板阻力
当时,可采用式(5.4)计算干板阻力
充气液层阻力(5.6)
其中,为充气因数且取0.4——0.5。
压力降:
(Pa)(5.7)
阀空气速(5.8)
其中,No为实排的阀孔数。
根据式(5.8)计算:
ms
精馏段塔板平均压力降(m液柱):
0.074m
精馏段塔板平均压力降:
445.14Pa
5.1.2气体通过塔板的压力降
(2)——提馏段
压力降(5.9)
塔板压力降应为10——526Pa
压力降用液柱高表示为(5.10)
其中,为干板压力降(m),为气体通过液层的压力降(m),为由表面张力产生的阻力损失。
(可忽略)
当阀全开前
(5.11)
当阀全开后
(5.12)
当阀刚刚全开时式(5.11)、(5.12)两式相等,求得的孔速为临界阀孔气速()
(5.13)
其中,为阀孔气速(ms),为精馏段液体密度(Kg),为精馏段气体密度(Kg)。
当时,可采用式(5.11)计算干板阻力
当时,可采用式(5.12)计算干板阻力
充气液层阻力(5.14)
其中,为充气因数且取0.4——0.5。
压力降:
(Pa)(5.15)
阀空气速(5.16)
其中,No为实排的阀孔数。
提馏段塔板平均压力降(m液柱):
0.071m
提馏段塔板平均压力降:
424.917Pa
5.2流体力学验算
(二)
5.2.1淹塔(液泛)验算
(1)——精馏段
判断是否成立,如不成立,则要发生液泛
当量清液层高(5.17)
(5.18)
其中,为上升气体的压力降(米液柱),为板上液层高(m),为液体通过降液管的压力降(米液柱),为板间距(m),为堰高(m),为充气系数且对一般物系取0.5,易发泡物系取0.3—0.4,不易发泡物系取0.6—0.7。
根据式(5.18)计算降液管的压力降(m):
m
根据式(5.17)计算当量清液层高(m):
m
:
0.3224
不能产生液泛
5.2.2淹塔(液泛)验算
(1)——提馏段
判断是否成立,如不成立,则要发生液泛
当量清液层高(5.19)
(5.20)
其中,为上升气体的压力降(米液柱),为板上液层高(m),为液体通过降液管的压力降(米液柱),为板间距(m),为堰高(m),为充气系数且对一般物系取0.5,易发泡物系取0.3—0.4,不易发泡物系取0.6—0.7。
根据式(5.20)计算降液管的压力降(m):
m
根据式(5.21)计算当量清液层高(m):
m
:
0.3133
不能产生液泛
5.3流体力学验算(三)
5.3.1物沫夹带
(1)——精馏段
当气体上升时雾沫夹带量时,泛点率应小于80%。
(5.21)
(5.22)
(5.23)
其中,为泛点率且应小于80%,为降液管宽度(m),为板上液体流径长(m),为塔截面积(),为板上液流面积(),为弓形降液管截面积(),D为塔径(m),为泛点负荷系数且查图得,K为物性系数且查表(正常系统取1)。
图5.1泛点负荷系数与密度的关系
根据式(5.22)计算液体流径长(m):
m
根据式(5.23)计算液流面积():
根据式(5.21)计算泛点率:
5.3.2物沫夹带
(2)——提馏段
当气体上升时雾沫夹带量时,泛点率应小于80%。
(5.24)
(5.25)
(5.26)
其中,为泛点率且应小于80%,为降液管宽度(m),为板上液体流径长(m),为塔截面积(),为板上液流面积(),为弓形降液管截面积(),D为塔径(m),为泛点负荷系数且查图得,K为物性系数且查表(正常系统取1)。
根据式(5.25)计算液体流径长(m):
m
根据式(5.26)计算液流面积():
根据式(5.24)计算泛点率:
50.887%
第六章负荷性能图
6.1确定雾沫夹带上限线方程
雾沫夹带上限线:
此线表示雾沫夹带量时的关系。
塔板的适宜操作区应在此线以下,否则因过多的雾沫夹带而使板效率严重降低。
方程获取的方法是让泛点率为最大值即等于80%。
(6.1)
(6.2)
根据式(6.2)可得精馏段雾沫夹带上限线方程为:
同理根据式(6.2)可得提馏段雾沫夹带上限线方程为:
6.2确定液泛线方程
液泛线表示降液管内泡沫层高度达到最大允许值时的的关系式。
塔板操作区应在此线以下,否则将可能发生液泛现象,破坏塔的正常操作。
液泛线由下式确定:
(6.3)
把上式中的物理量代入并整理后可得方程:
(6.4)
其中,,,,,、分别为精馏段气体、液体密度(Kgm),、分别为气体、液体的体积流量(),N为阀孔数,为堰高(m),为堰长(m),为系数,为降液管底隙高(m),为板间距(m),为充气系数,E为液流收缩系数(常取1)。
根据式(6.4)可得精馏段液泛线方程为:
同理根据式(6.4)可得提馏段液泛线方程为:
6.3液相负荷上限线
液相负荷上限线又称降液管超负荷线,此线反映对于液体在降液管内停留时间的起码要求,液体在降液管内停留时间过短,则气泡不能及时放出而进入下层塔板,造成气相返混,降低塔板效率,塔板适宜操作区应在此线左方。
液体在降液管内的停留时间最短不应低于5秒钟,依此列方程得:
(6.5)
(6.6)
根据式(6.6)可得精馏段液相负荷上限线方程为:
同理根据式(6.6)可得提馏段液相负荷上限线方程为:
6.4液相负荷下限线
对于平堰,一般取堰上液层高=0.006m作为液相负荷下限条件,低于此线,便不能保证板上液流均匀分